
Голцев Методы механических испытаний и механические 2012
.pdf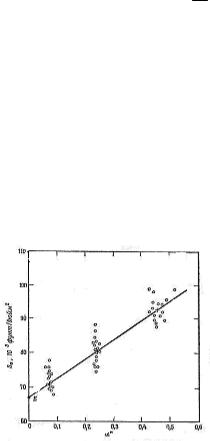
Метод Про основан на экспериментально установленной зависимости между амплитудой разрушающего напряжения ( )p и
скоростью возрастания амплитуды напряжения ( d )в виде: dt
( |
|
) |
|
|
|
k( |
d |
|
|
)m |
, |
(99) |
|
|
p |
1 |
dt |
|
|||||||||
|
|
|
|
|
|
|
|
где k и m ‒ параметры материала, определяемые экспериментально. Про считал, что m = 0,5, но экспериментально было показано, что m изменяется в зависимости от материала от 0,5 до 0,8.
После испытаний при трех различных скоростях изменения ам-
плитудного |
напряжения в координатах |
σmax‒ ( |
d |
|
|
)m |
строится |
||||
|
|
||||||||||
|
|
|
|
|
|
|
dt |
|
|
||
зависимость, которая экстраполируется |
на нулевое |
значение |
|||||||||
( |
d |
|
|
)m |
(рис. 97). |
|
|
|
|
|
|
|
|
|
|
|
|
|
|
||||
|
dt |
|
|
|
|
|
|
|
|
Рис. 97
Для сплавов, у которых отсутствует горизонтальный участок на кривой усталости, основное уравнение предложено записывать в виде
|
1 |
A |
max |
k( |
d |
|
|
)m . |
(100) |
|
dt |
||||||||||
|
|
|
|
|
|
Здесь σ‒1 – предел ограниченной выносливости на заданной базе, которая учитывается параметром А, m = 0,3÷0,39.
171

Метод Про не дает существенной экономии в образцах, но дает экономию времени порядка 50‒60 %. Кроме того, важной особенностью метода Про является то, что при известных постоянных материала k и m, он позволяет определять предел выносливости по результатам испытания каждого образца.
Метод Эномото является развитием метода Про. Было экспериментально подтверждено предположение, что отношение разрушающего напряжения к величине предела выносливости для заданной скорости возрастания амплитуды напряжения есть величина постоянная для отдельных групп материалов, т.е.
|
1 |
|
max |
, |
(101) |
|
|||||
|
|
C |
|
где С ‒ коэффициент, зависящий от скорости возрастания амплитуды напряжения. Наибольшая точность получена при скорости
( d ) =10-5 МН/м2цикл. При этой скорости возрастания ампли- dt
туды напряжения для стали С = 1,081.
Метод Локатти основан на предположении о возможности использования закона линейного суммирования повреждений. Строятся кривые усталости с использованием того или иного уравнения (кривые 1 и 2 на рис. 98) так, что реальная кривая усталости располагается между ними. В дополнение к кривым 1 и 2 строится кривая 3, которая располагается между кривыми 1 и 2. Задается программа ступенчатого нагружения образца так, что соответствующий график перекрывает кривые 1, 2, 3 по уровню напряжений. Выбирают такие режимы, чтобы разрушение происходило быстро. Затем, при использовании каждой из кривых усталости, подсчиты-
k |
n |
|
вается сумма |
i |
, где k – число ступеней нагружения, ni – число |
|
||
i 1 |
Ni |
циклов нагружения на каждой ступени нагружения, Ni – число циклов до разрушения на каждой ступени нагружения, и строится кри-
k |
n |
|
|
|
вая в координатах |
i |
‒ σ‒1 |
(рис. 98,б). Значение σ‒1 |
для задан- |
|
||||
i 1 |
Ni |
|
|
ного материала соответствует сумме, равной 1, если справедлив закон линейного суммирования повреждений.
172
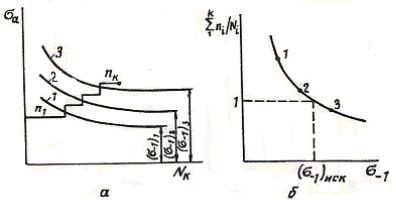
Рис. 98
Рассмотренные ускоренные методы определения предела выносливости дают ошибку в 10‒15 % при большой экономии времени испытания.
