
- •1.4.1. Процеживание
- •1.4.2. Отстаивание
- •4.3. Фильтрование
- •1.5.1.1. Электрокоагуляция
- •Усреднители
- •Песколовки
- •1.5.2. Флотация
- •1.5.2.1. Флотация с выделением воздуха из раствора
- •1.5.2.2. Флотация с механическим диспергированием воздуха
- •Необходимое число флотационных камер определяется из соотношения
- •1.5.2.3. Флотация с подачей воздуха через пористые материалы
- •1.5.2.4. Электрофлотация
- •1.5.2.5. Биологическая и химическая флотация
- •1.5.3. Сорбция
- •1.5.4. Экстракция
- •Таблица 1.3
- •1.5.6. Мембранные процессы
- •Таблица 1.4
- •Расход реагентов для нейтрализации 100 % кислот и щелочей
- •Расход реагентов, требуемых для удаления металлов
- •Реагенты
- •Вода
- •Известь
- •Осадок
- •Рис. 1.50. Нейтрализатор дымовых вод щелочными газами
- •Продукция
- •Производство
- •Асбест
- •Вода
- •В атмосферу
- •Выпуск отработанного воздуха
- •Рис. 1.56. Контактные аппараты для озонирования:
- •Осадок
- •Сточная
- •NaHSO2
- •Азота диоксид (газ)
- •Углерода оксид (газ)
- •Циклогексан (пары)
- •3. Переработка отходов производства и потребления
- •3.2. Способы утилизации промышленных отходов
- •3.3. Отходы потребления
- •3.4. Методы утилизации отходов производства и потребления
- •3.5. Переработка твердых бытовых отходов компостированием
- •СПИСОК ЛИТЕРАТУРЫ
- •Приемный корпус
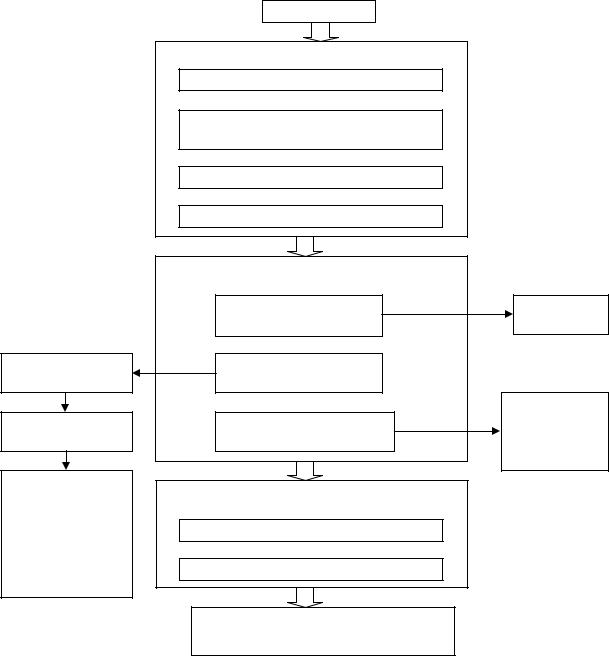
стированию. Эти материалы сжигают на компостных заводах или подвергают пиролизу для получения тепловой энергии или пирокарбона, используемого в металлургии, или вывозят на полигоны ТБО для захоронения.
Технологический процесс переработки ТБО полностью механизирован и управляют им с центрального пульта управления. Принципиальная технологическая схема производства компоста показана на рис. 3.4.
Бункер
металлолома
Пакетирующий
пресс
Подъемный кран с
магнитной шайбой для погрузки пакетов металлолома
|
Мусоровоз |
|
|
|
ТБО |
|
|
|
Приемный корпус |
|
|
|
Мусороприемный бункер |
|
|
|
Кран-балка |
|
|
|
с гейферным ковшом |
|
|
|
Дозирующий бункер |
|
|
|
Ленточный конвейер |
|
|
|
Сортировочный корпус |
|
|
|
Цилиндрический гро- |
Некомпос- |
Бункер бал- |
|
тируемые |
||
Черный, |
хот |
отходы |
ласта |
Электромагнитный се- |
|
|
|
цветной |
|
|
|
металл |
паратор |
|
Котельная или |
|
|
|
|
|
Аэродинамический сепа- |
Пленка, |
пиролизная |
|
ратор |
бумага |
установка |
|
Главный корпус |
|
|
|
Биотермический барабан |
|
|
|
Измельчитель компоста |
|
|
Штабеля компоста на площадках готовой продукции
Рис. 3.4. Принципиальная технологическая схема производства компоста
Бытовые отходы доставляют на завод кузовные мусоровозы, которые разгружаются в приемные бункера с днищами, выполненными в виде пластинчатых питателей. К пластинам питателей приваривают металлические штыри для лучшего захвата подаваемого материала. Крупногабаритные отходы изымают из бункеров и складывают в автоприцепы с помощью захвата, подвешенного к кранбалке.
Отходы из бункеров разгружают на ленточные конвейеры, по которым они направляются в сортировочный корпус, оснащенный грохотами, электромагнитными и аэродинамическими сепараторами, производящими первичную сортировку поступающих отходов.
154
С помощью конвейеров, подающих отходы из приемного корпуса, загружают цилинд-
рические грохоты. Диаметр сита грохота 2,5 м, длина 7,3 м. Размер ячеек сит 150÷250 мм, частота вращения грохота 15 мин–1, паспортная производительность до 20 т/ч. Крупные некомпостируемые фракции (картонные ячейки, бумага, текстиль и т. п.) или так называемые некомпостируемые отходы (НБО) направляют в бункер балласта. Черный и цветной металл выбирают электромагнитными сепараторами.
Просеянный материал по конвейерам подается в главный корпус, проходя последовательно сепараторы черного, цветного металла и аэросепараторы, выделяющие легкие фракции – пленку и бумагу (если есть потребитель, то эти фракции отгружают ему, если нет – отправляют на пиролиз).
Отобранный в цехе черный металл конвейерами подается на гидравлический пакетировочный пресс (производительность пресса 2,4 т/ч.). Полученные пакеты металла складируются на площадке, оборудованной кранбалкой грузоподъемностью 1 т с электромагнитной шайбой, а затем отгружаются потребителям. Цветной металл по конвейерам поступает в бункеры-накопители.
Отсортированные отходы, предназначенные для компостирования, подают в загрузочные устройства биотермических барабанов, выполненных в виде вращающихся цилиндров.
Биотермический процесс обезвреживания отходов происходит благодаря активному росту термофильных микроорганизмов в аэробных условиях.
Масса отходов сама разогревается до температуры 60 °С, при которой болезнетворные микроорганизмы, яйца гельминтов, личинки и куколки мух погибают, и масса отходов обезвреживается. Под действием развивающейся микрофлоры органические вещества разлагаются, образуя компост.
Ежедневно биобарабан загружается на 1/2 полезного объема свежими отходами и одновременно разгружается. Таким образом, свежие отходы попадают в среду с активным биотермическим процессом, что сокращает цикл их компостирования до двух суток. Пропускная способность одного биобарабана до 34 тыс. т/год.
Для обеспечения принудительной аэрации на корпусе биобарабана установлены венти- ляторы-наездники, которые подают свежий воздух в толщу отходов. Количество подаваемого воздуха регулируется по зонам в зависимости от температуры и влажности материала.
Оптимальная влажность для ускоренного процесса компостирования 40÷45 %.
Биобарабан выполняет две функции: обеспечение в компостируемой массе требуемого биотермического процесса и механическое истирание отходов.
Разгружаются биобарабаны на ленточные конвейеры, которые доставляют компост обратно в сортировочный корпус, где производится окончательная очистка компоста от балласта. Стекло и мелкий балласт ссыпаются в тележки-прицепы, а компост по системе конвейеров подается на складские площадки, где с помощью бульдозеров формируют штабеля, которые периодически перелопачивают и при необходимости увлажняют.
Большую часть территории, отводимой под размещение мусоро-перерабатывающего завода, занимают складские площадки для дозревания и хранения компоста. Примерное время дозревания компоста на складе обычно не менее 2 мес. при высоте штабеля до 2 м. Мощность мусороперерабатывающего завода 90 тыс. т/год.
Иногда в комплекс завода включают линии по производству экологически чистых древес- но-полимерных плит из отходов деревообработки и полиэтиленовой пленки, выделяемой аэросепараторами из ТБО.
3.5.2. Полевое компостирование ТБО
Наиболее простым и дешевым методом утилизации ТБО является полевое компостирование. Его целесообразно использовать в городах с населением свыше 50 тыс. жителей. Правильно организованное полевое компостирование обеспечивает защиту почвы, атмосферы, грунтовых и поверхностных вод от загрязнения ТБО. Технология полевого компостирования
155
позволяет производить совместное обезвреживаение и переработку ТБО с обезвоженным осадком сточных вод (в соотношении 3:7), получаемый при этом компост содержит больше азота и фосфора.
Существует две принципиальные схемы полевого компостирования:
-с предварительным дроблением ТБО;
-без предварительного дробления.
При использовании схемы с предварительным дроблением ТБО для измельчения отходов используют специальные дробилки.
Во втором случае (без предварительного дробления) измельчение происходит за счет многократного перелопачивания компостируемого материала. Неизмельченные фракции отделяют на контрольном грохоте.
Установки полевого компостирования, оснащенные дробилками для предварительного измельчения ТБО, обеспечивают больший выход компоста и дают меньше отходов производства. ТБО измельчают молотковыми дробилками или небольшими биотермическими барабанами (частота вращения барабана 3,5 мин–1). Барабан обеспечивает достаточное измельчение ТБО за
800÷1200 оборотов (4÷6 ч). После такой обработки 60÷70 % материала проходит через сито обечайки барабана с отверстиями диаметром 38 мм.
Сооружения и оборудование полевого компостирования должны обеспечить прием и предварительную подготовку ТБО, биотермическое обезвреживание и окончательную обработку компоста. ТБО разгружают в приемный буфер или на выровненную площадку. Бульдозером, грейферным краном или специальным оборудованием формируют штабеля, в которых происходят процессы аэробного биотермического компостирования.
Высота штабелей зависит от метода аэрации материала и при использовании принудительной аэрации может превышать 2,5 м. Ширина штабеля поверху не менее 2 м, длина –
10÷50 м, угол заложения откосов равен 45°. Между штабелями оставляют проезды шириной
3÷6 м [7].
Для предотвращения развеивания бумаги, выплода мух, устранения запаха поверхность штабеля покрывают изолирующим слоем торфа, зрелого компоста или земли толщиной 20 см. Выделяющееся под влиянием жизнедеятельности термофильных микроорганизмов тепло приводит к «саморазогреванию» компостируемого материала. При этом наружные слои материала в штабеле служат теплоизоляторами и сами разогреваются меньше, в связи с чем для надежного обезвреживания всей массы материала штабеля необходимо перелопачивать. Кроме того, перелопачивание способствует лучшей аэрации всей массы компостируемого материала. Продолжительность обезвреживания ТБО на площадках компостирования со-
ставляет 1÷6 мес. в зависимости от используемого оборудования, принятой технологии и сезона закладки штабелей.
При весенне-летней закладке недробленых ТБО температура в шатбеле компостируемого материала через 5 дней поднимается до 60÷70 °С и удерживается на таком уровне дветри недели, затем снижается до 40÷50 °С. В течение следующих 3÷4 мес. температура в шатбеле уменьшается до 30÷35 °С.
Перелопачивание способствует активизации процесса компостирования, через 4÷6 дней
после перелопачивания температура на несколько дней снова повышается до 60÷65 °С.
При осенне-зимней закладке температура в течение первого месяца поднимается только в отдельных очагах, а затем, по мере саморазогрева (1,5÷2 мес.) температура штабеля достигает 50÷60 °С и остается на таком уровне в течение двух недель. Затем в течение 2÷3 месяцев температура в штабеле удерживается на уровне 20÷30 °С, а с наступлением лета по-
вышается до 30÷40 °С.
В процессе компостирования активно снижается влажность материала, поэтому для ускорения биотермического процесса помимо перелопачивания и принудительной аэрации необходимо производить увлажнение материала.
Принципиальные схемы сооружений полевого компостировния ТБО приведены на рис.
156
3.5.
На рис. 2.5, а, б, в, г представлены схемы с предварительным измельчением ТБО, а на рис. 2.5, д обработка перенесена в конец технологической линии. На рис. 2.5, а, б, в ТБО разгружают в приемные бункера, оснащенные пластинчатым питателем, на рис. 2.5,г – в траншеи с последующим извлечением их грейферным краном. На рис. 2.5, а, б, г – измельчение ТБО осуществляют в дробилке с вертикальным валом, на рис. 2.5, в - в горизонтальном вращающемся биобарабане.
На рис. 2.5, а измельченные ТБО смешиваются с обезвоженным осадком сточных вод и затем направляются в штабеля, где они находятся в течение нескольких месяцев. За время компостирование материал несколько раз перелопачивается.
Технологическая схема компостирования в две стадии представлена на рис. 2.5,б. В течение первых десяти дней биотермический процесс происходит в закрытом помещении, разделенном подпорными продольными стенками на отсеки. Компостируемый материал каждые два дня перегружают специальной подвижной установкой из одного отсека в другой. Для активизации биотермического процесса через отверстия, расположенные в основании отсеков, производят принудительную аэрацию компостируемого материала.
Из закрытых отсеков компостируемый материал после грохочения перегружают на от-
крытую площадку, где он дозревает в штабелях в течение 2÷3 мес.
Схема, изображенная на рис. 2.5, в, отличается от остальных тем, что в качестве дробилки в ней используют биобарабан.
В схеме, показанной на рис. 2.5, г, используют двойное грохочение материала. Измельченный в дробилке материал при первичном грохочении разделяют на две фракции: крупную, направляемую на сжигание, и мелкую, направляемую на компостирование. Компостирование осуществляют в лотке, расположенном на открытой площадке. Лоток разделен продольными стенками на секции и оснащен установкой для перегрузки компостируемого материала в соседние секции. Зрелый компост подвергают повторному (контрольному) грохочению, после чего отправляют потребителю.
При отсутствии дробилки для ТБО может быть применена схема, изображенная на рис. 2.5, д, в которой грохочение, дробление и магнитная сепарация происходят в конце технологического цикла.
Простейшими и наиболее распространенными сооружениями по обезвреживанию ТБО являются полигоны [7]. Современные полигоны ТБО – это комплексные природоохранные сооружения, предназначенные для обезвреживания и захоронения отходов. Полигоны должны обеспечивать защиту от загрязнения отходами атмосферного воздуха, почвы, поверхностных и грунтовых вод, препятствовать распространению грызунов, насекомых и болезнетворных микроорганизмов.
157
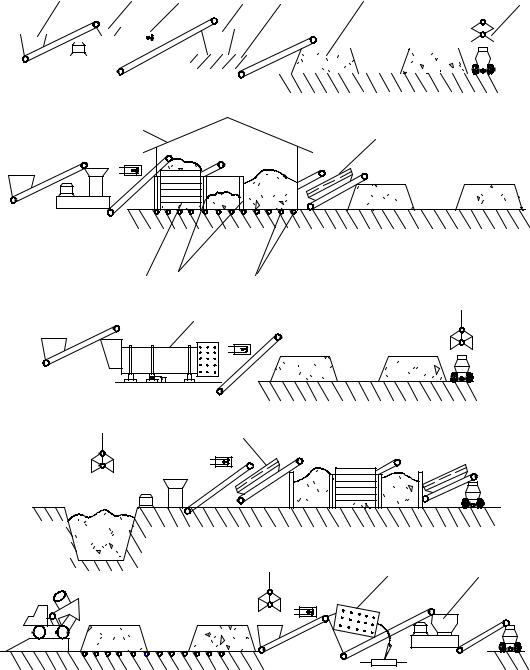
а) |
1 |
2 |
|
3 |
4 |
5 |
6 |
|
|
|
|
|
|
7 |
||||||||||||||||
|
||||||||||||||||||||||||||||||
|
|
|
|
|
|
|
|
|
|
|
|
|
|
|
|
|
|
|
|
|
|
|
|
|
|
|
|
|
|
|
|
|
|
|
|
|
|
|
|
|
|
|
|
|
|
|
|
|
|
|
|
|
|
|
|
|
|
|
|
|
|
|
|
|
|
|
|
|
|
|
|
|
|
|
|
|
|
|
|
|
|
|
|
|
|
|
|
|
|
|
|
|
|
|
|
|
|
|
|
|
|
|
|
|
|
|
|
|
|
|
|
|
|
|
|
|
|
|
|
|
|
|
|
|
|
|
|
|
|
|
|
|
|
|
|
|
|
|
|
|
|
|
|
|
|
|
|
|
|
|
|
|
|
|
|
|
|
|
|
|
|
|
|
|
|
|
|
|
|
|
|
|
|
|
|
|
|
|
|
|
|
|
|
|
|
|
|
|
|
|
|
|
|
|
|
|
|
|
|
|
|
|
|
|
|
|
|
|
|
|
|
|
|
|
|
|
|
|
|
|
|
|
|
|
|
|
|
|
|
|
|
|
|
|
|
|
|
|
|
|
|
|
|
|
|
|
|
б) |
8 |
12 |
|
9 |
10 |
11 |
в) |
|
13 |
14
г)
д) |
15 |
16 |
|
|
Рис. 3.5. Принципиальные схемы сооружений полевого компостирования ТБО:
а – совместная переработка ТБО и осадка сточных вод; б – двухстадийное компостирование ТБО; в – схема с предварительной обработкой ТБО в биобарабане; г – схема с компостированием в открытых отсеках и предварительным грохочением ТБО; д – компостирование недробленых ТБО:
1 – приемный бункер с пластинчатым питателем; 2 – дробилка для ТБО; 3 – подвесной электромагнитный сепаратор; 4 – подача осадков сточных вод; 5 – смеситель; 6 – штабеля; 7 – грейферный кран; 8 – закрытое помещение для первой стадии компостирования; 9 – подвижная установка для перелопачивания и перегрузки компоста; 10 – продольные подпорные стенки; 11 – аэраторы; 12 – контрольный грохот для компостера; 13– биобарабан; 14 – первичный грохот для дробленных ТБО; 15– цилиндрический контрольный грохот; 16 – дробилка для
компоста
Полигоны строят по проектам в соответствии со СНиП. Схема конструктивных эле-
158
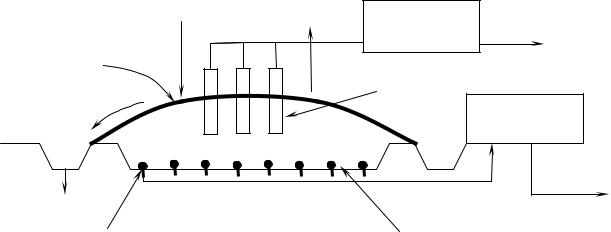
ментов полигона представлена на рис. 3.6.
Верхнее |
Осадки |
Биогаз |
Отбор |
Утилизация |
|
|
|
биогаза |
|||
перекрытие |
|
|
|
||
|
|
|
|
||
|
|
|
Газодренажные скважены |
||
Поверхностный |
|
|
|
Очистка |
|
сток |
|
|
|
||
Отходы |
Отходы |
фильтрата |
|||
|
|||||
|
|
||||
Сток |
Сбор фильтрата |
|
Сброс |
||
|
|
|
|||
|
|
|
|
||
Дренажи |
|
Подложка |
воды |
Рис. 3.6. Принципиальная схема устройства полигона ТБО
Дно полигона оборудуется противофильтрационным экраном – подложкой. Он состоит из глины и других водонепроницаемых слоев (битумогрунт, латекс) и предотвращает попадание фильтрата в грунтовые воды. Фильтрат – жидкость, содержащаяся в отходах, она стекает вниз, на дно полигона, и может просачиваться через его борта. Фильтрат – минерализованная жидкость, содержащая вредные вещества. Собирается фильтрат с помощью дренажных труб и отводится в резервуар для обезвреживания. Ежедневно в конце рабочего дня отходы покрываются специальным материалом и слоями грунта, а затем уплотняются катками. После заполнения секции полигона отходы покрываются верхним перекрытием.
Продуктом анаэробного разложения органических отходов является биогаз, представляющий собой в основном смесь метана и углекислого газа. Система сбора биогаза состоит из нескольких рядов вертикальных колодцев или горизонтальных траншей. П о- следние заполнены песком или щебнем и перфорированными трубами.
Все работы на полигонах по складированию, уплотнению, изоляции ТБО и последующей рекультивации участка должны быть полностью механизированы.
Полигоны ТБО должны обеспечивать охрану окружающей среды по шести показателям вредности:
1.Органолептический показатель вредности характеризует изменение запаха, привкуса и пищевой ценности фитотест-растений на прилегающих участках действующего полигона и территорий закрытого полигона, а также запаха атмосферного воздуха, вкуса, цвета и запаха грунтовых и поверхностных вод.
2.Общесанитарный показатель отражает процессы изменения биологической ак-
тивности и показателей самоочищения почвы прилегающих участков.
3.Фитоаккумуляционный (транслокационный) показатель характеризует процесс миграции химических веществ из почвы близлежащих участков и территории рекультивированных полигонов в культурные растения, используемые в качестве продуктов питания и фуража (в товарную массу).
4.Миграционно-водный показатель вредности выявляет процессы миграции хими-
ческих веществ фильтрата ТБО в поверхностные и подземные воды.
5.Миграционно-воздушный показатель отражает процессы поступления выбросов в атмосферный воздух с пылью, испарениями и газами.
6.Санитарно-токсикологический показатель суммарно характеризует эффект
влияния факторов, действующих в комплексе.
159
Недостатком такого способа утилизации отходов является то, что наряду с образующимся в толще полигона фильтратом, являющимся основным загрязнителем природной среды, в атмосферу попадают токсичные газы, которые не только загрязняют воздушное пространство вблизи полигона, но и отрицательно влияет на озоновый слой земли. Кроме того, при захоронении на полигонах теряются все ценные вещества и компоненты ТБО.
3.6. Термические методы переработки отходов
Термические методы переработки и утилизации ТБО:
1.Слоевое сжигание неподготовленных отходов в мусоросжигательных установках;
2.Слоевое и камерное сжигание специально подготовленных отходов в виде гранулированного топлива (освобожденного от балластных составляющих и имеющего постоянный фракционный состав) в топках энергетических котлов или цементных печах;
3.Пиролиз отходов, прошедших предварительную подготовку или без нее.
3.6.1. Сжигание предварительно неподготовленных отходов
Наиболее распространенным методом термической переработки ТБО является метод слоевого сжигания неподготовленных отходов в мусоросжигательных установках. При этом помимо обезвреживания отходов можно получить тепловую или электрическую энергию, сократить расстояние между местом сбора отходов и мусоросжигательным заводом, значительно сократить земельные площади, отводимые под захоронение ТБО.
Однако при сжигании отходов выделяются твердые и газообразные вредные вещества, поэтому все современные мусоросжигательные заводы (МСЗ) должны быть оборудованы высокоэффективными газоочистными устройствами.
Технологическая схема мусоросжигательного завода показана на рис. 3.7.
160

|
|
пар |
|
14 |
вода |
1 |
13 |
|
|
12 |
11 |
|
15 |
|
|
16 |
|
9 10
2 |
5 |
зола |
|
|
|
|
6 |
7 |
3 |
4 воздух |
8 |
|
||
|
шлак |
|
|
|
Рис. 2.7. Технологическая схема переработки отходов на мусоросжигательных заводах: 1 –
мостовой грейферный кран; 2 и 3 – мусорный и шлаковый отсеки бункера-накопителя; 4 – вентилятор первичного дутьевого воздуха; 5 – станция гидропривода; 6 – паровые калорифе- ры-воздухоподогреватели; 7 – шлакоизвлекатель; 8 – ленточные транспортеры для удаления шлака и золы; 9 – дымосос; 10 – дымовая труба; 11 – электростатический фильтр; 12 – котелутилизатор; 13 – вентилятор вторичного воздуха; 14 – загрузочный бункер; 15 – растопочная
горелка; 16 – колосниковая решетка
Мусор, доставляемый на МСЗ сжигают без какой-либо предварительной подготовки или обработки. При поступлении на завод мусоровозы взвешивают на платформенных автоматических весах. Затем мусоровозы поступают в приемное помещение, где осуществляется выгрузка ТБО в бункер-накопитель. Мусор из бункера-накопителя частями забирает мостовой кран, оборудованный грейферным ковшом. В приемном отделении поддерживается некоторое разряжение воздуха за счет забора из него дутьевого воздуха для поддержания процесса горения ТБО в котлоагрегатах, что предотвращает выброс неприятных запахов и пыли за пределы отделения. Мусор из приемного бункера подают в загрузочный желоб питателя печи котлоагрегата до определенной высоты. Емкость желоба образует буферный резерв питания печи. Образуемая таким образом колонна мусора обеспечивает герметичность между камерой горения и загрузочным бункером. Нижняя часть желоба защищена водяной рубашкой от перегрева в случае подъема пламени. Питатель распределяет мусор по колосниковой решетке, на которой сжигают мусор. Она является основным элементом печи.
Имеется несколько видов колосниковых решеток. Наибольшее применение получило топочное устройство, оборудованное обратно переталкивающей колосниковой решеткой системы «МАРТИН» (Германия), шириной 3 м и наклоненной под углом 26° к горизонтальной плоскости. Решетка имеет одну или несколько секций, каждая из которых состоит из 13 рядов чередующихся подвижных и неподвижных колосников.
161
Каждый второй колосник приводится в возвратно-поступательное движение общим устройством управления. Амплитуда возвратно-поступательного движения в направлении решетки снизу вверх составляет около 400 мм, а число циклов может изменяться от 0 до 60 в час.
Перемещение колосников решетки влияет на процесс сжигания мусора, который при каждом цикле медленно перемешивается и раскладывается по поверхности. Таким образом, в начале решетки образуется интенсивное пламя, при котором все стадии сжигания – сушка, возгорание и сжигание – происходят одновременно. Благодаря наличию сильного пламени в начале решетки газы, выделяющиеся на стадии сушки, смешиваются с очень горячими газами горения и сжигания.
Мусор, сжигаемый на решетке, постепенно перемещается вниз, постоянно перемешиваясь. Сжигание мусора завершается приблизительно на 2/3 длины решетки, а на оставшейся части мусор, превратившийся в шлак, постепенно охлаждается под действием подаваемого в топку воздуха.
Конструкция колосниковой решетки позволяет сжигать отходы с различной теплотой сгорания и большим (до 50 %) содержанием золы при высокой удельной производительности (более 400 кг/(м2·ч)). Площадь колосниковой решетки каждого агрегата 20 м2, номинальная производительность 8,33 т/ч при теплоте сгорания ТБО 6,3 МДж/кг. Температура в топочном пространстве регулируется автоматически и составляет 800…1000 °С, что обеспечивает выгорание твердых и газообразных горючих составляющих отходов.
Для обеспечения требуемого качества сжигания, т. е. для получения хорошо перегоревшего шлака, его необходимо сразу удалять. Шлак составляет около 25 % по массе от общего количества сжигаемых отходов.
Для удаления шлака используют барабаном с регулируемой скоростью вращения, позволяющий и сглаживать толщину слоя мусора и шлака на решетке, а также удалять шлак в бункер шлакового экстрактора. Горячий шлак падает в бункер, а затем в бак с водой, в кото-
ром охлаждается до 80÷90 ºС. Из бака шлак удаляется толкателем, который проталкивает его в желоб, установленный с обратным уклоном. Конструкция желоба позволяет, с одной стороны, уплотнять удаляемый материал без риска закупорки рабочего сечения желоба, а с другой – стекать избыточной влаге. Таким образом, потери воды за счет ее испарения и поглощения шлаком сводятся к минимуму.
Затем охлажденный шлак по системе ленточных транспортеров проходит через виброполотно, где с использованием с магнитного сепаратора, оборудованного электромагнитом, из шлака удаляют металлические частицы. Металлолом удаляют в специальные емкости, а шлак поступает по ленте в шлаковый отсек бункера-накопителя. Зола из-под воздушного короба и из бункеров котла удаляется вместе со шлаком.
Для обеспечения процесса горения отходов подают воздух, нагнетаемый вентилятором первичного дутья через короб, установленный под решеткой и состоящий из нескольких отсеков или зон. Каждая зона подачи воздуха под решетку обеспечивает впуск определенного количества воздуха под решетку и в слой мусора для обеспечения горения; сбор и удаление мелких частиц, просеивающихся под решетку.
В нижней части в подрешеточной зоне установлены воронки асимметричной формы, которые предназначены для сбора и удаления просева.
Дополнительно воздух подается вентилятором вторичного дутья под высоким давлением через сопла, расположенные на передней и задней стенках камеры горения, для полного сжигания газов в нижней части камеры сжигания.
Полученные при сжегании ТБО тепловая энергия и пар могут быть использованы на нужды централизованного теплоснабжения. Для снижения капитальных затрат рационально совмещать на одной площадке мусоросжигательную и промышленно-отопительную котельные. Поэтому целесообразно проектировать комбинированные котельные, имеющие как котлоагрегаты, сжигающие энергетическое топливо, так и котлоагрегаты, в топках которых сжигают ТБО. Таким образом, ТБО можно рассматривать как нетрадиционные виды топли-
162
ва.
3.6.2. Воздействие мусоросжигательных заводов на окружающую среду
Установки по сжиганию ТБО могут служить источником загрязнения воздушной среды взвешенными частицами золы и недожога, а также вредными газообразными примесями. Поэтому при проектировании их особое внимание уделяют совершенствованию средств по снижению выбросов вредных примесей. Физико-химические свойства отходящих газов при сжигании ТБО зависят от морфологического и фракционного составов, теплоты сгорания отходов и т. д.
Эти показатели существенно меняются в зависимости от климатических условий района и сезона года. Влажность ТБО колеблется в пределах 52÷58 % в зависимости от сезона
года, а содержание влаги в дымовых газах меняется в пределах 95÷119 г/м3.
Существует три вида выбросов из мусоросжигательных установок: газы, выходящие из дымовой трубы; сточные воды; летучая зола и шлак.
Наиболее вредными выбросами мусоросжигательных установок считают отходящие газы и летучую золу. Поскольку основной вредной составляющей дымовых газов являются содержащиеся в них взвешенные частицы и отравляющие вещества, то их концентрацию и принимают в качестве главного показателя санитарно-гигиенического аспекта работы таких сооружений.
Зола, образующаяся при сжигании ТБО, состоит в основном из минералов и несгоревших частиц органических соединений.
Содержание недожога обычно не превышает 2 %, а при неблагоприятных условиях может достигнуть 15 % и определяется конструктивными особенностями топочного устройства, а также технологическими условиями процесса горения. Концентрация золы в дымовых
газах мусоросжигательных установок составляет примерно 2÷5 г/м3 сухого газа. Загрязняющие вещества воздуха образуются в результате неполного сгорания части от-
ходов и из новых продуктов в процессе их горения. Продукты неполного сгорания включают оксиды углерода, амины, органические кислоты, полициклические ароматические соединения и т. д. Частные выбросы могут содержать тяжелые металлы, которые при сжигании не разрушаются.
Конечными продуктами сгорания обычно являются диоксид углерода и водяные пары. Другие продукты образуются в меньших количествах. Хлористый водород и небольшое количество хлора образуются в мусоросжигательных установках в процессе хлорирования углеводородов, фтористый водород – из органических фторидов, бромистый водород – из органических бромидов, оксиды серы, главным образом диоксид серы, – из имеющейся в отходах и дополнительном топливе серы, пятиокись фосфора – из фосфорорганических соединений, оксид азота – при горении на воздухе из соединений азота, входящих в состав ТБО.
В связи с постоянным увеличением в составе отходов доли синтетических материалов в будущем вероятно резкое превышение ПДК вредных газообразных веществ в дымовых газах мусоросжигательных установок (хлористого и фтористого водорода, полициклических ароматических углеводородов).
Выбор газоочистных устройств зависит от объема очищаемых газов, их запыленности, желаемой степени очистки (КПД улавливания), физических параметров газового потока (скорости, температуры, влажности, агрессивности), физико-химических свойств взвешенных частиц (дисперсности, слипаемости, абразивности и т. д.). При выборе газоочистных устройств следует учитывать, что труднее всего улавливаются частицы размером менее 5 мкм, масса которых может
достигать 22÷25 % общей массы твердых примесей, содержащихся в очищаемых газах. Выбирают и оценивают работу газоочистительного оборудования в первую очередь по
степени очистки уходящих газов и только во вторую – по ее стоимости. Существует различное газоочистительное оборудование. На современных крупных установках по сжиганию ТБО для улавливания твердых частиц, содержащихся в дымовых газах, применяют электро-
163

статические фильтраты, позволяющие улавливать до 99,8 % частиц практически любых размеров.
3.6.3. Сжигание специально подготовленных отходов
По прогнозам специалистов слоевое или камерное сжигание специально подготовленных отходов в топках котлов или цементных печах в ближайшее время получит широкое применение. В США и Великобритании с 70-х гг. проводятся работы по переработке отходов в гранулированное топливо «Refuse Dering Full» (RDF), которое длительное время можно хранить и транспортировать на относительно большие расстояния и при сжигании которого негативное воздействие на окружающую среду значительно меньше. Однако теплотехнические свойства топлива, получаемого этими странами различны. Так, в США за счет высоких капиталовложений стремятся получить высококачественное топливо, а в Великобритании создают простые дешевые способы получения RDF среднего качества. В США экономичны установки производительностью 1000 т/сут и выше перерабатываемых отходов, а в Великобритании – до 200...300 т/сут.
Технологический процесс получения RDF состоит из двух операций: дробления отходов и сепарации черных металлов. Если ограничиваться только этими двумя операциями, то получаемый в этом случае RDF будет содержать много балластных фракций и иметь низкое качество. Поэтому при изготовлении гранулированного топлива используют дополнительные машины, механизмы и агрегаты, позволяющие обогащать, гранулировать и брикетировать топливо из отходов, при этом возрастают капиталовложения и эксплуатационные расходы, но полученное топливо имеет значительно лучшее качество. Принципиальная схема производства гранулированного топлива приведена на рис. 2.8.
Прием ТБО
Черный Грубое дробление металл
ТБО
|
|
|
|
|
|
|
|
|
|
|
|
|
|
|
|
|
|
|
|
|
|
|
|
|
|
|
|
|
|
|
|
|
|
Сырье для |
|
|
|
|
|
|
|
|
|
|
|
|
|
|
|
|
|
||
Пневматический |
|
|
Тяжелые |
|
|
Магнитный се- |
|
|
|||||||||
|
|
|
|
|
|
получения |
|||||||||||
сепаратор |
|
|
фракции |
|
|
|
паратор |
|
|
|
|||||||
|
|
|
|
|
|
|
|
||||||||||
|
|
|
|
|
|
|
|
компоста |
|||||||||
|
|
|
|
|
|
|
|
|
|
|
|
|
|
|
|
||
|
|
|
|
|
|
|
|
|
|
|
|
|
|
|
|
|
|
|
|
|
|
|
|
|
|
|
|
|
|
|
|
|
|
|
|
Легкие фракции |
|
|
|
|
|
|
|
|
|
|
|
|
|
|
|
|
|
|
|
|
|
|
|
|
|
|
|
|
|
|
|
|
|
|
|
|
|
|
|
|
|
|
|
|
|
|
|
|
|
|
|
|
|
|
|
|
|
|
|
|
|
|
|
|
|
|
|
|
|
|
|
Барабанный |
Мелкие |
|
|
|
|
|
|
|
|
|
|||||||
грохот |
|
|
|
|
фракции |
|
|
|
|
|
|
|
|
|
|||
|
|
|
|
|
|
|
|
|
|
|
|
|
|
|
|
|
|
|
|
|
|
|
|
|
|
|
|
|
|
|
|
|
|
|
|
Крупные фракции |
Пресс- |
|
Гранулированное |
||||||||||||||
|
|
|
|
гранулятор |
|
|
|
|
топливо |
|
|||||||
|
|
|
|
|
|
|
|
|
|
|
Рис. 3.8. Принципиальная схема производства гранулированного топлива
Способ получения гранулированного топлива выбирают в зависимости от вида отходов, их состава, а также последующего способа использования – в качестве основного или дополнительного (вместе с основным – углем, торфом или т.д.) топлива. Теплота сгорания гранулированного топлива колеблется от 5300 до 17700 кДж/кг.
164
Многие котельные установки нуждаются лишь в небольшой модернизации для работы на гранулированном топливе, т. к. они оборудованы устройствами для удаления шлака и летучей золы.
3.6.4. Пиролиз отходов
Наиболее перспективным способом обезвреживания отходов потребления является переработка, состоящая из двух стадий:
1.аэробного биотермического компостирования органической части ТБО (биотермический метод) с получением компоста или биотоплива;
2.пиролиза некомпостируемой части бытовых отходов (НБО), включающих резину, кожу, пластмассы, дерево и т. д.
Под пиролизом понимают процесс термического разложения отходов без доступа ки-
слорода, в результате которого образуются пиролизный газ и твердый углеродистый остаток. Количество и состав продуктов пиролиза зависит от состава отходов и температуры разложения. Пиролиз НБО способствует созданию безотходных и малоотходных технологий
и рациональному использованию природных ресурсов.
Пиролизные установки в зависимости от температурного режима процесса разделяют:
−на низкотемпературные (450÷500 °С), характеризующиеся минимальным выходом газа, максимальным количеством смол, масел и твердых остатков;
−среднетемпературные (до 800 °С), характеризующиеся увеличенным выходом газа
суменьшенным количеством смол и масел;
−высокотемпературные (свыше 800 °С), характеризующиеся максимальным выхо-
дом газов и минимальным количеством смолообразных продуктов. Процесс пиролиза ИБО состоит из:
-пиролиза НБО в печи с внешним обогревом;
-дожига пиролизных газов;
-утилизации тепла отходящих газов в котле-утилизаторе с получением пара;
-очистки дымовых газов от пыли и химических примесей в пенном абсорбере;
-сушки абсорбционных растворов в распылительной сушилке;
-охлаждения пирокарбона в барабане-холодильнике;
-сепарации черного и цветного металла из пирокарбона;
-сепарации камней из пирокарбона;
-измельчения пирокарбона в конусной инерционной дробилке;
-фасовки пирокарбона в мешки и складирования.
Основной узел пиролизной установки – реактор, представляющий собой шахтную печь со встроенной швельшахтой и системой эвакуации газов, предотвращающей смешивание пиролизных и дымовых газов (рис. 3.9).
Из сортировочного отделения НБО по системе конвейерных транспортеров попадают в приемный бункер пиролизной установки. Из бункера отходы забирают грейферным ковшом, смонтированным на подъемном кране. Кран подает отходы в промежуточный бункер, днищем которого служит пластинчатый питатель, предназначенный для загрузки отходов в верхнюю часть реактора, оборудованную тремя затворами шиберного типа.
В печи пиролизной установки при температуре 500÷550 °С без доступа воздуха происходит термическая деструкция (пиролиз) НБО.
165

1
2
|
3 |
|
|
|
|
конденсат |
|
|
|
охлажденный |
|
10 |
4 |
воздух |
|
5 |
|||
|
|
12
|
|
|
6 |
|
9 |
|
|
|
|
|
отходящие |
|
|
|
газы |
11 |
8 |
4 |
7 |
Рис. 3.9. Схема установки высокотемпературного пиролиза:
1 – приемная воронка, 2 – затворы, 3 – конденсатор жидких продуктов, 4 – дроссельные заслонки, 5 – вентилятор, 6 – газоанализатор, 7 – дымосос, 8 – система газоочистки, 9 – сопло подачи подогретого воздуха,
10 – воздухоподогреватель, 11 – водяная ванна, 12 – швельшахта
В результате образуется парогазовая смесь, содержащая в своем составе летучие вещества, пары смолы и твердый углеродсодержащий продукт– пирокарбон.
Присутствующие в НБО кожа, пластмасса, резина и другие продукты разлагаются, образуя летучие вещества, которые помимо СО2 и Н2О, Сl, Р, SО2 содержат углеводороды (олефины, парафины и т. д.). Пиролизные газыподвергаются дальнейшему окислению в специальной камере дожига, превращаясь в менее опасные вещества. Камера дожига имеет горелку, через которую подают природный газ или мазут и воздух на горение, а для снижения температуры образующихся дымовых газов– воздух.
Камера дожига оборудована рубашкой, в которую поступает воздух, охлаждающий стенки камеры, в результате чего температура газов на выходе из камеры дожига снижается до 800 °С. Воздух на горение и разбавление подают дутьевыми вентиляторами.
Дымовые газы из камеры дожига направляются в рубашку печи пиролиза, где тепло дымовых газов используется для обогрева печи. Из рубашки печи пиролизадымовые газы темпе-
ратурой 600÷700 °С направляются для утилизации тепла в котел-утилизатор, в котором в ре-
зультате снижения температуры дымовых газов до 300÷350 °С получают пар.
Пар используют для нужд теплоснабжения производства. Затем дымовые газы температурой 300÷350 °С поступают на распылитель для сушки абсорбционных растворов, использо-
166
ванных в абсорберах, а затем с температурой 120 °С – на абсорбцию и после очистки выбрасываются в атмосферу.
Тепло дымовых газов используется для проведения процесса пиролиза НБО, что позволяет экономить топливо.
Полученный в печи пирокарбон с температурой 450÷500 ºС поступает в холодильный
барабан, где охлаждается до 40÷50 °С, затем по ленточному конвейеру подается на размол. Пирокарбон пройдя электромагнитный сепаратор для извлечения остатков черного металла, поступает на полигональное сито, где освобождается от крупных камней, которые вывозят на свалку. Затем пирокарбон подается на мельницу, где измельчается до 0,5 мм и менее. После измельчения пирокарбон вновь подают на сепарацию для извлечения цветных металлов, которые накапливают в контейнерах, а пирокарбон расфасовывают и затем направляют на склад готового продукта.
Физико-химические свойства пирокарбона: плотность – 2÷2,5 г/см3; удельная поверхность
–2200 см/г; насыпная плотность– 0,6÷0,7 т/м3; гранулометрический состав (d > 0,5 мм– 10 %, d
< 0,5 мм – 90 %). Теплофизические свойства пирокарбона: теплота сгорания – 12000÷13000 кДж/кг; теплопроводность– 0,106 Вт (м·°С); температуропроводность – 11,1 °С·10–8 м2/с.
Поступающие на установку отходы НБО более чем на 90 % состоят из органических веществ, в основной массе которых соотношение углерод : водород : кислород приблизительно
соответствует их соотношению в целлюлозе (С6Н10О5)n. Целлюлоза – высокомолекулярный полисахарид. Клетчатка – главная составная часть органической части отходов, например бумага почти на 100 % состоит из целлюлозы; хлопчатобумажные и текстильные изделия – более чем на 90 %; древесина – примерно на 50 %. При термической обработке целлюлозы (без доступа кислорода) она разлагается, образуя большое количество различных продуктов.
При быстром подъеме температуры образуется большое количество парогазовой смеси и температура внутри аппарата повышается.
Медленное нагревание сопровождается равномерным выделением продуктов реакции, при этом образующееся тепло удаляется с парогазовой смесью, не оказывая существенного влияния на температурный режим внутри аппарата.
Соотношение и состав получаемых газообразных, жидких и твердых продуктов зависят от условий пиролиза и состава исходного продукта.
Квредным составляющим НБО относят: серу, основным источником которой является резина; хлор, выделяющийся при сжигании полимерных материалов; оксиды азота; соединения фтора и т. д.
Для защиты окружающего атмосферного воздуха от загрязнений дымовые газы необходимо тщательно очищать как от золы, так и от химических веществ.
В качестве реагента для очистки дымовых газов применяют известковое молоко, выбор которого зависит от имеющихся в дымовых газах химических примесей и необходимости вывода химических загрязнителей (слабоили труднорастворимые соли) дымовых газов. Используя известковое молоко, достигают достаточно высокой степени очистки дымовых газов и обеспечивают доступность нейтрализующего реагента и простоту обращения с ним.
Система, включающая распылительную сушилку и абсорбер, рассчитана на очистку отхо-
дящих газов от двух одновременно работающих печей пиролиза. При этом качество выбрасываемых газов характеризуется следующими показателями: пыль – 30 мг/м3; SО2 – 50 мг/м3; NOx
–100 мг/м3; Сl– – 10 мг/м3; F– – 2 мг/м3.
Абсорбция пыли и химических примесей из отходящих топочных газов происходит в пенном абсорбере. В качестве орошающего раствора используют известковое молоко. В результате нейтрализации кислых окислов образуются кальциевые соли соответствующих кислот, раствор которых направляют в распылительную сушилку, где образуется сухой шлам – смесь солей и золы.
Шлам собирают в контейнеры и направляют в отвал для хранения или отправляют потребителю.
167
Количество загрязняющих веществ, выделяющихся при пиролизе, составляет примерно 50 % от выделяющихся при сжигании таких же объемов ТБО на МСЗ.
168
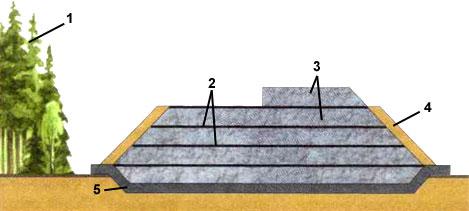
Санитарно-защитные зоны полигонов и контроль за состоянием окружающей
среды
Размеры санитарно-защитной зоны завода по обезвреживанию токсичных промышленных отходов мощностью 100 тыс. т и более следует принимать 1000 м, завода мощностью менее 100 тыс. т – 500 м. размеры санитарно-защитной зоны завода в конкретных условиях строительства должны быть уточнены расчетом рассеивания в атмосфере вредных выбросов. Размеры санитарно-защитной зоны участка захоронение токсичных промышленных отходов до населенных пунктов и открытых водоемов, а также до объектов, используемых в культур- но-оздоровительных целях, устанавливаются с учетом конкретных местных условий, но не менее 3000 м; до сельскохозяйственных угодий и автомобильных и железных дорог общей сети – 200 м; до границ леса и лесопосадок, не предназначенных для использования в рекреационных целях – 50 м.
Обезвреживание и утилизация твердых промышленных отходов - последняя ступень очистки. Методы обезвоживания твердых отходов делятся на ликвидационные (решают са- нитарно-гигиенические задачи) и утилизационные (решают задачи экологии и экономики).
Выделяют биологические методы (разрушение органической части микроорганизмами), термические (сжигание на мусороперерабатывающих предприятиях, пиролиз), химические (гидролиз), механические (прессование с применением связующих на полигонах). Выбор метода для конкретного города зависит от местных условий и осуществляется на основе технико-экономического сравнения. Особо вредные промышленные отходы принимают на полигон в герметически упакованных металлических контейнерах и захоранивают в глубоких котлованах. Кроме технологического паспорта, с каждой партией направляются два акта: в одном подтверждается герметичность упаковки контейнера, в другом указываются название отходов, их количество и причины списания с учета. Контейнеры автокраном спускают на дно котлована. Каждый контейнер со всех сторон засыпают слоем глины (0,5 м). Сверху располагается следующий ряд контейнеров. Размеры котлованов по низу 10х4 м, по верху - 18x12 м, глубина - 4 м в глине, сверху они также засыпаются слоем глины. Разрез полигона для захоронения твердых отходов показан на рис. 6.13.
Рис. 6.13. Разрез полигона для твердых отходов: 1 – лесозащитная полоса; 2 – промежуточный изолирующий слой; 3 – твердые отходы; 4 – укрывающий наружный слой растительного грунта; 5 – естественное или искусственное водоупорное основание (по М.И. Алексееву, Е.М. Протасовскому, 1990)
Большая часть твердых промышленных отходов токсична, поэтому захоранивать их нужно в толще водонепроницаемой глины или в техногенных пустотах шахт (рис.6.14). Например, широко распространен так называемый шведский способ размещения токсичных отходов в техногенных пустотах отработанных шахт, после извлечения из них угля. Шведский способ захоронения токсичных промышленных отходов применим и для захоронения ядови-
169

