
2293
.pdf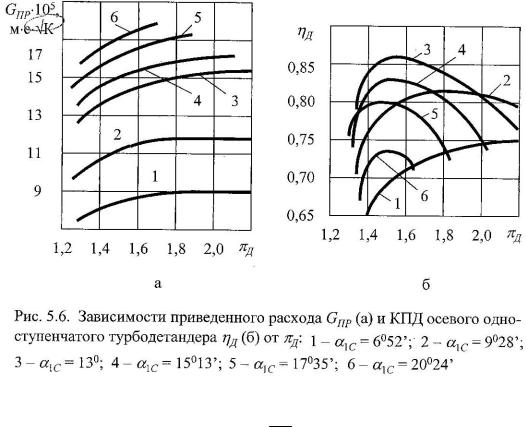
Другими концами стенки соединены телескопически: наружная – с корпусом ресивера, внутренняя – с верхним кожухом. Телескопические соединения крепятся хомутами.
Диффузор служит для уменьшения скорости потока после турбины. Он состоит из корпуса и обтекателя. Диффузор своими фланцами крепится к переходному фланцу и компенсатору. Корпус, диффузор, обтекатель и компенсатор изготовлены из стали Х18Н10Т. Компенсатор и телескопические соединения частей детандера служат для устранения монтажных погрешностей и снятия температурных напряжений.
Ресивер служит для выравнивания поля скоростей потока газа на входе в турбину. Для уменьшения теплопередачи между входящим и выходящим из детандера потоками рабочего вещества установлена теплоизоляция из пенопласта, закрытая кожухом. Составные части ресивера изготовлены из сталей Х18Н9Т и Х18Н10Т.
На рис. 5.6 приведена расходная характеристика осевого одноступенчатого турбодетандера и его коэффициента полезного действия Д. Характеристики построены по результатам испытания детандера на "сухом" (без конденсации водяных паров) воздухе для различных значений выходного угла 1С профиля лопаток соплового аппарата.
В качестве параметра приведенного расхода принят комплекс
GПР GT0* / p0* ,
140
где G – массовый расход, кг/с; T0* и p0* – полные температура и давление
потока на входе в детандер.
Полученные характеристики используются в дальнейшем для расчета процессов кристаллизации диоксида углерода из продуктов сгорания топлива при их расширении в турбодетандере.
Мультипликатор
Мультипликатор служит для повышения числа оборотов турбонагнетателя, передачи крутящего момента от электродвигателя к турбонагнетателю, а также привода масляного агрегата и ротора центробежного суфлера. Передаточное отношение мультипликатора составляет 7,18.
Турбонагнетатель
Турбонагнетатель – осевой семиступенчатый компрессор. Он предназначен для наддува воздуха в газотурбогенератор (рис. 5.7). Расход воздуха 2 кг/с, степень сжатия 2,3, диаметр проточной части 190 мм, частота вращения ротора 21200 об/мин. Турбонагнетатель состоит из статора и ротора. На роторе расположено семь рядов профилированных рабочих лопаток. Рабочее колесо и спрямляющий аппарат образуют ступень турбонагнетателя.
Основными составными частями нагнетателя являются: ротор, патрубок всасывания, корпус передний, корпус нагнетателя (статор) и корпус диффузора.
Ротор компрессора состоит из дисков, несущих на себе лопатки. Диски первой и седьмой ступеней имеют посадочные поверхности для подшипников. При помощи отверстий в кольце диска четвертой ступени и в диафрагмах дисков осуществляется разгрузка дисков по ступеням. Крутящий момент воспринимается через внутренние шлицы при помощи шлицевых втулок и шпонок.
Рабочая лопатка ротора состоит из пера и замка. Лопатки разных ступеней отличаются друг от друга длиной пера и углом установки их в диске. Лопатки с дисками соединяются замком типа "ласточкин хвост". Фиксация лопаток от смещения вдоль паза производится стопорным кольцом. Хвостовики дисков первой и седьмой ступеней имеют конусную поверхность, предназначенную для посадки шлицевых втулок. Шлицевые втулки входят в зацепление с рессорами, соединяющими турбонагнетатель с мультипликатором и турбодетандером. Диски ротора и лопатки изготовлены из стали 13Х14НВФРА.
