
3440
.pdfНаучный Вестник Воронежского государственного архитектурно-строительного университета
1900 кг/м3 и с требуемым набором реально-достижимых параметров прочности – от 0,1 до 600 кгс/см2. Используя процессы механо-химактивации, энергетической «накачки» мелкозернистой гидродинамической системы удается целенаправленно создавать структуры с заданными свойствами как на ранних, так и на всех последующих стадиях формирования искусственного камня.
Универсальность поризованного бетона заключается прежде всего в том, что из него монолитным способом можно исполнить практически все элементы зданий и сооружений, а также изготовить большой перечень строительных изделий и железо-бетонных конструкций (стеновых и фундаментных блоков, колодцевых колец, элементов для забора и др.). К тому же поризованный бетон по набору характеристик охватывает все диапазоны условного деления ячеистых бетонов на теплоизоляционный, конструкционно-теплоизоляционный и конструкционный.
Поризованные бетоны различной рецептуры являются не только универсальным материалом с точки зрения возможностей обходиться на стройплощадке без продукции стройиндустрии, обеспечивающей традиционные технологии строительства. Этот композитный материал легко дополняет и сочетается с любыми другими строительными материалами искусственного и естественного происхождения. Повышенная пластичность, высокая адгезионная и водоудерживающая способность позволяют применять смеси различной плотности для внутренних и внешних штукатурных работ.
Высокопористый бетон с плотностью D=200-400 кг/м3 способен заменить любые эффективные утеплители, тем более на химической, полимерной основе, которые выделяют, как правило, вредные вещества, имеют ограниченный временной ресурс и вызывают целый ряд других негативных проявлений в процессе эксплуатации объектов.
Технологические решения, разработанные на основе строительной системы «Монопор» позволяют приготавливать и использовать требуемые рецептуры смесей в построечных условиях в широком диапазоне природно-климатических условий (-30 ÷ +40 °С, дождь, снег) в режиме естественного набора прочности без использования специальных противоморозных добавок и без принудительного ускорения твердения с использованием тепловых установок. Поризованные бетоны различной плотности демонстрируют такую стабильную способность к самоорганизации на основе процессов гидратации при пониженных и отрицательных температурах, что можно смело утверждать о существовании так называемой криотехнологии бетонов.
Выявление в процессе опытно-экспериментального строительства и теоретических исследований закономерностей поведения поризованных бетонов позволяет разработчикам уверенно предлагать строителям позитивные результаты в виде технических средств, оснастки, измерительных приборов, ориентировочных рецептур и регламентов выполнения общестроительных и отделочных работ.
Варианты монолитного исполнения элементов зданий и сооружений из поризованных бетонов различной плотности и прочности дают возможность реализовать идею минимизации длины технологической цепочки по превращению исходного сырья в готовую строительную продукцию. Эта схема при использовании непосредственно на стройплощадке обеспечивает не только сокращение временного цикла в строительном производстве, но и значительно снижает затраты материальных, энергетических и трудовых ресурсов, минимизирует транспортные издержки и расходы на посредников.
Уникальные технологические особенности приготовления поризованных смесей позволяют значительно понизить уровень требований к исходному сырью в сравнении с обычными бетонными смесями. Это доказано примерами использования цемента, «закаменевшего» в мешках, песка с примесью глинистых до 20 %, воды из любого источника, включая морскую, грунта из смеси песка, гумуса, травы с корнями и др. Это
вовсе не означает, что разработчики технологий рекомендуют |
пользователям |
61 |
|
Научный Вестник Воронежского государственного архитектурно-строительного университета
некачественное исходное сырье, но то, что при определенных обстоятельствах для менее ответственных объектов можно использовать и его, следует считать доказанным.
Перечисленные факты можно рассматривать как демонстрацию технологических и экономических преимуществ предлагаемых инновационных разработок. Качество строительства, оцениваемое по набору основных эксплуатационных параметров, обеспечивается при этом на сравнительно высоком уровне и в меньшей степени зависит от профессиональной подготовки рабочих, чем при использовании традиционных материалов и технологий. Негативное влияние так называемого «человеческого» фактора может быть минимизировано стимулированием таких качеств у рабочих как внимательность, аккуратность, добросовестность. Простота технологических операций, заложенных в регламенты работ на основе строительной системы «Монопор», позволяет добиваться высокого качества и роста производительности труда.
