
3440
.pdf
Научный Вестник Воронежского государственного архитектурно-строительного университета
УДК 691.51: 666.9
С.М. Усачев, А.М. Усачев, О.М. Дроздов
ОЦЕНКА СВОЙСТВ ШЛАКОЩЕЛОЧНОГО ВЯЖУЩЕГО НА ОСНОВЕ ШЛАКОВ НЛМК
Изучен комплекс физико-механических характеристик шлакощелочного вяжущего, изготовленного на основе шлаков НЛМК. Проведена оценка водостойкости, атмосферостойкости и кислотостойкости. Изучены защитные свойства вяжущего по отношению к стальной арматуре. Доказана возможность получения на основе шлаков НЛМК вяжущего, растворов и бетонов, обладающих высокими эксплуатационно-техническими свойствами.
Ключевые слова: утилизация отходов, металлургические шлаки,шлакощелочное вяжущее, простота технологии, дешевизна, высокие физико-механические характеристики
S.M. Usachev, А.М. Usachev, O.M. Drozdov
EVALUATION OF THE PROPERTIES OF SLAG ALKALINE BINDER
ON THE BASIS OF SLAG NLMK
Investigated complex of physical-mechanical characteristics of slag alkaline binders, made on the basis of slag NLMK. The estimation of the water-resistance, weather resistance and acid.Studied the protective properties of the binder in relation to steel reinforcement.Proved the possibility of receipt on the basis of slag NLMK binder, solutions and concrete with high operational and technical properties.
Ключевыеслова: recycling of wastes, metallurgical slag, slag alkaline binder, the simplicity of the technology, low cost, high physical-mechanical properties
Введение. Проблема утилизации промышленных отходов сегодня является крайне актуальной. Ежегодно человечество использует приблизительно 10 млрд. т. минеральных и приблизительно столько же органических сырьевых материалов. При этом от 10 до 99 % исходного сырья превращаются в различные виды отходов, выбрасываемые в атмосферу, воды Мирового океана, загрязняющие землю [1].
Одними из основных источников загрязнения окружающей среды являются предприятия черной и цветной металлургии. В общем объеме образующихся отходов 70 % приходится на долю предприятий металлургической отрасли, что составляет около 190 млн. т. в год. Основная масса отходов металлургических процессов образуется в виде шлаков. Металлургические шлаки являются неизбежным побочным продуктом основного производства и составляют от 17 до 50 % объема произведенного металла. За время работы большинства металлургических предприятий накоплены значительные объемы отходов производства в виде металлургических шлаков, которые складируются в отвалах [2-4].
Металлургические шлаки представляют собой ценное сырье для промышленности строительных материалов. Сегодня на основе шлаков металлургии получают шлаковату, шлаковую пемзу, шлакоситаллы, мелкий и крупный заполнитель для бетонов и растворов, отощающие топливосодержащие добавки для керамических изделий. Большое количество шлаков применяется для изготовления различных вяжущих, таких как шлакопортландцемент, глиноземистый цемент, сульфатно-шлаковый цемент, известковошлаковый цемент [5-11].
© Усачев С.М., 2013
121
Научный Вестник Воронежского государственного архитектурно-строительного университета
Шлакощелочное вяжущее. На наш взгляд наиболее перспективным является применение шлака для получения шлакощелочного вяжущего (ШЩВ). Это обусловлено, вопервых тем, что при изготовлении ШЩВ утилизируется большое количество отходов. Вовторых, технология изготовления ШЩВ достаточно проста. Она не требует разработки и добычи природного сырья. В технологии отсутствует дорогостоящий процесс обжига сырьевой смеси. Как показывают исследования [12-15], удельные капиталовложения при производстве ШЩВ в 2-3 раза меньше, чем при производстве портландцемента (ПЦ); себестоимость ниже в 1,5-3 раза по сравнению с ПЦ; удельный расход условного топлива меньше в 3-5 раз, электроэнергии – в 2 раза.
