
Пустов Ю.А., Ракоч А.Г.- Диагностика и экспертиза коррозионных разрушений металлов - Курс Лекций
.pdf6.2.3. Вероятностные теории питтинговой коррозии
Питтинговая коррозия – вероятностный процесс. Основанием для такого заключения являются плохая воспроизводимость и большой разброс результатов определения Епит и τинд даже при условии тщательной подготовки поверхности и контроле состояния коррозионной среды. Появление питтингов происходит случайно во времени и в пространстве с определенной частотой. Вместе с тем распределение питтингов в пространстве нельзя считать строго случайным, поскольку их зарождение наблюдается на дефектных участках поверхности металла (вблизи неметаллических включений,
вторичных фаз, шероховатостях). Но, поскольку само распределение дефектов носит случайный характер, то в пределах этого статистического множества появление питтинга также является случайным.
Одна из вероятностных теорий основана на представлениях о динамическом равновесии процессов разрушения и восстановления пассивной пленки и ярко выраженном статистическом характере ПК. Возникновение питтинга во времени протекает случайно и может быть интерпретировано стохастическим (вероятностным)
процессом, в соответствии с которым зарождение питтинга означает гибель или повреждение образца, теряющего способность по поддержанию пассивного состояния.
Обратный этому − стахостический процесс рождения, соответствует репассивации питтинга или выживанию образца.
6.2.4.Влияние различных факторов на питтинговую коррозию металлов и сплавов
Влияние состава электролита
Увеличение концентрации галогенид-иона приводит к смещению Епит в
отрицательную сторону, причем Епит прямо пропорционален логарифму концентрации аниона (рис. 6.6): Епит =А−Вlg[Cl¯] в широком интервале концентраций. Значения коэффициентов А и В могут различаться в зависимости от условий. По данным Леки и Улига А=0,168 В, В=0,088 В. По данным И.Л.Розенфельда для стали Х18Н10Т в нейтральном растворе А=0,38 В, В=0,160 В.
Увеличение концентрации хлорид-ионов приводит к уменьшению τинд по уравнению 1/τинд = К[Cl¯], где К – коэффициент пропорциональности. Величина 1/τинд
характеризует скорость разрушения пассивного состояния.
51
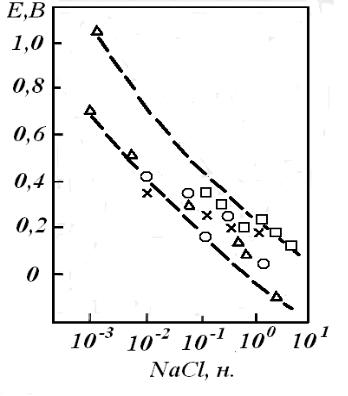
Рис.6.6. Зависимость Епит стали Х18Н10Т от концентрации NaCl (результаты нескольких независимых исследований)
Изменение рН среды в интервале 1,6…11,0 приводит к сдвигу Епит в
положительную сторону максимум на 10 мВ на каждую единицу рН. Для стали Х18Н10Т
при рН 1…5 зависимость Епит = f(pH) описывается уравнением Епит = 0,40+0,030рН. В
сильнощелочных растворах зависимость Епит от рН среды более значительна.
Присутствие в составе коррозионной среды наряду с хлорид-ионами других анионов вызывает ингибирование ПК, что проявляется в повышении Епит и уменьшении скорости ПК. По данным Леки и Улига ингибирующая способность анионов убывает в
ряду OH >NO >SO2 >ClO . |
По |
данным |
И.Л.Розенфельда наблюдается |
следующая |
|||
3 |
4 |
4 |
|
|
|
|
|
последовательность: |
|
NO >ClO |
>ClO >CrO2 >SO2 . Ингибирующее |
действие |
|||
|
|
3 |
3 |
4 |
4 |
4 |
|
оказывают также хроматы, молибдаты, вольфраматы: KCrO4, K2Cr2O7, Na2MoO4, Na2WO4.
Высокая эффективность ингибирующего действия нитрат-иона NO3 объясняется не только увеличением Епит, но и его способностью подавлять ПК при потенциалах более положительных, чем Епит.
Ингибирующее действие анионов объясняется их преимущественной адсорбцией на запассивированной поверхности металла, что обеспечивает вытеснение агрессивных галогенид-ионов, или образованием оксидов при анодной поляризации.