тых и радиоактивных отходов в специальных контейнерах. Вредные материалы помещаются в специальные контейнера - барабаны, а затем в бетонные кубы. После чего эти бетонные кубы помещаются в подземные пещеры или технологические пустоты шахт.
Рис. 6.14. Шведский способ захоронения токсичных промышленных отходов.
170
4. Конструирование безопасных аппаратов химических производств
4.1. Назначение и характеристика химических аппаратов
Аппараты химических и нефтехимических производств предназначены для ведения в них технологических процессов (химических реакций, теплообмена с изменением или без изменения агрегатного состояния веществ, кристаллизации, растворения, выпарки, адсорбции, абсорбции, ректификации, сепарации, фильтрации и т. д.), а также для хранения или перемещения различных химических веществ.
Содержащиеся и перерабатываемые в аппаратах вещества характеризуются различной химической активностью по отношению к применяемым для этих аппаратов конструкционным материалам и различной степенью воздействия на обслуживающий персонал. Широко применяют химические вещества, обладающие едкими, пожароили взрывоопасными свойствами. Химико-технологические процессы в аппаратах осуществляются при различных, свойственных каждому отдельному процессу технологических параметрах (от глубокого разрежения до избыточного давления в несколько сот МПа, при рабочих температурах от –
254до +900 °С).
Внастоящее время для ведения химико-технологических процессов применяют преимущественно стальные сварные аппараты, изготовленные в соответствии с требованиями ОСТ 26-291–79 [20]. Аппараты, работающие под избыточным давлением более 0,07 МПа (без учета гидростатического давления), кроме указанного стандарта должны соответствовать требованиям Правил устройства и безопасной эксплуатации сосудов, работающих под давлением [26].
Стальные сварные аппараты в зависимости от содержащихся в них веществ и их рабочих параметров в целях определения методов и объема контрольных операций для сварных соединений подразделяются на пять групп согласно табл. 4.1. Методы и объем контрольных операций для сварных соединений приведены в ОСТ 26-291–79.
Таблица 4.1. Характеристика химических аппаратов, ОСТ 26-291–79 [20]
Группа аппа- |
Назначение |
ап- |
Избыточное давление р, МПа |
Температура t, °C |
||||
ратов |
парата |
|
min |
max |
min |
max |
||
|
Для взрывоопас- |
|
|
|
|
|||
|
ных |
веществ |
и |
|
|
|
|
|
|
вредных веществ |
|
|
|
Не ограниче- |
|||
1 |
1-го и 2-го клас- |
0,07 |
16,0 |
–70* |
||||
на |
||||||||
|
сов |
опасности |
|
|
|
|||
|
|
|
|
|
||||
|
согласно ГОСТ |
|
|
|
|
|||
|
12.1.007–76* |
|
|
|
|
|
171
Продолжение табл. 4.1 |
|
|
|
|
|
|
|
||
|
|
|
|
|
|
|
|
||
Группа аппа- |
Назначение |
аппа- |
Избыточное давление р, МПа |
Температура t, °C |
|||||
ратов |
рата |
|
|
|
min |
max |
min |
max |
|
2 |
|
|
|
|
|
4,0 |
16,0 |
–70* |
–40 |
|
Для веществ, ко- |
5,0 |
–40 |
+200 |
|||||
|
|
2,5 |
|
+200 |
+400 |
||||
|
|
торые |
не |
преду- |
0,07 |
4,0 |
–70 * |
–40 |
|
3 |
|
смотрены в |
аппа- |
0,07 |
5,0 |
–40 |
–20 |
||
|
ратах 1-й группы |
1,60 |
5,0 |
–20 |
+200 |
||||
|
|
||||||||
|
|
|
|
|
|
0,07 |
2,5 |
+200 |
+400 |
4 |
|
|
|
|
|
0,07 |
1,6 |
–20 |
+200 |
|
|
Для взрыво- и по- |
|
|
|
|
|||
|
|
жароопасных |
ве- |
|
|
|
|
||
|
5а |
ществ |
и вредных |
|
|
|
|
||
|
веществ 1, 2 и 3-го |
|
|
|
|
||||
|
|
классов опасности |
|
|
|
|
|||
|
|
согласно |
ГОСТ |
|
|
|
|
||
5 |
|
12.1.007–76* |
|
Остаточное |
0,07 |
−70* |
He ограниче- |
||
|
Для взрыво- и по- |
650 Па |
на |
||||||
|
|
|
|
||||||
|
|
жаробезопасных |
|
|
|
|
|||
|
|
веществ и вредных |
|
|
|
|
|||
|
5б |
веществ 4-го клас- |
|
|
|
|
|||
|
|
са опасности |
со- |
|
|
|
|
||
|
|
гласно |
|
ГОСТ |
|
|
|
|
|
|
|
12.1.007–76* |
|
|
|
|
|
Примечание. К аппаратам 5-й группы следует относить также и аппараты вместимостью до 0,025 м3 при выполнении условия pV < 0,02, где р – давление в МПа; V – вместимость в м3.
* − Для аппаратов, выполняемых из сталей аустенитного класса, допускается более низкая рабочая температура, при которой ударная вязкость а11 > 0,3 мДж/м2.
4.2. Классификация опасных и вредных производственных факторов
Опасные и вредные производственные факторы классифицируют согласно ГОСТ 12.0.003–74* и подразделяют на физические, химические, биологические и психофизиологические.
При работе аппаратов в условиях химических и нефтехимических производств следует учитывать возможность возникновения следующих опасных и вредных производственных факторов:
1.Физические опасные и вредные производственные факторы: наличие подвижных частей аппаратов, повышенная загазованность и запыленность воздуха рабочей зоны, повышенная или пониженная температура поверхностей аппаратов и воздуха рабочей зоны, повышенные уровни звукового давления, вибрации, ультразвука, статического электричества, повышенное напряжение в электрической цепи, повышенная или пониженная влажность, подвижность и ионизация воздуха, острые кромки оборудования, расположение рабочих мест на значительной высоте.
2.Химические опасные и вредные производственные факторы в зависимости от воздействия на организм подразделяются на токсические, раздражающие, канцерогенные (вызывающие образование злокачественных опухолей), мутагенные (воздействующие на генетический аппарат клетки); они могут проникать в организм человека через органы дыхания, желудочно-кишечный тракт, кожные покровы и слизистые оболочки.
3.Биологические опасные и вредные производственные факторы: бактерии, вирусы и продукты их жизнедеятельности.
4.Психофизиологические опасные и вредные производственные факторы: физические
172
и нервно-психические перегрузки.
При определении наличия тех или иных опасных и вредных производственных факторов следует учитывать, что один и тот же фактор по природе своего действия может относиться одновременно к различным вышеперечисленным группам.
4.3. Требования к конструкционным материалам
Специфические условия работы химических аппаратов, характеризуемые диапазоном давлений от глубокого разрежения (вакуума) до избыточных давлений порядка 250 МПа и выше, большим интервалом рабочих температур (от –254 до +1000 °С и выше) при агрессивном воздействии среды, предъявляют высокие требования к выбору конструкционных материалов проектируемой аппаратуры.
Наряду с обычными требованиями высокой коррозионной стойкости в определенных агрессивных средах к конструкционным материалам, применяемым в химическом аппаратостроении, одновременно предъявляют также требования высокой механической прочности, жаростойкости и жаропрочности, сохранения удовлетворительных пластических свойств при высоких и низких температурах, устойчивости при знакопеременных или повторных нагрузках (циклической прочности), малой склонности к старению и др.
В расчетах на прочность химической аппаратуры конструктору приходится учитывать общую равномерную по поверхности коррозию металлов и сплавов, для чего необходимо знать проницаемость материала (в мм в год) при заданных рабочих условиях агрессивной среды (концентрация, температура, давление). В ряде случаев при конструировании химической аппаратуры необходимо учитывать также и другие виды коррозионного разрушения материалов. Например, в химических аппаратах, выполненных из кислотостойкой стали и находящихся под постоянным повышенным давлением, при совместном действии коррозионной среды и растягивающих напряжений в ряде случаев наблюдается коррозионное растрескивание металла. Этого не происходит при наличии в металле напряжений сжатия. Кроме того, коррозионное растрескивание происходит в небольшом количестве агрессивных сред и зависит от давления и температуры. Известно, что ускоренное растрескивание аппаратуры из кислотостойких хромоникелевых сталей с содержанием хрома около 18 % и никеля около 8 %, находящейся под постоянно действующей нагрузкой, имеет место в растворах NaCl, MgCl2, ZnCl2, LiCl, H2S, морской воде [33]. Латуни обнаруживают склонность к коррозионному растрескиванию в среде аммиака [33].
Для химической аппаратуры преимущественно применяют конструкционные материалы, стойкие и весьма стойкие в агрессивных средах. Материалы пониженной стойкости применяют в исключительных случаях, когда обоснована целесообразность использования их вместо стойких, но более дорогих и дефицитных материалов. Данные по коррозионной стойкости металлов и сплавов и химической стойкости неметаллических материалов в различных агрессивных средах приведены в специальной справочной литературе [13, 32, 33] и в других источниках, которыми рекомендуется пользоваться при конструировании химической аппаратуры. При отсутствии литературных данных характеристики коррозионной стойкости применяемых для проектируемой аппаратуры конструкционных материалов должны быть получены в результате проведения специальных исследований.
При выборе материалов для аппаратов, работающих под давлением при низких и высоких температурах, необходимо учитывать, что механические свойства материалов существенно изменяются в зависимости от температуры. Как правило, прочностные свойства металлов и сплавов повышаются при низких температурах и понижаются при высоких.
При статическом приложении нагрузки важными характеристиками для оценки прочности материала являются предел текучести σт (или условный предел текучести σ0,2) и предел прочности σв. Упругие свойства металлов характеризуются значениями модуля нор-
мальной упругости Е и коэффициентом Пуассона µ. Указанные характеристики являются основными при расчетах на прочность деталей аппаратуры, работающей под давлением при
173
низких (от –254 до –40 °С), средних (от –40 до +200 °С и высоких (выше +200 °С) температурах.
Для работы при низких температурах по нормам Ростехнадзора [31] следует выбирать металлы, у которых порог хладоломкости лежит ниже заданной рабочей температуры. Однако в химической промышленности на протяжении многих лет безаварийно эксплуатируют при рабочих температурах до –40 °С большое количество аппаратов, трубопроводов, арматуры, насосов и другого оборудования, изготовленных из углеродистой стали обыкновенного качества и из серого и ковкого чугуна, т. е. из материалов, имеющих ударную вязкость при указанной температуре менее 0,2 МДж/м2. Поэтому при выборе металла для работы при низких температурах следует исходить не только из величины ударной вязкости, но также учитывать величину и характер приложенной нагрузки (статическая, динамическая, пульсирующая), наличие и характер концентраторов напряжений и чувствительность металла к надрезам, начальные напряжения в конструкции, способ охлаждения металла (за счет содержащегося в аппарате хладоносителя или за счет окружающей среды).
При статическом приложении нагрузки в ряде случаев допускается изготовление аппаратов из металлов, приобретающих хрупкость при пониженных рабочих температурах, но не имеющих дефектов, нарушающих однородность структуры и способствующих концентрации напряжений. Технология изготовления аппаратов из таких материалов должна исключать возможность возникновения высоких начальных напряжений в конструкции. К таким аппаратам можно отнести свободно опирающиеся емкости для жидких и газообразных продуктов, содержащихся в них под небольшим избыточным давлением, металлоконструкции неответственного назначения и др.
При динамическом приложении нагрузки кроме указанных выше характеристик необходимо учитывать также и величину ударной вязкости. Для многих углеродистых и легированных сталей ударная вязкость при низких температурах (обычно ниже –40 °С) резко понижается, что исключает применение этих материалов в таких условиях. Ударная вязкость для большинства цветных металлов и сплавов (меди и ее сплавов, алюминия и его сплавов, никеля и его сплавов), а также хромоникелевых сталей аустенитного класса при низких температурах, как правило, уменьшается незначительно, и пластические свойства этих материалов сохраняются на достаточно высоком уровне, что и позволяет применять их при рабочих температурах до –254 °С.
Для оборудования, подверженного ударным и пульсирующим нагрузкам и предназначенного для работы при низких температурах, следует применять металлы и сплавы с ударной вязкостью не ниже 0,2 МДж/м2 при рабочих температурах. Для деталей, имеющих концентраторы напряжений (болты, шпильки), рекомендуются материалы, у которых при рабочей температуре ударная вязкость не менее 0,4 МДж/м2.
При высокой температуре наблюдается значительное снижение основных показателей, характеризующих прочностные свойства металлов и сплавов. Кроме того, поведение металлов под нагрузкой при высоких температурах отличается от поведения при нормальной тем-
пературе внутри производственных помещений. Предел прочности σв и предел текучести σт зависят от времени пребывания под нагрузкой и скорости нагружения, так как с повышением температуры металл из упругого состояния переходит в упругопластическое и под нагрузкой непрерывно деформируется (явление ползучести). Температуры, при которых начинается ползучесть, у разных металлов различны. Для углеродистых сталей обыкновенного качества ползучесть наступает уже при температурах выше 375 °С, для низколегированных сталей – при температурах выше 525 °С, для жаропрочных – при более высоких температурах.
С увеличением времени пребывания металла под нагрузкой характеристики прочности уменьшаются тем значительнее, чем выше температура эксплуатации оборудования. Поэтому при расчете на прочность аппаратов, работающих длительное время при высоких температурах, допускаемые напряжения определяют по отношению к условному пределу ползуче-
сти σпл или пределу длительной прочности σдл. Для химической аппаратуры допускаемая скорость ползучести принимается не выше 10−7 мм/(мм ч) (10−5 % в год), для крепежных де-
174
талей – не выше 10−9 мм/(мм ч) (10−7 % в год) [13].
Понижение механических свойств при высоких температурах обусловлено происходящими в металле структурными и фазовыми превращениями. В большинстве случаев для химической аппаратуры, предназначенной для работы при высоких температурах, применяют специальные марки жаропрочных сталей, характеризуемых достаточной механической прочностью и стабильностью структуры при высоких температурах. Наряду с жаропрочностью эти металлы должны обладать также и жаростойкостью, т. е. способностью противостоять коррозионному воздействию среды в условиях длительной работы при высоких температурах. При непрерывном процессе окалинообразования рабочее сечение металла уменьшается, что приводит к повышению рабочего напряжения и ухудшению условий безопасной эксплуатации оборудования.
Некоторые детали химической аппаратуры (пружины, болты, шпильки и др.) вследствие повышения пластичности металла. При высоких температурах работают в условиях постепенного снижения напряжений, вызванных первоначально приложенной нагрузкой (затягом), при сохранении геометрических размеров (явление релаксации напряжений). Такие детали следует рассчитывать на предварительную нагрузку (затяг), обеспечивающую на заданный период времени остаточную нагрузку, необходимую для нормальной работы конструкции.
В химическом аппаратостроении основным способом выполнения металлических неразъемных соединений является сварка, а в ряде случаев пайка. Хорошая свариваемость металлов является одним из основных и необходимых условий, определяющих пригодность материала для безопасной эксплуатации конструкции аппарата.
Таким образом, при конструировании химической аппаратуры, отвечающей требованиям безопасной эксплуатации, к конструкционным материалам должны предъявляться следующие основные требования:
1)достаточная общая химическая и коррозионная стойкость материала в агрессивной среде с заданными концентрацией, температурой и давлением, при которых осуществляется технологический процесс, а также стойкость против других возможных видов коррозионного разрушения (межкристаллитная коррозия, электрохимическая коррозия сопряженных металлов в электролитах, коррозия под напряжением и др.);
2)достаточная механическая прочность при заданных давлениях и температуре технологического процесса с учетом специфических требований, предъявляемых при испытании аппаратов (на прочность, герметичность и т. п.) и при эксплуатации (воздействие на аппараты различного рода дополнительных нагрузок: ветровой, прогиба от собственного веса и т.
д.);
3)наилучшая способность материала свариваться с обеспечением высоких механических свойств сварных соединений и коррозионной стойкости их в агрессивной среде.
Для изготовления сварной стальной химической аппаратуры применяются следующие стали в виде полуфабрикатов, удовлетворяющих вышеуказанным общим требованиям, предъявляемым к конструкционным материалам:
сталь углеродистая обыкновенного качества согласно ГОСТ 380–71*, поставляемая в виде листового, сортового и фасонного проката, труб, поковок и т. д., преимущественно группы В [поставляется по механическим свойствам и химическому составу, по степени раскисления – спокойная (сп), полуспокойная (пс), реже – кипящая (кп), по требованиям от второй до шестой категорий];
сталь качественная углеродистая конструкционная, поставляемая в виде листового проката согласно ГОСТ 5520–79* и в виде сортового проката и труб согласно ГОСТ 1050– 74**;
сталь низколегированная (с содержанием легированных элементов до 2,5 %), поставляемая в виде листового проката согласно ГОСТ 5520–79* и ГОСТ 19282–73*, сортового и фасонного проката, труб и поковок согласно ГОСТ 19281–73*;
сталь легированная конструкционная (с содержанием легирующих элементов до 10 %),
175
поставляемая в виде сортового проката, труб и поковок согласно ГОСТ 4543–71*; сталь теплоустойчивая согласно ГОСТ 20072–74*, поставляемая в виде листового и
сортового проката и труб; стали высоколегированные и сплавы коррозионно-стойкие, жаростойкие и жаропроч-
ные согласно ГОСТ 5632–72*, поставляемые в виде листового проката, труб и поковок; стали и сплавы с особыми свойствами, поставляемые в виде листового и сортового
проката и труб по специальным ТУ; стали двухслойные, поставляемые в виде листового проката согласно ГОСТ 10885–85 и
специальным ТУ с основным слоем из углеродистых, низколегированных и легированных сталей и плакирующим слоем из коррозионно-стойких материалов;
отливки из конструкционной, нелегированной и легированной сталей, поставляемые согласно ГОСТ 977–75*;
отливки из высоколегированных сталей, поставляемые согласно ГОСТ 2176–77* и специальным ТУ.
Кипящая углеродистая сталь не должна применяться в аппаратах, предназначенных для сжиженных газов, соприкасающихся со взрыво- и огнеопасными средами, средами высокой токсичности и средами, вызывающими коррозионное растрескивание металла.
Применение указанных марок на другие рабочие параметры, а также других материалов допускается только на основании заключения головного отраслевого института и разрешения соответствующего министерства.
Стали имеют следующее обозначение:
1)углеродистые обыкновенного качества – последовательно указываются группа, марка стали, степень раскисления и категория требований, например ВСтЗспЗ;
2)качественные, углеродистые конструкционные – обозначают двумя цифрами, показывающими среднее содержание углерода в сотых долях процента, например 20 (для обозначения котельных марок в конце ставится буква К, например 20К);
3)легированные – обозначают комплексом цифр и букв, причем первые две цифры указывают содержание углерода в сотых долях процента (отсутствие цифр означает, что среднее содержание углерода составляет около 0,01 %), затем последовательно идут буквы, означающие наличие в стали того или иного легирующего элемента, за каждой из букв одной или двумя цифрами указывается примерное содержание данного элемента в процентах (отсутствие цифр означает, что содержание данного элемента не превышает 1,5 %).
Буквенные обозначения в марках стали: Г – марганец, С – кремний, X – хром, Н – никель, М – молибден, В – вольфрам, Ф – ванадий, Т – титан, Д – медь, Ю – алюминий, Б – ниобий, Р – бор, А – азот (в конце обозначения не ставятся). Наличие в конце обозначения буквы А означает высококачественную сталь, а цифры III (через дефис) – особо высококачественную.
4.4. Обеспечение пожаро- и взрывобезопасности 4.4.1. Общие правила соблюдения пожаро- и взрывобезопасности
Для предупреждения взрыва необходимо исключить одновременное действие двух факторов: образования взрывоопасной среды и возникновения источника инициирования взрыва. При этом следует рассматривать возможность возникновения взрывоопасных условий как внутри оборудования, так и в окружающей аппараты среде.
Предупреждение возможности взрыва внутри аппаратов достигается путем поддер-
жания рабочей среды вне области концентрационных и температурных пределов воспламенения. В этих же целях применяют ингибирующие и флегматизирующие вещества. Например, для транспортирования путем передавливания легковоспламеняющихся, а также горю-
чих жидкостей, нагретых до температуры выше20 °C, необходимо применять инертный газ
[22].
Источниками инициирования взрыва могут быть искрение, возникающее вследствие
176