Оценка свойств ШЩВ. В данной работе проводилась оценка свойств шлакощелочного вяжущего вещества, полученного совместным помолом высушенного доменного гранулированного шлака и кальцинированной соды в соотношении 95 к 5 % по массе.
В качестве шлака использовался доменный гранулированный шлак Новолипецкого металлургического комбината (НЛМК), соответствующий требованиям ГОСТ 3476-76 «Шлаки доменные и электротермофосфорные гранулированные для производства цементов». Химический состав шлака НЛМК представлен в табл. 1.
|
|
|
|
|
|
|
Таблица 1 |
|
|
|
|
Химический состав шлака НЛМК |
|
|
|||
|
Содержание оксидов фактическое (рекомендуемое), % |
|
||||||
SiO2 |
Al2O3 |
FeO |
MnO |
CaO |
MgO |
SO3 |
TiO2 |
|
38,6 |
8,6 |
0,7 |
1,1 |
42,0 |
7,2 |
0,1-1,5 |
не |
|
(не более |
отмечено |
|||||||
(35- |
(не менее |
(0,5- |
(не более |
(не более |
(0,5- |
|||
42,0- |
(не более |
|||||||
40) |
8,0) |
1.0) |
4,0) |
15,0) |
1,5) |
|||
44,0) |
4,0) |
|||||||
|
|
|
|
|
|
По химическому составу шлак отвечает предъявляемым требованиям. Данный шлак характеризуется модулем основности Мо=1,04, модулем активности Ма=0,22 и коэффициентом качества К =1,5, что позволяет сделать вывод о его достаточно высокой гидратационной активности.
В качестве щелочного активатора выступала техническая сода, соответствующая требованиям ГОСТ 5100-85 «Сода кальцинированная техническая. Технические условия».
Полученное совместным помолом шлака и кальцинированной соды вяжущее характеризуется следующими показателями:
-удельная поверхность – 430-460 м2/кг;
-нормальная густота теста – 25-30 %;
-сроки схватывания: начало – не ранее 40 мин;
-окончание – не позднее 3 ч;
-водородный показатель рН – 12,5.
На основе ШЩВ готовился раствор в соотношении «вяжущее : песок» 1:3. К сухим компонентам добавлялась вода из расчета получения смеси нормальной консистенции после 30 встряхиваний в течение 30 с на встряхивающем столике. Смесь перемешивалась с водой в течение 1 мин. Далее из полученной смеси формовались стандартные образцы-балочки размером 4×4×16 см, которые уплотнялись на виброплощадке в течение 1,5-2 мин, проходили предварительную выдержку перед ТВО в течении 4 ч и подвергались тепловлажностной обработке в пропарочной камере по режиму 2+8+2 ч при температуре 95±5 оС. После прохождения тепловой обработки образцы испытывались для определения основных физико-механических характеристик, результаты которых представлены в табл. 2.
Из данных табл. 2 отмечаем высокие физико-механические характеристики ШЩВ. Предел прочности при сжатии после ТВО составляет 492 кгс/см2, что составляет около 70 % от марочной прочности. Поэтому можно сделать предварительный вывод о том, что на
122
Научный Вестник Воронежского государственного архитектурно-строительного университета
основе данного вяжущего можно получать цементы марок М500 и М600, а также растворы и бетоны с высокими эксплуатационными характеристиками. ШЩВ обладает незначительным водопоглощением (меньше 3 %) и высоким коэффициентом размягчения, что говорит о возможности эксплуатации изделий и конструкций на основе данного вяжущего в водной среде.
Очень важной с точки зрения области применения данного вяжущего является оценка стойкости в агрессивных средах. Оценку стойкости ШЩВ к действию агрессивных сред проводили согласно требованиям ГОСТ [16, 17]. В работе метод испытания был основан на определении химической стойкости образцов шлакощелочного раствора состава 1:3 по изменению массы и прочности после выдержки в агрессивной среде в течение контрольного периода времени. Определение относительной стойкости ШЩВ при воздействии химически агрессивных сред проводили в растворе серной кислоты концентрацией 0,5 % (рН = 2,0). Образцы хранились в агрессивной среде, а контрольные образцы – в воде в течение 20 суток. После проведения испытаний образцы осматривали, взвешивали и фиксировали изменения массы, а также определяли пределы прочности при сжатии.