Влияние химического состава сталей
52
Хром в водных растворах, содержащих галогенид-илоны, не склонен к ПК.
Исключением являются растворы с низким содержанием воды. Сильно выраженное положительное влияние хрома на сопротивляемость против ПК обусловлено его высокой стойкостью против активирования хлорид-ионами. При легировании стали 30…35 % и
более хрома сталь становится устойчивой в растворах хлоридов любой концентрации.
Никель склонен к ПК, но в одних и тех же условиях его Епит положительнее Епит
железа, поэтому легирование сплавов Fe-Cr никелем вызывает увеличение устойчивости сталей к ПК. Однако значительное смещение Епит в положительную сторону наблюдается при концентрации никеля более 14 %, после чего сталь в пассивной области не активируется.
Молибден оказывает сильное положительное воздействие на устойчивость к ПК.
Он не только вызывает увеличение Епит сталей всех структурных классов и уменьшение количества питтингов на единицу поверхности, но и приводит к значительному увеличению критических токов питтингообразования, получаемых при снятии поляризационных кривых в гальваностатическом режиме (табл. 6.1).
|
|
|
|
Таблица 6.1 |
|
Влияние молибдена на параметры ПК закаленных сталей |
|||
|
|
|
|
|
|
Епит, В |
iкр, |
Епит, В |
Число питтингов/см2 |
Сталь |
(по кривым |
(потенцио- |
(гальваностатическая поля- |
|
|
заряжения) |
мкА/см2 |
статический |
ризация, выдержка 30 мин) |
|
|
|
метод) |
|
Х18Н10Т |
0,45-0,60 |
5-10 |
0,550 |
50-60 |
Х18Н12М2Т |
0,75-0,85 |
10 |
0,825 |
18-22 |
Х18Н12М3Т |
1,40-1,50 |
10-100 |
1,275 |
12 |
Кроме того, молибден повышает критическую температуру питтингообразования.
Кремний при его содержании 3…4 % повышает сопротивляемость сталей к ПК, в
особенности сталей одновременно легированным молибденом. Однако при более высоких концентрациях (4…6 %) проявляется двойственная роль кремния: положительная,
связанная легированием твердого раствора и участием в образовании устойчивых пассивных пленок, и отрицательная – при образовании неметаллических включений,
содержащих SiO2, и неустойчивых при повышенных температурах и высоких концентрациях хлоридов.
Марганец вводится в состав хромоникелевых сталей для обеспечения стабильности аустенита и в качестве частичной или полной замены никеля. Поэтому его влияние на устойчивость к ПК рассматривается совместно с его способностью к изменению
53
структуры стали (аустенитообразованию). В структуре стали могут присутствовать аустенит, феррит, мартенсит.
В нержавеющих сталях с низким содержанием никеля (Х18Н6) при введении 6 %
марганца мартенситная структура переходит в аустенитную. При этом Епит резко уменьшается и при дальнейшем увеличении содержания марганца (до 10-15%)
практически не меняется. В аустенитных сталях (типа Х18Н10) резкое ухудшение стойкости против ПК наблюдается уже при содержании марганца 0,4-0,6%, после чего наблюдается не столь резкое снижение стойкости. Резкое ослабление стойкости против ПК обусловлено образованием марганцесодержащих сульфидов. Дальнейший рост содержания марганца влияет на ослабление стойкости к ПК уже за счет роли марганца как легирующего элемента, входящего в состав твердого раствора. Меняются и свойства самих сульфидов, в которых увеличивается содержание марганца.
Вредное влияние марганца на устойчивость к ПК преодолевается добавками молибдена и азота.
В ферритных хромистых сталях негативное влияние марганца проявляется даже при малых его концентрациях (0,15…0,30 %).
Азот оказывает благоприятное воздействие на стойкость хромоникелевых сталей против ПК. Наиболее полно его влияние изучено в сталях с пониженным содержанием никеля и повышенным содержанием марганца, куда азот вводится как аустенитообразующий элемент. В таблице 6.2 представлены результаты изучения влияния концентрации азота в стали 03Х18Н6Г10 на Епит в хлоридсодержащем растворе серной кислоты.
