
MS / Лекция_19
.pdf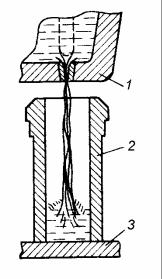
210
19 РАЗЛИВКА СТАЛИ В ИЗЛОЖНИЦЫ
19.1 Общая характеристика способов разливки стали в изложницы
Применяют два основных способа разливки стали в изложницы – разлив-
ку сверху и сифонную разливку.
При разливке сверху (рисунок 19.1) сталь непосредственно из ковша по-
ступает в изложницы, установленные на чугунных поддонах.
Рисунок 19.1 – Схема разливки стали сверху:
1 – сталеразливочный ковш; 2 – изложница; 3 – поддон
После наполнения каждой изложницы шиберный затвор (или стопор)
ковша закрывают, ковш транспортируют к следующей изложнице, вновь от-
крывают шиберный затвор и после наполнения сталью новой изложницы опи-
санный цикл операций повторяют.
С целью уменьшения напора струи и разбрызгивания металла на стенки изложниц разливку сверху иногда ведут через промежуточные ковши.
При сифонной разливке, основанной на принципе сообщающихся сосу-
дов, сталью одновременно заполняют от двух до шести изложниц (рисунок
19.2). При этом из сталеразливочного ковша сталь поступает в установленную на поддоне футерованную изнутри центровую, а из нее по каналам уложенной в поддоне сифонной проводки поступает в изложницы снизу. После наполнения всех установленных на поддоне изложниц шиберный затвор (или стопор) ков-
ша закрывают и ковш транспортируют к следующему поддону.
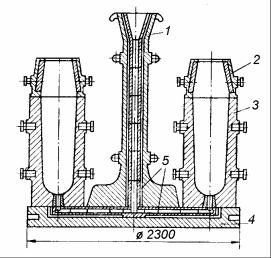
211
Рисунок 19.2 – Схема сифонной разливки
стали:
1 – центровая; 2 – прибыльная надставка; 3
– изложница (для разливки спокойной ста-
ли); 4 – поддон; 5 – сифонный припас
Сифонная разливка стали имеет следующие преимущества в сравнении с разливкой сверху:
∙одновременная отливка нескольких слитков сокращает длительность раз-
ливки плавки и позволяет разливать в слитки малого развеса плавки большой массы;
∙вследствие сокращения общей длительности разливки скорость подъема металла в изложнице может быть значительно меньше, чем при разливке сверху;
∙поверхность слитков получается чистой, так как металл в изложнице поднимается спокойно без разбрызгивания;
∙повышается стойкость футеровки ковша и улучшаются условия работы шиберного затвора вследствие меньшей длительности разливки и умень-
шения числа закрываний и открываний затвора;
∙во время разливки можно следить за поведением поднимающегося в из-
ложнице металла и в соответствии с этим регулировать скорость разлив-
ки.
Недостатками сифонной разливки в сравнении с разливкой сверху явля-
ются:
∙сложность и повышенная стоимость разливки, обусловленные расходом сифонного кирпича, установкой дополнительного оборудования и значи-
тельными затратами труда на сборку поддонов и центровых;
212
∙дополнительные потери металла в виде литников (0,7 – 2,5% от массы разливаемой стали) и возможность потери металла при прорывах через сифонные кирпичи;
∙температура металла перед разливкой должна быть выше, чем при раз-
ливке сверху, так как он дополнительно охлаждается в каналах сифонно-
го кирпича.
Преимуществами разливки сверху являются:
∙простая подготовка оборудования к разливке и меньшая его стоимость;
∙отсутствие расхода металла на литники;
∙температура металла перед разливкой может быть ниже, чем при сифон-
ной разливке.
Вместе с тем разливке сверху присущи следующие недостатки:
∙образование плен на поверхности нижней части слитков, что является следствием разбрызгивания металла при ударе струи о дно изложницы.
Застывшие на стенках изложницы и окисленные с поверхности брызги металла не растворяются в поднимающейся жидкой стали, образуя дефекты по-
верхности – плены, которые не свариваются с металлом при прокатке. В ре-
зультате этого поверхность прокатных заготовок приходится подвергать зачи-
стке.