Не менее важным является способность материала выдерживать циклические воздействия увлажнения и высушивания без заметных деформаций и потери механической прочности. Этот показатель носит название атмосферостойкости или воздухостойкости. Известно, что многократное увлажнение и высушивание вызывает в материале знакопеременные напряжения и со временем приводит к потере им несущей способности. Для любого материала показатель атмосферостойкости является важным критерием с точки зрения долговечности.
В работе атмосферостойкость ШЩВ оценивали путем долговременного сопротивления разрушающему действию влаги при периодическом увлажнении и высушивании материала. Из ШЩВ изготовлялись образцы-балочки размером 4×4×16 см.
Образцы проходили тепловлажностную обработку по режиму 4+(2+8+2) ч при температуре
95±5 оС.
После ТВО образцы подвергались испытанию на атмосферостойкость. Цикл испытаний образцов осуществляли следующим образом. Сначала образцы насыщали водой в течение 4 ч, затем их помещали в сушильный шкаф, где при температуре 105-110 оС высушивали в течение 19 ч, а затем охлаждали на воздухе 1 ч и снова погружали в воду. Через 20 циклов испытаний образцы осматривали, измеряли массу и определяли предел прочности при изгибе и сжатии. Оценку атмосферостойкости материала проводили по потере массы и изменению прочности.
|
|
|
|
|
|
|
Таблица 2 |
|
|
|
|
Физико-механические характеристики ШЩВ |
|
|
|||
|
|
|
|
|
|
|
|
|
Состав смеси на 1 л |
|
Физико-механические свойства |
|
|
||||
|
|
|
|
|
|
|
|
|
|
|
|
Средняя |
Предел |
Предел |
|
|
|
ШЩВ, |
Песок, |
Вода, |
прочности |
Водопоглоще- |
Коэффициент |
|
||
плотность, |
прочности при |
|
||||||
г |
г |
мл |
при сжатии, |
ние по массе, % |
размягчения |
|
||
кг/м3 |
изгибе, МПа |
|
||||||
|
|
|
|
|
МПа |
|
|
|
500 |
1500 |
200 |
2425 |
8,4 |
49,2 |
2,96 |
0,995 |
|
|
|
|
|
|
|
|
|
|
123
Научный Вестник Воронежского государственного архитектурно-строительного университета
Результаты определения химической стойкости и атмосферостойкости ШЩВ приведены в табл. 3 и 4.
|
|
|
|
|
|
Таблица 3 |
|
|
|
Химическая стойкость ШЩВ |
|
|
|||
|
|
|
|
|
|
|
|
|
Испытания после |
Испытания после выдерживания |
|||||
Время |
выдерживания в воде |
в Н2SO4 (0,5 %, pH=2) |
|
||||
|
Предел |
|
|
|
|
||
выдерживания |
Прирост массы |
Прирост массы |
Потеря |
Предел |
|
||
прочности |
Коэффициент |
||||||
в агрессивной |
по отношению к |
по отношению к |
или |
прочности |
|||
среде, сут |
первоначальной, |
при |
первоначальной, |
прирост |
при сжатии, |
стойкости, |
|
сжатии, |
Кст |
||||||
|
г |
г |
массы, % |
МПа |
|||
|
МПа |
|
|||||
|
|
|
|
|
|
||
20 |
4,7 |
48,2 |
9,0 |
+0,74 |
46,5 |
0,96 |
|
|
|
|
|
|
|
|
Таблица 4
Атмосферостойкость ШЩВ
|
|
|
|
Результаты |
|
|
|
||
Количество циклов |
До испытания |
|
|
После 20 циклов испытания |
|
||||
|
|
|
|
|
|
|
|
|
|
увлажнения и |
|
Предел |
|
|
|
|
Предел |
|
|
|
|
|
|
|
|
|
|
||
высушивания |
Масса, |
прочности |
Масса, |
|
|
|
|
||
m, % |
|
прочности при |
|
R, % |
|||||
г |
при сжатии, |
г |
|
|
|
||||
|
|
|
|
||||||
|
|
|
|
сжатии, МПа |
|
|
|||
|
|
МПа |
|
|
|
|
|
|
|
|
|
|
|
|
|
|
|
|
|
20 |
587,8 |
49,2 |
557,3 |
- 5,19 |
|
66,1 |
|
+34,0 |
|
|
|
|
|
|
|
|
|
|
|
Полученные данные (табл. 3) позволяют судить о достаточно высокой стойкости ШЩВ в 0,5 %-ном растворе серной кислоты. Для химически стойких бетонов коэффициент стойкости должен быть более 0,8.
