
2293
.pdfПробы газа для анализа отбираются газозаборными устройствами в середине боковых горизонтальных участков трубопровода на входе и выходе из аппаратов и турбодетандера. Перед отбором пробы заборная система должна подвергаться продувке.
Компонентный состав продуктов сгорания топлива может определяться и косвенным методом. Согласно формулам подразд. 4.1 состав ПСТ является однозначной функцией коэффициента избытка воздуха для определенного вида сжигаемого топлива. Коэффициент
= G / GОК ,
где G – масса воздуха, участвующего в процессе горения; GОК = m L0 – масса воздуха, необходимая для окисления m килограммов топлива; L0 – масса воздуха, необходимая для сжигания 1 кг топлива, зависящая от состава сжигаемого топлива.
Расход m топлива через газотурбогенератор определяется с помощью штрих-пробера и секундомера.
Определив в процессе эксперимента состав и массу сжигаемого топлива и расход G воздуха по формулам подразд. 4.1, найдем компонентный состав рабочего вещества на входе в турбодетандер.
Измерение влажности воздуха производится аспирационным психрометром Ассмана. Принцип действия психрометра основывается на измерении разности температур в потоке воздуха: температуры сухого термометра (реальная температура влажного воздуха) и температуры влажного термометра (температура полностью увлажненной поверхности, с которой вода испаряется в ненасыщенный влажный воздух).
В табл. П3 представлены перечень измеряемых параметров, необходимых для определения характеристик турбодетандера и его элементов, пределы измерений, абсолютные максимальные и средние квадратичные относительные погрешности. Размерность указана в единицах, в которых считываются показания приборов.
5.3. Экспериментальное исследование и тепловой баланс ТХЭА на режимах получения холода и твердого диоксида углерода
Экспериментальное исследование проводилось с целью выявления основных параметров ТХЭА при комплексном производстве теплоты и холода (СО2) за счет глубокого охлаждения продуктов сгорания с утилизацией высшей теплотворной способности топлива. В качестве топлива применялся керосин.
150
|
|
|
Таблица 5.1 |
|
Основные параметры работы экспериментального ТХЭА |
||||
|
|
|
|
|
Параметры работы агрегата |
Обозна- |
Единицы |
|
Вели- |
|
чение |
измерения |
|
чина |
Расход: |
G |
|
|
|
воздуха |
кг/c |
|
1,81 |
|
воды |
vW |
м3/ч |
|
23,4 |
топлива |
GТ |
кг/ч |
|
124 |
Температура газов: |
Т0 |
|
|
|
на входе в нагнетатель |
К |
|
303 |
|
на выходе из нагнетателя |
Т1' |
К |
|
365 |
на входе в тазотурбонагнетатель |
Т1 |
К |
|
305 |
на выходе из турбины |
Т4 |
К |
|
960 |
за напорным теплоутилизатором |
Т5' |
К |
|
303 |
на входе в турбодетандер |
Т6 |
К |
|
264 |
за турбодетандером |
Т7 |
К |
|
223 |
на выходе из регенератора |
Т9 |
К |
|
298 |
окружающей среды |
ТОС |
К |
|
303 |
Температура воды: |
ТW1 |
|
|
|
на входе в напорный теплоутилизатор |
К |
|
285 |
|
на выходе из напорного теплоутилизатора |
TW2 |
К |
|
358 |
Давление газов: |
р0 |
|
|
|
на входе в нагнетатель |
МПа |
|
0,101 |
|
на выходе из нагнетателя |
р1 |
МПа |
|
0,165 |
в камере сгорания |
р3 |
МПа |
|
0,543 |
за газотурбогенератором |
р4 |
МПа |
|
0,285 |
на входе в турбодетандер |
р6 |
МПа |
|
0,277 |
на выходе из турбодетандера |
р7 |
МПа |
|
0,111 |
атмосферное |
р0 |
МПа |
|
0,1013 |
Коэффициент избытка воздуха |
a |
|
|
3,26 |
Влагосодержание: |
g |
|
|
|
за газотурбогенератором (массовое) |
% |
|
2,33 |
|
за экономайзером |
d5' |
г/кг |
|
12,4 |
на входе в турбодетандер |
d6 |
г/кг |
|
2,30 |
на выходе из турбодетандера |
d7 |
г/кг |
|
1,0 |
Газовый состав продуктов сгорания топлива: |
gN |
|
|
|
массовая концентрация азота |
% |
|
78 |
|
массовая концентрация кислорода |
gO |
% |
|
16,0 |
массовая концентрация диоксида углерода |
gC |
% |
|
5,3 |
Степени повышения и понижения давлений |
|
|
|
|
в турбомашинах: |
|
|
|
|
в нагнетателе |
H |
|
|
1,65 |
в компрессоре |
К |
|
|
3,5 |
в турбине |
Т |
|
|
1,9 |
в детандере |
Д |
|
|
2,49 |
151 |
|
|
|
|
При испытании режим работы ТХЭА, основные параметры которого приведены в табл. 5.1, поддерживался постоянным. Степень повышения давления в нагнетателе Н = 1,65, в компрессоре газотурбогенератора (ГТГ) К = 3,5, а также степень расширения в турбине ГТГ Т = 1,9 соответствовала расчетным значениям. Температура продуктов сгорания топлива на выходе из турбины ГТГ составила Т4 = 960 К, температура в камере сгорания, полученная расчетным путем, Т3 = 1100 К.
