
SMU_METROLOGIA
.pdfна противоположный торец удлинителя, когда тот будет навинчен на го- ловку нутромера.
ВНИМАНИЕ: Каждый раз после навинчивания (отвинчивания) удли-
нителей снова ввинтить съемный измерительный наконечник в корпус нутромера.
|
|
|
|
Результаты измерений детали |
|
|
|
Табл. 8.2 |
|||||||
|
|
|
|
|
|
|
|
|
|
||||||
№ |
размер – |
|
|
размер – |
|
|
|
размер – |
|
|
|
|
|||
п/п |
по осн. |
|
по доп. |
размер |
по осн. |
|
по доп. |
размер |
|
по осн. |
|
по доп. |
|
размер |
|
|
шкале |
|
шкале |
|
шкале |
|
шкале |
|
|
шкале |
|
шкале |
|
|
|
|
мм |
|
мм |
мм |
мм |
|
мм |
мм |
|
мм |
|
мм |
|
мм |
|
1 |
|
|
|
|
|
|
|
|
|
|
|
|
|
|
|
|
|
|
|
|
|
|
|
|
|
|
|
|
|
|
|
2 |
|
|
|
|
|
|
|
|
|
|
|
|
|
|
|
|
|
|
|
|
|
|
|
|
|
|
|
|
|
|
|
3 |
|
|
|
|
|
|
|
|
|
|
|
|
|
|
|
|
|
|
|
|
|
|
|
|
|
|
|
|
|
|
|
|
|
|
|
|
|
|
|
|
|
|
|
|
|
|
|
6 |
|
|
|
|
|
|
|
|
|
|
|
|
|
|
|
|
|
|
|
|
|
|
|
|
|
|
|
|
|
|
|
ср. |
|
|
|
|
|
|
|
|
|
|
|
|
|
|
|
|
|
|
|
|
|
|
|
|
|
|
|
|
|
|
|
4. Измерить отверстие.
4.1.Для этого, предварительно, установив нутромер на приблизи- тельный размер, ввести его в измеряемое отверстие, уперев один из изме- рительных наконечников (неподвижный наконечник) в поверхность отвер- стия, а другой постепенно выдвигать поворотом барабана.
При этом осторожно покачивать нутромер в поперечной плоскости относительно оси отверстия до нахождения наибольшего значения диа- метра отверстия и в продольной плоскости (вверх-вниз) до нахождения наименьшего значения (до легкого заклинивания).
При выполнении этих процедур, нутромер должен плотно скользить своими измерительными поверхностями по поверхности отверстия в дета- ли без перекосов и заеданий.
4.2. После этого считать размер с обеих шкал (основной и дополни- тельной) и прибавить к значению по основной шкале размер самого нут- ромера (обычно 75мм), а также и размер удлинителя(ей) (если использо- вали). Измерение производится не менее трех раз. Данные занести в соот- ветствующие графы таблицы 8.2 отчета.
5.Рассчитать действительные (фактические) размеры внутреннего диаметра детали, просуммировав соответствующие графы таблицы 8.2 от- чета (размер по основной шкале и размер по дополнительной шкале).
6.Определить среднее значение внутреннего диаметра.
51
7.Показать данные промеров детали преподавателю. При необходи- мости сделать повторные замеры.
8.Оформить чистовой отчет.
9.Подготовиться к защите.
8.2.3. ИЗМЕРЕНИЕ ДЕТАЛЕЙ МИКРОМЕТРИЧЕСКИМ ГЛУБИНОМЕРОМ
1.Протереть измерительные поверхности траверсы сухой мягкой льняной тряпкой.
2.Установить измерительный стержень, соответствующий данному
размеру.
3.Проверить нулевую установку глубиномера. В случае неправиль- ной установки произвести установку на нуль (см. п. 8.1.8.).
4.Измерить глубину в соответствии с чертежом детали. Измерение каждого размера производится не менее 6 раз. При измерении плотно прижать рукой траверсу 1 (см. рис. 8.6 а) с обеих сторон от микрометрической головки к поверхности измеряемой детали.
Микрометрический винт вращать за трещотку до третьего щелчка (аналогично микрометру). Зафиксировать стопорный винт.
5.Снять показания с микрометрической головки (аналогично мик- рометру), помня при этом, что размер измерительного стержня 0-25 мм равен 0 мм, 25-50 мм равен 25 мм и т.д. Информацию о длине измери- тельного стержня можно узнать из рисунка 6б или путем сравнения их с «нулевым» (самый маленький в наборе).
6.Данные замеров глубины занести в соответствующие графы таб- лицы 8.2 отчета.