Из представленных данных (табл. 4) видно, что после 20 циклов попеременного увлажнения и высушивания образцов из ШЩВ при незначительном уменьшении массы (5,2 %) происходит значительное упрочнение их структуры. На наш взгляд это связано с продолжающимися процессами гидратации шлакощелочного вяжущего. Можно предположить, что данные процессы будут протекать и далее (как в классических портландцементах) и давать положительный эффект.
Важным аспектом любого гидравлического вяжущего является возможность его применения в железобетонных конструкциях. Поэтому в работе были исследованы защитные свойства бетона на основе ШЩВ по отношению к арматуре. Были рассмотрены основные виды атмосферных воздействий, оказывающих агрессивное воздействие на стальную арматуру в бетоне. Среди данных видов воздействий были изучены: попеременное увлажнение и высушивание (атмосферостойкость), воздействие СО2 (карбонизационная стойкость) и длительная водостойкость.
При проведении испытаний для всех видов воздействий эксплуатационных сред изготовляли армированные образцы-балочки размером 4×4×16 см из шлакощелочного раствора с соотношением вяжущего и песка 1:3 и водо-вяжущим отношением равным 0,4.
Толщину защитного слоя бетона до арматуры назначили минимальной и равной 20 мм. Арматурные стержни до укладки в формы отшлифовывали, обезжиривали и взвешивали на аналитических весах. Диаметр арматуры измеряли штангенциркулем.
После набора прочности образцы подвергали испытанию на атмосферостойкость, карбонизационную стойкость и длительную водостойкость. Совместно с образцами
124

Научный Вестник Воронежского государственного архитектурно-строительного университета
испытания проходили арматурные образцы-спутники – арматурная сталь того же диаметра и класса без защитного слоя бетона.
Оценку защитных свойств вели по потере массы металла арматуры в сравнении с образцами-спутниками, помещенными в ту же среду, но без защитного слоя бетона.
Результаты определения защитных свойств представлены в табл. 5.
Таблица 5
Результаты определения защитных свойств бетона на основе ШЩВ по отношению к арматуре
|
Степень коррозии арматуры по изменению массы, |
|
|
m, % |
|
Вид испытаний |
|
В защитном слое бетона |
|
Без защитного слоя бетона |
на основе шлакощелоч- |
|
|
ного вяжущего |
Атмосферостойкость (20 циклов) |
1,20 |
0,41 |
Карбонизационная стойкость (30 суток) |
0,70 |
0,17 |
Водостойкость (30 суток) |
1,90 |
0,73 |
Полученные данные показывают, что в бетонах, изготовленных на основе шлакощелочного вяжущего, стальная арматура будет надежно защищена от воздействий, вызывающих коррозионные процессы. Арматура в конструкциях не показывает признаков коррозии при переменном увлажнении и высушивании, при карбонизационном воздействии и при эксплуатации в водной среде.
Подбор состава бетона. В соответствии с нормативной документацией был подобран состав тяжелого бетона на основе ШЩВ. В качестве мелкого и крупного заполнителей применялись местный овражный кварцевый песок и гранитный щебень фракции 5-20 мм Павловского месторождения.
