
книги из ГПНТБ / Ряполов А.Ф. Изготовление и монтаж технологических трубопроводов высокого давления
.pdfотличаются от распространенных конструкций для тру бопроводов обычных давлений. Обязательным в указа телях уровня высокого давления является наличие двух запорных органов, из которых один должен быть быстрозапориым, позволяющим быстро отключать указатели при авариях.
На рис. 39 изображен указатель уровня жидкости,
рассчитанный на высокое давление. |
|
|
|
|
|
|
||||
|
|
Специальная |
|
арматура. |
К спе |
|||||
|
|
циальной |
|
арматуре |
могут |
быть |
||||
|
|
отнесены |
угловые |
запорные |
вен |
|||||
|
|
тили со специальным |
обратным |
|||||||
|
|
клапаном |
для |
манометров, |
пред |
|||||
|
|
назначенные |
к использованию в |
|||||||
|
|
качестве |
запорного |
и предохра |
||||||
|
|
нительных органов при установке |
||||||||
|
|
манометра |
на трубопроводах |
или |
||||||
|
|
аппаратах |
высокого давления. |
|||||||
|
ие? |
Приспособление |
типа |
обрат |
||||||
|
ного клапана в этом узле служит |
|||||||||
|
а д а |
для предохранения |
манометра от |
|||||||
|
|
повреждений |
при |
резком |
увели |
|||||
Рис. 40. Защитный кла |
чении скорости |
движения |
среды |
|||||||
пан |
манометра |
в трубопроводе |
и для |
мгновенно |
||||||
/ — к о р п у с ; |
2 — ф л а н е ц ; |
го перекрытия |
|
ее |
подвода |
к |
ма |
|||
3 — к л а п а н ; |
4 — п р у ж и н а ; |
нометру в случае его разрыва. |
||||||||
5 — |
с п е ц л и н з а |
|||||||||
|
|
Конструкция обратного защитно |
||||||||
|
|
го клапана |
для |
манометра |
пока |
|||||
зана на |
рис. 4U. На установках |
высокого |
давления |
для |
||||||
клапанов и седел арматуры приняты |
|
стали |
следующих |
марок: 2X13, 3X13 и 4X14IT14B2M (с азотированием). Не исключено также применение и других марок сталей, которые по своим свойствам соответствуют рабочим ус ловиям.
Клапаны и седла для дроссельной и регулирующей
арматуры изготовляют обычно из твердых |
сплавов ВК6 |
|
и ВК8 или из износостойкой керамики. |
|
|
Для давлений от 320 |
кгс/см2 и выше |
и температур |
более 200° С применяют |
специальные набивки, выбирае |
мые по ГОСТ 5152—66.
Для сальников арматуры, работающей при высоких температурах и давлениях, рекомендуется применение следующих набивок:
а) асбестовый шнур прорезиненный, вулканизирован
70
иый, снаружи графитизированный и пропитанный спе циальным составом марки НВДТ-1, поставляемый по МВТУ МХП №ШАУ 40-54 для давления до 320 кгс/см2 и температур до 200° С;
б) асбестовый шнур с латунной проволокой, проре зиненный, вулканизированный, снаружи графитизиро ванный и пропитанный составом марки НВДТ-2 для
давлений |
до |
600 кгс/см2 |
и температур до |
200° С |
(по тем |
|||
же ТУ); |
|
|
|
|
|
|
|
|
в) асбестовый шнур с латунной проволокой, проре |
||||||||
зиненный, |
вулканизированный, |
снаружи |
графитизиро |
|||||
ванный для |
давлений |
до |
650 |
кгс/см2 |
и |
температуры |
||
350—370° С; |
|
|
|
|
|
|
|
|
г) прорезиненная асбометаллическая |
набивка |
(с ме |
||||||
таллическим |
сердечником) |
марки АПГС |
производства |
Ленинградского завода асботехнических изделий для давлений до 320 кгс/см2 и температур до 400° С.
6. Приемка, складирование и хранение труб, готовых деталей и арматуры на складе до монтажа
Контроль и приемка труб до их обработки. Помимо контроля на заводе-изготовителе в соответствии с тех ническими условиями все трубы, поступившие на пло щадку, подлежат проверке перед выдачей их для изго товления деталей и трубопроводов.