Метод «лестницы», или метод «вверх ‒ вниз». Очень эффек-
тивным методом определения среднего значения и вариации сопротивления усталости при любой заданной долговечности является метод «вверх ‒ вниз», в равной степени пригодный и для определения предела выносливости, поскольку предел выносливости представляет собой сопротивление усталости при бесконечной долговечности. При проведении испытаний методом «вверх – вниз» для оценки сопротивления усталости при некотором значении долговечности отбирается группа не менее чем из 15 образцов. Испытания проводятся до разрушения или до завершения заданного числа циклов, соответствующего заданной величине долговечности. Если образец разрушается до достижения необходимой долговечности, амплитуда напряжения уменьшается на некоторую заданную величину, и второй образец испытывается при этой новой уменьшенной амплитуде напряжений. Если первый образец выживает, амплитуда напряжения увеличивается на некоторую заданную величину, и второй образец испытывается при новой, увеличенной амплитуде напряжения. Испытания проводятся последовательно таким образом, что каждый последующий образец испытывается при амплитуде напряжения выше или ниже на величину одного приращения амплитуды, при которой испытывался предшествующий образец, в зависимости от того, выжил он или разрушился.
173
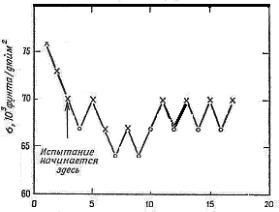
Результаты типичного испытания методом «вверх – вниз» показаны на рис. 99.
Рис. 99
Неразрушающие косвенные методы определения предела вы-
носливости материала. Примером такого испытания является изгиб вращающегося образца ступенчато возрастающей нагрузкой и регистрацией на каждой ступени нагружения показаний таких величин, как температура образца, прогиб образца в точках приложения нагрузки, реактивный момент привода, электрическое сопротивление образца и др. Резкое изменение зависимостей указанных величин от нагрузки, действующей на образец, принимается во внимание как момент достижения предела выносливости материала, который определяется по этой нагрузке. Проведенные многочисленные эксперименты показали, что такие методы не дают надежной оценки предела выносливости материала.
Стадии усталостного повреждения и разрушения. Рассеяние характеристик сопротивления материала усталости
Можно выделить две стадии накопления повреждений в процессе усталостного нагружения до полного разрушения: 1-я стадия – стадия накопления повреждений до появления первой макротрещины; 2-я стадия – стадия развития усталостной трещины. На 1-й стадии при внешнем стационарном нагружении действует стационарное напряженное состояние. На 2-й стадии при внешнем ста-
174
ционарном нагружении напряженное состояние непрерывно изменяется за счет уменьшения площади сечения образца и изменения концентрации напряжений перед фронтом трещины.
Пусть Nt – число циклов до появления первой трещины, Nk – число циклов при полном разрушении. Для гладких образцов Nt ≈ ≈ 0,9 Nk. Для образцов с концентраторами напряжений Nt « Nk. Так, для стали 45 с концентратором при коэффициенте концентрации напряжений 5 было установлено соотношение Nk = 25Nt . Это
указывает на то, что в условиях концентрации напряжений изделие работает длительное время при наличии развивающейся трещины.
В силу неоднородности структуры материала всегда наблюдается существенный разброс характеристик сопротивления материала усталости. Этот разброс зависит от уровня напряжений и существенно возрастает при напряжениях, соответствующих уровню предела выносливости. Высказанное замечание относится и к определяемым характеристикам появления первой макротрещины. В этой связи актуальны статистическая обработка результатов испытаний и их представление в виде кривых равной вероятности, относящихся как к моменту появления первой трещины, так и к полному разрушению образца, на основе которых могут быть получены детерминистские закономерности усталости.
