
3440
.pdf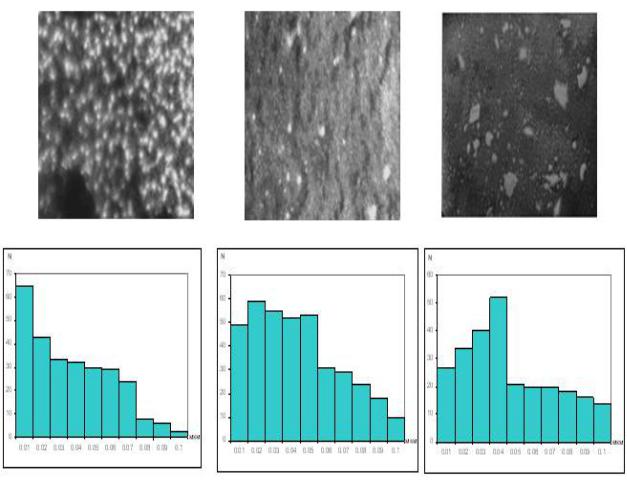
Научный Вестник Воронежского государственного архитектурно-строительного университета
-хлорида никеля 15 – 25;
-борной кислоты 25 – 40;
-лаурилсульфата натрия 0,01 – 0,05;
-декадигидробората натрия 0,02 – 0,1;
-рН раствора 2,5 – 5, температура 30 – 60 оС, плотность тока 0,5 – 5 А/дм2.
В работе в качестве стандартного был выбран режим со следующими параметрами: плотность катодного тока 2 А/дм2, кислотность - 4,0 ед. рН, температура электролита 40 °С и концентрация борсодержащей добавки 1 % , тип подложки – медная.
При осаждении получается плотное, беспористое эластичное покрытие никель-бор толщиной до 200 мкм с содержанием бора 1,5 %.
Дальнейшее повышение содержания бора в сплаве не приводит к значительному улучшению защитных свойств покрытия. Содержание бора в покрытии никель-бор корректируется концентрацией декагидробората натрия.
Обсуждение результатов
Влияние плотности катодного тока на структуру покрытия NiB.
Плотность катодного тока составляла 0,5; 2 и 4 А/дм2 при значении рН раствора 4,0, содержании бора в покрытии 1 % и температуре 40 оС. Визуальный осмотр поверхности покрытий показал, что они имеют полосчатый рельеф. С увеличением плотности катодного тока от 0,5 до 4 А/дм2 шероховатость поверхности увеличивается.
Рис. 1. Влияние плотности катодного тока на структуру покрытия NiB
41
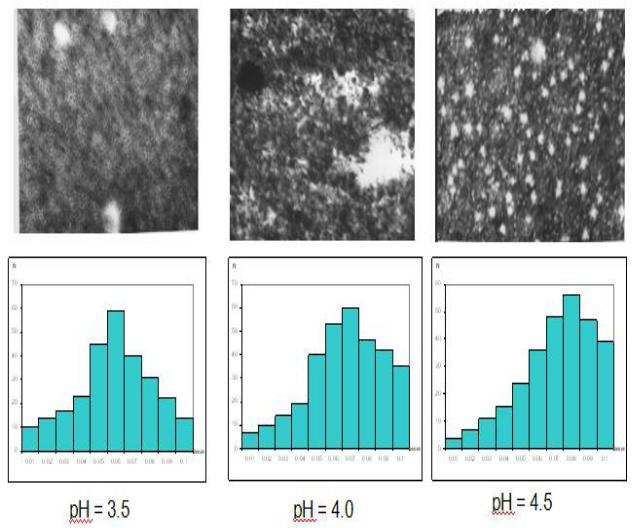
Научный Вестник Воронежского государственного архитектурно-строительного университета
Из фотографий и гистограмм (рис. 1) можно сделать вывод, что увеличение плотности катодного тока от 0,5 до 4 А/дм2 сглаживает разницу в размерах зерен и сдвигает их величину в сторону больших значений, Так, при iк = 0,5 А/дм2 доля крупных зерен составляет 10 %, а при iк = 4 А/дм2 ~ 30 %.
Влияние рН электролита на структуру покрытий NiB.
Изучение влияния кислотности электролита на процесс выделения NiB проводили в диапазоне рН от 3 до 5. Кислотность электролита составляла 3,5; 4,0 и 4,5 ед. рН при
значении плотности катодного тока 2 А/дм2, содержании бора в покрытии 1 % и температуре
40оС.