Результаты многолетнего экспериментального строительства позволяют заявить, что при выполнении общестроительных работ (возведение каркаса зданий и сооружений – фундаментов, стен, перекрытий, перегородок и даже монолитной крыши ) в расчете на 1 м2 полезной площади (при средней толщине стен не менее 0,5 м) достигнуты следующие уровни затрат в ресурсном виде:
1.трудовые ресурсы - 3 чел. дня;
2.строительные материалы:
-цемент ПЦ500Д0 - 300 кг;
- песок - 600 кг;
-вода - 300 литров;
-химическая добавка (ПАВ) - 0,6 литра;
-фибра - 0,5 кг;
3.электроэнергия - 3-5 квт/час;
4.амортизация оборудования и оснастки - не менее 300 руб/м2.
Эти результаты обусловливают достаточно низкий уровень себестоимости строительства, который недостижим при использовании традиционных строительных материалов и технологий. Если же учитывать капитальные затраты на оснащение одного рабочего места (для бригады из 3-5 чел.), которое составляет не более 250 тыс. рублей (на 1.01.2010 г.), то экономическая эффективность предлагаемого набора технологий строительства становится еще более очевидной.
Важным показателем ресурсосбережения является факт, что при малоэтажном строительстве (до 5 этажей) не требуется использования крановой техники - достаточно простейших подъемных механизмов.
При качественном исполнении монолитных стен и перекрытий возможно минимизировать объемы и даже полностью исключить такие виды отделочных работ, как оштукатуривание стен и потолков, заливку выравнивающей основы под полы. Для монолитных фундаментов возможно не выполнять наружную гидроизоляцию. При монолитном исполнении крыши чердачного типа или мансардных этажей достигается 100%-ное использование полезной площади при значительном сокращении расхода пиломатериалов и соответствующих видов работ.
Предлагаемые проектно-конструкторские, технические и технологические решения обеспечивают высокие теплозащитные параметры ограждающих элементов зданий и сооружений, требуемые прочностные значения несущих конструкций, необходимый уровень влаго- и морозостойкости. В отношении требуемых параметров пожаробезопасности или огнестойкости несущего каркаса объектов не существует никаких сомнений. Этот материал можно назвать деревянным бетоном или бетонным деревом. Сходство состоит не только в диапазоне плотности, при котором бетонные изделия легче воды и плавают. Этот материал
62
Научный Вестник Воронежского государственного архитектурно-строительного университета
легко пилится, сверлится, рубится топором, обрабатывается с помощью стаместки, в него забивают гвозди, ввинчивают саморезы и др.
Но в отличие от древесины он не гниет, не горит, не набухает при воздействии влаги и даже защищает металлические элементы от коррозии, что очень важно для несущих конструкций и во многом обусловливает надежность и долговечность зданий и сооружений,
Следует особо отметить, что монолитное исполнение всех элементов в сочетании с ячеистой структурой поризованных бетонов дают основания предполагать высокий уровень сейсмостойкости различных объектов строительства.
Если вспомнить о последнем из перечисленных этапов строительного производства – утилизации, то можно предположить, что это не составит особых затруднений. С существующим набором инструмента, способного расчленять металл, арматуру, возможно распилить на элементы каркас любого объекта, построенного из этого мелкозернистого, пористого, однородного, изотропного и экологически чистого материала. При этом полученные элементы как продукт утилизации могут быть пригодны для последующего использования в строительстве.
Важнейшей особенностью поризованных бетонов является то, что процесс гидратации вяжущего в нем идет десятилетиями. Это ведет к реорганизации структуры и к дальнейшему увеличению параметров прочности за счет термодинамического резерва не до конца прогидратировавших зерен цемента.
Перечисленные технологические, эксплуатационные и экономические показатели получены разработчиками инновационных решений на основе многолетнего опытноэкспериментального строительства, что является наилучшим доказательством их достоверности. Многие материаловедческие результаты подтверждены научноисследовательскими работами в различных научных школах страны (не менее 5 докторских и более 20 кандидатских диссертаций по тематике ячеистых бетонов).
Выводы.
