
книги из ГПНТБ / Шнейдер, Юрий Григорьевич. Холодная бесштамповая обработка точных деталей давлением
.pdfлении, определяется количеством зубьев или рифлений, располо женных по сечению обрабатываемого прутка.
На фиг. 27, а показана схема волочения прутка-заготовки для
пятизубых трибов с циклоидальным профилем зуба, а на фиг. 27, б —
схема образования |
зуба циклоидального |
профиля при |
волочении |
в роликах. Ролики |
устанавливаются в |
специальной |
головке |
(фиг. 27, в), закрепляемой |
на волочильном станке (фиг. 28); поло |
||
жение роликов |
относительно оси |
головки может регулироваться |
|
в зависимости |
от степени |
обжатия |
при каждом пропуске прутка; |
Фиг. 26. Приспособление для зажима конца прутка при волочении на протяжном станке.
число пропусков определяется свойствами материала, а также числом и размером зубьев. На Ленинградском заводе металлоизделий опи санным способом получают стальные (сталь марки 45) прутковые
заготовки (трибсталь) для шести- и девятизубых трибов. Результаты работы по получению трибстали эвольвентного
профиля с числом зубьев z = 12 |
показали |
следующее. Волочение |
производилось в приспособлении |
типа показанного на фиг. 27, в |
|
на станке с тяговым усилением до 2 500 кг\ |
скорость волочения — |
|
2 -н 6 м/мин. Заготовкой может |
служить |
проволока или пруток |
(проволока используется в качестве заготовки при изготовлении трибстали для трибов диаметром до 5 мм, в остальных случаях заго товкой служит пруток).
При волочении трибстали из бухты проволоки конец последней 'пропускается между роликами приспособления и захватывается клещевым зажимом. После протягивания на длину 1,5 н- 7 м без выключения станка производится отрезка около роликов, а высту пающий конец вновь захватывается зажимом станка. Первый проход совершается, таким образом, до полного использования бухты про волоки
59
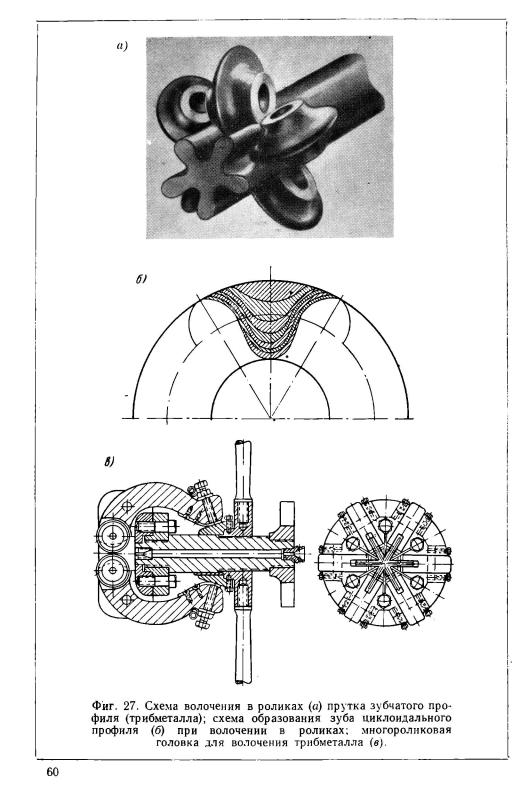
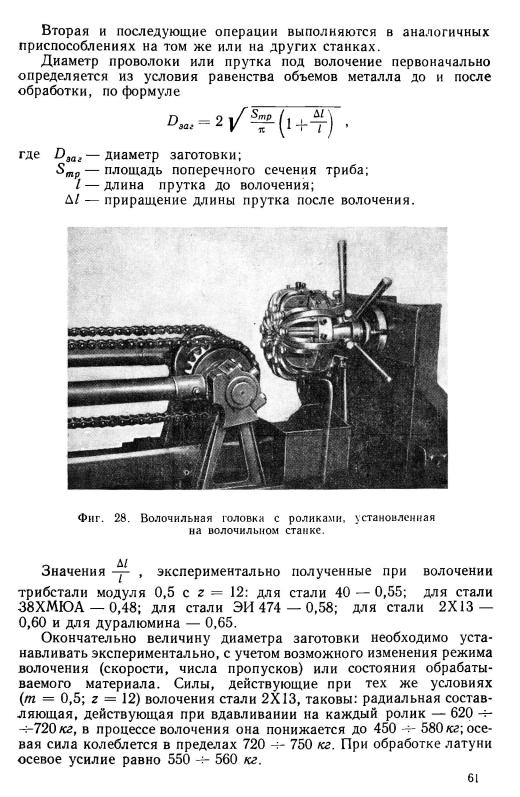
Технико-экономические показатели процесса волочения триб-
стали следующие:
1) точность соответствует 4-му классу по нормали 206МТ (для получения трибов 2 и 3-го классов точности необходимо вводить, операцию калибрования через жесткий профильный волок); чистота поверхности V?!
