
Корпоративные информационные системы
..pdfОбласть А – развитие информационных технологий:
1)использование профессиональных операционных систем (для серверов баз данных) и персональных компьютеров;
2)использование профессиональных систем управления базами данных (СУБД);
3)использование ERP-систем как ядра интегрированной информационной системы предприятия;
4)использование кооперативных технологий, обеспечивающих компьютерную поддержку параллельной согласованной работы группы («команды») сотрудников над одним проектом, документом и т.п.;
5)использование телекоммуникации, позволяющей исключить передачу бумажных документов и личных встреч, свести к минимуму необходимость переездовдляпроведения совещаний;
6)использование систем управления знаниями для организации хранилища и поиска неструктурированных документов.
Область В – развитие бизнес-платформы:
1)методики управления качеством (то есть целостная идеология управленияпредприятием) на базе стандартов ИСО серии 9000
вредакции2000 г.;
2)методики организации операционного менеджмента (ERP-стандарты);
3)методики управления требованиями и конструкторскими разработками (CALS-стандарты);
4)методики моделирования бизнес-процессов (SADT, IDEF0,
DFD, UML).
Область С определяет «психологию труда» и направлена на решение следующих задач:
1)внедрение принципа «Лидерство» (устранение недостатков производственной системы, а не отдельных работников);
2)внедрения принципа «Вовлечение работников» (повышение значимости и инициативности каждого работника);
3)снятие барьеров между производственными подразделениями, организация групповой «артельной работы»; образование так называемых «плоских» рабочих групп, использующих эдхократические (эдхократия – компетентная бюрократия) способы управления, опирающиеся на информационные технологии и организующие динамическое и неформальное распределение прав
311
и обязанностей сотрудников группы (такие группы реактивны, никому не дают монополию на истину, требуют проработки альтернативных решений);
4)формирование корпоративной культуры и повышение эдхократии в организации;
5)внедрение философии тотального управления качеством на всех рабочих местах (TQM);
6)внедрение философии организации производственных процессов «Точно вовремя» на всех рабочих местах (JIT).
В недавнем прошлом руководители отечественных предприятий, осознавая значительные культурные различия между нами и Западом, предполагали, что западные методики не будут работать в России. Однако когда ряд западных фирм открыли свои производства в России и добились успеха на нашем рынке, всем стало ясно, что рассмотренные выше методики могут успешно работать и на отечественных предприятиях.
6.5. МЕТОДОЛОГИЯ MRP
Методология MRP разрабатывалась в 60-х годах прошлого века под влиянием целого комплекса факторов. Послевоенное оживление экономики выдвинуло на повестку дня задачу эффективного управления себестоимостью продукции. В ответ на это активизировались исследования в области математической экономики, которые столкнулись не только с методологическими трудностями, но и с техническими проблемами: нужно было в пределах определенного промежутка времени уметь учитывать огромное множество параметров. С развитием вычислительной техники эти проблемы были преодолены. В результате появились первые автоматизированные системы планирования – системы планирования материальных ресурсов, MRP-системы.
Почему первые системы были ориентированы именно на работу с материалами?
Управление материальными ресурсами – одна из важных областей планирования.
Успешное функционирование промышленного предприятия напрямую зависит от того, насколько хорошо и ритмично
312
оно снабжается сырьем или комплектующими, насколько рационально используются складские площади, и, наконец, насколько тесно объемы выпуска связаны с заказами клиентов или потребностью рынка. Отклонение от оптимального значения любой из этих составляющих приводит к проблемам: перебои с поставками сырья ведут к простоям оборудования и снижению выпуска продукции; поступление большего, чем необходимо, количества материалов может повлечь необоснованные потери в виде избыточных запасов на складах (обычно такие запасы называют «омертвленными затратами»).
Проблема наличия необходимых материалов и комплектующих в нужное время, в нужном месте и в нужном количестве особенно актуальна для массовых сборочных производств, где простои конвейера недопустимы. Именно под такие производства и разрабатывалась методология MRP и соответствующие программные решения.