7.Рассчитать действительные (фактические) размеры глубины от- верстия или уступа детали просуммировав соответствующие графы табли- цы 2 отчета (размер по основной шкале и размер по дополнительной шка- ле). Определить среднее значение глубины.
8.Показать данные промеров детали преподавателю. При необходи- мости сделать повторные замеры.
9.Оформить чистовой отчет.
10.Подготовиться к защите.
8.3. ПЕРЕЧЕНЬ ВОПРОСОВ К ЗАЩИТЕ
1.Виды микрометрических инструментов и область их применения.
2.Существующие методы измерения и методы, применяемые при работе с микрометрическими инструментами.
52
3.Преимущества и недостатки микрометрических инструментов пе- ред другими типами мерительных инструментов.
4.Порядок измерения микрометрическими инструментами.
5.Факторы, влияющие на увеличение погрешности измерения мик- рометрическими инструментами.
6.Общие узлы и детали микрометрических инструментов.
7.Методика настройки микрометрических инструментов на ноль и проверка правильности настройки.
8.Указать механизм, на применении которого основана конструкция всех микрометрических инструментов.
9.Определить по техническим характеристикам погрешность мик- рометрических инструментов.
10.Указать, с какой точностью возможно произвести измерения де- тали данным микрометрическим инструментом.
11.Сравнить по методам измерения микрометрические инструменты
ирычажно-зубчатые (рычажную скобу и рычажный микрометр).
12.Какова связь шага микрометрического винта с ценой деления микрометрических инструментов.
13.Роль трещотки в конструкции микрометрических инструментов.
14.Назначение вставок (удлинителей) в конструкции микрометри- ческих инструментов и порядок работы с ними.
9. ЛАБОРАТОРНАЯ РАБОТА № 3 ИЗМЕРЕНИЕ ПОВЕРХНОСТЕЙ ДЕТАЛЕЙ ПРИ ПОМОЩИ
РЫЧАЖНО-ЗУБЧАТЫХ ПРИБОРОВ
Цель работы:
1.Ознакомиться с устройством и принципом действия рычажно- зубчатых приборов, овладеть навыками работы на них;
2.Произвести измерения партии деталей типа цилиндр с помощью рычажной скобы, определить вид отклонения формы поверхности деталей;
3.Произвести измерения партии деталей типа клапан ДВС с помо- щью рычажного микрометра, построить гистограмму распределения дей- ствительных размеров деталей;
9.1. ТЕОРЕТИЧЕСКАЯ ЧАСТЬ
Рычажная скоба и рычажный микрометр относятся к группе рычаж- но-зубчатых измерительных приборов и широко применяются в измери- тельных лабораториях, контрольных пунктах и на рабочих местах, особен-
но при работе на шлифовальных станках для контроля наружных размеров деталей 6 и 7 квалитетов.
Рычажные микрометры и скобы отличаются высокой точностью из-
мерений и значительно ускоряют процесс измерения за счет применения
53
относительного метода. Рычажно-зубчатые инструменты часто использу- ются вместо предельных калибров-скоб, так как обладают рядом преиму- ществ по сравнению с ними.
Основные преимущества:
1.Точность контроля выше, так как в рычажной скобе и рычажном микрометре обеспечивается постоянство измерительного давления.
2.Возможность установления абсолютной величины части припуска, которая еще подлежит снятию при обработке, в отличие от контрольных калибров, которые лишь фиксируют годность детали.
3.Возможность определения абсолютных величин отклонения от геометрической формы.
4.Применение рычажных скоб и микрометров резко (в несколько де- сятков раз) сокращает номенклатуру предельных калибров-скоб.
9.1.1. РЫЧАЖНАЯ СКОБА
Рычажная скоба является прибором для относительных измерений.
Основной особенностью конструкции рычажной скобы является сочетание рычажной и зубчатой передач, которое позволяет резко уменьшить габари- ты прибора при сравнительно больших передаточных отношениях.
Одна из конструкций рычажной скобы показана на рис. 9.1. В цилин- дрических направляющих жесткого корпуса 9 могут перемещаться по- движная пятка 2 и регулируемая пятка 1.
Регулируемая пятка 1 служит для установки скобы на размер по бло- ку концевых мер. Для закрепления регулируемой пятки служит стопорная гайка 10 (в других конструкциях стопорный колпачок 12).
Для установки регулируемой пятки на размер сначала отвинчивается стопорная гайка 10 (в других конструкциях стопорный колпачок), затем от- винчивается предохранительный колпачок 12 и регулируемая пятка уста-
навливается в требуемом положении вращением винта подачи за накатную головку 11 (в других конструкциях за накатную гайку на регулируемой пятке).