Проверку осуществляет специальная комиссия, соз даваемая дирекцией строящегося предприятия.
Вначале проверяют полноту технической документа ции и соответствие ее требованиям технических условий на изготовление труб; определяют твердость металла на обоих концах труб с внесением результатов, полученных по каждой трубе, в журнал. Величина твердости явля ется косвенным показателем прочности металла труб и равномерности термообработки ее по длине.
Кроме того, согласно требованиям технических усло вий на устройство трубопроводов высокого давления, трубы подвергают следующим повторным испытаниям: проверке химического состава и механических свойств металла труб, технологическим пробам и металлографи ческим исследованиям.
Контроль химического состава труб и деталей. Пер вым и наиболее ответственным испытанием является контроль химического состава труб и деталей, так как случайная или ошибочная замена легированных труб
71
углеродистыми может повлечь за собой серьезную ава рию.
Перепутыванпе труб различных марок стали может произойти в разных местах. Во-первых, уже на метал лургических заводах при изготовлении труб в данную партию трубных заготовок могут случайно попасть заго товки других марок стали. Еще большая опасность воз никает при наличии в производстве труб одинакового диаметра, но разных марок сталей. И наконец, это мо жет случиться при монтаже при отсутствии надлежаще го контроля.
Учитывая наличие значительного количества труб, используемых для установок высокого давления, этот контроль осуществляется наиболее простыми способами, например «капельной пробой», дающей возможность ка чественного определения легирующих элементов без от бора стружки.
Необходимые для контроля растворы, рекомендуе мые Днепропетровским трубопрокатным заводом имени
В. И. Ленина, приводятся |
ниже: |
|
|
№ 1—азотная кислота |
(плотностью) . |
1,12 г/см3 |
|
№ 2 — родоннстып |
калии (KCNS) . . |
5%-нын |
|
№ 3 — двухлористое |
олово |
35%-ный |
Поверхность металла предварительно очищается на пильником, а затем наждачной бумагой. На очищенную поверхность металла пипеткой или стеклянной палочкой наносят каплю раствора № 1. Через 1—2 мин после пре кращения выделения пузырьков газа при растворении металла азотной кислотой прикасаются к капле на по верхности металла фильтровальной бумагой (мокрым пятном), на которую предварительно нанесены капля раствора №2—родоннстого калия. На этом месте бума ги образуется пятно темно-красного цвета. Вслед за этим на образовавшееся пятно наносят 1—2 капли раствора № 3 — двухлористого олова. Если труба угле родистая, то бумага полностью обесцвечивается. При на личии молибдена остается легкое розовое окрашивание. Такой метод может широко применяться на монтажных площадках.
Методом «капельной пробы» производят качествен ный анализ стали на наличие молибдена и хрома. Для этого на трубе (детали) зашлифовывают до металличе ского блеска площадку около 2 см2, после чего на нее
72
наносят пипеткой каплю реактива и наблюдают проис ходящую реакцию окрашивания капли. После высыха ния капли следы реакции (окрашивания) сохраняются.
Для проведения качественного анализа молибдена приготовляют реактив следующего состава: 2 объемные
части H N O 3 |
плотностью 1,4 |
г/мм3; 9 объемных |
частей |
|
НС1 плотностью 1,19 г/мм3; |
15 объемных частей |
дистил |
||
лированной |
воды. |
|
|
|
При содержании в стали молибдена менее 0,2% кап |
||||
ля остается светлой и прозрачной, при наличии |
свыше |
|||
0,2% Мо через 3—4 мин после нанесения раствора |
кап |
|||
ля принимает светло-желтую окраску. |
|
|
||
Присутствие меди и ванадия не нарушает хода |
реак |
|||
ции, но хрома при этом должно быть не более 3%. |
|
Для определения хрома (в низколегированных ста лях) применяют реактив следующего состава: 30 объем ных частей HNO3 плотностью 1,4 г/мм3; 30 объемных частей H2SO4 плотностью 1,84 г/мм3; 40 объемных ча стей дистиллированной воды.
