
Голцев Методы механических испытаний и механические 2012
.pdfреальные (а не условные) механические характеристики материала по результатам испытания на изгиб. Обратим внимание на то, что
если |
dМи |
= |
const = |
Ми |
, |
тогда |
max |
|
6Ми |
, что соответствует |
|||||
|
|
|
|
||||||||||||
|
|
d |
|
|
|
|
bh2 |
dМи |
|
||||||
зависимости |
для упругой |
области нагружения. При |
0 , |
||||||||||||
|
|||||||||||||||
|
|
|
4Ми |
|
|
|
|
|
|
|
|
d |
|||
|
max |
|
, т.е. появляется «шарнир» пластичности, |
когда на- |
|||||||||||
bh2 |
|||||||||||||||
|
|
|
|
|
|
|
|
|
|
|
|
пряжения по всему сечению равны σmax.
Для хрупких материалов и материалов в малопластичном состоянии разрушающие напряжения вычисляются по формулам упругого изгиба, хотя всегда полному разрушению предшествует та или иная пластическая деформация или наблюдается развитие трещины разрушения, что проявляется в отклонении от линейной зависимости между изгибающими нагрузками и прогибами на диаграмме изгиба.
1.3.4. Характеристика изломов при испытании малопластичных материалов
Картина разрушения при изгибе определяется характером разрушения материала при растяжении, поскольку разрушение всегда начинается в растянутой зоне образца. У хрупких и малопластичных материалов наблюдается отрыв, т.е. излом будет перпендикулярен направлению растягивающих напряжений. У ряда материалов с ограниченной пластичностью четко выявляется характер разрушения в виде разрушения путем среза. Высокопластичные материалы, как отмечалось, не разрушаются при изгибе.
1.4. Испытание на кручение
1.4.1. Закономерности деформирования цилиндрического бруса при упругом и упругопластическом кручении
Деформация прямолинейного бруса, вызываемая парами сил, плоскости действия которых перпендикулярны к оси бруса, называется кручением. Деформация, возникающая при кручении круг-
61

лого бруса, имеет следующие особенности: поперечные сечения остаются плоскими и не изменяют своих размеров; расстояния между поперечными сечениями остаются неизменными; радиусы поперечных сечений остаются прямыми. Таким образом, поперечные сечения поворачиваются относительно друг друга как жесткие диски. Элемент, выделенный поперечными, цилиндрическими и осевыми сечениями, испытывает угловую деформацию, которая оценивается относительным сдвигом (углом сдвига). Деформация сдвига вызывается касательными напряжениями, действующими по граням элемента. Согласно закону Гука, эти напряжения в упругой области деформирования при сдвиге равны:
G G |
r |
, |
(24) |
|
|||
|
l |
|
где G – модуль сдвига; γ = r∙φ/l – относительный сдвиг; φ – угол поворота одного поперечного сечения бруса относительно другого; l – расстояние между этими сечениями; r – расстояние от центра тяжести поперечного сечения до точки, в которой определяются напряжения.
В точках поперечного сечения бруса, таким образом, действуют касательные напряжения xt , которые прямо пропорциональны расстоянию r и направлены перпендикулярно к радиусу.
Величину xt в любой точке круглого поперечного сечения можно подсчитать по формуле
|
xt |
|
Mx |
r, |
(25) |
|
|||||
|
|
Jp |
|
||
где Mx – крутящий момент в сечении; Jp |
– полярный момент |
инерции площади поперечного сечения.
По закону парности касательных напряжений в осевых сечениях скручиваемого бруса будут действовать напряжения xt tx .
