
Методическое пособие 799
.pdf
Рис. 1.30. "Бегунок", перемещая который можно проконтролировать процесс обработки в динамике
Рис.1.31. Команда "Постобработка"
Вопросы для контроля
1.Как происходит переход к работе в среде Inventor HSM?
2.Какое условие рекомендуется соблюдать на начальном этапе проектирования модели в Inventor для удобства дальнейшей работы и почему?
3.Как осуществляется доступ к библиотеке инструментов?
4.Для чего нужен журнал операции?
5.Как осуществляется визуальный контроль спроектированной опера-
ции?
21

ЛАБОРАТОРНАЯ РАБОТА № 2
Построение технологии двухкоординатной (2D) фрезерной обработки. Знакомство с понятием "Постобработка"
Цель работы: получить навык в проектировании стратегии двухкоординатной фрезерной обработки и создании УП на основе постобработки.
Содержание работы
2.1. Подготовка модели детали
Используя инструменты моделирования, создайте 3D модель детали по чертежу, представленному на рис. 2.1. В результате Вы должны получить деталь, представленную на рис. 2.2. Сохраните ее под именем "Postprocess" в папке проекта "CAM".
Замечание: При создании модели обращаем особое внимание на расположение осей координат (ось Z направлена параллельно оси вращения фрезы), как это было указано в Лабораторной работе 1.
Рис. 2.1. Чертеж детали для выполнения Лабораторной работы № 2
22

Рис. 2.2. Модель детали для выполнения Лабораторной работы № 2
После того, как была создана модель детали, следует переходить к моделированию технологического процесса механообработки. Это необходимо сделать в несколько этапов:
1.Определить параметры заготовки, так как на рабочее место станочника деталь приходит в виде далеком от конечной формы
2.Определить последовательность операций по удалению лишнего слоя материала.
2.2. Определение параметров заготовки
Рассмотрим первый этап, а именно определим параметры заготовки.
Замечание. Общие сведения о заготовках: Заготовки деталей получают на заготовительном производстве в виде проката или с помощью литья, ковки, штамповки, прессования, волочения и т.д. Заготовки бывают металлические и неметаллические.
Неметаллические заготовки в основном получают из пластмасс - синтетических веществ органического происхождения методом литья, прессования и выдавливания (экструзии).
К металлическим заготовкам относят прокат из стали и цветных металлов простых и сложных профилей в виде прутков и труб, поковки, листовая штамповка, отливки. В большинстве случаев в качестве заготовки для операций механообработки материал поставляется в виде сортового проката (лист, круг, пруток и т.п.).
Детали типа валов, втулок, шайб и колец изготовляют из заготовок, поставляемых в виде круглых, шестигранных и квадратных прутков. Крупные и сложные по форме детали получают из штучных заготовок литьем, ковкой или штамповкой.
Выбор вида заготовки (прутков круглого, шестигранного или квадратного сечений, поковки, отливки и т.д.) зависит от конструктивных особен-
23