2)предел прочности повышается у стали 40 на 25%, у стали
2X13 —на 10%;
3)по сравнению с зубофрезерованием, волочение трибстали поз
воляет экономить 30 -4- 40% металла;
4) общая производительность по сравнению с фрезерованием зуба повышается в 2 3 раза.
Метод волочения создает предпосылки для организации центра лизованного производства трибстали, в первую очередь из сталей, трудно поддающихся обработке резанием.
Трубы в большинстве случаев обрабатывают волочением через обычные волоки (кольца). Волочение осуществляется без оправок или на оправках, которые применяют главным образом при обработке труб диаметром более 25 -4- 30 мм. Степень технологи
ческого формоизменения при обработке труб волочением принято характеризовать величиной относительного удлинения X.
При обработке труб волочением без оправки (фиг. 29, а) обеспе чивается заданное уменьшение их внешнего диаметра при относи тельно небольшом нерегламентированном изменении толщины стенок.
Характер и величина изменения толщины стенок труб при таком спо собе обработки прежде всего зависят от коэффициента относительной
толщины стенок А:
А =
где Dm и Sm — соответственно наружный диаметр и толщина стенки труб в мм.
При А > 6 толщина стенки обычно несколько увеличивается,
апри А < 5 — уменьшается.
Впроцессе обработки тонкостенных труб малого диаметра при
Sm = 1,6 -н 1,8 мм и Dm = 5 -4- 10 мм толщина стенки может умень
шаться примерно |
на |
10% за один проход, а при Sm = 2 |
3 мм. |
|
и |
Dm — 14 -4- 18 |
мм |
толщина стенки, наоборот, увеличивается |
|
На |
10%. |
|
|
|
|
При волочении стальных труб без оправки относительное удли |
нение за один проход допускается в пределах до 35 -4- 50%. Волочение труб на длинных оправках (на стержнях, фиг. 29, б)
применяют в основном для одновременного получения наибольшего
обжатия и наибольшей вытяжки, чтобы таким образом сократить количество технологических переходов. Практически в этом случае
относительное удлинение за один проход получается максимальным
и для стальных труб может достигать 80%, а иногда и более. Волочение на короткой оправке (на пробке, фиг. 29, в) применяют
для уменьшения внешнего диаметра труб при одновременно заданном
62
уменьшении толщины их стенок. Оправка при этом способе обра ботки все время принудительно удерживается в зоне деформации, и диаметры трубы получаются соответствующими размерам инстру
мента. Таким образом, этот способ по сравнению с другими обеспе чивает наиболее точную форму и размеры сечения труб.
Фиг. 29. Схемы обработки волочением: а— без оправки; б—на стержне; в — на пробке; г — на плавающей оправке; д — между роликами; е — с противонатягом.