неправильного выбора электрооборудования или образования высоких потенциалов статического электричества, нагрев рабочей среды выше температуры самовоспламенения, тепловые проявления химических реакций, применение материалов, дающих искру при coyдарении.
Для устранения источников инициирования взрывов следует использовать электрооборудо-
вание с элементами защиты и средства защиты от статического электричества [23], применять коррозионно-стойкие материалы, не искрящие при соударении [34], ограничивать нагрев аппаратов температурами, указанными в табл. 4.2.
Таблица 4.2. Предельная температура нагрева наружных частей аппаратов и приводов, устанавливаемых во взрывоопасных зонах
Группа взрывоопасной смеси |
Предельная температура нагрева, °С |
Т1 |
450 |
Tl; T2 |
300 |
Т1–ТЗ |
200 |
Tl–T4 |
135 |
Tl–T5 |
100 |
Т1– Т6 |
85 |
Взрывозащита аппаратов обеспечивается установкой предохранительных устройств, а также применением взрывных клапанов [11] и автоматических систем подавления взрывов [8]. В экономически обоснованных случаях аппараты рассчитывают на давление, превышающее максимальное давление взрыва.
Пожарную опасность веществ и материалов оценивают в целях получения исходных данных для классификации производств по степени пожарной опасности и разработки противопожарных мероприятий.
К газам относят вещества, давление насыщенного пара которых при температуре 50 °С составляет не менее 0,3 МПа, к жидкостям – вещества с температурой плавления не более 50 °С, к твердым веществам – вещества с температурой плавления, превышающей 50 °С.
4.4.2. Классификация помещений и зданий по взрывопожарной
ипожарной опасности
Взависимости от физико-химических свойств применяемых веществ и характера технологического процесса помещения и здания подразделяются по взрывопожарной и пожарной опасности на категории А, Б, В, Г и Д (табл. 4.3).
Таблица 4.3. Категории помещений по взрывопожарной и пожарной опасности (согласно ОНТП 24–86)
Категория помеще- |
Характеристика веществ и материалов, находящихся (обращающихся) |
|
|
ния |
в помещении |
|
|
Горючие газы, легковоспламеняющиеся жидкости с температурой вспышки |
|
|
не более 28 °С в таком количестве, что могут образовывать взрывоопасные |
А |
(взрывопожароопас- |
парогазовоздушные смеси, при воспламенении которых развивается рас- |
четное избыточное давление взрыва в помещении, превышающее 5 кПа. |
||
ная) |
Вещества и материалы, способные взрываться и гореть при взаимодействии |
|
|
|
|
|
|
с водой, кислородом воздуха или друг с другом, в таком количестве, что |
|
|
расчетное избыточное давление взрыва в помещении превышает 5 кПа. |
|
|
Горючие пыли или волокна, легковоспламеняющиеся жидкости с темпера- |
Б |
(взрывопожароопас- |
турой вспышки более 28 °С, горючие жидкости в таком количестве, что мо- |
гут образовывать взрывоопасные пылевоздушные или паровоздушные сме- |
||
ная) |
си, при воспламенении которых развивается расчетное избыточное давле- |
|
|
|
|
|
|
ние взрыва в помещении, превышающее 5 кПа |
177
Продолжение табл. 4.3
Категория по- |
Характеристика веществ и материалов, находящихся (обращающихся) в |
|
мещения |
помещении |
|
|
Горючие и трудногорючие жидкости, твердые горючие и трудно горючие ве- |
|
В (пожароопас- |
щества и материалы (в том числе пыли и волокна), способные при взаимодей- |
|
ная) |
ствии с водой, кислородом воздуха или друг с другом только гореть, при усло- |
|
вии, что помещения, в которых они имеются в наличии или обращаются, не от- |
||
|
||
|
носятся к категориям А и Б. |
|
|
Негорючие вещества и материалы в горячем, раскаленном или расплавленном |
|
Г |
состоянии, процесс обработки которых сопровождается выделением лучистого |
|
тепла, искр и пламени; горючие газы, жидкости и твердые вещества, которые |
||
|
||
|
сжигаются или утилизируются в качестве топлива. |
|
|
Негорючие вещества и материалы в холодном состоянии. Допускается отно- |
|
|
сить к категории Д помещения, в которых находятся горючие жидкости в сис- |
|
Д |
темах смазки, охлаждения и гидропривода оборудования в количестве не более |
|
|
60 кг в единице оборудования при давлении не более 0,2 МПа, кабельные элек- |
|
|
тропроводки к оборудованию, отдельные предметы мебели на рабочих местах. |
Согласно СНиП 2.09.02–85, категории помещений и зданий устанавливаются в технологической части проекта в соответствии с общесоюзными нормами технологического проектирования (ОНТП 24–86) «Определение категорий помещений и зданий по взрывопожарной и пожарной опасности». При наличии ведомственных норм технологического проектирования или специальных перечней взрывопожароопасных и пожароопасных помещений, разработанных с учетом специфической опасности конкретных производств, категории зданий и помещений определяют по этим нормам и перечням.
Ниже приведены условия, которые должны выполняться при классификации зданий по взрывопожарной и пожарной опасности.
1.Здание относится к категории А, если в нем суммарная площадь помещений категории А превышает 5 % площади всех помещений или 200 м2. Допускается не относить здание
ккатегории А, если суммарная площадь помещений категории А в здании не превышает 25 % площади всех размещенных в нем помещений (но не более 1000 м2) и эти помещения оборудованы установками автоматического пожаротушения.
2.Здание относится к категории Б, если одновременно выполнены два условия: а) зда-
ние не относится к категории А; б) суммарная площадь помещений категорий А и Б превышает 5 % суммарной площади всех помещений или 200 м2. Допускается не относить здание к
категории Б, если суммарная площадь помещений категорий А и Б не превышает 25 % суммарной площади всех размещенных в здании помещений (но не более 1000 м2) и эти помещения оборудованы установками автоматического пожаротушения.
3.Здание относится к категории В, если одновременно выполнены два условия: а) здание не относится к категориям Аи Б; б) суммарная площадь помещений категорий А, Б и В превышает 5 % (10 %, если в здании отсутствуют помещения категорий А и Б) суммарной площади всех помещений. Допускается не относить здание к категории В, если суммарная
площадь помещений категорий А, Б и В в здании не превышает 25 % суммарной площади всех размещенных в нем помещений (но не более 3500 м2) и эти помещения оборудованы установками автоматического пожаротушения.
4.Здание относится к категории Г, если одновременно выполнены два условия: а) здание не относится к категориям А, Б или В; б) суммарная площадь помещений категорий А, Б, В и Г превышает 5 % суммарной площади всех помещений. Допускается не относить здание
ккатегории Г, если суммарная площадь помещений категорий А, Б, В и Г в здании не превышает 25 % суммарной площади всех размещенных в нем помещений (но не более 5000 м2) и помещения категорий А, Б, В оборудованы установками автоматического пожаротушения.
5.Здание относится к категории Д, если оно не относится к категориям А, Б, В, Г.
178
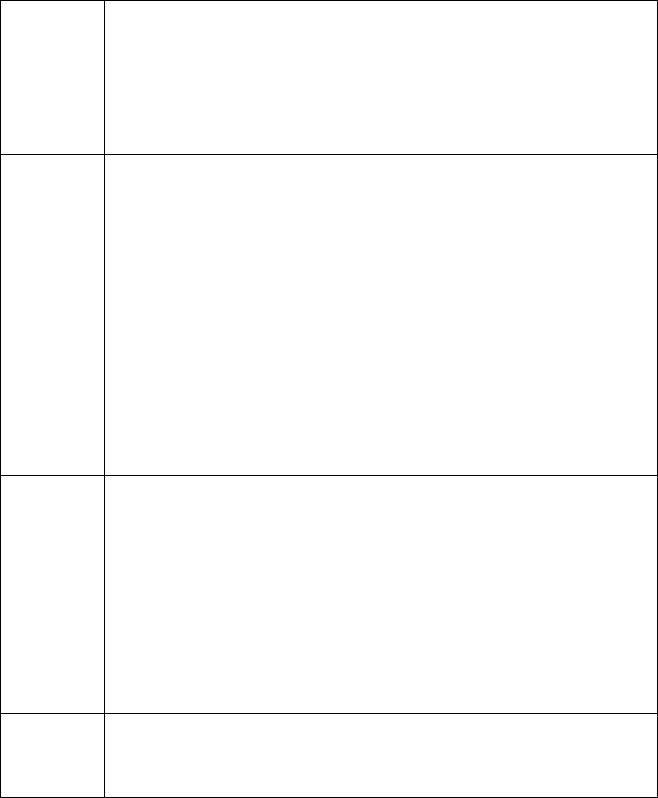
4.4.3. Выбор электрооборудования для аппаратов пожаро- и взрывоопасных производств
4.4.3.1. Классификация взрывоопасных зон
В зависимости от степени опасности применяемых веществ и особенностей технологических процессов все взрывоопасные зоны разделяются согласно Правилам устройства электроустановок [27] на следующие шесть классов табл. 4.4.
Таблица 4.4. Взрывоопасные зоны
Класс зоны |
Характеристика зоны |
|
Зоны, расположенные в помещениях, в которых выделяются горючие газы |
|
или пары в таком количестве и с такими свойствами, что они могут образовать с воз- |
B-I |
духом взрывоопасные смеси при нормальных режимах работы, например при загруз- |
|
ке или разгрузке технологических аппаратов, хранении или переливании легковос- |
|
пламеняющихся жидкостей (ЛВЖ), находящихся в открытых емкостях. |
|
Зоны, расположенные в помещениях, в которых при нормальной эксплуата- |
B-Ia |
ции взрывоопасные смеси горючих газов или паров ЛВЖ с воздухом не образуются, |
|
это может произойти только в результате аварии или неисправности оборудования. |
Зоны, расположенные в помещениях, в которых при нормальной эксплуатации
не образуются взрывоопасные смеси горючих газов или паров ЛВЖ с воздухом, это возможно только в результате аварий или неисправности оборудования. Эти зоны отличаются одной из следующих особенностей:
1.Горючие газы в этих зонах имеют нижний концентрационный предел воспламенения 15 % и более и резкий запах при предельно допустимых концентрациях согласно ГОСТ 12.1.005–76 (например, машинные залы аммиачных компрессорных установок);
2.Горючие газы и ЛВЖ в этих зонах имеются в количествах, недостаточных
B-Iб для создания взрывоопасной смеси, превышающей по объему 5 % свободного объема помещения; работа с горючими газами и ЛВЖ проводится без применения открытого пламени (например, лабораторные помещения); эти зоны не относятся к взрывоопасным, если работы с горючими газами и ЛВЖ проводятся в вытяжных шкафах или под вытяжными зонтами;
3. По условиям технологического процесса исключается образование взрывоопасной смеси водорода с воздухом в объеме, превышающем 5 % свободного объема помещения; при этом взрывоопасная зона условно принимается от отметки 0,75 общей высоты помещения, считая от уровня пола, но не выше кранового пути (например, помещения для электролиза воды).
Пространства у наружных установок. Взрывоопасные зоны у наружных уста-
новок ограничиваются по горизонтали и вертикали следующими размерами:
0,5 м – от проемов за наружными ограждающими конструкциями помещений
со взрывоопасными зонами классов B-I, B-Ia и В-ΙΙ;
3 м – от закрытых технологических аппаратов, содержащих горючие газы и ЛВЖ; от вытяжных вентиляторов, установленных вне помещения, но удаляющих за-
B-Iг грязненный воздух из помещения со взрывоопасными зонами любого класса;
5 м – от места выброса взрывоопасных и горючих веществ из предохранительных и дыхательных клапанов; от расположенных на зданиях устройств для выброса воздуха из систем вытяжной вентиляции помещений со взрывоопасными зонами любого класса;
8 м – от резервуаров с ЛВЖ газгольдеров, а при наличии обвалования – в пределах всей площади внутри обвалования;
20 м – от мест открытого слива и налива ЛВЖ на эстакадах.
Зоны, расположенные в помещениях, в которых выделяются переходящие во
взвешенное состояние горючие пыли или волокна в таком количестве и с такими B-II свойствами, что они способны образовывать с воздухом взрывоопасные смеси при нормальных режимах работы (например, при загрузке и разгрузке технологических
аппаратов).
179
Продолжение табл. 4.4
Класс зоны |
Характеристика зоны |
B-IIa |
Зоны, расположенные в помещениях, в которых опасные состояния, приня- |
тые для зон класса В-ΙΙ, не имеют места при нормальной эксплуатации, а возможны |
|
|
только в результате аварий или неисправностей оборудования. |
Определение класса взрывоопасной зоны и ее размеров проводится технологами совместно с электриками проектных организаций или предприятий, эксплуатирующих оборудование. Учитывая, что изложенные в Правилах устройства электроустановок [27] основы классификации взрывоопасных зон носят общий характер, для отдельных отраслей промышленности разработаны перечни взрывоопасных зон конкретных производств.
При определении классов взрывоопасных зон следует исходить из аварийной ситуации, когда имеет место серьезное повреждение аппаратов с выделением горючих веществ, образующих с воздухом взрывоопасные смеси.
При определении класса взрывоопасной зоны принимают:
а) взрывоопасная зона занимает весь объем помещения, если объем взрывоопасной смеси превышает 5 % свободного объема помещения;
б) взрывоопасной считается зона в пределах 5 м по горизонтали и вертикали от аппарата, из которого могут выделяться горючие газы или пары ЛВЖ, создающие взрывоопасную смесь в объеме, равном или менее 5 % свободного объема помещения.
Зоны в помещениях, где установлены вытяжные вентиляторы, обслуживающие взрывоопасные зоны любого класса, относятся к тому же классу.
Взрывоопасные зоны, содержащие легкие несжиженные горючие газы или ЛВЖ, при наличии признаков класса B-I, допускается относить к классу В-Ia при условиях:
а) установки резервных вентиляторов, автоматически включающихся при аварийной остановке основных вентиляторов;
б) устройства автоматической сигнализации, действующей при возникновении в любой точке помещения концентрации горючих газов или паров ЛВЖ не более 20 % от нижнего концентрационного предела воспламенения.
К числу взрывоопасных зон в части их электрооборудования не относятся:
1)зоны в помещениях и зоны наружных установок, в которых твердые, жидкие и газообразные вещества сжигаются в качестве топлива или утилизируются путем сжигания;
2)зоны в помещениях и зоны наружных установок в пределах 5 м по горизонтали и вертикали от аппаратов со взрывоопасными веществами при условий, что технологический процесс в этих аппаратах ведется с применением открытого огня или наружные поверхности аппаратов нагреты до температуры самовоспламенения применяемых веществ;
3)зоны расположения эстакад с закрытыми сливно-наливными устройствами и зона расположения опор под трубопроводы для горючих газов и ЛВЖ, за исключением зон, в которых находятся запорная арматура и фланцевые соединения этих трубопроводов;
4)зоны в помещениях приточных вентиляторов, обслуживающих взрывоопасные зоны любого класса, при условии оборудования напорных воздуховодов самозакрывающимися обратными клапанами, не допускающими проникновения взрывоопасных смесей в помещения приточных вентиляторов при прекращении подачи воздуха.
В производственных помещениях без взрывоопасной зоны, отделенных стенами от помещений, имеющих взрывоопасную зону, следует устанавливать взрывоопасную зону в пределах 5 м по горизонтали и вертикали от проема двери. Класс взрывоопасности этой зоны устанавливается в соответствии с табл. 4.5.
При классификации взрывоопасных производств должны учитываться условия, способствующие снижению класса взрывоопасности. К ним относятся:
а) надежная герметизация технологических аппаратов; б) обеспечение кратности воздухообмена во взрывоопасной зоне, гарантирующее сни-
жение концентрации взрывоопасной смеси менее 50 % от нижнего концентрационного пре-
180
дела воспламенения; в) применение газов, плотность которых менее 0,8 плотности воздуха, и естественной
вентиляции, обеспечивающей кратность обмена, предусмотренную технологическим регламентом;
г) оснащение взрывоопасных зон автоматическими газоанализаторами, подающими сигналы и отключающими электроэнергию при повышении концентрации взрывоопасных газов.
Таблица 4.5. Классификация помещений, смежных со взрывоопасными зонами соседних помещений
|
Класс зоны помещения, смежного со взрывоопасной зоной |
Класс взрывоопасной зоны |
соседнего помещения и отделенного от него стеной (пере- |
|
городкой) с дверью |
B-I |
В-Ιа |
В-Ιа |
B-Iб |
B-Iб |
Невзрыво- и непожароопасная |
В-ΙΙ |
В-ΙΙа |
В-ΙΙа |
Невзрыво- и непожароопасная |
Примечание. Помещения, смежные со взрывоопасной зоной другого помещения и отделенные от него стеной (перегородкой) без проемов или с проемами, оборудованными тамбур-шлюзами, относятся к невзрыво- и непожароопасным.
Следует также учитывать условия, способствующие увеличению вероятности образования взрывоопасных концентраций:
а) размещение во взрывоопасной зоне большого количества аппаратов, содержащих взрывоопасные газы и жидкости; б) применение веществ с относительной плотностью более 0,8 (по отношению к воздуху);
в) применение веществ, вызывающих усиленную коррозию аппаратов и трубопроводов (проницаемость выше 1 мм/год); г) наличие в аппаратах и установке большого количества фланцевых соединений и арматуры;
д) возможность стекания ЛВЖ по горячим стенкам аппаратов. Классификация пожароопасных зон выполняется на основании анализа горючих свойств материалов и особенностей их применения в технологическом процессе.
4.4.3.2. Классификация пожароопасных зон
В таблице 4.6 приведена классификация пожароопасных зон в соответствии с требованиями Правил устройства электроустановок.
Таблица 4.6. Пожароопасные зоны
Класс зоны |
Характеристика зоны |
|
П-I |
Зоны, расположенные в помещениях, в которых обращаются горючие |
|
жидкости с температурой вспышки выше 61 °С. |
||
|
||
|
Зоны, расположенные в помещениях, в которых выделяются горючая |
|
П-II |
пыль или волокна с нижним концентрационным пределом воспламенения |
|
|
более 65 г/м3 (к объему воздуха). |
|
П-IIa |
Зоны, расположенные в помещениях, в которых обращаются твердые |
|
горючие вещества. |
||
|
||
|
Зоны, расположенные вне помещения. В этих зонах обращаются го- |
|
П-III |
рючие жидкости с температурой вспышки выше 61 °С или твердые горючие |
|
|
вещества. |
181
К пожароопасным зонам в части их электрооборудования не относятся:
-зоны в помещениях и зоны наружных установок, в которых твердые, жидкие и газообразные горючие вещества сжигаются в качестве топлива или утилизируются путем сжигания;
-зоны в помещениях и зоны наружных установок в пределах до 5 м по горизонтали и вертикали от аппарата, в котором находится горючее вещество, но технологический процесс ведется с применением открытого огня, раскаленных частей, либо поверхности аппаратов нагреваются до температуры самовоспламенения горючих паров, пылей или волокон.
4.4.3.3. Классификация взрывоопасных смесей (согласно ГОСТ 12.1.011–78*)
Классификация взрывоопасных смесей необходима для получения исходных данных при выборе взрывозащищенного электрооборудования. В основу классификации положено разделение веществ на категории (в зависимости от величины безопасного экспериментального зазора) и на группы (в зависимости от температуры самовоспламенения).
Наряду с классификацией согласно ГОСТ 12.1.011–78* в отечественной промышленности сохранена классификация взрывоопасных смесей по ранее действовавшим Правилам изготовления взрывозащищенного и рудничного электрооборудования (ПИВРЭ) [24] и Правилам изготовления взрывозащищенного электрооборудования (ПИВЭ) [25]. В этих нормативных документах взрывоопасные смеси классифицируются в зависимости от критического зазора и температуры самовоспламенения.
Характеристика категорий взрывоопасных смесей приведена в табл. 4.7, характеристика групп взрывоопасных смесей – в табл. 4.8.
Таблица 4.7. Критерии взрывоопасных смесей
Согласно ГОСТ 12.1.011–78* |
|
|
По ПИВРЭ [24] и ПИВЭ [25] |
||||||||
Категория |
взрывоопасной |
Безопасный |
эксперимен- |
Категория |
взрыво- |
|
Критический |
||||
смеси опасной |
|
тальный максимальный за- |
опасной |
смеси опас- |
|
зазор, мм |
|||||
|
|
|
зор, мм |
|
ной |
|
|
|
|
|
|
|
I |
|
>1,0 |
|
|
1 |
|
|
>1,0 |
||
|
ΙΙА |
|
>0,9 |
|
|
2 |
|
|
>0,65–1,0 |
||
|
ΙΙВ |
|
>0,5−0,9 |
|
|
3 |
|
|
>0,35–0,65 |
||
|
ΙΙ |
|
<0,5 |
|
|
4 |
|
|
<0,35 |
||
Таблица 4.8. Группы взрывоопасных смесей |
|
|
|
|
|
|
|
|
|||
|
|
|
|
|
|
|
|
|
|||
Согласно ГОСТ 12.1.011–78* и ПИВРЭ [24] |
По ПИВЭ [25] |
|
|
|
|
|
|
||||
Группа взрывоопасной |
Температура самовос- |
Группа взрывоопасной |
|
Температура |
самовос- |
|
|||||
смеси |
|
пламенения, °С |
смеси |
|
|
пламенения, °С |
|
||||
|
Т1 |
|
>450 |
А |
|
|
|
>450 |
|
|
|
|
Т2 |
>300–450 |
Б |
|
|
|
>300–450 |
|
|
||
|
Т3 |
>200–300 |
Г |
|
|
|
>175–300 |
|
|
||
|
Т4 |
>135–200 |
Д |
|
|
|
>120–175 |
|
|
||
|
Т5 |
>100–135 |
− |
|
|
|
− |
|
|
||
|
Т61* |
|
>85–100 |
− |
|
|
|
− |
|
|
Примечание: 1*• Только для смесей по классификации ГОСТ 12.L011–78*.
4.4.3.4. Электрооборудование взрывоопасных и пожароопасных установок
При установке электрооборудования во взрывоопасных и пожароопасных установках нужно руководствоваться «Правилами устройства электроустановок» (ПУЭ); «Правилами технической эксплуатации и безопасности обслуживания электроустановок промышленных предприятий», а также «Правилами и нормами техники безопасности и промышленной сани-
182
тарии для проектирования и эксплуатации пожаро- и взрывоопасных производств».
Во взрывоопасных установках необходимо применять взрывозащищенное оборудова-
ние.
Взрывозащищенным называется электрооборудование, обеспечивающее безопасность его применения в условиях взрывоопасных помещений и установок, расположенных на открытых площадках. Оно может быть в следующих шести исполнениях:
1)взрывонепроницаемом, когда оболочки электрооборудования могут выдержать наибольшее давление внутреннего взрыва воспламеняемых газов, паров или пыли, которые могут проникнуть извне или образоваться внутри оболочек без повреждения их и распространения внутреннего воспламенения через зазоры или отверстия в окружающую взрывоопасную среду, на которую оболочки рассчитаны;
2)повышенной надежности против взрыва, когда электрооборудование изготовлено таким образом, что исключается возможность возникновения искр, электрической дуги и опасных температур в тех местах, где они не должны быть при нормальной работе и пусковом режиме, а нормально искрящиеся части должны быть в любом другом взрывозащищенном исполнении: взрывонепроницаемом, продуваемом под избыточным давлением, маслонаполненном, искробезопасном или специальном;
3)маслонаполненном, в котором все нормально искрящие и неискрящие части погружены в масло таким образом, что исключается возможность соприкосновения между этими частями, с одной стороны, и взрывоопасными смесями газов, паров или пыли с воздухом, с другой стороны.
При невозможности погружения всех частей машины, аппарата или прибора в масло отдельные неискрящие части, температура которых не превышает на поверхности допустимых величин, должны быть заключены во взрывонепроницаемую оболочку или оболочку в другом взрывозащищенном исполнении;
4)продуваемом под избыточным давлением, в котором электрооборудование заключается в плотно закрытые оболочки (допускается использование оболочек машин и аппаратов), продуваемые чистым воздухом нормального состава по замкнутому или разомкнутому циклу вентиляции. Внутри оболочек на все время работы установки поддерживается избыточное давление, предотвращающее засасывание в них взрывоопасных смесей из окружающей среды.
В случае невозможности продувания воздухом всех частей электрооборудования нормально неискрящие части их (например, присоединительные зажимы электрических машин) должны быть заключены во взрывонепроницаемую оболочку или оболочку в другом взрывозащищенном исполнении;
5)искробезопасном, в котором искры, возникающие при нормальной работе или могущие возникнуть при любых возможных повреждениях (обрыв, короткое замыкание и т. п.), не могут воспламенить взрывоопасную среду.
При невозможности выполнения всех частей электрооборудования в искробезопасном исполнении отдельные его части могут быть заключены во взрывонепроницаемую оболочку;
6)специальном, которое основано на иных принципах, чем указанные выше исполнения, например, токоведущие части электрооборудования заключены в оболочку с избыточным давлением воздуха или инертного газа без продувки; залиты эпоксидным» смолами; засыпаны кварцевым песком и др.
В таблице 4.9 приведены данные по распределению взрывоопасных смесей по категориям и группам.
В табл. 4.10 приведены исполнения и условные обозначения взрывозащищенного электрооборудования, а также среды, для которых рекомендуется его применение.
Расшифруем некоторые обозначения электродвигателей:
1)B1A: В – взрывонепроницаемое исполнение; 1 – категории; А – группа взрывоопасной смеси (табл. 4.8);
2)МНБ: М – маслонаполненное исполнение; Н – пыленепроницаемое присоедини-
183
тельное устройство; Б – группа взрывоопасной смеси (табл. 4.8); 3) Н0Г: Н – исполнение повышенной надежности против взрыва; 0 –указывает на от-
сутствие другие взрывозащищенных элементов; Г – группа взрывоопасной смеси (табл. 4.8). Таблица 4.9. Распределение взрывоопасных смесей по категориям и группам
Категория |
Группа взрывоопасной смеси |
|
|
|
|
|
|
|
|
|||||
взрывоопас- |
|
|
|
|
|
|
|
|
|
|
|
|
|
|
А |
|
|
|
Б |
|
|
|
Г |
|
|
|
|
Д |
|
ной смеси |
|
|
|
|
|
|
|
|
|
|
||||
|
|
|
|
|
|
|
|
|
|
|
|
|
|
|
1 |
Аммиак, метан, ди- |
Уксусный ангидрид, |
Уайт-спирит, циклогек- |
|
||||||||||
|
хлорэтан, уксусная |
изопрен, бутиловый |
сан, этилдихлортиофос- |
|
||||||||||
|
кислота, сольвент |
спирт (третичный), изо- |
фат, скипидар. |
|
|
|
||||||||
|
каменноугольный, |
бутиловый спирт, ви- |
Растворители: |
|
№ |
651, |
|
|||||||
|
изопропиловый |
|
нилацетат, амилацетат, |
полиэфир ТГМ-3 |
|
|
||||||||
|
спирт, циклогекса- |
метилметакрилат |
|
|
|
|
|
|
|
|||||
|
нон, α-метилстирол, |
Растворители: |
|
|
|
|
|
|
|
|||||
|
метилхлорформиат, |
№ 646, № 647, № 648, |
|
|
|
|
|
|
||||||
|
хлористый метил |
|
№649, РКБ-1, РКБ-2РТУ |
|
|
|
|
|
|
|||||
|
Растворители: |
|
М(2), РДВ, РС-2, Р-40 |
|
|
|
|
|
|
|||||
|
Р-5, РС-1, Р-4, РЭ-1, |
|
|
|
|
|
|
|
|
|
|
|||
|
метилфенилдихлор- |
|
|
|
|
|
|
|
|
|
|
|||
|
силан |
|
|
|
|
|
|
|
|
|
|
|
|
|
2 |
Этан, пропан, аце- |
Бутан, пентан, пропи- |
Гексан, топливо Т-1, |
|
||||||||||
|
тон, хлористый этил, |
лен, нитроциклогексан, |
ацетальдегид, |
|
этилцел- |
|
||||||||
|
диэтиламин, триэти- |
метиловый спирт, эти- |
лозольв, «гептил», «са- |
|
||||||||||
|
ламин, бензол, толу- |
ловый спирт, бутиловый |
мив», |
этилмеркаптан, |
|
|||||||||
|
ол, ксилол, этрилбен- |
спирт |
(нормальный), |
бутилметакрилат, |
бен- |
|
||||||||
|
зол, хлорбензол, изо- |
бутилацетат, |
дивинил, |
зин А-66, бензин Б-70, |
|
|||||||||
|
пропилбензол, |
сти- |
диоксан, |
изопентан, |
триметиламин, |
гидри- |
|
|||||||
|
рол, |
диизопропило- |
нитрилакриловая кисло- |
рованный керосин с |
|
|||||||||
|
вый эфир, доменный |
та, |
диметилдихлорси- |
трибутилфосфатом, тет- |
|
|||||||||
|
газ, бензин Б-100, |
лан, фурфурол, мети- |
рагидрофуран, |
бензин |
|
|||||||||
|
нафталин, |
пиридин, |
лакрилат, |
метиламин, |
«калоша», бензин А-72, |
|
||||||||
|
хлористый |
винил, |
диметиламин, метилви- |
бензин А-76 |
|
|
|
|
||||||
|
циклопентадиен |
|
нилдихлорсилан, |
этил- |
|
|
|
|
|
|
||||
|
|
|
|
|
ацетат |
|
|
|
|
|
|
|
|
|
3 |
Этилен, светильный |
Окись |
этилена, |
окись |
Серный эфир, этилди- |
|
||||||||
|
газ, |
коксовый |
газ |
пропилена |
|
|
хлорсилан; |
винилтри- |
|
|||||
|
(метана 40% и водо- |
|
|
|
|
хлорсилан |
|
|
|
|
||||
|
рода 60%) |
|
|
|
|
|
|
|
|
|
|
|
|
|
4 |
Водород, водяной газ |
Метилдихлорсилан |
Сероводород, |
трихлор- |
Сероуг- |
|||||||||
|
|
|
|
|
|
|
|
|
силан |
|
|
|
|
лерод |
Таблица 4.10. Исполнения и условные обозначения взрывозащищенного электрооборудования
№ п. |
Электрооборудование |
Взрывоопасная |
Обозначение |
|
п. |
|
среда |
|
|
1 |
Взрывонепроницаемое |
Метан |
В1А |
|
2 |
Взрывонепроницаемое |
Пентан |
В2Б |
|
|
Маслонаполненное: |
Сероуглерод |
М0Д |
|
|
а) со взрывонепроницаемыми элементами; |
Этилен |
М3А |
|
3 |
б) с элементами повышенной надежности против |
Пентан |
МНБ |
|
взрыва; |
||||
|
|
|
||
|
в) с элементами взрывонепроницаемыми и специаль- |
Эфир |
М3ГС |
|
|
ными |
|
|
184
Продолжение табл. 4.10
№ п. |
Электрооборудование |
Взрывоопасная |
Обозначение |
||||||
п. |
|
среда |
|
|
|
|
|
|
|
|
Повышенной надежности против взрыва: |
|
|
|
|
|
|
|
|
|
а) без взрывонепроницаемых элементов; |
Эфир |
Н0Г |
|
|
|
|
||
|
б) со взрывонепроницаемыми элементами; |
Толуол |
Н2А |
|
|
|
|
||
4 |
в) с продуваемыми под избыточным давлением эле- |
Сероуглерод |
НПД |
|
|
|
|
||
ментами; |
|
|
|
|
|||||
|
г) с маслонаполненными элементами; |
Сероуглерод |
НМД |
|
|
|
|
||
|
д) с искробезопасными элементами |
Бензол |
Н0А |
И |
|
||||
|
бензол |
||||||||
|
|
|
|
|
|
||||
5 |
Продуваемое под избыточным давлением: |
Водород |
П0А |
|
|
|
|
||
а) со взрывонепроницаемыми элементами; |
Гексан |
П2Г |
|
|
|
|
|||
|
б) без взрывонепроницаемых элементов |
Водород |
П0А |
|
|
|
|
||
|
Искробезопасное: |
|
ИО |
|
|
|
|
||
|
а) со взрывонепроницаемыми элементами; |
Эфир |
|
И3Г |
|
|
|
|
|
6 |
|
эфир |
|
|
|
|
|||
|
|
|
|
|
|
|
|||
|
б) без взрывонепроницаемых элементов |
Водород |
|
И0 |
|
||||
|
|
водород |
|||||||
|
|
|
|
||||||
|
Специальное |
Сероводород |
С0Г |
|
|
|
|
||
7 |
То же, с искробезопасными элементами |
Водород |
С0А |
|
|
И |
|
||
|
|
водород |
|||||||
|
|
|
|
|
|
4.4.3.5. Классификация и маркировка взрывозащищенного электрооборудования (согласно ГОСТ 12.2.020–76*)
Классификация. Взрывозащищенное электрооборудование классифицируется согласно ГОСТ 12.2.020–76* в зависимости от уровня и вида взрывозащиты, области применения и температурного класса. Электрооборудование старых разработок классифицируется по ПИВРЭ [24] и ПИВЭ [25].
ГОСТ 12.2.020–76* устанавливает следующие уровни взрывозащиты: электрооборудование повышенной надежности против взрыва; взрывобезопасное электрооборудование; особовзрывобезопасное электрооборудование.
По классификации ПИВРЭ [24] вместо уровня «особовзрывобезопасное электрооборудование» был принят уровень «электрооборудование, взрывобезопасное при любых количествах повреждении», а в соответствии с ПИВЭ [25] электрооборудование по уровню взрывозащиты вообще не классифицировалось.
При наличии в одном электрооборудовании элементов с различными уровнями взрывозащиты общий уровень взрывозащиты должен устанавливаться по элементу, имеющему наиболее низкий уровень.
Согласно ГОСТ 12.2.020–76*, взрывозащищенное электрооборудование, предназначенное для внутренней и наружной установки в пределах взрывоопасных зон, может иметь следующие виды взрывозащиты: взрывонепроницаемую оболочку; искро-безопасную электрическую цепь; защиту вида «е»; заполнение или продувку оболочками под избыточным давлением; масляное заполнение оболочки; кварцевое заполнение оболочки; специальный вид взрывозащиты.
Аналогичный принцип классификации взрывозащищенного электрооборудования по видам взрывозащиты принят в ПИВРЭ [24] и ПИВЭ [25].
В зависимости от области применения взрывозащищенное электрооборудование разделено на две группы:
I – рудничное взрывозащищенное электрооборудование;
185
II – взрывозащищенное электрооборудование для внутренней и наружной установки. Ниже рассматривается только электрооборудование группы II как применяемое для ус-
тановки в пределах взрывоопасных зон химических и нефтехимических производств. Электрооборудование с видом взрывозащиты «взрывонепроницаемая оболочка» или
«искробезопасная электрическая цепь» в зависимости от категории применяемой взрыво-
опасной смеси подразделяется на подгруппы ΙΙА, ΙΙВ, ΙΙС.
Классификация предусматривает также разделение взрывозащищенного электрооборудования в зависимости от степени нагрева оболочки на температурные классы (табл. 11.11).
Таблица 11.11. Температурные классы взрывозащитного электрооборудования
|
|
|
|
|
|
|
Группа |
взрывоопас- |
|
Обозначение |
температурного класса |
Предельная |
температура |
нагрева |
ной смеси, в которой |
||||
электрооборудование |
|||||||||
электрооборудования |
|
оболочки, °С |
|
|
|||||
|
|
|
является |
электроза- |
|||||
|
|
|
|
|
|
|
|||
|
|
|
|
|
|
|
щищенным |
||
ГОСТ |
|
по ПИВ- |
по ПИВЭ |
ГОСТ |
по ПИВ- |
по ПИ- |
|
|
|
12.2.020−76* |
|
РЭ [24] |
[25] |
12.2.020−76* |
РЭ [24] |
ВЭ [25] |
|
|
|
Т1 |
|
Т1 |
− |
450 |
450 |
− |
|
|
|
Т2 |
|
Т2 |
− |
300 |
300 |
− |
|
|
|
Т3 |
|
Т3 |
А |
200 |
200 |
200 |
|
|
|
Т4 |
|
Т4 |
Б |
135 |
135 |
155 |
|
|
|
Т5 |
|
Т5 |
Г |
100 |
100 |
100 |
|
|
|
Т6 |
|
|
Д |
85 |
− |
80 |
|
|
Маркировка. Маркировка взрывозащищенного электрооборудования кроме обозначений согласно ГОСТ 18620–86 Е содержит маркировку по взрывозащите в соответствии с ГОСТ 12.2.020–76*. Маркировка по взрывозащите содержит знаки в следующей последовательности: знак уровня взрывозащиты; знак Ех, указывающий, что электрооборудование соответствует ГОСТ 12.2.020–76* и стандартам на виды взрывозащиты; знак вида взрывозащиты; знак группы или подгруппы электрооборудования; знак температурного класса.
Знаки уровня и вида взрывозащиты приведены в табл. 4.12. Таблица 4.12. Знаки уровня и виды взрывозащиты электрооборудования
Наименование знака |
|
Знак маркировки |
|
|
|
|
ГОСТ 12.2.020−76* |
ПИВРЭ |
ПИВЭ |
||
|
|
||||
|
|
Уровень взрывозащиты |
|
||
Повышенная надежность |
2 |
Н |
− |
||
против взрыва |
|
||||
|
|
|
|
||
Взрывобезопасное |
элек- |
1 |
В |
− |
|
трооборудование |
|
||||
|
|
|
|
||
Особовзрывобезопасное |
0 |
− |
− |
||
электрооборудование |
|||||
|
|
|
|||
Взрывобезопасное |
элек- |
|
|
|
|
трооборудование при лю- |
− |
О |
− |
||
бом количестве повреж- |
|||||
|
|
|
|||
дений |
|
|
|
|
|
|
|
Вид взрывозащиты |
|
||
Взрывонепроницаемая |
d |
В |
В |
||
оболочка |
|
||||
|
|
|
|
186
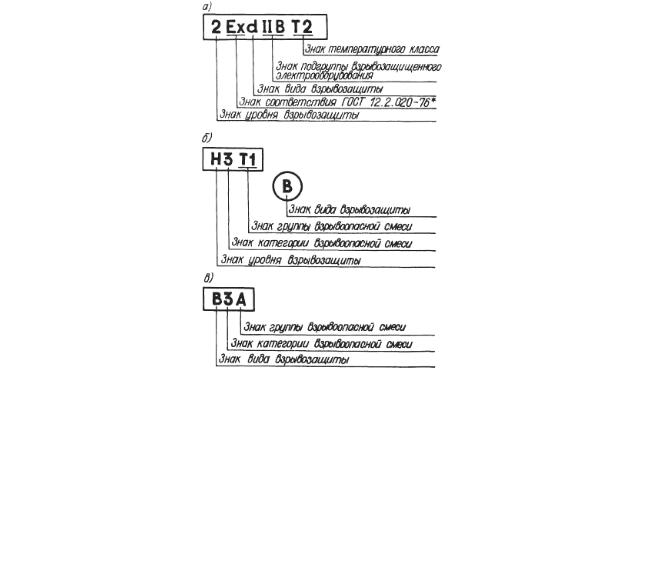
Продолжение табл. 4.12
Наименование знака |
Знак маркировки |
|
|
|||
ГОСТ 12.2.020−76* |
ПИВРЭ |
ПИВЭ |
||||
|
|
|
||||
Искробезопасная |
элек- |
i |
И |
И |
||
трическая цепь |
|
|||||
|
|
|
|
|||
Защита вида «е» |
|
e |
− |
− |
||
Повышенная |
надежность |
− |
Н |
Н |
||
против взрыва |
|
|
||||
|
|
|
|
|
||
Масляное |
заполнение |
o |
М |
М |
||
оболочки |
|
|
||||
|
|
|
|
|
||
Заполнение или продувка |
|
|
|
|||
оболочки под |
избыточ- |
p |
П |
П |
||
ным давлением |
|
|
|
|
||
Кварцевое |
заполнение |
q |
К |
− |
||
оболочки |
|
|
||||
|
|
|
|
|
||
Специальный вид взрыво- |
s |
С |
С |
|||
защиты |
|
|
||||
|
|
|
|
|
Маркировка по взрывозащите наносится на электрооборудование в виде цельного, не разделенного на части знака, помещенного в прямоугольнике (рис. 4.1, а). В конструкторской документации исполнение электрооборудования по взрывозащите допускается указывать без прямоугольника, например 2ExdIIBT3.
Рис. 4.1. Примеры маркировки взрывозащищенного электр оборудования, предназначенного для экс-
плуатации во взрывоопасной зоне класса В-Ιа, где рабочей средой является этилен: а – маркировка согласно ГОСТ 12.2.020–76; б – маркировка по ПИВРЭ [24]; в –маркировка по ПИВЭ [25]
Если электрооборудование разработано для эксплуатации в условиях взрывоопасных зон, содержащих определенную взрывоопасную смесь, то вместо знака температурного класса допускается указывать предельную температуру взрывозащищенного электрооборудова-
ния для этой смеси, например lExdΙΙA630 °C.
Если значение предельной температуры для конкретной смеси менее 450 °С, то допускается дополнительно в скобках указывать и температурный класс этого электрооборудования, например 2ExdIIB320 °C (T2). В маркировке взрывозащиты могут помещаться дополни-
187
тельные знаки или надписи, если это предусмотрено в стандартах на конкретные виды взрывозащиты.
Маркировка наносится на оболочку электрооборудования рельефными знаками или помещается на табличке, прикрепленной к оболочке таким способом, чтобы была обеспечена сохранность ее в течение всего срока службы электрооборудования.
Маркировка взрывозащищенного электрооборудования по ПИВРЭ [24] выполняется, в отличие от маркировки согласно ГОСТ 12.2.020–76*, в виде разделенного на части знака, содержащего: в прямоугольнике – знак уровня взрывозащиты, знаки категории и группы взрывоопасной смеси; в кружке под прямоугольником – знак вида взрывозащиты (рис. 4.1, б).
Маркировка взрывозащищенного электрооборудования по ПИВЭ [25] выполнялась аналогично маркировке по ПИВРЭ [24], но без обозначения уровня взрывозащиты (рис. 4.1,
в).
4.4.3.6. Требования к электрооборудованию для взрывоопасных и пожароопасных зон
Электрооборудование, предназначенное для установки в пределах взрыво- и пожароопасных зон, должно соответствовать требованиям ПУЭ [27].
Основанием для выбора электрооборудования, комплектующего аппараты химических и нефтехимических производств, являются сведения, содержащиеся в техническом задании на разработку или в исходных требованиях заказчика, прилагаемых, согласно ГОСТ 15.001– 73*, к заявке на разработку изделия.
Уровень взрывозащиты электрооборудования рекомендуется выбирать следующим образом: определяют категорию и группу взрывоопасной смеси, характеризующие наибольшую опасность данного производства; анализируют характер взрывоопасных зон в помещениях и наружных установках, в которых будет размещено электрооборудование, и при необходимости намечают защитные и профилактические мероприятия для снижения класса взрывоопасной зоны; определяют температурный режим окружающей среды; анализируют механическое и химическое воздействие на оборудование окружающей среды; учитывают возможность применения в процессе производства новых взрывоопасных веществ. Выбор уровня защиты электрооборудования для работы во взрыво-и пожароопасных зонах должен проводиться по табл. 4.13 и 4.14. Допускается замена электрооборудования, указанного в таблицах, электрооборудованием более высокого уровня взрывозащиты и более высокой степени защиты оболочки от воздействия внешней среды. Например, вместо электрооборудования уровня «повышенной надежности против взрыва» может быть использовано электрооборудование уровня «взрывобезопасное».
В зонах, взрывоопасность которых определяется горючими жидкостями с температурой вспышки выше 61 °С, может применяться любое взрывозащищенное электрооборудование с температурой нагрева поверхности ниже температуры самовоспламенения данного вещества.
Во взрывоопасных зонах классов В-ΙΙ и В-ΙΙа следует применять электрооборудование, специально предназначенное для работы в среде горючих пылей и волокон. При отсутствии
такого электрооборудования допускается применять в зонах класса В-ΙΙ взрывозащищенное электрооборудование, предназначенное для работы в средах со взрывоопасными смесями
паров и газов с воздухом, а в зонах класса В-Па − электрооборудование общего назначения (без взрывозащиты), но имеющее степень защиты оболочки не менее IP54. Температура поверхностей электрооборудования, на которые могут осесть горючие пыли или волокна, должна быть на 50 °С ниже температуры тления для тлеющих пылей или составлять не более двух третей от температуры самовоспламенения для нетлеющих пылей.
Взрывозащищенное электрооборудование, работающее в условиях химически активных и влажных сред, должно иметь защиту от воздействия этих сред.
188
Таблица 4.13. Допустимые уровни взрывозащиты электрооборудования для работы во взрывоопасных зонах [27]
Вид |
электрооборудова- |
Допустимый уровень взрывозащиты для классов взрывоопасных зон |
|
|
|
|
|||||||||||||
ния |
|
|
|
|
|
В − Ι |
В − Ιа |
В − Ιб |
|
|
В − Ιг |
В − ΙΙ |
|
В − ΙΙа |
|
|
|||
|
|
|
|
|
|
|
|
|
Без |
|
средств |
|
|
|
Без |
средств |
|||
|
|
|
|
|
|
|
|
|
взрывозащиты. |
|
|
|
|||||||
|
|
|
|
|
|
|
|
|
|
|
|
взрыво защиты. |
|||||||
|
|
|
|
|
|
|
|
|
Оболочки |
со |
|
|
|
||||||
|
|
|
|
|
|
|
|
|
Повы- |
|
|
Оболочка |
|
со |
|||||
|
|
|
|
|
|
|
|
|
степенью защи- |
|
|
|
|||||||
|
|
|
|
|
|
|
|
|
|
|
степенью защи- |
||||||||
|
|
|
|
|
|
|
|
|
ты |
не |
менее |
шен- |
|
|
|||||
|
|
|
|
|
|
|
|
|
|
|
ты |
IP54. |
|
Ис- |
|||||
|
|
|
|
|
|
|
|
|
IP44. |
Искрящие |
ной |
Взры- |
|
|
|||||
Электрические машины |
|
Повышенной |
|
крящие |
части |
||||||||||||||
Взрывобе- |
части |
машины |
надеж- |
|
|||||||||||||||
стационарные и |
пере- |
надежности |
(например, кон- |
ности |
вобе- |
|
машины |
|
(на- |
||||||||||
движные |
|
|
|
|
зопасное |
против взрыва |
тактные кольца) |
против |
зопас- |
|
пример, |
|
кон- |
||||||
|
|
|
|
|
|
|
|
|
должны |
|
быть |
взрыва |
ное |
|
тактные кольца) |
||||
|
|
|
|
|
|
|
|
|
заключены |
в |
|
|
|
должны |
|
быть |
|||
|
|
|
|
|
|
|
|
|
|
|
|
заключены |
в |
||||||
|
|
|
|
|
|
|
|
|
оболочку также |
|
|
|
|||||||
|
|
|
|
|
|
|
|
|
|
|
|
оболочку также |
|||||||
|
|
|
|
|
|
|
|
|
со |
степенью |
|
|
|
||||||
|
|
|
|
|
|
|
|
|
|
|
|
со |
степенью |
||||||
|
|
|
|
|
|
|
|
|
защиты |
не |
ме- |
|
|
|
|||||
|
|
|
|
|
|
|
|
|
|
|
|
защиты IP54 |
|||||||
|
|
|
|
|
|
|
|
|
нее IP44 |
|
|
|
|
||||||
|
|
|
|
|
|
|
|
|
|
|
|
|
|
|
|
|
|||
|
|
|
|
|
|
|
|
|
|
|
|
|
|
Взры- |
|
|
|
|
|
|
|
|
искрящие |
|
|
|
Без |
|
средств |
|
вобе- |
|
Без |
средств |
|||||
|
|
|
Взрывобе- |
|
|
|
|
зопас- |
|
||||||||||
|
|
|
или |
подвер- |
|
|
взрывозащиты. |
|
|
взрывозащиты. |
|||||||||
|
|
|
зопасное, |
|
|
|
ное, |
|
|||||||||||
|
|
|
женные |
на- |
особо- |
То же |
Оболочка |
со |
То же |
особо- |
|
Оболочка |
|
со |
|||||
|
|
|
греву |
|
до |
взрывобе- |
|
|
степенью защи- |
|
взры- |
|
степенью защи- |
||||||
|
|
|
температуры |
|
|
ты |
не |
менее |
|
|
ты |
не |
менее |
||||||
|
|
|
зопасное |
|
|
|
вобе- |
|
|||||||||||
Элек- |
|
80 °С |
|
|
|
|
|
IP44 |
|
|
|
|
зопас- |
|
IP54 |
|
|
|
|
|
|
|
|
|
|
|
|
|
|
|
|
ное |
|
|
|
|
|
||
триче- |
|
|
|
|
|
|
|
|
|
|
|
|
|
|
|
|
|
||
|
|
|
|
|
|
|
|
|
|
|
Без |
|
|
|
|
|
|
||
ские |
|
|
|
|
|
|
|
|
|
|
|
|
|
|
|
|
|
||
|
|
|
|
|
|
|
|
|
|
|
средст |
|
|
|
|
|
|
||
аппара- |
|
|
|
|
|
|
|
|
|
|
|
|
|
|
|
|
|
||
|
|
|
|
|
|
|
|
|
|
|
в |
|
|
|
|
|
|
||
ты |
и |
|
|
|
|
|
|
|
|
|
|
|
Повы- |
|
|
|
|
|
|
|
|
|
|
|
|
|
|
|
|
|
взры- |
|
|
|
|
|
|||
прибо- |
|
|
|
|
|
|
|
|
|
|
|
|
|
|
|
|
|||
|
|
|
|
|
|
|
|
|
|
|
воза- |
шен- |
|
|
|
|
|
||
ры |
ста- |
|
не искрящие |
|
Без |
средств |
|
|
|
|
|
|
|
|
|
||||
|
|
|
|
|
|
щиты. |
ной |
|
|
|
|
|
|||||||
цио- |
|
и не подвер- |
|
взрывозащи- |
|
|
|
|
|
|
|
|
|
||||||
|
|
|
|
|
|
Обо- |
надеж- |
|
|
|
|
|
|||||||
нарные: |
женные на- |
|
ты. |
Оболочка |
|
|
|
|
|
|
|
|
|
||||||
То же |
То же |
|
|
лочка |
ности |
|
То же |
|
|
||||||||||
|
|
|
греву |
|
до |
|
со |
степенью |
|
|
|
|
со |
против |
|
|
|
|
|
|
|
|
температуры |
|
защиты не ме- |
|
|
|
|
|
|
|
|
|
|||||
|
|
|
|
|
|
|
|
степе- |
взрыва |
|
|
|
|
|
|||||
|
|
|
выше80 °С |
|
нее IP54 |
|
|
|
|
|
|
|
|
|
|||||
|
|
|
|
|
|
|
|
нью |
|
|
|
|
|
|
|||||
|
|
|
|
|
|
|
|
|
|
|
|
|
|
|
|
|
|
|
|
|
|
|
|
|
|
|
|
|
|
|
|
|
защи- |
|
|
|
|
|
|
|
|
|
|
|
|
|
|
|
|
|
|
|
ты не |
|
|
|
|
|
|
|
|
|
|
|
|
|
|
|
|
|
|
|
менее |
|
|
|
|
|
|
|
|
|
|
|
|
|
|
|
|
|
|
|
IP54 |
|
|
|
|
|
|
|
|
|
|
|
|
|
|
|
|
|
|
|
Повы- |
|
|
|
|
|
|
Электрические |
аппара- |
|
|
|
|
|
|
|
шен- |
|
|
|
|
|
|
||||
|
Взрывобезо- |
|
|
|
|
ной |
|
|
|
|
|
|
|||||||
ты и приборы пере- |
|
Повышен |
ной |
надеж- |
|
|
|
|
|
|
|||||||||
|
пасное, особо- |
То же |
|
То же |
|
|
|||||||||||||
движные |
|
или |
являю- |
То же |
надежности |
ности |
|
|
|
||||||||||
щиеся |
частью |
|
пере- |
|
взрывобезо- |
против взрыва |
против |
|
|
|
|
|
|
||||||
|
|
пасное |
|
|
|
|
|
|
|||||||||||
движных установок |
|
|
|
|
|
взрыва |
|
|
|
|
|
|
|||||||
|
|
|
|
|
|
|
|
|
|
|
|
|
|||||||
|
|
|
|
|
|
|
|
|
|
|
|
|
|
|
|
|
|
|
|
Во взрывоопасных зонах могут применяться электродвигатели с классом напряжения до 10 кВ при условии, что уровень их взрывозащиты или степень защиты оболочки согласно
ГОСТ 17494−72* соответствует значениям, приведенным в табл. 4.13, или является более высоким.
189
Таблица 4.14. Допустимая степень защиты оболочек электрооборудования в зависимости от класса пожарной опасности
|
Допустимая степень защиты оболочки для классов зон по- |
|||
Вид электрооборудования |
жарной опасности |
|
|
|
|
П−Ι |
П−ΙΙ |
П−ΙΙа |
П−ΙΙΙ |
Электрические машины стацио- |
|
|
|
|
нарные: |
|
|
|
|
искрящие или с искрящими час- |
IP44 |
IP54 |
IP44 |
IP44 |
тями по условиям работы; |
|
|
|
|
не искрящие и без искрящих час- |
IP44 |
IP44 |
IP44 |
IP44 |
тей по условиям работы. |
|
|
|
|
Электрические машины с частями, |
|
|
|
|
искрящими и не искрящими по |
|
|
|
|
условиям работы, установленные |
IP44 |
IP54 |
IP44 |
IP44 |
на передвижных механизмах и ус- |
|
|
|
|
тановках |
|
|
|
|
Электрические аппараты и прибо- |
|
|
|
|
ры, установленные стационарно |
|
|
|
|
или на передвижных механизмах |
|
|
|
|
и установках: |
|
|
|
|
искрящие по условиям работы; |
IP44 |
IP54 |
IP44 |
IP44 |
не искрящие по условиям работы. |
IP44 |
IP44 |
IP44 |
IP44 |
Электродвигатели с защитой вида «е» следует устанавливать только на аппаратах, работающих без перегрузок, частых остановок и реверсов. Такие электродвигатели должны иметь защиту от перегрузок, срабатывающую в течение времени, необходимого для нагрева электродвигателя пусковым током до температуры не превышающей предельную температуру для данной взрывоопасной смеси по табл. 4.8.
Электродвигатели с видом взрывозащиты «взрывонепроницаемая оболочка», предназначенные для установки в пределах взрывоопасной зоны со средой категории ПС, должны быть расположены так, чтобы взрывонепроницаемые фланцевые зазоры не примыкали вплотную к какой-либо поверхности, а находились от нее на расстоянии не менее 50 мм.
Электродвигатели с видом взрывозащиты «заполнение или продувка оболочки под избыточным давлением» должны применяться при выполнении следующих условий:
а) осуществлены все мероприятия, предусмотренные ГОСТ 22782.4–78* и инструкцией по монтажу и эксплуатации данного электродвигателя;
б) выполнены системы вентиляции и контроля давления и температуры защитного газа; в) исключена возможность образования непродуваемых зон в фундаментных ямах и га-
зопроводах защитного газа; г) исключена возможность прокладки трубопроводов защитного газа в пределах и под
полом помещений со взрывоопасными зонами; д) предусмотрена установка устройств для защитного газа вне пределов взрывоопасных
зон.
Электроаппараты с видом взрывозащиты «масляное заполнение оболочки» допускается применять в том случае, если они не подвержены поломкам и вибрации, а также если в них предусмотрены устройства для предотвращения выплескивания масла.
4.4.3.7. Согласование технической документации на изготовление взрывозащищенного электрооборудования
Изготовление взрывозащищенного электрооборудования разрешается при наличии: для опытных образцов – письменного положительного заключения о взрывозащищенности электрооборудования; для серийного производства – свидетельства о взрывозащищенности электрооборудования, утвержденного Госэнергонадзором РФ.
190
Право на выдачу заключений и свидетельств о взрывозащищенности электрооборудования для внутренней и наружной установки предоставлено следующим организациям: Всероссийскому научно-исследовательскому институту взрывозащитного и рудничного электрооборудования (ВНИИВЭ); Восточному научно-исследовательскому горнорудному институту (ВостНИГРИ).
Письменные заключения и свидетельства оформляются испытательной организацией после согласования технической документации на взрывозащищенное электрооборудование и положительных результатов испытаний этого оборудования.
Представляемая на согласование техническая документация должна содержать: технические условия или отраслевые стандарты, по которым изготовлено электрооборудование; инструкцию по монтажу и эксплуатации; сборочные чертежи каждого электротехнического устройства со спецификациями; принципиальные схемы и схемы соединения.
В перечисленных документах должны быть указаны параметры взрывозащиты и конструкция сборочных единиц и деталей, обеспечивающих взрывозащиту, маркировка взрывозащиты и предупредительные надписи, электроизоляционные материалы, длина пути утечки и электрические зазоры (где это требуется).
Вся документация представляется в двух экземплярах и должна быть переплетена. Если в комплект взрывозащищенного электрооборудования входят устройства, уста-
навливаемые вне взрывоопасных зон, но влияющие на работу взрывозащищенного электрооборудования (например, блоки питания искробезопасных датчиков), то в комплект представляемой документации следует включать эти устройства.
Образец электрооборудования, представляемый для проведения испытаний, должен быть снабжен документацией в объеме, указанном в табл. 4.15.
Свидетельства о взрывозащищенности электрооборудования выдаются на срок действия 5 лет.
По документации, представляемой без образцов электрооборудования, а также по отдельным документам испытательная организация дает только замечания.
Порядок согласования технической документации, проведения испытаний и выдачи заключений приведен в ГОСТ 12.2.021–76.
4.5. Номенклатура взрывозащищенного электрооборудования
Взрывозащищенные электродвигатели. В качестве приводов аппаратов, предназначенных для работы в условиях взрывоопасных зон, применяют взрывозащищенные электродвигатели единой серии В. Номенклатура выпускаемых отечественной промышленностью взрывозащищенных электродвигателей единой серии В приведена на рис. 4.2. Ранее выпускались электродвигатели серии ВАО, которые в настоящее время находятся в эксплуатации на многих видах химического оборудования. При замене электродвигателей серии ВАО на электродвигатели единой серии В необходимо учитывать фактическую мощность, потребляемую оборудованием, и выбирать электродвигатели серии В по установленной стандартной мощности с минимальным запасом. Это позволит улучшить коэффициент полезного
действия и коэффициент мощности (cos ϕ) в эксплуатации, а также снизить массу, габаритные размеры и маховые моменты оборудования.
191
Таблица 4.15. Документация, представляемая в испытательную организацию с образцом электрооборудования
|
|
|
|
|
|
Вид взрывозащиты электрооборудования |
|
|
|||||
Документ |
|
|
|
Взрывонепроницаемая оболочка |
Искробезопасная электрическая цепь |
Защита вида «е» |
Масляное заполнение оболочки |
Заполнение и продувка оболочки под избыточным давлением |
Кварцевое заполнение оболочки |
Специальная защита |
|||
|
|
|
|
|
|
||||||||
|
|
|
|
|
|
|
|
|
|
||||
Справка |
об |
испыта- |
|
|
|
|
|
|
|
||||
нии электрического |
|
|
|
|
|
|
|
||||||
устройства |
и |
соот- |
+ |
+ |
+ |
+ |
+ |
+ |
+ |
||||
ветствии |
его |
техни- |
|||||||||||
|
|
|
|
|
|
|
|||||||
ческой |
|
документа- |
|
|
|
|
|
|
|
||||
ции |
|
|
|
|
|
|
|
|
|
|
|
|
|
Протоколы |
гидрав- |
+ |
|
|
+ |
|
+ |
|
|||||
лических испытаний |
− |
− |
− |
− |
|||||||||
оболочек |
|
|
|
|
|
|
|
|
|
|
|
||
Гидравлические |
|
|
|
|
|
|
|
|
|||||
схемы |
с |
указанием |
|
|
|
|
|
|
|
||||
способов и мест кре- |
◊ |
− |
− |
− |
− |
− |
− |
||||||
пления |
деталей |
и |
|
|
|
|
|
|
|
||||
оболочек |
|
|
|
|
|
|
|
|
|
|
|
||
Протоколы |
испыта- |
|
|
|
|
+ |
|
+ |
|||||
ний |
оболочек |
на |
◊ |
− |
− |
− |
− |
||||||
прочность |
|
|
|
|
|
|
|
|
|
|
|||
Протоколы тепловых |
◊ |
◊ |
+ |
◊ |
◊ |
◊ |
◊ |
||||||
испытаний |
|
|
|
||||||||||
|
|
|
|
|
|
|
|
|
|
||||
Расчет схемы венти- |
− |
− |
− |
− |
◊ |
− |
− |
||||||
ляции |
|
|
|
|
|
||||||||
|
|
|
|
|
|
|
|
|
|
|
|
||
Сертификат |
на |
за- |
|
|
|
|
|
+ |
+ |
||||
полнитель |
(кварце- |
− |
− |
− |
− |
− |
|||||||
вый песок и т. д.) |
|
|
|
|
|
|
|
|
Примечание. Условные обозначения: + – документ обязателен; – – документ не представляется; ◊ – документ представляется по требованию испытательной организации.
Мотор-редукторы с взрыво-защищенными электродвигателями. Для аппаратов, ра-
ботающих в интервале частот вращения 0,066…5,25 с−1 (4…315 об/мин), в качестве привода следует применять мотор-редукторы типа МР [15, 16].
Мотор-редуктор представляет собой блок асинхронного обдуваемого электродвигателя и планетарной передачи, смонтированной в чугунном корпусе.
Для установки в пределах взрывоопасных зон мотор-редукторы комплектуются взрывозащищенными электродвигателями серии В в исполнении по взрывозащите ВЗТ4. Такие мотор-редукторы могут работать во взрывоопасных зонах с содержанием непроводящей пыли до 10 мг/л и относительной влажностью до 95 % при температуре до 35 °С.
В зависимости от числа ступеней планетарной передачи мотор-редукторы подразделяются на одноступенчатые МР-1, двухступенчатые МР-2 и трехступенчатые МР-3. Коэффициент полезного действия планетарной передачи следует принимать 98 % для моторредукторов МР-1, 96 % для МР-2 и 93 % для МР-3.
192
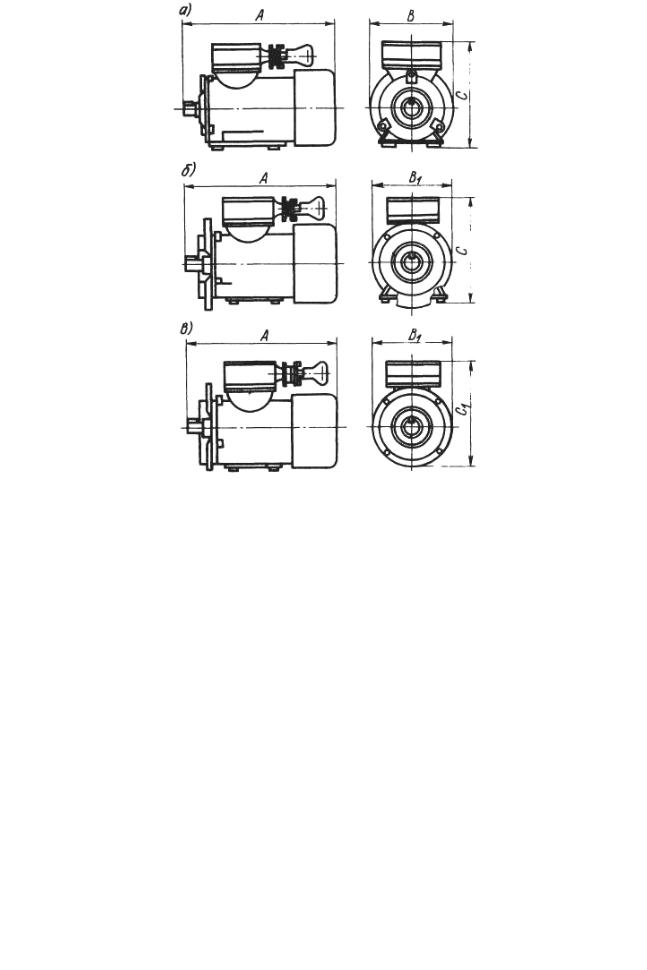
Рис. 4.2. Взрывозащищенные электродвигатели: а – исполнение по монтажу Ml00; б – исполнение по монтажу М200; в – исполнение по монтажу М300
В зависимости от положения в пространстве и способа соединения с аппаратами моторредукторы выпускаются в следующих исполнениях:
Ф-1В – вертикальные с цилиндрическим концом выходного вала, направленным вниз; Ф-2В – горизонтальные с цилиндрическим концом выходного вала; Ф-1П – вертикальные с концом выходного вала, направленным вниз, выполненным в
виде фланцевой полумуфты со встроенным зубчатым компенсатором.
Для типов МР-2 и МР-3 в исполнениях Ф-1В и Ф -2В допускается установка ведомой шестерни или звездочки непосредственно на валу мотор-редуктора. При этом радиальные осевые нагрузки, приведенные к середине посадочной поверхности вала, не должны превышать значений с учетом коэффициента безопасности (Kб), указанных в табл. 4.16. Значения Кб приведены в табл. 4.17.
Для аппаратов с перемешивающими устройствами жесткое соединение вала моторредуктора с валом мешалки не допускается. В этих случаях рекомендуется применять моторредукторы МР-1-315, МР-2-315 и МР-1-500 в исполнении Ф-1П. Для присоединения вала мотор-редуктора в исполнении Ф-1П на валу аппарата должен быть предусмотрен фланец нижней полумуфты. Фланцы соединяются с помощью конических болтов, входящих в комплект поставки мотор-редуктора.
Для мотор-редукторов МР-1-500 и МР-2-500 мощностью выше 90 кВт необходима принудительная смазка от отдельной масло-станции с расходом масла не менее 5 л/мин. В мотор-редукторе МР-3-800 предусмотрена принудительная замкнутая система смазки, включающая маслонасос с автономным электроприводом. Смазка мотор-редукторов других типов осуществляется путем заливки в корпус мотор-редуктора жидкою смазочного масла.
193