Через несколько минут после нанесения раствора на испытуемой поверхности появляется пена или солевой налет, имеющий окраску:
а) при отсутствии хрома — от желто-коричневой до коричневой;
б) при содержании хрома свыше 0,6% —от светлой серо-зеленой до темно-серой, в зависимости от содержа ния хрома;
в) при содержании хрома свыше 8% — капля оста ется прозрачной.
Присутствие молибдена и меди в обычных количест вах не мешает ходу реакции. Но определение становит ся невозможным при содержании в стали Ni свыше0,2%.
Одним из методов контроля химического состава ме талла является также спектральный анализ (переносны ми стилоскопами типа СЛП-1 или СЛП-2)*.
Спектральный анализ осуществляют путем рассмот рения через окуляр стилоскопа спектра свечения паров металла, возникающего при создании электрической ду ги (или искры) между электродом прибора и испыты ваемым металлом, и сравнения его с контрольной таб лицей.
* Новосибирского приборостроительного завода имени В. И. Ле нина.
73
В настоящее время разработаны шкалы для всех ос новных элементов, дающие возможность не только ка чественного, но и количественного их определения.
Перед спектральным анализом на исследуемой дета ли зачищают шлифовальным кругом или напильником площадку величиной около 2 см2. Продолжительность анализа для определения содержания в металле пятишести элементов составляет в среднем 5 мин.
Механические испытания. Контрольные испытания ме ханических свойств обязательны для каждой партии труб и деталей, поступающих на площадку. Неудовлетвори тельные результаты контрольных испытаний механичес ких свойств служат основанием для предъявления рекла мации заводам-изготовителям, в этом случае трубы не могут быть допущены в производство.
Для проведения испытаний от каждой партии отбира ют две трубы с максимальной и минимальной твердостью, от которых отрезают образцы для контрольных испыта ний их механических и технологических свойств и прово дят одновременно металлографические исследования ме талла труб.
От каждой трубы отрезают и обрабатывают образцы
в количестве |
9 шт.: 2 — для испытания |
на растяжение, |
|
2 — н а ударную вязкость, 1 — для исследования |
макро |
||
структуры, 2 |
— то же, микроструктуры, |
1 — для |
испыта |
ния на сплющивание и 1 — на изгиб. Для металлографи ческих исследований допускается использование разру шенных образцов после определения ударной вязкости.
Партия труб считается годной, если результаты испы таний всех образцов оказались удовлетворительными и соответствуют данным сертификатов.
При неудовлетворительных результатах испытания хотя бы одного образца партию труб подвергают повтор ному испытанию при удвоенном количестве образцов. Образцы в этом случае берут лишь для тех видов испы таний, по которым получены неудовлетворительные ре зультаты. При неудовлетворительных результатах пов торных испытаний всю партию труб бракуют или подвер гают 100%-ной проверке.
Технологические пробы. В технических условиях пре дусматриваются выполнение технологических проб мате риала труб на сплющивание и холодный загиб. Эти ис пытания играют существенную роль, так как характери зуют пластические свойства труб в состоянии поставки,
74
что особенно важно при выполнении такой распростра ненной операции при изготовлении трубопроводов, как гибка труб.
Подобными испытаниями проб могут быть обнаруже ны и грубые дефекты металла труб — расслоения, плены, трещины и др.
Испытания проб на сплющивание производят на коль цах, отрезанных от труб (ГОСТ 8695—58). Кромки проб ных колец закругляют напильником. При испытании на сплющивание в качестве показателя берут предельную ве личину просвета между внутренней поверхностью трубы. Испытанию на сплющивание подлежат лишь трубы с на ружным диаметром более 35 мм.
Кольца из труб углеродистой стали (марка 20) сплю щивают до получения просвета, равного 50% внутреннего номинального диаметра. Кольца из труб легированных сталей сплющивают до появления первой трещины. Ре зультаты испытаний на сплющивание в этом случае яв ляются факультативными.
Кольца для испытаний на сплющивание можно не от делять от труб, а надрезать и сплющивать на самой трубе.
Металлографические исследования. Для металлов из делий, предназначенных для работы при высоких темпе ратурах, контроль микроструктуры практически является наиболее доступным и эффективным для определения пригодности металла для работы при высоких темпера турах.