МетодологияMRP служит для реализацииследующих целей:
♦минимизировать запасы на складах сырья и готовой продукции;
♦оптимизировать поступление материалов и комплектующих в производство и исключить простои оборудования из-за не прибывших вовремя материалов и комплектующих.
В соответствии с этим закупки материалов и комплектующих всего отрезка планирования автоматически распределяются по плановым периодам (например, дням), причем объем и время закупок рассчитываются так, чтобы в каждый плановый период на предприятие поступало именно столько материалов и комплектующих, сколько требуется производству в этом плановом периоде.
6.5.1.Логика работы MRP-модуля: информация на входе и выходе
Остановимся подробнее на алгоритме работы MRP-мо- дуля. Для простоты речь ниже будет идти о дискретном производстве. Как и всякая компьютерная программа, MRP-система обменивается с окружающей средой входной и выходной информацией (рис. 6.15).
313

Рис. 6.15. Вход и выход MRP-цикла
Для работы MRP-модуля требуются следующие входные данные:
♦основной производственный план-график (объемно-
календарный план, Master Production Schedule – MPS) – документ,
в котором расписано, сколько единиц конечного изделия будет производиться в каждый плановый период отрезка планирования;
♦данные о состоянии запасов (книга учета запасов, Inventory Status File) – документ, максимально полно раскрывающий информацию о каждой учетной единице сырья, материалов, комплектующих, конечных изделий, включающую:
общее описание – идентифицирующий код, характеристику, размер, вес и пр.;
данные о запасах: единица запаса, расположение, размер запаса, статус (например, находится на руках, на складе, в текущих заказах), оптимальный запас, страховой запас и пр.;
данные по закупкам и продажам для сырья, материалов и комплектующих: единица закупки/продажи, основные поставщики/покупатели, цена, время доставки, реквизиты поставщиков/покупателей, дополнительная информация (например, возможные задержки поставок);
данные по производству для полуфабрикатов и конечных изделий: размер партии, длительность производственного цикла;
♦спецификация состава изделия (Bill of Materials File – BOM) – документ, содержащий:
314
♦перечень сырья, материалов и комплектующих, необходимых для производства конечного изделия, с указанием нормативов по их использованию;
♦иерархическое описание структуры конечного изделия. Результатами работы MRP-модуля являются следующие
документы:
♦график заказов на закупку/производство материалов и комплектующих (Planned Order Schedule) – документ, расписывающий, какое количество сырья, материалов, комплектующих должно быть заказано в каждый плановый период в течение срока планирования. Этот документ определяет внутрипроизводственный план сборки комплектующих и план внешних закупок;
♦изменения к графику заказов на закупку/производство материалов и комплектующих (Changes in planned orders) – документ, содержащий корректировки ранее спланированных заказов на закупку/производство материалов и комплектующих. Входные
ивыходные данные MRP-модуля представляются в виде таблиц базы данных.
6.5.2. Логика работы MRP-модуля: схема цикла
На рис. 6.16 приведен пример, иллюстрирующий логическую схему MRP-цикла. Собственно MRP-цикл состоит из следующих шагов.
1.Составляется таблица общих потребностей в материалах
икомплектующих. Последовательность ее создания такова.
1.1.Древовидная структура состава изделия разворачивается в линейный список материалов и комплектующих (1а):
– узловые элементы различных уровней сборки кодируют-
ся – корневому элементу присваивается код 0, элементам самого верхнего уровня сборки – код 1 и т.д. по уровням;
–если некоторый элемент встречается на различных уровнях, ему присваивается код самого нижнего из этих уровней (и, таким образом, в линейном списке этот элемент встретится только один раз);
–разузлование состава изделия происходит последовательно по уровням – сначала обрабатывается уровень 0, затем уровень 1 и т.д.