Таблица 4.16. Допускаемые нагрузки на выходные валы мотор-редукторов исполнений Ф-
1В и Ф-2В [15]
Типоразмер мотор-редуктора |
Допускаемая нагрузка, кН |
|
Осевая (А) в любом направле- |
Радиальная (Р) и совместные |
|
|
нии |
действия нагрузок (Р + 1,5А) |
МР-2-315 |
5 Kб |
12 Kб |
МР-2-500 |
15 Kб |
25 Kб |
МР-3-500 |
20 Kб |
30 Kб |
МР-3-800 |
25 Kб |
40 Kб |
Таблица 4.17. Коэффициент безопасности Kб [15]
Характер нагрузки |
Признаки нагрузки |
Kб |
|
Местная |
Передача крутящего момента на вал агрегата посредством |
1,0 |
|
зубчатых цепных передач |
|||
|
|
||
Колебательная |
Вал мотор-редуктора жестко соединен с валом агрегата. |
0,8 |
|
|
Имеются незначительные колебания аппарата |
|
|
Колебательная ударная |
Значительные колебания вала аппарата, вызывающие коле- |
0,6 |
|
|
бания мотор-редуктора вместе с фундаментом |
|
Конструкция мотор-редукторов серии МР, укомплектованных взрывозащищенными электродвигателями, приведена на рис. 4.3.
Масса мотор-редукторов зависит от исполнения комплектующего электропривода. Массы мотор-редукторов без электроприводов: МР-1-315 – 125 кг; МР-1-500 – 400 кг; МР-2- 315 – 350 кг; МР-2-500 – 870 кг; МР-3-500 – 1050 кг; МР-3-800 – 2500 кг.
Рис. 4.3. Мотор-редукторы серии МР: а типа МР-1; б - типа МР-2
Экранированные электроприводы. Экранированными электроприводами комплектуются герметичные аппараты с перемешивающими устройствами [12].
Экранированный электропривод (рис. 4.4) представляет собой взрывозащищенный асинхронный трехфазный электродвигатель с короткозамкнутым ротором, с защитными гильзами, предохраняющими активные части ротора и статора от воздействия среды, заполняющей полость ротора электродвигателя. Полость статора заполнена трансформаторным сухим маслом согласно ГОСТ 982–80*. На одном конце вала ротора установлено перемешивающее устройство, на другом – центробежный насос для обеспечения циркуляции жидкости в автономном контуре электропривода, необходимой для смазки подшипников и охлаждения электропривода. В качестве подпиточной жидкости может быть использована жидкость, являющаяся одним из компонентов рабочей среды, или какая-либо другая жидкость, нейтраль-
ная к ней, с кинематической вязкостью не более 5 10−5 м2/с, не склонная к налипанию, не со-
194
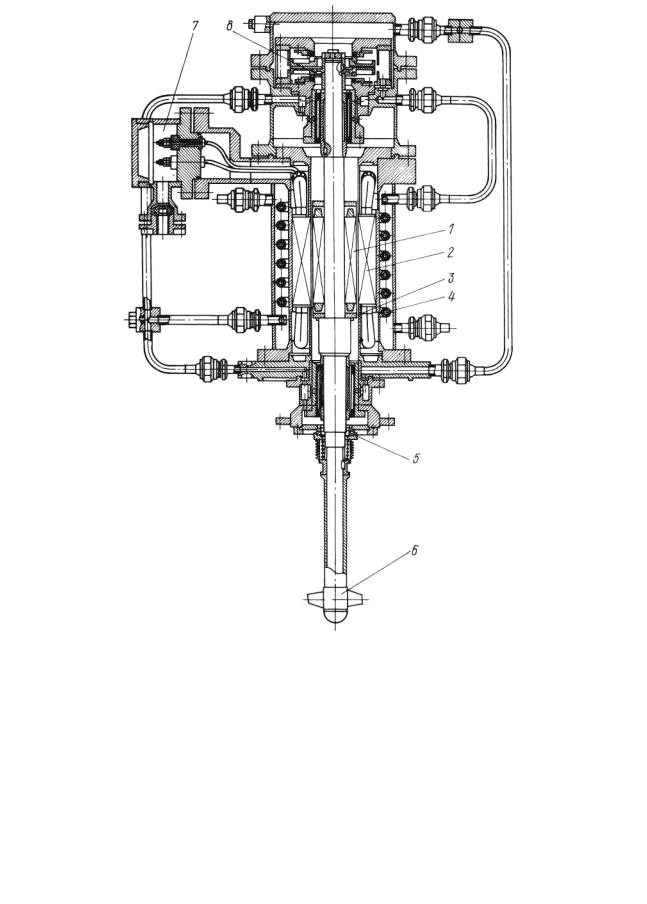
держащая взвешенных твердых частиц или растворенных веществ, которые в процессе работы могут выпадать в осадок, а также не склонная к образованию газовой фазы при температуре до 90 °С и нормальном давлении (0,1 МПа).
Рис. 4.4. Экранированный электропривод:
1 − ротор; 2 − статор; 3 − экранирующая защитная гильза; 4 − теплообменник; 5 − торцовое уплотнение вала; 6 − перемешивающее устройство; 7 − токоввод; 8 − центробежный насос
Полость ротора электродвигателя отделена от полости статора защитной экранирующей гильзой из немагнитной стали, а от реакционной полости – внутренним разделительным торцовым уплотнением.
Для надежной работы электропривода необходимо исключить возможность попадания реакционной среды в его полость. Для этого в полости электропривода давление жидкости должно превышать давление рабочей среды в аппарате. Допустимая перетечка подпиточной жидкости через внутреннее торцовое уплотнение – не более 300 г/ч. Рабочая температура в автономном контуре не должна превышать 80 °С.
Экранированные электроприводы изготовляют в двух исполнениях в соответствии с
ПИВРЭ [24] или ГОСТ 12.2.020–76*: В4Т4-МСВ или lExdosΙΙСТ4 и ВЗТ4 или lExdosΙΙВТ4. Применение в герметичных аппаратах высокооборотных перемешивающих устройств с
195
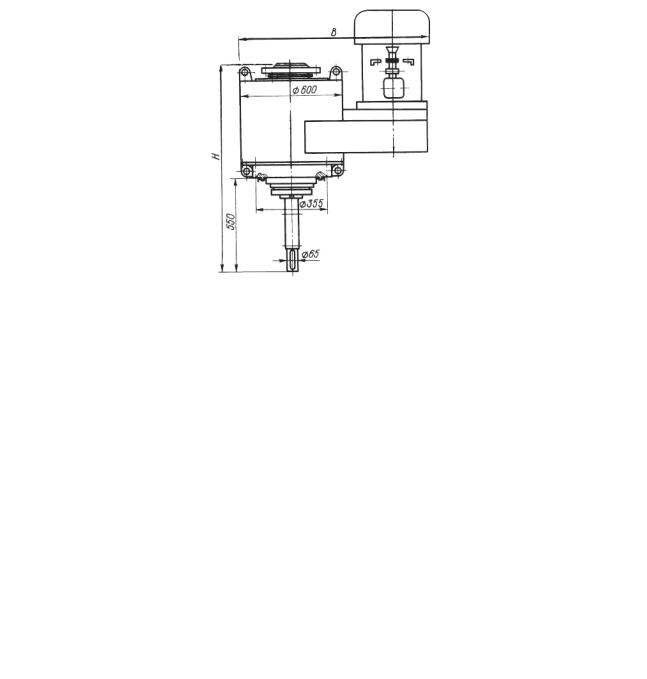
экранированными электроприводами обеспечивает надежную и безопасную работу с высокотоксичными, агрессивными, пожаро- и взрывоопасными средами, предотвращает загрязнение окружающей среды, улучшает санитарно-гигиенические условия труда и позволяет в ряде случаев существенно интенсифицировать технологические процессы за счет высокой частоты вращения перевешивающего устройства.
Магнитные узлы вращения. Магнитные узлы вращения представляют собой герметичные приводы, предназначенные для установки на аппараты с относительно малой частотой вращения перемешивающих устройств.
Магнитный узел вращения (рис. 4.5) состоит из базовой магнитной синхронной экранированной муфты и приводного устройства. В качестве привода используют электродвигатели серии В (вертикального исполнения). Передача движения осуществляется при помощи клиноременной или зубчатой передачи. При использовании клиноременной передачи необходимо осуществить мероприятия по предупреждению возникновения зарядов статического электричества в соответствии с правилами защиты от статического электричества в производствах химической, нефтехимической, нефтеперерабатывающей промышленности [23].
Рис. 4.5. Магнитный узел вращения
Магнитные узлы вращения могут эксплуатироваться на аппаратах, работающих во взрывоопасных зонах класса не выше В-Ia по ПУЭ [27], в которых могут образовываться взрывоопасные смеси не выше ЗТ4 по классификации ПИВРЭ.
Условия охлаждения переходной стойки должны обеспечивать температуру в полости герметичного экрана не выше 150 °С.
Основные параметры и характеристики магнитных узлов вращения должны соответст-
вовать ТУ 26-01-807–80.
Техническая характеристика магнитных узлов вращения:
Крутящий момент на выходном валу, Н м: |
|
номинальный |
315 |
предельный, не менее |
380 |
Допустимая нагрузка на выходном валу, Н: |
|
радиальная |
1000 |
аксиальная |
1800 |
Рабочее давление в полости герметизирующего экрана:
избыточное, МПа |
1,6 |
остаточное, Па |
133 |
Рабочая температура в полости экрана, °С от –20 до +150 Коэффициент полезного действия не менее 0,9
196
4.6. Применение взрывозащитного электрооборудования зарубежного производства
Взрывозащищенное электрооборудование зарубежного производства выбирают в соответствии с ОСТ 16.0.800.703–79 [17]. Условные знаки, входящие в маркировку взрывозащищенного электрооборудования, согласно действующим стандартам различных стран, указаны в табл. 4.18. Соответствие категорий и групп взрывоопасных смесей по классификациям различных стран приведено в табл. 4.19 и 4.20, соответствие зон взрывоопасности (взрывоопасных установок) – в табл. 4.21. Соответствие допустимых уровней и видов взрывозащиты электрооборудования в зонах взрывоопасности по классификациям различных стран приведено в табл. 4.22.
Анализ возможности применения зарубежного электрооборудования в условиях взрывоопасных зон на отечественных предприятиях должен включать: сопоставление классов взрывоопасных зон – по табл. 4.21, уровня и вида взрывозащиты электрооборудования – по табл. 4.22, категории и группы взрывоопасной смеси, применяемой в данном производстве, –
по табл. 4.19 и 4.20.
Таблица 4.18. Условные знаки, входящие в маркировку взрывозащищенного электрооборудования различных стран, ОСТ 16.0.800.702 – 79 [17]
Наименование знака |
Обозначение знака |
|
|
|
|
|||
Россия |
Англия |
Италия |
ФРГ |
Франция |
Япония |
|||
|
|
|||||||
Общий знак взрывоза- |
|
|
|
|
|
|
||
щищенности |
(взрыво- |
Ех |
Ех |
Ех |
Ех |
Ех |
− |
|
безопасности) |
|
|
|
|
|
|
||
Знаки, характеризующие виды взрывозащиты: |
|
|
|
|
||||
взрывонепроницаемая |
d |
d |
d |
d |
d |
d |
||
оболочка |
|
|
|
|
|
|
|
|
продувка оболочки под |
p |
p |
p |
p |
p |
f |
||
избыточным давлением |
|
|
|
|
|
|
||
масляное |
заполнение |
0 |
0 |
0 |
0 |
0 |
0 |
|
оболочки |
|
|
|
|
|
|
|
|
кварцевое |
заполнение |
q |
q |
q |
q |
q |
s |
|
оболочки |
|
|
|
|
|
|
|
|
специальный вид взры- |
s |
s |
s |
s |
− |
s |
||
возащиты |
|
|
|
|
|
|
|
|
газовое |
заполнение |
p |
p |
− |
p |
− |
f |
|
оболочки под избыточ- |
|
|
|
|
|
|
||
ным давлением |
|
|
|
|
|
|
||
защита вида «е» (по- |
e |
e |
e |
e |
e |
e |
||
вышенная надежность) |
|
|
|
|
|
|
||
искробезопасная элек- |
i |
i |
i |
i |
i |
i |
||
трическая цепь |
|
|
|
|
|
|
Таблица 4.19. Соответствие категорий взрывоопасных смесей по классификации различных стран, ОСТ 6.0.800.700–79 [17]
Обозначение, принятое в |
|
|
|
|
||
СССР |
согласно |
ГОСТ |
Англия, Италия, ФРГ, Франция |
Япония |
|
|
12.1.011–76* |
|
|
|
|
|
|
|
ΙΙА |
|
ΙΙА |
|
1 |
|
|
ΙΙВ |
|
ΙΙВ |
|
2 |
|
|
ΙΙС |
|
ΙΙС |
3а |
|
3n |
|
|
3b |
|
|||
|
|
|
|
3c |
|
|
197

Таблица 4.20. Соответствие групп взрывоопасных смесей по классификациям различных стран, ОСТ 16.0.800.700–79 [17]
Температура самовоспламене- |
Обозначение группы взрывоопасных смесей |
|
ния, °С |
СССР, Англия, Италия, ФРГ, |
Япония |
|
Франция |
|
Св. 450 |
Т1 |
G1 |
» 300 |
Т2 |
G2 |
» 200 |
Т3 |
G3 |
» 135 |
Т4 |
G4 |
» 100 |
Т5 |
G5 |
» 85 |
Т6 |
− |
Таблица 4.21. Соответствие зон взрывоопасности (взрывоопасных установок) по классификации различных стран, ОСТ 16.0.800.701–79 [17]
|
|
Обозначение зоны взрывоопасности по классифи- |
||||||
Зона взрывоопасности по |
классифи- |
кациям различных стран |
|
|
|
|||
кации, принятой в СССР |
|
Англия |
Италия |
|
Фран- |
ФРГ |
Япония |
|
|
|
|
|
|||||
|
|
|
|
|
ция |
|
|
|
– |
|
Div. 0 |
Classe |
1, |
Zone 0 |
Zone 0 |
Classe |
0 |
|
|
|
Div. 0 |
|
|
|
Location |
|
Зона класса B-I |
|
Div. 1 |
Classe |
1, |
Zone 1 |
Zone 1 |
Classe |
1 |
|
|
|
Div. 1 |
|
|
|
Location |
|
Зона класса В- Iа |
|
Div. 2 |
Classe |
1, |
Zone 2 |
Zone 2 |
Classe |
2 |
|
|
|
Div. 2 |
|
|
|
Location |
|
Зона класса B-I6 |
|
− |
− |
|
− |
− |
− |
|
|
|
|
|
|
|
|
|
|
– |
|
Div. 0 |
Classe |
1, |
Zone 0 |
Zone 0 |
Classe |
0 |
|
|
|
Div. 0 |
|
|
|
Location |
|
|
|
Div. 1 |
Classe |
1, |
Zone 1 |
Zone 1 |
Classe |
1 |
Зона класса В- Iг |
|
|
Div. 1 |
|
|
|
Location |
|
|
Div. 2 |
Classe |
1, |
Zone 2 |
Zone 2 |
Classe |
2 |
|
|
|
|||||||
|
|
|
Div. 2 |
|
|
|
Location |
|
Зона класса В- II |
|
− |
− |
|
Classe |
Zone 10 |
– |
|
Зона класса В- IIа |
|
− |
− |
|
2 |
Zone 11 |
– |
|
|
|
|
|
|||||
|
|
|
|
|
|
|
|
|
Кроме сопоставления маркировки электрооборудования необходимо анализировать его конструктивные особенности, обращая особое внимание на примененные виды взрывозащиты.
При выборе зарубежного электрооборудования необходимо учитывать следующее:
1)категория взрывоопасной смеси принимается во внимание только при выборе электрооборудования с видами взрывозащиты «взрывонепроницаемая оболочка» и «искробезопасная электрическая цепь»; для других видов взрывозащиты категория во внимание не принимается;
2)электрооборудование с источником теплоты, маркировка взрывозащиты которого, согласно национальному стандарту, не содержит знака группы взрывоопасной смеси, должно выбираться в зависимости от максимальной температуры нагрева наружных (внутренних для защиты вида «е»);
3)электрооборудование с видом взрывозащиты «искробезопасная электрическая цепь» не зависит от группы воспламеняемости взрывоопасной смеси и может эксплуатироваться во взрывоопасных средах любой группы воспламеняемости;
4)электрооборудование с видом взрывозащиты «искробезопасная электрическая цепь»,
198
рассчитанное на водородовоздушную смесь, может применяться во взрывоопасных смесях всех категорий и групп; .
5)электрооборудование с защитой вида «е», для которого указано время нагрева пусковым током от температуры, обусловленной длительной работой при номинальной нагруз-
ке, до предельной температуры (te), должно быть укомплектовано пусковой и защитной аппаратурой, обеспечивающей его отключение в аварийном режиме;
6)электрооборудование с видом взрывозащиты «продувка или заполнение оболочки под избыточным давлением» должно быть укомплектовано блокировочными устройствами, обеспечивающими предварительную продувку оболочки перед пуском, подачу сигнала или отключения электрооборудования при снижении избыточного давления защитного газа в оболочке ниже допустимого значения, указанного в фирменной инструкции по эксплуатации;
7)стационарные электроаппараты и приборы, которые не подвержены нагреву выше 80 °С, не имеют искрящих элементов и предназначены для работы в условиях взрывоопасных
зон классов B-Ia и В-Ιг, могут выбираться без средств взрывозащиты, но должны иметь степень защиты IP54;
8)электрооборудование США, Канады и Бельгии, которое не имеет маркировки обозначений видов взрывозащиты, должно выбираться с учетом соответствующего уровня взрывозащиты;
9)электрооборудование, предназначенное для взрывоопасных сред более высокой категории и группы, может применяться в средах более низкой категории и группы.
Таблица 4.22. Соответствие допустимых уровней и видов взрывозащиты электрооборудования в зонах взрывоопасности по классификации различных стран, ОСТ 16.0.800.703–79 [17]
Обозначения, принятые в СССР |
|
Обозначение вида |
взрывозащиты электрообору- |
|||||
|
дования в различных странах |
|
|
|||||
|
|
|
|
|
||||
Уровень |
|
|
|
|
|
|
|
|
взрывозащиты |
Класс взрыво- |
Вид взрыво- |
|
|
|
|
|
|
согласно |
опасной зоны |
защиты ГОСТ |
Англия |
Италия |
ФРГ |
Франция |
Япония |
|
ГОСТ |
по ПУЭ [27] |
12.2.020–76* |
|
|
|
|
|
|
12.2.020–76* |
|
|
|
|
|
|
|
|
0 |
|
i |
ia |
IA |
i |
ia |
i |
|
B-I |
s |
s |
s |
s |
− |
s |
||
|
||||||||
|
В- Iа |
d |
d |
d (PE) |
d |
d |
d |
|
|
B-I6 |
p |
p |
p (SI) |
p |
p |
f |
|
1 |
B-Iг |
o |
o |
o |
o |
o |
o |
|
|
B-II |
q |
q |
q |
q |
q |
s |
|
|
|
e |
e |
e |
e |
e |
e |
|
|
В- Iа |
i |
ib |
iB |
i |
ib |
i |
|
2 |
B-I6 |
p |
p |
p |
p |
p |
f |
|
|
B-Iг |
|||||||
|
|
|
|
|
|
|
Ремонт зарубежного взрывозащищенного электрооборудования проводится в порядке, установленном для ремонта отечественного взрывозащищенного электрооборудования. В условиях эксплуатации могут проводиться только профилактические осмотры и текущие ремонты, не связанные с восстановлением взрывозащищенности электрооборудования. Средний и капитальный ремонты, связанные с нарушением взрывозащищенности, должны выполняться на специализированных ремонтных предприятиях, зарегистрированных в органах Госгортехнадзора РФ, оснащенных специальным оборудованием и имеющих разрешение вышестоящей организации. При сдаче электрооборудования в ремонт на нем должны быть сохранены фирменные таблички с маркировкой взрывозащиты и приложена вся имеющаяся техническая документация.
Взрывозащищенное электрооборудование, поставляемое в РФ как индивидуально, так
199
и в комплекте с технологическими аппаратами, должно пройти освидетельствование средств взрывозащиты во ВНИИВЭ. По согласованию с внешнеторговыми организациями освидетельствование средств взрывозащиты электрооборудования до поставки его в РФ может проводить фирма, поставляющая это электрооборудование.
При использовании зарубежного электрооборудования для конкретных условий, для работы с хорошо известными взрывоопасными средами освидетельствование допускается не проводить, а ограничиваться соответствующим заключением головной проектной организации, ответственной за оснащение электрооборудованием данной отрасли промышленности или данного производства [35].
4.7. Защита аппаратов от превышения давления 4.7.1. Источники аварийного повышения давления в аппаратах и расчет
аварийного притока среды в аппарат
Технологическое оборудование, в котором возможно аварийное повышение давления, представляет серьезную опасность при эксплуатации из-за разрушения под действием давления газов. Поэтому во всех случаях, когда в аппарате может быть превышено предельно допустимое давление, определяемое его прочностью, аппарат должен быть надежно защищен от разрушения с помощью различных предохранительных устройств (ПУ), работающих по принципу сброса из аппарата излишнего количества среды.
Источниками аварийного роста давления в аппаратах могут являться внезапные, не предусмотренные рабочим процессом случаи:
а) приток в аппарат газа, пара или жидкости при закрытом выходе из него; б) обогрев или нарушение охлаждения аппарата, в результате чего происходит нагрев
газа или пара, испарение жидкости в нем или интенсификация химической реакции; в) взрыв среды в аппарате.
Причинами аварийного повышения давления могут являться: а) ошибки обслуживающего персонала; б) отказ запорно-регулирующей арматуры;
в) нарушение функционирования системы автоматического управления; г) внезапное разрушение внутренних устройств аппарата: труб, змеевиков, рубашек и
др.;
д) замерзание охлаждающей воды; е) выход из-под контроля химических реакций;
ж) интенсивный нагрев поверхности аппарата от внешнего источника, например в результате пожара, солнечной радиации и т. п.
Для выбора предохранительного устройства необходимо знать величину аварийного притока среды и характер его изменения в зависимости от источника повышения давления.
Наиболее опасной аварийной ситуацией является та, при которой в аппарат поступает наибольшее количество среды или давление растет с максимальной скоростью. Выбор ПУ следует выполнять именно на такие экстремальные условия.
Под аварийным расходом та понимают массовый расход среды через ПУ при давлении, превышающем рабочее давление в аппарате на величину, определяемую Правилами Ростехнадзора [26].
Аварийный расход среды в различных случаях определяют следующим образом.
При постоянной подаче рабочей среды в аппарат поршневыми компрессором и насосом в случае перекрытия выхода среды из аппарата аварийный расход равен массовой подаче компрессора тк или насоса тн:
та = тк ; та = тн . |
(4.1) |
200
При внезапном разрушении элементов внутренних устройств с выходом среды из них в корпус аппарата, имеющего давление ниже, чем в разрушенных элементах, аварийный расход определяют как максимально возможный расход среды через максимально возможную площадь сечения разрушенного элемента (элементов). Он зависит от площади сечения разрушения Fa, давления р1а и температуры t1а в разрушенном элементе, рабочего давления в корпусе аппарата р2а, физико-химических свойств среды в разрушенном элементе (показателя адиабаты kа, удельной газовой постоянной Rа, молярной массы М) и коэффициента расхо-
да через отверстие разрушения αа.
При отказе запорной арматуры и перетекании среды из полости более высокого давления в полость более низкого давления аварийный расход определяют аналогично предыдущему случаю, но при площади сечения и коэффициенте расхода полностью открытой арматуры. Расчетные формулы для определения аварийного расхода в этом случае те же, что и при определении пропускной способности ПУ (п. 4.7.6).
При пожаре вблизи аппарата, заполненного жидкостью и имеющего закрытый выход, аварийный расход определяют по формуле
ma = kFап (tг − tж ) |
, |
(4.2) |
r |
|
|
где Fап – площадь наружной поверхности аппарата, м2; tг – температура газовоздушной сме-
си, омывающей при пожаре наружную поверхность аппарата, при расчетах принимают tr = 600…700 °С; tж – температура кипения жидкости при давлении внутри аппарата, °С; r – теплота испарения жидкости при температуре tж, Дж/кг; k – общий коэффициент теплопередачи от окружающей газовоздушной смеси через стенку аппарата к содержащейся в нем жидко-
сти, Вт/(м2 К); для неизолированных неохлаждаемых аппаратов принимают k = 25 Вт/(м2 К); для изолированных и охлаждаемых аппаратов k определяют в зависимости от степени охлаждения, толщины и коэффициента теплопроводности изоляции.
Для аппаратов, имеющих специальное водное оросительное устройство, в числителе формулы (4.2) вводят понижающий коэффициент 0,5.
В аппаратах, где химические реакции протекают с выделением тепла, при недостаточном его отводе вследствие нарушения системы охлаждения, а также при непредусмотренном технологическим процессом обогреве избыточное давление для системы определенного объема зависит от интенсивности тепловыделения и теплового обогрева, а аварийный расход, т. е. количество рабочей среды, подлежащей сбросу в аварийном режиме, может быть различным в каждом конкретном случае.
Для определения величины аварийного притока среды в случае выхода из-под контроля химических реакций или прорыва легкокипящих жидкостей необходимо знать динамику развития процессов. Во многих случаях наиболее опасной аварийной ситуацией является взрыв технологической среды внутри аппарата.
Основной характеристикой динамики развития взрыва является скорость роста давле-
ния dp / dτ, которая зависит от физико-химических свойств взрывоопасной среды, степени турбулизации ее в аппарате, объема и формы аппарата и других факторов.
Аварийный расход в этом случае связан с соответствующей ему скоростью нарастания давления уравнением состояния:
mа = |
MV dp |
, |
(4.3) |
||
|
|
||||
RуTm dτ |
|||||
|
|
|
где М – молярная масса технологической среды в аппарате, кг/кмоль; V – емкость аппарата, м3; Тт – средняя абсолютная температура истекающих продуктов взрыва, К; р – абсолютное
давление, Па; dp/dτ – скорость роста давления в аппарате при взрыве, Па/с.
Максимальную скорость роста давления в аппарате определяют по следующей форму-
ле [28]:
201
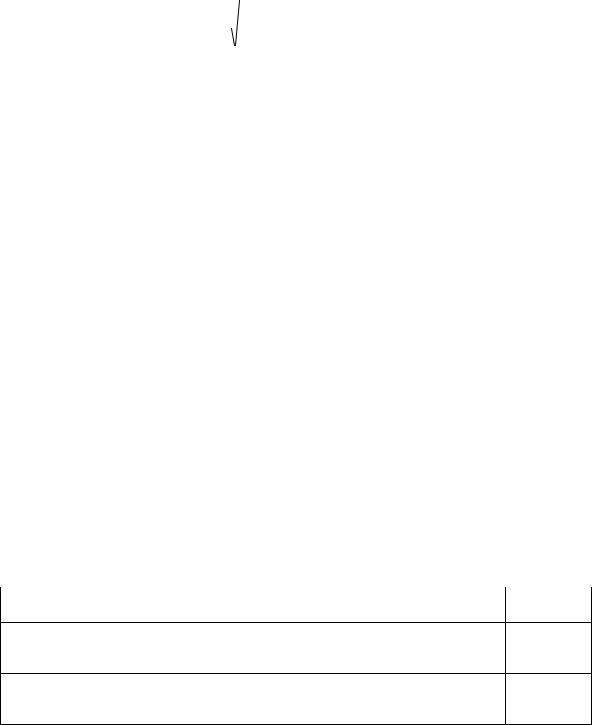
dp |
|
dp |
pр + 0,1 |
|
|
|
|
||
= K |
|
V |
|
|
|||||
dτ |
|
|
|
|
3 |
0 |
, |
(4.4) |
|
0,1 |
|
||||||||
|
T dτ 0 |
|
|
V |
|
|
где КТ – коэффициент турбулизации фронта пламени, принимаемый по табл. 4.23; (dp/dτ)0 – максимальная скорость роста давления в экспериментальной бомбе емкостью V0 = 0,01 м3 при взрыве смеси технологической среды с воздухом, имеющей оптимальную концентрацию и содержащейся без начального избыточного давления при температуре 300 К (значения
(dp/dτ)0 для некоторых сред приведены в табл. 4.24); pр – рабочее давление технологической среды в аппарате до возникновения взрыва, МПа.
При отсутствии экспериментальных данных о скорости роста давления при взрыве величину dp/dτ определяют по формуле:
dp |
|
( pр + 0,1)106 uпл (ε −1) |
|
p |
+ 0,1 |
|
1/ k |
|
|
|
= K F |
|
|
1 |
|
|
, |
(4.5) |
|
dτ |
V |
pр + 0,1 |
|||||||
T пл |
|
|
|
||||||
|
|
|
|
|
|
|
|
где Fпл – максимально возможная площадь поверхности фронта пламени при сгорании смеси технологической среды с воздухом в аппарате, м2; ипл – нормальная скорость распростране-
ния пламени в горючей среде, содержащейся в аппарате, м/с, определяемая по табл. 4.25; ε – степень относительного увеличения давления данной горючей среды в закрытой бомбе, определяемая по табл. 4.25; р1 – избыточное давление технологической среды в аппарате при условиях срабатывания ПУ, МПа; k – показатель изоэнтропы горючей смеси, принимаемый равным показателю изоэнтропы среды при нормальных условиях без учета влияния температуры при взрыве, т. е. kн (табл. 4.26).
Величину Fпл определяют геометрическим путем из условия, что пламя распространяется сферически из точки инициирования взрыва. Наиболее опасной точкой инициирования взрыва в аппарате является геометрический центр его внутренней полости.
В частности, для аппаратов цилиндрической формы диаметром D и высотой Н:
Fпл = πD2 при D ≤ H;
Fпл = πDH при D > H;
Для сферических аппаратов с диаметром D площадь поверхности фронта пламени Fпл = πD2. Таблица 4.23. Коэффициент КТ турбулизации фронта пламени в аппарате [28]
Тип аппарата |
КТ |
Сосуд, в который нет притока технологической среды |
1,5…2,0 |
Сосуд при наличии притока технологической среды, находящейся в турбули-
зованном состоянии; наличие внутри аппарата конструктивных элементов 2,0…5,0 (лопасти, ребра и т. п.), способствующих возникновению турбулизации
Сосуд, снабженный устройством, создающим внутри его интенсивную тур-
булизацию технологической среды (встроенный вентилятор, тангенциальный 5,0…10,0 ввод газа в аппарат с большой линейной скоростью)
Таблица 4.24. Значения (dp/dτ)0 для некоторых веществ [28]
Вещество |
(dp/dτ)0, МПа/с |
Адипиновая кислота |
17,3 |
Алюминий распыленный |
14,7 |
Диметилизофталат |
51,0 |
Диметилтерефталат |
77,0 |
Динитроортокрезол |
14,0 |
Дициклопентадиен |
61,0 |
Изофталевая кислота |
19,8 |
Лигнин чистый |
30,0 |
Поливинилацетат |
6,4 |
Поливинилбутираль |
12,8 |
202
Продолжение табл. 4.24
Вещество |
(dp/dτ)0, МПа/с |
Полиоксиметилен |
83,0 |
Полимер акриламида |
17,5 |
Полимер акрилонитрила |
77,3 |
Полиметилметакрилат |
12,8 |
Полипропилен нестабилизированный |
35,0 |
Полипропилен стабилизированный |
25,0 |
Полистирол |
32,0 |
Полиформальдегид |
26,3 |
Полиэтилен высокого давления |
25,6 |
Полиэтилен низкого давления |
48,0 |
Сера |
12,5 |
Сополимер акрилонитрила и винилпиридина |
42,1 |
Сополимер метилметакрилата и этилакрилата |
42,1 |
Сополимер метилметакрилата, стирола, бутадиена и этилакрилата |
30,2 |
Сополимер стирола и акрилонитриловой кислоты |
9,0 |
Сополимер стирола и малеинового ангидрида |
25,0 |
Сополимер этилена и малеинового ангидрида |
8,5 |
Терефталиевая кислота |
51,0 |
Фенилофурфурольная смола |
54,5 |
Фенолформальдегидная смола |
22,2 |
Фталевый ангидрид |
27,0 |
Таблица 4.25. Значения ипл и ε для различных горючих смесей веществ с воздухом [28]
Вещество |
ипл |
ε |
Аммиак |
0,23 |
7,0 |
Ацетилен |
1,70 |
11,3 |
Ацетилен1* |
15,40 |
– |
Ацетон |
0,44 |
9,9 |
Бензол |
0,48 |
10,0 |
н-Бутан |
0,45 |
9,6 |
Водород |
2,70 |
8,4 |
Водород1* |
13,80 |
– |
Водород2* |
2,20 |
– |
н-Гексан |
0,39 |
9,6 |
н-Гептан |
0,43 |
9,6 |
Диэтиловый эфир |
0,49 |
10,2 |
Изооктан |
0,41 |
9,1 |
Метан |
0,34 |
8,2 |
Метанол |
0,50 |
8,4 |
Окись углерода |
0,33 |
8,3 |
Окись этилена |
0,89 |
10,9 |
Органические пыли |
0,3–0,8 |
– |
н-Пентан |
0,44 |
9,6 |
Пропан |
0,46 |
9,6 |
Сероуглерод |
0,59 |
8,8 |
Углеводороды |
0,3–0,5 |
– |
Циклогексан |
0,44 |
9,6 |
Этилен |
0,74 |
9,9 |
Этил амин |
0,46 |
10,6 |
Этиловый спирт |
0,56 |
8,4 |
Примечания: 1* − Смесь с кислородом; 2* − Смесь с хлором.
203
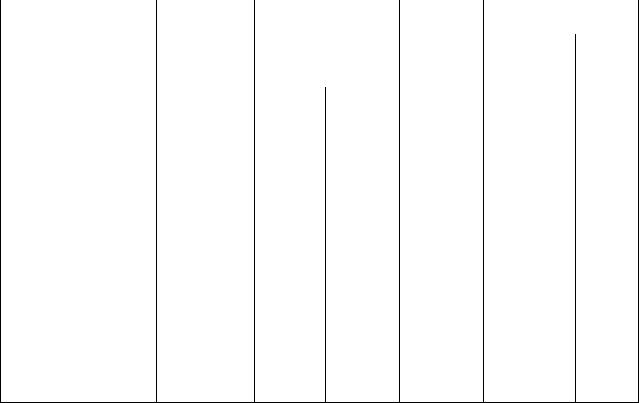
Таблица 4.26. Характеристики газов и паров
|
|
kН |
|
β |
|
Параметры |
критиче- |
|
Химическая |
|
М, |
ской точки |
|
||
Газ |
|
|
|
|
|||
При 0 °С |
и избы- |
|
|
||||
формула |
кг/кмоль |
ркр. т (абс), |
Ткр. т, К |
||||
|
|
точном |
давлении |
|
МПа |
||
|
|
0,101 МПа |
|
|
|
||
|
|
|
|
|
|
||
Азот |
N2 |
1,40 |
|
0,528 |
28,02 |
3,35 |
126,0 |
Аммиак |
NH3 |
1,32 |
|
0,543 |
17,03 |
11,30 |
405,4 |
Аргон |
Аг |
1,67 |
|
0,488 |
39,94 |
4,80 |
150,6 |
Ацетилен |
С2Н2 |
1,23 |
|
0,559 |
26,04 |
6,24 |
308,5 |
Бутан |
С4Н10 |
1,10 |
|
0,585 |
58,12 |
3,89 |
425,0 |
Водород |
Н2 |
1,41 |
|
0,527 |
2,02 |
1,28 |
32,8 |
Воздух |
– |
1,40 |
|
0,528 |
28,96 |
3,77 |
132,5 |
Гелий |
Не |
1,66 |
|
0,488 |
4,00 |
0,23 |
5,04 |
Двуокись углерода |
СО2 |
1,31 |
|
0,546 |
44,01 |
7,53 |
304,4 |
Дифтордихлорметан |
CF2Cl2 |
1,14 |
|
0,576 |
120,92 |
3,96 |
384,7 |
Кислород |
О2 |
1,40 |
|
0,528 |
32,00 |
5,01 |
154,6 |
Метан |
СН4 |
1,30 |
|
0,546 |
16,04 |
4,64 |
190,5 |
Окись углерода |
СО |
1,40 |
|
0,528 |
28,01 |
3,45 |
133,0 |
Пропан |
С3Н8 |
1,14 |
|
0,576 |
44,09 |
4,27 |
369,8 |
Сероводород |
H2S |
1,30 |
|
0,546 |
34,08 |
9,00 |
373,4 |
Хлор |
С12 |
1,34 |
|
0,540 |
70,91 |
7,61 |
417,0 |
Этан |
С2Н6 |
1,22 |
|
0,560 |
30,07 |
4,86 |
305,3 |
Этилен |
С2Н4 |
1,24 |
|
0,557 |
28,05 |
5,03 |
282,9 |
Примечания: Формулы для расчета параметров смесей:
(ркр. т)см = Σ (ркр. т)iri; |
(Rу)см = 8314/ ΣMiri; |
(Ткр. т)см = Σ (Ткр. т)iri; |
kсм = 1 + 1 / Σ(ri / (ki – 1)) |
(Z)см = Σ (Z)iri; |
Мсм = Σ Мiri; |
4.7.2. Допустимые кратковременные повышения давления в аппарате
В соответствии с требованиями Ростехнадзора [26] для аппаратов, работающих под давлением пара или газа, число ПУ, их размеры и пропускную способность выбирают таким
образом, чтобы избыточное давление в аппарате р1 |
при действии ПУ не превышало следую- |
|||||
щих допустимых значений: |
|
|
|
|
|
|
|
рр, МПа |
≤ 0,3 |
|
Св. 0,3 до 6,0 |
Св. 6,0 |
|
|
р1, МПа |
рр+0,05 |
|
1,15рр |
1,1рр |
|
В обоснованных случаях, например при резких колебаниях давления рабочей среды в защищаемой системе, допускается во время действия ПУ повышение давления в аппарате до 25 % от рабочего при условии, что это превышение давления предусмотрено проектом и отражено в паспорте аппарата.
Для аппаратов, работающих под давлением жидкости, превышение давления над избыточным рабочим при работе ПУ допускается не более чем на 0,1 МПа для рабочих давлений до 0,4 МПа включительно и на 25 % от рр для более высоких рабочих давлений.
Кроме того, следует учитывать, что при допущении повышения давления в аппарате во время действия ПУ более чем на 10 % от рр этот аппарат необходимо рассчитывать на прочность по давлению, равному 90 % от давления при полном открытии ПУ, но не менее, чем рабочее давление.
Для предохранительных клапанов (ПК) указанные предельные значения относят к разности давлений полного открытия рп. о. и настройки клапана рн.
Стандарт СТ СЭВ 3085–81 устанавливает следующие значения предельной разности давлений полного открытия рп. о. и начала открытия рн. о. для ПК, работающих на паре или га-
204
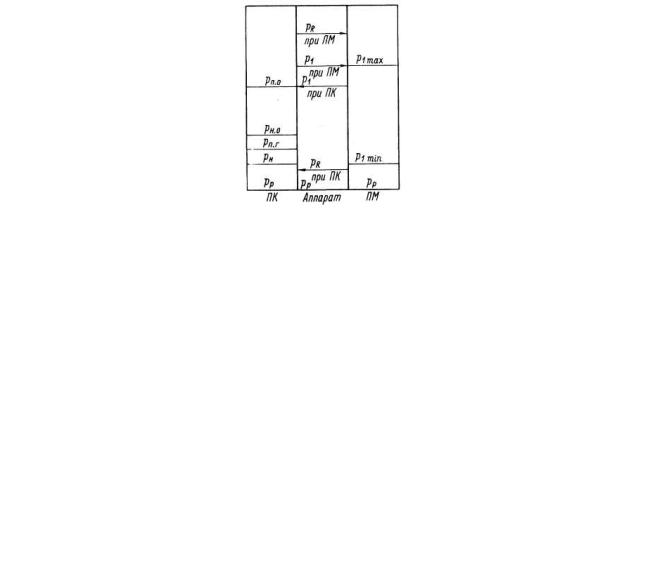
зе:
рр, МПа |
< 0,25 |
>0,25 |
рп. о. – рн. о., МПа |
0,15 рн. о. |
0,1рн. о. |
Для жидкостей при любом рабочем давлении в аппарате рп. о. ≤ 1,25 рн. о..
При этом ПК должны быть рассчитаны и отрегулированы так, чтобы в аппарате не могло образоваться избыточное давление более 1,1 рр.
В производствах нефтехимической и нефтеперерабатывающей промышленности для аппаратов, работающих при избыточном давлении рр < 10 МПа, в целях уменьшения загрязнения атмосферы и сокращения потерь продуктов принимают следующие превышения избыточного расчетного давления в аппарате над рабочим давлением рр согласно табл. 4.27:
Таблица 4.27
Технологическая сре- |
Нейтральная |
Взрывоопасная, 1-го и 2-го классов опасности |
|
да в аппарате |
|
согласно ГОСТ 12.1.007–76* |
|
рр, МПа |
≤ 10 |
≤ 4,0 |
Св. 4,0 до 10,0 |
рR, МПа |
1,1рр, но ≥ рр+0,1 |
1,2рр, но ≥ рр + 0,3 |
1,15рр |
Вэтих случаях допустимое кратковременное повышение давления в аппарате при действии ПУ рассчитывают не относительно рр, а относительно pR (расчетное давление).
Всоответствии с особенностями работы ПУ – предохранительных клапанов (ПК) и предохранительных мембран (ПМ) – установлены следующие понятия давлений (рис. 4.6).
Рис. 4.6. Давление в аппарате при срабатывании предохранительных клапанов (ПК)
или предохранительных мембран (ПМ)
Рабочее давление (рр) – наибольшее избыточное давление в аппарате при нормальном протекании технологического процесса без учета допустимого кратковременного повышения давления во время действия ПУ.
Расчетное давление (pR) – наименьшее избыточное давление, принятое при расчете на прочность элементов аппарата, работающего под давлением, равное рабочему давлению или превышающее его.
Максимально допустимое давление в аппарате (р1) – максимальное избыточное давле-
ние в защищаемом ПУ аппарате, допускаемое официальными нормами при сбросе среды через ПУ.
Давление настройки ПК (рн) – наибольшее избыточное давление на входе в ПК, при котором обеспечивается заданная герметичность в затворе. Давление рн равно рабочему или превышает его, но не более чем на 25 %.
Давление потери герметичности ПК (рп. г.) – избыточное давление на входе в ПК, при котором начинается протечка, превышающая допустимую; значение рп. г. несколько выше рн.
Давление начала открытия ПК (рн. о.) – избыточное давление на входе в ПК, при котором сила, направленная на открытие клапана, уравновешена силами, удерживающими золотник на седле. При этом давлении заданная герметичность в затворе нарушена и начинается
205
подъем золотника; рн. о. ≥ 1,05 рр.
Давление полного открытия ПК (рп. о.) – наименьшее избыточное давление на входе в ПК, при котором золотник клапана поднят на расчетную высоту, обеспечивающую заданную
пропускную способность ПК; рп. о. ≤ р1; в клапанах непрямого действия рп. о. = рн. о.
Давление закрытия ПК (рз) – избыточное давление на входе в ПК, при котором после сброса технологической среды происходит посадка золотника на седло с обеспечением заданной герметичности. Значение рз допускают не менее (0,8…0,95) рр.
Давление срабатывания ПМ (р1) – избыточное давление в аппарате на входе в ПМ, при котором происходит разрушение мембраны. Назначают минимальное и максимальное значения р1 в зависимости от рр и pR в защищаемом аппарате. При этом р1 mln принимают не менее чем 1,05рр для исключения возможности ложных срабатываний ПМ, а р1 max должно быть не больше 1,1 рр.
Противодавление (р2) – максимальное избыточное давление за ПУ, равное статическому давлению в закрытой емкости, куда сбрасывается среда из ПУ, или атмосферному давлению при сбросе среды на свечу. В зависимости от давления перед ПУ и размеров сбросной системы в ней при работе ПУ может образоваться динамическое противодавление, которое прибавляется к статическому давлению р2.
4.7.3. Классификация предохранительных устройств
Предохранительные устройства (ПУ) – вид арматуры, используемой для автоматического выпуска рабочей среды из аппарата при чрезмерном повышении давления в нем. Классификация ПУ показана на рис. 4.7.
По кратности использования ПУ подразделяют на две основные группы:
1)многократно используемые устройства – предохранительные клапаны (ПК) с самодействующим замыкающим элементом (рис. 4.8);
2)устройства одноразового действия – предохранительные мембраны (ПМ) (рис. 4.9) – специально ослабленные элементы с точно рассчитанным порогом разрушения по давлению.
Предохранительные клапаны
По принципу действия различают следующие ПК:
1)клапаны прямого действия (рис. 4.8, а–д), открывающиеся непосредственно под действием давления рабочей среды;
2)клапаны непрямого действия (рис. 4.8, е), в которых главный предохранительный клапан открывается с помощью специального привода.
Клапаны прямого действия (рис. 4.8, а–д). Классифицировать ПК прямого действия принято по нескольким признакам.
По виду нагрузки на золотник:
1)грузовые ПК с прямым нагружением груза на золотник и рычажно-грузовые с нагружением через рычаг (рис. 4.8, а);
2)клапаны с газовой камерой, у которых нагрузка создается сжатым газом, находящимся в герметически закрытой камере и действующим через специальную мембрану и шток на золотник клапана; такие ПК весьма чувствительны к колебаниям температуры окружающей среды, вызывающим изменение настройки клапана;
3)рычажно-пружинные клапаны (применяются очень редко);
4)пружинные клапаны с прямым действием пружины на золотник (рис. 4.8, б, г); они просты по конструкции, обладают высокой чувствительностью и надежностью в эксплуатации, благодаря чему нашли наиболее широкое распространение во всех отраслях промышленности;
5)магнитно-пружинные ПК (рис. 4.8, д), в которых усилие магнита добавляется к усилию пружины при закрытом клапане, чем достигается высокая герметичность в затворе. В таких клапанах открытие происходит быстро, двухпозиционно, закрытие – постепенно, благодаря действию магнита (ход клапана пропорционален снижению давления).
206

