
Корпоративные информационные системы
..pdf♦ особенности работы с опасными материалами, условия их краткосрочного и долгосрочного хранения.
Результаты ЛА представляются в форме реляционной базы данных.
Контрольные вопросы к главе 4
1.Каково значение PDM в структуре CALS?
2.ИЛП и оптимизация стоимости ЖЦИ.
3.Связь ЖЦИ и ИЛП.
4.Каково основное назначение логистического анализа?
5.Разбиение ЛА на группы задач.
6.Охарактеризовать пригодность ЛА к поддержке.
201
5. СОСТАВЛЯЮЩИЕ МОДУЛИ ИНФОРМАЦИОННОЙ ТЕХНОЛОГИИ
5.1. MRP – СТАНДАРТ ПЛАНИРОВАНИЯ МАТЕРИАЛЬНЫХ
РЕСУРСОВ
В результате поиска решений в области автоматизации производственных систем родилась парадигма планирования потребностей в материалах (MRP). Следует отметить, что этот подход использовался на нескольких предприятиях в Европе еще до начала Второй мировой войны, но не в компьютерном варианте. MRP – это метод эффективного планирования всех ресурсов производственного предприятия. В идеале он позволяет осуществлять производственное планирование в натуральных единицах измерения, финансовое планирование – в стоимостных единицах измерения и предоставляет возможность осуществлять моделирование с целью ответа на вопросы типа «что будет, если…?».
Цель планирования потребностей в материалах – так спланировать поставку всех комплектующих, чтобы исключить простои производства и минимизировать запасы на складе. Уменьшение запасов материалов/комплектующих, кроме очевидной разгрузки складов и уменьшения затрат на хранение дает ряд неоспоримых преимуществ, главное из которых – минимизация замороженных средств, вложенных в закупку материалов, не сразу идущих на конвейер, аподолгудожидающихся своейучасти.
Концепция MRP-системы фактически сводится к двум основным принципам:
♦если есть потребность в конечном изделии, то есть потребность во всех составляющих его компонентах, то есть MRP системы ориентированы на удовлетворение зависимого спроса;
♦обеспечивать производство требующимися компонентами нужно как можно позднее, чтобы сократить уровень запасов
202
с целью сокращения складских расходов и эффективного использования активов предприятия.
MRP-системы помогают достичь следующих целей одновременно:
♦проверить, что материалы и изделия доступны для производства или доставки заказчикам;
♦управлять наименьшим возможным уровнем инвента-
ризации;
♦планировать производственные процессы, поставки
изакупки.
Главной задачей MRP является гарантированное обеспечение необходимым количеством требуемых материалов в любой момент времени в рамках срока планирования, наряду с возможным уменьшением постоянных запасов, а следовательно, разгрузкой склада. Это обеспечивается формированием такой последовательности производственных операций, которая позволяет соотносить своевременное изготовление продукции с заложенным планом выпуска.
Входными элементами MRP являются:
♦описание состояния материалов (Inventory Status File).
Отражается в соответствующих таблицах БД. Этот элемент является основным входным элементом MRP-модуля. В нем должна быть отражена максимально полная информация о всех типах сырья, материалах и комплектующих, необходимых для производства конечного продукта. В этом элементе должен быть указан статус каждого материала, определяющий, имеется ли он на руках, на складе, в текущих заказах или его заказ только планируется, а также описания его запасов, расположения, цены, возможных задержек поставок, реквизитов поставщиков. Информация по всем вышеперечисленным позициям должна быть заложена отдельно по каждому материалу, участвующему в производственном процессе;
♦данные о потребности в изделиях независимого спроса.
Заинтересованность в получении тех или иных номенклатурных позиций (готовые изделия, запасные части, продаваемые на сторону полуфабрикаты и комплектующие и т.п.) проявляет непосредственно потребитель продукции предприятия. Потребность может быть представлена или прогнозом продаж, или уже имеющимися в наличиизаказамипокупателей, или итемидругимодновременно;
203
♦программа производства MPS (Master Production Schedule). Этот элемент представляет собой оптимизированный график распределения времени для производства необходимой партии готовой продукции за планируемый период или диапазон периодов. Информация о прогнозах продаж и заказах на продажу является основанием для формирования главного календарного плана производства, охватывающего все включаемые в план производства номенклатурные позиции. MPS формируется как в объемном, так и в календарном исполнении. В отечественной терминологии соответствующий документ имеет название «Главный план-график производства». Разработка производственного плана, как правило, является итерационным процессом. Первоначально формируется черновой вариант производственного плана для оценки возможности его реализации по имеющимся производственным мощностям. После проведения необходимых итераций план утверждается как действующий и его данные поступают на вход системы планирования;
♦перечень составляющих конечного продукта BOM
(Bills of Material File). Спецификация изделия, за которую отвечает конструкторский отдел. Этот элемент представляет собой номенклатурный перечень запасов продукции, сборочных единиц, материалов и их количество, требуемое для производства конечного продукта, а также информация об открытых заказах. При этом очень важную роль играет время. Для того чтобы учитывать время, системе необходимо знать технологию выпуска продукции (или технологическую цепочку, т.е. последовательность операций
иих продолжительность). На основании плана выпуска продукции, BOM и технологической цепочки осуществляется расчет потребностей в материалах, привязанный к конкретным срокам.