Ввиду больших потерь на трение и опасности обрывов, обжатие, которое можно получить за один проход, в этом случае оказывается меньшим, чем в предыдущем. Относительное удлинение стальных труб за один проход при волочении их на короткой оправке обычно не превышает 45-н50%.
Волочение труб на плавающей (свободной) оправке (фиг. 29, г)
отличается от волочения на короткой оправке тем, что оправка удерживается в зоне деформации не механически, а самостоятельно,, благодаря равновесию действующих на нее сил. Это равновесие обеспечивается формой и размерами оправки, которые выбираются на основе расчета.
Волочение на плавающей оправке обеспечивает уменьшение диа метров и толщины стенок трубы. Относительное удлинение стальной
63
трубы за один проход при этом может достигать примерно 36 -г- 42%. Этот способ обработки может широко использоваться и при волоче нии труб на барабанных станках, когда оправки иных видов непри менимы.
Трубы с квадратными, прямоугольными, треугольными, шести гранными, овальными и другими формами сечений обычно изготов ляют из круглых труб волочением их через волок с неподвижными
деформирующими поверхностями. Если толщина стенок, форма и раз меры сечения таких труб должны быть точными, обжатие их при
последнем переходе осуществляется на короткой оправке соответ ствующей формы.
Трубы с овальными, эллипсовидными и некоторыми другими формами сечения успешно изготовляются из круглых путем протя гивания их между двумя или несколькими свободно вращающимися роликами ' (фиг. 29, д).
Наибольшее возможное удлинение стальных фасонных труб за один проход при волочении часто оказывается на 8 -:- 12% меньшим, чем при обработке круглых труб. Это обычно объясняется более сложными условиями течения металла в зоне деформации.
При волочении с противонатягом (реактивное волочение, фиг. 29, е)
необработанный конец заготовки, двигаясь в сторону волока, непре рывно притормаживается усилием противоположного направления. Благодаря этому металл вводится в волок в растянутом упруго напряженном состоянии и деформируется при значительно меньшем давлении на поверхностях контакта. Таким образом сокращаются потери на трение в волоке, уменьшается его нагрев и износ и увели чивается стойкость инструмента.
При плющении-волочении заготовка за один проход последова тельно протягивается между роликами и через обычный волок.
При этом предварительное большее обжатие заготовки осуществ ляется плющением с меньшими потерями на трение, а окончательное
относительно небольшее обжатие происходит в волоке. Совмещение в этом процессе плющения и волочения позволяет пользоваться преймуществами плющения, избегая свойственных ему недостатков. Волочение осуществляется с противонатягом, усилие которого исполь зуется для плющения заготовки. Благодаря противонатягу усилие плющения-волочения получается меньшим суммы усилий плю щения и волочения, производимых с теми же обжатиями, но порознь.
Относительное обжатие за один проход при плющении-воло чении может быть на 8-4- 10% больше, чем при обычном воло чении.
Как и при прокатке, производительность и качество обработки при волочении в значительной степени зависят от правильного выбора числа пропусков и величины обжатия при каждом пропуске, от формы
и размера заготовки.
Необходимое наиболее целесообразное для получения заданного профиля прутка число пропусков обусловлено степенью деформации или величиной относительного допустимого обжатия за каждый
64
пропуск. Величина относительного обжатия, как и при прокатке,
находится из отношения
К = Д=^-ЮО°/о,
|
|
Л) |
0 |
|
где Fo — площадь |
поперечного |
сечения |
прутка |
до деформации (до |
волочения); |
сечения |
прутка |
после деформации |
|
F — площадь |
поперечного |
(после волочения).
Аналогично показателям прокатки, технико-экономические пока затели волочения зависят от правильности выбора режима: скорости,
количества пропусков, степени обжатия при каждом пропуске, смазки.