Напряженное состояние, возникающее при кручении бруса, называется чистым сдвигом. В площадках, наклоненных под углом 45° к площадкам, в которых действуют xt , будут действовать главные
напряжения 1 и 3 ( 2 0), причем 1 3 xt . Наибольшего значения напряжения достигают в периферийных
точках сечения и обращаются в нуль в центре. Для точек, находящихся на контуре сечения,
62
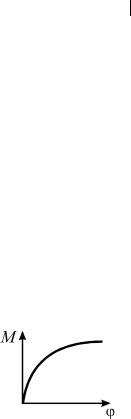
|
xt |
|
max |
|
|
|
Mx |
|
|
, |
(26) |
|
|||||||||||
|
|
|
|||||||||
|
|
|
|
|
|
||||||
|
|
|
|
|
Wp |
|
|||||
|
|
|
|
|
где Wp J p /rmax – полярный момент сопротивления сечения при
кручении.
Угол закручивания одного сечения относительно другого в упругой области определяется по формуле Mxl/(GJp ).
1.4.2. Характеристики прочности и пластичности и их определения по ГОСТ 3565
Обычно испытания на кручение проводятся на цилиндрических образцах круглого поперечного сечения. При этом деформация как правило равномерно распределена по длине образца. Сопротивление материала деформированию при кручении характеризуется диаграммой деформирования M x . Типичная диаграмма
Mx для малоуглеродистой стали представлена на рис. 33. При кручении тонкостенного трубчатого образца кольцевого поперечного сечения в поперечном сечении реализуется равномерное распределение напряжений. В этом случае на диаграмме M может быть выявлена площадка текучести для материала, у которого площадка текуче-
Рис. 33
сти проявляется при испытании на
растяжение. Однако при испытании тонкостенных трубчатых образцов наступает потеря устойчивости образца уже на ранней стадии пластического деформирования.
Для материала в хрупком состоянии диаграмма M имеет линейный характер вплоть до момента разрушения образца.
Отметим характерную особенность диаграммы M , отличающую ее от машинной диаграммы растяжения пластичного образца. На диаграмме M отсутствует снижение нагрузки после
максимума, что свидетельствует о равномерном деформировании образца по длине вплоть до момента разрушения.
63
В соответствии с ГОСТ 3565 при испытании образцов на кручение определяются следующие механические характеристики сопротивления металла деформированию и разрушению:
•модуль сдвига G, МПа (кгс/мм2), – отношение касательного напряжения к упругой угловой деформации в точке;
•предел пропорциональности при кручении пц , МПа (кгс/мм2),
–касательное напряжение в периферийных точках поперечного сечения, вычисленное по формуле для упругого кручения, при котором отступление от линейной зависимости между нагрузкой (моментом) и углом закручивания достигает такой величины, что тангенс угла, образованного касательной к кривой деформации и осью нагрузок, увеличивается на 50 % своего значения на линейном участке;
предел текучести при кручении 0,3 , МПа (кгс/мм2), – касательное напряжение, вычисленное по формуле для упругого кручения, при котором образец получает остаточный сдвиг, равный
0,3 %;
условный предел прочности при кручении пч , МПа
(кгс/мм2), – касательное напряжение, равное отношению наибольшего момента при кручении, предшествующего разрушению образа, к полярному моменту сопротивления образца;
истинный предел прочности при кручении tк , МПа (кгс/мм2), – наибольшее истинное касательное напряжение при разрушении образца, вычисленное с учетом перераспределения напряжений при пластической деформации;
максимальный остаточный сдвиг при кручении γmax, рад, – максимальная остаточная деформация в точке на поверхности образца для испытаний в момент разрушения.
Способность материала деформироваться при кручении на различных стадиях нагружения оценивается величинами относительного угла закручивания θ = φ/l и относительного сдвига γ = φd/(2l) (для малых углов закручивания, когда γ ≤ 0,1) или γ = arctg φd/(2l) (когда γ > 0,1). Отметим, что как при упругом, так и пластическом кручении деформация, измеряемая относительным сдвигом γ, прямо пропорциональна расстоянию точки от оси образца;
срез или отрыв – характер разрушения при кручении – определяется по ориентации поверхности разрушения. Разрушение от ка-
64
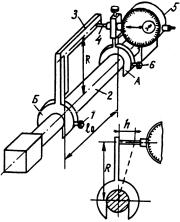
сательных напряжений (путем среза) происходит по поперечному сечению образца. Разрушение от растягивающих напряжений (путем отрыва) происходит по винтовой поверхности, след которой на наружной поверхности образца образует винтовую линию, касательная к которой направлена под углом примерно 45° к оси образца.