Микроструктурный анализ позволяет составить наи более полную характеристику металла труб (и сварных соединений) путем определения характера структурных составляющих, однородности структуры по всему сече нию, величины зерна в состоянии поставки, наличия по сторонних включений и микродефектов—пор, трещин и др.
Шлифы должны просматриваться при разных увели чениях. Для наиболее характерных участков следует де лать фотоснимки структуры, которые впоследствии при кладывают к сдаточной документации. Объективным критерием для качественной оценки и установления бра ковочных признаков служит заключение специалистов металлографической лаборатории.
Приемка труб по наружному осмотру. В ТУ на трубы имеется указание, что материал не должен иметь трещин, плен, закатов и других дефектов.
75
Тем не менее, несмотря на наличие заводских серти фикатов, подписанных ОТК завода-изготовителя, в прак тике поставки труб все же указанные дефекты имеются. При допуске партии к монтажу после проверки механиче ских свойств наружному осмотру подвергают все трубы в партии. Все трубы из углеродистой и низколегирован ных сталей, кроме труб с наружным диаметром до 14 лш, перед их осмотром подвергают травлению в течение вре мени, достаточного для удаления окалины, но исключаю щего возможность значительной коррозии металла.
Травление труб осуществляют в 10%-ном растворе сер ной или соляной кислоты с применением ингибитора1 , после чего каждую трубу промывают и тщательно осмат ривают снаружи и внутри.
Если после травления кислотой поверхность трубы по лучается темной или не полностью удалена окалина, вследствие чего затруднителен осмотр поверхности тру бы снаружи, а трубы Dy более 60 мм также и внутри очищают при помощи пескоструйного аппарата. Поверх ность трубы должна быть чистой и гладкой. При наличии на ней трещин, закатов свищей и других дефектов, ого воренных в технических условиях на изготовление, тру бы бракуют. Незначительные риски, волосовины, ракови ны и все подозрительные места обязательно зачищают напильником или абразивным кругом, причем эту опера цию следует выполнять в поперечном направлении (или под некоторым углом), а не в продольном направлении. Толщина стенки в месте выведения поверхностных де фектов не должна выходить за пределы установленных для труб допусков.
При проверке готовых труб на макроструктуру неод нократно было установлено наличие на поверхности во лосовин, располагаемых обычно винтообразно по длине трубы, глубиной, нередко достигающей 0,5—1 мм.
Волосовины следует устранять во всех случаях, даже когда их величина не выходит за пределы допусков на толщину стенки трубы (после выборочной проверки в двух-трех местах).
На рис. 41 приведены два образца труб Dy 40 мм, из которых на одном волосовина была предварительно выведена ручной опиловкой. При сплющивании первого
1 Широкое применение получили присадки КС, ЧМ «Уникод» ма рок МН, МН-2, МН-10 и др.
76
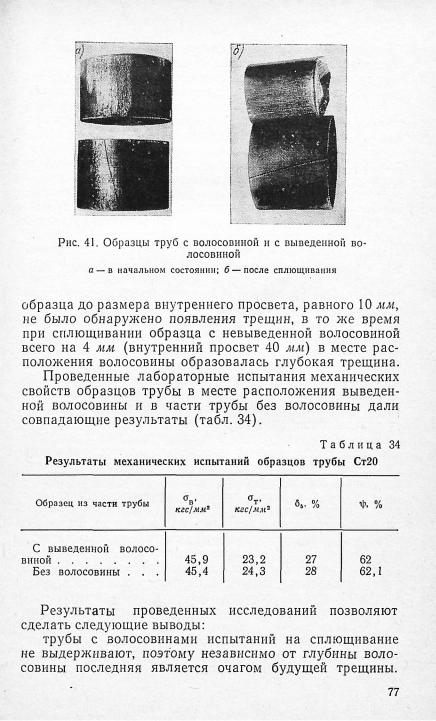
Следовательно, нельзя оставлять волосовины на трубах вне зависимости от их размеров (глубины);
трубы, с поверхности которых волосовины удалены (выведены опиловкой), следует считать равнопрочными с нормальными трубами, не имеющими волосовин, при прочих равных условиях; механические свойства и по ведение их являются вполне удовлетворительными.
