
книги из ГПНТБ / Шнейдер, Юрий Григорьевич. Холодная бесштамповая обработка точных деталей давлением
.pdfФиг. 41. Станок РК-1 для профильного ротационного обжатия.
Между копирным кольцом и шпинделем 1 помещен конический сепаратор 5, состоящий из двух колец и вставок между ними. Между вставками находятся ролики 4. Головка пустотелого шпинделя имеет два взаимно-перпендикулярных паза, в которые вставляются две пары обжимных матриц 1 и бойков 3 (фиг. 42). Бойки при помощи пазового соединения связаны с крыльями 2, молоткообразная головка
которых несколько больше кругового шага роликов. Это устройство,
обеспечивая непрерывное контактирование бойков с роликами,
приводит к |
снижению |
шума |
и |
увеличению |
срока |
службы бойков |
||||||
и роликов |
(значительный шум |
и |
быстрый износ |
матриц, |
бойков |
|||||||
и роликов являются |
основными |
недостатками всех |
ротационно- |
|||||||||
2 |
3 |
2 |
обжимных |
станков, |
несколько огра |
|||||||
ничивающими их применение). Прин |
||||||||||||
|
|
|
цип обжатия заготовки такой же, |
|||||||||
|
|
|
как у обычных ротационно обжим |
|||||||||
|
|
|
ных |
станков. |
Бойки |
и |
матрицы |
|||||
|
|
|
(в станке РК-1 четыре матрицы) совер |
|||||||||
|
|
|
шают наряду с вращательным воз |
|||||||||
|
|
|
вратно-поступательное |
движение |
||||||||
|
|
|
(в радиальном направлении). При |
|||||||||
|
|
|
перемещении |
копирного |
кольца |
|||||||
|
|
|
вправо |
(в |
сторону подачи) |
система |
||||||
|
|
|
ролик—боек—матрица |
удаляется |
||||||||
|
|
|
от центра; в это время происходит |
|||||||||
|
|
|
обжатие заготовки на конус с посте |
|||||||||
|
|
|
пенным уменьшением степени дефор |
|||||||||
Фиг. 42. Узел матрицы, бойка |
мации. |
Вершина конуса будет обра |
||||||||||
щена вправо, в сторону |
подачи. При |
|||||||||||
и |
крыльев. |
|
||||||||||
обжимается |
|
|
перемещении копирного кольца влево |
|||||||||
конус с вершиной, обращенной в обратную сторону. |
||||||||||||
При обжатии цилиндрического |
участка |
копирное кольцо остается |
неподвижным. Такой принцип работы станка обеспечивает возмож ность обработки сложных профильных деталей одной установки заготовки.
Перемещение копирного кольца осуществляется специальным профилирующим устройством. Для предотвращения изгиба прутка
впроцессе обжатия цанговое устройство вместе с прутком вращается
всторону, обратную движению шпинделя рабочей головки (и прут ка — 60 об/мин.).