ностей деталей. Например, болт с шестигранной головкой целесообразно изготовлять из шестигранного прутка, а не из круглого.
Заготовка должна иметь большие размеры, чем готовая деталь, т.е. предусматривается слой металла, снимаемый при механической обработке. Этот слой металла называется припуском на обработку. Его величина должна быть наименьшей, но при этом обеспечивать получение годной детали, т.е. заготовка по форме и размерам должна приближаться к форме и размерам готовой детали.
Применительно к рассматриваемому примеру в качестве заготовки выберем прямоугольную призму, размеры которой будут превышать габаритные размеры детали на 2 мм "на сторону". Размер детали по оси Х составляет 228,16 мм, следовательно, размер заготовки по этой оси будет не менее
228,16 + 2 + 2 = 232,16 мм (см. рис. 2.3); по оси Y не менее 160,16 + 2+ 2 =
164,16 мм, и по оси Z будем считать, что механическая обработка будет производится только со стороны расположения фигурного паза, т.е. размер заготовки 29,2 + 2 = 31,2 мм. Это нам потребуется при проектировании процесса механической обработки данной детали.
Рис. 2.3. Габаритные размеры детали
Для этого перейдем на вкладку "САМ" (рис. 2.4). Выберем команду "Настройка" и в открывшемся диалоговом окне выберем команду "Заготовка". На данной вкладке появляется возможность настройки формы и размеров заготовки в зависимости от имеющегося оборудования и возможностей производственных мощностей (рис. 2.5).
Замечание. Выбор формы и метода заготовки обосновывается путем технологических расчетов исходя из понятия "технологической наследственности", которое рассматривается в курсе "Технология машиностроения", что
24
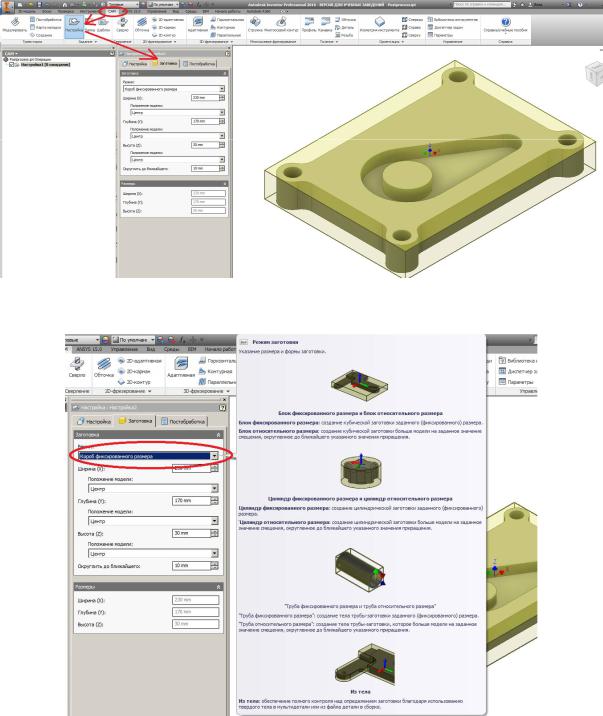
не входит в задачи настоящего пособия. В нашем случае размеры и форма заготовки назначаются исходя из учебных целей.
Рис. 2.4. Настройка вида заготовки для механической обработки детали
Рис. 2.5. Варианты выбора вида заготовки
Для условий лабораторной работы выбираем "Режим" заготовки – "короб относительного размера". Это позволит нам назначать необходимый припуск относительно габаритных размеров детали (рис. 2.6). Выбираем
"Режим смещения заготовки" – "Добавить припуск по сторонам и свер-
ху-снизу". Это дает возможность назначать симметричный припуск "на сторону" (т.е. по осям X и Y) и ассиметричный припуск по высоте (по оси Z).
25

Выставим значения параметров припуска "Боковое смещение" и "Смещение сверху" равным 2 мм, "Смещение снизу" – 0 мм, "Округлить до ближайшего" – 1 мм (рис. 2.6 и 2.7). Параметр "Смещение снизу" принят нами исходя из условия того, что нижняя грань заготовки совпадает с нижней гранью детали, т.е. она была обработана на этапе заготовительного производства и конструкторская и технологическая базы совпадают.
Замечание. Как правило, на предварительных этапах механической обработки добиваются либо совмещения, либо формирования технологических и конструкторских баз, но в данной лабораторной работе этот момент не рассматривается.
Параметр "Округлить до ближайшего" равный 1 мм позволяет округлять размеры до ближайшего большего целого значения (рис. 2.6).
Рис. 2.6. Настройка размеров заготовки
Рис. 2.7. Вид заготовки с припуском для механической обработки по оси Y и Z
На этом настройка параметров заготовке закончена, переходим к построению маршрутной технологии механообработки.
26

