
MS / Лекция_18
.pdf168
18 СОВРЕМЕННАЯ ТЕХНОЛОГИЯ ВНЕПЕЧНОЙ ОБРАБОТКИ СТАЛИ
В настоящее время наиболее широко используются следующие способы внепечной обработки стали: раскисление и модифицирование; продувка инерт- ным газом; внепечная десульфурация; вакуумирование с целью дегазации и глубокого обезуглероживания; корректировка химического состава металла.
18.1 Раскисление стали
18.1.1 Сущность процесса раскисления и способы его реализации
Раскислением называют технологическую операцию, в ходе которой со- держание растворенного в металле кислорода понижают до требуемого уровня.
Основными задачами раскисления стали являются:
∙обеспечение необходимого характера поведения стали при затвердевании в изложницах и кристаллизаторах МНЛЗ;
∙получение продуктов раскисления (неметаллических включений), кото- рые оказывают наименьшее негативное воздействие на механические и
эксплуатационные свойства металла.
При высоком содержании кислорода в стали затвердевание ее может сопро- вождаться выделением из расплава оксида углерода в результате протекания у фронта кристаллизации реакции между растворенными в металле углеродом и ки- слородом
[C] + [O] = {CO} . |
(18.1) |
Необходимая интенсивность протекания этой реакции при затвердевании стали в изложницах и кристаллизаторах МНЛЗ определяет основные требования к организации разливки металла, а также структуру полученных слитков.
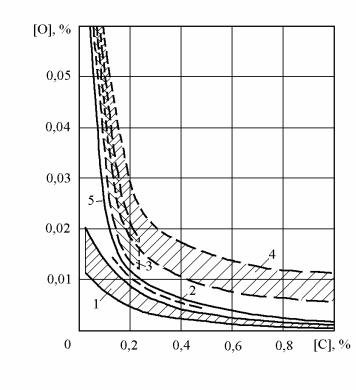
169
В зависимости от характера поведения стали при затвердевании ее приня- то подразделять на кипящую, полуспокойную и спокойную.
Затвердевание кипящей стали сопровождается выделением из металла большого количества оксида углерода, которое принято называть кипением. За- твердевание полуспокойной стали должно сопровождаться слабым, непродол- жительным кипением, для обозначения которого используют термин «искре- ние». Затвердевание спокойной стали должно протекать без видимого газовы- деления.
Основные подходы к решению первой задачи раскисления стали иллюст- рирует рисунок 18.1.
Рисунок 18.1 – Схема решения основной задачи раскисления при производстве различных типов стали: 1 – 3 – области нормального остаточного содержания ки- слорода в металле при производстве спокойной, полуспокойной и кипящей ста- ли; 4 – обычное содержание кислорода в металле перед раскислением; 5 – содер- жание кислорода в равновесии с растворенным в металле углеродом
Наиболее широко используются следующие способы раскисления стали: осаждающее, экстракционное (диффузионное) и вакуумно-углеродное.
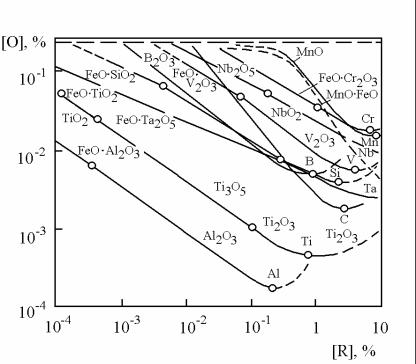
170
18.1.2 Осаждающее раскисление
При осаждающем раскислении элементы, обладающие высоким химиче- ским сродством к кислороду (раскислители), вводят непосредственно в жидкий металл. Растворяясь в нем, раскислители взаимодействуют с растворенным в стали кислородом. Так как плотность оксидов большинства раскислителей меньше плотности жидкой стали, они всплывают из металла и частично удаля- ются в шлак.
Для сравнительной оценки раскислительной способности отдельных элемен- тов-раскислителей могут быть использованы данные рисунка 18.2.