С увеличением рН поверхность покрытия становится более развитой, на ней появляются неровности и включения (рис. 2).
Рис. 2. Влияние рН электролита на структуру покрытий NiB
С увеличением рН от 3,5 до 4,5 максимумы по размеру зерен сдвигаются вправо, и наблюдается формирование крупнозернистой структуры. При рН электролита 3,5 число мелких зерен составляет 25 %, средних и крупных ~ 75 % от общего числа зерен.
При рН электролита 4,5 преобладает доля крупных зерен − 70 %, а сумма средних и мелких с диаметром менее 0,08 мкм ~ 30 % от общего числа зерен. Микроструктурные исследования согласуются с поляризационными данными и содержанием бора в покрытии
42
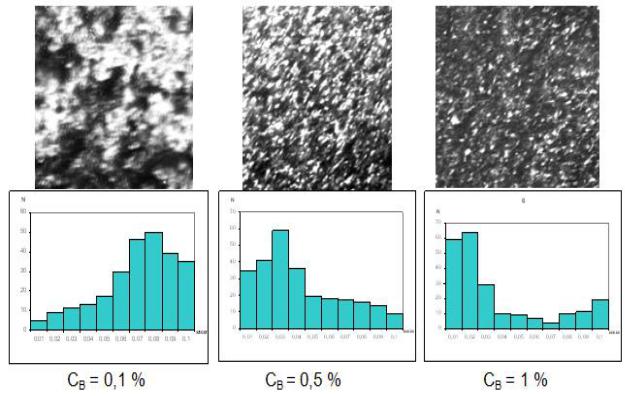
Научный Вестник Воронежского государственного архитектурно-строительного университета
Ni – B. Доля тока, приходящаяся на выделение Н2, уменьшается с повышением рН, а на образование NiB − увеличивается. При этом обогащенные бором оказываются осадки, полученные из электролитов с более высокой кислотнстью [2].
Влияние концентрации бора в электролите на структуру покрытий никель-бор
Процентное содержание бора в электролите составляло 0,1; 0,5 и 1 %, рН электролита 4,0, температура – 40 °С, iк = 2 А/дм2. С увеличением количества бора в электролите шероховатость покрытий увеличивается − они становятся неоднородными и бугристыми
(рис. 3).
Рис. 3. Влияние концентрации бора в электролите на структуру покрытий Ni - B
Из представленных фотографий и гистограмм можно сделать вывод, что с увеличением концентрации борсодержащей добавки размер зерна имеет тенденцию к уменьшению.
С увеличением концентрации бора в покрытии от 0,1 до 1 % максимумы по размеру зерен сдвигаются влево, и наблюдается формирование мелкнозернистой структуры. При концентрации бора в покрытии 0,1 % число мелких зерен составляет 20 %, средних и крупных ~ 80 % от общего числа зерен.
При концентрации бора в покрытии 1 % преобладает число мелких зерен 85 %, а сумма средних и крупных ~ 15 % от общего числа зерен.
Увеличение доли тока на выделение Н2 и уменьшение на образование Ni–B с увеличением концентрации бора. Это свидетельствует о снижении скорости электровосстановления ионов Ni2+ и увеличении дисперсности формируемой пленки.
Влияние температуры электролита на структуру покрытий NiB
Температура электролита 30, 40 и 50 °С, значение рН 4,0, содержании бора в покрытии − 1 % (при концентрации борсодержащей добавки электролита 1 %) и iк = 2 А/дм2. Присутствие таких дефектов как поры, несплошности, водородные камеры в структуре
43
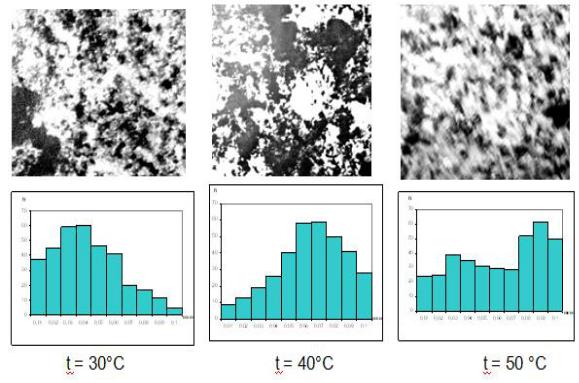
Научный Вестник Воронежского государственного архитектурно-строительного университета
покрытий объясняется спецификой процесса электроосаждения, когда имеет место одновременный разряд ионов никеля и водорода на поверхности катода (рис. 4).
