
Голцев Методы механических испытаний и механические 2012
.pdf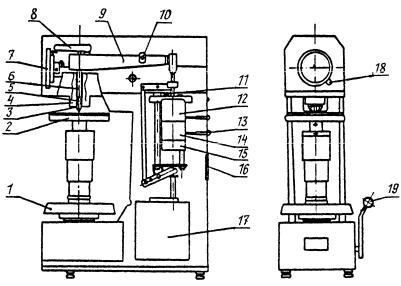
Для каждого изделия рекомендуется произвести не менее четырех испытаний. Первое испытание во внимание не принимается. Чтобы обеспечить достоверность результатов, чистота испытываемой поверхности должна быть не ниже Rα = 1,25 мкм. Поверхность испытываемого изделия должна быть сухой и чистой и не иметь трещин, выбоин и грубых следов обработки. Минимальная толщина испытуемого изделия должна быть не менее восьмикратной глубины внедрения алмазного конуса или шарика. Не разрешается производить испытания неоднородных по структуре сплавов хрупких изделий, а также изделий, которые могут пружинить или деформироваться под действием нагрузки. При проведении испытаний необходимо, чтобы расстояние центра отпечатка от края изделия или центра другого отпечатка было не менее 2 мм.
Рис. 42
На рис. 42 цифрами обозначены следующие части прибора: 1 – маховик; 2 – предметный столик; 3 – наконечник; 4 – пружина; 5 – ограничитель; 6 – шпиндель; 7 – индикатор; 8 – рычаг; 9 – грузовой рычаг; 10 – груз; 11 – шток; 12, 14, 15 – грузы; 13 – ручка; 16 – таблица; 17 – привод; 18 – ручка; 19 – рукоятка.
81
1.5.4. Твердость по Виккерсу (ГОСТ 2999)
Твердость по Виккерсу определяют вдавливанием в испытываемый объект алмазного наконечника, имеющего форму правильной четырехгранной пирамиды, при нагрузках от 1 до 100 кгс, приложенных в течение определенного времени, и измерением диагоналей отпечатков d1 и d2, оставшихся на поверхности образца после снятия нагрузки. Угол между противоположными гранями пирамиды равен 136°. Выбор угла определялся тем, чтобы числа твердости по Виккерсу были по возможности близки к числам твердости по Бринеллю. Диагональ квадратного отпечатка принята как средний диаметр отпечатка при испытании по Бринеллю.
Обычно диаметр отпечатка при испытании по Бринеллю ограничивается диапазоном 0,25D ≤ d ≤ 0,5D, где D – диаметр шарика, и тогда средний диаметр dср=0,375D. При таком выборе среднего диаметра угол между гранями пирамиды соответствует 136°. Число твердости по Виккерсу (HV) определяется делением нагрузки в кгс на площадь боковой поверхности получившегося пирамидального отпечатка в мм2.
|
P |
|
2P sin |
|
|
|
P |
|
|
HV= |
|
2 |
|
1,854 |
(для =136°), |
(37) |
|||
|
d2 |
|
|
d2 |
|||||
|
F |
|
|
|
|
|
где d – среднеарифметическое значение двух диагоналей, измеренных во взаимно-перпендикулярных направлениях.
Применяются нагрузки 1; 2; 2,5; 3; 5; 10; 20; 30; 50 и 100 кгс.
Нагрузка выбирается в зависимости от толщины и твердости испытуемого материала. Минимальная толщина образца должна быть для стальных изделий больше диагонали отпечатка в 1,2 раза; для изделий из цветных металлов – в 1,5 раза. Расстояние от центра отпечатка до края образца или края следующего отпечатка должно быть не менее 2,5 диагоналей отпечатка. Обычная продолжительность выдержки под нагрузкой составляет 10‒15 с. Для этого метода, отличающегося высокой точностью измерения диагонали отпечатка, очень важны чистота поверхности образца (0,16 мкм) и отсутствие нагрева и наклепа при его изготовлении. Важную роль играет также время выдержки под нагрузкой. При обозначении числа твердости по Виккерсу обязательно указывается время вы-
82
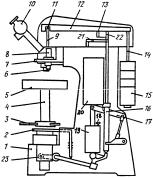
держки (например, 540 HV20/30 обозначает число твердости 540, полученное под нагрузкой 20 кгс, действующей в течение 30 с).