Технико-экономические показатели станка РК-1 при обработке шпинделей следующие. Производительность в смену с учетом вре
мени на наладку составляет 1300 -г- 1400 шпинделей (при обслужи вании двумя рабочими 4-го разряда). Экономия металла (сталь ШХ9)
по сравнению с токарной обработкой — 40%, или НО г на один шпиндель. Точность обработки в пределах 3 -н 4-го класса. Чистота поверхности соответствует 9 ч- 10-му классам. Износ рабочего про филя матриц (матрицы изготовляются из сталей марок ХВГ или 5ХВС и закаливаются до твердости RC =61 -г- 64) наступает после изготовления 4000 5000 заготовок шпинделей. Затем матрицы
80
|
|
|
|
|
|
|
|
Таблица 9 |
|
Механические свойства обжатых сырых и |
|
закаленных образцов |
|
||||||
|
Обточенные образцы |
|
|
|
Обжатые образцы |
|
|||
Термическая |
|
|
|
|
8 |
|
|
|
|
обработка |
Твердость |
|
°в |
в |
|
Твердость |
°в |
6 |
|
|
в |
»/„ |
В °/о |
||||||
|
|
кг/мм.1 |
|
в кг]мм1- |
Исходное |
со |
НВ = 1594-167 |
65,1 |
24 |
НВ = 250 |
101,3 |
14,5 |
|
стояние |
|
|
||||||
|
|
|
|
|
|
|
|
|
Нагрев |
до |
t = |
|
|
|
|
|
|
= 680°, |
выдержка |
НВ = 1594-167 |
65 |
16 |
НВ = 250 |
103,1 |
10,2 |
|
30 мин., охлажде |
||||||||
ние на воздухе |
|
|
|
|
|
|
||
Закалка: |
подо |
|
|
|
|
|
|
|
грев до |
t = 680°, |
|
|
|
|
|
|
|
выдержка 30 мин., |
|
|
|
|
|
|
||
охлаждение в масле |
RC = 494-52 |
208 |
4 |
7? С=494-52 |
208 |
4 |
||
до t = 160°; отпуск |
|
|
|
|
|
|
||
в селитровой ванне |
|
|
|
|
|
|
||
при t = 3404-350°, |
|
|
|
|
|
|
||
выдержка 15 |
мин. |
|
|
|
|
|
|
подвергаются шлифованию; количество допускаемых перешлифовок
комплекта матриц — пятнадцать.
Представляют интерес приведенные в табл. 9 данные о механи
ческих свойствах обжатых сырых и закаленных образцов [18].
Из таблицы следует, что в исходном состоянии металл, подвергнутый
обжатию, обладает значительно большей прочностью, чем обычный холоднотянутый, а после термической обработки заготовки, обра ботанные резанием и давлением, имеют близкие показатели по меха ническим свойствам.
Однако металлографический анализ показал, что заготовки шпинделей, изготовленных методом профильного обжатия, после закалки имеют более благоприятную структуру (мелкоигольчатый мартенсит), чем после обработки точением; соответственно и износ при эксплуатации характеризуется лучшими показателями.
Сочетание высокой производительности с высокой точностью и хорошим качеством поверхности обрабатываемых деталей позво ляет считать метод ротационного обжатия одним из совершенных и перспективных способов холодной обработки металлов давлением, применение которого способствует решению основной технологи ческой задачи — предельного сокращения пути превращения заго товки в готовую деталь.
6 Ю. Г. Шнейдер 648 |
81 |
8. Обжатие трубчатых деталей фильерой,
роликами и шариками
Обработка тонкостенных трубчатых деталей с различной вдоль оси толщиной стенок инструментом с металлическим лезвием связана с большими трудностями. Значительные силы резания и выделяю щееся в процессе резания тепло приводят к деформированию тонко стенной маложесткой заготовки и к образованию разностенности. Более совершенным процессом обработки тонкостенных трубчатых деталей является обжатие фильерами или свободно вращающимися роликами или шариками. Схема обжатия фильерой показана на фиг. 43.
Заготовка 1, получая вращение от шпинделя станка, подается в отверстие фильеры 2.
Подача может осуществляться также путем поступательного пере
|
|
мещения |
головки |
с |
вращающейся |
||||
|
|
фильерой. Засчетнатяга, равного раз |
|||||||
|
|
ностидиаметров заготовки и отверстия |
|||||||
|
|
фильеры, |
при подаче заготовки про |
||||||
|
|
исходит |
обжатие |
ее |
по |
наружному |
|||
|
|
и внутреннему контуру. Заготовка |
|||||||
|
|
испытывает сложную |
деформацию |
||||||
|
|
сжатия, продольного изгиба и кру |
|||||||
|
|
чения, что ограничивает применение |
|||||||
|
|
этого |
метода |
обработки |
для де- |
||||
Фиг. 43. Схема обработки |
обжа- |
талей |
сравнительно небольшой дли- |
||||||
тием фильерой. |
ны. |
Так, ПрИ |
обжатии |
трубчатых |
|||||
|
|
заготовок из латуни марки ЛС62 до |
|||||||
пустимые значения |
находятся в |
пределах |
10-н 12 |
(/ — длина, |
d — диаметр заготовки). Основными параметрами режима обжатия
являются: степень обжатия, подача и скорость вращения фильеры или заготовки. Значения этих составляющих тем выше, чем легче пластически деформируется обрабатываемый металл. Например,
оптимальными значениями составляющих режима обжатия латунной (ЛС62) трубки диаметром 3 мм с толщиной стенки 0,5 мм явля
ются: степень обжатия за один проход 10 -н 15%, число оборотов
фильеры |
960 в мин., продольная подача заготовки 0,5 мм за |
1 оборот |
фильеры. |
Последовательным многократным обжатием можно достичь сте пени обжатия равной 50 -н 70%.