Влияние температуры электролита на структуру покрытий никель – бор можно проследить из сравнения гистограмм. Понижение температуры электролита до 30 оС приводит к изменению вида гистограмм. При низкой температуре максимумы по размеру зерен сдвигаются влево, и наблюдается значительная дисперсность зерен. Число мелких зерен составляет ~ 66 %, средних и крупных ~ 34 % от общего числа зерен. Это свидетельствует о формировании неравнозернистой структуры. При повышении температуры до 50 оС происходит выравнивание размера зерна. Уменьшается доля мелких зерен до ~ 60 % и увеличивается число средних и крупных зерен на 15 %.
Рис. 4. Влияние температуры электролита на структуру покрытий NiB
Формирование такой структуры объясняется тем, что повышение температуры электролита, как уже говорилось выше, облегчает отрыв водорода от поверхности катода, и, следовательно, при этом уменьшается блокировка активных центров кристаллизации, за счѐт чего большее их число получает возможность развиваться, и структура покрытия становится более равномерной и мелкозернистой [3]. Кроме того, с повышением температуры электролита растѐт вероятность осаждения на катоде гидроксида никеля, что также увеличивает число активных центров кристаллизации.
Выводы. Результаты микроструктурных исследований позволяют сделать вывод о том, что покрытия NiB независимо от режимов нанесения имеют поликристаллическую структуру. Величина зерна и характер зернистой структуры определяются условиями электроосаждения покрытий. Хотя однозначной зависимости размера зерна от режима осаждения выявить не удалось, но с увеличением плотности катодного тока сглаживается разница в размерах зерен и сдвигается их величина в сторону больших значений; с увеличением кислотности электролита максимумы по размеру зерен сдвигаются вправо, и наблюдается формирование крупнозернистой структуры; с увеличением концентрации бора в покрытии максимумы по размеру зерен сдвигаются влево, и наблюдается формирование мелкозернистой структуры; с понижением температуры максимумы по размеру зерен
44
Научный Вестник Воронежского государственного архитектурно-строительного университета
сдвигаются влево, а при повышении температуры до 50 оС происходит выравнивание размера зерна.
Список литературы
1.Кудрявцева В.Н., Маккавеева С.С., Пилипенко Д.Г. Электроосаждение никеля и сплава Ni-B из аммиачно-цитратного электролита // Гальванотехника и обработка поверхности. - 2001. - Т. 9. - № 4. - С. 25-30.
2.Габаевская Т.В., Новоторцев И.Г., Цыбульская Л.С. Процесс изомеризации пентангексановой фракции // Журн. прикладной химии. - 2005. - Т. 68. - № 4. - С.587-592.
3.Прусов Ю. В., Макаров В. Ф. Обоснование новых проектных решений в химическом производстве // Журн. прикладной химии. - 2010. -Т. 73. - № 5. - С. 753 – 755.
____________________________________________________________________
Березина Наталья Николаевна – доцент кафедры материаловедения и физики металлов Воронежского государственного технического университета.
Лукин Анатолий Александрович - к.ф.-м.н., доцент кафедры материаловедения и физики металлов Воронежского государственного технического университета. E-mail: toto_luk@mail.ru
Тарханов Андрей Константинович - к.ф.-м.н., доцент кафедры физики Воронежского государственного архитектурно-строительного университета. E-mail: anvetkin@yandex.ru
Лукин Олег Анатольевич - к.ф.-м.н., доцент кафедры экономики Московского института инженеров транспорта (МИИТ, Воронежский филиал).
45

Научный Вестник Воронежского государственного архитектурно-строительного университета
УДК 691.263.5:666.951
А.В. Уколова, Ю.С. Дедова КОМПЛЕКСНЫЙ МОДИФИКАТОР В ШЛАКОЩЕЛОЧНОМ ВЯЖУЩЕМ
Статья посвящена теоретическим и практическим исследованиям условий улучшения свойств шлакощелочного вяжущего, что позволит использовать его при получении высокопрочных, долговечных композиционных материалов. Определен оптимальный состав комплексного модификатора в составе шлакощелочного вяжущего, обеспечивающий существенное увеличение прочности микробетона.