Таблица 6.2
Потенциал питтингообразования Епит стали 03Х18Н6Г10 с различным содержанием азота в растворе 0,5 М H2SO4 c добавкой NaCl (потенциодинамическая поляризация, 2 мВ/ч)
|
NaCl, моль/л |
||
N, % |
|
|
|
0,05 |
|
0,1 |
|
|
|
|
|
|
|
Епит , мВ |
|
|
|
|
|
0,07 |
510 |
|
340 |
0,12 |
640 |
|
490 |
0,17 |
690 |
|
480 |
0,25 |
910 |
|
550 |
0,35 |
930 |
|
680 |
|
|
|
|
54
Положительный эффект легирования азотом связывают либо с образованием нитрат-иона, который возникает как результат коррозии матрицы или нитридов и карбонитридов и действует как ингибитор ПК, либо подщелачиваением приэлектродного пространства в результате образования аммония как продукта разложения нитридов хрома.
Углерод оказывает отрицательное воздействие на устойчивость сталей к ПК как при нахождении его в твердом растворе (закаленное состояние), так и в виде первичных
(т.е. существующих уже в состоянии закалки сталей) карбидов или карбонитридов типа
TiCN, NbCN. или вторичных (т.е. образующихся при отпуске).
Высокой устойчивостью против ПК обладают только те стали (в частности,
суперферриты), содержание углерода в которых не превышает 0,001…0,002 %.
Ниобий, титан, цирконий, тантал, ванадий, церий повышают склонность хромоникелевых сталей к ПК. Причина − увеличение степени гетерогенности структуры из-за высокой склонности к образованию карбидов и карбонитридов.
В частности, сильно отрицательная роль титана проявляется в кислых средах с достаточно высоким окислительно-восстановительным потенциалом из-за анодного окисления карбида титана. Церий понижает стойкость против ПК в результате появления в стали неметаллических включений (химически нестойких оксидов).
Ванадий увеличивает стойкость против ПК. Его действие связывают главным образом не со снижением скорости растворения в питтинге, а со способностью препятствовать зарождению питтинга и повышению склонности сталей к репассивации.
Повышенная устойчивость ванадийсодержащих сталей к зарождению питтинга связана с повышенным содержанием этого компонента в составе пассивной пленки.
Сера и фосфор. Ввиду чрезвычайно низкой растворимости в железе вредное влияние серы на устойчивость к ПК связано с ее участием в образовании сульфидов MnS, FeS, а также окси- и карбосульфидов. Распределение серы между марганцем, железом и хромом в простых и сложных сульфидах зависит от содержания марганца в стали. Однако отсутствие серы в стали, исключающее образование сульфидов, не устраняет возможности возникновения питтингов, связанных с другими факторами, в частности из-
за наличия неметаллических включений на основе оксидов, нитридов и т.д.
Прямого отрицательного влияния фосфора на устойчивость сталей к ПК не установлено, однако косвенные признаки дают основание полагать, что способность фосфора сегрегировать по границам зерен закаленных хромоникелевых сталей увеличивает дефектность границ и, следовательно, вероятность возникновения ПК.
55
Влияние фазового состава и термической обработки сталей
Ярко выраженного влияния структурного состояния сталей на устойчивость к ПК не установлено. Считается, что аустенитная структура несколько более устойчива против ПК. На это косвенно указывает смещение Епит на 69…90 мВ в отрицательную сторону при появлении в структуре аустенитной стали δ-феррита (при термообработке) и мартенсита
(при деформации). Однако понижение стойкости против ПК связано не с появлением δ-
феррита как фазы, а с локальным изменением химического состава аустенита и питтингообразование идет преимущественно на границах зерен аустенит-феррит.
Аустенитные стали наиболее стойки в закаленном состоянии. Отпуск в области температур, вызывающих склонность к МКК (650ºС), значительно снижает и устойчивость к ПК. Образование вдоль границ зерен карбидов хрома приводит к обеднению твердого раствора этим элементом, ухудшает способность к пассивации приграничных зон и предопределяет преимущественное возникновение питтингов именно в этих областях.
Считается, что влияние химического состава сталей на устойчивость к ПК в значительной степени превосходит влияние структурного фактора, а наблюдаемые различия в склонности к ПК объясняются ориентировкой зерен аустенита и феррита и свойствами различных граней о.ц.к и г.ц.к. решеток. При этом скорость растворения той или иной грани зависит не только от ее ориентации ({111}, {110} или {100}), но и от природы металла.