141
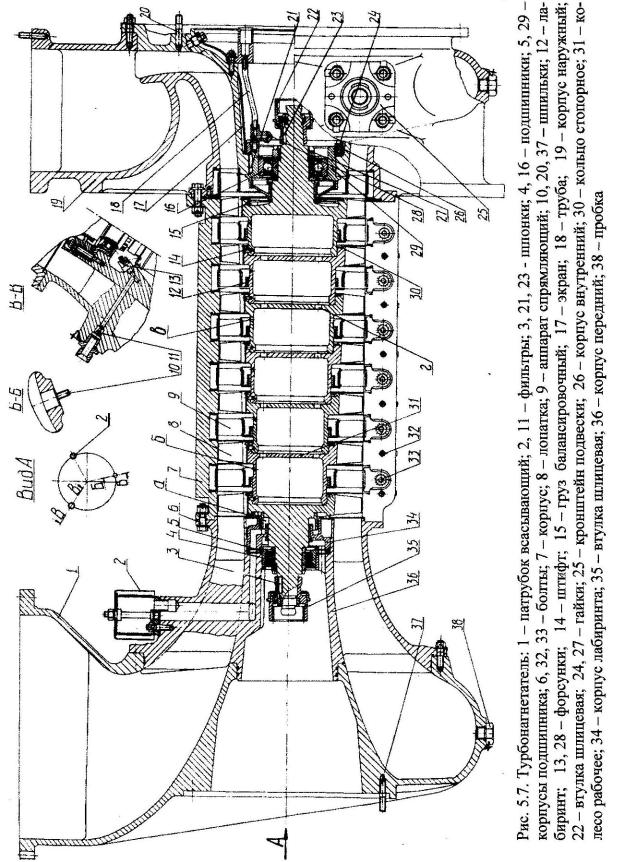
142
Патрубок всасывания является входным устройством турбонагнетателя
ипредназначен для обеспечения равномерного входа воздуха в первое колесо ротора. Патрубок крепится к переднему корпусу и корпусу мультипликатора.
Корпус передний является продолжением входного устройства турбонагнетателя и служит передней опорой ротора.
Корпус турбонагнетателя имеет продольный разъем в вертикальной плоскости. В кольцевых проточках установлены полукольца спрямляющих аппаратов, которые совместно с ротором и корпусом турбонагнетателя образуют проточную часть.
Спрямляющий аппарат состоит из наружного и внутреннего полуколец
испрямляющих лопаток и крепится к корпусу нагнетателя болтами. Корпус по разъему соединен болтами. К торцевым фланцам корпуса
крепятся корпус передний и корпус диффузора. Последний состоит из наружного и внутреннего корпусов. Во внутреннем корпусе установлен корпус задней опоры. В наружном корпусе установлен спрямляющий аппарат седьмой ступени. Шпильками корпус диффузора крепится к корпусу турбонагнетателя. Корпус диффузора литой из сплава АЛ-9, корпус задней опоры из стали 30ХМЮА.
Регенераторы
Регенераторы двойные переключающиеся служат для понижения температуры продуктов сгорания топлива перед расширением в турбодетандере. При охлаждении ПСТ в регенераторах происходит вымораживание влаги, которая осаждается на насадке. При переключении регенераторов обратный поток газа выбрасывает вымороженную влагу в атмосферу. Кроме этого, происходит теплообмен между ПСТ и насадкой. Анализ выпускаемых промышленностью регенераторов показал, что наиболее близкими по характеристикам являются регенераторы турбохолодильной машины МТХМ-1-25.
Каждый регенератор (рис. 5.8) представляет собой цилиндр диаметром 800 мм и длиной 2000 мм, состоящий из двух корпусов с приваренными конусами. Корпусы соединяются между собой при помощи фланцев.