Примером применения метода обжатия фильерой может служить обработка латунного штыря штепсельного разъема (фиг. 98, б) после двукратного ротационного обжатия заготовки на специальном многопозиционном автомате. В этом случае одновременно с обжатием
фильерой до диаметра 1,5_0,1з осуществляется осаживание бур тика.
Иногда способ обжатия фильерой применяется с целью калибро
вания размера не только трубчатых деталей, но и деталей типа осей и валиков.
82
Усилие обжатия фильерой, имеющей в рабочей части цилиндри ческий поясок, может быть определено по формуле [90]
где Р — усилие |
обжатия; |
Р == FoVpn |
|
||
заготовки; |
|
||||
— исходное |
сечение |
|
|||
<зрн ■— рабочее |
осевое напряжение. |
|
|||
Значения арн |
в зависимости от степени вытяжки Т получены |
||||
экспериментально: |
стали 20 |
арн — 4,1 |
111,61’; |
||
для |
|||||
для |
стали |
45 |
<зрн = 9,0 |
209,6Г; |
|
для стали |
40Харн = 6,5 + 186 Г. |
Обжатием фильерами до
стигается 3 и 2-й классы
точности и 9-й класс чистоты поверхности. В зависимости от свойств обрабатываемого металла и условий обработки микротвердость по сравнению
с исходной |
повышается на |
|
||
10 ч- 20%. |
|
недостатками |
|
|
Основными |
|
|||
описанного |
процесса |
явля |
|
|
ются, во-первых, наличие |
|
|||
больших сил |
трения |
между |
|
|
поверхностью |
обрабатывае |
|
||
мой заготовки и фильерой |
|
|||
и, во-вторых, сильное нали |
|
|||
пание на рабочие поверхности |
|
|||
инструмента |
|
металла |
заго |
|
товки, особенно при обжатии |
|
|||
таких вязких металлов, как |
|
|||
латунь и медь. В результате |
|
|||
налипания металла резко воз |
Фиг. 44. Тонкостенная трубка, обрабатывае |
|||
растают силы трения и увели |
мая обжатием роликами (а); схема обработки |
|||
чивается натяг, что в рядеслу- |
тонкостенной трубки обжатием тремя роли |
|||
чаев приводит |
к разрушению |
ками (б). |
||
|
заготовок. Некоторому уменьшению налипания способствует хроми рование рабочих поверхностей фильеры.
Более благоприятные условия пластического деформирования
металла создаются при обжатии трубчатых заготовок роликами,
свободно вращающимися на своих осях. Замена трения скольжения трением качения между роликами и заготовкой обеспечивает воз
можность работы со значительно меньшими усилиями, чем при
обжатии фильерами. Это способствует уменьшению деформации заготовки и повышению точности ее обработки, устранению нали пания металла и стойкости инструмента (роликов).
Уменьшение усилий, прилагаемых для деформирования металла,
особенно существенно при изготовлении тонкостенных деталей,
6* |
83 |
так как возникающая при обжатии деформация скручивания огра
ничивает возможности этого процесса обработкой деталей лишь со сравнительно большой толщиной стенок.