Состав бетона и полученные основные характеристики приведены в табл. 6.
Таблица 6 Рекомендуемый состав тяжелого бетона на основе ШЩВ и его характеристики
|
Состав смеси на 1 м3 |
|
Марка по |
|
Свойства |
|
|||
|
|
|
|
|
|
Предел |
|
|
|
|
|
|
Щебень |
|
удобоук- |
Средняя |
|
Марка по |
|
ШЩВ, |
|
Песок, |
Вода |
прочности |
Класс |
||||
|
фракции |
ладывае- |
плотность, |
морозостой- |
|||||
кг |
|
кг |
, л |
при сжатии, |
бетона |
||||
|
5-20 мм, кг |
мости |
кг/м3 |
кости |
|||||
|
|
|
|
|
|
|
МПа |
|
|
420 |
|
675 |
1350 |
200 |
П1 |
2440 |
43,6 |
В30 |
F50 |
|
|
|
|
|
|
|
|
|
|
Полученные на основе шлакощелочного вяжущего бетоны обладают высокими физико-механическими свойствами, что находит отражение в показателях средней плотности и прочности. Отмечаем также высокую морозостойкость (не менее 50 циклов попеременного замораживания и оттаивания).
На основе шлака НЛМК можно получать качественные конструкционные бетоны с достаточно высокими эксплуатационно-техническими характеристиками. При этом в качестве связующего вещества применяется более дешевое шлакощелочное вяжущее.
Выводы. Выполненные экспериментальные исследования позволяют сделать следующие выводы.
1.Доказана возможность применения шлакощелочного вяжущего на основе шлаков НЛМК.
2.Шлакощелочное вяжущее, полученное совместным помолом высушенного доменного гранулированного шлака и кальцинированной соды в соотношении % по массе:
125
Научный Вестник Воронежского государственного архитектурно-строительного университета
шлак – 95, сода – 5, имеет удельную поверхность 430-460 м2/кг.
3.Установлено, что предел прочности при изгибе ШЩВ составляет 8,4 МПа, предел прочности при сжатии – 49,2 МПа.
4.ШЩВ является водостойким материалом (коэффициент размягчения 0,995) и может применяться как в воздушно-сухих, так и во влажностных условиях эксплуатации.
5.Стойкость ШЩВ в растворе серной кислоты концентрацией 0,5 % в течение 20 суток характеризуется коэффициентом стойкости равным 0,96.
6.Атмосферостойкость ШЩВ, оцениваемая после 20 циклов переменного увлажнения и высушивания, характеризуется приростом прочности на 34,0 %.
7.Исследованиями, проведенные с целью определения сохраняемости арматуры в ШЩВ, установлено, что показатели потерь массы стержней после пребывания в течении 20
и30 суток в бетонах, находящихся в различных условиях эксплуатации, составляет от 0,7 до 1,9 %. Это говорит о том, что арматура хорошо сохраняется в бетоне вследствие наличия щелочной среды (рН=12), которая обусловливает отсутствие процессов окисления и коррозии.
8.Подобран оптимальный состав бетона с использованием традиционных заполнителей и шлакощелочного вяжущего (420 кг/м3), обладающий средней плотностью 2440 кг/м3, классом по прочности В30 (М400), морозостойкостью не ниже F50.
Список литературы
1.Комар А.Г. Опыт использования отходов промышленности в строительстве // Изв. вузов. Строительство, 1997. – С. 49-50.
2.Цыганков В.Н. Использование шлаков металлургического производства для строительства природоохранных объектов // Матер. V междунар. конгресса по управлению отходами и природоохранными технологиями. – М.: ВэйстТэк, 2007.
3.Черепанов К.А. Утилизация вторичных материальных ресурсов в металлургии: Учеб. пособие для вузов. – М.: Металлургия, 1994. – 344 с.