Внутренний объем регенератора заполнен насадкой, которая изготовлена из алюминиевой ленты шириной 50 мм, толщиной 0,4 мм, и имеет гофры под углом 450 к продольной оси ленты. Две ленты с взаимно перпендикулярным расположением гофр наматываются на алюминиевый сердечник до диаметра, равного внутреннему диаметру обечайки корпуса, образуя диск. Гофры препятствуют плотному прилеганию витков друг к другу и образуют косые каналы для прохода газа.
143

144
Изготовленные таким образом диски укладывают внутрь корпусов регенератора и с торцов фиксируют решетками. По наружному диаметру между дисками устанавливаются разделительные проволочные прокладки для уменьшения продольной теплопроводности регенератора.
Для крепления регенератора к раме с внешней стороны обечайки приварена коробчатая опора. К корпусам решеток приварены два кронштейна для крепления стяжек, связывающих регенераторы между собой. На поверхности корпусов приварены бобышки, используемые для установки датчиков замера температуры газа.
В нижней части корпуса приварена бобышка, в которую ввернута трубка слива конденсата, образовавшегося при обогреве регенераторов. К корпусам приварены патрубки с прямоугольными фланцами для крепления клапанных коробок. Наружная поверхность регенератора покрыта слоем теплоизоляции из жидкозаливного пенопласта ПУ-104.
При переключении клапанных коробок регенераторы соединяются попеременно по схеме "сеть ТХЭА регенератор турбодетандер" либо "сепаратор твердого диоксида углерода регенератор – атмосфера". Причем когда один регенератор работает по первой схеме, другой работает по второй, и наоборот. Переключение регенераторов происходит через 30 с или 1 мин.
На регенераторах установлены две клапанные коробки, предназначенные для периодического изменения направления потока газа. Каждая клапанная коробка представляет собой крестообразный кран, в котором за счет поворота дросселя на 900 происходит поочередное соединение вертикальных и горизонтальных каналов.
Привод клапанной коробки, установленной на "теплом" конце регенераторов, осуществляется при помощи силового гидроциклона. В циклон под давлением, создаваемым масляным агрегатом, подводится масло из четырехходового золотника. Привод клапанной коробки, установленной на "холодном" конце регенераторов, осуществляется от "теплой" клапанной коробки через рессору.
Влагоотделитель
Влагоотделитель предназначен для отделения сконденсировавшейся из продуктов сгорания топлива влаги после котла-утилизатора. Наиболее эффективным является влагоотделитель циклонного типа, обеспечивающий при повышенном давлении продуктов сгорания коэффициент влагоотделения порядка 75 85 %. Продукты сгорания, содержащие в себе сконденсированную влагу, подаются в корпус влагоотделителя через входной патрубок тангенциально. Под действием центробежных сил капельки воды от-
145

брасываются на стенки корпуса и стекают в водяной объем влагоотделите- |
|||||
ля, закрытый отражательной тарелкой. |
|
|
|
||
Сепаратор для отделения твердого диоксида углерода |
|||||
Продукты сгорания топлива после расширения в турбодетандере охла- |
|||||
ждаются до температуры ниже температуры кристаллизации диоксида уг- |
|||||
лерода, и из потока газа начинают выпадать частицы твердого СО2 . Раз- |
|||||
меры частиц могут колебаться в пределах 0,5 0,01 мкм. Указанные преде- |
|||||
лы размеров частиц являются в значительной части условными, т.к. части- |
|||||
|
|
|
цы могут объединяться (коагулиро- |
||
|
d |
|
ваться) в более крупные комплексы |
||
|
|
|
и образовывать частицы, превы- |
||
hB |
|
|
шающие по размерам даже частицы |
||
a |
|
механических взвесей. |
|||
|
|
||||
|
|
Одним из наиболее эффектив- |
|||
a |
|
|
|||
|
ных способов механической очист- |
||||
|
l |
hT |
ки газов от твердых частиц являет- |
||
|
ся центробежный способ, который |
||||
|
|
|
реализуется в циклонах. Коэффи- |