В ТХЭА происходит процесс глубокого охлаждения продуктов сгорания топлива. При охлаждении в напорном утилизаторе теплоты температура продуктов сгорания снижалась с Т4 = 960 К на входе до 293 303 К на выходе, при этом охлаждающая вода подогревалась с 280 285 К на входе в напорный утилизатор теплоты до 350 358 К на выходе. Среднестатистическое значение давления продуктов сгорания на входе в турбодетандер при испытании составило р6 = 0,277 МПа.
Гидравлические потери на участке от газовой турбины до турбодетандера, т.е. в напорном утилизаторе теплоты, влагоотделителе и регенераторах прямого хода, составили в среднем 0,009 МПа, превысив расчетные значения на 0,002 МПа. Регенераторы обратного хода более чувствительны к изменению режима работы, так как работают при пониженном давлении, следовательно, обладают большим гидравлическим сопротивлением. Среднестатистическое значение давления потока на выходе из турбодетандера составило величину р7 = 0,11 МПа. Общее гидравлическое сопротивление регенераторов и циклона составило 0,01 МПа, что превышает расчетное значение потерь на 0,002 МПа. При снижении температуры потока на входе в турбодетандер с Т6 = 293 К до 156 К повышения давления на выходе из турбодетандера отмечено не было. Это подтверждает, что гидравлическое сопротивление регенераторов оставалось практически постоянным, следовательно, регенераторы в период проведения испытаний водным льдом не забивались. Вынос влаги из регенераторов осуществлялся обратным потоком. Регенераторы полностью справлялись с нагрузкой, на что указывает наличие обычной для их работы недорекуперации на теплом конце, составляющей ТР = 5 К. Степень расширения продуктов сгорания топлива в турбодетандере при изменении температуры на входе оставалась практически постоянной. Среднестатистическая величина Д = 2,49, вместо 2,74 по расчету, что связано с увеличением потерь в теплообменных аппаратах ТХЭА.
Основные параметры работы ТХЭА позволили составить баланс мощности агрегата, расчет которого сведен в табл. 5.2. Снижение Д с 2,74 до 2,49 привело к увеличению мощности, потребляемой электродвигателем из сети, до 20,15 кВт.
152
Таблица 5.2
Баланс мощности ТХЭА
Наименование |
|
|
|
|
|
|
|
|
|
|
|
|
|
|
|
|
|
|
|
|
|
|
|
|
|
|
|
|
|
|
|
|
|
|
|
|
|
|
|
|
|
|
|
|
Ед. |
Вели- |
расчетных величин |
|
|
|
|
|
|
|
|
Расчетная формула |
|
|
|
|
|
|
|
|
|
|
|
|
|
|
изм. |
чина |
|||||||||||||||||||||
1 |
|
|
|
|
|
|
|
|
|
|
|
|
|
|
|
|
|
|
2 |
|
|
|
|
|
|
|
|
|
|
|
|
|
|
|
|
|
|
|
|
|
|
3 |
4 |
|||
Мощность турбонагне- |
|