Влияние термической обработки на устойчивость против ПК проявляется в виде изменения степени гетерогенности структуры. Наибольшей стойкостью обладает полностью гомогенная структура. Появление при термообработке других структурных составляющих ухудшает стойкость против ПК прежде всего по причине возникновения обедненных хромом и молибденом приграничных зон. При этом пониженное содержание хрома и молибдена по границам зерен приводит к появлению здесь питтинга даже в отсутствие склонности стали к МКК (рис. 6.7). Области склонности к МКК и ПК не совпадают: при низких температурах отпуска бóльшая скорость ПК проявляется еще до проявления склонности к МКК.
56
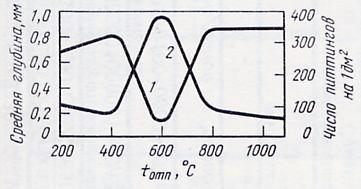
Рис.6.7. Влияние термической обработки на склонность к ПК стали 12Х18Н9Т в электролите 2%FeNH4(SO4)2∙12H2O+3%NH4Cl: 1- средняя глубина питтингов; 2 – число питтингов на 1 дм2
Однако даже в отсутствие обедненных хромом приграничных зон существование в структуре стали избыточных фаз увеличивает склонность к ПК. Причины этого следующие:
неустойчивость самих фаз, активирующихся при более отрицательных потенциалах, чем потенциал питтинговой коррозии твердого раствора;
уменьшение стойкости твердого раствора в областях, граничащих с частицами этой фазы, в частности из-за механических напряжений, возникающих при ее выделении из твердого раствора.
Поэтому термическая обработка, приводящая к растворению избыточных фаз, т.е. к
повышению гомогенности структуры, является одним из наиболее возможных способов повышения устойчивости сталей против ПК.
На устойчивость к ПК оказывает влияние размер зерен. Мелкозернистая сталь имеет более положительное значение Епит и меньшую скорость ПК. Причиной этого считается увеличение межзеренной поверхности, вызывающее уменьшение плотности распределения неметаллических включений и других мест зарождения питтинга. Однако по другим источникам (Н.Д.Томашов с сотр.) зависимость склонности к ПК (сталь Х18Н9)
носит противоположный характер. При увеличении размера зерна от 0,005 мм до 0,070 мм
Епит возрастает на 170 мВ в растворе 0,1 моль/л NaCl, а в растворе FeCl2 наблюдается уменьшение скорости ПК.
Влияние температуры коррозионной среды
Повышение температуры среды вызывает сдвиг Епит в отрицательную сторону, а
характер (монотонный или скачкообразный) этого смещения зависит от состава стали и состава среды.
57
Для оценки стойкости аустенитных сталей против ПК при повышении температуры коррозионной среды используют критическую температуру питтингообразования (КТП), зависящую от содержания молибдена: КТП (ºС)=10 + 7∙(%
Мо). Более точную связь между химическим составом стали и КТП устанавливает эквивалент питтингостойкости (ЭСП) против ПК: ЭСП = % Cr+3,3∙(% Mo). Чем больше величина ЭСП, тем выше КТП. В сталях, легированных азотом, учитывают также и его положительное влияние на стойкость против ПК: ЭСП = % Cr + 3,3∙(% Mo + 16∙(% N).
Влияние состояния поверхности
Состояние поверхности при прочих равных условиях играет определяющую роль в проявлении большей или меньшей склонности сталей к ПК. Наличие на запассивированной поверхности макродефектов (задиров, закатов окалины, вмятин,
технологических загрязнений), повышающих гетерогенность и облегчающих возникновение концентрационных неоднородностей, способствует снижению устойчивости против ПК. Максимальную устойчивость стали данного состава обеспечивает удаление этих дефектов путем тонкого шлифования, полирования и последующего пассивирования.
Влияние неметаллических включений
Питтинги в коррозионностойких сталях всех классов образуются только около частиц неметаллических включений (НВ). Этими включениями в большинстве случаев являются оксисульфиды. Питтинг начинается с зарождения узкой канавки вокруг включения, которое некоторое время сохраняет свою целостность. По мере развития коррозионного процесса канавка расширяется и углубляется, что приводит к постепенному разрушению самого НВ, его растворению и удалению из питтинга.
В закаленных сталях питтинг возникает у НВ, расположенных в теле зерен, в то время как в отпущенных сталях – около включений на границах зерен, что является результатом изменения состояния твердого раствора в ходе термической обработки.
Однако основной причиной локальной активации запассивированной поверхности металла и возникновения ПК являются не сами НВ, а необходимая концентрация активирующих ионов в коррозионной среде. НВ только облегчают процесс зарождения питтингов.