К настоящему времени существует определенный набор нормативных документов для использования в проектировании и строительстве некоторых видов ячеистых бетонов. Применительно к поризованным бетонам, как особого вида композиционных материалов на минеральных вяжущих, наработана значительная основа для использования ее в широкой строительной практике с перспективами дальнейшего совершенствования и развития.
Список литературы
1.Сватовская Л.Б. Фундаментальные основы свойств композиций на неорганических вяжущих.– СПб.: Петербургский гос. ун-т путей сообщения, 2006. – 84 с.
2.Борисов Ю.М., Черноусенко Г.И. Эффективные инновационные решения при выполнении общестроительных работ // Строительные материалы, оборудование, технологии XXI века. – 2008. - № 7. – С. 78-79.
3.Моргун Л.В. Композиционные материалы // Строительные материалы: учеб. пособие // под ред. Г.А. Айрапетова и Г.В. Несветаева. - Ростов н/Д: Феникс, 2004. – С. 540562.
4.Славчева Г.С. Поризованный бетон: структура и строительно-технологические свойства: монография. – Воронеж: Воронеж. гос. арх.-строит. ун-т. – Воронеж, 2009. – 136 с.
____________________________________________________________________
Черноусенко Г.И - технолог ООО «Экострой». Тел/факс: (473) 296-94-48, 296-94-49 (многоканальный),
89155889689. E-mail: es-zavod@mail.ru
63

Научный Вестник Воронежского государственного архитектурно-строительного университета
УДК 666.368
А.Е. Турченко, А.А. Суслов
КЕРАМИЧЕСКИЕ ОБЪЕМНООКРАШЕННЫЕ СТЕНОВЫЕ ИЗДЕЛИЯ ИЗ МЕСТНОГО ГЛИНИСТОГО СЫРЬЯ ВОРОНЕЖСКОЙ ОБЛАСТИ
В представленной работе приведены результаты по получению стеновых керамических материалов на основе глин воронежской области. Разработанные составы керамических масс позволят получать керамические изделия с высокими физико-механическими свойствами и различными цветовыми оттенками
Ключевые слова: глины воронежской области, керамический кирпич и камни,пигмент, объемное окрашивание, способ формования, прочность
А.Е. Turchenko, А.А. Suslov
CERAMIC VOLUME COLORING WALL PRODUCTS FROM LOCAL CLAY RAW MATERIALS OF THE VORONEZH REGION
Results on receiving wall ceramic materials are given in the presented work on the basis of clays of the Voronezh region. The developed structures of ceramic masses will allow to receive pottery with high physicomechanical properties and various color shades.
Key words: clays of the Voronezh region, ceramic brick and stones, pigment, volume coloring, way of formation, durability
Введение. Основным требованием современного рынка керамических стеновых изделий является высокое их качество, определяемое как стабильностью прочностных показателей, цветовых оттенков изделий, так и четкостью формы, размеров, отвечающим требованиям современного дизайна [1]. Наличие последнего расширяет круг потребителей и обеспечивает преимущества в повышении цены на выпускаемую продукцию.
Поэтому, сегодня основными задачами для многих предприятий керамической отрасли является - расширение номенклатуры керамических изделий, повышение их качества (особенно лицевых кирпича и камней) при снижении энергетических и материальных затрат на их производство. На ряду с вышеуказанным, актуально использование местного глинистого сырья. Исследованию этой проблемы посвящены труды Ю.И. Гончарова, С.В. Солопова [2] и др.
Они отмечают, что расширение цветовой гаммы керамических изделий (от светложелтого до коричневого и черного) может быть достигнуто введением в состав шихты добавок, представленных светложгущимися каолинитовыми глинами, оксидами железа.
Задачами данной работы являлось:
1.Определение рационального содержания красящих оксидов в шихтовых составах в зависимости от химического и минералогического состава глинистого сырья для получения лицевого кирпича декоративных разновидностей.
2.Оценка влияния красящих оксидов на спекание керамического черепка.
3.Оптимизация шихтовых составов по показателям предела прочности при сжатии обожженных керамических материалов, их водопоглощения и полной объемной усадки.
4.Разработка шихтового составалицевого объемно-окрашенного керамического
кирпича.