Возможности процесса обжатия роликами наглядно иллюстри руются примером обработки детали (фиг. 44, а) с толщиной стенки 0,6 лии. Схема обжатия показана на фиг. 44, б. Трубчатая заготовка 2 надевается на оправку 1, закрепленную в шпинделе сверлильного станка (для обжатия роликами могут быть использованы и другие металлообрабатывающие станки), и устанавливается между тремя
роликами 3, свободно вращающимися на
|
прецизионных |
игольчатых |
подшипниках. |
|||
|
Оси |
роликов, расположенные через |
каждые |
|||
|
120°, |
закреплены в |
специальном приспосо |
|||
|
блении, устанавливаемом на столе сверлиль |
|||||
|
ного станка (фиг. 45). |
|
|
|||
|
Положение одного из роликов относи |
|||||
|
тельно двух других |
регулируется |
враще |
|||
|
нием рукоятки, |
перемещающей каретку с по |
||||
|
движным роликом, и определяет величину |
|||||
|
утонения стенки заготовки за один проход. |
|||||
|
Вращаясь, заготовка одновременно пере |
|||||
|
мещается вдоль оси роликов, |
которые |
||||
|
обжимают ее до требуемого размера. |
|||||
|
Деталь, показанная на фиг. 44, а, обжи |
|||||
|
мается за один проход. |
|
|
|||
|
Точность формы и размеров обрабатывае |
|||||
|
мых деталей в значительной степени зависит |
|||||
|
от тщательности изготовления роликов, ко |
|||||
|
торыми производится обжатие. Ролики изго |
|||||
Фиг. 45. Приспособление |
товляются из инструментальной углероди |
|||||
стой |
стали. Они должны быть закалены до |
|||||
к сверлильному станку |
твердости 63 -4- |
65 RC и тщательно |
отполи |
|||
для обжатия тонкостенных |
||||||
трубок. |
рованы; биение роликов не |
должно |
превы |
|||
|
шать |
0,005 мм. |
|
|
|
|
Применение разъемных фасонных оправок позволяет производить обработку описанным способом не только гладких цилиндрических деталей, но и деталей, имеющих ребра, рифление, а также узорчатую поверхность.
Обжатию роликами могут подвергаться как детали из мягких
исплавов (медь, алюминиевые сплавы), так и из весьма твердых
металлов (твердые стали, молибден и др.).
Для обжатия трубчатых деталей с успехом могут быть применены
иразличные устройства, в которых обжимающие ролики заменяются шариками. Так, на ленинградском заводе «Автоарматура» шариками, установленными в обойме, на доделочном станке обжимаются концы составных трубок (из нержавеющей стали) автомобильной антенны.
Во всех случаях обжатия роликами и шариками точность обра ботки зависит от стабильности механических свойств обрабатываемых заготовок и их исходных размеров под обжатие и может достигать
84
Таблица 10
Режимы выдавливания на токарно-давильном станке
Обрабатываемый
материал
Алюминий
Сталь холодно катаная
Сталь нержавеющая
Медь
Латунь
Диаметр |
Толщина |
Число оборотов |
Скорость выда |
детали в мм |
материала в мм |
шпинделя |
вливания |
|
|
в минуту |
в м/мин |
20 |
0,4 |
2400 |
150 |
150 |
0,8 |
1225 |
586 |
230 |
1,6 |
920 |
660 |
360 |
2,5 |
525 |
600 |
920 |
3,2 |
450 |
1300 |
3660 |
6,5 |
112 |
1300 |
50 |
0,65 |
1225 |
190 |
180 |
0,8 |
1000 |
570 |
230 |
0,9 |
920 |
670 |
250 |
1,0 |
920 |
720 |
460 |
2,8 |
575 |
830 |
460 |
3,2 |
325 |
470 |
640 |
3,2 |
242 |
485 |
380 |
0,2 |
525 |
630 |
920 |
0,2 |
375 |
1080 |
120 |
02 |
2400 |
150 |
125 |
0,4 |
1225 |
480 |
230 |
1,0 |
1000 |
720 |
360 |
1,6 |
575 |
650 |
50 |
0,4 |
1225 |
190 |
180 |
0,8 |
1000 |
570 |
200 |
1,0 |
575 |
360 |
300 |
1,25 |
525 |
500 |
610 |
2,5 |
450 |
860 |
920 |
3,2 |
325 |
940 |
1800 |
4,8 |
242 |
1360 |
85
3-го и даже 2-го класса. Чистота обрабатываемых поверхностей в первую очередь определяется состоянием рабочих поверхностей
обжимающих роликов и шариков и характеризуется 9 -н 10-м клас сами.