Статистические и детерминистские закономерности усталости
Для данного образца процесс накопления повреждений детерминирован. Степень повреждения этого образца зависит от напряженного состояния, градиента напряжений, числа циклов нагружения и др. факторов D f ( max ,G,N). При заданной степени повреждения D=const можно записать ND ( max ). Это ‒ уравне-
ние кривой усталости, соответствующей данной степени повреждения. Вид этой функции закономерно связан с характером силового воздействия, вида напряженного состояния и ряда других факторов. Получить эту функцию из испытаний одного образца невозможно, так как невозможно один и тот же образец разрушить на разных уровнях напряжений. Из испытаний ряда образцов получаем частные результаты распределения случайной величины N на
175

фиксированном уровне напряжений. Область рассеяния представляет семейство линий равной вероятности, что дает исчерпывающую информацию для данной повреждаемости D. Линии равной вероятности равного повреждения отождествляются с кривыми усталости равнопрочных образцов с ND ( max ) . Таким обра-
зом, если бы можно было провести испытания двух совершенно одинаковых образцов на разных уровнях напряжения, то соответствующие точки легли бы на одну и ту же кривую усталости для определенной вероятности.
Закономерности, определенные по таким кривым, носят характер устойчивых функциональных связей и, в этом смысле, рассматриваются как детерминистские. Таким образом, количественная оценка связана с рассеянием, где вероятность повреждения выступает как параметр этой оценки, и необходим совместный анализ статистических и детерминистских закономерностей.
3.2.Закономерности распространения усталостной трещины
Впоследние годы большое внимание уделяется изучению кинетики роста усталостных трещин на основе подходов механики разрушения. Возникшая усталостная трещина (или любой другой начальный дефект конструкции) будет расти при дальнейшем циклическом нагружении до тех пор, пока не достигнет критического размера, после чего в соответствии с законами механики разрушения начнется быстрое катастрофическое разрушение. Как правило, время роста возникшей усталостной трещины до критического размера составляет значительную часть времени полезного использования конструкции.
Основой для расчетных оценок живучести служат диаграммы циклической трещиностойкости – зависимости между скоростью
роста усталостной трещины da и размахом коэффициента интен- dN
сивности напряжений K на N-м цикле нагружения. Диаграмма циклической трещиностойкости обладает существенной инвариантностью относительно типа образца, его размеров, способов нагружения, уровня действующего напряжения. Обычно она строится в двойных логарифмических координатах (рис. 100). Диаграмма располагается между двумя асимптотами, определяемыми значе-
176
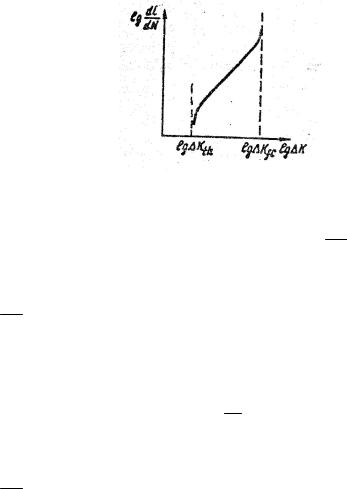
ниями Kth (размахом порогового коэффициента интенсивности напряжений, ниже которого трещина не распространяется) и Kfc (циклической вязкостью разрушения, по достижению которой происходит долом образца).
Рис. 100
Для оценки скорости роста усталостной трещины до критической величины предложено много различных моделей. Было пока-
зано, что скорость роста усталостной трещины da зависит от dN
размаха циклических напряжений Δσ, длины трещины α и некоторого параметра С, зависящего от свойств материала
da f ( , a, C). Наиболее часто используется формула Пари- dN
са:
da |
C( K)m , |
(102) |
|
||
dN |
|
где K – размах коэффициента интенсивности напряжений, равный
разности (Kmax Kmin ); K a ; С и т – постоянные материала. С ростом трещины увеличивается напряжение и размах коэффициента интенсивности напряжений. Скорость роста трещины
da характеризуется наклоном кривых зависимости a от N, полу- dN
чаемых экспериментально при испытании образцов в условиях постоянного размаха циклической нагрузки Р. Соответствующие значения K вычисляются по размаху действующей нагрузки и среднему значению длины трещины на каждом интервале с помощью формулы для коэффициента интенсивности напряжений. Эта
177
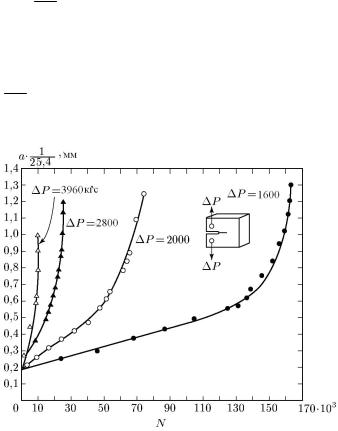
формула должна соответствовать заданной геометрии испытываемого образца с трещиной.