315
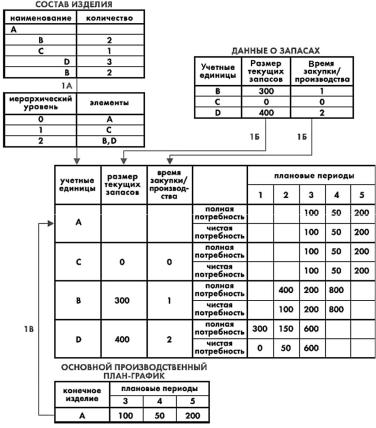
Примечание 1. В приведенном ниже примере изделию A будет присвоен код 0, узлу C – код 1, узлам D и B – код 2. Узел B встречается на более высоком уровне сборки, но учитывается на нижнем уровне.
1.2.Из книги учета запасов переносятся данные о материалах и комплектующих, необходимых для производства конечного изделия, в частности данные о времени выполнения заказа на их поставку/производство (1б).
1.3.Переносятся плановые показатели выпуска конечного изделия из основного план-графика производства (1в).
Рис. 6.16. Логическая схема MRP-цикла
316
1.4. По каждому материалу и узлу для каждого планового периода рассчитывается общая производственная потребность в этом материале/узле; при этом используются данные состава изделия (количество каждого материала/узла, необходимое для производства конечного изделия или промежуточного узла) и информация о временипоставки/производстваматериаловикомплектующих.
Примечание 2. В приведенном ниже примере общая потребность в элементе В во втором плановом периоде (она равна 400) получается так: потребность производства «А» в элементе «В» в третьем плановом периоде – 200 элементов (100·2), потребность производства «С» в элементе «В» в третьем плановом периоде – тоже 200 элементов. С учетом того, что время поставки/производства элемента «В» – один плановый период, заказ элемента «В» записывается во второй плановый период в количестве 400 единиц (200+200). Аналогично рассчитываются остальные ячейки таблицы.
2.По каждому материалу на каждый плановый период считается чистая потребность в этом материале. При этом используются данные осостояниизапасов.
Чистая потребность считается по формуле Чистая потребность = общая потребность – ( текущие запа-
сы + активные заказы – страховой запас).
Примечание 3. В идеале MRP-система не должна создавать страховых запасов. Однако в реальности случаются непредвиденные
инеустранимые срывы поставок материалов. Для поддержания процесса производства в подобных ситуациях создают страховой запас. Его размер определяется заранее компетентными лицами и зависит отконкретных условий производственного процесса.
3.По ненулевым чистым потребностям формируется график заказов на закупку/производство материалов и комплектующих. При его создании учитывается времявыполнениякаждого заказа.
4.Просматриваются заказы, сгенерированные ранее текущего периода планирования. В случае необходимости система пересчитывает сроки и размер заказа и вносит корректировки в сформированный ранее план-график закупок. Эти изменения автоматически регистрируются в базе данных о состоянии запасов (поскольку создание, отмена или модификация заказа влияет на статус соответствующего ему материала).
317
Представленная схема работы MRP-цикла очень упрощена. В реальности необходимо учитывать огромный спектр особенностей конкретного производственного процесса (например, широкий ассортимент производимых товаров, конструктивную сложность конечных изделий, территориальную разбросанность складов, регулярные сбои поставок комплектующих). Поэтому MRP-системам приходится просчитывать огромное количество информации, и длительность MRP-цикла может измеряться часами даже на современном уровне развития вычислительной техники.
6.5.3. Уровни планирования
Существует несколько уровней планирования.
1. Стратегическое планирование (Strategic Planning). Из всех уровней этот – наименее интегрированный и наименее точный, поскольку планирование осуществляется для достаточно длительного периода. Исполнительным и финансовым директорам компаний необходимо прогнозировать спрос не только в рамках ближайшего года, но и последующих, для того чтобы установить прогноз предполагаемого роста компании. Стратегические планы устанавливают границы (guidelines) для планирования производства и продаж на текущий год или даже более длительный период. Стратегический план устанавливает общие цели для организации, касающиеся в основном валовых продаж (gross sales) или общего дохода (overall income). Чтобы проверить реальность выполнения такого плана, вы должны посмотреть на общие затраты (total outlays) и сравнить их с общим доходом (total income). Если вы тратите больше, чем зарабатываете, то рентабельными вы не будете.
2. Планирование производства (Production Planning).