Подвижная пятка является измерительным стержнем рычажной ско- бы. Перемещение подвижной пятки заставляет перемещаться стрелку с помощью рычажно-зубчатой передачи.
Отсчет показаний производится по шкале 5 при помощи стрелки 6.
Два подвижных ограничителя 4 позволяют настраивать скобу на контроль заданного допуска детали.
Для предохранения измерительных поверхностей скобы от износа при установке скобы на измеряемую деталь и при снятии ее с детали по- движная пятка 2 должна быть отведена нажатием кнопки 3 (Рис. 9.1).
Схема передаточного механизма рычажной скобы показана на рис.
9.2.
54
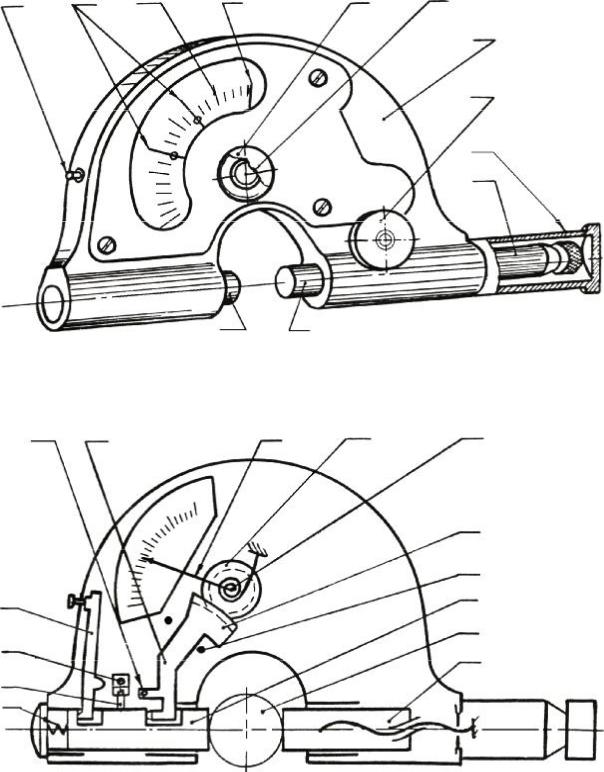
3 |
4 |
5 |
6 |
7 |
8 |
9
10
12
11
2 1
Рис. 9.1. Внешний вид рычажной скобы
14 |
4 |
9 |
10 |
11 |
|
12 |
|
|
13 |
|
8 |
3 |
|
2 |
||
7 |
||
1 |
||
|
||
6 |
|
|
5 |
|
Рис. 9.2. Внутреннее устройство рычажной скобы
При введении контролируемой детали 2 между измерительными поверхностями, подвижная пятка 3 перемещается в осевом направлении и поворачивает рычаг 4 вокруг оси 14.
55
На конце большого рычага 4 имеется зубчатый сектор 12, находя- щийся в зацеплении с шестеренкой 10. Поворот рычага 4 вызывает поворот стрелки 9, жестко закрепленной на оси шестерни 10.
Пружина 11 обеспечивает контакт рычага 4 с подвижной пяткой 3 и заставляет зубчатую передачу работать одной стороной зубьев, благодаря чему устраняется мертвый ход.
Для предостережения поворота подвижной пятки вокруг своей оси служит штифт 6, передвигающийся в пазу колодки 7.
Ограничение поворота рычага осуществляется упорами 13. Спи- ральная пружина 5, упирающаяся в подвижную пятку, обеспечивает изме- рительное давление.
Рычажные скобы выпускаются шести типоразмеров, охватывающих диапазон измерения от 0 до 150мм.
9.1.2. РЫЧАЖНЫЙ МИКРОМЕТР
Основное отличие рычажного микрометра (см. рис. 9.3) от рычаж- ной скобы состоит в том, что рычажный микрометр снабжен микрометри- ческой головкой, наличие которой дает рычажному микрометру ряд серь- езных преимуществ по сравнению со скобой.
Рычажным микрометром можно производить измерения как относи- тельным, так и абсолютным способами с непосредственной оценкой всей измерительной величины с помощью микрометрической головки.
При измерении абсолютным способом отпадает необходимость настройки рычажного микрометра по плоскопараллельным концевым ме- рам.
Кроме того, рычажный микрометр дает возможность производить измерение нескольких размеров у одной или партии деталей, что особо важно в условиях мелкосерийного и единичного производства.