∙большая длительность разливки;
∙из-за большой длительности разливки снижается стойкость футеровки ковша и ухудшаются условия работы шиберного затвора.
Высококачественные углеродистые и легированные стали разливают,
главным образом, сифоном. Сифонную разливку используют также при разлив-
ке углеродистой стали обыкновенного качества в слитки малого развеса.
При сифонной разливке и разливке стали сверху потери металла в виде скрапа и недоливков составляют 0,6 – 1,9%. При сифонной разливке 0,7 – 2,5%
разливаемой стали дополнительно теряется в виде литников.
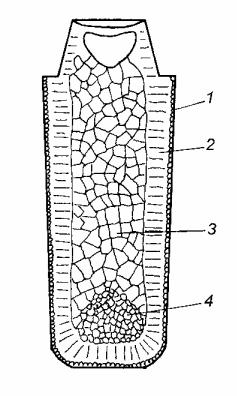
213
19.2 Разливка спокойной стали
19.2.1 Структура слитка спокойной стали
В слитке спокойной стали выделяют следующие структурные зоны, от-
личающиеся формой кристаллов и их размерами (рисунок 19.3): тонкую на-
ружную корку из мелких равноосных кристаллов; зону вытянутых столбчатых кристаллов; центральную зону крупных неориентированных кристаллов; зону мелких неориентированных кристаллов в нижней части слитка, имеющую ко-
нусообразную форму (конус осаждения).
Рисунок 19.3 – Структурные зоны слитка спо-
койной стали:
1 – наружная корковая зона; 2 – зона столбчатых кристаллов; 3 – зона крупных равноосных кри-
сталлов в центральной части слитка; 4 – конус осаждения
В верхней части слитка находится полость – так называемая усадочная раковина. Причиной ее образования является усадка стали в процессе затверде-
вания, т. е. увеличение ее плотности при переходе из жидкого состояния в твердое. В зависимости от химического состава стали величина усадки обычно составляет 2,0 – 5,3%. Усадочная раковина может быть закрытой, если в голов-
ной части слитка из-за недостаточной теплоизоляции затвердевает верхний слой металла («мост»). При использовании теплоизолирующих и экзотермиче-
214
ских засыпок, а также обогреве верха слитка усадочная раковина получается открытой.
При прокатке на обжимных станах часть слитка, в которой располагается усадочная раковина, обычно удаляют (головная обрезь).
19.2.2 Основные требования к организации отливки слитков спокойной стали
Чтобы уменьшить потери металла с головной обрезью при прокатке, не-
обходимо уменьшить глубину проникновения усадочной раковины в тело слит-
ка. С этой целью при отливке слитков спокойной стали должны выполняться следующие требования:
∙спокойную сталь, как правило, разливают в изложницы, расширяющиеся кверху. Большая масса жидкого металла в верхней части слитка способ-
ствует замедленному ее охлаждению;
∙при отливке слитков спокойной стали на изложницу устанавливают при-
быльную надставку, которую также наполняют жидким металлом. По-
ступление дополнительного количества металла из прибыльной надстав-
ки в тело слитка позволяет заполнить образующиеся в нем усадочные пустоты;
∙чтобы металл в прибыльной надставке затвердевал в последнюю очередь,
боковые поверхности расположенной в ней головной части слитка тепло-
изолируют;
∙после наполнения слитка поверхность металла в прибыльной надставке засыпают теплоизолирующими или разогревающими смесями.
Вкачестве теплоизолирующих засыпок используют асбест, обожженный вермикулит, коксо-шлаковые смеси и др.
Более эффективно применение разогревающих засыпок – люнкеритов,
которые представляют собой порошкообразную смесь горючих и нейтральных компонентов. В качестве горючих компонентов используют алюминий (14 –
215
28%), ферросилиций (0 – 15%), коксик и древесный уголь (0 – 50%). В качестве нейтральных компонентов – шамот, боксит, вермикулит. В прибыльной над-
ставке горючие компоненты смеси медленно окисляются с выделением тепла,
которое расходуется на обогрев жидкого металла. Нейтральные компоненты смеси и продукты окисления горючих ее компонентов образуют теплоизоляци-
онный слой, который уменьшает скорость отвода тепла от верха слитка. Расход люнкеритов обычно составляет 0,5 – 2,0 кг/т стали.