207
Рис. 4.7. Классификация предохранительных устройств
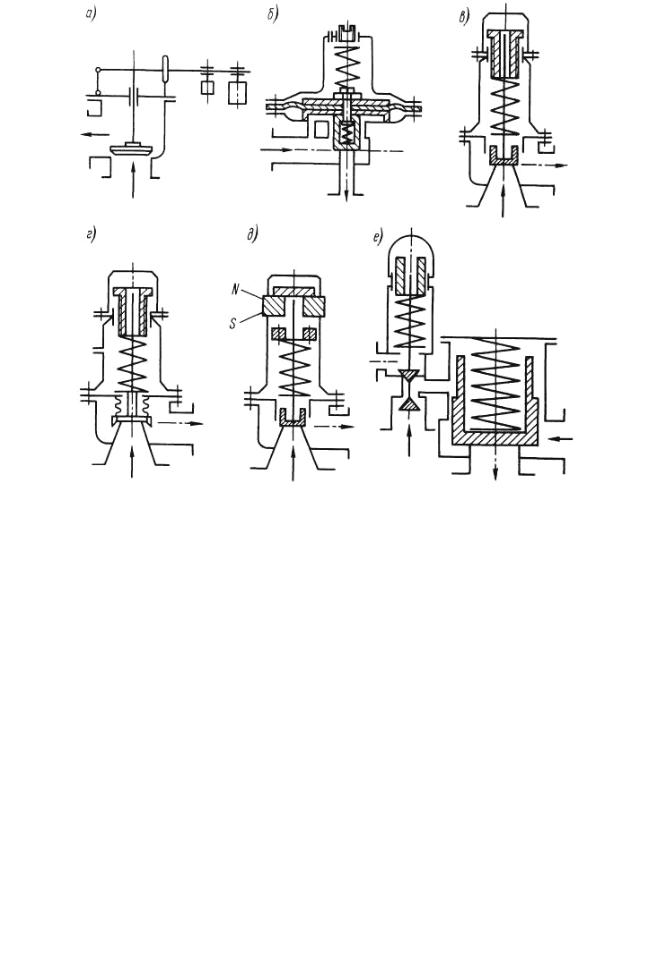
Рис. 4.8. Предохранительные клапаны: а–д – прямого действия (а – рычажно-грузовые;
б– с подачей среды на золотник и с чувствительным элементом в виде мембраны;
в– пропорционального действия; г – двухпозиционного действия с разгрузочным элементом в виде сильфона; д – магнитно-пружинные); е – непрямого действия
симпульсом от рабочего давления
По виду сообщения послезолотниковой полости клапана с атмосферой:
1)открытые, в которых рабочая среда выпускается в атмосферу (такие клапаны работают без статического противодавления);
2)закрытые, не сообщающиеся с атмосферой (такие клапаны выпускают рабочую среду в закрытую систему); в этом случае клапан работает с противодавлением, равным статическому давлению в выпускной системе и сопротивлению трубопровода при протекании по нему сбрасываемой среды.
По виду разгрузки послезолотниковой полости:
1)неразгруженные ПК, в которых на золотник действует сила от статического и динамического противодавлений, последнее возникает в надзолотниковой полости клапана из-за сопротивления отводящей линии. Такие ПК предназначены для установки в линиях с малым сопротивлением на сбросе при постоянном статическом противодавлении, изменение которого не рекомендуется допускать более 10 %;
2)разгруженные ПК (рис. 4.8, г), в которых сила от противодавления не воздействует на золотник на площади, равной площади прохода в седле. Они выполняются с разгрузочным элементом в виде сильфона, мембраны или поршня, предназначены работать в системах
сбольшим и переменным противодавлением.
По высоте подъема замыкающего элемента:
1) малоподъемные пропорционального действия, в которых подъем золотника hmax ≤ 0,05dc. Лимитирующим сечением является щель, образованная между уплотняющими по-
208
верхностями золотника и седла. Малоподъемными обычно выполняют рычажно-грузовые, но также и пружинные ПК. Установка их допускается при небольших расходах, в основном на жидких средах;
2)среднеподъемные, в которых при пропорциональной характеристике h = f (p) благодаря статическому давлению среды на площадь золотника достигается конструктивно огра-
ниченный подъем hmax = (0,083…0,1) dc. Лимитирующим сечением в них является щель. Среднеподъемные ПК применяют преимущественно для жидкостей;
3)полноподъемные (высокоподъемные) двухпозиционного действия, в которых благодаря специальным конструктивным устройствам, способствующим увеличению силы, дейст-
вующей в направлении подъема золотника, достигается высота hmax ≥ 0,25dc (рис. 4.8, г). Лимитирующим сечением в них является самое узкое сечение в седле клапана с диаметром dc. Полноподъемные ПК характеризуются быстротой срабатывания на полный ход золотника. Время их открытия 0,008…0,04 с. Полноподъемными выполняют пружинные клапаны и клапаны непрямого действия.
По характеру подъема замыкающего элемента:
1)клапаны пропорционального действия (рис. 4.8, в), имеющие пропорциональную характеристику подъема h = f (p); в них подъем золотника происходит равномерно, пропорционально повышению давления в системе; применяют их главным образом для жидкостей, а также в системах с непостоянным расходом газа в аварийном режиме;
2)клапаны двухпозиционного действия (рис. 4.8, г). В этих клапанах после небольшого повышения давления золотник рывком поднимается на заданную величину практически без изменения давления среды. Такие клапаны применяют в системах с постоянным расходом газа в аварийном режиме.
По направлению воздействия среды на золотник клапана:
1)клапаны с подачей среды под золотник (рис. 4.8, в–д);
2)клапаны с подачей среды на золотник (рис. 4.8, б). Чувствительным элементом здесь может служить поршень, сильфон или мембрана. При этом иногда седло может быть расположено на подвижном элементе, на который воздействует давление среды.
Клапаны непрямого действия (рис. 4.8, е). Эти ПК подразделяют на следующие типы:
1)импульсно-предохранительные (ИПУ), в которых импульсом для срабатывания привода служит та же рабочая среда, поступающая из импульсного ПК, настроенного на заданное повышение давления;
2)со вспомогательным управлением, в которых осуществляется принудительное открытие от постороннего источника энергии – давления вспомогательной среды (воздух, пар), электромагнита и др.
3)комбинированные клапаны со вспомогательным управлением, аналогичные указанным выше, но в которых главный ПК должен работать так же, как и клапан прямого действия – на случай выхода из строя вспомогательного управления.
Предохранительные мембраны
В зависимости от характера разрушения мембраны подразделяют на следующие типы:
1)разрывные (рис. 4.9, а). Мембраны 1 изготовляют из тонколистового проката и уста-
навливают во фланцевых соединениях при помощи специальных зажимных колец 2, 3. Их выполняют сплошными, с прорезями и с герметизирующей подложкой в виде пленки из кор- розионно-стойкого материала или с вакуумной подложкой;
2)хлопающие (рис. 4.9, б). Мембраны 1 имеют форму сферического купола, выпуклая сторона которого обращена к зоне повышенного давления. При срабатывании купол выворачивается в обратную сторону, ударяется о крестообразный нож 2 и разрушается. Используют для низких давлений. Изготовляют из пластичного материала;
3)ломающиеся (рис. 4.9, в). Мембраны изготовляют из хрупких материалов (чугуна,
графита). Эти ПМ наименее инерционны, поскольку их срабатыванию не предшествует пластическая деформация;
4) срезные (рис. 4.9, а). Мембраны 1 при срабатывании срезаются согласно ГОСТрой
209
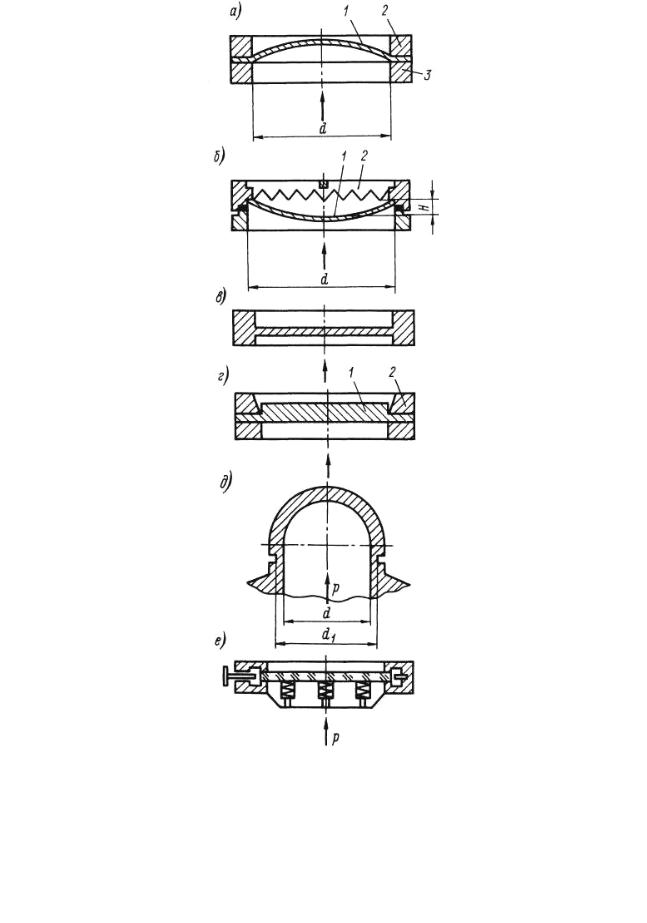
кромке прижимного кольца 2; изготавливаются из мягких материалов. Во избежание деформаций прогиба мембрана имеет утолщение по всей рабочей части. Недостатком является большой разброс давления срабатывания;
Рис. 4.9. Предохранительные мембраны: а – разрывные;
б− г- хлопающие; в – ломающиеся; г – срезные;
д– отрывные; е – специальные
5)отрывные (рис. 4.9, д). Мембраны имеют форму колпачков с ослабленным сечением
ввиде канавки или проточки;
6)специальные. Мембраны выполняются с разрывными стержнями или болтами, с
пружинным механизмом, а также стеклянными с ударным механизмом (рис. 4.9, е) и др. Разрабатывают для условий, не позволяющих использовать типовые конструкции ПМ.
210
4.7.4. Рекомендации по выбору предохранительных устройств
Четкость функционирования ПУ зависит от правильного выбора наиболее подходящих типов для конкретных условий эксплуатации оборудования. Наиболее широкое применение находят пружинные ПК и ПМ. Грузовые и рычажно-пружинные ПК в настоящее время почти не применяют. Рычажно-грузовые клапаны довольно широко распространены в химической, нефтехимической и энергетической отраслях промышленности.
Основным недостатком ПМ является то, что после их срабатывания из аппарата сбрасывается вся находящаяся в нем технологическая среда, так как выходное отверстие в мембране остается открытым до замены разрушенной мембраны. Это ограничивает применение ПМ.
Основным недостатком ПК по сравнению с ПМ является большая их сложность, а следовательно, меньшая надежность в эксплуатации, особенно при работе на средах, склонных к полимеризации, осаждению, кристаллизации; меньшая герметичность затвора, вследствие чего при протечках технологической среды иногда наблюдается примерзание золотника к седлу; большая инерционность действия, что не позволяет использовать ПК для защиты оборудования от взрывов технологической среды.
Указанные недостатки ПК и ПМ могут быть в значительной мере устранены установкой ПК совместно с ПМ, помещаемой перед ПК.
Для защиты аппаратов химических и нефтехимических производств рекомендуется применять пружинные полноподъемные ПК прямого действия.
Предохранительные клапаны других типов целесообразно использовать в следующих случаях:
а) пружинные и рычажно-грузовые мало- и среднеподъемные – для гидравлических систем при небольших или переменных расходах различных сред; при этом рычажногрузовые ПК нельзя применять на установках, подверженных вибрации;
б) разгруженные пружинные ПК – для систем с противодавлением р2 > 0,1рр и с переменным противодавлением;
в) пружинные ПК с подачей давления на золотник – для систем с небольшим аварийным расходом;
г) ПК непрямого действия со вспомогательным управлением – для систем высокого давления, систем с большим аварийным расходом, при высоком требовании к герметичности, для узкого диапазона давлений при открытии, при возможности пригорания или прилипания золотника к седлу.
Кроме того, в химической промышленности существует требование установки пружинных ПК на аппараты, содержащие взрывопожароопасные вещества и вещества, отнесенные к 1-му и 2-му классам опасности согласно ГОСТ 12.1.007–76*, а рычажно-грузовых предохранительных клапанов – на аппараты, содержащие нейтральные среды.
При выборе типа ПМ для защиты конкретного аппарата прежде всего следует исходить из условия максимальной надежности защиты. Наиболее надежными в этом отношении являются предельно простые по конструкции разрывные мембраны.
Предохранительные разрывные мембраны со сплошным куполом рекомендуется применять при возможности резкого повышения давления или взрыва среды в аппарате; при требовании повышенной герметичности аппарата; при рабочих средах, склонных к полимеризации, осаждению, кристаллизации.
Предохранительные мембраны других типов рекомендуется применять в следующих случаях.
Разрывные мембраны с прорезями применяют при отсутствии проката, нужного для изготовления разрывных мембран со сплошным куполом.
Хлопающие мембраны по сравнению с разрывными менее надежны из-за более сложной конструкции и высокой чувствительности даже к незначительным повреждениям (вмятинам) купола. Однако хлопающие мембраны хорошо противостоят знакопеременным на-
211
грузкам, в то время как разрывные мембраны из тонколистового проката таким свойством не обладают. Основная область применения хлопающих мембран – защита от превышения избыточного давления аппаратов, работающих под вакуумом или подвергаемых периодическому вакуумированию. В зависимости от материала мембран существует нижний предел их применения по давлению: мембраны из алюминия – 0,02 МПа, из никеля – 0,03 МПа, из нержавеющей стали – 0,08 МПа.
Ломающиеся мембраны применяют для условий динамических и знакопеременных нагрузок.
Отрывные мембраны применяют для аппаратов и на гидравлических линиях высокого и сверхвысокого давления при небольших диаметрах сбросных отверстий.
Для систем с переменным аварийным расходом, который может резко возрасти в условиях пожара, непредусмотренной химической реакции или взрыва, рекомендуется параллельная установка пружинного ПК и ПМ.
В системах, для которых резкое снижение давления и полный сброс рабочей среды при срабатывании ПМ недопустимы, а использование ПК невозможно по причине забивки его проточной части продуктами полимеризации, рекомендуется последовательная установка ПМ и ПК.
4.7.5. Конструкции предохранительных устройств
4.7.5.1. Предохранительные клапаны
Отечественная промышленность серийно изготовляет пружинные полноподъемные и малоподъемные предохранительные клапаны (ПК), а также рычажно-грузовые малоподъем-
ные [29].
Впружинных ПК замыкающий элемент (золотник) прижимается к седлу пружиной, которая на требуемое давление регулируется винтом. Сила пружины увеличивается с подъемом золотника.
Врычажно-грузовых ПК золотник прижимается к седлу рычагом через шарнирно соединенный с ним шток. На рычаге закреплены грузы, масса которых и место расположения зависят от рабочего давления защищаемого аппарата. Таким образом, усилие на золотник при его подъеме остается постоянным. Рычажно-грузовые ПК предназначены для работы без противодавления. Они выполняются в основном малоподъемными.
Пружинные ПК более совершенны по конструкции, чем рычажно-грузовые, имеют меньшую инерционность при срабатывании, меньшие массу и габаритные размеры.
Современные пружинные полноподъемные двухпозиционные ПК выполняются с седлом
ввиде сопла, свободным корпусом и развитым выходным патрубком. Высокая пропускная способность клапана обеспечивается высоким подъемом золотника, при котором расход среды через клапан ограничивает проходное сечение седла, а не щели. Для достижения высокого подъема используют различные конструктивные устройства, увеличивающие эффективную площадь действия давления среды в направлении подъема, в сочетании с реактивным действием выходящего потока. В лучших современных конструкциях коэффициент расхода приближается к коэффициенту расхода сопла.
На рис. 4.10 приведена конструкция серийно выпускаемых Благовещенским арматурным заводом пружинных полноподъемных фланцевых предохранительных клапанов типа
СППК для жидких и газообразных химических и нефтяных сред.
В ЛенНИИхиммаше проведена унификация и разработана техническая документация на пружинные полноподъемные ПК для компрессорных установок [30] в соответствии с параметрическим рядом, начиная с dc = 5 мм (табл. 4.28). Клапаны обладают высокой пропуск-
ной способностью: их коэффициент расхода α1 = 0,8…0,84 при высоте подъема золотника hmax = 0,4dc. Некоторые компрессоростроительные и другие заводы изготовляют отдельные клапаны из этого ряда для установки на своих машинах и аппаратах.
212

Рис. 4.10. Предохранительные клапаны пружинные фланцевые с рычагом для принудительного открытия и продувки
Таблица 4.28. Клапаны предохранительные пружинные полноподъёмные для газообразных сред [30]
Диаметр |
Эквивалентная площадь клапана Fэ 106, м2, при избыточном давлении ру, МПа |
|||||||
седла dc, |
|
|
|
|
|
|
|
|
0,6 |
1,0 |
1,6 |
4,0 |
10 |
20 |
32 |
||
мм |
||||||||
|
|
|
|
|
|
|
||
5 |
− |
− |
16,1 |
16,1 |
16,1 |
16,1 |
16,1 |
|
6 |
− |
− |
23,8 |
23,8 |
23,8 |
23,8 |
23,8 |
|
8 |
− |
− |
42,3 |
42,3 |
42,3 |
42,3 |
42,3 |
|
10 |
− |
− |
66,0 |
66,0 |
66,0 |
66,0 |
66,0 |
|
12 |
− |
|
95,0 |
95,0 |
95,0 |
95,0 |
95,0 |
|
16 |
− |
169 |
169 |
169 |
169 |
169 |
169 |
|
20 |
264 |
264 |
264 |
264 |
264 |
− |
− |
|
25 |
412 |
412 |
412 |
412 |
412 |
− |
− |
|
32 |
675 |
675 |
675 |
675 |
− |
− |
− |
|
40 |
1050 |
1050 |
1050 |
1050 |
− |
− |
− |
|
50 |
1650 |
1650 |
1650 |
− |
− |
− |
− |
|
60 |
2400 |
2400 |
− |
− |
− |
− |
− |
|
80 |
4260 |
− |
− |
− |
− |
− |
− |
|
100 |
6680 |
− |
− |
− |
− |
− |
− |
4.7.5.2. Предохранительные мембраны
Типовые конструкции. Для наиболее распространенных типов ПМ разработаны типовые конструкции узлов их крепления. В РТМ 6-28-009–82 и монографиях [11, 28] приведены рабочие чертежи узлов и деталей крепления разрывных мембран со сплошным куполом и с прорезями, а также хлопающих мембран. Узлы предназначены для установки в стандартных
213
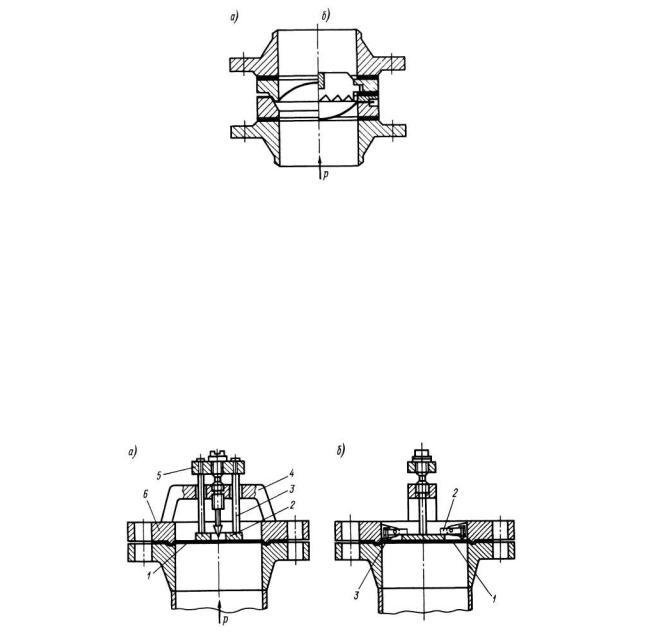
фланцевых соединениях с различными уплотнительными поверхностями: плоскими, коническими, типа шип – паз, выступ – впадина. При установке мембранного узла во фланцевое соединение увеличивается длина стягивающих шпилек. Уплотнение при помощи прокладок между фланцем и зажимным кольцом полностью соответствует уплотнению фланцевого соединения; мембраны между кольцами должны зажиматься без прокладок.
На рис. 4.11, б показана конструкция, а в табл. 4.29–4.31 приведены типоразмеры ряда мембран со сплошным куполом, с куполом и прорезями и хлопающих.
Рис. 4.11. Типовые узлы крепления предохранительных мембран: а – со сплошным куполом и куполом с прорезями; б – хлопающая
Рекомендации по конструированию нетиповых мембранных ПУ: Нетиповые мем-
бранные ПУ рекомендуется применять в тех случаях, когда типовые конструкции нельзя использовать вследствие специфических условий работы защищаемой аппаратуры.
Предохранительные мембраны с разрывным стержнем (рис. 4.12) рекомендуется применять там, где требуется высокая точность срабатывания. Особенностью такого ПУ является то, что элементом, определяющим давление разрушения, является не сама мембрана, а разрывной калиброванный на заданное давление стержень. Мембрана в данном устройстве является разделительной перегородкой, но не рабочим элементом.
В ЛенНИИхиммаше разработаны две модификации: с центральным неподвижным ножом (рис. 4.12, а) и с подвижными ножами, расположенными по периферии мембраны (рис.
4.12, б).
Рис. 4.12. Предохранительные мембраны с разрывным стержнем
Давление в аппарате через мембрану 1 и реверс 2, 3 передается на разрывной стержень, нижний конец которого неподвижно закреплен в бугеле 4, приваренном к корпусу 6, а верхний конец шарнирно связан с траверсой 5 реверса. При повышении давления в аппарате до установочного значения калиброванная часть разрывного стержня разрушается и усилие от давления мгновенно передается мембране, которая при движении напарывается на нож (рис. 4.12, а) и, разрушаясь, раскрывает проходное сечение устройства.
В устройстве с подвижными ножами (рис. 4.12, б) разрушение мембраны происходит на периферии вследствие передачи усилия от движения мембраны через нажимное кольцо реверса на свободные концы коромысел 2, которые, поворачиваясь вокруг неподвижной оси,
214
ножами 3 прорезают мембрану 1.
Таблица 4.29. Типоразмерный ряд разрывных предохранительных мембран [28]
Тип узла |
ру, |
Условный диаметр присоединительного трубопровода Dy, мм |
|||||||||||
|
|
МПа |
25−125 |
150 |
175 |
200 |
225 |
250 |
300 |
350 |
400 |
450 |
500 |
Со |
сплош- |
≤0,6 |
|
|
|
|
|
|
|
|
|
|
|
ным купо- |
1,0 |
|
|
|
|
|
|
|
|
|
|
|
|
|
|
|
|
|
|
|
|
|
|
|
|||
лом |
1,6 |
|
|
|
|
|
|
|
|
|
|
|
|
|
|
|
|
|
|
|
|
|
|
|
|||
|
|
2,5 |
|
|
|
|
|
|
|
|
|
|
|
|
|
4,0 |
|
|
|
|
|
|
|
|
|
|
|
|
|
6,4 |
|
|
|
|
|
|
|
|
|
|
|
|
|
10,0 |
|
|
|
|
|
|
|
|
|
|
|
|
|
16,0 |
|
|
|
|
|
|
|
|
|
|
|
|
|
|
|
|
|
|
|
|
|
|
|
|
|
|
|
20,0 |
|
|
|
|
|
|
|
|
|
|
|
|
|
|
|
|
|
|
|
|
|
|
|
|
|
С |
куполом |
≤0,6 |
|
|
|
|
|
|
|
|
|
|
|
|
|
|
|
|
|
|
|
|
|
|
|||
и |
прорезя- |
1,0 |
|
|
|
|
|
|
|
|
|
|
|
|
|
|
|
|
|
|
|
|
|
|
|||
ми |
|
|
|
|
|
|
|
|
|
|
|
|
|
|
1,6 |
|
|
|
|
|
|
|
|
|
|
|
|
|
|
2,5 |
|
|
|
|
|
|
|
|
|
|
|
|
|
4,0 |
|
|
|
|
|
|
|
|
|
|
|
Таблица 4.30. Типоразмерный ряд хлопающих разрывных мембран с плоскими или коническими зажимами [28]
ру, |
Условный диаметр присоединительного трубопровода Dy, мм |
||||||||
МПа |
50−175 |
200 |
225 |
250 |
300 |
350 |
400 |
450 |
500 |
≤0,6 |
|
|
|
|
|
|
|
|
|
1,0 |
|
|
|
|
|
|
|
|
|
1,6 |
|
|
|
|
|
|
|
|
|
Таблица 4.31. Типоразмерный ряд и диапазон давлений разрушения для мембран конструкции ВНИПИнефть
Диаметр |
Давление разрушения, МПа, для мембран |
|
|
|||
мембраны, |
Из нержавеющей стали |
|
Из никеля |
|
Из монель-металла |
Из титана ВТ1-0 |
мм |
12Х18Н10Т |
|
НП2 |
|
НМЖМц28-2,5-1,5 |
|
|
|
Разрывные мембраны |
|
|||
10 |
20…60 |
|
4…40 |
|
12…60 |
6…60 |
16 |
15…20 |
|
2,5…25 |
|
8…40 |
4…40 |
25 |
10…50 |
|
1,6…16 |
|
5…25 |
3…30 |
32 |
8…40 |
|
1,2…12 |
|
4…20 |
2…20 |
40 |
5…25 |
|
1,0…10 |
|
3…15 |
1,5…15 |
50 |
4…20 |
|
0,8…8 |
|
2,5…12,5 |
1,2…12 |
65 |
3…15 |
|
0,6…6 |
|
2…10 |
1,0…10 |
80 |
2,5…12,5 |
|
0,5…5 |
|
1,5…7,5 |
0,8…8 |
100 |
2…10 |
|
0,4…4 |
|
1,2…6 |
0,6…6 |
125 |
1,5…7,5 |
|
0,3…3 |
|
1,0…5 |
0,5…5 |
150 |
1,2…6 |
|
0,2…2 |
|
0,8…4 |
0,4…4 |
200 |
1,0…5 |
|
− |
|
− |
− |
250 |
0,8…4 |
|
− |
|
− |
− |
300 |
0,7…3,5 |
|
− |
|
− |
− |
350 |
0,6…3 |
|
− |
|
− |
− |
|
|
Хлопающие мембраны |
|
|||
40 |
0,5…5 |
|
0,5…5 |
|
0,5…5 |
0,5…5 |
50 |
0,4…4 |
|
0,4…4 |
|
0,4…4 |
0,4…4 |
215
Продолжение табл. 4.31
Диаметр |
Давление разрушения, МПа, для мембран |
|
|
||
мембраны, |
Из нержавеющей стали |
Из никеля |
|
Из монель-металла |
Из титана ВТ1-0 |
мм |
12Х18Н10Т |
НП2 |
|
НМЖМц28-2,5-1,5 |
|
65 |
0,3…3 |
0,3…3 |
|
0,3…3 |
0,3…3 |
80 |
0,2…2 |
0,2…1,5 |
|
0,2…2 |
0,2…2 |
100 |
0,1…1,5 |
0,1…1,0 |
|
0,1…1,5 |
0,1…1,5 |
125 |
0,08…1,2 |
0,08…1,0 |
|
0,08…1,0 |
0,08…1,0 |
150 |
0,01…1,0 |
0,07…0,8 |
|
0,07…0,8 |
0,07…0,8 |
200 |
0,06 |
− |
|
− |
− |
250 |
0,05 |
− |
|
− |
− |
300 |
0,04 |
− |
|
− |
− |
350 |
0,03 |
− |
|
− |
− |
Заданное разрушающее давление обеспечивается за счет соответствующего выбора мембраны, диаметра и длины калиброванной части разрывного стержня при известных значениях его механических характеристик. Высота положения ножа регулируется в зависимости от типа устройства и диаметра проходного сечения.
Недостатками ПУ с разрывными ножами кроме присущих всем мембранным устройст-
вам являются: малый коэффициент расхода α ≈ 0,58, особенно при малых диаметрах, вследствие перекрытия прохода держателями ножей; при малых установочных давлениях уменьшается точность срабатывания с 2 до 5 %.
Типоразмерный ряд и диапазон давлений разрушения для мембран с разрывным стержнем приведены в табл. 4.32.
Мембранные ПУ, содержащие вакуумную опору, применяют для защиты аппаратов, работающих под вакуумом. Вакуумные опоры делают многократного и одноразового использования.
Таблица 4.32. Типоразмерный ряд и диапазон давлений разрушения для мембран с разрывным стержнем конструкции ЛенНИИхиммаша
Диаметр мембраны, мм |
Давление разрушения, |
Тип мембраны |
|
МПа |
|||
|
|
||
40 |
|
|
|
50 |
0,7…6,4 |
С неподвижным ножом (рис. 4.12, а) |
|
65 |
|||
|
|
||
80 |
|
|
|
100 |
|
|
|
125 |
0,3…4,0 |
|
|
150 |
С подвижным ножом (рис. 4.12, б) |
||
|
|||
200 |
|
||
250 |
0,15…2,5 |
|
|
300 |
0,07…2,5 |
|
|
350 |
|
||
|
|
Так как вакуумные опоры многократного использования значительно снижают пропускную способность мембран, получили распространение опоры разового использования, которые разрушаются вместе с мембраной и полностью освобождают проходное сечение сбросного отверстия. Одна из конструкций такой опоры показана на рис. 4.13. Размеры d и Н должны совпадать с соответствующими размерами разрывной мембраны. Вся рабочая поверхность опоры 1 разрезана на четыре сектора, а для увеличения жесткости опоры при ее работе под вакуумом в центре установлен диск 2, скрепляемый с одним из отогнутых лепестков точечной сваркой, а с остальными тремя – отгибными усиками 3. Для облегчения раскрытия секторов по окружности расположения периферийных отверстий выполнены надре-
216
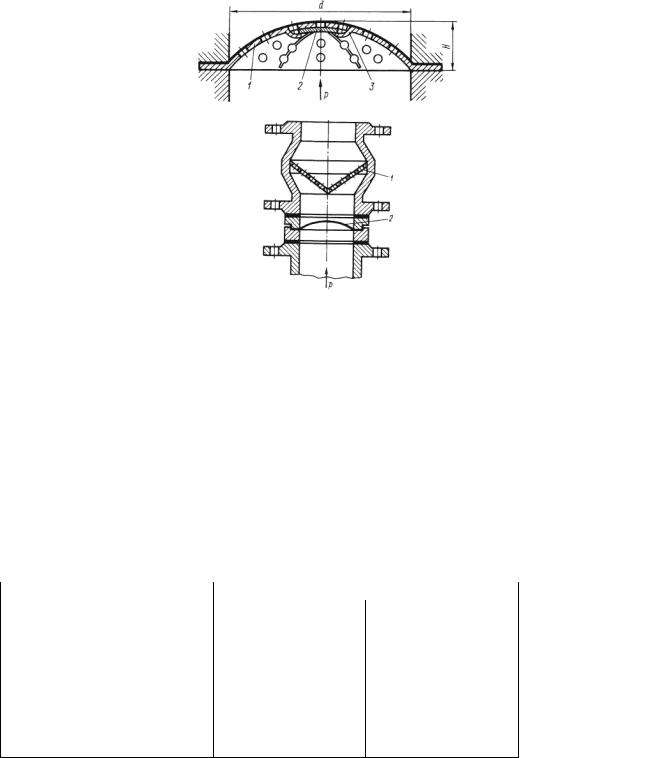
зы.
В тех случаях, когда необходимо обеспечить защиту обслуживающего персонала от разлета осколков при разрушении мембраны или когда мембрану устанавливают перед ПК, в конструкцию мембранного узла вводят устройство для улавливания осколков с плоскими или коническими решетками (рис. 4.14). Решетки 1 устанавливают или в сбросном трубопроводе, или в специальном расширителе; при этом суммарная площадь отверстий в решетке должна быть вдвое больше площади сбросного отверстия мембраны 2. Диаметр отверстий в решетке зависит от величины осколков, которые допускается выбрасывать, и принимается в пределах 3…10 мм. Для предотвращения попадания осколков в защищаемый аппарат рекомендуется устанавливать перед мембраной вторую решетку.
Рис. 4.13. Вакуумная опора одноразового использования
Рис. 4.14. Устройство с коническими решетками для улавливания осколков
В случае защиты от превышения давления аппаратов, в которых рабочие температуры технологической среды превышают указанные в табл. 4.33, в конструкцию мембранных ПУ вводят специальные устройства для их охлаждения. На рис. 4.15, а показана конструкция мембранного узла с тепловой защитой. Материал теплоизолирующего слоя должен быть непрочным, легким и пористым, чтобы давление в аппарате свободно подводилось к мембране, а при ее срабатывании теплоизолирующий материал должен беспрепятственно вылетать вместе со сбрасываемыми газами. Данные о материалах, используемых для теплоизолирующего слоя, приведены в табл. 4.34. В зависимости от рабочего диаметра мембраны d выбирают следующую максимально допустимую высоту насыпного слоя теплоизолирующего материала hсл:
d, мм ≤ 50 |
Св.50 до 100 Св. 100 до 200 |
Св.200до 350Св.350 до 500 |
||
hсл, мм 60 |
90 |
120 |
200 |
220 |
Таблица 4.33. Предельно допустимые температуры для мембран [28] |
|
|||
|
|
|
|
|
Материал |
|
Предельно допустимая температура, °С |
|
|
Нержавеющая сталь |
|
400 |
450 |
|
Никель |
|
400 |
300 |
|
Монель-металл |
|
450 |
300 |
|
Алюминий |
|
120 |
100 |
|
Медь |
|
160 |
160 |
|
Фторопласт1* |
|
200 |
200 |
|
Полиэтилен1* |
|
60 |
60 |
|
Алюминий (фольга)1* |
|
350 |
350 |
|
Свинец (фольга)1* |
|
150 |
150 |
|
Примечание: 1* Данные относятся только к случаю, если материал применяется в качестве защит-
217
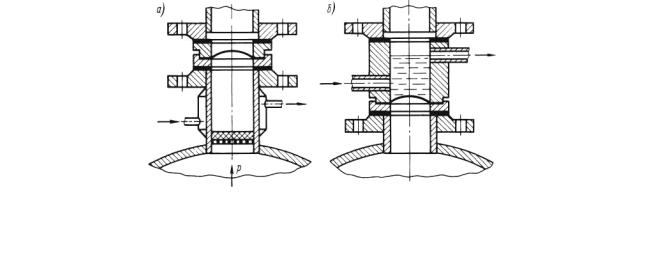
ных покрытий для мембран, изготовленных из других материалов, или в качестве герметизирующих подложек для мембран с прорезями.
Рис. 4.15. Устройства, ограничивающие нагрев предохранительных мембран: а – с теплоизоляционным слоем и охлаждающей рубашкой; б –с непосредственным жидкостным охлаждением мембраны
Таблица 4.34. Материалы для тепловой защиты предохранительных мембран [28]
Наименование |
Состояние материала |
Предельно допускаемая |
|
|
температура, °С |
Асбомагнезит |
Крошка |
350 |
Асбоцемент |
Крошка или сектора |
450 |
Стеклянная вата |
Волокна |
450 |
Совелит |
Порошок |
500 |
Вулканит |
Крошка |
600 |
Асбестодиатомит |
Порошок |
600 |
Картон асбестовый |
Лист |
600 |
Перлит вспученный |
Крошка или сектора |
900 |
Вермикулит вспученный |
Крошка или сектора |
900 |
Перлитокерамика |
Крошка |
900 |
Керамика ячеистая |
Крошка |
900 |
Во избежание травмирования обслуживающего персонала при срабатывании мембранных узлов с тепловой защитой отходящие газы должны сбрасываться в специальную емкость или в специально отведенное место.
Для снижения температуры мембран в ряде случаев целесообразно применять устройства с жидкостным охлаждением подводящего патрубка (рис. 4.15, а) или устройства с непосредственным жидкостным охлаждением (рис. 4.15, б), в которых достигается более эффективное охлаждение мембраны. В последнем случае температура мембраны практически равна температуре охлаждающей жидкости. В устройстве, изображенном на рис. 4.15, б, уровень жидкости над вершиной купола мембраны должен быть в пределах 20…50 мм; его задают соответствующим расположением сливного штуцера. Следует иметь в виду, что при срабатывании мембраны продолжающая поступать через подводящий штуцер охлаждающая жидкость будет попадать в аппарат, поэтому в случае недопустимости такой ситуации данный способ охлаждения мембранного узла неприемлем.
Применение рассмотренных способов снижения температуры мембранных узлов возможно только в тех случаях, когда в защищаемых аппаратах отсутствуют технологические среды, склонные к кристаллизации или полимеризации на охлажденной поверхности подводящего патрубка мембранного узла. В противном случае весь патрубок может быстро полностью заполниться прочными твердыми отложениями.
В химической промышленности при работе с технологическими средами, склонными к образованию различного рода твердых отложений на стенках аппаратов, патрубков и трубопроводов, в том числе к кристаллизации и полимеризации, применяют конструкцию мембранного предохранительного устройства, показанного на рис. 4.16.
218
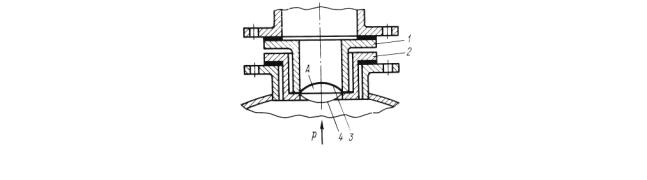
Рис. 4.16. Предохранительное устройство для сред, склонных к образованию на стенках твердых отложений
Зажимные кольца – держатели 1 и 2 – выполнены таким образом, что мембрана утоплена в штуцере и располагается практически в полости защищаемого аппарата, благодаря чему отсутствует глухая полость перед мембраной, способная забиваться отложениями. Мембрана 3 и тонкая защитная пленка 4 выполнены и защищены таким образом, что между ними образуется глухая герметичная полость А. Пленку 4 изготовляют из адгезионного кор- розионно-стойкого материала, например из фторопласта. При достижении в аппарате рабочего избыточного давления пленка 4 деформируется, объем камеры А уменьшается и давление в ней устанавливается равным давлению в аппарате. К тому же весьма эластичная пленка 4, реагируя на колебания давления в аппарате, совершает соответствующие перемещения, что также препятствует образованию на ней каких-либо отложений. При превышении давления в аппарате сверх установленного мембрана и пленка разрываются и происходит сброс среды из аппарата.
Если в защищаемом аппарате содержатся пожаровзрывоопасные газы, то для мембран следует выбирать материал, не образующий искр при разрыве и при ударе осколков о зажимные кольца, о стенки сбросного трубопровода и другие детали. В тех случаях, когда это требование невыполнимо из-за отсутствия необходимых материалов, рекомендуется применять мембранные устройства со сдвоенной мембраной, аналогичные по конструктивному оформлению устройству, показанному на рис. 4.16, а полость А между мембранами заполнять жидкостью, например водой или специальными ингибиторами горения, например хладонами [11].
Испытания на разрушение: Мембраны должны изготовляться специализированным предприятием в соответствии с требованиями РТМ 6-28-009–82. Выпуску каждой партии ПМ должно предшествовать два вида испытаний на разрушение: статистические и контрольные. Статистические испытания проводятся в целях определения гарантируемых пределов возможных отклонений давления срабатывания мембраны данной партии. Контрольные испытания проводятся для контроля партии мембран. Давление срабатывания записывается в акт. При отклонении давления разрушения за пределы минимального и максимального допускаемых давлений вся партия бракуется. Изготовленные мембраны маркируются: указываются рабочий диаметр, пределы давления срабатывания, максимальная температура в месте установки мембраны. На каждую партию оформляется паспорт.
Срок службы мембран. Одной из важных характеристик ПМ является их долговечность. Основные факторы, влияющие на срок службы мембран, следующие: коррозионная стойкость материала в среде защищаемого аппарата; температура; степень нагружения (соотношение между рабочим давлением и давлением срабатывания мембраны); характер нагрузки (статическая, пульсирующая, знакопеременная).
Коррозия мембран недопустима, поэтому материал мембраны следует выбирать из условия его наибольшей коррозионной стойкости в данной среде. В зависимости от скорости коррозии должен определяться срок службы мембран.
В случае необходимости для защиты ПМ от коррозии в ряде случаев целесообразно применять полимерные покрытия из пленки.
Из полимерных материалов наиболее универсальной химической стойкостью обладают фторопласты и пентапласты. Для коррозионной защиты рекомендуется применять только
219
ориентированные фторопластовые пленки, так как неориентированные пористые не обеспечивают требуемую защиту. Пентапласты характеризуются по сравнению с другими термопластами повышенными механической прочностью, теплостойкостью и химической стойкостью. По химической сопротивляемости агрессивным средам пентапласты уступают только фторопластам. Предел рабочей температуры пентапластов 120 °С. Существенной особенностью пентапластов является возможность нанесения покрытия в виде суспензии и лака.
Для защиты ПМ от коррозии можно применять также лакокрасочные покрытия. К химически стойким относятся покрытия на основе перхлорвиниловых, эпоксидных, фторорганических и фенольных смол, а также полиэтилена, сополимера хлорвинила и хлорвинилидена, хлоркаучука и др. Эти лакокрасочные покрытия используют главным образом для защиты от воздействия неконцентрированных кислот, щелочей, растворов солей и промышленных газов.
Для защиты мембран, работающих при высоких температурах, необходимо применять термостойкие лакокрасочные покрытия, руководствуясь следующими рекомендациями таб-
лицы 4.36 [11]:
Таблица 4.36
Рабочая температура мембраны, °С |
Вид термостойкого покрытия |
≤ 100 |
Этилцеллюлозные |
Св. 100 до 150 |
Алкидные на высыхающих маслах |
Св. 150 до 200 |
Алкидные на полувысыхающих маслах, феноломасляные, |
|
полиакриловые и полистирольные |
Св. 200 до 250 |
Эпоксидные |
Св. 250 до 280 |
Поливинилбутиральные |
Св. 280 до 550 |
Поликсилоксановые |
Для защиты мембран от атмосферных воздействий применяют покрытия на основе перхлорвиниловых смол, полиакриловые лаки и эмалевые покрытия, пентафталевые, алкид- но-меламиновые эмали и др. [11].
Температура оказывает существенное влияние на механические свойства мембраны и, следовательно, на давление их срабатывания. С повышением температуры увеличиваются также скорость коррозии и ползучесть металла. Все это приводит к значительному влиянию температуры на долговечность мембран. Для мембран из различных материалов установлены предельные значения температур (табл. 4.34).
Под ползучестью понимают пластическое течение материала под воздействием постоянной нагрузки. Для мембран основными факторами, определяющими ползучесть, являются степень нагружения и температура. Срок службы мембран должен ограничиваться стадией установившейся ползучести, при которой деформация происходит с постоянной скоростью. Стадия ускорения ползучести, оканчивающаяся разрушением металла, для мембран недопустима. В табл. 4.37 приведены предельные значения температур и степени нагружения для мембран из различных металлов. В более тяжелых условиях (по сравнению с указанными в табл. 4.37) срок службы мембран настолько мал, что они становятся практически неработоспособными.
Для мембран, работающих при знакопеременной и пульсирующей нагрузках, характерна усталость металла, которая проявляется в образовании внутренних микротрещин, приводящих к полному разрушению мембраны.
Многие аппараты, защищенные ПМ, работают в режиме повторно-статических нагрузок. В этом режиме работает большинство аппаратов периодического действия. В наиболее трудных условиях работают мембраны на аппаратах, находящихся под давлением или вакуумом, в которых нагрузка изменяется с большой частотой, вследствие чего усталостное разрушение мембран наступает довольно быстро.
Долговечность разрывных мембран, работающих в условиях повторно-статических нагрузок, может быть повышена за счет их предварительного выпучивания. При этом давление
220