|
|
|
|
|
|
|
|
|
|
|
|
|
|
|
|
|
|
|
|
|
|
|
|
к 1 |
|
|
|
|
|
|
|
|
|
|
|
|
|
кВт |
104,1 |
|||||
|
|
|
|
|
|
|
|
|
|
|
|
|
|
|
|
|
|
|
|
|
|
|
|
|
|
|
|
|
|
|
|
|
|
|
||||||||||||
|
|
|
|
|
|
|
|
|
|
|
|
|
|
|
|
|
|
|
|
|
к |
|
|
|
|
|
|
|
|
|
|
|||||||||||||||
тателя |
|
|
|
|
|
|
|
|
|
|
|
|
|
|
|
|
к |
|
|
|
|
р1' |
|
|
|
|
|
|
|
|
1 |
|
|
|
|
|
|
|||||||||
|
|
|
|
|
|
|
|
|
|
|
|
|
|
|
|
|
|
|
|
|
|
|
|
|
|
|
|
|
|
|
|
|
|
|
|
|
||||||||||
|
|
NК GRT0 |
|
|
|
|
|
|
|
|
|
|
|
|
|
|
|
|
1 |
|
|
|
|
|
|
|
|
|
|
|||||||||||||||||
|
|
|
|
|
|
|
|
|
|
|
|
|
|
|
|
|
|
|
|
|
|
|
|
|
||||||||||||||||||||||
|
|
|
|
|
|
|
|
|
|
|
|
|
|
|
|
|
|
|
|
|
|
|
|
|
|
|
|
|
|
|
|
|
|
|
|
|
|
|
|
|
|
|
||||
|
|
|
|
|
|
|
|
|
|
|
|
|
|
к 1 |
|
p0 |
|
|
|
|
|
|
|
|
Н |
|
|
|
|
|
||||||||||||||||
|
|
|
|
|
|
|
|
|
|
|
|
|
|
|
|
|
|
|
|
|
|
|
|
|
|
|
|
|
||||||||||||||||||
|
|
|
|
|
|
|
|
|
|
|
|
|
|
|
|
|
|
|
|
|
|
|
|
|
|
|
|
|
|
|
|
|
|
|
|
|
|
|
|
|
|
|||||
|
|
|
|
|
|
|
|
|
|
|
|
|
|
|
|
|
|
|
|
|
|
|
|
|
|
|
|
|
|
|
|
|
|
|
|
|
|
|
|
|
|
|
||||
|
|
|
N |
|
|
GRT |
|
|
|
к |
|
|
|
|
к 1 |
|
|
1 |
|
|
|
|
|
|
|
|
282,1 |
|||||||||||||||||||
Мощность компрессо- |
|
|
K |
|
|
|
|
|
|
|
|
|
к |
1 |
|
|
|
|
|
|
|
|
|
|
кВт |
|
||||||||||||||||||||
|
|
|
|
|
|
|
|
|
|
|
|
|
|
|
|
|
||||||||||||||||||||||||||||||
ра |
|
|
|
|
|
|
|
|
|
|
|
1 |
|
к 1 |
|
|
К |
|
|
|
|
|
|
|
К |
|
|
|
|
|
|
|
|
|||||||||||||
|
|
|
|
|
|
|
|
|
|
|
|
|
|
|
|
|
|
|
|
|
|
|
|
|
|
|
|
|
|
|
|
|
|
|||||||||||||
Температура в камере |
|
|
|
T3 |
|
|
|
|
|
|
|
|
|
|
|
|
|
|
T4 |
|
|
|
|
|
|
|
|
|
|
|
|
|
|
|
|
|
|
|
|
|
||||||
|
|
|
|
|
|
|
|
|
|
|
|
|
кПС 1 |
|
|
|
|
|
|
|
|
|
|
|
|
|
|
|
|
|
|
|
|
|
|
|||||||||||
сгорания |
|
|
|
|
|
|
|
|
|
|
|
p4 |
|
|
|
|
|
|
|
|
|
|
|
|
|
|
|
|
|
|
|
|
|
|
|
|
|
|
К |
1100 |
||||||
|
|
|
|
|
|
|
|
|
кПС |
|
|
|
|
|
|
|
|
|
|
|
|
|
|
|
|
|
|
|
|
|
||||||||||||||||
|
|
|
|
|
|
|
|
|
|
|
|
|
|
|
|
|
|
Т |
|
1 Т |
|
|
|
|
|
|
|
|
|
|
||||||||||||||||
|
|
|
|
|
|
|
|
|
|
|
|
|
|
|
|
|
|
|
|
|
|
|
|
|
|
|
||||||||||||||||||||
|
|
|
|
|
|
|
|
|
|
|
|
|
|
|
|
|
|
|
|
|
|
|
|
|
|
|
|
|
|
|
|
|||||||||||||||
|
|
|
|
|
|
|
|
|
|
|
|
p3 |
|
|
|
|
|
|
|
|
|
|
|
|
|
|
|
|
|
|
|
|
|
|
|
|
|
|
|
|
||||||
|
|
NПТ |
|
|
|
|
|
|
|
|
|
|
|
|
|
|
|
|
|
|
|
|
|
|
|
|
|
|
|
|
|
|
|
|
|
|
|
|
|
|
|
|
|
|||
Полная мощность тур- |
|
|
|
|
|
|
|
|
|
|
|
|
|
кПС |
|
|
|
|
|
|
р4 |
|
|
|
кПС 1 |
|
|
|
|
кВт |
300,2 |
|||||||||||||||
|
|
|
|
|
|
|
|
|
|
|
|
|
|
|
|
|
|
|
|
|
|
|||||||||||||||||||||||||
бины |
|
|