Ключевые слова: модификатор, шлакощелочное вяжущее, новообразование, структура, прочность, цеолиты, микробетон
А.V. Ukolova, D.S. Dedova
THE COMPLEX MODIFIER IN CINDER-ALKALINE ASTRINGENT COMPONENT
The article is devoted to theoretical and practical research to improve the properties of slag-alkaline conditions binder, which will use it in the preparation of high-strength, durable composite materials. The optimum composition of complex modifier in the slag-alkaline binder, providing a significant increase in strength microconcrete.
Keywords: modifier slag-alkaline binder, neoplasm, structure, strength, zeolites, microconcrete
Введение. В связи с повышением требований к качеству материалов для выполнения строительных работ, особое внимание ученых обращено к высокопрочным смесям, например на основе шлаковых составляющих. Использование местных сырьевых ресурсов и побочных продуктов различных производств, в том числе шлаков, является одним из путей удешевления отечественного производства. Особое внимание уделяется модифицированным шлакощелочным вяжущим. Важным моментом при получении материалов и изделий на их основе является изыскание путей улучшения их свойств и стабилизации их во времени.
Теоретическая часть. Известно, что на свойства искусственного конгломерата оказывают существенное влияние фазовый состав гидратных новообразований, скорость их формирования, прочность связей в кристаллогидратных комплексах, поровая структура. Причем основные параметры, предопределяющие синтез прочности искусственного камня, в значительной степени зависят от состава и качества сырьевой смеси, вида щелочного компонента, условий гидратации и твердения. Влияние указанных факторов на долговечность шлакощелочных материалов неоднозначно и требует детального исследования. Выбор неоптимальных технологических параметров, как правило, является причиной получения бетона с нестабильными физико-механическими свойствами. Следует отвести при этом значительную роль корректирующим добавкам, оказывающим модифицирующее влияние на формирование структуры конгломерата, повышая в конечном итоге его долговечность.
На основании анализа литературных данных о структурных ионообменных характеристиках природных цеолитов, особенно термоактивированных, в которых исходные алюмосиликаты переходят в смесь активных Al2O3 и SiO2, а так же о влиянии их на интенсивность связывания щелочи с образованием водостойких композитов шлакощелочного искусственного камня, можно заключить, что эффективными в данном случае могут быть высококремнеземистые цеолиты Na2O·Al2O3·nSiO2·mH2O [1,2].
© Уколова А.В., 2013
46
Научный Вестник Воронежского государственного архитектурно-строительного университета
Они характеризуются значительными размерами полостей и каналов, которые соизмеримы с размерами ионов Na+, K+ и SO42-. Эти цеолиты обладают высокой ионообменной способностью, что обусловливает процессы замены цеолитной воды в их полостях, в том числе межплоскостном пространстве молекулами, содержащими, например ионы Na+, K+ , SO42- и др. [3, 4]. Это приводит к формированию в составе продуктов твердения дополнительных структурообразующих элементов в виде природных аналогов, например минерала нозеана, в полостях которого компонент, содержащий, например ионы Na+ и SO42-, прочно удерживается структурными связями [4, 5]. Исследованиями установлено, что в природном цеолите атомы алюминия находятся в тетраэдрической координации, а в системе «цеолит – Na2SO4» ионы алюминия имеют октаэдрическую координацию.
Это обстоятельство обусловлено образованием связей Al-S и Al-O-S за счет химического связывания молекул Na2SO4 в полостях цеолита. При этом формируется каркасная структура новообразований, что повышает жесткость цементного шлакощелочного камня и приводит к стабильности его прочностных и деформативных характеристик по сравнению с аналогичными показателями для образцов на основе бездобавочного ШЩВ [5]. В связи с перечисленным, с научной точки зрения интерес для исследования представляет комплексное сочетание шлака, щелочного активизатора, добавки глинистых минералов в обожженном состоянии и компонента, содержащего ион SO42-.
Экспериментальная часть. В наших исследованиях была поставлена задача - изучить влияние комплексного модификатора на прочность микробетона и стабилизацию ее во времени.
В качестве сырьевых материалов использован тонкомолотый (S=350±20 м2/кг) гранулированный доменный шлак Липецкого металлургического комбината с коэффициентом основности 1,1 – 1,2. В качестве щелочного компонента применена сода. Химический состав термоактивированной глинистой добавки (боя керамического кирпича)
%: SiO2 – 67; Al2O3 – 12; Fe2O3+FeO – 5; CaO – 4; MgO – 1,5; SO3 – 0,15.