При измерении партии детали рычажным микрометром относитель-
ным методом настройка микрометра на размер может производиться либо по микрометрической головке (после настройки микровинт 2 закрепляется гайкой 3), либо по блоку измерительных плиток (при проверке точных де- талей).
При измерении рычажным микрометром абсолютным методом, от-
счет размера производиться по микрометрической головке до сотых долей миллиметра, а по шкале рычажно-зубчатого механизма до тысячных долей.
Устройство рычажного микрометра (см. рис. 9.4) по микрометриче- ской головке аналогично обычному микрометру, а по рычажно-зубчатому механизму аналогично рычажной скобе.
56
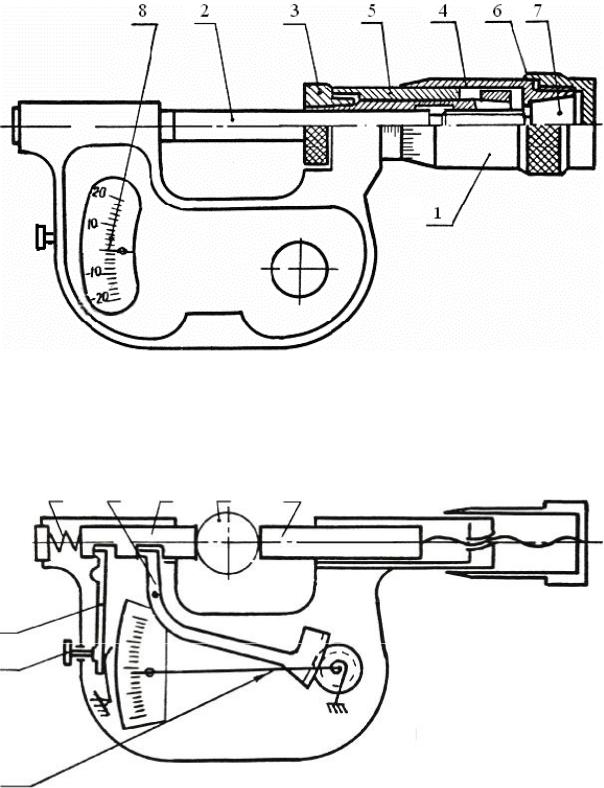
Рис. 9.3. Внешний вид рычажного микрометра
5 |
4 |
3 |
2 |
1 |
6
7
8
Рис. 9.4. Внутреннее устройство рычажного микрометра
57

Микрометрическая головка основана на применении винтовой пары. Микрометрический винт 2 (см. рис. 9.3) является регулируемой измери- тельной поверхностью. Выдвижение микрометрического винта осуществ- ляется при помощи барабана 4, который посредством колпачка 6 своей ко- нической поверхностью соединен с конусом 7 микровинта. Показания микрометрической головки снимают с основной шкалы на гильзе 5 (цена деления основной шкалы 0,5мм по верхней шкале) и с дополнительной шкалы на барабане 4 (цена деления нониуса 0,01мм). Для фиксации мик- ровинта применяется накатная гайка 3.
Схема рычажно-зубчатого механизма рычажного микрометра показа- на на рис 4. и соответствует схеме механизма рычажной скобы, описание которой произведено выше (нумерация позиций не совпадает).
Рычажные микрометры выпускаются двух типов размеров с преде- лами измерения 0-25мм и 25-50мм.
9.2.ПРАКТИЧЕСКАЯ ЧАСТЬ
9.2.1.ИЗМЕРЕНИЕ ПАРТИИ ДЕТАЛЕЙ (ЦИЛИНДРОВ) РЫЧАЖНОЙ СКОБОЙ
1.Рассчитать схему полей допусков предложенной партии деталей (цилиндров) согласно нанесенной на них маркировке по номинальному диаметру вала, посадке и квалитету по таблицам СТ СЭВ 144-75 (см. при- ложение 1 и приложение 2). Схемы расположения полей допусков цилин- дров изобразить графически в отчете (под изображением цилиндров). Обо- значить на них все размеры.
2.Взять рычажную скобу соответствующего диапазона измерений и внести ее данные (завод изготовитель, заводской номер и предел измере- ния) в таблицу 9.1. Протереть измерительные плоскости поверхности де- талей мягкой льняной тряпочкой.
Таблица 9.1
Характеристики применяемых инструментов и приборов
3.Набрать блок измерительных плиток (набор ПКМД) по ранее
рассчитанному из схемы расположения полей допусков среднему диаметру измеряемого цилиндра.
4.Отвинтить предохранительный колпачок 12 (см. рис. 9.1).