При определении модуля сдвига, пределов пропорциональности и текучести в процессе испытания образца необходимо использовать чувствительный измеритель деформации, чтобы регистрировать малые углы закручивания в упругой области деформирования образца.
Одна из конструкций угломера представлена на рис. 34. Угломер состоит из частей А и Б, каждая из которых с помощью фиксирующих винтов 1 и 6 закрепляется на образце 2. Расстояние l0 между
плоскостями, перпендикулярными к оси образца и проходящими через оси фиксирующих винтов, называется базой угломера. При закручивании образца часть Б угломера поворачивается относительно части А. При этом измерительный наконечник 4 индикатора 5, укрепленный на неподвижной части А угломера, опирающийся на планку 3 подвижной части Б угломера,
замеряет перемещение h, возникающее в результате взаимного поворота сечений.
Малые углы закручивания вычисляют по формуле
h/R, рад, (27)
где R – расстояние от оси образца до измерительного наконечника индикатора. При R=40 мм и цене деления индикатора часового типа 0,01 мм минимальный регистрируемый угол закручивания равен
0,00025 рад, или 0,014°.
Процедура определения модуля сдвига и предела пропорциональности материала аналогична используемой при испытании на растяжение. Образец после обмера устанавливают в захваты испы-
65
тательной машины и подгружают крутящим моментом, соответствующим начальному касательному напряжению τ0, составляющему ~10 % ожидаемого предела пропорциональности исследуемого материала. Устанавливают на образец индикаторный угломер. Далее нагружают образец вначале большими (не менее трех), а затем малыми ступенями нагрузки, отмечая после каждой ступени угловую деформацию. Нагружение большими ступенями осуществляют до 80 % ожидаемого предела пропорциональности. Ступени малых нагружений выбирают так, чтобы до достижения предела пропорциональности было проведено не менее пяти ступеней малых нагружений. Значение малой ступени нагружения должно соответствовать увеличению касательного напряжения не более чем на 10 МПа (1,02 кгс/мм2). Результаты показаний заносят в табл. 5.
|
|
|
Taблицa 5 |
|
М, Нм (кгс∙м) |
Отсчет по шкале |
∆h = hn–hn-1 |
∆φ = ∆h/R |
|
индикатора h, мм |
||||
|
|
|
||
|
|
|
|
|
|
|
|
|
Такое нагружение продолжают до тех пор, пока прирост угловой деформации от нагружения малой ступенью не превысит примерно в два раза среднее значение приращения угловой деформации, полученное на предыдущих малых ступенях нагружения на линейном участке.
Модуль сдвига G в МПа (кгс/мм2) находят по формуле
G |
Ml0 |
, |
(28) |
|
Jp |
||||
|
|
|
где ∆М – большая ступень нагружения – крутящий момент на упругом участке нагружения (до предела пропорциональности), Нм (кгс∙м); ∆φ – средний прирост угла закручивания в радианах на расчетной длине l0, приходящийся на одну ступень нагружения ∆М на упругом участке нагружения; Jp – полярный момент инер-
ции, мм4.
Предел пропорциональности находят следующим образом: на участке, на котором еще не наблюдается отклонение от закона Гука, определяют средний угол закручивания на малую ступень на-
66
гружения. Найденную величину среднего угла закручивания нужно увеличить на 50 % в соответствии с принятым допуском. В ряду моментов при нагружении малыми ступенями находят ближайший к максимальному на линейном участке деформирования, при котором отмечается полуторократный прирост деформации на одну малую ступень нагружения. Этот момент принимается за Мпц. При необходимости уточнения значения Mпц допускается применение
линейной интерполяции. Предел пропорциональности при кручении пц в МПа (кгс/мм2) подсчитывают по формуле
пц Mпц/Wp .