При решении задачи учитываются не только запасы готовой продукции, отгружаемой на сторону, и сырья, закупаемого у поставщиков, но и запасы номенклатурных позиций всех промежуточных стадий производства продукции (полуфабрикаты собственного изготовления, сборочные единицы, узлы и т.п.).
Таким образом, каждый конечный продукт имеет свой перечень составляющих. Кроме того, здесь содержится описание структуры конечного продукта, т.е. перечень содержит в себе полную информацию по последовательности его сборки. Чрезвычайно важ-
204
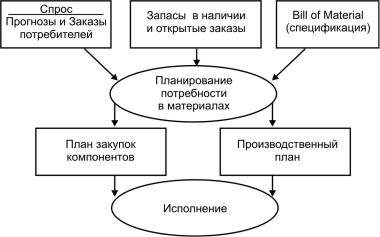
но поддерживать точность всех записей в этом элементе и соответственно корректировать их всякий раз при внесении изменений в структуру и\илитехнологию производстваконечногопродукта.
Каждый из вышеуказанных входных элементов представляет собой компьютерный файл данных, использующийся MRPпрограммой. В настоящий момент MRP-системы реализованы на самых разнообразных аппаратных платформах и включены в качестве модулей в большинство финансово-экономических систем.
Информационные элементы MRP-системы как компьютерной программы логически могут быть представлены в виде диаграммы, приведенной на рис. 5.1.
Рис. 5.1. Планирование потребности в материалах
Метод MRP позволял обеспечивать компоненты, требуемые в соответствии с планом производства конечной продукции (на сегодняшний день «основной план производства») точно в том количестве и в те сроки, которые требовались для изготовления конечных изделий.
Собственно методология MRP является реализацией двух известных принципов JIT (Just In Time – вовремя заказать) и KanBan (вовремя произвести). JIT – это система управления материалами впроизводстве, при которой компоненты с предыдущей операции
205
(или от внешнего поставщика) доставляются именно в тот момент, когда они требуются, но не раньше. Партии компонентов настолько малы, насколько это возможно (это зависит от времени выполнения
истабильности цикла доставки). Наибольший успех система JIT имеет на предприятиях среднего масштаба с серийным типом производства, где стандартные изделия производятся с высокой скоростью с непрерывным потоком материалов и комплектующих. В данной ситуации процедуры планирования и контроля в достаточной степени стандартизованы и просты. На крупных, высокотехнологичных предприятиях, где процедура планирования и контроля производственных процессов является сложной, JIT практически не используется.
После появления концепции MRP, казалось бы, все основные проблемы производства были решены, активно создавались
ипродавались компьютерные программы, реализующие ее нехитрые принципы. Однако в процессе дальнейшего анализа существующей ситуации в мировом бизнесе и ее развития выяснилось, что всю большую составляющую себестоимости продукции занимают затраты, напрямую не связанные с процессом и объемом производства.
5.2.ОСНОВНЫЕ ОПЕРАЦИИ, ДОСТОИНСТВА
ИНЕДОСТАТКИ MRP-СИСТЕМЫ
На основании входных данных MRP-система выполняет следующие основные операции:
♦MRP-система, анализируя принятую программу производства, определяет оптимальный график производства на планируемый период;
♦по данным MPS определяется количество конечных изделий для каждого периода времени планирования;
♦формируется описание потребности предприятия в произ-
водимых и закупаемых номенклатурных позициях, выраженное ввиде календарного плана. MRP формирует два массива сообщений:
плановые заказы (Planned Orders) и рекомендации (Action Messages).
Материалы, не включенные в производственную программу, но при-
206
сутствующие в текущих заказах, включаются в планирование как отдельныйпункт;
♦на основе утвержденной программы производства и заказов на комплектующие, не входящие в нее, для каждого отдельно взятого материала вычисляется полная потребность в соответствии с перечнем составляющих конечного продукта. Общая потребность материалов корректируется с учётом состояния запасов для каждого периода времени планирования;
♦к составу конечных изделий добавляются запасные части, не включённые в MPS;
♦на основе полной потребности, учитывая текущий статус материала, для каждого периода времени и для каждого материала вычисляется чистая потребность, по указанной формуле. Если чистая потребность в материале больше нуля, то системой автоматически создается заказ на материал с учётом необходимого времени опережения;
♦все заказы, созданные ранее текущего периода планирования, рассматриваются и в них при необходимости вносятся изменения, чтобы предотвратить преждевременные поставки и задержки поставокотпоставщиков.
Таким образом, в результате работы MRP-программы производится ряд изменений в имеющихся заказах и при необходимости создаются новые для обеспечения оптимальной динамики хода производственного процесса. Эти изменения автоматически модифицируют описание состояния материалов, так как создание, отмена или модификация заказа соответственно влияет на статус материала, к которому он относится.
