
книги из ГПНТБ / Шнейдер, Юрий Григорьевич. Холодная бесштамповая обработка точных деталей давлением
.pdfФиг. 31. Схема работы ротационно-обжимного станка
Фиг. 33. Типовые детали, обрабатываемые ротационным обжатием.
69
При вращении шпинделя с бойками и матрицами последние под действием центробежной силы отходят от центра к периферии в тот момент, когда ролики 1 находятся в пространстве между роли ками 2 (фиг. 31, а), и сходятся к центру, когда ролики 1 натал киваются на ролики 2 (фиг. 31, б). При этом матрицы своими рабочими
поверхностями приходят в соприкосновение с металлом заготовки 6,
пластически деформируя его; заготовка обжимается и вытягивается. Таким образом, во время работы ротационно-обжимного станка матрицы, сходясь и расходясь от центра, производят периодические обжатия заготовки, теоретическое число которых в минуту может
быть определено по формуле
|
N = n-k, |
где N — число |
обжатий (ударов) в минуту; |
п — число |
оборотов матриц в минуту; |
k — число |
роликов в обойме. |
На фиг. 33 показаны некоторые типовые детали, обрабатываемые ротационным обжатием.
Способ ротационного обжатия наиболее производителен и при менение его особенно экономически целесообразно при изготовлении цилиндрических деталей небольшого диаметра (от 1 до 15 мм) и большой длины, обработка которых обычными способами затруд нительна.
Основными преимуществами этого метода по сравнению с обра
боткой точением в условиях крупносерийного и массового произ водства являются:
1) |
увеличение производительности в 5 н- 6 раз; |
||
2) |
значительная экономия металла; |
||
3) |
высокая |
точность |
(3 -н 2-й классы); |
4) |
высокая |
чистота |
поверхности (8 -ь 10-й классы); |
5) повышение механических свойств поверхностного слоя обра батываемого металла за счет холодного наклепа и создания напря
жений сжатия.
Достоинства метода ротационного обжатия наглядно иллюстри
руются двумя приводимыми ниже примерами его применения в при боре- и машиностроении, с описанием конструкции применяемых
ротационно-обжимных станков.
На фиг. 34 показана кинематическая схема ротационно-обжимного автомата для изготовления конических штифтов (конусность 1 : 50)
малого диаметра [17].
От электродвигателя 1 посредством ремня 2 вращение передается шпинделю 3 обжимной головки, а от шпинделя через ременную передачу 4, карданный валик 5, коническую пару 6, сменные зубча
тые |
колеса 15 и 14 и червячную пару 9 — на распределительный |
вал |
8. |
На распределительном валу установлены кулачок 13, осуще ствляющий подачу задней бабки станка с прутком и отвод ее, кула чок 12, подающий пруток, и кулачок 7, подающий дисковый резец для отрезки готового штифта,
70
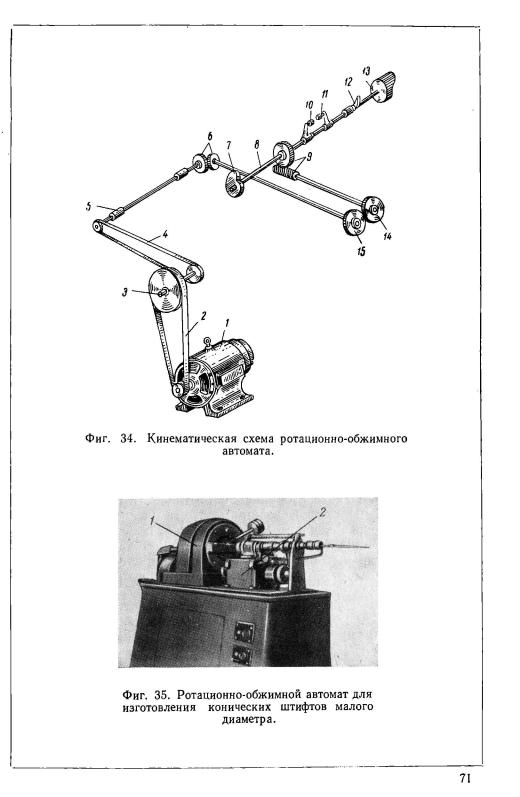
Автомат состоит из двух основных узлов: передней бабки 1
(фиг. 35) с обжимной головкой и задней бабки 2 с механизмами зажима и подачи прутка. Конструкция передней бабки в радиальном сечении (по обойме) показана на фиг. 36, конструкция задней бабки — на фиг. 37.