Рисунок 18.2 – Раскислительная способность элементов при 1600оС
Из приведенных данных видно, что среди широко применяемых раскислите- лей сравнительно малой является раскислительная способность марганца и хрома. Высокой раскислительной способностью отличаются алюминий и титан. Наиболее высокой раскислительной способностью обладают щелочноземельные и редкозе- мельные металлы.
171
Осаждающее раскисление получило наиболее широкое распространение главным образом благодаря простоте его реализации. Главным его недостатком является то, что за время отстаивания ковша перед разливкой из металла удаля- ются только наиболее крупные неметаллические включения. Значительная часть образовавшихся при раскислении неметаллических включений остается в стали вплоть до ее затвердевания.
Из рисунка 18.1 видно, что раскисление кипящей стали заключается лишь в некотором понижении содержания кислорода в расплаве при сохранении его на уровне выше равновесного с растворенным в металле углеродом. Обычно это достигается раскислением металла ферромарганцем при остаточном содер- жании марганца 0,3 – 0,6%. Следует также обратить внимание на то, что интен- сивное кипение стали при затвердевании возможно только при низком содер- жании углерода. В связи с этим концентрация углерода в кипящей стали обыч- но не превышает 0,27%.
При производстве полуспокойной стали содержание кислорода в металле необходимо получить несколько ниже равновесного с растворенным в металле углеродом (около 0,9 от равновесной концентрации). Только при выполнении этого условия реакция (18.1) протекает лишь в той мере, в какой она необходи- ма для заполнения газами усадочных пустот, неизбежно возникающих при кри- сталлизации слитка. В большинстве случаев при раскислении полуспокойной стали металл обрабатывают ферромарганцем и ферросилицием. Различные мар- ки полуспокойной стали содержат 0,05 – 0,5% C, 0,35 – 1,6% Mn и не более
0,12% Si.
Раскисление спокойной стали можно считать нормальным, если остаточ- ное содержание кислорода получается значительно меньше равновесного с рас- творенным в металле углеродом. Для этого достаточно иметь в готовом металле 0,4 – 0,6% марганца и 0,17 – 0,35% кремния. Дополнительно к ним для раскис- ления спокойной стали часто используют алюминий, титан, РЗМ и другие ак- тивные раскислители.
172
18.1.3 Экстракционное раскисление
При экстракционном раскислении металл выдерживают под восстанови- тельным шлаком, содержание оксидов железа в котором во много раз меньше, чем в шлаке периода окислительного рафинирования. Концентрация FeO в вос- становительных шлаках обычно не превышает 1 – 1,5%. При этом приближение системы к состоянию термодинамического равновесия протекает путем диффу- зионной массопередачи кислорода из металла в шлак. В результате этого кон- центрация кислорода в стали уменьшается, приближаясь к равновесной с вос- становительным шлаком. В литературе такой способ обработки называют так- же диффузионным раскислением.
Преимущество экстракционного раскисления перед осаждающим состоит в том, что продукты раскисления не загрязняют металл. Однако, его реализация требует дополнительного расхода шлакообразующих материалов, энергии и приводит к существенному увеличению продолжительности плавки. Кроме то- го, при выполнении этой операции в сталеплавильных агрегатах происходит полное восстановление находящегося в шлаке фосфора и переход его в сталь.
Работа кислородных конвертеров и мартеновских печей связана с необ- ходимостью непрерывной подачи кислорода в рабочее пространство агрегата. В этих условиях получение шлаков с содержанием FeO менее 3% представляет собой сложную задачу. По этой причине при выплавке стали в конвертерах и мартеновских печах экстракционное раскисление металла обычно не использу- ется.
Экстракционное раскисление стали широко используется в восстанови- тельном периоде плавки в дуговых электросталеплавильных печах. Экстракци- онное раскисление стали протекает также при обработке синтетическими шла- ками в ковше по ходу выпуска плавки и на агрегатах ковш-печь.
173
18.1.4 Вакуумно-углеродное раскисление
Вакуумно-углеродное раскисление основано на протекании реакции (18.1) в направлении образования дополнительного количества оксида углерода при понижении парциального давления СО в продуктах взаимодействия. По- нижение парциального давления СО в удаляющихся из металла пузырях газа может достигаться обработкой стали в вакууме или продувкой металла ней- тральным газом, в котором парциальное давление СО близко к нулю («химиче- ский вакуум»).