|
|
|
|
|
|
|
|
|
|
|
|
|
|
|
|
|
кПС |
|
|
|
|
|
|
|
|||||||||||||||||||
|
|
G |
ПС |
R |
ПС |
T |
|
|
|
|
|
|
|
|
|
|
|
|
|
1 |
|
|
|
|
|
|
|
|
|
|
Т |
|
|
|||||||||||||
|
|
|
|
|
|
|
|
|
|
|
|
|
|
|
|
|
|
|
|
|
|
|
|
|
||||||||||||||||||||||
|
|
|
|
3 |
|
кПС |
1 |
|
|
|
|
|
р3 |
|
|
|
|
|
|
|
|
|
|
|
||||||||||||||||||||||
|
|
|
|
|
|
|
|
|
|
|
|
|
|
|
|
|
|
|
|
|
|
|
|
|
|
|
|
|
|
|
||||||||||||||||
|
|
|
|
|
|
|
|
|
|
|
|
|
|
|
|
|
|
|
|
|
|
|
|
|
|
|
|
|
|
|
|
|
|
|
|
|
|
|
|
|
|
|
|
|
||
Полезная мощность |
|
NT |
|
|
|
|
|
|
|
|
|
|
|
|
|
|
|
|
|
|
|
|
|
|
|
|
|
|
|
|
|
|
|
|
|
|
|
|
|
|
|
|
|
|
|
|
|
|
|
|
|
|
|
|
|
|
|
|
|
|
|
|
|
|
|
|
|
|
|
|
|
|
|
|
|
|
|
кПС 1 |
|
|
|
|
|
|
|||||||||
турбины |
|
|
|
|
|
|
|
|
|
|
|
|
|
|
|
|
|
|
|
|
|
|
|
|
|
|
|
|
|
|
|
|
|
кВт |
286,9 |
|||||||||||
|
|
|
|
|
|
|
|
|
|
|
|
кПС |
|
|
|
|
1 |
|
|
кПС |
|
|||||||||||||||||||||||||
|
|
|
|
|
|
|
|
|
|
|
|
|
|
|
|
|
|
|
|
|
|
|
|
|
|
|
||||||||||||||||||||
|
|
G |
ПС |
R |
ПС |
T |
|
|
|
|
|
|
|
|
|
|
|
1 |
|
|
|
|
|
|
|
|
|
|
|
Т |
|
|
||||||||||||||
|
|
|
|
|
|
|
|
|
|
|
|
|
|
|
|
|
|
|
|
|
|
|
||||||||||||||||||||||||
|
|
|
|
|
|
|
3 |
|
кПС |
1 |
|
|
|
|
|
|
|
|
|
|
|
|
|
|
|
|
||||||||||||||||||||
|
|
|
|
|
|
|
|
|
|
|
|
|
|
|
|
T |
|
|
|
|
|
|
|
|
|
|
|
|
|
|||||||||||||||||
|
|
|
|
|
|
|
|
|
|
|
|
|
|
|
|
|
|
|
|
|
|
|
|
|
|
|
|
|
|
|
|
|
|
|
|
|
|
|
|
|
|
|
|
|
||
Потери мощности тур- |
|
|
|
|
|
|
|
|
|
|
|
|
|
|
|
|
|
|
|
|
|
|
|
|
|
|
|
|
|
|
|
|
|
|
|
|
|
|
|
|
|
|
|
|
|
|
бины на гидравличе- |
|
|
|
|
|
|
|
|
|
|
|
NТ =NПТ NТ |
|
|
|
|
|
|
|
|
|
|
|
|
|
|
|
|
кВт |
13,3 |
||||||||||||||||
ские сопротивления |
|
NНД |
|
|
|
|
|
|
|
|
|
|
|
|
|
|
|
|
|
|
|
|
|
|
|
|
|
|
|
|
|
|
|
|
|
|
|
|
|
|
|
|
|
|||
Полная мощность тур- |
|
|
|
|
|
|
|
|
|
|
|
|
|
|
|
|
|
|
|
|
|
|
|
|
|
|
|
|
|
|
|
|
|
|
|
|
|
|
|
|
|
|
||||
|
|
|
|
|
|
|
|
|
|
|
|
|
|
|
|
|
|
|
|
|
|
|
|
|
|
|
|
|
|
|
кПС 1 |
|
|
|
|
|
|
|||||||||
бодетандера |
|
|
|
|
|
|
|
|
|
|
|
|
|
кПС |
|
|
|
|
|
|
р0 |
|
|
|
|
|
кВт |
96,1 |
||||||||||||||||||
|
|
|
|
|
|
|
|
|
|
|
|
|
|
|
|
|
|
|
кПС |
|
|
|
|
|
|
|
|
|
||||||||||||||||||
|
|
G |
ПС |
R |
ПС |
T |
|
|
|
|
|
|
|
|
|
|
|
|
|
1 |
|
|
|
|
|
|
|
|
|
|
|
Д |
|
|
||||||||||||
|
|
|
|
|
|
|
|
|
|
|
|
|
|
|
|
|
|
|
|
|
|
|
|
|
||||||||||||||||||||||
|
|
|
|
6 |
|
кПС |
1 |
|
|
|
|
р6 |
|
|
|
|
|
|
|
|
|
|||||||||||||||||||||||||
|
|
|
|
|
|
|
|
|
|
|
|
|
|
|
|
|
|
|
|
|
|
|
|
|
|
|
|
|
||||||||||||||||||
|
|
|
|
|
|
|
|
|
|
|
|
|
|
|
|
|
|
|
|
|
|
|
|
|
|
|
|
|
|
|