Работа матриц, расположенных в передней бабке автомата, описана выше. Зажим и подача заготовки производятся следующим образом. В тот момент, когда закончена обработка очередного штифта и обжимные матрицы находятся в разжатом состоянии, кулачок 12 (фиг. 34) посредством рычага 1 (фиг. 37) и толкателя 2 перемещает
подающую |
цангу 3 вместе с |
прутком-заготовкой |
в направлении |
к передней |
бабке. |
зажимную цангу 10. |
Далее срабаты |
При этом пруток входит в |
вает кулачок 10 (фиг. 34), приводящий в действие механизм зажима
прутка. Зубчатое колесо 8, поворачиваясь на определенный угол,
выступами, расположенными на его ступице, приподнимает концы рычагов 5. Рычаги повертываются на своих осях, укрепленных в муфте 4, и через втулку 6 подают вперед гильзу 9. Гильза своей внутренней конусной поверхностью находит на наружную конусную часть цанги 10, которая зажимает пруток, упираясь торцом в кула чок 11. Во время перемещения вперед гильзы 9 между дном гильзы и задним торцом цанги сжимается цилиндрическая спиральная пружина 7.
При отжиме прутка описанный выше механизм срабатывает в обратной последовательности под действием кулачка 11 (фиг. 34).
Когда рычаги 5 освобождают гильзу 9, она под действием пружины 7
возвращается в исходное положение.
Полный цикл работы автомата таков. После зажима прутка кулачок 13 (фиг. 34) ускоренно подводит заднюю бабку к обжимной головке, после чего производит замедленную рабочую подачу прутка.
По окончании обжатия готовый штифт отрезается от прутка дисковым резцом, движением которого управляет кулачок 7 (фиг. 34). После отрезки задняя бабка под действием груза ускоренно отводится
в исходное положение, цанга 10 разжимается, производится подача прутка, и весь цикл работы автомата повторяется.
Точность и производительность ротационно-обжимных станков
во многом зависят от конструкции, точности изготовления и стой кости матриц.
Конструкция сменной матрицы для обработки конического штифта диаметром 1 мм видна из фиг. 38 (слева пунктирной линией
показана вторая матрица, скомплектованная с первой). Рабочие
размеры матриц для обработки штифтов диаметром 1; 1,5; 2 и 3 мм приведены в таблице на фиг. 38.
В момент максимального сближения матрицы образуют полость,
по форме и размерам соответствующую обрабатываемой детали, а на входном торце — коническую поверхность с углом конусности,
равным в данном случае 8°.
При обжатии цилиндрических деталей угол конуса у матриц для облегчения деформации металла и создания плавного перехода
72
Фиг. 37. Задняя бабка ротационно-обжимного автомата.
d+1
Диаметр |
d |
1 |
R |
штифтамм |
|||
1 |
0,9 |
21 |
0,3 |
1,5 |
|
16 |
0,9 |
2 |
1,9 |
19 |
0,9 |
3 |
2,9 |
6 |
0,5 |
Фиг. 38. Матрица для обработки обжатием конического штифта.
74
от недеформированной части прутковой заготовки к утоненной обжатием части обычно принимается равным 11 -т-20°.
Степень обжатия цилиндрической заготовки определяется из
отношения
d— dr d ’
где d — диаметр заготовки;
di — диаметр цилиндрической части полости матриц в замкнутом положении (диаметр утоненной обжатием части заготовки).
Стойкость матриц зависит от их материала и технологии изго товления.