Для определения предела текучести необходимо предварительно определить относительный сдвиг пц и показания индикатора
угломера, соответствующие пределу пропорциональности. Деформацию до предела пропорциональности считают упругой, а за пределом пропорциональности – упругопластической. Относительный сдвиг пц вычисляют по формуле
|
|
|
пцd |
(29) |
|
|
пц |
|
|
, |
|
|
|||||
|
|
2l0 |
|
где пц – угол закручивания на расчетной длине l0, определяемый как суммарный угол закручивания, соответствующий Mпц .
К вычисленному для предела пропорциональности относительному сдвигу пц прибавляют 0,003 (допуск 0,3 % на остаточный
сдвиг). Это означает, что угол закручивания пц на базе l0 должен быть увеличен на ∆φ=2 ∙ 0,003l0 /d=2 ∙ 0,003 ∙ 5/1 = 0,03 рад, а в пе-
ресчете на перемещение ножки индикатора угломера
∆h = ∆φR = 0,03 ∙ 40 =1,20 мм,
т.е. на 120 делений шкалы индикатора при цене деления 0,01 мм, базе индикаторного угломера l0 = 50 мм и диаметре образца
d = 10 мм.
Таким образом, для определения предела текучести нужно предварительно определить показание индикатора угломера, соответствующее остаточному сдвигу на уровне предела пропорциональности, прибавить к нему 120 делений. Затем, в процессе не-
67
прерывного монотонного нагружения образца зафиксировать показание стрелки диаграммного аппарата машины M0,3 при достиже-
нии зафиксированной деформации. Монотонное нагружение образца предпочтительно в связи с возникающей релаксацией напряжений и, соответственно, момента при остановке нагружения.
Предел текучести при кручении 0,3 вМПа (кгс/мм2) вычисляют по формуле 0,3 M0,3/Wp .
При выборе допуска на остаточную деформацию для определения предела текучести при напряженном состоянии, отличном от одноосного, принято, что он должен быть таким же, как при растяжении.
Известно, что при любом деформированном состоянии
max =εmax – εmin или max = ε1 – ε3,
где εmax и εmin ‒ экстремальные линейные деформации.
При одноосном растяжении остаточная деформация εmax, соответствующая пределу текучести σ0,2, равна 0,2 %, или 0,002. Тогда остаточная угловая деформация max составит 0,003, или 0,3 %, так
как из условия постоянства объема при пластическом деформиро-
вании ε1 + ε2 + ε3 = 0, ε2 = ε3 = ‒0,5 ε1 и γmax = 1,5 ε1. Таким образом,
принимается один и тот же допуск на остаточный сдвиг как при одноосном растяжении, так и чистом сдвиге.
Условный предел прочности при кручении пч в МПа (кгс/мм2) вычисляют по формуле пч Mк /Wp ,
где Mк – максимальный момент, предшествующий разрушению образца.
Сопоставим условный предел текучести материала, определенный при испытании образца на кручение, с действительным пределом текучести материала при сдвиге. Будем рассматривать кручение образца круглого сечения, изготовленного из идеально пластичного материала, диаграмма деформирования которого представлена на рис. 35,а.