Добавкой, содержащей ион SO42-, являлся полуводный гипс. Осуществлялось поэтапное исследование от простых систем к сложным: шлак + сода; шлакощелочное вяжущее + термоактивированная добавка; шлакощелочное вяжущее + термоактивированная добавка + гипс. Поэтапное усложнение изучаемой системы, а также сравнительные испытания позволили уточнить роль отдельных компонентов сырьевой смеси и условия управления их взаимодействием. Осуществлялось пассивное и активное планирование эксперимента. Пассивное - позволило установить рациональные границы варьирования изучаемых факторов, а активное – оптимизировать состав исследуемых систем в экспериментально установленных границах. Изготавливались образцы микробетона размером 2×2×2 см в лабораторных условиях, шлакощелочная смесь приготавливалась в турбинном смесителе. Перемешивание обеспечило получение однородной массы. Подвижность раствора по Суттарду составила 30-32 см.
При исследовании влияния составов сырьевой смеси на прочность микробетона применен метод активного планирования двухфакторного эксперимента. Варьируемыми параметрами приняты: дозировка гипса (х1), дозировка глинистой добавки (х2).
Уровни варьирования независимых переменных представлены в таблице. Тепловлажностная обработка (ТВО) проводилась при 90 °С, изотермическая
выдержка – 5 часов. После ТВО образцы выдерживались сутки в естественных условиях и испытывались на сжатие. Результаты экспериментов обрабатывались методами математической статистики. Доверительные интервалы оценок получаемых показателей определялись на основании результатов испытаний малых выборок с использованием распределения Стьюдента с надежностью 0,95.
47
Научный Вестник Воронежского государственного архитектурно-строительного университета
Таблица
Уровни варьирования независимых переменных
Уровни варьирования |
|
|
Значения переменных |
|
||||
|
|
|
|
|
|
Дегидратированная глина |
|
|
независимых переменных |
|
Гипс (х1) |
|
|
|
|
||
|
|
|
|
(х2) |
|
|||
|
|
|
|
|
|
|
|
|
Верхний уровень (+1) |
|
6 |
|
|
|
|
15 |
|
Основной уровень (0) |
|
4 |
|
|
|
|
10 |
|
Нижний уровень (-1) |
|
2 |
|
|
|
|
5 |
|
По результатам определения предела прочности при сжатии была получена |
||||||||
функциональная зависимость: |
|
|
|
|
|
|
|
|
|
|
y 44,3 19,1x |
15,4x |
2 |
12,1x2 |
3,6x2 |
||
|
|
1 |
|
1 |
2 |
|
Оптимальный состав содержал: гипса 4 %, дегидратированной глинистой добавки 15 %, остальное - шлакощелочное вяжущее. Прочность микробетона (цементного камня) составляла 56 МПа, что в 1,3 раза больше по сравнению с бездобавочными образцами на шлакощелочном вяжущем и существенно выше по сравнению с образцами, содержащими в качестве добавки только дегидратированную глину или только гипс. Образцы оптимального состава при длительном хранении (один год) в естественных условиях не имели трещин, а в эталонных образцах на шлакощелочном вяжущем они наблюдались. Следовательно, представляется возможным утверждать, что комплексный модификатор из термоактивированной глинистой добавки и гипса обеспечивает эффект относительной стабилизации прочностных характеристик получаемого искусственного камня.
Заключение. В работе убедительно показана эффективность применения комплексного модификатора оптимального состава в шлакощелочном вяжущем. Можно заключить, что открывается возможность создания шлакощелочных вяжущих нового поколения. Они получаются путем совместного помола шлака с цеолитовой породой и сульфатосодержащим сырьем. Эти вяжущие сохраняют способность к гидратационному твердению в течение длительного времени и обеспечивают получение долговечных шлакощелочных бетонов высоких марок.
Список литературы
1.Бутт Ю.М., Тимашев В.В. Портландцемент // М.: Стройиздат, 1974. – 325с.
2.Брек Д. Цеолитовые молекулярные сита // М.: Мир. - 1976.
3.Уколова А.В., Бубнова М.Н. Шлакощелочной композиционный материал с глинистыми минералами // I междунар. практ. конф. Высокие технологии в экологии. - Воронеж, 2009.
4.Белов Н.В. Кристаллохимия силикатов с крупными катионами // АН СССР. – М., 1961. – 67с.