Испытания матриц на стойкость [9] показали, что их следует изготовлять из хромистой стали ЭХ 12 или инструментальной угле родистой У10А, как обеспечивающих наиболее высокую стойкость, хорошую обрабатываемость и низкую стоимость.
Режим работы ротационно-обжимного станка определяет произ водительность процесса; составляющими режима являются: подача
прутковой заготовки s и число оборотов шпинделя п.
Расчет величины подачи и числа оборотов шпинделя может быть произведен по следующим формулам [16].
Подача Si за время одного обжатия матрицами заготовки в мм
составляет
0.074d, S1 — (d — dx) d ’
где d и di — диаметры заготовки (соответственно) до и после
вытяжки в мм\ 0,074 — экспериментально полученный коэффициент для обжа
тия стали У10А (а8 = 65 -г- 75 кг/мм2), диаметром от 1 до 15 мм.
Подача s2 за один оборот шпинделя s2 = f-k-s,
где f — коэффициент, учитывающий относительное движение обоймы; k — число роликов в обойме.
Подача в мм/сек.
где п — число оборотов шпинделя.
Число оборотов шгГинделя определяется по формуле
240 • dj • г? • tg
r.D (d2 — df) (sin 2-jj + sin 2~[2)
где v — допускаемая средняя скорость перемещения частиц металла;
— угол конуса матриц;
D — диаметр окружности точек соприкосновения роликов
и бойков В ММ',
75
71 |
— начальное |
значение угла, определяемого в зависимости |
|
от подачи, |
радиуса ролика и расстояния между центром |
|
вращения |
шпинделя и ролика; |
Т2 |
— конечное |
значение угла, соответствующее окончанию |
|
процесса |
редуцирования. |
Допускаемая средняя скорость перемещения частиц металла при
процессе обжатия может быть определена по формуле
к (d? — ) |
-------A5------ м/мин, |
V = ----- --------------- - |
|
4 sin |
а2 +4—в |
|
где А — коэффициент скорости течения металла в мм!мин-, В — коэффициент, зависящий от степени обжатия, определяемый
экспериментальным путем в зависимости от материала и размера заготовки.
Так, для стали У10А диаметром от 1 до 15 мм при внутреннем диаметре обоймы редуцирного станка, равном 121 мм, А = 120 мм/мин и В = 3,5, а при диаметре обоймы, равном 243 мм, А = 154 мм/мин,
В = 3,5.
На ротационно-обжимном автомате для обработки конических штифтов, конструкция которого описана выше, шпиндель имеет две скорости, соответствующие числам оборотов 500 и 600 в мин.; число подач — шесть. Изменение величины подачи осуществляется посредством сменных зубчатых колес (фиг. 34).
Данные о производительности автомата при различных режимах
его работы приведены в |
табл. 8. |
|
Таблица 8 |
|
|
|
|
|
|
Производительность |
ротационно-обжимного |
автомата |
||
Число зубьев сменных |
|
Количество обрабатываемых штифтов |
||
|
в минуту при числе оборотов шпинделя |
|||
зубчатых колес |
|
|
в |
минуту |
по фиг. 34, колесо 15 по фиг. |
34, |
колесо 14 |
500 |
600 |
26 |
54 |
|
5 |
6 |
36 |
44 |
|
8 |
10 |
40 |
40 |
|
10 |
12 |
44 |
36 |
|
12 |
15 |
Таким образом, даже при среднем режиме, когда в минуту обра
батывается шесть штифтов, производительность ротационно-обжим
ного автомата превышает |
производительность токарного |
автомата |
в 3 -г- 3,5 раза; при этом |
обеспечивается 3 -г- 2-й класс |
точности, |
9 -т- 10-й класс чистоты поверхности, и удовлетворяется требование прямолинейности образующей.
С увеличением длины обрабатываемых деталей (длина конических штифтов, изготовляемых на автомате, не превышает 30 мм),
76
производительность редуцирования по сравнению с обработкой на токарных станках и автоматах еще возрастает.