4.Долгопол В.И. Использование шлаков черной металлургии. – М.: Металлургия, 1978. – 256 с.
5.Бутт Ю.М., Майер А.А., Варшал Б.Г. Металлургические шлаки и применение их в строительстве // Сб. трудов. – М.: Госстройиздат, 1962. – 288 с.
6.Данилов Б.П., Бородицкая Р.М., Попов В.В. Применение шлаковых вяжущих в производстве сборного железобетона. – Киев.:Будивельник, 1964. – 88 с.
7.Горшков B.C., Александров С.Е., Иващенко С.И., Горшкова И.В. Комплексная переработка и использование металлургических шлаков в строительстве. – М.:Стройиздат, 1985. – 273 с.
8.Маясова Л.А. Исследование свойств шлакощелочных вяжущих и бетонов на основе ваграночных шлаков: автореф. дис.... канд. техн. наук. - Киев, 1979. – 23 с.
9.Мирюк О.А., Ахметов И.С. Оценка техногенного сырья для получения вяжущих веществ // Строительные материалы. – 2002. - № 9. – С. 7-9.
10.Сухапов М.А., Ефимов С.И., Долгополов Н.Н., Жуков Н.Ю. Новые пути использования отходов металлургической и энергетической промышленности в технологии вяжущих // Строительные материалы. – 1991. - № 7. – С. 22-23.
11.Ицкович С.М., Балашевич В.А., Богдан В.А., Тихомиров И.Н. Отходы металлургии – строительству. – Минск: Полымя, 1973. – 56 с.
12.Глуховский В.Д., Ростовская Г.С. Исследование и внедрение в производство шлакощелочных вяжущих, бетонов и конструкций на их основе. – К.: Знание, 1979. – 253 с.
13.Калашников В.И. Стеновые материалы на основе шлаковых композитов // Матер. Всерос. науч.-технич. конф. – Томск, 1998. – 276 с.
126

Научный Вестник Воронежского государственного архитектурно-строительного университета
14.Волженский А.В., Буров Ю.С., Виноградов Б.П., Гладких К.В. Бетоны и изделия из шлаковых и зольных материалов. – М.: Стройиздат, 1969. – 273 с.
15.Хвастунов В.Л. Экспериментально-теоретические основы получения композиционных вяжущих и строительных материалов из шлаков и высокодисперсных горных пород: дис…. д-ра техн. наук. – Пенза: 2005. – 534 с.
16.ГОСТ 25246-82. Бетоны химически стойкие. Технические условия. – М.: Изд-во стандартов, 1983. – 8 с.
17.ГОСТ 25881-83. Бетоны химически стойкие. Методы испытаний. – М.: Изд-во стандартов, 1984. – 14 с.
Усачев Сергей Михайлович - к.т.н., доцент кафедры технологии строительных материалов, изделий и конструкций Воронежского ГАСУ. Тел.: (473) 271-59-26.
Усачев Александр Михайлович - к.т.н., доцент кафедры технологии строительных материалов, изделий и конструкций Воронежского ГАСУ. E-mail: u00066@vgasu.vrn.ru. Тел.: (473) 271-52-35.
Дроздов Олег Михайлович - магистрант кафедры технологии строительных материалов, изделий и конструкций Воронежского ГАСУ.
127

Научный Вестник Воронежского государственного архитектурно-строительного университета
УДК 539.2:669.782
А.А. Лукин, А.К. Тарханов, О.А. Лукин
ИССЛЕДОВАНИЯ СТРУКТУРЫ И ФАЗОВОГО СОСТАВА ПОВЕРХНОСТНОГО СЛОЯ ПРИ ЦЕМЕНТАЦИИ
В работе исследовался фазовый состав поверхностных слоев после цементации в сталях 20 и 20Х. Установлено влияние исходного структурного состояния на структуру и свойства стали 20Х, упрочненной по различным режимам ХТО.