На рис. 101 приведены кривые роста усталостной трещины α при различных пульсирующих растягивающих нагрузках Р в стали Ni–Mo–V при частоте 1800 циклов/мин. Эти кривые обработаны по указанной выше схеме, и результаты такой обработки представлены в виде отдельных точек на рис. 102 зависимости скорости ро-
ста трещины da от размаха коэффициента интенсивности напря- dN
жений K. Следует отметить, что обработка всех кривых на рис. 101 дает единственную кривую на рис. 102, описываемую уравнением Париса, где т – наклон прямой, изображающей зависи-
мость lg da от lg K, а С – эмпирический параметр, который dN
зависит от свойств материала.
Рис. 101
Таким образом, при известных значениях С и m длина трещины после N циклов нагружения может быть подсчитана по формуле
178
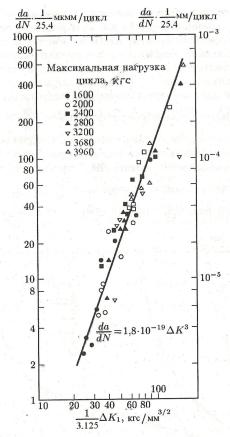
m |
|
aN ai C K dN , |
(103) |
где ai – начальная длина трещины; N – полное число циклов на-
гружения. Зная критический коэффициент интенсивности напряжений материала Kc (вязкость разрушения), определяемый при однократном статическом нагружении, можно найти циклическую долговечность конструкции с начальной трещиной длиной ai .
Рис. 102
Следует отметить, что формулы (102) и (103) относятся лишь к линейной части кривой на рис. 102. Хотя чаще всего ссылаются на
179
формулу Париса при описании закономерности роста усталостной трещины, нужно иметь в виду, что она не учитывает ни пика напряжений, ни существование предельного значения Kth. Для учета этих факторов чаще всего используется соотношение
da |
C Kn |
|
||
|
= |
|
, |
(104) |
|
|
dN (1 R)Kc K
где R – коэффициент асимметрии цикла и Kc – вязкость разрушения. В результате дальнейшей модификации этого выражения с целью учета наблюдаемых предельных значений коэффициента интенсивности напряжений Kth для распространения трещины предложено соотношение
da |
C( K K |
|
)n |
|
||
|
= |
|
th |
|
. |
(105) |
|
|
|
|
dN (1 R)Kc K
3.3. Малоцикловая усталость
Исследование малоцикловой усталости и разработка соответствующих методов расчета представляют интерес для таких изделий, как лопатки и роторы авиационных газовых турбин, топливные элементы и баки атомных реакторов, роторы и корпуса паровых турбин. В таких изделиях изредка действуют большие механические нагрузки и температурные перепады, особенно на переходных режимах работы, которые способствуют накоплению больших деформаций и разрушению за несколько сотен или тысяч циклов. Анализ типичной кривой усталости, построенной во всем диапазоне изменения напряжений (рис. 103), показывает, что в диапазоне
изменения числа циклов от 1 до 103 усталостная прочность почти
4
постоянна и близка к пределу прочности материала в . Это выра-
жается в том, что кривая усталости в указанном диапазоне, в котором материал циклически пластически деформируется, идет почти горизонтально. В этой области пластического поведения материала гораздо точнее определять его усталостную долговечность в виде функции амплитуды циклической деформации, а не в виде функции циклического напряжения. Зависимость напряжения от деформации при этом графически изображается петлей гистерезиса, показанной на рис. 104.
180