Наиболее чувствительные места для зарождения питтингов − сульфидные НВ.
Питтинги возникают либо на самих сульфидах, либо на сульфидной оболочке,
окружающей оксиды. Установлено, что металл вокруг включений обладает повышенной растворимостью, скорость которой может более чем в 100 раз превышать скорость
58
растворения стали. Причиной этого может являться либо локальная деформация металла вокруг НВ, возникающая из-за разницы коэффициентов термического расширения металла и НВ, и порождающая структурные дефекты (дислокации), либо активирующее действие продуктов растворения включений.
6.3.Щелевая коррозия
6.3.1.Определение щелевой коррозии, зоны проявления, особенности и
диагностические признаки
Щелевая коррозия (ЩК) – интенсивное, избирательное коррозионное разрушение металлов и сплавов в щелях и зазорах. ЩК возникает в тех случаях, когда конструкция содержит узкие щели, резьбовые соединения, застойные зоны или тогда, когда металлический материал имеет технологические дефекты в виде микрощелей или микротрещин. Началом развития ЩК часто является возникновение в перечисленных дефектах коррозионных питтингов.
Зонами проявления ЩК являются области между:
•металлическими деталями при их сочленении;
•металлом и прокладочными материалами;
•обшивкой судов и наросшими микроорганизмами;
•металлом и строительными материалами.
Главные особенности ЩК − пониженная концентрация окислителей (кислорода и др.) в щелях по сравнению с их концентрацией в объеме электролита и замедленный отвод продуктов коррозионной реакции.
Диагностическими признаками проявления ЩК являются:
•для пассивирующихся металлов − более высокая скорость растворения металла в щели по сравнению со скоростью растворения металла на открытой части поверхности;
•для непассивирующихся металлов − более высокая скорость растворения открытой части поверхности, граничащей со щелью, по сравнению со скоростью растворения металла в щели.
6.3.2. Механизм щелевой коррозии
Пассивирующиеся металлы и сплавы
Вследствие затруднения доступа окислителя в щель и расходования его в коррозионном процессе значительно снижается эффективность катодного процесса.
59
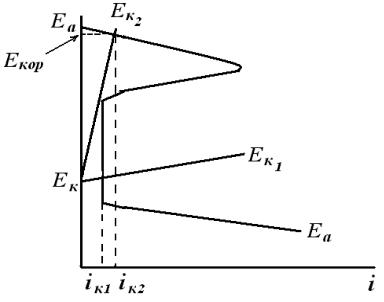
Однако, если при уменьшении концентрации окислителя в щели катодный ток все еще обеспечивает поддержание металла в щели в пассивном состоянии заметных различий в скоростях растворения металла и щели и открытой поверхности не обнаруживается и коррозионный ток не меняется (рис. 6.8, катодная кривая Ек – Ек1, ток iк1).
Рис.6.8. Схематическая коррозионная диаграмма, поясняющая механизм ЩК пассивирующихся металлов
При дальнейшем уменьшении концентрации окислителя перенапряжение катодного процесса в щели становится настолько большим, а катодный ток настолько малым, что потенциал металла смещается в отрицательную сторону, металл в щели переходит в активное состояние и скорость его растворения увеличивается (iк2).
Выходящие в раствор продукты коррозии подвергаются гидролизу (например, Fe3+ + 3H2O→Fe(OH)2 + 3H+, Cr3+ + 3H2O→Cr(OH)2 + 3H+), который вызывает подкисление раствора. Затрудненный отвод из щели продуктов коррозии и ограниченный подвод в щель свежего электролита способствуют усилению кислотности раствора (уменьшение рН), облегчают анодный процесса растворения металла в щели и создают условия для протекания процесса с водородной деполяризацией. Процесс коррозии в щели при подкислении раствора особенно ускоряется, если поверхность металла в щели становиться анодом по отношению к открытой поверхности, находящейся в пассивном состоянии.
Для металлов, находящихся в активном состоянии, и коррозирующих с катодным контролем (углеродистые стали, железо в нейтральных растворах), возможно, наоборот,
уменьшение скорости коррозии металла в щели по сравнению со скоростью коррозии открытой поверхности из-за уменьшения скорости катодной реакции в связи с ограниченным доступом деполяризатора (кислорода). На рисунке 6.9 представлена коррозионная диаграмма для непассивирующихся металлов.
60