Ключевые слова: фазовый состав, текстура, рассеяние текстуры, полюсная фигура, феррито-перлитная структура
А.А. Лукин, А.К. Тарханов, О.А. Лукин
RESEARCH OF STRUCTURE AND PHASE COMPOSITION THE SURFACE LAYER DURING CEMENTATION
In the work we investigated the phase composition of the surface layers after cementation in steels 20 and 20X. It is the effect of the initial structural state of the structure and properties of steel 20X, hardened by different modes HTO.
Keywords: phase composition, texture, texture scattering, pole figure, ferrite-pearlite structure
Введение. Актуальными в настоящее время являются вопросы повышения надѐжности и долговечности машин, приборов, установок, повышение их качества и эффективности работы, а, следовательно, вопросы экономии металлов, борьбы с коррозией и износом деталей машин. Роль этих проблем особенно возросла в настоящее время, так как развитие большинства отраслей промышленности (авиационная, ракетная, теплоэнергетика, атомная энергетика, радиоэлектроника и др.) связано с повышением нагрузок, температур, агрессивности сред, в которых работает деталь. Решение этих проблем, прежде всего, связано с упрочнением поверхностных слоѐв изделий.
Изменить свойства поверхности можно различными способами: нанесением на поверхность нового материала с необходимыми свойствами; изменением состава поверхностного слоя металла.
Во втором случае поверхностные слои металла подвергают диффузионной химикотермической обработке (ХТО), в результате которой на поверхности изделия образуется новый, отличающийся от сердцевины, сплав.
Химико-термическая обработка позволяет получить в поверхностном слое изделия сплав практически любого состава и, следовательно, обеспечить комплекс необходимых свойств – физических, химических, механических и других [1].
Одним из распространѐнных методов ХТО является цементация. Процесс цементации широко применяют в промышленности благодаря его высокой эффективности и доступности. Он позволяет создавать на рабочей поверхности детали слой, обладающий высокой твѐрдостью после закалки, износостойкостью, эрозионной стойкостью, контактной выносливостью и усталостной прочностью при изгибе. Эти свойства обеспечиваются при относительно мягкой и вязкой сердцевине, придающей детали необходимую конструктивную прочность.
© Лукин А.А., 2013
128
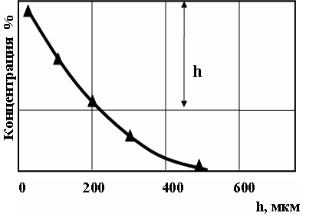
Научный Вестник Воронежского государственного архитектурно-строительного университета
Теоретическая часть. Для цементации применяются низкоуглеродистые и легированные стали с содержанием углероде 0,1-0,3 %. Выбор таких сталей необходим для того, чтобы сердцевина изделия, не насыщающаяся углеродом при цементации, сохраняла высокую вязкость после закалки [2].
В работе исследовались стали 20 и 20Х, химический состав которых представлен в табл. 1.
Таблица 1
Химический состав сталей 20 и 20Х
Cталь |
|
С |
|
Si |
|
Mn |
Cr |
S |
|
P |
|
Cu |
|
Ni |
|
As |
|
|
|
|
|
|
|
|
|
|
|
|
|
|
|
|
|
|
|
|
|
|
|
|
|
|
|
не более |
|
|
|
|
|
|
|
|
|
|
|
|
|
|
|
|
|
|
|
|
|
|
|
20 |
|
0,17-0,24 |
|
0,17-0,35 |
|
0,35-0,65 |
0,25 |
0,04 |
|
0,035 |
|
0,25 |
|
0,25 |
|
0,08 |
|
|
|
|
|
|
|
|
|
|
|
|
|
|
|
|
|
20Х |
|
0,17-0,23 |
|
0,17-0,35 |
|
0,5-0,8 |
0,7-1,0 |
0,035 |
|
0,035 |
|
0,3 |
|
0,3 |
|
- |
|
|
|
|
|
|
|
|
|
|
|||||||
|
При цементации происходит, поверхностное насыщение стали углеродом, в |
|||||||||||||||
результате чего образуется высокоуглеродистый поверхностный слой [3]. |
|
|
|
|
|
|||||||||||
|
В |
результате |
диффузии |
на поверхности |
металла |
образуется |
максимальная |
концентрация диффундирующего элемента, которая понижается по мере удаления от поверхности.