Скорость при волочении зависит в первую очередь от формы и размеров сечения прутков и от свойств металла. Так, при волочении на цепных станах круглых прутков из стали марок
30 -ч- 60 диаметром 10 -г- 20 мм ориентировочная расчетная выход
ная скорость |
01 |
= 8,0 |
17,5 |
м/мин.-, при диаметре |
30 -4- 50 мм |
= 6,0 -г- 15,0 |
м/мин, |
а при |
диаметре 80 -ч- 100 мм |
v3 = 1,5 -ч- |
|
4-3,8 м/мин |
[37]. |
|
|
|
Соответственно, для тех же интервалов диаметров при волочении
прутков из сталей марок 40Х, ШХ и ЗОХМА Ui |
= 8,5 4- 11,0 |
м/мин, |
|||||||
v2 = 3,5 -ч- 8,0 м/мин, |
vs = 1,5-4-30 м/мин. |
При волочении прут |
|||||||
ков из сталей марок Р9 и Р18 |
Oi = 4,2 -г- 4,9 |
м/мин. |
= 20 4- |
||||||
При волочении |
стальных труб на |
цепных |
станах |
||||||
-н40 |
м/мин (толщина |
стенки |
трубы |
а |
1,0 4- 1,5), v3 |
= 12 4- |
|||
-ч- 32 |
м/мин (а 45; |
3,5), |
vs = 3 4- 9 м/мин (а =5; 10,0). |
|
|||||
С |
увеличением |
мощности |
станов |
и |
при |
|
соответствующей их |
модернизации скорости волочения могут быть увеличены. По данным заводов ФРГ, волочение круглых, прямоугольных и шестигранных прутков из мягкой стали на комбинированных станах Schumag с относительно небольшими обжатиями производится со скоростями
25 4- 35 м/мин.
Усилие волочения Р (в кг) для установившегося про цесса можно приближенно определять по следующим формулам.
1. При обработке прутков или профилей — по формуле [38]
Р = Р^тсР(\ + A7-ctga')ln-^,
где Fo и Fi — площади поперечного сечения обрабатываемого прут ка или профиля до и после данного прохода обработ
ки |
В ММ2', |
|
предела |
текучести |
металла |
сТср—среднее значение |
|||||
до |
и после |
данного |
прохода |
обработки в |
кг/мм2; |
f — коэффициент трения |
в волоке; |
|
|||
a — некоторый |
условно |
приведенный угол; |
|
А— численный коэффициент, представляющий собой отно шение периметра сечения протянутого фасонного профиля к длине окружности равновеликого круга. (При волочении круглых прутков А — 1.)
5 Ю. Г. Шнейдер 648 |
65 |
Величина ctg а' определяется |
по формуле |
|
|
|
|||||
|
|
|
|
|
2/рб |
|
|
|
|
|
|
|
|
ctga' = do — di ’ |
|
|
|
||
где |
10б — общая длина очага деформации в мм; |
|
равновели |
||||||
di, |
dQ |
— диаметры действительного или приведенного |
|||||||
|
|
кого |
круга |
сечения обрабатываемого прутка до и после |
|||||
При |
обработки волочением в мм. |
|
|
волоки |
на |
||||
волочении стальных изделий через стальные |
|||||||||
неактивированной смазке коэффициент трения f можно |
принимать |
||||||||
в пределах примерно от 0,12 до |
0,15, |
а через волоки из твердых |
|||||||
сплавов |
на активированной смазке — в |
пределах примерно от |
0,08 |
||||||
до 0,10. |
При расчетах по данной формуле величина |
Р может полу |
|||||||
чаться |
на 12 н- 15% |
больше ее |
действительного |
значения |
при |
||||
установившемся |
процессе. |
формуле |
|
|
|
||||
2. При обработке |
труб — по |
|
|
|
|||||
|
|
|
|
Р = В<зт C0-kFK%, |
|
|
|
||
|
|
|
|
J |
Су |
/V ’ |
|
|
|
де В — численный коэффициент, принимаемый для волочения тол
|
стостенных |
труб без оправки при s> 0,1 |
г равным 1,2; |
|||||||
|
для волочения тонкостенных труб при |
s<0,lr — рав |
||||||||
|
ным 1,1 |
и |
для волочения на короткой оправке — равным |
|||||||
|
1,05; |
стенки трубы; |
|
|
|
|
|
|||
$ — толщина |
|
|
|
|
|
|||||
г — средний |
радиус трубы до волочения; |
|
|
|
||||||
3 — относительное обжатие |
трубы; |
|
|
|
||||||
FK — площадь поперечного сечения трубы (кольцо) после воло |
||||||||||
|
чения; |
|
коэффициент, |
определяемый |
по |
|
формулам: |
|||
k — численный |
|
|||||||||
для |
волочения |
без |
оправки |
A |
1 |
f |
|
|
|
|
+ |
|
|
|
|||||||
для |
волочения |
на |
оправке k |
1 |
Л / |
г |
\ |
• |
||
Н—р (1 + |
|
|
||||||||
Здесь — угол |
наклона образующей деформирующего конуса |
волока в радианах, а г0 и гк — средние радиусы трубы до и после волочения.