выпучивания должно быть несколько выше максимального рабочего давления в защищаемом аппарате [11].
Таблица 4.37. Зависимость предельной степени нагружения (рр/р1)max разрывных мембран от рабочей температуры [28]
Материал |
|
|
(рр/р1)max при рабочих температурах мембраны, °С |
|
|
|||||||||
мембран |
20 |
40 |
60 |
80 |
100 |
120 |
150 |
200 |
250 |
300 |
350 |
400 |
500 |
|
Алюминий |
0,67 |
0,59 |
0,53 |
0,48 |
.0,43 |
0,4 |
− |
− |
− |
− |
− |
− |
− |
|
Медь |
0,77 |
0,74 |
0,71 |
0,69 |
0,67 |
0,63 |
0,60 |
− |
− |
− |
− |
− |
− |
|
Никель |
0,95 |
0,94 |
0,93 |
0,92 |
0,92 |
0,91 |
0,90 |
0,88 |
0,86 |
0,84 |
0,82 |
0,81 |
− |
|
Нержавеющая |
0,91 |
0,90 |
0,89 |
0,88 |
0,88 |
0,86 |
0,85 |
0,83 |
0,82 |
0,81 |
0,79 |
0,78 |
− |
|
сталь |
|
|
|
|
|
|
|
|
|
|
|
|
|
|
Монель- |
0,96 |
0,95 |
0,94 |
0,93 |
0,92 |
0,92 |
0,91 |
0,88 |
0,87 |
0,85 |
0,83 |
0,82 |
0,80 |
|
металл |
||||||||||||||
|
|
|
|
|
|
|
|
|
|
|
|
|
Срок службы мембран в промышленных условиях необходимо определять с учетом всех факторов, влияющих на их работу. Для ориентировочной оценки срока службы разрыв-
ных мембран τ (лет) рекомендуется пользоваться следующей эмпирической зависимостью
[11]:
|
(1 − pр / p1 )2 |
|
t − 20 |
|
|
|
τ = |
|
|
1 − 0,85 |
|
|
(4.6) |
|
|
|||||
|
|
tm − 20 |
, |
|||
|
2(П/S - αпл ) |
|
|
|
где рp/рi – отношение рабочего давления в аппарате к давлению срабатывания мембраны; П – проницаемость (скорость коррозии) материала мембраны в данной технологической среде
при 20 °С, мм/год; S – толщина проката, из которого изготовлена мембрана, мм; αпл – показатель ползучести материала, год −1 (для алюминия αпл = 0,04; для меди αпл = 0,02; для монель-
металла αпл = 0,006; для никеля αпл = 0,007; для нержавеющей стали αпл = 0,005); t – рабочая температура мембраны, °С; tm – предельно допустимая температура для мембран из данного материала, °С (табл. 4.34).
Хлопающие мембраны лучше разрывных сопротивляются длительным нагрузкам, их срок службы при одинаковой степени нагружения примерно в 10 раз больше. Однако это не относится к мембранам из алюминия, работающим в области упругопластических деформаций; срок их службы находится на уровне срока службы разрывных мембран [11]. Для мембран, работающих в области упругих деформаций, срок службы часто определяется коррози-
ей металла. В этом случае срок службы τ (лет) можно определить по формуле
τ = S(1 − |
|
)/ П . |
|
pр / p1 |
(4.7) |
Приведенные формулы для определения срока службы не учитывают всего многообразия факторов, воздействующих на мембрану, поэтому они пригодны лишь для ориентировочной оценки. Более точные данные о сроках службы мембран могут быть получены только экспериментально для конкретных условий их применения.
4.7.5.3. Совместное использование предохранительных клапанов и мембран
Для защиты аппаратов непрерывно действующих химических производств целесообразно устанавливать совместно мембрану и предохранительный клапан. Это позволяет избежать немедленной остановки производства при разрушении мембраны, так как некоторое время аппарат может работать под защитой только предохранительного клапана.
Установленная перед клапаном мембрана в несколько раз увеличивает срок службы клапана, предотвращает забивку затвора клапана продуктами полимеризации и кристаллизации, повышает герметичность защищаемого аппарата.
Следует помнить, что при последовательной установке предохранительной мембраны и
221
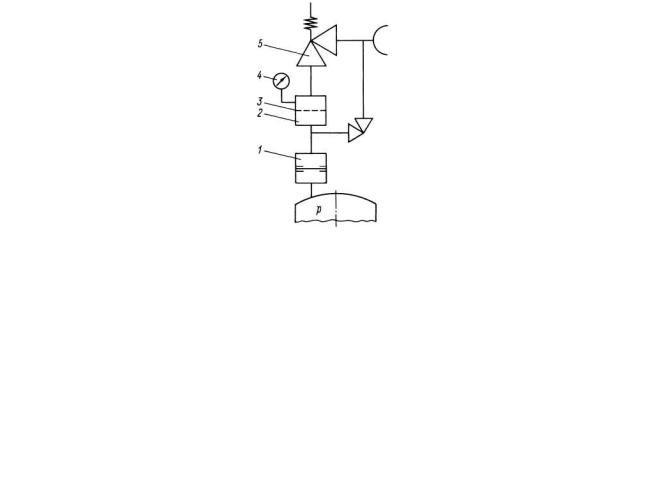
клапана должна быть полностью исключена возможность повышения давления в полости между мембраной и клапаном, так как возникшее противодавление не позволит мембране сработать при заданных параметрах. Поэтому полость между предохранительной мембраной и клапаном соединяют со сбросным трубопроводом перепускной линией с установленным на ней вентилем. Вентиль должен быть постоянно открыт и закрываться только после срабатывания мембраны. Для регистрации срабатывания мембраны устанавливают манометр, а в обоснованных случаях – световую и звуковую сигнализацию.
Схема последовательной установки предохранительной мембраны и клапана приведена на рис. 4.17.
Рис. 4.17. Схема последовательного размещения мембраны и предохранительного клапана: 1 – мембрана; 2 – расширитель; 3 – решетка для улавливания осколков; 4 – манометр; 5 – предохранительный клапан
Отечественной промышленностью выпускается специальная модификация предохранительных клапанов, предназначенных для совместной установки с предохранительными мембранами. Клапаны снабжены устройствами, позволяющими держать золотник в открытом положении до срабатывания мембраны. При срабатывании мембраны и снижении в аппарате давления до рабочих параметров ПК закрывается и работает далее как обычный предохранительный клапан. Характеристика специальных модификаций ПК, выпускаемых Благовещенским арматурным заводом, приведена в табл. 4.38.
Таблица 4.38. Номенклатура предохранительных клапанов для совместной установки с мембранами [28]
Условное обо- |
ру, МПа |
Dy, мм |
Материал |
||
|
уплотняющих |
||||
значение клапана |
корпуса |
||||
|
|
|
|
поверхностей |
|
УФ 55067-050 |
1,6 |
50 |
|
|
|
УФ 55067-080 |
80 |
|
Коррозионно- |
||
УФ 55067-100 |
|
100 |
Сталь 20Л – 25Л |
||
УФ 55068-050 |
4,0 |
50 |
стойкая сталь |
||
|
|||||
УФ 55068-080 |
80 |
|
|
||
УФ 55068-100 |
|
100 |
|
|
|
УФ 55070-050 |
6,4 |
50 |
Сталь |
Твердый сплав |
|
УФ 55070-080 |
80 |
||||
10Х18Н9ТЛ |
|||||
УФ 55070-100 |
|
100 |
|
||
|
|
|
|||
УФ 55071-050 |
6,4 |
50 |
Сталь 20Л – 25Л |
Коррозионно- |
|
УФ 55071-080 |
80 |
||||
стойкая сталь |
|||||
УФ 55071-100 |
|
100 |
|
||
|
|
|
При использовании специальной модификации ПК между ним и ПМ не образуется глухих полостей, а следовательно, не требуется применять устройства, предотвращающие обра-
222
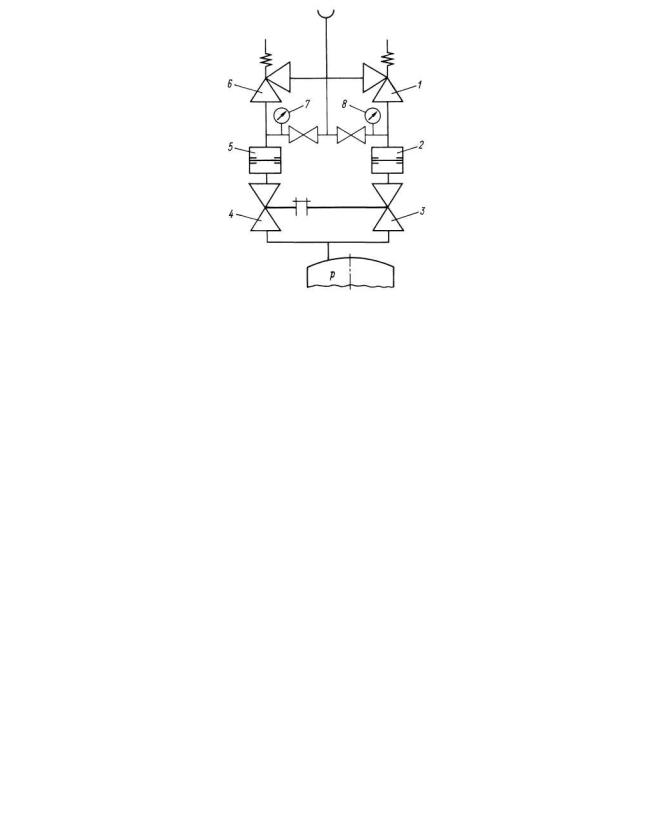
зование противодавления.
Имеются схемы, позволяющие заменять сработавшие мембраны или неисправные клапаны без остановки непрерывного технологического процесса и разгерметизации аппаратов. В этом случае рекомендуется установка спаренных ПУ с переключающей арматурой (рис. 4.18). В качестве переключающей арматуры можно использовать трехходовые краны или вентили, соединенные между собой штоками так, чтобы один из ПУ всегда находился в открытом положении.
Рис. 4.18. Схема установки спаренных предохранительных устройств: 1, 6 – предохранительные клапаны; 2, 5 – мембраны; 3, 4 – сблокированные вентили; 7, 8 – манометры
Мембраны, применяемые для совместной установки с предохранительными клапанами, не должны образовывать осколки, способные повредить уплотняющие поверхности затвора клапана. Для совместной установки с предохранительными клапанами пригодны разрывные мембраны с дисками и хлопающие мембраны с разрезными ножами. В случае использования хлопающей мембраны между нею и клапаном следует устанавливать расширитель с объемом не менее V = 8d3, исключающий образование противодавления при выворачивании купола мембраны.
Для защиты аппаратов, в которых аварийное увеличение давления возможно не только при отказе средств регулирования или повреждении внутренних устройств, но и в случае взрыва паров перерабатываемого продукта, целесообразно применять параллельную установку предохранительных мембран и клапанов.
При параллельной установке предохранительный клапан должен быть отрегулирован на меньшее давление срабатывания, чем предохранительная мембрана. Это исключит срабатывание мембраны во всех случаях, кроме взрыва в аппарате паров перерабатываемого продукта.
4.7.6. Требования к установке и эксплуатации предохранительных устройств
Для защиты аппаратов допускаются только такие ПУ, применение которых разрешено Ростехнадзором. Поставщик должен представить заказчику вместе с ПУ паспорт (сертификат) и инструкцию по эксплуатации.
Пружинные и рычажно-грузовые ПК должны иметь устройство для проверки исправности действия клапана в рабочем со стоянии путем принудительного открывания его во время работы сосуда при давлении не менее 80 % от рабочего давления. Допускается установка ПК без приспособления для принудительного открывания, если последнее недопустимо по свойствам среды (чрезвычайно вредная, взрывоопасная и т. д.) или по условиям технологического процесса. В этом случае клапаны следует проверять периодически в сроки, ус-
223
тановленные технологическим регламентом, но не реже одного раза в 6 месяцев при условии исключения возможности примерзания, прикипания или забивки клапана рабочей средой
[26].
Массу груза и длину рычага рычажно-грузового ПК следует выбирать так, чтобы груз находился на конце рычага. Отношение плеч рычага не должно превышать 10 : 1. Если применяется груз с подвеской, то их соединение должно быть неразъемным. Масса груза не должна превышать 60 кг и должна указываться на поверхности груза.
Предохранительные клапаны, открывающиеся с помощью электроэнергии, должны быть снабжены двумя независимыми друг от друга источниками питания. Установка запорных устройств на импульсных линиях не допускается.
Предохранительные устройства должны устанавливаться на патрубках или трубопроводах, непосредственно присоединенных к аппарату, в местах, доступных для их осмотра, по возможности в вертикальном положении колпачком вверх.
При установке на одном патрубке (трубопроводе) нескольких ПУ площадь поперечного сечения патрубка (трубопровода) должна быть не менее 1,25 суммарной площади сечения патрубков ПУ, установленных на нем. Отбор рабочей среды из патрубков и на участках присоединительных трубопроводов от сосуда до ПУ не допускается. Внутренний диаметр подводящего трубопровода следует рассчитывать на максимальную пропускную способность ПУ.
Падение давления в трубопроводе при использовании ПК прямого действия не должно превышать 3 % от давления настройки ПК, но диаметр должен быть не менее максимального внутреннего диаметра подводящего патрубка клапана.
Вподводящих трубопроводах к ПУ допускается падение давления свыше 3 % при условии, что повышенное сопротивление не приведет к снижению пропускной способности ПУ ниже заданных значений.
Внутренний диаметр отводящего трубопровода должен быть рассчитан так, чтобы при расходе, равном максимальной пропускной способности ПУ, противодавление в его выходном патрубке не превышало максимально допустимого противодавления, но диаметр не должен быть менее наибольшего внутреннего диаметра выходного патрубка ПУ.
Вслучае объединения сбросных трубопроводов от нескольких ПУ, установленных на одном аппарате, сечение коллектора должно быть не менее суммы сечений сбросных трубопроводов от этих клапанов и давление в выходном патрубке не должно превышать величину, установленную заводом-изготовителем.
При определении пропускной способности ПУ необходимо учитывать гидравлическое сопротивление подводящих и отводящих трубопроводов.
Втрубопроводах ПУ должна быть обеспечена необходимая компенсация температурных удлинений. Крепление корпуса ПК и трубопроводов должно быть рассчитано с учетом статических и динамических усилий, возникающих при срабатывании клапанов.
На подводящих и отводящих трубопроводах установка запорных устройств не допуска-
ется.
Допускается установка между аппаратом и ПК трехходовых и других устройств, исключающих возможность одновременного отключения всех ПК. При отключении одного или нескольких ПК остальные должны обеспечивать необходимую пропускную способность. Если расчетное давление в аппарате равно или больше давления питающего его источника и
ваппарате исключается возможность повышения давления от химической реакции или обогрева, то установка на нем предохранительных клапанов не обязательна при наличии их на источнике давления.
Предохранительные клапаны должны регулироваться на давление настройки. Следует учитывать, что клапаны типа СППК4 открываются полностью, если давление превышает давление настройки на 10 %.
На аппаратах непрерывно действующих производств допускается устанавливать рабочий и резервный ПК. Рабочий и резервный клапаны должны устанавливаться на отдельных
224
присоединительных патрубках, иметь одинаковую пропускную способность и обеспечивать в отдельности полную защиту аппарата от превышения давления. Допускается установка на аппараты рабочих и резервных клапанов с использованием переключающего устройства при условии, что в любом положении переключающего устройства с аппаратом будут соединены оба или один ПК.
Для уменьшения, случаев выброса через рабочие ПК в атмосферу аппараты, содержащие взрывоопасные газы и вещества, отнесенные к 1-му и 2-му классам опасности согласно ГОСТ 12.1.007–76*, должны иметь две системы ПК: рабочую – со сбросом в атмосферу; контрольную – со сбросом в закрытую систему (на улавливание или сжигание).
Давление начала открытия контрольных ПК должно быть меньше давления начала открытия рабочих клапанов и не должно превышать расчетное давление в аппарате.
Для аппаратов, работающих под давлением до 10 МПа в производствах нефтехимической и нефтеперерабатывающей промышленности, рекомендуются следующие значения
давлений настройки рн ПК: для рабочих клапанов рв ≤ pR; для контрольных клапанов: при pR
≤ 6,0 МПа рн ≤ 0,9рв, но не менее чем на 0,15 МПа меньше рR; при pR > 6,0 МПа рн ≤ 0,89рR. Рабочие и контрольные ПК в отдельности должны обеспечивать полную защиту аппа-
рата от превышения давления. Для отключения контрольных клапанов на ремонт и ревизию допускается установка запорной арматуры до и после этих клапанов.
Если источником повышения давления является быстро отключаемый агрегат (компрессор, насос, нагревательный элемент), допускается вместо контрольных клапанов применять защитную блокировку, отключающую источники давления при достижении параметров, соответствующих началу открытия контрольных ПК. Защитная блокировка не может быть использована в случае, если источником повышения давления является неуправляемая химическая реакция.
Применение контрольных ПК обязательно на аппаратах, пред назначенных для хранения сжиженных газов и жидкостей с температурой кипения менее 45 °С.
Предохранительные устройства должны устанавливаться с таким расчетом, чтобы в первую очередь из аппаратов удалялась парогазовая фаза. На вертикальных аппаратах ПУ устанавливаются на верхних днищах или в местах наибольшего скопления паров и газов. Исключение составляют аппараты колонного типа с числом тарелок более 40. В таких аппаратах в целях исключения значительной разности давлений между верхней и кубовой частями ПУ устанавливают в кубовой части аппарата. Размещение ПУ в верхней части аппаратов колонного типа допускается при условии регулирования их на давление настройки (клапана), определенное с учетом сопротивления внутренних устройств и возможного увеличения сопротивления в процессе эксплуатации. На горизонтальных цилиндрических аппаратах ПУ устанавливают по длине верхней образующей.
Технологическая среда, сбрасываемая через ПУ, должна отводиться в безопасное ме-
сто.
Сбросные трубопроводы, отводящие газ от ПУ, должны быть защищены от замерзания и иметь устройство для непрерывного отвода конденсата, а при сбросе в атмосферу – защиту от попадания в них атмосферных осадков. В наиболее низкой точке сбросного трубопровода должно быть предусмотрено дренажное устройство для спуска накопившейся жидкости. Если при срабатывании ПУ вместе с газом возможен унос жидкости, то подводящий трубопровод должен иметь уклон в сторону защищаемого объекта, а на сбросном трубопроводе должен быть предусмотрен сепаратор (отбойник). В этом случае сбросный трубопровод должен прокладываться с уклоном не менее 0,002.
Пары и газы, направляемые от ПУ в факельную систему, должны иметь температуру не более 200 °С, а температура газа на входе в газгольдер не должна превышать 60 °С.
Газы, содержащие более 8 % сероводорода, должны отводиться для сжигания в факел по специальному трубопроводу. Рекомендации по отводу сбросов от рабочих и контрольных ПК приведены в табл. 4.39.
225
Таблица 4.39. Рекомендации по отводу сбросов от предохранительных устройств
Отводимое вещество |
|
|
Сброс |
||
|
|
от рабочего клапана |
от контрольного клапана |
||
|
|
|
|
||
Вода — чистая или загрязнен- |
В промышленную канализа- |
Не требуется |
|||
ная углеводородами |
|
|
цию |
|
|
Вода, |
содержащая |
прочие |
В химически загрязненную ка- |
Не требуется |
|
вредные химические вещества |
нализацию |
|
|||
Воздух, водяной пар, инертный |
В атмосферу через стояк |
Не требуется |
|||
газ |
|
|
|
|
|
Газ с объемным содержанием |
В атмосферу в безопасное ме- |
Не требуется |
|||
водорода 60 % и выше |
|
|
сто |
|
|
Углеводородные пары |
и |
газы |
В атмосферу в безопасное ме- |
В закрытую систему на улав- |
|
(при установке двух систем |
сто |
ливание или сжигание в факеле |
|||
клапанов) |
|
|
|
|
|
Жидкие |
углеводородные |
про- |
В дренажную емкость с отво- |
Не требуется |
|
дукты |
|
|
|
дом паров из нее через конден- |
|
|
|
|
|
сатор в атмосферу |
|
Углеводородные газы |
и |
пары |
Через сепаратор (отбойник) и |
В закрытую систему на улав- |
|
ПВЖ с температурой кипения |
стояк в атмосферу |
ливание или сжигание в факеле |
|||
до 45 °С (на складах хранения) |
|
|
|||
Сероводород (при установке |
Через сепаратор поглощения в |
На установку сероочистки или |
|||
двух систем клапанов) |
|
|
атмосферу |
на сжигание в факеле |
|
Аммиак в газовой фазе |
|
|
Через стояк в атмосферу * |
Не требуется |
|
Жидкие углеводороды в смеси |
|
|
|||
с фенолом, крезолом, фурфу- |
|
|
|||
ролом: |
|
|
|
В емкость. Из емкости пары |
Не требуется |
при t ≤ 100 °С |
|
|
|||
|
|
|
|
выводят через стояк в атмо- |
|
|
|
|
|
сферу |
|
при t > 100 °С |
|
|
В емкость. Из емкости пары |
Не требуется |
|
|
|
|
|
после охлаждения выводят че- |
|
|
|
|
|
рез стояк в атмосферу |
|
Примечание: * Сброс аммиака в атмосферу допускается только при соответствующих обоснованиях. В остальных случаях следует предусматривать систему его поглощения.
Предохранительные клапаны и сбросные трубопроводы должны быть закреплены так, чтобы ими надежно воспринимались силы реакции от массы газа или пара, вытекающего с большой скоростью при быстром открытии предохранительного устройства. Недоучет при проектировании клапанов и опорных конструкций больших реактивных сил, воздействующих на корпус клапана и сбросные трубопроводы, может привести к изгибу отводящих трубопроводов во время срабатывания ПУ, отрыву клапанов и трубопроводов и возникновению аварийной ситуации.
Для уменьшения усилий на опоры следует стремиться к увеличению сечения сбросных трубопроводов и исключению в них поворотов.
Трубопроводы сброса среды из мембранных ПУ также должны иметь надежные крепления, чтобы разгрузить ПУ от дополнительных усилий – реактивных сил и весовых нагрузок. Присоединительные патрубки на аппарате должны иметь большую жесткость.
При расчете усилий, действующих на корпус ПК и опоры отводящих трубопроводов, должны учитываться реактивные силы от сбрасываемой среды.
Предохранительные клапаны перед установкой на аппарат должны быть отрегулированы на давление настройки и проверены на плотность затвора и разъемных соединений.
Установленные на аппараты ПК в зависимости от применяемой среды должны проходить ревизию в следующие сроки:
1) на технологических аппаратах со сжатым воздухом, инертным газом, водяным паром
226

независимо от их температуры, а также на аппаратах с неагрессивными, незагрязненными и неполимеризующимися средами при температуре до 250 °С – не реже одного раза в 12 месяцев;
2)на технологических аппаратах с неагрессивными, незагрязненными и неполимеризующимися средами при температуре выше 250 °С – не реже одного раза в 6 месяцев;
3)на технологических аппаратах с агрессивными, загрязненными и полимеризующимися средами, сжиженными газами, а также на аппаратах с температурой процесса более 250 С°, при ко торой возможно коксование продукта, – не реже одного раза в 3 месяца;
4)на складских емкостях сжиженных газов – не реже одного раза в 4 месяца. Изменение сроков ревизии ПК допускается по разрешению руководителя предприятия,
их эксплуатирующего, на срок не более трех месяцев при условии предварительного обследования этих клапанов специальной комиссией.
4.7.7.Расчет сил, действующих на крепления предохранительных клапанов
итрубопроводов
На узлы крепления и опоры предохранительных клапанов и трубопроводов действуют силы: сила давления среды; реактивные силы при стационарном течении, возникающие вследствие изменения направления потока газа при поворотах трубы и вследствие вытекания с большой скоростью массы газа из выходного сечения сбросного трубопровода; сила ударной волны при мгновенном открытии клапана (здесь не рассматривается) и вес клапана и трубопроводов.
В соответствии с рис. 4.19 сила, обусловленная давлением внутри трубы и изменением направления потока при установившемся движении, действует на криволинейный участок трубы (считается, что в месте изгиба трубы давление и скорость равны таковым в выходном сечении трубы)
P = [(p2к + 0,1)106 Fтр2 |
+ ma wвых2 |
] |
1 − cosα |
|
, |
(4.8) |
|
sin(α/ 2) |
|||||||
|
|
|
|
|
где р2к – давление в колене, МПа; Fтр2 – площадь сечения трубы, м2; ma – расход среды, кг/с; wвых2 – скорость потока в выходном трубопроводе, м/с; α - угол установки колена.
Рис. 4.19. Схема предохранительного клапана с отводящим трубопроводом
При скорости потока, равной скорости звука (wвых2 = wзв2), |
|
|
||||||
P = [(p2к + 0,1)106 Fтр2 |
+ k2к |
(p2к + 0,1)106 Fтр2 |
] |
1 − cosα |
|
, |
(4.9) |
|
sin(α/ 2) |
||||||||
|
|
|
|
|
|
где k2к (p2к + 0,1) 106Fтp2 = ma wзв2.
227
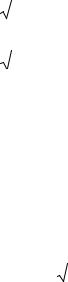
При повороте трубы на угол α = 90° формула (29) преобразуется следующим образом:
P |
|
= |
|
|
[(p2к + 0,1)106 Fтр2 |
+ ma wвых2 ], |
|
||||||
0 |
2 |
(4.10) |
|||||||||||
90 |
|
|
|
|
|
|
|
|
|
|
|
|
|
и формула (30) при wвых2 = wзв2 |
примет вид |
|
|||||||||||
P |
|
= |
|
(1 + k |
|
|
)(p |
|
+ 0,1)106 F |
|
|
||
0 |
2 |
2 |
к |
2к |
. |
(4.11) |
|||||||
90 |
|
|
|
|
|
|
|
тр2 |
|
|
Сила реакции при установившемся истечении среды из выходного сечения трубы
R = (p |
2 |
к |
− p |
)106 F |
|
+ m |
w |
вых2 |
− m |
w |
2 |
. |
(4.12) |
||||||||||
|
|
2 |
|
|
тр2 |
|
|
|
|
a |
|
|
a |
|
|
|
|
||||||
При выбрасывании газа в атмосферу р2 = 0 и w2 = 0, тогда |
|
||||||||||||||||||||||
R = (p |
2 |
к |
− 0)106 F |
|
+ m |
w |
вых2 |
. |
|
|
|
|
|
(4.13) |
|||||||||
|
|
|
|
тр2 |
|
|
|
|
a |
|
|
|
|
|
|
|
|
|
|||||
При wвых2 = wзв2 |
|
|
(p |
|
|
+ 0,1)106 F |
|
|
|
|
|
||||||||||||
R = p |
2 |
к |
106 F |
|
+ k |
2к |
2 |
к |
|
. |
|
(4.14) |
|||||||||||
|
|
тр2 |
|
|
|
|
|
|
|
|
|
тр2 |
|
|
|
|
Горизонтальные Рх и Rx и вертикальные Ру и Ry составляющие, действующие на коленья, выполненные под углом α = 90°,
Px = Py = P900 |
|
/ 2; Rx = 0; Ry = R . |
|
2 |
(4.15) |
Полная вертикальная составляющая, действующая на опору трубопровода, равна
V = R + Ру. |
(4.16) |
В случае отсутствия опоры эта сила создает изгибающий момент Mv = Vlv, действующий в месте закрепления входного патрубка перед клапаном.
От горизонтальной составляющей Рх на присоединительный патрубок действует изгибающий момент Мх = Pxl.
Учитывая динамическое действие реактивных сил при срабатывании клапана или разрыве мембраны, вызывающих увеличенную или колеблющуюся нагрузку, при расчете на прочность вводят динамический коэффициент Кл = 1,5, увеличивающий расчетное усилие.
Вформулах (4.8) – (4.16) давление – избыточное, в МПа, площадь сечения трубы Fтp2 –
вм2, длины lv и l – в м, сила – в Н, расход среды mа – в кг/с, скорость – в м/с.
Уменьшения реактивных сил от вытекающего потока на конце сбросного трубопровода можно достигнуть разветвлением выходного конца (штриховые линии на рис. 4.19). В этом случае силы реакции R в выходных сечениях уравновешиваются.
4.8. Герметизация аппаратов
4.8.1. Общие требования к герметичности аппаратов
Аппараты, содержащие взрывоопасные, пожароопасные и вредные вещества, должны быть герметичны по отношению к внешней среде. Основные характеристики взрыво- и пожароопасности веществ приведены в табл. 6.1 и 6.7.
Согласно ГОСТ 12.1.007–76*, все вредные вещества в зависимости от их действия на организм человека разделены на четыре класса опасности.
1-й класс – вещества чрезвычайно опасные;
2-й класс – вещества высокоопасные;
3-й класс – вещества умеренно опасные;
4-й класс – вещества малоопасные.
Предельно допустимые концентрации вредных веществ в воз духе рабочей зоны по классам опасности приведены в табл. 8.1 и 8.2. Для веществ, не указанных в табл. 8.1 и 8.2, классы опасности устанавливают специализированные медицинские организации по показателям, предусмотренным в ГОСТ 12.1.007–76*.
4.8.2. Уплотнение валов аппаратов
Для обеспечения требуемой герметичности аппаратов в местах выхода валов наиболее
228
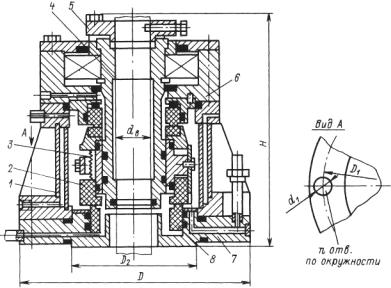
широкое применение нашли торцовые и сальниковые уплотнения [18, 19].
Торцовые уплотнения (рис. 4.20) позволяют практически полностью предотвратить утечки рабочей среды из аппарата или попадание воздуха внутрь аппарата.
Рис. 4.20. Торцовое уплотнение типа Т4:
1 – корпус; 2 – подвижное кольцо: 3 – пружина; 4 – втулка; 5 – водило; 6 – крышка; 7 – неподвижное кольцо; 8 – уловитель
Для уплотнения валов вертикальных аппаратов, содержащих взрывоопасные, пожароопасные и вредные среды, наибольшее применение нашли торцовые уплотнения типа Т4 (табл. 4.40). Не рекомендуется применять уплотнения типа Т2 для аппаратов, содержащих взрывоопасные, пожароопасные и вредные среды при избыточном давлении. Уплотнения типа Т1 применяют в аппаратах, где требуется стерильность технологического процесса, например в биохимическом производстве.
Таблица 4.40. Основные размеры торцовых уплотнений типа Т4, ОСТ 26-01-1243 – 81 [18] (рис. 4.20)
|
dв |
D |
D1 |
D2 |
Н, не |
D1 |
|
|
Масса, |
Типоразмер |
более |
|
n |
кг, не бо- |
|||||
|
мм |
|
|
|
|
|
|
|
лее |
Т4-50-25 |
50 |
270 |
240 |
165 |
155 |
|
18 |
|
85 |
Т4-60-25 |
60 |
|
|
||||||
|
|
|
|
|
|
|
|
||
Т4-80-25 |
80 |
330 |
280 |
195 |
365 |
|
27 |
12 |
110 |
Т4-95-25 |
95 |
|
|||||||
|
|
|
|
|
|
|
|||
Т4-110-25 |
110 |
360 |
310 |
225 |
375 |
|
|
|
150 |
Т4-130-25 |
130 |
395 |
340 |
400 |
|
30 |
|
175 |
|
|
|
|
Примечания: 1. В обозначении типоразмера цифры после первого дефиса – диаметр уплотняемого вала, мм, цифры после второго дефиса – рабочее давление в аппарате, кгс/см2. После цифр могут помещаться дополнительные буквы, обозначающие исполнение по материалу металлических деталей и сборочных единиц, соприкасающихся с рабочей средой (К – сталь 12Х18Н10Т; КЕ – сталь 10Х17Н13М2Т; КН – сплав 06ХН28МДТ; Т – титан ВТ-1-0).
2. Уплотнения на расчетное давление 3,2 МПа изготовляются по специальному заказу с размерами, соответствующими основным размерам и другим рабочим параметрам уплотнений на давление
2,5 МПа.
Радиальное и угловое биения вала аппарата в зоне торцового уплотнения, а также смещения неподвижных деталей корпуса уплотнения относительно оси вала не должны превышать 0,2 мм и 0,25° соответственно.
Потери расчетной мощности на дополнительные осевые усилия и трение при наиболь-
229

шей скорости вращения вала аппарата определяют по рис. 4.21.
Рис. 4.21. Потери мощности на трение в торцовом уплотнении:
1 – уплотнения типов Т3, Т4, Т5, Т6, Т7 и Т8; 2 – уплотнения типов Т1 и Т2
При установившемся режиме работы торцового уплотнения допускаются следующие утечки жидкости через пару трения со стороны большего давления:
Диаметр вала, мм. |
40 |
50 |
65 |
80 |
95 |
110 |
130 |
Утечки, см3/ч |
4 |
5 |
6,5 |
8 |
9,5 |
11 |
13 |
При неподвижном вале утечки жидкости, а также газовой среды в виде пузырьков не допускаются.
Работоспособность торцовых уплотнений обеспечивается правильным выбором схемы подачи запирающей жидкости, которая одновременно обеспечивает охлаждение и смазку деталей уплотнения. Для уплотнений типов Т1 и Т2 допускается подача уплотняющей жидкости наливом без дополнительных устройств. Для двойных торцовых уплотнений типов Т3, Т4, Т5, Т6, Т7, Т8, Т9 должны применяться схемы с естественной или принудительной циркуляцией запирающей жидкости.
Схему обвязки с естественной циркуляцией запирающей жидкости (рис. 4.22, а) рекомендуется применять при работе уплотнения в следующих условиях: частота вращения вала
до 5 с-1; температура рабочей среды в аппарате от –30 до +150 °С.
Рис. 4.22. Схемы обвязки торцовых уплотнений:
а - с естественной циркуляцией запирающей жидкости; б - с принудительной циркуляцией запирающей жидкости: 1 – камера торцевого уплотнения; 2 – теплообменник; 3 – фильтр; 4 – пневмогидроаккумулятор; 5 – бак; 6 – воронка; 7 – манометры; 8 – запорная аппаратура; 9 – регулирующий
клапан; 10 − насос; 11 − обратный клапан
Давление запирающей жидкости поддерживается за счет давления в аппарате, если среда не вредная и не взрывоопасная, или за счет подачи азота под давлением при взрыво-
230
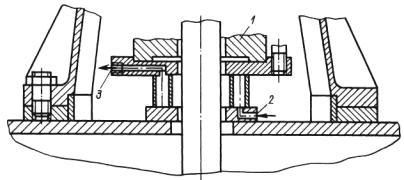
опасной и токсичной среде. Запирающая жидкость циркулирует в замкнутом контуре вследствие разности плотностей нагретых и охлажденных слоев жидкости на разных уровнях. Для лучшей циркуляции холодильник и пневмо-гидроаккумулятор следует устанавливать в непосредственной близости от уплотнения на высоте не менее 2 м.
Схему обвязки с принудительной циркуляцией уплотняющей жидкости (рис. 4.22, б) рекомендуется применять при диаметре уплотняемого вала более 80 мм, частоте вращения
не менее 5 с-1 и температуре рабочей среды в аппарате до 150 °С. Запирающая жидкость подается в уплотнение специальным насосом или централизованно из общей магистрали. Для сглаживания пульсации давления и поддержания работоспособности уплотнения при кратковременных остановках насоса в схему обвязки включен ресивер.
В целях повышения надежности работы торцовых уплотнений при температуре среды в аппарате более 150 °С следует устанавливать дополнительное охлаждающее устройство (рис.
4.23).
Рис. 4.23. Охлаждающее устройство:
1 − корпус торцового уплотнения: 2 – вход охлаждающей жидкости; 3 - выход охлаждающей жидкости
Вкачестве запирающей жидкости применяют обессоленную воду, масло или другие жидкости, химически совместимые с рабочей средой, но не вредные и не взрывоопасные. Температура запирающей жидкости на выходе из уплотнения типа Т1 не должна превышать 140 °С, для остальных типов – не более 80 °С. Давление запирающей жидкости должно быть выше давления среды в аппарате на 0,05…0,1 МПа.
Максимальное давление в камере уплотнения при отсутствии давления в аппарате не должно превышать следующих значений: 0,45 МПа – для уплотнений типов Т3 (с давлением 0,6 МПа), Т5 и Т6; 0,85 МПа – для уплотнений типов Т3 (с давлением 3,2 МПа) и Т4.
Вуплотнениях типов Т1 и Т2, а также при остаточном давлении в аппарате запирающая жидкость должна подаваться в камеру уплотнения при атмосферном давлении.
Направление вращения вала не влияет на работоспособность торцовых уплотнений, за исключением уплотнений типа Т1, для которых направление вращения вала следует принимать по часовой стрелке (со стороны привода).
Сальниковые уплотнения (рис. 4.24) устанавливаются на аппараты, содержащие нейтральные среды или вещества, отнесенные к четвертому классу вредности. Применение сальниковых уплотнений для аппаратов, содержащих вредные вещества, отнесенные к первому – третьему классам опасности, допускается при условии наличия паров этих веществ над поверхностью жидкости в аппарате в количестве, не превышающем предельно допустимые концентрации. Применение сальниковых уплотнений для аппаратов, содержащих взрывоопасные вещества, не рекомендуется.
231
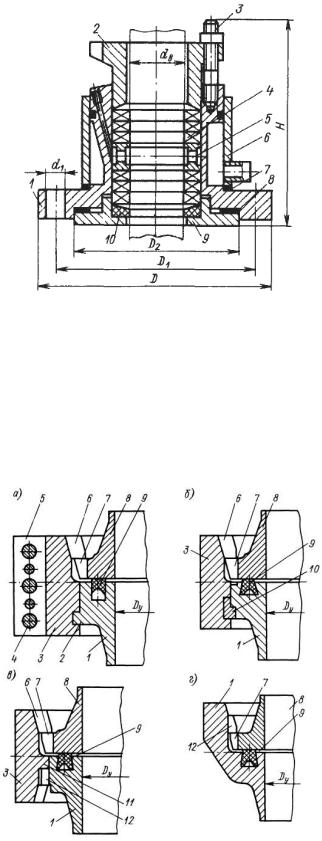
Рис. 4.24. Сальниковое уплотнение с охлаждением корпуса и подводом смазывающей или уплотняющей жидкости к валу: 1 – корпус; 2 – нажимная втулка; 3 – шпилька с гайкой; 4 – набивка; 5 – фонарь; 6 – рубашка; 7, 8 – прокладки: 9 – опорное кольцо; 10 – кольцо
4.8.3. Уплотнение байонетных затворов
Внастоящее время наиболее широкое распространение получили байонетные затворы
сцельным байонетным кольцом, с разъемным байонетным кольцом, а также двусторонние байонетные затворы и затворы с поворотной крышкой. Их конструкции приведены на рис. 4.25. Применение байонетных затворов позволяет резко сократить время, необходимое для загрузки и выгрузки из аппаратов перерабатываемых веществ и материалов.
Рис. 4.25. Конструкции байонетных затворов: а – с разъемным байонетным кольцом; б – с цельным байонетным кольцом; в – двусторонний байонетный затвор; г – с байонетной крышкой;
1 – фланец корпуса; 2 – упорный бурт фланца корпуса; 3 – байонетное кольцо; 4 – стяжные болты байонетного кольца; 5 – фланцы байонетного кольца; 6 – впадины байонетного кольца; 7 – выступы на фланце байонетной крышки; 8 – фланец байонетной крышки; 9 – резиновый уплотнитель; 10 – промежуточное разрезное кольцо; 11 – упорный бурт байонетного кольца; 12 – выступы на байонетном фланце корпуса
232
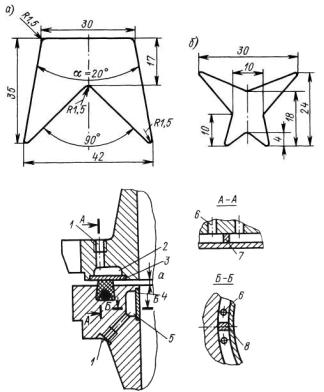
Работоспособность байонетных затворов в значительной степени зависит от надежности уплотняющих устройств.
В качестве уплотняющих устройств для байонетных затворов рекомендуется применять резиновые уплотнители [14, 16], показанные на рис. 4.26. Однако резиновые уплотнители в нормальных условиях работы могут применяться только до температуры 140 °С. В случае необходимости использования байонетных затворов при температурах до 250 °С следует предусматривать защиту резиновых уплотнителей от действия высоких температур. С этой целью применяют охлаждение пазов под резиновые уплотнители, расположенные во фланцах корпуса и крышки аппарата (рис. 4.27).
Рис. 4.26. Резиновые уплотнители: а – типа а; б – типа б
Рис. 4.27. Схема системы охлаждения уплотнителя:
1 – отверстие для подвода охлаждающей жидкости; 2, 5 – охлаждающие каналы; 3, 4 – кольца, закрывающие охлаждающие каналы; 6 – отверстие для отвода охлаждающей жидкости; 7, 8 – перегородки
Для обеспечения надежной герметичности байонетного затвора под резиновым уплотнителем должно поддерживаться избыточное давление.
При использовании в аппаратах в качестве рабочей среды воды, воздуха, масла, водяного пара и инертных газов герметичность затвора в начальный период пуска обеспечивается подачей давления под уплотнитель от автономного источника, а при достижении в аппарате избыточного давления 0,2…0,3 МПа уплотняющее устройство соединяется с внутренним пространством аппарата (рис. 4.28, а).
В аппаратах, работающих с агрессивными, вредными, взрыво- и пожароопасными средами, соединение внутренней полости аппарата с уплотняющим устройством недопустимо. В этом случае давление под уплотнителем создается от автономного пневматического или гидравлического источника, оно должно превышать рабочее давление в аппарате на
0,05…0,1 МПа (рис. 4.28, б).
233