|
|
|
|
|
|
|
|
|
|
|
|
|
|
||
|
|
|
|
|
|
|
|
|
|
|
|
|
|
|
|
|
|
|
|
|
|
|
|
|
|
|
|
|
|
|
|
|
|
|
|
|
|
|
|
|
|
|
|
|
|
|
153

Окончание табл. 5.2
1 |
|
|
|
|
|
|
|
2 |
|
|
|
|
|
|
|
|
3 |
4 |
||
|
NД |
|
|
|
|
|
|
|
|
|
|
|
|
|
|
|
|
|
|
|
Полезная мощность |
|
|
|
|
|
|
|
|
|
|
|
|
|
|
|
кПС 1 |
|
|
кВт |
88,1 |
|
|
|
|
|
|
кПС |
|
|
|
|
1 кПС |
|||||||||
турбодетандера |
|
|
|
|
|
|
|
|
|
|
|
|
|
|
|
|||||
|
G |
ПС |
R |
ПС |
T |
|
|
|
|
|
1 |
|
|
|
|
Д |
|
|
||
|
|
|
|
|
|
|
|
|
||||||||||||
|
|
|
6 |
|
|
|
|
|
|
|
|
|
|
|
|
|
||||
|
|
|
|
|
|
|
кПС 1 |
|
Д |
|
|
|
|
|||||||
|
|
|
|
|
|
|
|
|
|
|
|
|
|
|
|
|
|
|
|
|
Потери мощности тур- |
|
|
|
|
|
|
|
|
|
|
|
|
|
|
|
|
|
|
|
|
бодетандера на гидрав- |
|
|
|
|
|
|
NД = NП - N |
|
|
|
|
|
|
кВт |
8,04 |
|||||
лические сопротивле- |
|
|
|
|
|
|
|
|
|
|
|
|
|
|
|
|
|
|
|
|
ния |
|
|
|
|
|
|
|
|
|
|
|
|
|
|
|
|
|
|
|
|
Мощность, потребляе- |
|
|
|
|
|
|
|
|
|
|
|
|
|
|
|
|
|
|
|
|
мая электродвигателем |
|
|
|
|
NПЭ = |
|
|
IU cos |
|
|
кВт |
20,15 |
||||||||
|
|
|
|
|
3 |
|
||||||||||||||
из сети |
|
|
|
|
|
Э = NЭ / NПЭ |
|
|
|
|
||||||||||
Полный КПД электро- |
|
|
|
|
|
|
|
- |
0,91 |
|||||||||||
двигателя |
|
|
|
|
|
|
|
|
|
|
|
|
|
|
|
|
|
|
|
|
Баланс мощности: |
|
|
|
|
|
|
|
|
|
|
|
|
|
|
|
|
|
|
|
|
а) подведенная мощ- |
|
|
|
NПОДВ = NПТ – NПД + NЭ |
|
|
кВт |
414,6 |
||||||||||||
ность; |
|
|
|
|
|
|
|
|
|
|
|
|
|
|
|
|
|
|
|
|
б) отведенная мощ- |
|
|
|
|
|
|
|
|
|
|
|
|
|
|
|
|
|
|
|
|
ность с учетом меха- |
|
|
NОТВ = (NH + NK + N) / М |
|
|
кВт |
411,6 |
|||||||||||||
нического КПД |
|
|
|
|
|
|
|
|
|
|
|
|
|
|
|
|
|
|
|
|
Погрешность баланса |
|
|
|
|
NПОДВ NОТВ |
100 |
|
|
% |
0,74 |
||||||||||
|
|
|
|
|
||||||||||||||||
мощности |
|
|
|
|
|
|
NОТВ |
|
|
|
|
|
|
|
|
|
Баланс теплоты, включающей основные процессы ее подвода и отвода, представлен в табл. 5.3. Анализ показывает, что в ТХЭА осуществляется утилизация высшей теплотворной способности топлива. При этом теплота конденсации водяных паров, образовавшихся при сгорании топлива, полезно используется в экономайзере для получения горячей воды. В условиях проведенных экспериментов конденсация паров начиналась при температурах, на 5 10 К превышающих температуру точки росы в обычных условиях. Это подтверждается количеством конденсата и балансом сконденсировавшихся водяных паров. В условиях повышенного давления становится возможным охладить продукты сгорания топлива до температуры окружающей среды, т.е. полезно использовать весь имеющийся температурный напор.