Определение твердости по Виккерсу является более совершенным, чем определение ее методами Бринелля и Роквелла. К числу основных преимуществ указанного метода следует отнести: полное геометрическое подобие отпечатков независимо от значения прилагаемой нагрузки; возможность определения твердости на азотированных, цементированных поверхностях, а также на тонких листовых материалах; хорошее совпадение значений твердости по Виккерсу и Бринеллю в пределах 100–450 ед.
Обычно размеры отпечатка при определении твердости по Виккерсу очень малы. При грубой структуре образца это может вызвать большой разброс значений. Для получения достоверных средних значений приходится делать на каждом образце не менее 5–10 замеров.
На рис. 43 показан серийный прибор ТП, который позволяет измерять твердость при нагрузках в 5, 10, 20. 30, 50, 100 и 120 кгс. Элементы твердомера (см. рис. 43): 1 – станина; 2 – педаль; 3 – маховичок; 4 – подъемный винт; 5 – опорный столик; 6 – индентор; 7 – рукоятка; 8 – шпиндель с индентором; 9 – промежуточный шпиндель; 10 – измерительный микроскоп; 11 – призмы; 12 – рычаг; 13 – штырь; 14 – подвеска; 15 – сменные грузы; 16 – пустотелый шпиндель; 17 – ломаный рычаг; 18 – винт; 19 – масляный амортизатор; 20 – груз; 21,22 – рычаги; 23 – рукоятка. Твердость по Виккерсу определяется по величине диагонали отпечатка с помощью таблиц или рассчитывается по формуле (37).
Рис. 43
83
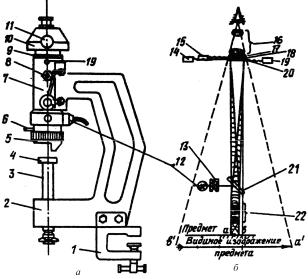
Переносной прибор типа ТПП-2 (рис. 44) крепится к столу с помощью съемного кронштейна 1. Основная часть этого прибора ‒ испытательная головка 7, смонтированная в алюминиевом корпусе 2.
Испытательная головка состоит из двух систем:
1)нагружения – для создания испытательных нагрузок, под действием которых алмазный наконечник вдавливается в испытываемую деталь;
2)проекционно-измерительной – для проецирования полученного отпечатка на экран измерительной головки и измерения длины диагонали отпечатка с погрешностью до 0,001 мм. Перемещение испытательной головки осуществляется вручную поворотной рукояткой 11.
Рис. 44
Система нагружения состоит из алмазного наконечника, который крепится в конусе 5; из сменных стаканов на 5 и 10 кгс; валика эксцентрикового, поворот которого осуществляется рукояткой 8; подвижного стакана, в нижней части которого на полуосях смонтирована поворотная рамка 21. В зависимости от положения поворотной рамки, которое регулируется ручкой 6, алмазный наконечник может находиться либо в рабочем, либо в нерабочем положении.
84
При повороте рамки на угол 17–18° от вертикали вводится в
действие проекционно-измерительная система. Проекционно-измерительная система состоит из измерительной
головки 10 (измерительная головка от микроскопа МПВ-1), переходника 9, рамки с плоскопараллельной пластинкой 21, объектива 22 и осветителя 12. В верхней части головки имеется окуляр 16 с увеличением 12,5. Объектив ОМ-2 с увеличением 10 предназначен для проецирования отпечатка на экран измерительной головки. Регулировка освещенности отпечатка производится перемещением патрона с лампочкой.