©Турченко А.Е., 2013
64
Научный Вестник Воронежского государственного архитектурно-строительного университета
Результаты исследований. В выполненных исследованиях использовалось глинистое сырье Масловского месторождения Воронежской области (химический состав представлен в табл. 1) и добавки пигменты: сурик (Fe2O3) и мел (CaСО3), конверторный шлак НЛМК (НЛМК – новолипецкий металлургический комбинат) CaO = 48-54,2 %, MgO =1,9 – 10,6 %, FeO = 8,1-11,3 %.
Таблица 1
Химический состав сырьевых материалов
|
|
|
Содержание оксидов, масс. % |
|
|
||||
Вид материала |
|
|
|
|
|
|
|
|
|
SiO2 |
Al2O3 |
CaO |
MgO |
MnO |
FeO |
Na2O + |
Fe2O3 |
||
|
|||||||||
|
|
|
|
|
|
|
K2O |
|
|
Суглинок Масловского |
52-66 |
11,4- |
4,9 – |
2,1- |
- |
- |
3,8 |
4,0 - |
|
месторождения |
|
14,7 |
8,0 |
3,8 |
|
|
-4,3 |
4,95 |
|
Воронежской области |
|
|
|
|
|
|
|
|
|
Шлак конверторный |
2,7- |
1,7-6,3 |
48- |
1,9-10,6 |
2,6-4,6 |
8,1- |
- |
2,7- |
|
НЛМК |
17 |
|
54,2 |
|
|
11,3 |
|
17 |
|
|
|
|
|
|
|
|
|
|
Сырьевые материалы высушивались при температуре 110 ºС и измельчались до прохождения через сито 0,63. Затем готовились шихтовые составы. Содержание пигментов в них было принято на основании ранее выполненных исследований [3]. Компоненты перемешивались сухими. Подготовленная шихта увлажнялась до состояния формовочной влажности и выдерживалась 48 часов. Из шихты методом пластического формования изготавливались образцы размером 5х5х5 см. Затем образцы высушивались при температуре 60 ºС и обжигались при температурах 900, 950, 1000 ºС, установленной для легкоплавких глин. Результаты определения физических показателей экспериментальных образцов представлены в табл. 2.
Таблица 2 Результаты физико-механических испытаний полученных керамических
материалов образцов
Вид пиг- |
Мас- |
|
|
|
Предел |
|
мента |
совая |
Температура |
Средняя |
Водопогло- |
прочности |
Цвет |
|
доля в |
изотермической |
плотность, |
при сжатии, |
|
|
|
щение, % |
|
||||
|
шихте, |
выдержки, ºС |
кг/м³ |
МПа |
|
|
|
|
|
||||
|
% |
|
|
|
|
|
|
|
900 |
1770 |
13,7 |
13 |
Светло-красный |
- |
- |
950 |
1820 |
10,7 |
15 |
Красно- |
|
|
|
|
|
|
коричневый |
|
|
1000 |
1735 |
12,4 |
19 |
Красно- |
|
|
|
|
|
|
коричневый |
Мел |
|
900 |
1810 |
12,5 |
22 |
Светло- |
|
5 |
|
|
|
|
оранжевый |
|
|
950 |
1850 |
14 |
29 |
оранжевый |
|
|
1000 |
1748 |
14.2 |
28 |
оранжевый |
Сурик |
|
900 |
1800 |
12 |
24 |
светло- |
|
|
|
|
|
|
коричневый |
|
2 |
950 |
1840 |
13 |
20 |
красно- |
|
|
|
|
|
|
коричневый |
|
|
1000 |
1630 |
12,4 |
19 |
темно красно- |
|
|
|
|
|
|
коричневый |
Шлак |
|
900 |
1734 |
17,5 |
14 |
светло-розовый |
НЛМК |
|
950 |
1770 |
18,2 |
15 |
светло-розовый |
|
6 |
1000 |
1736 |
17,2 |
16 |
розовый |
65
Научный Вестник Воронежского государственного архитектурно-строительного университета
Выводы. В результате работы:
1. Показано влияния пигментов на изменение цвета керамического черепка на основе шихтовых составов на основе суглинка Воронежской области. Наиболее выразительные цветовые характеристики получены при использовании сурика (Fe2О3).