Рис. 4.28. Схемы устройства для создания давления под уплотнителем: а – с промежуточным резервуаром; б – без промежуточного резервуара; 1 – трубопровод, соединяющий резервуар с уплотнением затвора;
2 – контрольныйкран; 3 – манометр; 4 – смотровое стекло; 5 – резервуар; 6 – воронка или заменяющий ее трубопровод; 7 – предохранительный клапан; 8 – коллектор
4.9. Обеспечение электробезопасности
4.9.1. Термины и определения
Аппараты антистатические – аппараты, в которых поверхности, имеющие контакт с перерабатываемыми веществами, изготовлены из материалов с удельным объемным элек-
трическим сопротивлением не более 108 Ом м.
Аппараты диэлектрические – аппараты, в которых поверхности, имеющие контакт с перерабатываемыми веществами, изготовлены из материалов с удельным объемным элек-
трическим сопротивлением более 108 Ом м.
Аппараты электропроводные – аппараты, поверхности которых имеют контакт с перерабатываемыми веществами и изготовлены из материалов с удельным объемным электриче-
ским сопротивлением не более 105 Ом м.
Заземлитель – проводник или совокупность металлически соединенных проводников, находящихся в соприкосновении с землей или её эквивалентом.
Заземлитель естественный – заземлитель, в качестве которого используют электропроводящие части строительных и производственных конструкций.
Заземляющее устройство – совокупность конструктивно объединенных заземляющих проводников и заземлителя.
Заземляющий проводник – проводник, соединяющий заземляемые части с заземлите-
лем.
Защитное заземление – преднамеренное электрическое соединение с землей или ее эквивалентом металлических нетоковедущих частей, которые могут оказаться под напряжением.
Электробезопасность – система организационных и технических мероприятий и средств, обеспечивающих защиту людей от вредного и опасного воздействия электрического тока, электрической дуги, электромагнитного поля и статического электричества.
4.9.2. Требования к электрооборудованию для аппаратов химических производств
В зависимости от условий эксплуатации электрооборудование, устанавливаемое на аппаратах химических и нефтехимических производств, может иметь взрывозащищенное или общепромышленное исполнение.
Электрооборудование общепромышленного исполнения может иметь различные степени защиты от соприкосновения персонала с вращающимися частями, от попадания внутрь электрооборудования твердых частиц и воды: IP00, IP01, IP10, IP11, IP12, IP13, IP20, IP21,
234
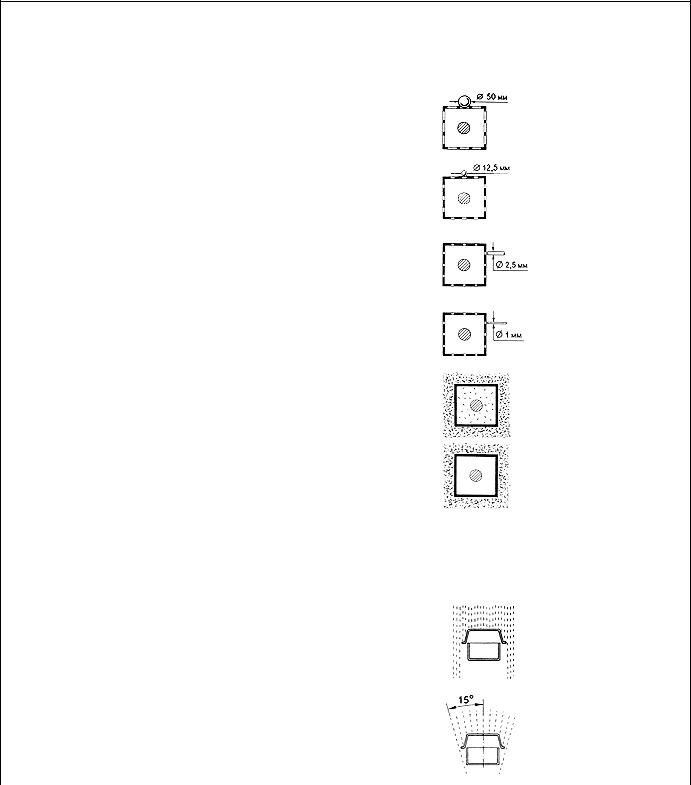
IP22, IP23, IP43, IP44, IP54, IP55, IP56. Буква I и первая цифра после буквы Р обозначают степень защиты от соприкосновения и попадания посторонних предметов, буква Р и вторая цифра – степень защиты от проникновения воды в электродвигатель. Схемы методов испытаний степени защиты (IPхx) от проникновения посторонних твердых тел, пыли, воды приведена в табл. 4.41. Данные о применении электродвигателей с различными степенями защиты приведены в табл. 4.42.
Таблица 4.41. Схемы методов испытаний степени защиты (IPХx) от проникновения посторонних твердых тел, пыли, воды
Защита от посторонних твердых тел, пыли
Первая |
|
|
|
|
|
|
|
|
|
цифра |
Вид защиты |
|
|
Краткое описание |
Схема метода испытаний |
||||
IP(Xx) |
|
|
|
|
|
|
|
|
|
0 |
Защиты нет |
|
|
Нет защиты |
|
|
|
||
|
|
|
|
|
Защищено от доступа к |
|
Шарик диаметром |
||
|
Защита от твердых тел раз- |
|
опасным частям тыль- |
|
|||||
1 |
|
|
50 мм и стандартный |
||||||
мером ≥ 50 мм |
|
|
ной стороной руки |
|
|||||
|
|
|
|
испытательный щуп |
|||||
|
|
|
|
|
|
|
|
|
|
|
|
|
|
|
|
|
|
||
|
|
|
|
|
Защищено от доступа к |
|
Шарик диаметром |
||
2 |
Защита от твердых тел раз- |
|
опасным частям |
паль- |
|
12,5 мм и стандарт- |
|||
мером ≥ 12,5 мм |
|
|
цем |
|
|
ный испытательный |
|||
|
|
|
|
|
|||||
|
|
|
|
|
|
|
|
|
щуп |
|
|
|
|
|
Защищено от доступа к |
|
стандартный испы- |
||
3 |
Защита от твердых тел раз- |
|
опасным частям |
инст- |
|
тательный щуп (или |
|||
мером ≥ 2,5 мм |
|
|
рументом |
|
|
провод диаметром |
|||
|
|
|
|
|
|||||
|
|
|
|
|
|
|
|
|
2,5 мм) |
|
|
|
|
|
Защищено от доступа к |
|
стандартный испы- |
||
4 |
Защита от твердых тел раз- |
|
опасным частям |
про- |
|
тательный щуп (или |
|||
мером ≥ 1,0 мм |
|
|
волокой |
|
|
провод диаметром |
|||
|
|
|
|
|
|||||
|
|
|
|
|
|
|
|
|
1,0 мм) |
|
|
|
|
|
Защищено от доступа к |
|
|
||
5 |
Частичная защита от пыли |
|
опасным частям |
про- |
|
Камера пыли (цир- |
|||
|
волокой |
|
|
куляция талька) |
|||||
|
|
|
|
|
|
|
|||
|
|
|
|
|
|
|
|
||
|
|
|
|
|
Защищено от доступа к |
|
|
||
6 |
Полная защита от пыли |
|
|
опасным частям |
про- |
|
Камера пыли (цир- |
||
|
|
волокой |
|
|
куляция талька) |
||||
|
|
|
|
|
|
|
|||
|
|
|
|
|
|
|
|
|
|
|
|
|
|
|
|
Защита от воды |
|
|
|
Первая |
|
|
|
|
|
|
|
|
|
цифра |
Вид защиты |
|
|
|
Краткое описание |
Схема метода испытаний |
|||
IP(Xx) |
|
|
|
|
|
|
|
|
|
0 |
Нет защиты |
|
|
|
|
|
|
|
|
|
Защищено от верти- |
|
Вертикально падающие кап- |
|
|
||||
|
кально падающих ка- |
|
ли воды не должны оказы- |
|
Оросительная сис- |
||||
1 |
пель воды |
|
вать вредного воздействия |
|
тема в камере искус- |
||||
|
|
|
|
|
|
|
|
|
ственного дождя |
|
|
|
|
|
|
||||
|
Защищено от верти- |
|
Вертикально падающие кап- |
|
|
||||
|
кально падающих ка- |
|
ли |
не |
должны оказывать |
|
Оросительная сис- |
||
|
пель воды, когда обо- |
|
вредного |
воздействия, |
когда |
|
|||
2 |
|
|
тема в камере искус- |
||||||
лочка отклонена на |
|
оболочка |
отклонена от |
вер- |
|
||||
|
|
|
ственного дождя |
||||||
|
угол до 15° |
|
тикали в любую сторону на |
|
|||||
|
|
|
|
||||||
|
|
|
угол до 15° включительно |
|
|
235
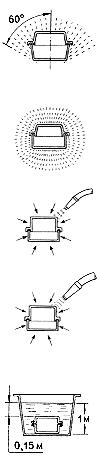
Продолжение табл. 4.41
Первая |
|
|
|
|
|
|
|
|
|
цифра |
Вид защиты |
Краткое описание |
|
Схема метода испытаний |
|||||
IP(Xx) |
|
|
|
|
|
|
|
|
|
|
Защищено от воды, |
Вода, падающая в виде брызг |
|
Дождевальная уста- |
|||||
|
падающей в виде до- |
в любом направлении, со- |
|
||||||
3 |
ждя |
ставляющем |
угол |
до |
60° |
|
новка с поворотным |
||
|
включительно с вертикалью, |
|
выходным патруб- |
||||||
|
|
|
|||||||
|
|
не должна оказывать вредно- |
|
ком |
|||||
|
|
го воздействия |
|
|
|
|
|
||
|
Защищено от сплош- |
Вода, падающая в виде брызг |
|
Дождевальная уста- |
|||||
|
ного обрызгивания |
на оболочку |
с |
любого |
на- |
|
|||
|
|
новка с поворотным |
|||||||
4 |
|
правления, не должна оказы- |
|
||||||
|
|
выходным патруб- |
|||||||
|
|
вать вредного воздействия |
|
|
|||||
|
|
|
|
ком |
|||||
|
|
|
|
|
|
|
|
|
|
|
|
|
|
|
|||||
|
Защищено от водяных |
Вода, направляемая на обо- |
|
Гидронасос со |
|||||
|
струй |
лочку в виде струй с любого |
|
шлангом и насадкой |
|||||
5 |
|
направления, не должна ока- |
|
диаметром 6,3 мм, |
|||||
|
|
зывать вредного воздействия |
|
расход воды 12,5 |
|||||
|
|
|
|
|
|
|
|
|
л/мин |
|
Защищено от сильных |
Вода, направляемая на обо- |
|
Гидронасос со |
|||||
|
водяных струй |
лочку в виде сильных струй с |
|
шлангом и насадкой |
|||||
6 |
|
любого |
направления, |
не |
|
диаметром 12,5 мм, |
|||
|
|
должна |
оказывать вредного |
|
расход воды 100 |
||||
|
|
воздействия |
|
|
|
|
|
л/мин |
|
|
Защищено от воздей- |
Должно |
быть |
исключено |
|
|
|||
|
ствия при временном |
проникновение |
воды |
внутрь |
|
|
|||
|
(непродолжительном) |
оболочки в количестве, вы- |
|
Погружение в ванну |
|||||
7 |
погружении в воду |
зывающем вредное воздейст- |
|
||||||
|
вие, при ее погружении на |
|
со слоем воды 1 м |
||||||
|
|
|
|||||||
|
|
короткое время при стандар- |
|
|
|||||
|
|
тизованных условиях по дав- |
|
|
|||||
|
|
лению и длительности |
|
|
|
||||
|
Защищено от воздей- |
Должно |
быть |
исключено |
|
|
|||
|
ствия при длительном |
проникновение воды в обо- |
|
|
|||||
|
погружении в воду |
лочку в количествах, вызы- |
|
|
|||||
|
|
вающих вредное воздействие, |
Испытания по методике, согласован- |
||||||
8 |
|
при ее длительном погруже- |
ной с заказчиком или конечным потре- |
||||||
|
|
нии в воду при условиях, со- |
бителем |
||||||
|
|
гласованных |
между |
изгото- |
|
|
|||
|
|
вителем и потребителем, од- |
|
|
|||||
|
|
нако более жестких, чем ус- |
|
|
|||||
|
|
ловия для цифры 7 |
|
|
|
|
Таблица 4.42. Выбор электродвигателей для установки в производственных помещениях
№ |
Вид помещения |
Характеристика помещения |
Степень |
защиты |
|
по ПУЭ [27] |
электродвигателя |
||||
1 |
Сухое |
Относительная влажность воздуха не превы- |
IP00 или IP20 |
||
|
|
шает 60 % |
|
|
|
2 |
Влажное |
Относительная влажность воздуха более 60 |
IP20 |
|
|
|
|
%, но не превышает 75 % |
|
|
|
3 |
Сырое |
Относительная влажность воздуха длительное |
IP43 с |
влагостойкой |
|
время превышает 75 % |
изоляцией |
||||
|
|
||||
4 |
Особо сырое |
Относительная влажность воздуха близка к |
То же |
|
|
100 % (потолки, стены, пол покрыты влагой) |
|
||||
|
|
|
|
236
Продолжение табл. 4.42
№ |
Вид помещения |
Характеристика помещения |
Степень |
|
защиты |
||
по ПУЭ [27] |
электродвигателя |
||||||
|
|
Температура воздуха длительное время пре- |
Исполнение |
обдувае- |
|||
5 |
Жаркое |
мое или продуваемое с |
|||||
вышает 40 °С |
подводом чистого воз- |
||||||
|
|
||||||
|
|
|
духа |
|
|
|
|
6 |
Пыльное |
Выделяется пыль в количестве, достаточном |
IP44 |
или |
исполнение |
||
для проникновения внутрь оборудования |
продуваемое |
с подво- |
|||||
|
|
дом чистого воздуха |
|||||
|
|
|
|||||
|
С химически ак- |
Длительное время содержатся пары или обра- |
IP44 |
или |
исполнение |
||
7 |
зуются отложения, разрушающие изоляцию и |
продуваемое |
с подво- |
||||
|
тивной средой |
токоведущие части электрооборудования |
дом чистого воздуха |
||||
|
|
||||||
8 |
Пожароопасное |
Помещения с пожароопасными зонами всех |
IP44 |
|
|
|
|
классов |
|
|
|
||||
|
|
|
|
|
|
||
|
|
Помещения со взрывоопасными зонами клас- |
Взрывозащищенное |
||||
9 |
Взрывоопасное |
сов B-I, В-Ia, В-1г В-ΙΙ |
исполнение |
|
|
||
Помещения со взрывоопасными зонами клас- |
IP54 |
|
|
|
|||
|
|
|
|
|
|||
|
|
сов B-Iб и В-ΙΙа |
|
|
|
|
Примечания: 1. При отсутствии условий, приведенных в пп. 4 – 6, помещения называют нормальными.
2. До освоения электропромышленностью машин со степенью защиты оболочки IP54 разрешается применять машины со степенью защиты IP44.
Электродвигатели и другое электрооборудование, предназначенное для комплектации аппаратов, размещенных на открытых производственных площадках, должны иметь исполнение не ниже IP44 или специальное, соответствующее условиям их работы (например, для особо низких температур).
В обозначении степеней защиты могут дополнительно использоваться буквы S, M, W, имеющие следующие значения: S – испытано на проникновение воды при неработающем изделии; М – испытано на проникновение воды при работающем изделии; W – изделие имеет дополнительные средства защиты для работы в особых климатических условиях.
Если электрооборудование имеет только одну степень защиты, то пропущенная цифра может заменяться буквой X, например: IP2X, IPX2.
Аппараты, не требующие регулирования частоты вращения внутренних устройств, должны комплектоваться синхронными и асинхронными электродвигателями с короткозамкнутым ротором. Электродвигатели постоянного тока могут применяться только в тех случаях, когда электродвигатели переменного тока не обеспечивают требуемых характеристик или неэкономичны.
При установке электродвигателей должны выдерживаться следующие расстояния:
а) между необслуживаемыми сторонами электродвигателей, а также между электродвигателем и стеной или колонной здания – не менее 0,3 м при высоте его расположения до 1 м от уровня пола и не менее 0,6 м при высоте расположения электродвигателя более 1 м;
б) при наличии прохода между электродвигателями, а также между электродвигателем и стеной здания – не менее 1 м.
Допускаются местные сужения проходов между выступающими частями электродвигателей и строительными конструкциями до 0,6 м на длине не более 0,5 м.
Установка на аппаратах электродвигателей и другого электрооборудования должна обеспечивать возможность их периодического осмотра и ремонта.
4.9.3. Заземление и защитные меры по обеспечению электробезопасности
Заземление является наиболее распространенным средством защиты персонала от поражения электрическим током при повреждении изоляции электрооборудования, установ-
237
ленного на аппаратах.
Заземлению подлежат корпуса аппаратов, электрооборудование и металлические части, доступные для прикосновения человека и не имеющие других видов защиты, обеспечивающих электробезопасность.
Во взрывоопасных зонах любого класса заземлению подлежат аппараты с установленным на них электрооборудованием, работающим при всех напряжениях переменного и постоянного тока, в том числе аппараты, установленные на заземленных металлических конструкциях, которые в невзрывоопасных зонах допускается не заземлять. Это требование не распространяется на электрооборудование, установленное внутри заземленных корпусов шкафов и пультов.
В невзрывоопасных зонах защитное заземление следует выполнять:
1)при переменном токе с номинальным напряжением 380 В и выше и при постоянном токе с напряжением 440 В и выше – во всех случаях;
2)при переменном токе с номинальным напряжением от 42 до 380 В и при постоянном токе с напряжением от 110 до 440 В – при работах в условиях повышенной опасности и особоопасных условиях.
К условиям повышенной опасности поражения людей электрическим током относятся: а) влажность (пары или конденсирующаяся влага выделяются в виде мелких капель, и
относительная влажность воздуха превышает 75 %); б) присутствие проводящей пыли (технологическая или другая пыль, оседая на прово-
дах, проникая внутрь машин и аппаратов и отлагаясь на электроустановках, ухудшает условия охлаждения и изоляции, но не вызывает опасности пожара или взрыва);
в) наличие токопроводящих оснований (металлических, земляных, железобетонных, кирпичных);
г) повышенная температура (независимо от времени года и различных тепловых излучений температура длительное время превышает 35 °С, кратковременно 40 °С);
д) возможность одновременного прикосновения человека к имеющим соединение с землей металлоконструкциям зданий, технологическим аппаратам, механизмам и т.п., с одной стороны, и к металлическим корпусам электрооборудования – с другой.
К особоопасным условиям поражения людей электрическим током относятся:
а) сырость (дождь, снег, частое опрыскивание и покрытие влагой внутренних поверхностей помещения);
б) присутствие химически активной среды (постоянно или длительное время в воздухе содержатся агрессивные пары, газы, жидкость, образующие отложения или плесень, действующие разрушающе на изоляцию или токоведущие части электрооборудования);
в) наличие одновременно двух или более условий повышенной опасности.
Защитное заземление допускается не выполнять на аппаратах: предназначенных для установки в недоступных, без применения специальных средств, местах (в том числе внутри других изделий); предназначенных для установки только на заземленных металлических конструкциях, если при этом обеспечивается стабильный электрический контакт соприкасающихся поверхностей; заземление которых не допускается принципом действия или назначением.
Заземляющие проводники должны крепиться к аппаратам при помощи резьбовых соединений или сварки. Сопротивление между элементом заземления (шпилькой, болтом) и каждой доступной прикосновению металлической нетоковедущей частью аппарата, которая может оказаться под напряжением, не должно превышать 0,1 Ом.
Способы присоединения к аппаратам заземляющих проводников с помощью сварки показаны на рис. 4.29.
Заземляющие элементы со шпилькой или болтом устанавливаются на сварных аппаратах при помощи специальных бобышек, а на литых аппаратах – на приливах. Конструкция и размеры бобышек приведены в табл. 4.43.
238

Рис. 4.29. Присоединение к аппаратам заземляющих проводников с помощью сварки: Ι – VΙ − различные способы присоединения
Таблица 4.43. Бобышки под шпильки и болты для заземляющих зажимов, ГОСТ 21130–75*
d, мм |
D, мм |
Н, мм |
с, мм |
Масса бобышки, кг |
||
под шпиль- |
под болт |
под шпильку |
под болт |
|||
|
|
ку |
|
|
|
|
М6 |
12 |
10 |
20 |
1,0 |
0,011 |
0,022 |
М8 |
17 |
12 |
25 |
1,6 |
0,020 |
0,040 |
М10 |
21 |
14 |
28 |
1,6 |
0,038 |
0,075 |
М12 |
24 |
15 |
30 |
1,6 |
0,052 |
0,104 |
М16 |
35 |
20 |
40 |
1,6 |
0,150 |
0,300 |
Примечание. Материал – сталь марки Ст2 согласно ГОСТ 380–71*
Шпильки, болты и гайки для элементов заземления должны изготовляться из стали или латуни. Между заземляющим проводником и шпилькой (болтом) следует устанавливать контргайки и пружинные шайбы. Вокруг шпильки (болта) должна предусматриваться неокрашенная контактная площадка для присоединения заземляющего проводника. Размеры шпилек (болтов) и контактных площадок выбирают в зависимости от силы тока по табл. 4.44. Использование для присоединения заземляющих проводников шпилек и болтов, служащих для соединения между собой частей аппаратов и трубопроводов, недопустимо.
239
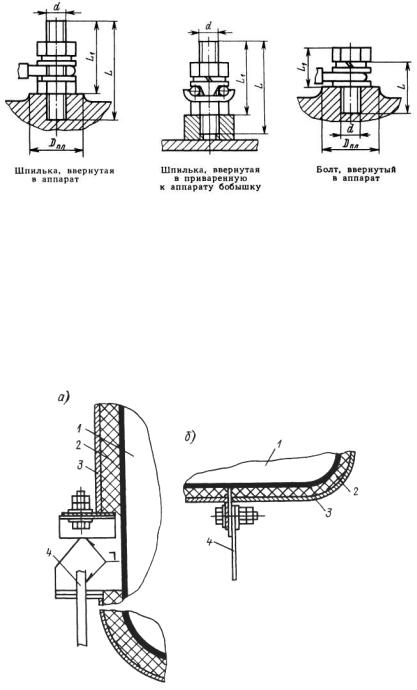
Таблица 4.44. Заземляющие зажимы, ГОСТ21130–75*
|
d |
Шпилька |
|
Болт |
Dпл |
||
Сила тока, А |
L |
L1 |
L |
|
L1 |
||
|
|
||||||
|
мм |
|
|
|
|
|
|
До 100 |
М6 |
30; 35 |
22 |
12; 16 |
|
12 |
16 |
Св. 100 до 250 |
М8 |
35; 40; 45 |
26 |
20; 25 |
|
15 |
20 |
Св. 250 до 630 |
М10 |
45; 50; 55 |
34 |
25; 30 |
|
21 |
25 |
Св. 630 |
М12 |
55; 60; 65 |
42 |
30; 35 |
|
25 |
28 |
М16 |
70 |
50 |
40 |
|
30 |
− |
|
|
|
Варианты присоединения заземляющих проводников к аппаратам с теплоизоляцией, защищенной металлическим кожухом, показаны на рис. 4.30.
Рис. 4.30. Варианты присоединения заземляющих проводников к аппаратам с теплоизоляцией, защищенной металлическим кожухом: а – к опоре; б – к корпусу аппарата;
1 – корпус аппарата; 2 – теплоизоляция; 3 – металлический кожух; 4 – заземляющий проводник
В качестве заземляющих проводников могут применяться изолированные и неизолированные провода, полосовой прокат и другие материалы, указанные в табл. 4.45.
При необходимости заземления подвижных частей аппаратов следует применять гибкие проводники или скользящие контакты. Пример заземления аппарата с гибкой вставкой приведен на рис. 4.31.
Рядом с заземляющим элементом должен быть помещен знак заземления. Этот знак допускается выполнять методом штамповки на пластине, прикрепляемой к аппарату, или методами литья в металле согласно ГОСТ 21130–75*.
Расчет защитного заземления выполняют на стадии проектирования технологической установки в целом. Цель этого расчета – определить число, размеры и место размещения
240

одиночных заземлителей и заземляющих проводов, при которых напряжения прикосновения и шага в период замыкания фазы на заземленный корпус аппарата не превышают безопасных значений. Порядок расчета защитного заземления приведен в специальной литературе [34].
Рис. 4.31. Устройство контактной перемычки в местах гибких вставок: 1 – металлический корпус аппарата; 2 – тканевый соединительный рукав; 3 – соединительный проводник; 4 – металлический воздуховод
Таблица 4.45. Размеры заземляющих проводников [27]
|
|
Материал проводника |
|
|
|
||
Заземляющий проводник |
|
|
Сталь |
|
|
||
Медь |
Алюминий |
Местонахождение проводника |
|||||
в здани- |
в наружных |
в земле |
|||||
|
|
|
|
||||
|
|
|
|
ях |
установках |
||
|
|
|
|
|
|||
Неизолированные провода: |
|
|
|
|
|
||
площадь сечения, мм2 |
4 |
6 |
– |
– |
– |
||
диаметр, мм |
|
− |
− |
5 |
6 |
10 |
|
Изолированные |
провода, |
1,5 |
2,5 |
– |
– |
– |
|
площадь сечения, мм2 |
|
|
|
|
|
||
Угловой прокат, толщина по- |
– |
– |
2 |
2,5 |
4 |
||
лосы, мм |
|
|
|
|
|
|
|
Полосовой прокат: |
|
|
|
|
|
|
|
площадь сечения, мм2 |
– |
– |
24 |
48 |
48 |
||
толщина, мм |
|
– |
– |
3 |
4 |
4 |
|
Водопроводные трубы, тол- |
– |
– |
2,5 |
2,5 |
3,5 |
||
щина стенки, мм |
|
|
|
|
|
|
|
Тонкостенные трубы, толщи- |
– |
– |
1,5 |
2,5 |
Не допускает- |
||
на стенки, мм |
|
|
|
|
|
ся |
4.9.4. Защита от статического электричества
Заряды статического электричества могут возникать при перемешивании, фильтрации, сливе, разбрызгивании, кристаллизации и испарении жидкостей, при деформации или дроблении твердых тел, а также при относительном перемещении двух находящихся в контакте твердых тел. Способность веществ и материалов образовывать заряды статического электри-
чества зависит в основном от их удельного электрического сопротивления ρv. Вещества и
материалы, имеющие удельные объемные электрические сопротивления ρv < 105 Ом м, при отсутствии их разбрызгивания или распыления не электризуются, и, следовательно, применять меры защиты от статического электричества при работе с такими веществами и материалами не требуется.
При обработке легковоспламеняющихся и горючих жидкостей необходимо учитывать степень электролизации их поверхности. Предельно допустимым считается такое значение поверхностной плотности заряда, напряженности поля или потенциала, при котором максимально возможная энергия разряда с поверхности данного вещества не превосходит 1/4 зна-
241
чения минимальной энергии воспламенения окружающей среды ρv.
Мероприятия по защите от статического электричества должны осуществляться только в пределах взрыво- и пожароопасных зон, установленных классификацией Правил устройства электроустановок (ПУЭ) – см. гл. 6. В остальных производствах защита должна предусматриваться только в случаях отрицательного влияния статического электричества на производственный процесс. Основным способом защиты аппаратов от опасных потенциалов статического электричества является заземление. В обоснованных случаях дополнительно к заземлению можно применять другие меры защиты (уменьшение объемного или поверхностного сопротивления, нейтрализацию зарядов).
Заземляющие устройства для защиты от статического электричества следует, как правило, объединять с заземляющими устройствами для электрооборудования и выполнять в соответствии с требованиями ПУЭ. Сопротивление заземляющего устройства, предназначенного исключительно для защиты от статического электричества, допускается до 100 Ом.
Неметаллические аппараты считаются электростатически заземленными, если сопротивление любой точки их внутренней и внешней поверхностей относительно контура зазем-
ления не превышает 107 Ом м.
Металлические и электропроводные неметаллические аппараты и трубопроводы, расположенные в производственных помещениях и на наружных установках, должны быть объединены в непрерывную электрическую цепь, которая должна присоединяться к контуру заземления не менее чем в двух точках. Присоединять к контуру заземления при помощи отдельного ответвления независимо от заземления соединенных с ними коммуникаций следует аппараты, в которых происходит дробление, распыление, разбрызгивание продуктов, эмалированные и футерованные аппараты, а также аппараты, не соединенные трубопроводами с общей системой заземления аппаратов и трубопроводов.
Если заземление аппаратов не предотвращает накопление опасных потенциалов статического электричества, то в качестве дополнительной меры следует применять способ рассеяния зарядов путем уменьшения удельного объемного и поверхностного электрического сопротивления. С этой целью увлажняют воздух в рабочей зоне производственного помещения, а также обрабатывают изделия растворами поверхностно-активных веществ или вводят поверхностно-активные вещества при вальцевании, экструзии и смешении.
Способ нейтрализации зарядов рекомендуется применять в случаях, когда нельзя отвести заряды статического электричества с помощью более простых средств, описанных выше. Для нейтрализации зарядов статического электричества во взрывоопасных зонах всех классов рекомендуется применять радиоизотопные нейтрализаторы.
Для нейтрализации зарядов статического электричества на открытых поверхностях (пленки, ленты, ткани, листы) используют нейтрализаторы на основе плутония-239 или трития. При этом расстояние от нейтрализатора до заряженной поверхности не должно превышать в первом случае 50 мм, во втором – 25 мм.
В местах, где установка нейтрализаторов затруднена, следует применять вдувание ионизированного воздуха. В случае применения этого способа во взрывоопасных зонах ионизаторы должны быть во взрывозащищенном исполнении или располагаться в соседних зонах, не являющихся взрывоопасными.
Для предотвращения накопления опасных потенциалов статического электричества движение жидкостей по трубопроводам и их истечение в аппараты ограничивают следующими скоростями:
o 10 м/с и менее – для жидкостей с удельным объемным электрическим сопротивлени-
ем не более 105 Ом м;
o 5 м/с и менее – для жидкостей с удельным объемным электрическим сопротивлением
не более 109 Ом м;
o 1,2 м/с – для жидкостей с удельным объемным электрическим сопротивлением более
109 Ом м при диаметрах трубопроводов до 200 мм;
o 1 м/с – в начале заполнения порожнего аппарата жидкостями, имеющими удельное
242