||
hЦ |
|
|
циент полезного действия циклонов |
||
|
|
практически равен 70 80 % . |
|||
|
|
|
|||
|
D |
|
Циклон (рис. 5.9) состоит из |
||
|
|
вертикального |
цилиндрического |
||
|
|
|
корпуса с конической нижней ча- |
||
|
|
|
стью. Продукты сгорания, содер- |
||
|
|
|
жащие взвешенные частицы твер- |
||
hК |
|
|
дого СО2 , поступают во входной |
||
|
|
патрубок в цилиндрическую часть |
|||
hФ |
d1 |
|
циклона, |
закрытую крышкой (ско- |
|
|
|
рость входа газа составляет ~ 20 |
|||
|
|
|
|||
|
|
|
м/с). Попав в цилиндр, газовый по- |
||
|
|
|
ток продолжает двигаться по спи- |
||
|
|
|
рали вдоль внутренней поверхности |
||
|
|
|
аппарата. Под действием центро- |
||
|
|
|
бежной силы частицы СО2 движут- |
||
|
в |
в1 |
ся в радиальном направлении, а за- |
||
|
|
|
тем вместе с крайними слоями – |
||
Рис. 5.9. Циклон |
|
вдоль стенок аппарата. Часть нис- |
|||
|
ходящего потока, достигая нижнего |
||||
|
|
|
|||
|
|
|
отверстия |
выхлопной трубы, вхо- |
|
дит в нее, продолжая свое вращательное движение. При движении осталь- |
146
ного газа по конической части циклона внутренние слои газа поворачиваются к оси аппарата и образуют восходящий поток. Таким образом, в циклоне происходит движение газа вдоль оси аппарата, направленное в противоположные стороны. Твердый СО2 , движущийся с продуктами сгорания по стенкам конуса, удаляется через отводящий патрубок.
На основании расхода ПСТ и рекомендаций для разработанного ТХЭА выбран циклон ЦН-15, имеющий следующие размеры: угол наклона крышки и входного патрубка циклона = 15 0; внутренний диаметр циклона D = 600 мм; высота входного патрубка а = 396 мм; высота выходной трубы с фланцем hТ = 1044 мм; ширина входного патрубка в = 120 мм; ширина входного патрубка у фланца вТ = 156 мм; высота цилиндрической части корпуса циклона hЦ = 1356 мм; высота конуса циклона hК = 1200 мм; наружный диаметр выходной трубы d = 360 мм; высота внешней части выходной трубы hВ = 180 мм; длина входного патрубка l = 360 мм; внутренний диаметр спускного отверстия d1 = 240 мм; высота установки фланца hФ = 180 мм; общая высота циклона с бункером НЦ = 2740 мм; диаметр бункера DБ = 690 мм; высота бункера НБ = 1440 мм.
Опыт создания установок для комплексного производства теплоты и твердого СО2 может быть полезен для проектирования и создания установок подобного типа.
5.2. Теплофизические измерения при испытаниях ТХЭА
Для выяснения условий измерений вначале необходимо оценить возможные пределы изменения давления, температуры, скорости и концентрации компонентов продуктов сгорания топлива в турбомашинах, аппаратах и трубопроводах экспериментального стенда, а также определить пределы изменения расхода рабочего вещества и скорости вращения ротора турбодетандера и газотурбогенератора и на основании этого выбрать соответствующие контрольно-измерительные приборы.
Измерение давления. Статическое давление и перепад давлений воздуха и продуктов сгорания топлива в элементах ТХЭА измеряют на стенках соответствующих элементов. Отбор давлений осуществляется через отверстия диаметром 0,7 мм, выполненные перпендикулярно поверхности, омываемой потоком газа. На кромках отверстий заусенцы и фаски должны отсутствовать.
Для регистрации сравнительно небольших давлений и перепадов давлений можно использовать U-образные водяные манометры высотой около двух метров, а для измерения относительно больших давлений – U-образ- ные ртутные манометры типа ДТ-50, а также образцовые пружинные ма-
147

нометры класса точности 0,4. Погрешность измерения водяными манометрами составляет 2 2,5 мм вод. ст., ртутными – 2,5 3 мм рт.ст.
Барометрическое давление можно определять мембранными баромет- рами-анероидами типа МД-49-2, а контролировать – данными гидрометеослужбы.
Измерение температуры можно проводить медьконстантановыми термопарами или платиновыми термометрами сопротивления типа ТСП-037К.