2. Установлено влияние добавки конверторного шлака, содержащего более 50 % красящих оксидов на физико-механические свойства керамических изделий. Введение конверторного шлака в состав шихты рационально в количестве 6 % при обжиге изделий с максимальной температурой изотермической выдержки 950 ºС.
3. Разработаны рациональные шихтовые составы на основе пылевато-гидрослюдистого суглинка Воронежской области по показателям (предела прочности при сжатии, водопоглощения, полной объемной усадки) для производства керамического облицовочного кирпича. Составы содержат минимальное количество пигмента - сурика (2 %). Рекомендуемая максимальная температура изотермической выдержки при обжиге 950 ºС.
Список литературы
1.Химическая технология керамики: учеб. пособие для вузов / Под ред. И.Я. Гузмана. – М.: ООО РИФ «Стройматериалы», 2003. – 496 с.
2.Солопов С.В. Лицевой керамический кирпич на основе низкосортного глинистого сырья: автореф. дисс… канд. техн. наук. – Орел, 2010. – 24 c.
____________________________________________________________________
Турченко А.Е., канд. техн. наук, доцент кафедры технологии строительных материалов, изделий и конструкций Воронежского государственного архитектурно-строительного университета.
Суслов А.А., канд. техн. наук, доцент кафедры технологии строительных материалов, изделий и конструкций Воронежского государственного архитектурно-строительного университета.
Тел. 8(473)2715321
66

Научный Вестник Воронежского государственного архитектурно-строительного университета
УДК 621.793.3
О.В. Слепцова
ВЗАИМОСВЯЗЬ МИКРОРЕЛЬЕФА ПОВЕРХНОСТИ И СВОЙСТВ НИКЕЛЬ-ФОСФОРНЫХ ПОКРЫТИЙ
Выявлена взаимосвязь микрорельефа поверхности и защитных свойств никель-фосфорных покрытий, полученных из гипофосфитного электролита химического никелирования в присутствии органических добавок-стабилизаторов. Подтверждено участие серо- и азотсодержащей добавок в различных стадиях процесса химического никелирования.
Ключевые слова: никель-фосфорное покрытие, микрорельеф поверхности, атомно-силовая микроскопия
O.V. Sleptsova
INTERRELATION SURFACE MICRORELIEF AND PROPERTIES OF NIKEL-
FOSFORUS COATINGS
The correlation between the surface microrelief and protective properties of the nickel-phosphorus coatings produced from gipofosfitny chemical nickel plating electrolyte in the presence of organic additivesstabilizers. The participation of sulfur-and nitrogen-containing additives in the various stages of chemical nickel plating
Keywords: nickel-phosphorus coating, microrelief surface, atomicforce microscopy
Введение. Никель-фосфорные сплавы формируются на металлических и полимерных подложках в результате протекания автокаталитической окислительно-восстановительной реакции в электролитах, содержащих соль никеля и гипофосфит натрия в качестве восстановителя, образуя покрытия, обладающие рядом ценных функциональных свойств [1]. В частности, наличием фосфора, который соосаждается совместно с никелем, вызвана повышенная коррозионная стойкость таких сплавов [2, 3].
Лежащая в основе процесса химического осаждения Ni-P-сплавов (химического никелирования, ХН) окислительно-восстановительная реакция протекает не только на целевой поверхности, но и в объеме электролита. Уменьшения скорости побочной реакции в объеме электролита химического никелирования достигают введением в него органических микродобавок-стабилизаторов, которые влияют и на процессы, протекающие на целевой поверхности. Адсорбируясь на растущей поверхности, органические добавки могут включаться в осаждаемые покрытия [4, 5]. Это приводит к изменению состава и свойств формирующихся покрытий. Существенный вклад в характеристику свойств покрытий вносит изменение состояния поверхности в процессе осаждения сплава.
В исследовании поверхности вещества одним из наиболее мощных и многосторонних методов является сканирующая зондовая микроскопия (СЗМ). В частности, атомно-силовая микроскопия (АСМ) позволяет получать в нанометровом диапазоне трехмерные изображения поверхности образцов с разным типом проводимости. Последующая цифровая обработка данных дает возможность анализа различных характеристик поверхности для изучения локальной структуры и шероховатости поверхности материалов [6].