58
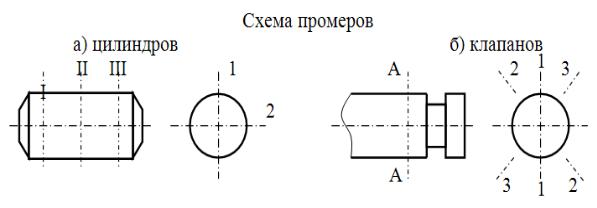
5.Отпустить стопорную гайку 10.
6.Поместить блок плиток между измерительными плоскостями ры- чажной скобы.
7.Вращать накатанную гайку 11 до тех пор, пока стрелка рычажной скобы не установится против нулевого деления шкалы (внимание: в зави-
симости от конструктивного исполнения скобы накатная гайка 11 может находиться не на правом торце микровинта 1, а ровно по середине).
8.Затянуть гайку 10. Если после затяжки гайки 10 стрелка рычаж- ной скобы отойдет от нулевого деления, установку повторить.
9.Нажав на кнопку 3, удалить блок плиток.
10.Завинтить предохранительный колпачок 12.
11.Нажав кнопку 3 ввести деталь между измерительными плоско- стями рычажной скобы.
12.Определить отклонение действительного размера детали от раз- мера блока плиток по шкале 5 с соответствующим знаком “+” или “-“. Из- мерение проводится согласно схеме промеров в трех сечениях - I, II, III и в двух положениях - 1, 2 (смотри рисунок 9.5). Данные занести в соответ- ствующие графы таблицы 9.2 отчета.
Рис. 9.5
13.Нажав кнопку 3, удалить деталь.
14.Подсчитать действительный размер детали как сумму размера блока набранных плиток и отклонения, полученного по шкале скобы.
15.Определить отклонение от геометрической формы цилиндров ис- пользуя справочную литературу или плакатный материал (овальность, боч- кообразность, вогнутость, конусность, седловидность и т.д.).
16.Повторить п. 11-15 для второго цилиндра.
17.Заполнить отчет по работе и сделать заключение о годности ци- линдров (сравнив действительные размеры со стандартными).
59
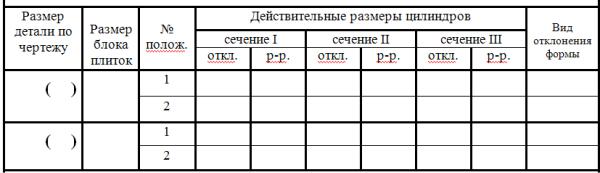
Таблица 9.2
Результаты измерений партии деталей – цилиндров
9.2.2. ИЗМЕРЕНИЕ ПАРТИИ ДЕТАЛЕЙ (КЛАПАНОВ) РЫЧАЖНЫМ МИКРОМЕТРОМ.
1.Взять рычажный микрометр соответствующего диапазона измере- ний и внести его данные (завод изготовитель, заводской номер и предел измерения) в таблицу 9.1. Протереть детали и измерительные плоскости микрометра мягкой льняной тряпочкой.
2.Проверить нулевую установку микрометра аналогично обычному микрометру (см. п. 8.1.6.) только вместо трещотки использовать нулевое показание стрелки 8 (см. рис. 9.3). Для этого свести измерительные плос- кости (для микрометра с пределами 0-25 мм) так, чтобы стрелка установи- лась против нулевого деления шкалы. При этом нулевое деление микро- метрического барабана 4 (см. рис. 9.3) должно совпадать с продольным штрихом гильзы 5, а нулевое деление основной шкалы на гильзе 5 с реб-
ром барабана 4 (не забывать, что основная шкала имеет верхнюю шкалу, смещенную на 0,5мм относительно нижней).
Если микрометр настроен неверно, затянуть гайку 3, отпустить кол- пачок 6, подать барабан 4 в осевом направлении к скобе (т.е. снять барабан
сконуса 7) и поворотом барабана 4 совместить его нулевое деление с про- дольным штрихом на гильзе 5. После этого затянуть колпачок 6, придер- живая за барабан 4 так, чтобы он не сместился. Отпустить гайку 3.
3.Повторно проверить нулевую установку (т.е. повторить п. 2). Если
погрешность нулевой установки рычажного микрометра устранить путем многократных настроек не удается, то нужно обратиться к преподавателю.
4.Произвести настройку рычажного микрометра на измерение пар- тии клапанов.
4.1.Взять из партии один любой клапан и довести измерительные плоскости микрометра до соприкосновения с его поверхностью в сечении А-А (см. рис. 9.5) так, чтобы стрелка 8 установилась против нулевого де- ления шкалы.
60