9. Выдавливание полых деталей на давильных станках
Средне- и крупногабаритные полые детали типа стаканов, чашек
и фасонных кожухов из листовых заготовок, в тех случаях, когда штамповка экономически не оправдана или неосуществима, наиболее целесообразно выполнять методом холодного выдавливания и вытяж ки на давильных Станках. Однако осуществление этого процесса
на предприятиях местной промышленности, а также на некоторых заводах, на специально приспособленных устаревших изношенных станках, вручную давильниками, при изготовлении посуды или
осветительной арматуры — непроизводительно и малоэффективно. В то же время опыт некоторых отечественных и зарубежных предприятий убедительно свидетельствует о больших возможностях этого метода обработки давлением, при условии осуществления его
на специальных высокомощных быстроходных жестких станках, позволяющих применять огромные давления при высоких скоростях обжатия.
Особенно широкое распространение в промышленности получили
давильные работы |
на |
специальных токарно-давильных станках |
за последние пять |
лет, |
первоначально преимущественно в ФРГ |
и США, а затем в Англии, Канаде и Италии. Приводимые ниже примеры наглядно иллюстрируют возможности этого способа обра ботки в отношении универсальности, производительности и точности.
Фирмой «Лайфельд» (ФРГ) выпускаются токарно-давильные (фиг. 46, а) и токарно-вытяжные станки с гидравлической подачей суппортов, отдельные модели которых снабжены гидрокопировальными следящими системами, обеспечивающими получение деталей с точно заданной переменной толщиной стенок.
На этих станках выдавливаются разнообразные детали из нержа
веющей стали толщиной от 0,6 до 4,5 мм и диаметром до 4,8 л и из
алюминия толщиной до 8,5 мм.
Типичные примеры обработки деталей, получаемых на этих давильных станках, показаны на фиг. 47, а данные по режимам выдав ливания некоторых деталей приведены в табл. 10.
В результате проведенных исследований в США [20] был создан новый тип давильно-вытяжного станка (фиг. 46, б), предназначенного
для формообразования деталей из нержавеющих, жаропрочных, углеродистых и других сталей путем холодного выдавливания.1
Выдавливание производится двумя свободно вращающимися на осях роликами 1 (фиг. 48), обжимающими и вытягивающими заготовку 2 вокруг принудительно вращающейся стальной оправки 3,
закрепленной |
в шпинделе станка. |
|
1 |
Этот способ |
обработки в иностранной технической литературе иногда назы |
вают |
«гидроспиннингом», «силовым обжатием». |
86
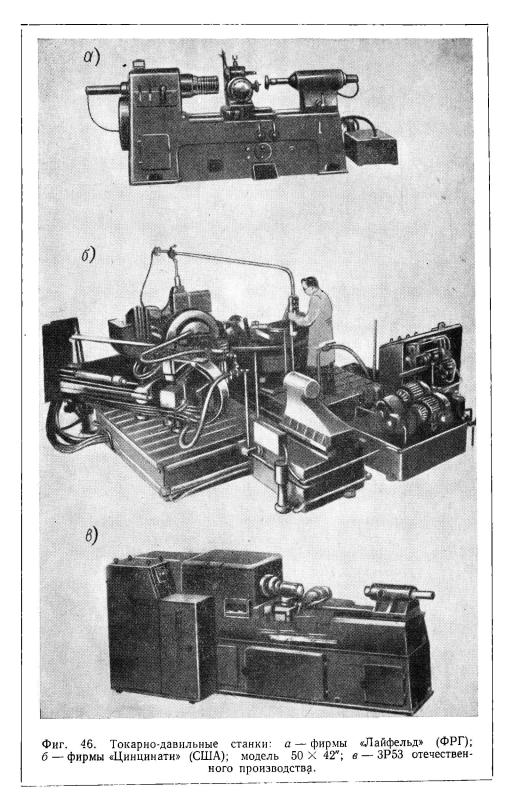
Фиг. 47. Последовательность обработки на давильном станке: а — конуса; б — фигурного стакана.