© Слепцова О.В., 2013
67

Научный Вестник Воронежского государственного архитектурно-строительного университета
В настоящей работе исследовано влияние на микрорельеф поверхности и защитные свойства Ni-P-покрытий серо- и азотсодержащих органических соединений – тиомочевины
(NH2)2CS и гуанидина (NH2)2CNH.
Методика эксперимента. Процесс химического осаждения никеля на изделия из стали Ст3 осуществляли из кислого электролита (рН 5,5), содержащего соль никеля NiCl2, гипофосфит натрия NaH2PO2 в качестве восстановителя, глицин NH2CH2COOH в качестве комплексообразователя и ацетат натрия CH3COONa в качестве буферирующей добавки [7]. В электролит также добавляли органические добавки-стабилизаторы, которые используются для предотвращения протекания реакции осаждения сплава Ni-P в объеме электролита, на стенках стакана, т.е. нецелевых процессов. В качестве добавок были выбраны серосодержащий стабилизатор – тиомочевина и азотсодержащий – гуанидин, имеющие сходное строение (табл. 1).
Опытным путем были выбраны максимальные концентрации, при которых протекает процесс осаждения на целевой поверхности. При более высоких концентрациях процесс осаждения прекращается.
Таблица 1
Органические добавки
Название |
Структурная |
Условное |
|||
добавки |
формула |
обозначение |
|||
|
S |
|
|||
Тиомочевина |
|
|
|
Т |
|
H2N NH2 |
|||||
|
|
||||
|
NH |
|
|||
Гуанидин |
|
|
|
Г |
|
H2N NH2 |
|||||
|
|
||||
|
|
|
|
|
Покрываемые образцы предварительно очищали от механических загрязнений, обезжиривали и травили [7]. Температура в процессе осаждения поддерживалась на уровне 80±2 оС с помощью термостата «UTU». Процесс химического никелирования каталитический, самопроизвольно инициируется только на некоторых металлах (никель, палладий, железо), поэтому для инициирования процесса на латунных образцах их приводили в контакт со стальной проволокой. Время никелирования 30 минут. Промытые в воде и высушенные образцы до и после процесса осаждения взвешивали на аналитических весах с точностью ± 5.10-4 г.
Толщину покрытия h (мкм) и скорость его осаждения V (мкм/ч) оценивали по увеличению массы образца согласно формулам:
h |
m2 m1 |
и |
V |
h |
, |
78,5 10 3 s |
|
где m2 – масса образца после опыта, г; m1 – масса образца до опыта, г; η – время никелирования, ч; s – площадь покрываемой поверхности, дм2; 78,5. 10-3 г/дм2 . ч =1 мкм/ч.
Пористость покрытия определяли путем выявления в нем пор с помощью реактивов, взаимодействующих с покрываемым металлом с образованием окрашенных соединений. Выявление пор в покрытиях на стальных образцах проводили методом погружения в раствор, содержащий гексацианоферрат калия K3[Fe(CN)6] [8]. Температура раствора 25–35 оС, время погружения 5 минут. По истечения этого времени образцы извлекали из раствора и осушали в подвешенном состоянии. Затем подсчитывали количество пор Nср (см-2), соответствующее числу синих точек на каждом образце.
68
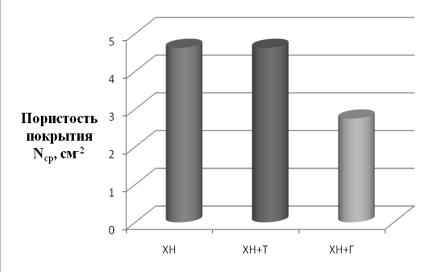
Научный Вестник Воронежского государственного архитектурно-строительного университета
Микрорельеф поверхности покрытий изучали с использованием атомно-силового микроскопа «NanoЕducator» фирмы NT-MDT (г. Зеленоград) на образцах со свежеосажденным Ni-P-сплавом. Размер скана 10,21 мкм 10,21 мкм, разрешение 276
276. Оценку шероховатости поверхности осуществляли на основе средней квадратичной шероховатости Sq, являющейся определяющей характеристикой шероховатости [6], вычисление которой проводили с помощью программного обеспечения сканирующего зондового микроскопа.