1.5.5. Микротвердость (ГОСТ 9450)
Метод микротвердости позволяет определять твердость, а через нее и механические свойства изделий и образцов из разных материалов, таких как металлы, сплавы, стекло, пластмасса, тонких пленок и покрытий и вообще изделий в весьма малых объемах и даже структурных составляющих материалов. ГОСТ 9450 устанавливает два метода испытаний: по восстановленному отпечатку (основной метод) ‒ обмер отпечатка после снятия нагрузки, и по не восстановленному отпечатку (дополнительный метод) – измерение глубины внедрения наконечника под нагрузкой. В обоих случаях мерой твердости является сопротивление материала процессу вдавливания индентора к поверхности полученного отпечатка. В качестве инденторов используются: прямоугольная пирамида Виккерса; треугольная пирамида, в основании которой находится равносторонний треугольник; четырехугольная пирамида, в основании которой ‒ ромб с определенным соотношением диагоналей, и двуцилиндрический наконечник с углом между осями цилиндров, равном 136°. В методе используются нагрузки от 1 до 500 г. Подсчет твердости осуществляется по формулам, учитывающим результаты обмера восстановленного отпечатка или глубины внедрения индентора под нагрузкой. Твердость обозначается как H с индексом, соответствующим типу использованного индентора (например, H□, H∆, H◊,).
Для измерения микротвердости используют настольный прибор ПМТ-3 (рис. 45), представляющий собой вертикальный микроскоп, укрепленный на массивной стойке 3 с ленточной резьбой. На тяжелой станине 1 стойки установлен предметный столик 2 с крестооб-
85
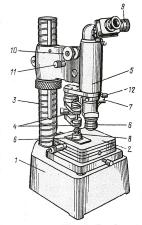
разным микрометрическим перемещением, по 10 мм в каждом направлении. Кроме того, столик имеет вращательное перемещение, ось вращения столика расположена строго посередине между оптической осью визирования микроскопа и осью индентора с точностью до 2‒3 мкм. Оправка с алмазной пирамидой 8 крепится на нижнем конце легкого и короткого штока, укрепленного на одном конце двух плоских пружин 4.
Рис. 45
1.5.6. Динамические методы определения твердости. Твердость при отскоке бойка от поверхности и без отскока. Метод Шора
Динамические методы определения твердости предполагают, что на исследуемую поверхность падает с некоторой высоты боек с наконечником. Эти методы можно разделить на две группы.
Первая группа методов предусматривает, что внедрение наконечника при падении бойка происходит без отскока от поверхности образца. Вес бойка с наконечником выбирается таким, чтобы не было упругого отскока. Число твердости условно определяют путем деления затраченной энергии на объем отпечатка.
При втором методе вес бойка с наконечником выбирают так, чтобы был упругий отскок. В качестве характеристики твердости принимают работу W=q(H‒h). При методе упругого отскока всегда наблюдается малая пластическая деформация.
86
Метод упругого отскока по Шору (ГОСТ 23273) использует условную шкалу твердости от 20 до 140 единиц, по которой высота отскока от поверхности твердой инструментальной стали принимается за 100 дел. (ед.). Масса бойка с алмазным наконечником равна 36 г и падает с высоты 19 мм. Твердость по Шору обозначается индексом HSD, например 85HSD. Величина твердости по Шору не имеет точного метода перевода ее на другие величины твердости или прочности при растяжении.
Следует отметить, что величина упругого отскока зависит от упругих характеристик материала, и поэтому сравнение чисел твердости будет правомерным, если материалы обладают одними и теми же упругими свойствами.
Существуют различные модификации указанных выше методов, и все они используются главным образом для сравнительной оценки состояния одного и того же материала после различной обработки и при повышенных температурах испытания с тем, чтобы не допустить размягчения наконечника, уменьшив время контакта наконечника с образцом.
Все рассмотренные так называемые динамические методы являются, по существу, статическими, так как скорости нагружения не велики.
1.6. Нестандартные методы статических испытаний
В ряде отраслевых лабораторий практикуются различные нестандартные испытания и пробы, позволяющие оценить поведение материала в конкретных условиях эксплуатации или исследовать влияние различных технологических факторов. Рассмотрим некоторые из этих методов испытания, нашедших применение для оценки механических свойств материалов.
1.6.1. Микромеханические испытания. Требования к оборудованию
Микромеханические испытания проводят для определения механических свойств металлов и сплавов в малых объемах. По сути дела, речь идет о испытании малоразмерных образцов на растяжение, сжатие, кручение, изгиб, твердость (микротвердость) и т.д.