5.Кривенко П.В. Шлакощелочные вяжущие нового поколения // Докл. III научнопракт. конф. - Киев: 1989. - С. 170-176.
____________________________________________________________________
Уколова Альбина Васильевна – к.т.н., профессор кафедры строительных материалов изделий и конструкций Воронежского государственного архитектурно-строительного университета. Тел.:89518601930.
Дедова Юлия Сергеевна – магистрант Воронежского государственного архитектурно-строительного университета. Тел.:89507657860.
48
Научный Вестник Воронежского государственного архитектурно-строительного университета
УДК 691.263.5:666.961
Т.Ф. Ткаченко, В.Т. Перцев, С.П. Козодаев
К ВОПРОСУ ЭНЕРГОСБЕРЕЖЕНИЯ В ТЕХНОЛОГИИ ПЕНОБЕТОНОВ НЕАВТОКЛАВНОГО ТВЕРДЕНИЯ
Показаны преимущества одностадийной технологии неавтоклавных пенобетонов, пути обеспечения экономии энергетических затрат на их производство при условии получения материала с заданной средней плотностью и прочностью.
Ключевые слова: неавтоклавный пенобетон, технология, энергосбережение, пенобетоносмеситель, гидродинамические критерии
T.F. Tkachenko, V.T. Pertcev, S.P. Kozodaev
FOR QUESTION OF ENERGY ECONOMY IN THE FOAMCONCRETE OF NOAUTOCLAVE HARDENER TECHNOLOGY
Showed advantages of one stage technology noautoclave foamconcretes, ways of economy energy expenditures on the them production with receipt materials of set middle density and firmer.
Keywords: noautoclave foamconcretes, technology, economy energy expenditures, foamconcretes mixer, hidro-dinamis criterions
Введение. В современных условиях перед строительной отраслью стоит вопрос об определении путей перехода к более эффективным материалам и технологиям с целью обеспечения экономии материальных и энергетических затрат. В настоящее время в качестве основных конструкционных легких бетонов используются силикатные автоклавные ячеистые бетоны. Однако, производство газосиликатных ячеистых бетонов затруднено из-за сложности их технологии, значительной энергоемкости, высокой стоимости оборудования, ограниченности номенклатуры изделий, обусловленной автоклавным способом тепловой обработки. Так, на тепловую обработку этих материалов затрачивается до 30 % стоимости их производства, расходуется до 80 % энергии, потребляемой производством. Одним из наиболее перспективных материалов, отвечающим требованиям энергосбережения и одновременно являющимся экологически чистым и эффективным по теплофизическим параметрам, выступает конструкционно-теплоизоляционный пенобетон неавтоклавного твердения [1].
Технологии пенобетонов неавтоклавного твердения характеризуются относительной простотой. Вместе с тем, они осложняются из-за варьирования качества сырьевых компонентов, режимов перемешивания, условий формования и твердения, что зачастую вызывает нестабильность структуры и свойств получаемых изделий. В целом результаты многочисленных исследований и опыт практического применения показывают, что имеющиеся технологии неавтоклавных пенобетонов являются несовершенными и нуждаются в улучшении. В настоящее время из всех существующих технологий неавтоклавных пенобетонов наиболее перспективной на наш взгляд представляется одностадийная технология, при которой процессы приготовления пены и компонентов пенобетона совмещены.