Результаты и их обсуждение. Исследования показали, что выбранные органические добавки оказывают различное влияние на свойства Ni-P-покрытий, а именно на скорость их осаждения и пористость, характеризующую защитные свойства покрытий (табл. 2).
Введение в уксуснокислый электролит химического никелирования тиомочевины (10-7 М) повышает скорость целевой реакции осаждения Ni-P-покрытия. Поэтому при заданном времени ведения процесса никелирования (30 мин) покрытие, осаждаемое в присутствии тиомочевины, имеет большую толщину (табл. 2).
|
|
|
|
|
Таблица 2 |
|
Свойства никель-фосфорных покрытий |
|
|||
|
|
|
|
|
|
Добавка в электролите |
|
Скорость |
Толщина |
Пористость |
Шерохо- |
|
осаждения |
покрытия |
ватость |
||
ХН |
|
Nср, см-2 |
|||
|
|
V, мкм/ч |
h, мкм |
|
Sq, нм |
Без добавки |
|
11,3 |
7,5 |
4,63 |
21,562 |
|
|
|
|
|
|
Тиомочевина (10-7 М) |
|
18,6 |
12,1 |
4,60 |
92,672 |
Гуанидин (10-6 М) |
|
11,4 |
7,6 |
2,75 |
14,641 |
Однако пористость при более высокой получившейся толщине покрытия за счет более высокой скорости осаждения остается неизменной (рис. 1). Введение гуанидина (10-6 М) в электролит химического никелирования не влияет на скорость осаждения сплава и толщину покрытий на поверхности образцов, но существенно снижает их пористость, увеличивая в результате их коррозионную устойчивость (табл. 2, рис. 1). Явное снижение пористости покрытий при введении гуанидина свидетельствует об изменении структурных характеристик как самого покрытия, так и микроструктуры его поверхности.
Рис. 1. Пористость покрытий Nср, полученных в электролитах химического никелирования без стабилизирующей добавки (ХН), с добавкой тиомочевины (ХН+Т) и гуанидина (ХН+Г)
69
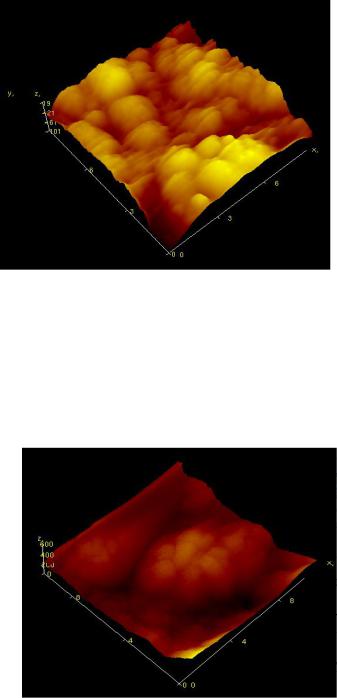
Научный Вестник Воронежского государственного архитектурно-строительного университета
Для выяснения связи защитных свойств покрытий, а именно их толщины и пористости с микрорельефом поверхности никель-фосфорных покрытий, были привлечены данные, полученные методом сканирующей атомно-силовой микроскопии. На изображениях микрорельефа поверхности Ni-P-сплава, осажденного из электролита химического никелирования без добавок, просматриваются вытянутые в плоскости подложки сфероиды высотой до 100 нм (рис. 2), наличие которых свидетельствует об аморфной структуре сплава. Аморфной структура покрытий становится вследствие включения фосфора, осаждающегося совместно с никелем и приводящего к разрушению кристаллической структуры, характерной для чистого никеля.
Рис. 2. 3D–изображение поверхности никель-фосфорного сплава, осажденного из электролита химического никелирования, полученное методом АСМ
На Ni-P-покрытиях, осажденных из электролита, содержащего тиомочевину, наблюдается ярко выраженная зернистость сфероидов несколько более выраженная, чем у покрытий, полученных в отсутствие добавок (рис. 3). При этом введение в электролит тиомочевины приводит к существенному возрастанию фактора шероховатости Sq, определенного с помощью программного обеспечения атомно-силового микроскопа (табл. 1).
Рис. 3. 3D-изображение поверхности Ni-P-покрытия, осажденного из электролита химического никелирования, содержащего тиомочевину, полученное методом АСМ
70