154
Таблица 5.3
Тепловой баланс ТХЭА
|
Наименование |
|
|
|
|
Ед. |
Вели- |
|
расчетных величин |
Расчетная формула |
изм. |
чина |
|||||
Высшая |
теплотворная |
способ- |
|
gТ |
кДж/кг |
46154 |
||
ность топлива (керосин) |
|
|
|
|
|
|
||
Коэффициент полноты |
сгорания |
|
Т |
|
0,98 |
|||
топлива |
|
|
|
|
|
|
|
|
Подвод теплоты при сгорании то- |
QТ = GTgT T / 3600 |
кВт |
1567 |
|||||
плива |
|
|
|
Q0ВП = GПС r (d0 – d8) |
|
|
||
Подвод |
теплоты кристаллизации |
кВт |
6,4 |
|||||
водяных паров |
|
QР = GПС сР (ТР – ТОС) |
|
|
||||
Недорекуперация на теплом кон- |
кВт |
8,9 |
||||||
це регенераторов |
|
|
|
|
|
|
||
Подвод |
теплоты в холодильную |
Q0ИЗ = ИЗ F0 TCP |
кВт |
0,2 |
||||
камеру через теплоизоляцию |
|
|
|
|
|
|||
Подвод |
теплоты в холодильной |
Q0 = NД – Q0ВП QP – Q0ИЗ |
кВт |
28,1 |
||||
камере |
|
(холодопроизводитель- |
|
|
|
|
|
|
ность) |
|
|
|
|
|
|
|
|
Подвод энергии на привод турбо- |
NЭ = NПН NД |
кВт |
18,34 |
|||||
нагнетателя |
|
QЭ = GПС сР (Т4 – Т5') |
|
|
||||
Отвод |
теплоты в экономайзере |
кВт |
1407 |
|||||
без учета |
конденсации |
водяных |
|
|
|
|
|
|
паров |
|
|
|
QЭВП = GПС r (d5' – d5) |
|
|
||
Отвод |
теплоты в экономайзере |
кВт |
117,4 |
|||||
при конденсации водяных паров |
QТО = G cP (T1' –T1) |
|
|
|||||
Отвод теплоты в промежуточном |
кВт |
113,1 |
||||||
теплообменнике |
|
|
|
|
|
|
||
Потери теплоты в окружающую |
QОС = F ТСР |
кВт |
14,2 |
|||||
среду |
|
|
|
QП = QT + Q0 + Q0ВП + |
|
|
||
Подведенная теплота |
|
кВт |
1700 |
|||||
|
|
|
|
+ Q0ИЗ + QP + NЭ |
|
|
||
Отведенная теплота |
|
QОТВ = QЭ + QЭВП + QTO + QОС |
кВт |
1652 |
||||
Погрешность теплового баланса |
|
QП QОТВ |
100 |
% |
2,8 |
|||
|
||||||||
|
|
|
|
|
QОТВ |
|
|
Проведение экспериментальных исследований в режимах получения холода показало, что на входе в турбодетандер в начальный период охлаждения поступают продукты сгорания топлива, содержащие пары воды в насыщенном состоянии. При расширении ПСТ на выходе из турбодетандера визуально через смотровые окна наблюдалось образование тумана. Следовательно, из-за больших скоростей охлаждения при расширении, кроме обычных стабильных, возникают метастабильные состояния перена-
155
сыщения водяных паров при t > 0 0C и переохлаждение жидкости при t < 0 0С. В дальнейшем при изменении направления и снижении скорости потока в регенераторах происходит конденсация или кристаллизация водяных паров, и система переходит в равновесное состояние. После серии опытов в режимах конденсации и кристаллизации водяных паров эрозионного износа лопаток соплового аппарата и рабочего колеса турбодетандера обнаружено не было.
Дальнейшее охлаждение потока приводит к тому, что зона кристаллизации водяных паров перемещается в регенераторы.
При снижении температуры продуктов сгорания топлива перед турбодетандером до температуры, соответствующей насыщению парами диоксида углерода, визуально за турбодетандером наблюдалось образование тумана, который по мере уменьшения температуры потока становился все более плотным. Снижение скорости потока в центробежном циклоне приводило к выпадению СО2 в виде мелкокристаллической снегообразной массы.