68
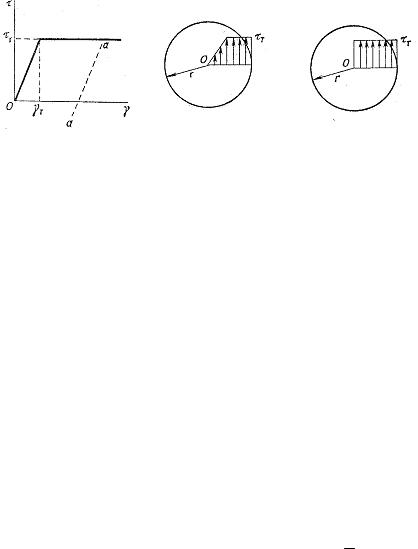
а |
б |
в |
Рис. 35
На рис. 35,б показано распределение касательных напряжений в сечении на стадии упругопластического деформирования. Во внутренней части круглого сечения сохраняется область упругого деформирования с максимальным радиусом rT. Во внешней зоне действует постоянное напряжение Т . Тогда результирующий крутящий момент Мк , будет равен
|
|
|
|
r |
3 |
R |
r |
3 |
|
2 |
T |
|
3 |
3 |
|
|
|
|
|
|
T |
r 2 rdr T r= T |
T |
|
|
|
|||||
|
Mк= T |
|
|
|
|
|
|
|
|
(R |
|
rT )= |
|||
|
2 |
|
2 |
|
3 |
|
|
||||||||
|
|
|
|
|
|
|
T |
|
|
|
|
|
|
|
|
|
2 |
R3 |
|
r3 |
|
|
|
|
|
|
|
|
|
|
|
= T |
( |
|
|
T |
). |
|
|
|
|
|
|
|
|
||
|
|
|
|
|
|
|
|
|
|
||||||
|
3 |
|
6 |
|
|
|
|
|
|
|
|
|
|
Условный предел текучести при кручении будет равен
|
|
|
M |
|
|
|
|
|
|
|
2 |
R3 |
r3 |
|
|
4 |
|
r3 |
|
|
|
|
T,кр |
= |
|
к |
= |
|
|
T |
|
( |
|
T |
)= |
T |
( |
|
|
T |
). |
(30) |
|
|
|
|
|
|
|
|
|||||||||||||||
|
|
Wp |
R3 |
|
|
3 |
|
6 |
|
|
3 |
|
3R3 |
|
|
||||||
|
|
|
|
|
|
|
2 |
|
|
|
|
|
|
|
|
|
|
|
|
|
|
Таким образом, допуск на остаточную деформацию при кручении бруса круглого поперечного сечения определяется размером rT, который может принимать значения в диапазоне 0 ≤ rT ≤ R. В этом
4
случае T,кр будет изменяться в пределах Т ≤ T,кр ≤ 3 T , т.е. ус-
ловный предел текучести при кручении всегда больше действительного предела текучести при чистом сдвиге. Реально предел текучести при кручении, определенный по допуску 0,3 %, на 15 %
69

больше действительного предела текучести Т , определенного при чистом сдвиге.
1.4.3. Построение диаграммы деформации при чистом сдвигеmax – γmax (tmax – gmax) по результатам испытания на кручение
цилиндрического образца из пластичногоматериала
Предполагается, что зависимость между касательным напряжением и угловой деформацией есть монотонно возрастающая
функция = ( ), что отражает условия деформационного упрочнения.
Выразим крутящий момент Mк через напряжение , действующее в поперечном сечении радиуса R в площадке dF на расстоянии r от центра круга:
Mк = rdF ,
F
где dF – элементарная площадка, равная dF = 2 rdr.
В свою очередь, выразим момент Mк в зависимости от , учи-
тывая, что r = , а dr = d ,
|
R |
|
|
|
d |
|
|
|
|
|
|
|
|
|
R |
|
|
|
Mк = |
2 |
|
( ) |
|
, или Mк∙ 3 = 2 ( ) 2d . |
|
||||||||||
|
|
|
|
|
|
||||||||||||
|
0 |
|
|
|
|
|
0 |
|
|||||||||
Продифференцируем последнее выражение по . |
|
||||||||||||||||
|
|
|
Mк3 2 |
3 |
|
dMк |
2 max R2 2R , |
|
|||||||||
|
|
|
|
|
|
||||||||||||
|
|
|
|
|
|
|
|
|
|
|
|
|
d |
|
|||
откуда |
|
max |
1 |
|
(3Mк |
dMк |
) |
(31) |
|||||||||
|
|
|
|
||||||||||||||
|
|
|
|
|
|
2 R3 |
|
|
|
d |
|
||||||
при max |
R. |
|
|
|
|
|
|
|
|
|
|
Таким образом, диаграмму кручения образца Mк‒ можно перестроить в диаграмму истинных напряжений max max , учиты-
вающую перераспределение касательных напряжений в сечении с учетом пластической деформации. Для каждого значения и соответствующего ему угла закручивания φ определяют max и max .
70