По окончании наружного осмотра трубы для нейт рализации остатков кислоты промывают 15%-ным ра
створом |
каустика в течение 10—15 |
мин, а затем горячей |
|
водой и |
протирают чистыми салфетками |
(концами). |
|
Трубы |
из высоколегированных |
сталей |
(X18IT10T, |
Х17Н16МЗТ и др.), как правило, поставляют осветлен ными и протравке на площадке не подвергают.
Результаты наружного осмотра труб внутри и сна ружи являются одним из основных показателей годно сти труб, поэтому осмотр их должен проводиться тща тельно с помощью лупы и электрической лампочки для освещения внутренних полостей труб.
Для осмотра внутренних поверхностей труб эффек тивными являются приборы типа РВП, хорошо выявля ющие наличие трещин, пористости, коррозии и других дефектов. Наибольшее распространение для проверки внутренних поверхностей толстостенных труб получили приборы: РВП-457 — для труб с внутренним диаметром 15—30 мм, и РВП-456 — для труб с внутренним диамет ром свыше 30 до 400 мм.
Для неразрушающего контроля изделий, применяе мых для коммуникаций высокого давления, возможно применять (экспериментально) электромагнитный ин дуктивный дефектоскоп типа ЭМИД-8. При помощи это го прибора возможно выявлять: дефекты, связанные с нарушением сплошности (трещины, закаты, раковины) на толстостенных трубах, поковках и готовых изделиях, производить проверку и сортировку изделий по маркам стали и оценивать качество термической обработки.
Одновременно с проведением наружного осмотра замеряют толщину стенок на торцах трубы и ее наруж ный диаметр, сопоставляя при этом полученные изме рения с допусками, указанными в технических условиях на трубы.
Проверка труб методом магнитной .дефектоскопии.
Дефектоскопия проводится с целью выявления поверх ностных и внутренних подкорковых дефектов в трубах,
78
а нередко и в готовых изделиях (фланцах, тройниках, коленах и др.).
Метод магнитной дефектоскопии, в данном случае метод магнитной суспензии (магнофлокс), основан на выявлении изменений в распределении магнитного по тока, вызываемых дефектами в металле, которые возни кают под ними в процессе или после намагничивания изделий.
В намагниченном изделии магнитные силовые линии, встречая дефект, огибают его как препятствие с малой магнитной проницаемостью и образуют над ним поле рас сеяния. Поле рассеяния над дефектом обладает большой энергией, так как магнитная проницаемость воздуха зна чительно меньше проницаемости ферромагнитного метал ла. Тенденция поля — уменьшить свою энергию до воз можно меньшей величины — удовлетворяется в этом слу чае отложением ферромагнитных частиц по силовым ли ниям поля рассеяния, демаскирует дефект и тем самым дает возможность его обнаруживать.
Для выявления возможных дефектов намагниченная деталь (труба) обливается магнитной суспензией. Сус пензия может быть приготовлена в необходимых количе ствах, например из мелкого порошка закись-окисного же леза ( Р е з 0 4 ) , взятого из соотношения: на каждые 35 г порошка для получения суспензии 1 л трансформаторно го масла.
Продолжительность соприкосновения дефекта изделия с магнитной суспензией определяют опытным путем. Практически обычно достаточно 2—3-минутной выдержки детали под осаждающейся магнитной суспензией.
В связи с тем что размер зерен ферромагнитного по рошка колеблется обычно в пределах от 10- 2 до Ю-6 мм, частицы порошка со столь незначительной массой нахо дятся при соответствующей вязкости среды во взвешен ном состоянии и только под действием магнитного поля рассеяния образуют ясно видимые скопления.
При этом необходимо иметь в виду, что дефект выяв ляется наиболее резко и четко в том случае, если направ ление намагничивающего поля составляет угол с направ
лением наибольшей протяженности |
дефекта, |
близкий |
||
или равный |
90°. |
|
|
|
Следует |
также отметить, что |
с увеличением |
частоты |
|
магнитное поле распространяется |
ближе к поверхности |
|||
магнитопровода (явление магнитного |
скинэффекта), и |
79