При расчетах по данной формуле величина Р может получиться
сотклонениями в пределах примерно +10%.
Вначале процесса волочения при втягивании в волок части заготовки, следующей непосредственно за хвостовиком, может наблюдаться кратковременное увеличение усилия волочения при
мерно на 20 -г- 45%. Это увеличение тем больше, чем выше скорость волочения и чем больше металла одновременно начинает пластически
деформироваться.
Формы и размеры сечений заготовок следует выбирать такими, чтобы весь контур по всему его сечению полу
чался обжатым.
Если при волочении заготовки калибруют только за один проход
то их сечение можно выбирать таким, чтобы общее относительное
66
обжатие составляло не менее 6 -н 9%, а обжатие на сторону по всему периметру — примерно от 2 до 4% от величины основного размера сечения.
При выборе формы и размеров сечения заготовки для фасонного
профиля необходимо учесть следующее:
1)усилия деформирования металла в волоке должны взаимно уравновешиваться как по горизонтальной, так и по вертикальной
осям сечения обжимаемого профиля, иначе заготовка в волоке будет
смещаться и заданные формы сечения не получатся. Следует отметить,
что при соблюдении условия равновесия на предварительных пере ходах заготовку можно обжимать и не по всему контуру ее сечения;
2)деформирование в волоке всех обжимаемых элементов контура сечения заготовки должно начинаться одновременно, в противном
случае возможны утяжки металла;
3)при завершающем (калибрующем) пропуске для лучшего заполнения граней заготовку следует обжимать по всему контуру
еесечения; обжатие со всех сторон должно быть примерно одинако вым;
4)при термообработке металл может «обгорать», а при травле нии — разъедаться травильным раствором, поэтому следует преду смотреть соответственное увеличение размеров сечений заготовок.
Количество пропусков, необходимое для изготовления волоче нием фасонных профилей, устанавливается в зависимости от величины полного обжатия и максимально допустимых величин частных обжатий отдельных проходов. Для фасонных профилей относительное обжатие за один проход берут в пределах до 22 ч- 25%, а обжатие на сторону — не менее 2 -н 4% и не более 12 -н 14% от величин
сечения. В отдельных случаях указанные наибольшие значения могут быть увеличены. В целях сокращения количества пропусков
обработки, если возможно, всегда следует назначать наибольшие единичные обжатия. Для каждого пропуска обработки по приведен ным формулам определяется усилие волочения и проверяется запас
прочности хвостовика.
и |
Намеченный маршрут волочения (попереходное изменение формы |
размеров сечения полуфабриката) проверяется практически |
|
и |
в него вносятся соответствующие коррективы. Отдельные примеры |
маршрутов изготовления стальных профилей волочением, освоенные в производственных условиях, показаны на фиг. 21.