Рис. 1. Распределение диффундирующего элемента по мере удаления от поверхности
Глубина диффузионного слоя, характеризуется величиной «h», которая прямо пропорционально зависит от температуры и времени процесса, концентрации диффундирующего элемента на поверхности.
С целью установления причин недостаточной стойкости рабочих элементов прессового инструмента и последующей корректировки существующих параметров упрочняющей обработки исследовали структуру и твердость (рис. 2) образцов прессформ, изготовленных из листовой стали 20Х после обработки по следующим режимам [4].
В настоящей работе исследовался фазовый состав поверхностных слоев после цементации на сталях 20 и 20Х. Съемка велась в излучении трубки с железным и хромовым анодом на дифрактометре ДРОН-2,0 и в камере РКД.
Обсуждение результатов. Дифрактограмма образца после цементации, содержит много взаимоналагающихся дифракционных максимумов от карбидов (Fe,Cr)7C3 ,(Fe,Cr)23C6, Fe3С, а также от α-Fe. Толщина слоя, участвующего в формировании дифрактограммы в
129
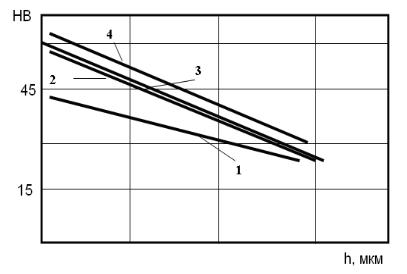
Научный Вестник Воронежского государственного архитектурно-строительного университета
данных условиях съемки, не превышает 25 мкм. Поэтому проводилось послойное удаление шлифовкой цементованного слоя по 25 мкм.
|
Таблица 2 |
|
Режимы цементации |
|
|
Режимы |
Виды операций |
|
|
Режим 1. |
Цементация в твердом карбюризаторе при температуре 920-950 оС с |
|
выдержкой 10-12 часов, охлаждение на воздухе. |
|
|
Режим 2. |
Закалка с цементационного нагрева после подстуживания до 870 оС. |
|
|
Режим 3. |
Закалка с цементационного нагрева после подстуживания до 800 оС. |
|
|
Режим 4. |
Обработка по режиму 2 + закалка с отдельного нагрева до 800 оС. |
|
|
Режим 5. |
Отжиг при 870 оС перед цементацией, цементация с последующим |
|
охлаждением на воздухе, закалка с отдельного нагрева от 800 оС. . |
|
|
Режим 6. |
Закалка от 870 оС перед цементацией, цементация с последующим |
|
охлаждением на воздухе, закалка с отдельного нагрева от 800 оС |
|
|
Рис. 2. Изменение твердости (НВ) при различных режимах цементации
Карбиды (Fe,Cr)7C3, (Fe,Cr)23C6 и Fe3С наблюдаются во всем цементованном слое, и исчезают на глубине около 2-х мм, а также от α-Fe. На этой глубине обнаруживается только феррит.
Результаты рентгеноструктурных исследований позволяют предположить, что снижение твердости стали, закаленной с цементационного нагрева, может быть связано с повышенным содержанием остаточного аустенита в поверхностном слое. При изучении структуры цементованного слоя после закалки с цементационного нагрева было выявлено наличие крупнозернистой структуры со средним размером зерна 70 мкм. Проведение закалки с отдельного нагрева привело к получению более дисперсной структуры аустенита со средним размером зерна 10-15 мкм. Анализ распределения зерен аустенита по размерам, показывает, что более мелкое и более равномерное зерно аустенита в цементованном слое формируется после двойной закалки.
В связи с тем, что плиты прессформ изготавливаются из листа, в том числе полученного и контролируемой прокаткой, в исходном состоянии металл характеризуется
130