объемное электрическое сопротивление более 105 Ом м, до момента затопления конца загрузочной трубы.
Снижение скорости истечения жидкости может быть достигнуто применением релаксационных емкостей, которые представляют собой горизонтальный участок трубопровода увеличенного диаметра, находящегося непосредственно у входа в аппарат.
Диаметр релаксационной емкости D вычисляют по формуле
D = |
2dтр2 ϖж |
, |
(4.17) |
где dтр – диаметр трубопровода до релаксационной емкости, м; ϖж – скорость жидкости в трубопроводе, м/с.
Длина релаксационной емкости
L = 2,2 10−11 ερv , |
(4.18) |
где ε – диэлектрическая постоянная жидкости; ρv – удельное объемное электрическое сопро-
тивление жидкости, Ом м.
Жидкости в аппараты должны, как правило, подаваться ниже уровня находящихся в этих аппаратах заполняющих жидкостей.
Не допускается подача жидкостей в аппараты свободно падающей струей. Расстояние от конца загрузочной трубы до днища аппарата не должно превышать 200 мм.
Допускается направлять струю жидкости вдоль стенки аппарата, при этом форма конца трубы и скорость подачи жидкости должны быть выбраны так, чтобы исключить ее разбрызгивание.
Возникновение опасных искровых разрядов при движении горючих паров и газов в аппаратах и трубопроводах предотвращается путем заземления всех металлических частей, находящихся в газовом потоке, и исключением возможности присутствия в этих потоках твердых и жидких частиц. Не рекомендуется отводить заряды из газового потока путем введения в него заземленных металлических сеток, пластин, рассекателей, коаксиальных стержней и других аналогичных устройств.
В футерованных аппаратах заземлению подлежат металлические корпуса, детали, арматура и другие электропроводные поверхности. Исключение составляют аппараты с антистатической футеровкой, в которых перерабатываются жидкости с удельным объемным
электрическим сопротивлением не более 109 Ом м, перемещаемые со скоростью до 2 м/с. В таких аппаратах заземляют только их металлические корпуса. В антистатических и диэлектрических неметаллических аппаратах не допускается наличие металлических частей и деталей, имеющих сопротивление относительно земли более 100 Ом.
Для обеспечения электропроводности неметаллические антистатические и диэлектрические аппараты должны покрываться снаружи и внутри слоем лака или эмали, обладающих электропроводными свойствами. При этом должен быть обеспечен надежный контакт покрытия с заземленной металлической арматурой.
Введение в неметаллические антистатические и диэлектрические аппараты дополнительных заземленных электродов допускается в случаях:
а) при невозможности покрытия наружных и внутренних поверхностей аппаратов электропроводным лаком или эмалью;
б) при обработке веществ, способных накапливать заряды при контактном или индуктивном воздействии наэлектризованной поверхности аппаратов и имеющих удельное объем-
ное электрическое сопротивление не более 105 Ом м.
Вводимые в аппарат электроды не должны выступать над поверхностью жидкости или нарушать герметичность аппарата.
В аппаратах должны заземляться все вращающиеся и движущиеся части, контакт которых с заземленным корпусом может быть нарушен из-за наличия слоя смазки в подшипниках или применения диэлектрических антифрикционных материалов. Обеспечение контакта в электропроводных подшипниках достигается применением электропроводной смазки.
Передача движения от электродвигателей к аппаратам должна осуществляться через
243
муфту, редуктор или, в виде исключения, через клиноременное устройство. Применение плоскоременных передач не допускается. Клиноременные передачи должны выполняться из
материалов, имеющих удельное объемное электрическое сопротивление не более 105 Ом м, а вся установка (ограждение и другие металлические детали вблизи ремня) должна заземляться. В частности, находят применение антистатические клиновые ремни по ТУ 38-105-275–71. В случае использования обычных клиновых ремней следует применять один из следующих способов предотвращения опасной электризации:
1)увеличение относительной влажности воздуха в месте расположения клиноременной передачи не менее чем до 70 %;
2)покрытие ремней электропроводной смазкой;
3)ионизацию воздуха с помощью установленных с внутренней стороны ремня (возможно ближе к точке его схода со шкива) нейтрализаторов.
Запрещается смазывать ремни канифолью, воском и другими веществами, увеличивающими поверхностное сопротивление, во взрывоопасных помещениях всех классов.
4.10. Защитные ограждения и устройства для обслуживания аппаратов
4.10.1. Защитные ограждения
Ограждениями называются устройства, ограничивающие доступ персонала в опасные зоны, образуемые движущимися частями аппаратов, частями, находящимися под повышенным напряжением электрического тока, и другими видами опасности. Ограждения могут быть постоянно закрепленными или периодически открывающимися. Ограждения не должны затруднять обслуживание аппаратов или ограничивать их технические возможности.
Предпочтительно применять сплошные ограждения, выполненные в соответствии с ГОСТ 12.2.009–80*, из листовой стали толщиной не менее 0,8 мм, листового алюминия толщиной не менее 2 мм или прочной пластмассы толщиной не менее 4 мм. В защитных ограждениях допускается устройство смотровых окон из стекол согласно ГОСТ 5727–83* Е и ГОСТ 9424–79* или другого прозрачного материала, не уступающего по эксплуатационным свойствам указанным выше материалам.
Защитные ограждения, изготовляемые из сетки или перфорированного материала, должны иметь конструкцию, обеспечивающую жесткость и постоянство формы. Расстояния между ограждением из сетки или перфорированного материала и ограждаемым элементом устанавливает ГОСТ 12.2.062–81 * выдержки из которого приведены в табл. 4.46:
Таблица 4.46
Диаметр |
окружности, |
|
|
|
|
|
вписанной в ячейку сетки |
До 8 |
Св. 8 до 10 |
Св. 10 |
до 25 |
Св. 25 до 40 |
|
(решетки), мм |
|
|
|
|
|
|
Расстояние |
от огражде- |
|
|
|
|
|
ния до опасного элемен- |
Не менее 15 |
Св. 15 до 35 |
Св. 35 |
до 120 |
Св. 120 до 200 |
|
та, мм |
|
|
|
|
|
|
Прочность ограждений должна определяться из расчета воздействия на них разрушившихся частей аппарата или выброса жидких продуктов. Следует учитывать возможность воздействия на ограждения обслуживающего персонала.
Ограждения должны иметь надежное крепление, исключающее их самооткрывание. Если по производственной необходимости ограждения должны сниматься чаще одного раза в смену, то масса таких ограждений или их съемных частей должна быть не более 6 кг, а их крепление осуществляться без помощи ключей или отверток. Ограждения открывающегося типа должны открываться с усилием не более 40 Н.
Съемные и открывающиеся ограждения должны иметь соответствующие ручки или скобы и фиксироваться в открытом положении.
В случае, если речь идет о крупногабаритных узлах или целых аппаратах, целесообраз-
244
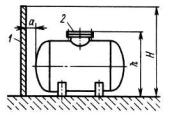
но применять ограждения, открытые сверху (табл. 4.47 и рис. 4.32).
Рис. 4.32. Ограждение, открытое сверху; 1 − ограждение; 2 – ограждаемый аппарат
Таблица 4.47. Высота открытых сверху ограждений в зависимости от расположения опасного элемента, ГОСТ 12.2.062–81*
Высота |
располо- |
Высота защитного ограждения Н, мм |
|
|
|
||||
жения |
опасного |
2400 |
2200 |
2000 |
1800 |
1600 |
1400 |
1200 |
1000 и менее |
элемента h, мм |
Расстояние от опасного элемента до ограждения а, мм |
|
|||||||
2600 |
|
100 |
100 |
100 |
100 |
100 |
100 |
100 |
100 |
2400 |
|
|
100 |
100 |
150 |
150 |
200 |
200 |
200 |
2200 |
|
|
250 |
350 |
400 |
500 |
500 |
600 |
600 |
2000 |
|
|
|
350 |
500 |
600 |
700 |
900 |
1100 |
1800 |
|
|
|
|
600 |
900 |
900 |
1000 |
1100 |
1600 |
|
|
|
|
500 |
900 |
900 |
1000 |
1300 |
1400 |
|
|
|
|
100 |
800 |
900 |
1000 |
1300 |
1200 |
|
|
|
|
|
500 |
900 |
1000 |
1400 |
1000 |
|
|
|
|
|
300 |
900 |
1000 |
1400 |
800 |
|
|
|
|
|
|
600 |
900 |
1300 |
600 |
|
|
|
|
|
|
|
500 |
1200 |
400 |
|
|
|
|
|
|
|
300 |
1200 |
200 |
|
|
|
|
|
|
|
200 |
1100 |
Наружную поверхность защитного ограждения окрашивают в тот же цвет, что и аппарат, на котором оно установлено. Внутренняя поверхность съемных и откидных ограждений должна быть окрашена в желтый цвет. На наружную сторону таких ограждений наносят предупреждающий знак опасности (желтого цвета равносторонний треугольник с черным восклицательным знаком в середине). Под знаком наносится табличка согласно ГОСТ 12.4.026– 76* с поясняющей надписью «При работающем аппарате не открывать».
4.10.2. Площадки и лестницы для обслуживания аппаратов
При необходимости систематического обслуживания аппаратов, арматуры и приборов, установленных на высоте более 1800 мм от уровня пола или нулевой отметки, следует предусматривать рабочие площадки. Высота потолка над полом рабочих площадок должна быть не менее 2150 мм. Минимальная ширина площадок 800 мм. Настил изготовляют из сплошных стальных листов. Рабочие площадки должны иметь перила высотой 1000 мм и дополнительную ограждающую планку посередине высоты перил. В нижней части перил следует предусматривать сплошную обшивку в виде полосы высотой не менее 150 мм.
Доступ к рабочим площадкам должен обеспечиваться с помощью стационарных маршевых лестниц шириной не менее 700 мм и с уклоном к горизонту не менее 45°. Для доступа к редко обслуживаемым аппаратам, арматуре и приборам допускается устройство служебных лестниц с уклоном 60° или использование стремянок с уклоном к горизонту 75–90°.
При высоте лестниц или стремянок более 1000 мм следует предусматривать площадки для отдыха через каждые 5000 мм.
Маршевые и служебные лестницы должны иметь плоские ступени из стальных рифленых листов и перила высотой 1000 мм по вертикали. Ширина стремянок должна быть не менее 400 мм. Начиная с высоты 3000 мм стремянки должны быть, оборудованы ограждениями
245
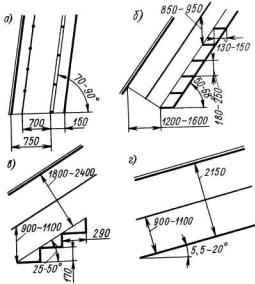
в виде дуг. Дуги располагаются на расстоянии 800 мм друг от друга и соединяются между собой не менее чем тремя продольными полосами. Расстояние от стремянки до дуги должно быть не менее 700 мм при радиусе 400 мм. Рекомендуемые размеры элементов лестниц приведены на рис. 4.33.
Рис. 4.33. Размеры элементов лестниц: а – стремянка; б – служебная лестница; в –хозяйственная лестница; г – пандус
Число открытых маршевых лестниц от рабочих площадок и технологических этажерок, предназначенных для размещения и обслуживания аппаратов с легковоспламеняющимися и горючими жидкостями и газами, должно соответствовать следующим требованиям:
а) при длине наружной этажерки или площадки от 18 до 80 м – не менее двух маршевых открытых лестниц;
б) при длине наружной этажерки или площадки более 80 м число лестниц определяется из расчета их расположения на расстоянии не более 80 м одна от другой.
Лестницы наружных этажерок должны располагаться по наружному периметру.
Для колонных аппаратов, не требующих повседневного обслуживания, при длине рабочих площадок не более 24 м допускается устройство одной маршевой лестницы и одной вертикальной. При групповой установке аппаратов колонного типа для отдельных аппаратов, возвышающихся над остальными, допускается устраивать вертикальные стремянки.
При устройстве рабочих площадок на аппаратах большого диаметра (типа резервуаров) верхняя площадка лестницы, ведущей на аппарат, должна находиться на одном уровне с крышкой аппарата и иметь ограждающие перила, идущие по краю крышки аппарата на расстоянии не менее 1800 мм в каждую сторону от лестницы. При необходимости обслуживания арматуры и приборов, расположенных на разных участках крышки такого аппарата, к ним должны быть подведены площадки с ограждением.
4.11. Снижение шума и вибрации аппаратов
4.11.1. Снижение шума и вибрации в подшипниковых узлах
При разработке аппаратов для химических производств в качестве опор для вращающихся узлов и деталей применяют в основном подшипники качения. Уровень шума и вибрации подшипников качения зависит от их размера, серии, частоты вращения вала, типа тел качения, а также от условий монтажа и эксплуатации.
При выборе подшипников следует учитывать, что шум и вибрация возрастают в среднем на 1–2 дБ с увеличением номера, определяющего типоразмер подшипника. Шум роликовых подшипников на 1–3 дБ сильнее шума шариковых подшипников тех же размеров [8]. Уровень вибрации роликовых подшипников превышает уровень вибрации шариковых подшипников в среднем на 5 дБ. На такую же величину уровень вибрации подшипников тяже-
246
лой серии больше уровня вибрации подшипников средней серии. Применение подшипников более высокого класса точности ведет к снижению вибрации на 1–2 дБ [11]. Шум подшипников при увеличении нагрузки возрастает, но не более чем на 5 дБ. Увеличение частоты вращения подшипников приводит к возрастанию шума на величину, определяемую по формуле
∆L = 23,3lg(n2 / n1 ), |
(4.19) |
где ∆L – прирост шума, дБ; n1, n2 – соответственно начальная и конечная частоты вращения
вала подшипника, с−1.
Параметры шума и вибрации подшипников изменяются в зависимости от типа и качества применяемой смазки. Смазка должна быть химически и физически стабильна, не содержать посторонних примесей, выдерживать заданную температуру и контактное давление. Для подшипниковых узлов емкостных аппаратов с перемешивающими устройствами, рабо-
тающими с частотой вращения вала до 8,3 с−1, в интервале температур от –60 до +90 °С рекомендуется применять пластичную смазку ЦИАТИМ-201 согласно ГОСТ 6267–74* или смазку с улучшенными противозадирными свойствами ЦИАТИМ-203 согласно ГОСТ 8773– 73*. При более высокой частоте вращения вала и диапазоне температур от –50 до +120 °С применяют смазку ЦИАТИМ-202.
В качестве средства, значительно уменьшающего шум и вибрацию в подшипниковых узлах, используют специальные вкладыши с высоким коэффициентом затухания (металловолокнистые, резиновые, пластмассовые). Такие вкладыши компенсируют геометрическое несовершенство посадочных мест и виброизолируют корпус узла от подшипника. Установка
вкладышей снижает шум и вибрацию подшипникового узла на 12÷15 дБ.
На уровень шума и вибрации влияют осевые натяги и перекосы подшипников в про-
цессе монтажа аппарата. При этом параметры шума и вибрации могут возрасти на 12÷15 дБ. Для снижения параметров шума и вибрации аппаратов, имеющих опорные узлы с под-
шипниками качения, рекомендуются следующие решения [11]:
а) выбирать подшипники минимально необходимого размера и по возможности более легкой серии;
б) применять по возможности однорядные радиальные шариковые подшипники; в) применять самоустанавливающиеся опоры; г) применять упругие вкладыши из вибродемпфирующих материалов;
д) обеспечивать соосность посадочных мест на валу и в корпусе подшипникового узла; е) обеспечивать минимальный радиальный зазор между подшипником и корпусом узла; ж) обеспечивать параметры шероховатости посадочных мест в соответствии с классом
точности выбранного подшипника; з) предусматривать предварительное осевое напряжение наружного кольца подшипни-
ка с ориентировочным усилием р = (5÷15) dвн, Н, где dвн – внутренний диаметр подшипника, мм;
и) предусматривать заполнение камер подшипниковых узлов смазочным материалом не более чем на 50 % объема, обеспечивая при этом надежное уплотнение в местах установки крышек.
12.11.2. Снижение шума и вибрации в зубчатых передачах и редукторах
Шум и вибрация в зубчатых передачах возникают как вследствие деформации сопрягаемых зубьев под действием передаваемой мощности, так и вследствие динамических процессов, обусловленных дефектами, допущенными при изготовлении и монтаже передачи.
По имеющимся данным [8, 9], при двукратном увеличении частоты вращения или пе-
редаваемой мощности уровень шума зубчатой передачи возрастает на 5÷6 дБ. При работе зубчатой передачи в режиме размыкания с большой частотой вращения уровень шума увеличивается на 10–15 дБ. Снижение шума в этих случаях может быть достигнуто применением двухступенчатых редукторов, а также использованием зубчатых колес с возможно мень-
247
шим диаметром и большой шириной зуба. Косозубые шестерни обеспечивают снижение шума на 2–6 дБ по сравнению с прямозубыми. Снижению шума зубчатой передачи способствует размещение колес вблизи опор на двухопорных валах, посадка по возможности должна быть неподвижной.
Существенное значение имеет выбор материала для зубчатых передач и его термообработка. Замена стали на чугун снижает уровни шума на 3–4 дБ. Закалка и другие виды термообработки, связанные с неизбежной деформацией обрабатываемых колес, ведут к увеличению уровня шума на 4–6 дБ [8]. На уровень шума зубчатых передач оказывает влияние количество применяемого смазочного масла, при недостатке которого шум может возрасти на
10–15 дБ.
Ориентировочно уровень звукового давления силовой зубчатой передачи мощностью более 50 кВт можно определить по формуле [8], дБ
L = L0 + 201g и, (4.20)
где L0 – поправка на уровень звукового давления, зависящая от качества изготовления зубчатых колес, дБ, L0 = 40…55 дБ; и – окружная скорость вращения зубчатых колес, м/с.
Шум в редукторах складывается в основном из шума, возникающего вследствие колебания корпуса под действием работающих в нем зубчатых передач, и шума, производимого воздухом, проникающим через неплотности в соединениях корпуса и смотровых окон. В целях снижения шума редукторов кроме выполнения приведенных выше рекомендаций целесообразно покрывать корпуса звукоизолирующими материалами, предусматривать установку вибропоглощающих прокладок в соединениях корпуса, применять упругие муфты для соединения вала редуктора с валом электродвигателя.
4.11.3. Снижение шума и вибрации, вызванных неуравновешенностью вращающихся деталей
Одной из причин повышенного шума и вибрации аппаратов является неуравновешенность вращающихся деталей (перемешивающих устройств, скребков, шнеков и т. д.). В зависимости от расположения оси инерции и оси вращения различают статическую, моментную и динамическую неуравновешенность вращающихся деталей [8].
Статическая неуравновешенность вращающейся детали вызвана разностью масс конструктивных элементов, находящихся на противоположных сторонах детали, а также кривизной вала или несоосностью поверхности детали с поверхностью шеек вала. При статической неуравновешенности главная центральная ось инерции и ось вращения детали параллельны.
Моментная неуравновешенность вращающейся детали возникает в случае пересечения в центре масс оси вращения и главной центральной оси инерции. При этом приведение всех неуравновешенных сил к центру массы вращения детали дает только главный момент.
Динамическая неуравновешенность вращающейся детали характеризуется пересечением главной центральной оси инерции с осью вращения не в центре масс детали.
Частота вибрации неуравновешенных деталей равна частоте их вращения.
Устранение вибрации, вызванной неуравновешенностью деталей, достигается их балансировкой. Приемы балансировки описаны в специальной литературе [12], а допустимые значения остаточного дисбаланса приведены в государственных и отраслевых стандартах для конкретных типов оборудования.
Например, в соответствии с ГОСТ 25167–82 Е для перемешивающих устройств вертикальных емкостных аппаратов, работающих при частоте вращения более 80 мин−1, допустимый остаточный дисбаланс не должен превышать величину М = 300 т n−0,5, где М –
остаточный дисбаланс, г см; т – масса мешалки, кг; n – частота вращения, мин−1.
При проворачивании вручную радиальное биение свободного конца консольного вала с мешалкой не должно превышать значения δ = 0,0025 l п−1/3, где δ – радиальное биение, мм; l
– длина консольной части вала, мм; п – рабочая частота вращения, мин−1.
Вид балансировки и методы устранения дисбаланса указываются в конструкторской
248
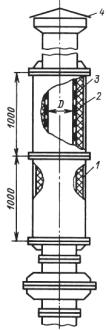
документации на конкретное изделие.
Причиной повышенной вибрации может быть нарушение соосности валов аппарата и привода. При этом угловое смещение валов увеличивает осевую вибрацию, а параллельное смещение – вибрацию в поперечном направлении. Вибрация аппарата может возрасти вследствие дефектов, допущенных при изготовлении соединительных муфт (например, неточная разметка отверстий под соединительные пальцы муфты). В этом случае на основную вибрацию, равную частоте вращения вала, накладывается высокочастотная вибрация от неравномерной работы пальцев в соединительной муфте [8]. Снижение уровня вибрации, связанное с нарушением соосности валов, достигается правильной их центровкой.
4.11.4. Снижение шума газодинамических процессов
Ваппаратах, заполненных газообразной средой, может возникать шум от протекающих
внем газодинамических процессов. Причинами газодинамического шума являются вихревые процессы в потоке рабочей среды, колебания среды под действием рабочих органов, пульсация давления, а также колебания, вызванные неоднородностью потока.
Снижение газодинамического шума непосредственно в аппарате достигается увеличением зазора между деталями, находящимися в газовой струе, и улучшением газодинамических характеристик проточной части аппарата.
Снижению шума способствует также установка специальных насадок на срезе трубопроводов, подающих среду в аппарат.
Действие насадки основано на переводе спектра шума в высокочастотную или ультра-
звуковую область, В отдельных случаях применение насадок снижает уровень шума на 8÷12 дБ, однако из-за дополнительного сопротивления насадки ухудшают рабочие характеристики аппаратов.
Значительное снижение уровня шума дает установка глушителей на всасывающих и выхлопных линиях. В специальной литературе [8, 9] описаны конструкции различных глушителей. На всасывающих линиях при скорости потока до 10 м/с целесообразно устанавливать трубчатые глушители с наполнением из стекловолокна или базальтового волокна со средней объемной плотностью соответственно 25 и 20 кг/м3 (рис. 4.34). На выхлопных линиях при тех же скоростях потока устанавливают вертикальные трубчатые глушители с набивкой из минераловатных плит со средней объемной плотностью 100 кг/м3. Технические характеристики трубчатых глушителей шума приведены в табл. 4.48.
Рис. 4.34. Схема трубчатого глушителя: 1 – секции глушителя; 2 – звукопоглощающий материал; 3 – перфорированная труба;4 – защитный зонт
249
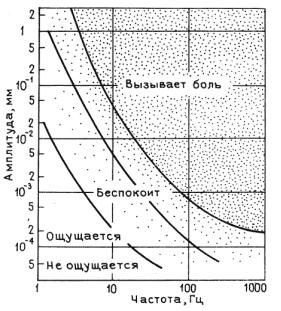
Таблица 4.48. Характеристики трубчатых глушителей шума
D, мм |
Число |
Снижение уровня звукового давления, дБ, при среднегеометрической частоте ок- |
|||||||||||||||||||
тавных полос, Гц |
|
|
|
|
|
|
|
|
|
|
|
|
|
|
|
|
|||||
(рис. |
сек- |
|
|
|
|
|
|
|
|
|
|
|
|
|
|
|
|
|
|
|
|
63 |
|
125 |
|
250 |
|
500 |
|
1000 |
|
2000 |
|
4000 |
|
8000 |
|
||||||
4.34) |
ций |
|
|
|
|
|
|
|
|
||||||||||||
а |
б |
а |
б |
а |
б |
а |
б |
а |
|
б |
а |
|
б |
а |
|
б |
а |
|
б |
||
|
|
|
|
|
|
||||||||||||||||
115 |
1 |
22 |
25 |
21 |
26 |
37 |
33 |
30 |
40 |
39 |
|
40 |
37 |
|
44 |
40 |
|
46 |
31 |
|
40 |
2 |
27 |
30 |
29 |
35 |
60 |
51 |
56 |
66 |
75 |
|
69 |
70 |
|
75 |
72 |
|
75 |
53 |
|
61 |
|
|
3 |
31 |
35 |
38 |
44 |
60 |
60 |
70 |
70 |
75 |
|
75 |
75 |
|
75 |
75 |
|
75 |
70 |
|
70 |
194 |
1 |
17 |
20 |
15 |
23 |
26 |
30 |
21 |
32 |
27 |
|
32 |
33 |
|
38 |
29 |
|
36 |
23 |
|
31 |
2 |
20 |
21 |
22 |
31 |
46 |
46 |
39 |
52 |
51 |
|
54 |
58 |
|
60 |
58 |
|
54 |
58 |
|
43 |
|
|
3 |
24 |
28 |
29 |
39 |
60 |
60 |
57 |
70 |
75 |
|
75 |
75 |
|
75 |
68 |
|
72 |
49 |
|
55 |
285 |
1 |
13 |
18 |
13 |
20 |
16 |
23 |
15 |
25 |
19 |
|
30 |
25 |
|
31 |
20 |
|
26 |
15 |
|
22 |
2 |
16 |
21 |
18 |
26 |
29 |
34 |
26 |
40 |
33 |
|
46 |
41 |
|
45 |
30 |
|
33 |
25 |
|
25 |
|
|
3 |
18 |
24 |
24 |
32 |
42 |
45 |
37 |
55 |
47 |
|
62 |
57 |
|
59 |
40 |
|
40 |
25 |
|
28 |
375 |
1 |
11 |
17 |
9 |
18 |
15 |
22 |
13 |
25 |
20 |
|
28 |
22 |
|
27 |
17 |
|
25 |
13 |
|
22 |
2 |
12 |
20 |
14 |
23 |
27 |
32 |
23 |
39 |
33 |
|
40 |
34 |
|
36 |
23 |
|
31 |
16 |
|
25 |
|
|
3 |
14 |
23 |
18 |
28 |
39 |
42 |
32 |
53 |
46 |
|
52 |
47 |
|
45 |
30 |
|
37 |
19 |
|
28 |
440 |
1 |
10 |
17 |
10 |
18 |
14 |
21 |
11 |
23 |
19 |
|
26 |
19 |
|
26 |
13 |
|
24 |
10 |
|
22 |
2 |
11 |
20 |
13 |
23 |
24 |
30 |
18 |
35 |
29 |
|
36 |
29 |
|
34 |
15 |
|
29 |
11 |
|
24 |
|
|
3 |
12 |
23 |
17 |
28 |
35 |
39 |
25 |
47 |
40 |
|
46 |
39 |
|
42 |
18 |
|
34 |
12 |
|
26 |
Примечание. Принятые обозначения: а – для глушителей на линии всасывания; б – для глушителей на линии выхлопа.
4.11.5. Снижение вибрации путем вибропоглощения и виброизоляции
Воздействие вибрации на человека приведено на рис. 4.35.
Рис. 4.35. Воздействие вибрации на человека
Опасные уровни вибрации могут быть значительно снижены путем применения вибропоглощающих и виброизолирующих устройств и материалов [12].
Вибропоглощение. Вибропоглощение заключается в уменьшении амплитуды колебаний аппарата или его отдельных частей. Вибропоглощение обеспечивается облицовкой вибрирующих поверхностей специальными жесткими или мягкими демпфирующими покрытиями.
В качестве жестких покрытий используют пластмассы с динамическим модулем упругости 100…1000 МПа. Жесткие покрытия более эффективны для снижения вибрации на низких и средних частотах.
250

Для уменьшения высокочастотных вибраций используют мягкие покрытия, имеющие динамический модуль упругости порядка 10 МПа (мягкие резины и пластмассы, различные мастики).
Обычно вибропоглощающие покрытия крепят к аппаратам при помощи клея, можно также наносить их на аппараты путем напыления. Практически толщину вибропоглощающего слоя принимают не более двух-трех толщин стенки защищаемого оборудования.
Сведения о некоторых материалах, применяемых в качестве вибропоглощающих покрытий, приведены в табл. 4.49.
Таблица 4.49. Характеристики вибропоглощающих материалов [12]
Материал |
Плотность, г/см3 |
Модуль упру- |
Рабочий диапазон |
|
|
|
гости, МПа |
температур, °С |
|
Пластикат |
1,52 |
700 |
От –20 |
до 100 |
Паронит |
2 |
100 |
От –20 |
до 150 |
Герметик |
1 |
100 |
От –60 |
до 110 |
Асбокартон согласно |
1 |
580 |
От –20 |
до +450 |
ГОСТ 2850–80* |
|
|
|
|
Виброизоляция. Виброизоляция аппаратов заключается в создании упругой связи путем установки амортизаторов между источником колебаний и поддерживающей его конструкцией. В качестве амортизаторов используют стальные пружины или упругие прокладки из резины, пробки, стекловолокна. Однако применение амортизаторов без предварительного расчета может привести к возникновению резонанса и увеличить передачу динамических сил на основание. Эффективность виброизоляции характеризуется коэффициентом передачи силы на основание К, который зависит от отношения частоты возмущающей силы к частоте собственных вертикальных колебаний системы, состоящей из аппарата, опорной плиты и виброизоляторов. Пренебрегая затуханием, получаем [12]
К = [(f / f0z )2 − 1]−1 , |
(4.21) |
где f – частота колебаний системы под действием возмущающей силы, Гц; f0z – частота собственных вертикальных колебаний системы, Гц. Из формулы (4.21) следует:
1)при f < f0z система имеет упругое сопротивление, сила действует как статическая и полностью передается основанию;
2)при f = f0z возникает явление резонанса;
3) при f ≥ 2 f0z система оказывает инерционное сопротивление и эффективность
виброизоляторов возрастает с увеличением частоты колебания.
Следовательно, условием надежной работы виброизоляторов является обеспечение со-
отношения f0z = f / 2 .
Известно [12], что при отношениях частот, равных 2,5; 3; 4; 5, эффективность виброизоляции составляет соответственно 81; 87,5; 93 и 96 %.
Частота собственных колебаний системы
f0z = 5xст−0,5 . |
(4.22) |
Здесь хст – статическая осадка виброизолятора, см: |
|
xст = m / Kz = hσ/ E , |
(4.23) |
где m − суммарная масса аппарата и опорной плиты, кг; Кz – упругость виброизолятора в вертикальном направлении, кг/см; h – высота виброизолятора, см; σ = mg/F – напряжение в
материале виброизолятора, МПа (F – площадь всех виброизоляторов, м2); Е − модуль упругости амортизатора, МПа.
Если динамический модуль упругости материала виброизолятора отличается от статического, то частоту собственных колебаний системы определяют по формуле
251
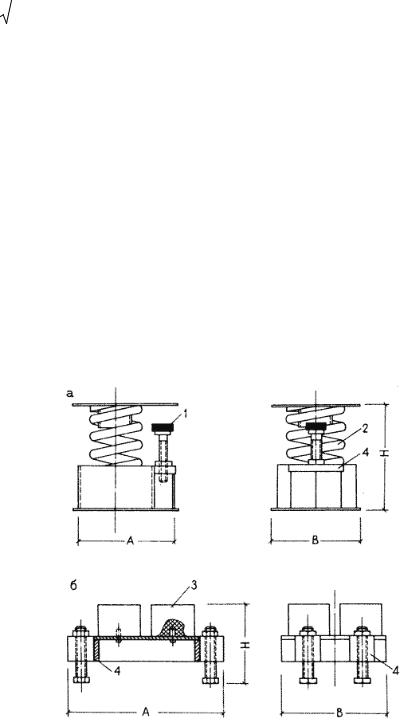
f0z = 5 |
|
, |
|
Eдин /(xст Ест ) |
(4.24) |
где Един, Ест – соответственно динамический и статический модули упругости материала виброизолятора, МПа.
Пружинные амортизаторы (рис. 4.36, а) могут использоваться для ослабления вибрации любых частот, но наиболее эффективны на частотах ниже 15 Гц. Расчет пружинного амортизатора сводится к определению диаметра пружины и числа витков. Методика определения размеров пружин и основных параметров витков приведена в ГОСТ 13764–68*–ГОСТ 1377668.
Резиновые амортизаторы (рис. 4.36, б) рекомендуется применять для снижения среднечастотных и высокочастотных вибраций. Расчет резиновых амортизаторов сводится к определению их количества, поперечных размеров и высоты. В качестве высоты резинового амортизатора принимают высоту его деформируемой части [12]
Н = хст Един / σ, |
(4.25) |
где Един – динамический модуль упругости резины, МПа; σ – расчетное статическое напря-
жение в резине, МПа, σ = P / F; Р − нагрузка, приходящаяся на все резиновые виброизоляторы, МН; F – площадь поперечного сечения всех виброизоляторов, м2.
Резиновые амортизаторы должны выполняться в виде ребристых или дырчатых плит, обеспечивающих свободное расширение резины в стороны. При использовании для изготовления амортизаторов листовой резины каждый амортизатор должен иметь вид ленты с отношением толщины к ширине не более 1 : 3.
Рис. 4.36. Амортизаторы (разработаны ЦНИИ Промзданий)
а – пружинный виброизолятор марки ВП -1 – ВП-5; б – резиновый виброизолятор марки ВР-1 – ВР-3; 1 – резиновая прокладка; 2 – пружина; 3 – резиновый элемент; 4 – опорная часть
При необходимости снижения низкочастотных вибраций, начиная с 4–6 Гц, рекомендуется применять комбинированные металлорезиновые амортизаторы (рис. 4.37).
При установке любых амортизаторов необходимо соблюдать следующее условие: центр жесткости амортизатора и центр тяжести приходящейся на него нагрузки должны находиться на одной вертикали. В комбинированных амортизаторах центры жесткости пружин и резины также должны быть на одной вертикали.
Центром жесткости системы амортизаторов называется точка, через которую проходит равнодействующая реакций всех амортизаторов при одинаковой их деформации [12].
252
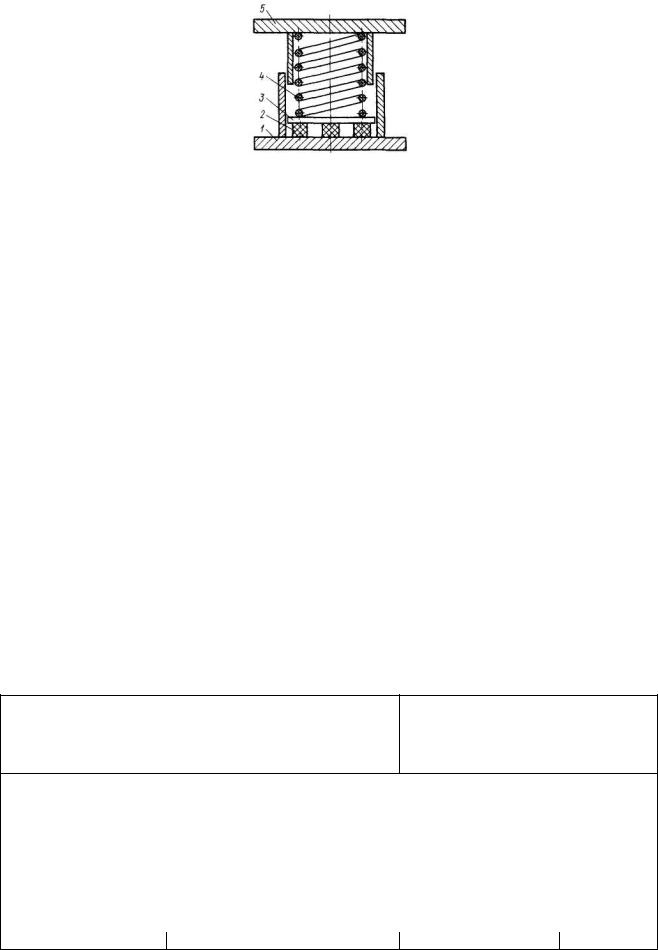
Рис. 4.37. Схема комбинированного амортизатора: 1 – нижняя плита; 2 – резиновая шайба; 3 − металлическая шайба; 4 – пружина; 5 – опорная плита
4.11.6. Определение шумовых и вибрационных характеристик
В соответствии с ГОСТ 12.1.023–80* основной шумовой характеристикой производственного оборудования являются уровни звуковой мощности в октавных полосах со среднегеометрическими частотами 63, 125, 250, 500, 1000, 2000, 4000 и 8000 Гц. В обоснованных случаях, например для оборудования, которое комплектуется непосредственно на предпри- ятиях-потребителях, в качестве шумовой характеристики допускается принимать уровни звукового давления в указанных выше октавных полосах частот. При этом измерения должны выполняться не менее чем в трех контрольных точках. Для аппаратов с механическими перемешивающими устройствами в качестве нормируемой шумовой характеристики кроме уровня звукового давления допускается применять эквивалентный уровень звука, измеренный по характеристике А шумомера (ГОСТ 17187–81).
Предельно допустимые значения шумовых характеристик аппаратов (ПДШХ) в процессе их разработки определяют в соответствии с требованиями ГОСТ 12.1.003–83 и ГОСТ 12.1.023–80* с учетом условий размещения аппаратов и допускаемых уровней звукового давления на рабочих местах (табл. 4.50). Уровень звуковой мощности для каждой октавной полосы определяется по формуле, дБ
Lpi = Li + 10lg(F / F1 )− ∆L , |
(4.26) |
где Li – допускаемый уровень звукового давления на рабочем месте, дБ (по табл. 4.50); F– площадь измерительной поверхности (полусферы), м2, определяемая по формуле F = 2πR2 (R
– расстояние от рабочего места до центра проекции аппарата на его основании, м); F1 – па-
раметр, равный 1 м2; ∆L – поправка на групповую установку аппаратов в типовых условиях эксплуатации, дБ (табл. 4.51).
Таблица 4.50. Допускаемые уровни звукового давления и эквивалентные уровни звука на рабочих местах, ГОСТ 12.1.003 – 83
|
Постоянные рабочие места и рабочие |
Среднегеометрическая |
зоны в производственных помещени- |
частота октавных полос, |
ях и на территории предприятий, по- |
Гц |
стоянные рабочие места стационар- |
|
ных машин |
Кабины наблюдения и дистанционного
управления
с речевой связью по те- |
без |
речевой |
связи по теле- |
||
лефону |
фону |
|
|
|
Допускаемый уровень звукового давления Li, дБ
63 |
|
99 (95) |
83 |
94 (91) |
125 |
|
92 (87) |
74 |
87 (83) |
250 |
|
86 (82) |
68 |
82 (77) |
500 |
|
83 (78) |
63 |
78 (73) |
1000 |
|
80 (75) |
60 |
75 (70) |
2000 |
|
78 (73) |
57 |
73 (68) |
4000 |
|
76 (71) |
55 |
71 (66) |
8000 |
|
74 (69) |
54 |
70 (64) |
Эквивалентный уровень звука, дБА |
|
|
|
|
− |
85 (80) |
65 |
80 (75) |
Примечание. В скобках приведены уровни звукового давления по «Санитарным нормам допус-
253

тимых уровней шума на рабочих местах». Утв. Главным санитарным врачом СССР 12.03.85, № 3223
– 85.
Для одиночно устанавливаемых аппаратов ∆L = 0.
Уровень шума аппаратов химических производств, установленных в помещениях и на открытых площадках, измеряется в соответствии с ГОСТ 12.1.028–80. При необходимости получения более точных шумовых характеристик измерения выполняются согласно ГОСТ
12.1.024–81*, ГОСТ 12.1.027–80.
Согласно ГОСТ 12.1.023–80*, контроль шумовых характеристик должен проводиться в ходе приемочных периодических и типовых испытаний аппаратов.
В паспорте или инструкции по эксплуатации аппарата указывают шумовые характеристики, полученные в процессе испытания аппарата, или предельно допускаемые шумовые характеристики, рассчитанные по формуле (47).
Таблица 4.51. Поправка ∆L в зависимости от габаритных размеров аппарата
Габаритные |
|
|
|
|
размеры аппа- |
До 1,5 |
Св. 1,5 до 3,5 |
Св. 3,5 до 5,0 |
Св. 5,0 |
рата, м |
|
|
|
|
∆L, дБ |
10 |
6 |
3 |
0 |
В качестве защиты от шума могут применяться защитные кожухи (рис. 4.38).
Рис. 4.38. Конструкция шумозащитного кожуха:
1 – кожух; 2 – звукоизолирующий материал; 3 – источник шума; 4 – виброизолирующая прокладка
Вибрационной характеристикой аппаратов химических производств являются среднеквадратические значения виброскорости в октавных полосах частот 2, 4, 8, 16, 31,5 и 63 Гц, измеренные на головках болтов, крепящих аппараты к фундаменту, или на площадке перекрытия. Значения вибрационных характеристик устанавливаются исходя из условий обеспечения безопасности конструкции аппарата с учетом требований гигиенических норм вибрации на рабочих местах. Гигиенические нормы вибрации при определении методом частотного анализа приведены в табл. 4.52.
Таблица 4.52. Гигиенические нормы общей вибрации на рабочих местах в производственных помещениях, ГОСТ 12.1.012–78*
|
|
|
Значение параметра при среднегеометрической частоте ок- |
|||||
Параметр |
|
|
тавной полосы, Гц |
|
|
|
|
|
|
|
|
2 |
4 |
8 |
16 |
31,5 |
63 |
Средняя |
квадратическая |
1,30 |
0,45 |
0,22 |
0,22 |
0,22 |
0,22 |
|
виброскорость, см/с |
|
|||||||
|
|
|
|
|
|
|
||
Логарифмический |
уровень |
108 |
99 |
93 |
92 |
92 |
92 |
|
виброскорости, дБ |
|
|||||||
|
|
|
|
|
|
|
В паспорт или инструкцию по эксплуатации аппарата вносят значения вибрационных характеристик, измеренные согласно ГОСТ 12.1.034–81 в ходе испытаний аппарата.
При необходимости применения виброизолирующих устройств или при возможности передачи вибрации на несущие строительные конструкции вибрационная характеристика
254
аппарата должна содержать следующие данные: направление и характер прилагаемой нагрузки (сосредоточенные силы, моменты, распределенные нагрузки); характер изменения нагрузки во времени (период и амплитуда колебаний); скорость убывания частоты вращения вала аппарата; положение центра масс аппарата; моменты инерции аппарата относительно центральных осей [10].
Вибрационные характеристики не вносятся в паспорта аппаратов, у которых динамические нагрузки, передаваемые основанию, равны или меньше 50 Н.
4.12. Требования эргономики
4.12.1. Показатели эргономики
Эргономика – это дисциплина, изучающая функциональные возможности человека в трудовых процессах, выявляющая возможности и закономерности создания оптимальных условий для высокопроизводительного труда и обеспечения необходимых удобств, содействующих развитию способностей работника.
Для изделий отрасли химического и нефтяного машиностроения определяются следующие эргономические показатели: температура поверхности аппарата в зоне обслуживания; уровень шума и ультразвука; вибрация; соответствие конструкции и формы аппарата антропометрическим данным; выделение газов, пыли и вредных веществ; удобство монтажа, обслуживания и ремонта аппарата.
Ниже приведено примерное содержание работ по эргономике на различных стадиях создания аппаратов.
На стадии разработки технического задания: анализ эргономических характеристик аналогов и прототипов разрабатываемого аппарата; ориентировочное распределение функций в системе человек – машина; определение ориентировочных требований эргономики на основе нормативных документов.
На стадии разработки технического предложения и эскизного проекта: конкретизация и реализация ориентировочных показателей эргономики, относящихся к оборудованию, рабочему месту, производственной среде; эргономическая оценка вариантов проекта; проведение исследований в лабораторных и производственных условиях в целях уточнения алгоритмов работы и показателей эргономики.
На стадии разработки технического проекта: проверка выполнения требований эргономики, намеченных на стадии технического задания; окончательное распределение функций в системе человек–машина.
На стадии разработки рабочих чертежей и изготовления аппарата: разработка требований эргономики в инструкции по эксплуатации; эргономическая оценка качества изготовления аппарата.
На стадии испытания и эксплуатации аппарата: анализ и экспертная оценка эргономических показателей в условиях эксплуатации; разработка предложений по совершенствованию эргономических характеристик аппарата; корректировка технической документации.
При решении задач эргономики в процессе конструирования оборудования целесообразно следующее разделение функций между человеком и машиной:
1)функции машины: высокая надежность в работе; стойкость к агрессивным воздействиям технологической среды; применение значительных механических усилий и энергетических затрат; монотонность проводимых операций; высокая скорость реакции на сигналы; плавность и точность приложения усилий; переработка и хранение больших объемов информации;
2)функции человека: решение задач планирования, программирования и контроля технологического процесса; принятие решений в непредвиденных ситуациях; высокая чувствительность к различным сигналам; многообразие ответных реакций; приспособление к изменяющимся условиям.
255
4.12.2. Критерии физической нагрузки
Физические нагрузки разделяются на оптимальные (не приводящие в конце смены к выраженному утомлению, оказывающие тренировочное действие, повышающие функциональные возможности организма) и допустимые (не вызывающие к концу смены чрезмерного утомления и отклонений в состоянии здоровья в течение всего трудового периода).
Выполняемую человеком динамическую работу при перемещении какого-либо тела определяют по формуле [21]
A = 6gm(H + 0,5H1 + 0,11l), |
(4.27) |
где m – масса перемещаемого тела, кг; H – высота подъема тела из исходного положения, м;
Н1 − высота спуска тела, м; l – расстояние, на которое перемещается тело по горизонтали, м. Среднее значение развиваемой человеком мощности при совершении динамической работы находят по формуле
N = A/ τ, |
(4.28) |
где N – мощность, Вт; τ – время всей рабочей смены, с.
Статическая нагрузка, связанная с приложением человекам усилия без перемещения тела или его отдельных частей, характеризуется произведением величины усилия на время его приложения. В случае различных усилий статическая нагрузка определяется отдельно для каждого из них и полученные величины суммируются.
В зависимости от общих энергозатрат все выполняемые человеком работы разделяются на три категории тяжести:
Затрачиваемая мощность, Вт |
<172 |
172–293 |
>293 |
Категория тяжести физической работы |
Легкая |
Средняя |
Тяжелая |
4.12.3. Требования к размещению органов управления и средств Отображения информации на аппаратах
Органы управления предназначены для передачи управляющих воздействий от человека к производственному оборудованию. В целях обеспечения безопасности персонала органы управления должны исключать возможность самопроизвольного включения и выключения производственного оборудования, иметь форму и размеры, удобные для работы, располагаться в рабочей зоне так, чтобы расстояние между ними не затрудняло выполнения операций.
Для привода органов управления, размещаемых непосредственно на аппаратах химических и нефтехимических производств, следует использовать маховики, штурвалы и кривошипные рукоятки. Маховики и штурвалы применяют для медленного вращения в условиях, требующих приложения значительных физических усилий. Конструкция маховиков и штурвалов должна отвечать требованиям ГОСТ 21752–76*. Кривошипные рукоятки применяют для быстрого вращения органов управления при относительно небольших усилиях. Радиус
(плечо) кривошипной рукоятки при моментах до 2,5 Н м должен находиться в пределах
12…75 мм, при моментах 2,5…5,0 Н м – в пределах 100…200 мм. Просвет между окружностями вращения соседних кривошипных рукояток: при вращении одной рукоятки – 60…100 мм; при вращении обеих рукояток одновременно – 75…125 мм.
Органы управления при выполнении работ стоя следует размещать в пределах зон, указанных на рис. 4.36, с учетом частоты их использования. Степень частоты использования органов управления определяется из следующих условий (ГОСТ 12.2.033–78):
Число операций в час |
До 2 |
Св. 2 до 120 |
Св. 120 |
Частота использования |
Редко |
Часто |
Очень часто |
Органы управления, часто используемые при выполнении тяжелых работ, не допускается располагать выше 1000 мм от уровня площадки, на которой стоит рабочий. Органы управления, используемые менее пяти раз в смену, допускается располагать за пределами
256

зоны досягаемости (зона 3 на рис. 4.39).
Аварийные органы управления должны быть расположены в пределах зоны досягаемости, отличаться формой от остальных элементов управления, иметь надписи о назначении и исключать возможность пуска аппарата до устранения аварийной ситуации. Если аппараты, представляющие повышенную опасность для обслуживающего персонала, находятся вне пределов видимости оператора, то следует предусмотреть дополнительные аварийные выключатели.
Рис. 4.39. Зоны размещения органов управления на аппаратах: а – в вертикальной плоскости; б – в горизонтальной плоскости; 1 – для очень часто используемых органов управления;
2 – для часто используемых органов управления; 3 –для редко используемых органов управления; 4 – край рабочей поверхности
Общие требования к расположению органов управления при выполнении работ стоя приведены в ГОСТ 12.2.033–78.
Средняя высота расположения средств отображения информации при работе стоя составляет 1365 мм. Рекомендуемые зоны зрительного наблюдения в вертикальной и горизонтальной плоскостях приведены на рис. 4.40.
В соответствии с требованиями Ростехнадзора [26] запрещается установка показывающих манометров на высоте более 5 м от уровня площадки обслуживания.
Рис. 4.40. Зоны зрительного наблюдения: а – в вертикальной плоскости; б – в горизонтальной плоскости;
1 – горизонтальная линия взгляда: 2 – нормальная линия взгляда; 3 – сагиттальная плоскость
4.12.4. Требования к сигнальной окраске, надписям и знакам безопасности
Поверхности аппаратов или их отдельные элементы, которые могут служить источником опасности для обслуживающего персонала, окрашивают в соответствующие сигнальные цвета.
Красный сигнальный цвет применяется для обозначения отключающих устройств, в том числе для рукояток кранов аварийного сброса давления и кнопок аварийного отключения электрооборудования; для окраски внутренних поверхностей открывающихся ограждений и корпусов; для окраски стекол сигнальных ламп) извещающих о нарушении условий безопасности.
Желтый сигнальный цвет применяется для окраски элементов аппаратов, неосторожное обращение с которыми представляет опасность для работающих. В желтый цвет окра-
257
шиваются движущиеся элементы аппаратов и кромки ограждений, не полностью закрывающих движущиеся элементы аппаратов. Желтая полоса шириной 50–150 мм наносится на емкости, содержащие вещества с опасными для человека свойствами.
Зеленый сигнальный цвет применяется для предписывающих знаков и сигнальных
ламп.
Синий сигнальный цвет применяется для указательных знаков.
На аппараты, представляющие повышенную опасность для обслуживающего персонала, наносят запрещающие и предупредительные знаки.
Запрещающий знак представляет собой круг красного цвета с белым полем внутри, белой каймой по контуру знака и символическим изображением черного цвета внутри, перечеркнутым полосой красного цвета с углом наклона 45°. Ширина красного кольца составляет 0,09–0,1 внешнего диаметра, ширина наклонной полосы – 0,08 внешнего диаметра знака, ширина белой каймы – 0,02 внешнего диаметра знака.
Предупредительный знак представляет собой равносторонний треугольник желтого цвета со скругленными углами, обращенный вершиной вверх, с каймой черного цвета шириной 0,05 стороны и символическим изображением опасности, выполненным черным цветом.
Допускается применять запрещающие и предупредительные знаки с пояснительной надписью черного цвета. При этом на запрещающих знаках наклонную красную полосу не наносят. Поясняющие надписи можно выполнять на табличках, помещенных над знаком безопасности. Таблички должны окрашиваться в цвет знака или иметь белый цвет с черными поясняющими надписями.
В соответствии с Правилами Ростехнадзора [26] баллоны, содержащие сжатые, растворенные и сжиженные газы, а также цистерны и бочки для транспортирования сжиженных газов должны иметь соответствующую окраску и надписи. Цвета окраски сосудов и текст надписей приведены в табл. 4.53.
Таблица 4.53. Цвета окраски баллонов и бочек и наносимых на них надписей [26]
|
Текст надписи на баллоне, |
Окраска корпу- |
|
|
||
Сосуд |
содержащем |
соответст- |
Цвет надписи |
Цвет полосы |
||
|
вующий газ |
|
са |
|
|
|
|
|
|
|
|
||
|
Азот |
|
Черная |
Желтый |
Коричневый |
|
|
Аммиак |
|
Желтая |
Черный |
− |
|
|
Аргон технический |
Черная |
Синий |
Синий |
||
|
Ацетилен |
|
Белая |
Красный |
− |
|
|
Бутилен |
|
Красная |
Желтый |
Черный |
|
|
Бутан |
|
Красная |
Белый |
− |
|
|
Водород |
|
Зеленая |
Красный |
− |
|
|
Воздух |
|
Черная |
Белый |
− |
|
|
Гелий |
|
Коричневая |
Белый |
− |
|
|
Закись азота |
|
Серая |
Черный |
− |
|
|
Кислород |
|
Голубая |
Черный |
− |
|
Баллон |
Сероводород |
|
Белая |
Красный |
Красный |
|
Сернистый ангидрид |
Черная |
Белый |
Желтый |
|||
|
||||||
|
Углекислота |
|
Черная |
Желтый |
− |
|
|
Фосген |
|
Защитная |
− |
Красный |
|
|
Хладон-11 |
|
Алюминиевая |
Черный |
Синий |
|
|
Хладон-12 |
|
Алюминиевая |
Черный |
− |
|
|
Хладон-13 |
|
Алюминиевая |
Черный |
Две красные |
|
|
Хладон-22 |
|
Алюминиевая |
Черный |
Две желтые |
|
|
Хлор |
|
Защитная |
− |
Зеленый |
|
|
Циклопропан |
|
Оранжевая |
Черный |
− |
|
|
Этилен |
|
Фиолетовая |
Красный |
− |
|
|
Другие горючие газы |
Красная |
Белый |
− |
||
|
Другие негорючие газы |
Черная |
Желтый |
− |
258
Продолжение табл. 4.53
|
|
Текст надписи на баллоне, |
Окраска корпу- |
|
|
|
Сосуд |
|
содержащем |
соответст- |
Цвет надписи |
Цвет полосы |
|
|
|
вующий газ |
|
са |
|
|
|
|
|
|
|
|
|
|
|
Аммиак |
|
|
Черный |
Желтый |
Цистерна |
или |
Хлор |
|
|
Зеленый |
Защитный |
Фосген |
|
Любой цвет |
Красный |
Защитный |
||
бочка |
|
Кислород |
|
Черный |
Голубой |
|
|
|
|
||||
|
|
Другие негорючие газы |
|
Желтый |
Черный |
|
|
|
Горючие газы |
|
|
Черный |
Красный |
259