Круглые трубы и заготовки, из которых волочением за один пропуск без оправки изготовляют трубы фасонных сечений, под бираются таким образом, чтобы их внешний периметр был больше
периметра изготовляемой трубы примерно на 12 -н 15%. Правиль ность выбора заготовки обязательно проверяют экспериментом.
Смазка при волочении оказывает заметное влияние на усилие, качество поверхности и стойкость инструмента. Наилуч шие результаты в этом отношении дают активированные смазки, к которым относятся смазки из минеральных масел с добавлением мылонафта (до 5%) или присадки КС (до 25%), а также смазки на
торфяном сале (50% торфяного сала и 50% машинного масла).
5» |
67 |
Смазка на торфяном сале употребляется в виде пасты или наносится в жидком виде после нагрева до 65 ч- 70°. Использование таких смазок вместо обычно применяемых смесей машинного масла, мазута и солидола уменьшает усилие волочения примерно на 30%, при увеличении стойкости волоков в 1,5 -н 2 раза [37].
7. Ротационное обжатие цилиндрических и профильных деталей
Процесс ротационного обжатия (редуцирования) — способ обра
ботки металлов давлением — сводится к периодическому обжатию
и вытягиванию продольно движущейся прутковой заготовки ударами
матриц, |
совершающих как возвратно-поступательное, |
так и враща |
|||||||||
|
|
|
|
тельное движение вокруг продоль |
|||||||
|
|
|
|
ной оси заготовки. Заготовка |
|||||||
|
|
|
|
может совершать также враща |
|||||||
|
|
|
|
тельное |
движение |
относительно |
|||||
|
|
|
|
матриц. При ротационном обжатии |
|||||||
|
|
|
|
имеют |
место деформации сжатия |
||||||
|
|
|
|
и |
растяжения |
и создаются |
наи |
||||
|
|
|
|
более благоприятные условия для |
|||||||
|
|
|
|
формообразования: |
затрудняются |
||||||
|
|
|
|
межкристаллические сдвиги, при |
|||||||
|
|
|
|
водящие |
к нарушению механиче |
||||||
|
|
|
|
ских связей, и пластическая де |
|||||||
|
|
|
Р |
формация происходит в |
основном |
||||||
Фиг. 30. |
|
Схема |
деформации металла |
за |
счет |
внутрикристаллических |
|||||
заготовки |
при |
ротационном обжатии: |
сдвигов. |
|
|
|
|
|
|||
1 — матрицы; 2 — заготовка; / — / — кри |
|
Как |
и |
при |
других видах |
хо |
|||||
тическое |
сечение; |
А и В — направление |
лодной |
обработки давлением, |
при |
||||||
течения |
металла; |
5 — направление по |
|||||||||
дачи; |
Р — усилие деформирования. |
ротационном |
обжатии |
исходный |
|||||||
|
|
|
|
объем металла |
остается |
постоян |
ным и значительно повышаются прочностные характеристики металла. Схема деформации матрицами металла заготовки показана на фиг. 30 [16 ].
Заготовка круглого сечения подается в заборный конус матриц, которые под действием внешних сжимающих сил, оказывая давление на заготовку, деформируют ее. При этом уменьшается поперечное
сечение заготовки, металл которой перемещается в обе |
стороны |
от места контакта с матрицами. |
принятый |
Принцип действия ротационно-обжимных станков, |
как у нас, так и за рубежом, поясняется фиг. 31 и 32.1 Шпиндель 3 обжимной головки, вращающейся со скоростью около 500 об/мин.,
имеет диаметральный паз прямоугольного сечения, по которому к центру и от центра свободно перемещаются бойки с матрицами 5. На внешних торцах бойков установлены опорные ролики 1. Шпин дель 3 расположен внутри обоймы-сепаратора 4, в отверстиях кото
рого по окружности свободно сидят ролики 2 таким образом, что их боковые поверхности частично выступают из обоймы.
1 Цифровые обозначения одноименных деталей на фиг. 31 и 32 одинаковы.
68