Основные параметры работы ТХЭА в режиме вымораживания диоксида углерода приведены в табл. 5.1 и 5.4. Анализ табл. 5.4 показывает, что снижение степени расширения в турбодетандере по сравнению с расчетной приводит к уменьшению мощности, вырабатываемой турбодетандером, до NД = 48,4 кВт, и соответственно к увеличению мощности, потребляемой электродвигателем из сети, до NПЭ = 61,3 кВт. Производительность по диоксиду углерода снизилась с GТ = 180 кг/ч до 162 кг/ч, т.е. на 10 % . Однако общий баланс мощностей и теплоты в агрегате сохраняется.
Таблица 5.4
Основные параметры работы экспериментального ТХЭА в режиме вымораживания диоксида углерода
Наименование величин |
Обозна- |
Единица |
Вели- |
|
чение |
измерения |
чина |
Температура газов: |
Т6 |
|
|
на входе в турбодетандер |
К |
156 |
|
за турбодетандером |
Т7 |
К |
144,8 |
Мощность, развиваемая турбодетандером |
NД |
кВт |
48,4 |
Мощность, подводимая к турбонагнетателю |
NЭ |
кВт |
55,74 |
от электродвигателя |
NПЭ |
|
|
Мощность, потребляемая электродвигателем |
кВт |
61,3 |
|
из сети |
GС |
|
|
Производительность по диоксиду углерода |
кг/с |
0,045 |
Массовая концентрация диоксида углерода в продуктах сгорания топлива при испытании составляла 5 10 % . С целью повышения концентра-
156
ции осуществлялась рециркуляция продуктов сгорания частичным перепуском с выхлопа на всасывание.
При неоднократном вскрытии и осмотре турбодетандера, сразу после работы в режиме вымораживания СО2 , его отложений в проточной части не обнаружено. Диоксид углерода хорошо транспортировался потоком и откладывался только в спокойных местах.
Вывод твердого диоксида углерода из циклона осуществлялся шнековым прессователем, позволяющим непрерывно отводить и прессовать накапливающуюся массу. Кроме этого шнековый прессователь герметизирует выходное устройство циклона. Диоксид углерода отводился в виде блоков цилиндрической формы диаметром 60 мм с максимальной плотностью на поверхности блока до 1600 кг/м3. Расход мощности при этом не превышал 2 кВт.
Результаты расчета экономической эффективности ТХЭА по экспериментальным исследованиям приведены в табл. 5.5.
|
|
|
|
|
|
|
Таблица 5.5 |
|
|
Результаты расчета экономической эффективности ТХЭА |
|||||||
|
|
|
|
|
|
|
|
|
Расход |
|
|
Расход условного топлива |
|
Экономия |
|||
условного |
|
|
в замещаемых установках |
|
условного |
|
||
топлива |
|
ВТ, кг/с |
|
ВХ, кг/с |
|
ВС, кг/с |
топлива |
|
в ТХЭА |
|
|
|
|
|
|
|
|
0,056 |
|
0,062 |
|
0,0055 |
|
- |
0,168 |
|
0,0629 |
|
0,062 |
|
- |
|
0,035 |
0,361 |
|
Анализ результатов показывает, что комплексное производство теплоты и холода в экспериментальном ТХЭА позволяет эффективно использовать высшую теплотворную способность топлива. Это позволило получить экономию тепловой энергии (или снизить расход топлива) в ТХЭА при производстве теплоты и холода на 16,8 % , при производстве теплоты и СО2 на 36, % по сравнению с раздельными способами.
Расчет энергетической эффективности вырабатываемого холода, как уже отмечалось, обычно производят с помощью холодильного коэффициента. В [35] приведены зависимости действительного холодильного коэффициента, рассчитанного по затратам электроэнергии на выработку холода для паровых и газовых холодильных машин. Сравнить коэффициент эффективности вырабатываемого холода в ТХЭА, рассчитанного по затратам тепловой энергии, и холодильный коэффициент невозможно. Однако в большинстве случаев на выработку электрической энергии расходуется топливо, поэтому целесообразно произвести пересчет холодильного коэффициента по затратам топлива или его теплотворной способности и сравнить с коэффициентом эффективности.
157
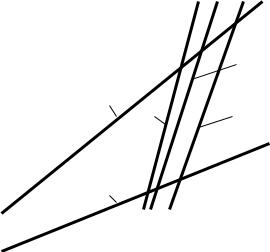
Удельный расход условного топлива на один отпущенный киловаттчас электроэнергии по электростанциям общего пользования составляет величину порядка 349 г. Исходя из этого был пересчитан холодильный коэффициент и произведено сравнение с коэффициентом эффективности вырабатываемого холода в ТХЭА. Результаты сравнения представлены на рис. 5.10. Из сравнения видно, что при температурах от Т6 = 228 К ( 45 0С) до Т6 = 215 К ( 58 0С) ТХЭА становятся энергетически равноценными паровым холодильным машинам, а при более низких температурах – более совершенными, чем последние.