Главным преимуществом вакуумно-углеродного раскисления является то, что газообразные продукты реакции не растворяются в металле и полностью удаляются из него. Однако, реализация этого способа обработки связана с не- обходимостью наличия достаточно сложного и дорогостоящего оборудования.
При температурах внепечной обработки стали влияние парциального давления СО в продуктах реакции (18.1) на соотношение между равновесными концентрациями углерода и кислорода в металле описывает уравнение
[C][O] = 0,0025 P . |
(18.2) |
CO |
|
В настоящее время в лабораторных условиях величина остаточного дав- ления при вакуумировании может быть понижена до 0,1 Па, а при вакуумиро- вании на промышленных установках – до 100 – 200 Па. Согласно уравнению (18.2) при этом произведение равновесных концентраций углерода и кислорода при вакуумировании стали в лабораторных экспериментах должно составлять около 2,5·10–9, а в промышленных условиях – (2,5 – 5)·10–6.
Однако, реальные остаточные концентрации углерода и кислорода в ста- ли после вакуумирования на несколько порядков выше теоретических. Это объ- ясняется рядом причин, среди которых чаще других называют следующие:
∙при вакуумировании стали давление над поверхностью расплава не может быть ниже давления насыщенного пара железа при температуре обработки;
174
∙в реальных условиях на поверхности металла всегда имеется некоторое ко- личество шлака, давлением которого нельзя пренебрегать при малой величи- не остаточного давления над расплавом;
∙при малых значениях остаточного давления над поверхностью металла нель- зя пренебрегать влиянием капиллярного давления на величину парциального давления СО в поднимающихся в расплаве пузырях;
∙при исключительно малых концентрациях взаимодействующих веществ ско- рости химических реакций быстро уменьшаются, что не позволяет достичь состояния термодинамического равновесия за время обработки.
Обычно в лабораторных условиях произведение остаточных концентра- ций углерода и кислорода в стали после вакуумирования не удается получить менее 10–5, а при обработке на промышленных установках – менее (3 – 4)·10–4.
Анализ результатов промышленных исследований показывает, что соот- ношения между остаточными концентрациями углерода и кислорода в стали после вакуумирования чаще всего близки к расчетным значениям, полученным с использованием парциального давления СО равного 10 кПа. При содержании углерода в стали 0,2% и выше это позволяет после вакуумирования понижать концентрацию растворенного в металле кислорода до 0,002–0,004%. Такое со- держание кислорода значительно меньше равновесного с кремнием при обыч- ной концентрации его в стали.
В ряде случаев высокая раскислительная способность углерода в вакууме не может быть реализована в связи с поступлением кислорода из шамотной футеровки ковша, а также из оксидов железа и кремнезема в шлаке. В качестве примера на рисунке 18.3 показаны результаты исследования влияния содержания кремне- зема в ковшевом шлаке на окисленность стали после вакуумирования.
Чтобы реализовать высокую раскислительную способность углерода в ус- ловиях вакуумно-углеродного раскисления рекомендуется:
∙отказаться от использования для разливки стали ковшей с шамотной футе- ровкой;
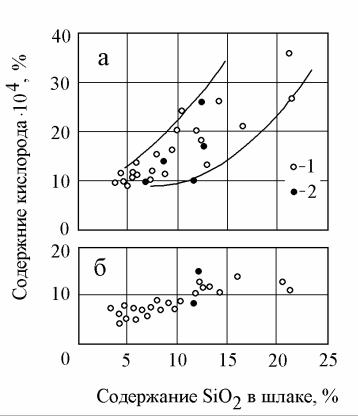
175
Рисунок 18.3 – Влияние концентрации кремнезема в шлаке и футеровки камеры на содержание кислорода в стали после вакуумирования: а – вакуумирование в печи-ковше; б – циркуляционное вакуумирование; 1 – высокоглиноземистая фу- теровка; 2 – футеровка MgO – C
∙при выпуске металла из сталеплавильного агрегата проводить мероприятия, направленные на предотвращение попадания в ковш окисленного печного шлака;
∙наводить в ковше новый шлак высокой основности с минимальным содер- жанием оксидов железа.