2.3. Разработка технологии механообработки детали
На данном этапе следует определить наиболее целесообразную последовательность механической обработки заготовки, которая обеспечит удовлетворение технических требований конструкторской документации (рабочего чертежа) по физико-механическим свойствам и конструктивнотехнологическим параметрам (точность размеров, микрорельеф и т.д.). Различают маршрутную и операционную технологии. Процесс их разработки подробно рассматривается в курсах "Основы технологии машиностроения" и "Технология машиностроения". Для наших целей достаточно будет принять логически обоснованную последовательность технологических операций, а именно:
- фрезерование верхней грани заготовки до получения нужной высоты готовой детали, равной 29,2 мм. Для этого нами будет использован инстру-
мент "Обточка" ; - фрезерование внешнего контура детали, используется инструмент
"2D-контур" ;
- обработка внутреннего фасонного углубления – кармана, для которо-
го используется инструмент "2D-карман" ;
- разметка 4-х отверстий (цековка), используется инструмент "Сверло"
;
- сверление 4-х ступенчатых отверстий, используется инструмент
"Сверло" .
2.3.1. Назначение режимов и моделирование перехода "Обточка"
На данном переходе следует выполнить удаление припуска с верхней плоскости детали с целью получения высоты по оси Z 29,2 мм и обеспечения параллельности верхней и нижней плоскостей заготовки.
Выберите на ленте в панели "2D-фрезерование" инструмент "Обточ-
ка" .
В браузере будет создан новая операция обточки и откроется диалоговое окно "Обточка" (рис. 2.8). Все вкладки диалогового окна "Обточка" разделены на несколько групп, в которых можно выбрать инструмент, изменить параметры управления траекторией перемещения инструмента, а также выбрать фактическую геометрию для обработки.
Аналогично Лабораторной работе 1 произведем выбор инструмента для данной операции из "Библиотеки инструментов". В качестве рабочего инструмента принимаем торцевую фрезу Ø50 мм (рис. 2.9).
27

Рис. 2.8. Создание нового перехода "Обточка"
Рис. 2.9. Выбор инструмента для операции "Обточка"
Переходим на закладку "Геометрия" , в которой определяется размер заготовки, отображаемый оранжевым контуром на детали (рис. 2.10). В нашем случае заготовка уже определена и ее контуры подходят для использования, и поэтому их не нужно переопределять вручную.
28

Рис. 2.10. Результат определения "Геометрии" для операции "Обточка"
Закладка "Значения высоты" позволяет настраивать технологически необходимые значения подвода, отвода и работы инструмента. В нашем случае они корректно определены автоматически и в изменениях не нуждаются.
Переходим на закладку "Проходы" , которая предназначена для фактического управления траекторией перемещения инструмента при обточке. Изменим параметр "Продление прохода" на значение 5 мм. Это необходимо, что бы обеспечить выход инструмента фреза за границы контура детали и гарантированного удаления припуска на лицевой поверхности детали (рис. 2.11).
Рис. 2.11. Задание величины "Продления прохода" за границы контура детали
После настройки всех параметров запускаем автоматический расчет траектории перемещения инструмента, нажав кнопку "ОК" в нижней части диалогового окна.
29

Траектория перемещения инструмента рассчитывается, в окне Браузера отражается результат построения траектории, а в графическом окне доступен предварительный просмотр (рис. 2.12).
а)
б)
Рис. 2.12. Результат построения рабочей траектории операции "Обточка": а) собственно траектория; б) траектория с инструментом
В графической области участки траектории, где происходит резка материала, выделены синим цветом, перемещения подвода и отвода инструмента зеленым цветом, а быстрые перемещения - желтым цветом. Начало и конец траектории перемещения инструмента обозначены красным и зеленым треугольником соответственно.
2.3.2. Назначение режимов и моделирование перехода "2D-контур"
Произведем моделирование фрезерной обработки наружного контура детали. Для этого используется инструмент "2D-фрезерование" "2D-
контур" .
Аналогично пункту 3.1 проведем выбор инструмента.
30