Эти планы составляются на уровне завода (factory) или площадки (site) работниками, ответственными за достижение целей, установленных руководителями компании. Им необходимо следить за всеми видами деятельности на площадке и осуществлять координацию. Когда эти планы разработаны, они являются руководством к действию для работников, ответственных за производ-
318
ство конкретных номенклатурных позиций, относящихся к определенным группам продуктов. Этот план создается для завода, площадки, подразделения (division) или отдела, где прогноз продаж, прогноз производства и предполагаемый доход являются сферой деятельности различных работников. Для проверки реальности выполнения плана все эти прогнозы должны быть сбалансированы. Вы не сможете продать то, что не произведете.
3. Планирование конечного продукта (End Item Planning).
Эти планы обычно составляются создающими главные календарные планы работниками (master schedulers), которые оценивают спрос на продукт и определяют, какое количество продукта необходимо произвести. Эти работники обладают информацией о ближайшем будущем и изменяют производственные планы для того, чтобы регулировать текущую ситуацию на производстве. Горизонт планирования производства конечного продукта обычно приближенно равен общей длительности цикла (cumulative lead time). Этот план рассматривает ряд приоритетных позиций (конечные продукты, номенклатурные позиции 1-го уровня, запасные части (service parts) и т.д.), которые будут произведены, а также календарный план их производства. Проверкой достижимости такого плана является наличие достаточного объема критических ресурсов. Если вы хотите произвести 50 изделий за следующую неделю, а ваше производство изготавливает только 25 единиц за неделю, вы не выполните план.
4. Планирование компонентов (Component Planning).
Главный календарный план формирует спрос на компоненты; ППМ использует этот спрос для планирования заказов на компоненты. Плановики и работники цехов (Planners and shop floor people) используют результаты ППМ для определения календарного плана производства, который имеет такой же горизонт планирования, как и главный календарный план. Этот план позволяет вам определить, какие рабочие центры (группы взаимозаменяемого оборудования) и компоненты будут использованы для реализации плана. Проверкой выполнимости плана является определение того, имеют ли рабочие центры необходимые мощности для выполнения календарного плана.
319
6.5.4.Многоуровневое планирование
врамках MFG/PRO
Вконцепции MRP/ERP, заложенной в рамках MFG/PRO, предусматривается сквозное планирование, согласование и оперативное корректирование планов и действий снабженческих, производственных и сбытовых звеньев предприятия. Планы снабжения, производства и сбыта могут согласовываться в долгосрочной перспективе
(Strategic Planning) исреднесрочнойперспективе(Tactical Planning).
На первом этапе осуществляется агрегированное планирование с использованием прогнозов спроса на готовую продукцию
иданных о фактически поступивших заказах. Сформированный план в рамках системы MFG/PRO проверяют на возможность выполнения с точки зрения критичных ресурсов.
На втором этапе осуществляется формирование графика производства, дезагрегирование плана производства с указанием конкретных дат. Сформированный план в рамках системы MFG/PRO проверяют на возможность выполнения с точки зрения критичных ресурсов.
На третьем этапе с помощью МРП производится расчет потребности в материальных ресурсах и производственных мощностях под график производства. Информационное обеспечение МРП включает данные плана производства, файл материалов (формируемый на основе плана производства и включающий
специфицированные наименования необходимых материалов с указанием их количества в расчете на ед. готовой продукции), файл запасов (данные по необходимым, для выполнения плана производства, материальным ресурсам – как по имеющимся на складе, так и заказанным, но еще не поставленным; по срокам выполнения заказов; страховыми запасами и др.). План МРП проверяется на выполнение с помощью модуля CRP, который анализирует загрузку рабочих центров. Ресурсами, используемыми для обработки заказов в производстве, являются мощности рабочих центров. Производственный календарь определяет фактическое число рабочих дней в периоде. CRP моделирует расходование часов РЦ, используя заказы как производственный спрос. Технологические маршруты нарядов-заказов обеспечивают информацию о том, какие заказы и когда используют РЦ. Планирования является сердцевиной MFG/PRO (рис. 6.17, 6.18). Решение задач
320