87
Наиболее целесообразной формой образца для микромеханических испытаний является цилиндрический образец размером 0,8‒2 мм, изготовленный по классу точности 2а и геометрически подобный стандартным образцам. Исследование листовых материалов производится на плоских образцах, изготовляемых по шаблону.
Точность изготовления и измерения образцов оказывает решающее влияние на результаты испытания. Как известно, относительные погрешности изготовления и измерения образцов сильно возрастают с уменьшением диаметра, усугубляемым еще и тем обстоятельством, что при расчете характеристик прочности диаметр входит в квадрате.
Образцы испытывают на машинах, рассчитанных на малые предельные нагрузки и оснащенных специальными захватными приспособлениями.
В испытаниях на растяжение, сжатие, кручение, изгиб определяются те же механические характеристики, что и стандартных образцов, причем методология их определения также не отличается.
1.6.2. Испытания кольцевых образцов на растяжение. Определение стандартных механических свойств материала
Для определения механических свойств материала трубы в окружном направлении, т.е. в направлении, где главным образом происходит разрушение трубы под действием внутреннего давления, испытывают кольцевые образцы на растяжение на вкладышах (рис. 46). В этих испытаниях определяются стандартные механические свойства материала: предел текучести, временное сопротивление, относительное удлинение, относительное поперечное сужение, а также относительное равномерное удлинение. Следует иметь в виду, что в связи с ограниченной расчетной длиной образца определяемые характеристики условны.
Так, записываемая диаграмма деформирования образца может рассматриваться как действительная, пока идет процесс симметричного равномерного деформирования. При образовании шейки (как правило, с одной стороны кольца) появляется перекос образца и происходит дальнейший рост деформации по ослабленному сечению вплоть до разрушения.
88
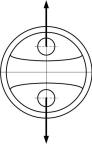
Рис. 46
Предел текучести и временное сопротивление материала определяют стандартным образом по диаграмме деформирования, а характеристики деформации – путем измерения изменения размеров начальной и конечных длин участков разрушенной и не разрушенной частей образца и изменения размеров поперечного сечения в месте разрушения.
1.6.3. Испытание на изгиб пластин, опертых по контуру. Определение сопротивления разрушению – характеристики прочности малопластичных материалов
Испытание на изгиб дисков, опертых по контуру, – один из методов оценки склонности материала к хрупкому разрушению. Испытание дисков при различных температурах в среде хладогента позволяет определить сопротивление отрыву сталей и их сварных соединений и может быть использовано для определения критической температуры хладоломкости; рекомендуется при сравнительной оценке материалов для сосудов, работающих под действием внутреннего давления.
Диски, опертые по контуру, испытываются на любой универсальной машине или прессе по схеме, показанной на рис. 47.
Круглый диск 1 из листа или другого полуфабриката толщиной h = 3÷6 мм опирается на кольцо 2 с внутренним диаметром D =
= 50÷60 мм; пуансон 3 диаметром d = 10÷20 мм перемещается в обойме 4 и под действием силы изгибает диск. Изгиб тонкостенного диска вызывает двухосное напряженное состояние: в радиальных и окружных сечениях действуют только нормальные напряжения. Наибольшие нормальные напряжения возникают на поверхно-
89
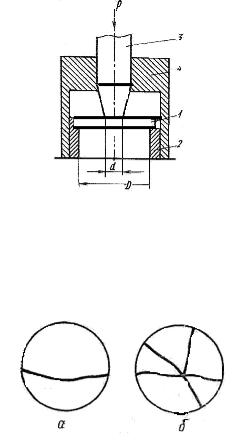
сти диска: с одной стороны, от срединной плоскости – растягивающие, с другой – сжимающие.
Рис. 47
На рис. 48 представлена характерная картина хрупкого разрушения дисков. Излом проходит в одном или нескольких диаметральных направлениях, при этом число линий излома, как правило, увеличивается с ростом хрупкости материала.
Рис. 48
Подсчет напряжений при разрушении (определение сопротивления отрыву ‒ или хрупкой прочности) возможен только при отсутствии пластического прогиба и производится в соответствии с первой теорией прочности по формуле
|
3P |
[4 (1 )( |
d |
)2 |
4(1 )ln |
d |
], |
(38) |
8 h2 |
|
|
||||||
|
|
D |
|
D |
|
90