Вакуумно-углеродное раскисление является также эффективным спосо-
бом управления размерами оксидных неметаллических включений. Наблюдаемые в стали неметаллические включения принято подразделять
на экзогенные и эндогенные.
Экзогенные включения или включения внешнего происхождения попада- ют в металл в результате разрушения огнеупорных материалов или из шлака. Эти включения механически увлекаются потоками жидкой стали во время вы-
176
пуска и разливки и фиксируются в затвердевшем металле. Их количество обычно не велико и не превышает 5 – 10% общего количества присутствующих в стали неметаллических включений.
Основное количество наблюдаемых в стали неметаллических включений представляет собой эндогенные включения или включения внутреннего проис- хождения. Они образуются в результате протекания различных физико- химических процессов в самом металле во время его раскисления, кристалли- зации и охлаждения в жидком и твердом состоянии. Основное количество эн- догенных включений представляет собой продукты взаимодействия кислорода, серы, фосфора, углерода и азота с другими компонентами расплава.
Согласно предложенной В.И. Явойским классификации эндогенных не- металлических включений в зависимости от момента образования их подразде- ляют на первичные, вторичные, третичные и четвертичные.
Первичные эндогенные включения образуются непосредственно после ввода ферросплавов в жидкий металл, когда резко изменяется химический со- став стали и возникают благоприятные условия для протекания химических ре- акций, которые сопровождаются образованием нерастворимых в железе про- дуктов взаимодействия и выделением их из расплава в виде неметаллических включений.
Вторичные эндогенные включения образуются во время охлаждения жидкого металла от температуры раскисления до температуры кристаллизации. Возникновение их связано с тем, что все реакции раскисления являются экзо- термическими. Поэтому при понижении температуры равновесие реакций сме- щается в сторону образования дополнительного количества нерастворимых в металле оксидов.
Третичные эндогенные включения образуются в процессе кристаллиза- ции стали. Их выделение обусловлено тем, что при переходе металла из жидко- го состояния в твердое резко понижается растворимость в нем кислорода, серы и других примесей, а также продуктов их взаимодействия с компонентами рас- плава.
177
Четвертичные эндогенные включения выделяются при охлаждении затвер- девшей стали от температуры кристаллизации до комнатных температур. Их вы- деление связано с уменьшением растворимости примесей в твердом металле при понижении температуры и фазовых превращениях.
В зарубежной научно-технической литературе под первичными часто подразумевают все эндогенные включения, образовавшиеся в жидком металле до начала кристаллизации. При использовании такого определения эти включе- ния соответствуют первичным и вторичным неметаллическим включениям со- гласно классификации В.И. Явойского.
Наиболее сильное отрицательное воздействие на качество стали оказыва- ет наличие в металле крупных оксидных включений и их скоплений. Имеются экспериментальные доказательства того, что среди эндогенных включений наиболее крупными обычно являются первичные и частично вторичные вклю- чения. От момента образования этих включений до начала затвердевания стали проходит длительное время, в течение которого они могут укрупняться путем коагуляции или коалесценции, а также формировать локальные скопления. Ос- тальные включения практически не укрупняются, поэтому они имеют малые размеры и распределены в металле более равномерно, чем первичные.
Избежать образования крупных первичных неметаллических включений можно, если к моменту присадки ферросплавов понизить содержание растворенно- го в стали кислорода до уровня, который не превышает концентрации его в равно- весии с раскислителем при температуре обработки.
При содержании углерода в стали 0,2% и более в результате вакуумно- углеродного раскисления концентрацию кислорода в металле удается понижать до 0,002 – 0,004%. Такая концентрация кислорода ниже равновесной с обычным содержанием кремния в стали. Поэтому при введении кремния в сталь после ваку- умно-углеродного раскисления первичные эндогенные включения не образуются. Такой способ обработки получил распространение при производстве стали, сво- бодной от крупных оксидных включений и их локальных скоплений.