Например, при обжатии заготовки из стали У10А диаметром d =
= 7,8 мм и длиной I = 175 мм до диаметра dY = 6,3 мм степень обжатия составляла
k = (rf-^.lOQQ/o |
(7,8-6,3)-100% |
19 230/о |
Удлинение заготовки составляло 105 мм (60%). Режим работы редуцирного станка характеризовался числом оборотов шпинделя п = 420 об/мин. и подачей на одно обжатие sx — 0,042 мм; время редуцирования t = 52 сек.
На предварительную и чистовую обработку подобной детали на токарном станке при средних режимах, применяемых на приборо строительных заводах, затрачивается около 5 мин. Если учесть при этом дополнительные затраты времени, связанные с использова
нием люнета для деталей с большим отношением , производи
тельность ротационного обжатия будет в 6 -н 7 раз выше производи тельности обработки точением.
Детали, более сложные по конфигурации, чем штифты, шпильки,
оси и многоступенчатые валики, на станках описанного типа обра батываются за несколько переходов, что оказывается менее произ водительным и н всегда экономически целесообразным. При обра ботке на таких станках деталей, ограниченных коническими поверх
ностями значительной длины, приходится увеличивать габариты обжимной головки, так как длина рабочего конуса матриц, офор мляющего коническую поверхность, должна быть такой же, как длина конуса, образуемого на заготовке. Для обработки конусов большой длины и сложных профильных поверхностей применяется другая схема и, соответственно, другие станки для ротационного обжатия. Если для описанных станков характерно постоянное положение матриц относительно оси заготовки в конце каждого обжатия, то при так называемом профильном ротационном обжатии матрицы 1 (фиг. 39) меняют свое положение вдоль оси заготовки 5
под действием копирного кольца 4, внутренняя поверхность которого
имеет профиль, соответствующий форме обжимаемой детали; так,
при обработке конических деталей эта поверхность коническая; ролики 3 выполнены также конусными и с одной стороны соприка
саются с бойками 2, а с другой — с внутренней рабочей поверхно стью копирного кольца 4, как показано на схеме фиг. 39.1 Благодаря
кинематической связи между перемещением копирного кольца
(ходом матриц в радиальном направлении) и подачей заготовки обеспечивается постепенное изменение величины обжатия заготовки
при образовании сложных профилей. Как профильные детали, так
идлинные конические поверхности обжимаются матрицами, имею
1Способ профильного ротационного обжатия длинных конических поверх ностей разработан В. И. Любвиным и С. И. Ермишиным.
77
щими относительно небольшую длину рабочего желобка. Примером эффективного применения профильного ротационного обжатия может служить обработка шпинделя прядильного веретена (фиг. 40) на специальном ротационно-обжимном станке РК-1 [18].
На обычных станках для ротационного обжатия эту деталь получают за три операции тремя комплектами матриц. Полное
Фиг. 39. Схема механизма профильного ротационного обжатия.
время обработки составляет 40 сек., и даже при такой технологии
производительность редуцирования давлением в два |
раза |
выше, |
|
чем производительность токарной |
обработки. Полное |
время |
обра |
ботки шпинделя на станке РК-1 |
составляет около 18 |
сек. |
|
133,5 -------- - |
—4------------------ |
гог, 5 |
---------------------------- |
|
337,3-д^------------ |
Фиг. 40. Шпиндель веретена.
Исходной заготовкой является пруток длиной 2,5 м и диаметром 10 н- 10,5 мм, из которого получается 10 -г- 12 шпинделей. Станок работает по автоматическому циклу и состоит из следующих основных
узлов (фиг. 41): рабочей головки А, люнета Б, профилирующего
механизма В, механизма перемещения барабана Г, каретки Д,
направляющих каретки и механизма подачи.
В передней части рабочей головки, выполненной за одно целое со станиной 2, расположено копирное кольцо 3, перемещающееся в обе стороны в осевом направлении. Внутренняя поверхность кольца конусная (угол конуса 8°).
78