Воздушные (газовые) холодильные машины энергетически равноценны паровым при температурах от 70 0С до 80 0С [35]. А так как ТХЭА представляет сочетание парогазовой установки и газовой холодильной машины, использующей в качестве рабочего вещества продукты сгорания топлива, то, следовательно, комплексное производство теплоты и холода в агрегате расширяет температурные границы рационального получения холода на 30 40 % по сравнению с воздушными холодильными машинами.
КЭ |
|
|
|
|
|
|
|
|
|
0,31 |
|
|
|
|
|
|
|
|
Рис. 5.10. Зависимость коэффициента |
|
|
|
|
|
|
5 |
|
||
|
|
|
|
|
|
|
|
||
|
|
|
|
|
|
|
|
эффективности вырабатываемого хо- |
|
0,27 |
|
|
|
|
|
|
|
|
|
|
|
|
|
|
|
|
|
лода от температуры Т6 на входе в |
|
|
|
1 |
|
|
|
|
|
||
|
|
|
3 |
|
|
4 |
|
турбодетандер: 1 – ТХЭА; 2 – воздуш- |
|
|
|
|
|
|
|
|
|||
0,23 |
|
|
|
|
|
|
|
|
ная холодильная машина ТХМ-1-25; |
|
|
|
|
|
|
|
|
||
|
|
|
|
|
|
|
|
|
3 – двухступенчатая паровая холо- |
0,19 |
|
|
|
|
|
|
|
|
дильная машина (ПХМ) при работе |
|
|
|
|
|
|
|
|
на R717; 4 – ПХМ при работе на R12; |
|
|
|
2 |
|
|
|
|
|
||
|
|
|
|
|
|
|
|
||
|
|
|
|
|
|
|
|
5 – ПХМ при работе на R22 |
|
0,15 |
|
|
|
|
|
|
|
|
|
|
|
|
|
|
|
|
|
|
|
|
|
|
|
|
|
|
|
|
|
0,11 |
|
|
|
|
|
|
|
|
|
|
|
|
|
|
|
|
|
|
|
173 183 193 203 |
213 223 Т6 , К |
|
Анализ работы экспериментального ТХЭА показывает, что КПД турбомашин недостаточно высок и при работе с малорасходным газотурбогенератором необходим подвод дополнительный энергии на привод турбонагнетателя. Расчеты [13] показывают, что применение более эффективных газотурбинных двигателей не потребует дополнительного подвода энергии, а подбор турбомашин, способных работать в составе ТХЭА с высоким КПД, позволит получить экономию топлива в 30 40 % по сравнению с раздельным производством теплоты и холода (СО2) в обычных установках.
158
ЗАКЛЮЧЕНИЕ
Заканчивая изложение вопросов, связанных с основами теории и методами расчета ТХЭА, которые не получили еще достаточного освещения в существующих учебниках, нужно отметить, что на многие вопросы создания и использования ТХЭА в энергосистемах нам тоже не удалось ответить. Причиной этого является еще недостаточный опыт исследований, эксплуатации и проектирования соответствующего оборудования и систем теплохладоснабжения.
Для полного описания процессов в системе охлаждения продуктов сгорания топлива необходимо более подробное рассмотрение процессов теплообмена в напорных утилизаторах теплоты, описание процессов кристаллизации твердого диоксида углерода в системе и отделения его в циклонах, а также вопросов, связанных с переводом твердого СО2 в жидкое и газообразное состояния.
Особенно важными для дальнейшего развития таких энергоустановок являются создание и исследование крупномасштабного стенда на базе ГТУ для производства электроэнергии, теплоты и диоксида углерода в рамках программы ГКНТ "Экологически чистая электростанция", предусматривающей ориентацию на широкое использование в энергетике парогазовых установок с внутрицикловой газификацией твердого топлива и отделением твердого диоксида углерода. Способ может представлять также самостоятельный интерес и явиться прообразом котельных, работающих на природном газе и характеризующихся существенной экономией топлива по сравнению с котельными обычного типа.
Другим не менее важным является вопрос отработки технологии использования выработанного диоксида углерода в различных отраслях промышленности, что определяет не только существенный экологический эффект за счет снижения выброса СО2 в атмосферу, но и значительный эффект в связи с полезным использованием СО2 .
В недалекой перспективе, когда значительную часть жидких топлив придется вырабатывать из каменных углей и сланцев, получат широкое распространение энерготехнологические установки, основой которых и могут стать парогазовые установки с внутрицикловой газификацией и отделением диоксида углерода. Одновременно будет снижаться выброс всех опасных для окружающей среды веществ.
Однако проблем, решение которых зависит от ученых и инженеров, работающих в области тепло- и хладоэнергетики, предостаточно.
Авторы надеются, что учебное пособие окажет определенную помощь в повышении уровня знаний выпускаемых инженеров.
159