Термопары необходимо выполнять одинаковой длины и соединять по схеме с нулевой термопарой через точечный переключатель типа ПМТ-12 с универсальным вольтметром. "Водные" спаи термопар необходимо термостатировать в ледяной ванне с приготовлением льда из дистиллированной воды.
Термопары и термометры сопротивления необходимо подвергать индивидуальной тарировке. В качестве реперных точек можно принять температуры плавления водяного льда и кипения воды. Измерение разности температур можно проводить дифференциальными термометрами.
Измерение расхода рабочего вещества через элементы ТХЭА можно проводить косвенным методом при помощи нормальной диафрагмы, изготовленной согласно правилам 28-64 и установленной в трубопроводе, например, на входе в турбодетандер. Диаметр диафрагмы, а следовательно, и модуль m выбираются в зависимости от диапазона измеряемого расхода. Диафрагму необходимо устанавливать на горизонтальном прямолинейном трубопроводе со стабилизирующими участками длиной не менее 17D на входе и 10D на выходе, где D – диаметр трубы.
Перепад давлений на диафрагме желательно измерять водяным дифференциальным манометром, а давление перед диафрагмой – ртутным дифференциальным манометром типа ДТ-50.
Расход рабочего вещества G через диафрагму рассчитывается по формуле
G |
10 |
d2 |
|
|
|
, |
|
p p |
2 |
|
|||||
|
|||||||
9 |
|
1 |
|
|
|||
|
|
|
|
|
где – коэффициент расхода, зависящий от модуля диафрагмы; – поправочный множитель, зависящий от относительного изменения давления и модуля диафрагмы; d – диаметр диафрагмы, м; р1 и р2 – статические давления измеряемой среды до и после диафрагмы, Па; – плотность измеряемого рабочего вещества до диафрагмы, кг/м3.
Плотность определяется по измеренным значениям давления и температуры на входе в диафрагму. Температуру измеряют тремя термометрами сопротивления, равномерно расположенными по окружности трубо-
148
провода. Значения коэффициентов и определяются по справочной литературе.
Дополнительную тарировку расходомерной диафрагмы можно производить:
–траверсированием потока по проходному сечению трубопровода при помощи эталонной трубки Пито-Прандтля;
–при помощи специального насадка, имеющего лемнискатный меридиональный обвод и установленного на входе в нагнетатель экспериментального стенда.
Измерение частоты вращения ротора турбодетандера. Частота вра-
щения ротора определяется (см. рис. 5.1) передаточным числом i мультип-
ликатора и частотой вращения ЭД ротора электродвигателя:
Д i ЭД .
Всвою очередь, ЭД зависит от синхронной частоты вращения 0 магнитного потока и скольжения S 0 ЭД 0 , которое для асинхронного
двигателя средней мощности составляет 0,02 0,06 и зависит от нагрузки на электродвигатель.
Величину ЭД измеряют цифровым электронно-счетным частотомером
типа ЧЗ-33, на вход которого подается сигнал от датчика индуктивного типа, установленного вблизи муфты электродвигателя.
С помощью датчика индукционного типа и частотомера определяется частота вращения ротора газотурбогенератора.
Измерение компонентного состава рабочего вещества. Измерение концентрации газообразного диоксида углерода в продуктах сгорания топлива осуществляется с помощью газоанализатора типа ТП2220, принцип действия которого основан на изменении теплопроводности газовой смеси в зависимости от концентрации определяемого компонента. Пределы допускаемой основной погрешности 2,5 % от диапазона измерения. Запаздывание показаний газоанализатора при изменении концентрации газовой смеси на входе штуцера приемного преобразователя не превышает 4 мин.
Периодический анализ состава рабочего вещества может проводиться на хроматографе ЛХМ-8МД лабораторного типа. Принцип работы хроматографа основан на различной адсорбируемости компонентов твердыми адсорбентами, представляющими собой пористые вещества с большой поверхностью. Основное преимущество хроматографии – полнота информации по всем компонентам сложных газовых смесей. Общая продолжительность анализа составляет 30 мин.
149