__________________________________________
© Ткаченко Т.Ф., 2013
49
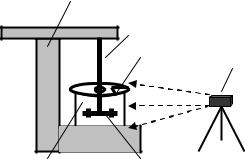
Научный Вестник Воронежского государственного архитектурно-строительного университета |
||||||||||||
Эта технология за счет регулирования гидродинамических, массообменных и |
||||||||||||
энергетических характеристик позволяет осуществлять управление процессами |
||||||||||||
формирования ранней структуры пенобетона при перемешивании. Сущность способа |
||||||||||||
заключается в том, что процесс приготовления пенобетонной смеси осуществляется при |
||||||||||||
помощи скоростного пенобетоносмесителя турбулентного типа. Раствор пенообразователя и |
||||||||||||
вода дозируется по объему, компоненты твердой фазы – по массе, и все составляющие |
||||||||||||
последовательно подаются в пенобетоносмеситель, из которого после перемешивания |
||||||||||||
пенобетонная смесь растворонасосом перекачивается к месту укладки в формы или в |
||||||||||||
монолитную конструкцию. |
|
|
|
|
|
|
|
|
|
|
|
|
Технология неавтоклавных пенобетонов. В технологии неавтоклавных |
||||||||||||
пенобетонов, как и во всех других технологиях, большое значение имеет энергосбережение. |
||||||||||||
Для решения этой проблемы основную роль играют конструктивные и технические |
||||||||||||
характеристики используемого оборудования для приготовления пенобетонной смеси. |
||||||||||||
Главная практическая задача технологии неавтоклавных пенобетонов состоит в обеспечении |
||||||||||||
стабильных по величине и устойчивых во времени характеристик замкнутого воздушного |
||||||||||||
порового пространства, гарантирующих получение материала с заданной средней |
||||||||||||
плотностью, а также приемлемые сроки набора «распалубочной» и «отпускной» прочности. |
||||||||||||
Перемешивание в высокоскоростных смесителях. В данной работе для |
||||||||||||
осуществления процесса массопереноса в системах «обводненная дисперсная среда-воздух» |
||||||||||||
рекомендуется использовать высокоскоростной смеситель турбулентного типа, в котором |
||||||||||||
реализуется достаточно сложная структура потоков перемещения исходных компонентов, |
||||||||||||
изменяющаяся при перемешивании в масштабе смесителя за счет перераспределения |
||||||||||||
компонентов фаз по траекториям и времени пребывания в смесителе. При перемешивании в |
||||||||||||
высокоскоростных смесителях турбулентного типа реализуются |
два |
механизма |
|
переноса |
||||||||
вещества через межфазную поверхность - молекулярной и вихревой (турбулентной) |
||||||||||||
диффузиями. В процессе турбулентной диффузии перенос вещества определяется |
||||||||||||
турбулентностью потока, его гидродинамическим состоянием. Следует отметить, что из-за |
||||||||||||
конструктивных особенностей пенобетоносмесителя помимо межфазной турбулентности в |
||||||||||||
жидкой фазе может возникать и турбулентность, вызванная неравномерностью скоростей |
||||||||||||
потоков, перекрестными потоками, способствующими образованию поверхностных вихрей. |
||||||||||||
Изучение процесса воздухововлечения и определение энергозатрат при |
||||||||||||
перемешивании |
осуществлялось |
с использованием |
экспериментально полученных |
|||||||||
1 |
|
|
зависимостей |
изменения |
средней |
плотности |
||||||
|
|
пенобетонной смеси от времени перемешивания, |
||||||||||
|
|
|
||||||||||
|
4 |
|
скорости вращения мешалки и дозировки добавки. |
|||||||||
|
|
Для |
изучения |
распределения |
|
потоков |
||||||
|
3 |
|
|
|||||||||
|
|
распределения |
|
воздушной |
фазы |
была |
||||||
|
6 |
|
|
|||||||||
|
|
|
сконструирована установка (рис. 1), состоящая из |
|||||||||
|
|
|
смесителя турбулентного типа и прозрачного |
|||||||||
|
|
|
сосуда с крышкой и течкой для загрузки |
|||||||||
|
|
|
модельных частиц, имитирующих воздушную |
|||||||||
2 |
5 |
|
фазу. Пузырьки воздушной фазы моделировались |
|||||||||
|
вспененными |
|
гранулами |
|
пенополистирола |
|||||||
|
|
|
|
|
||||||||
Рис. 1. Схема установки для изучения |
|
плотностью |
|
10 |
кг/м3 |
2 . |
В |
|
качестве |
|||
процесса воздухововлечения: |
|
дисперсионной |
среды |
использовался |
|
глицерин |
||||||
|
|
|
|
|||||||||
1- модель смесителя турбулентного типа; |
|
плотностью 1260 кг/м3 и вязкостью 1,49.103 Па.с. |
||||||||||
2- емкость из органического стекла |
|
|
Формирование |
структуры |
|
потоков. |
||||||
3 - течка для загрузки компонентов смеси; |
|
Результаты |
изучения |
формирования |
структуры |
|||||||
4 - вал смесителя; 5 - мешалка с лопастями; |
потоков |
и |
поверхности |
перемешиваемой |
||||||||
6 - цифровой фотоаппарат марки Canon |
|
|||||||||||
|
модельной системы приведены на рис. 2 [3]. |
|||||||||||
с автоматической настройкой |
|
|||||||||||
|
|
|
|
|
|
|
|
|
|
|
50