Результатом работы MRP-системы является план-график (Planned Order Schedule) снабжения материальными ресурсами производства (потребность каждой учётной единицы материалов
икомплектующих для каждого периода времени). Для реализации план-графика снабжения система создаёт график заказов в привязке к периодам времени. Он используется для размещения заказов поставщикам материалов и комплектующих или для планирования самостоятельного изготовления с возможностью внесения корректировок в процессе производства. Системы класса MRP по соотношению цена – качество подходят для небольших предприятий, где функции управления ограничиваются учётом
207
(бухгалтерским, складским, оперативным), управлением запасами на складах и управлением кадрами.
Производители, которые успешно внедрили систему MRP, имеют:
♦уменьшенные складские запасы;
♦уменьшенное время выхода на рынок новых продуктов;
♦увеличение прибыльности.
Явным недостатком на данном этапе развития технологии MRP была невозможность обновить итоговую информацию, получаемую в ходе работы MRP, т.е. подстроиться под изменения, возникающие в случае открытых заказов. Из-за этого первые MRPсистемы называли «запустил и забыл» (launch and forget). Однако возможность обновления очень важна, так как среда, в которой используется MRP, весьма динамична, а частые изменения размеров заказов и сроков их выполнения не являются редкостью. Отсюда вытекает необходимостьотслеживатьтекущее состояниедел.
Следует учитывать, что в то время преобладал пакетный тип обработки информации на удаленных вычислительных центрах (кустовых или корпоративных). Интерактивные технологии еще не получили развития, и анализ «а что будет, если…» практически не проводился. По сути, MRP просто фиксировала ситуацию в «развернутом» виде.
5.3.СИСТЕМA MRP (CLOSED-LOOP MRP)
ВЗАМКНУТОМ ЦИКЛЕ
Изобретение менее дорогостоящих вычислительных систем реального времени и опыт работы с MRP I привели к разработке вконце 70-х систем MRP в замкнутом цикле (Closed-loop MRP), которые нашлив настоящеевремяширокое применение.
MRP в замкнутом цикле – это система, построенная на основе MRP, которая включает дополнительные функции планирования: планирование производства, планирование требуемой мощности с формированием основного плана производства. Под «замкнутым циклом» подразумевается обратная связь по состоянию выполнения, что позволяет убедиться в том, что план является действительным.
208

Основная идея данного усовершенствования технологии MRP заключается в создании замкнутого цикла путем налаживания обратных связей, улучшающих отслеживание текущего состояния производственной системы. Информация передается обратно через вычислительную систему, но при этом никакие действия не предпринимаются. Принятие решения о корректировке плана остается за человеком. Дополнительная реализация мониторинга выполнения плана снабжения и производственных операций позволила снять ограничения степени достоверности результата планирования, ранее присущие MRP I, которые существовали из-за невозможности отследить состояние открытых заказов. Отличие MRP I/CRP от Closed-loop MRP хорошо поясняется схемой на рис. 5.2.
Рис. 5.2. Сравнение MRP I/CRP и Замкнутого цикла MRP
Возникшая в конце 1960-х г. технология MRP затем была расширена до более общей технология планирования производственных ресурсов (см. MRP II) и концепции управления ресурсами предприятия (см. ERP).
209
5.4. УПРАВЛЕНИЕ ПРОИЗВОДСТВЕННЫМИ РЕСУРСАМИ
Управление производственными ресурсами (Manufacturing Resource Planning – MRPII) – метод эффективного планирования всех ресурсов предприятия-производителя. На основе производственной программы для каждого вида готового изделия определяют требуемое расписание закупки и/или внутреннего производства всех материалов комплектующих этого изделия, и, соответственно, их сборку.
Этот модуль необходим для расчета потребности во всех номенклатурных позициях, не представляющих собой изделия независимого спроса, потребность предприятия в которых может быть вычислена на основании данных о спросе (в виде прогнозов или заказов) на изделия зависимого спроса, т.е. на те, которые компания реализует контрагентам. К ним относятся материалы, компоненты, детали и т.д. Исторически это был первый разработанный модуль в рамках систем MRP II, а последующая функциональность «наслаивалась» на него. Можно сказать, что данный модуль является ядром любой системы MRP II.
Метод позволяет осуществлять операционное планирование (в единицах продукции), финансовое планирование (в долларах) и моделировать различные ситуации, отвечая на вопросы «что если?». Состоит из набора взаимосвязанных функций, основными из которых являются:
♦бизнес-планирование;
♦планирование производства и продаж;
♦планирование выпуска продукции;
♦составлениеосновногопроизводственногоплана(см. MSP);
♦планирование потребности в материалах (см. MRP);
♦планирование потребности в производственных мощностях (см. CRP);
♦системы поддержки управления производственными мощностями и материалами.
Функция планирования потребности в системе MRP II включает три процесса:
1)планирование потребности в материалах (MRP);
2)планирование потребности в производственных мощно-
стях (CRP);
3)статистическое управление складскими запасами (SIC).
210