19.3 Разливка кипящей стали
19.3.1 Структура слитка кипящей стали
В слитке кипящей стали выделяют следующие структурные зоны (рису-
нок 19.4 а): плотную наружную корку; зону продолговатых сотовых пузырей;
промежуточную зону плотного металла; зону вторичных пузырей; плотную центральную зону со скоплением пузырей в верхней ее части.
Чтобы избежать чрезмерного развития ликвации в слитках кипящей стали используют операцию закупоривания слитков, сущность которой заключается в прекращении кипения металла в изложницах. В настоящее время наиболее ши-
роко используют химическое закупоривание слитков, для чего через 1,0 – 1,5
минуты после наполнения изложницы в металл вводят гранулированный или жидкий алюминий. Расход алюминия выбирают таким образом, чтобы даль-
нейшее затвердевание слитка сопровождалось незначительным газовыделени-
ем, которое должно компенсировать усадку стали и предотвратить образование концентрированной усадочной раковины.
В химически закупоренном слитке кипящей стали выделяют следующие структурные зоны (рисунок 19.4 б): плотную наружную корку; короткие сото-
вые пузыри в нижней части слитка; пузыри и усадочные пустоты в верхней части слитка, над которыми расположен «мост» плотного металла. При высо-
кой окисленности металла наблюдаются прорывы поверхности слитка пузыря-
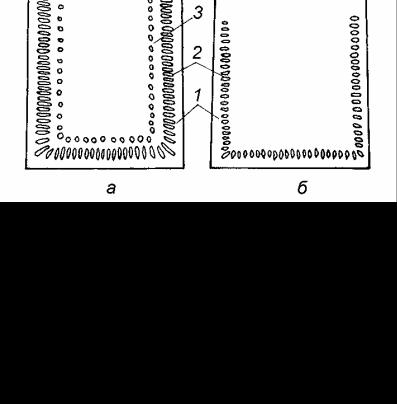
216
Рисунок 19.4 – Структурные зоны слитков кипящей стали:
а – обычный слиток; б – химически закупоренный слиток; 1 – наружная корка; 2 – сотовые пузыри; 3 – промежуточная зона плотного металла; 4 – зона вто-
ричных пузырей; 5 – скопление пузырей в верхней части слитка; 6 – пузыри и усадочные пустоты в верхней части слитка; 7 – «мост» плотного металла
ми СО («свищи»).
19.3.2Основные требования к организации отливки слитков кипящей стали
В слитке кипящей стали отсутствует концентрированная усадочная рако-
вина. По этой причине кипящую сталь обычно разливают в сквозные расши-
ряющиеся книзу изложницы, которые являются наиболее простыми в обслужи-
вании.
Чтобы избежать окисления поверхности сотовых пузырей, толщина плот-
ной наружной корки слитка должна быть больше толщины слоя металла, кото-
217
рый окисляется при нагреве слитка под прокатку (> 8 – 10 мм). С этой целью при разливке кипящей стали скорость разливки (скоростью подъема уровня ме-
талла в изложнице) должна быть не более 1,0 м/мин.
Если разливку стали необходимо вести с большей скоростью, прибегают к использованию интенсификаторов кипения. В изложницу во время разливки вводят порошкообразные смеси, содержащие оксиды железа, в виде брикетов или окатышей. При этом поступление в металл дополнительного количества кислорода обеспечивает повышение интенсивности кипения, что позволяет увеличить скорость разливки до 2,0 – 2,5 м/мин.
Чтобы избежать чрезмерного развития ликвации при отливке слитков ки-
пящей стали используют операцию закупоривания.
При отливке крупных слитков кипящей стали используют сочетание ско-
ростной разливки с химическим закупориванием. В этом случае разливку ведут со скоростью 3 – 5 м/мин без применения интенсификаторов кипения. При та-
кой скорости разливки плотная корка не образуется, и зарождение пузырей на-
чинается у поверхности слитка. Благодаря раннему химическому закупорива-
нию размеры пузырей малы, и они полностью локализованы в слое металла, ко-
торый окисляется при нагреве слитка под прокатку. Поэтому рванины на по-
верхности проката не образуются.
19.4 Разливка полуспокойной стали
19.4.1 Структура слитка полуспокойной стали
Затвердевание полуспокойной стали сопровождается слабым непродол-
жительным кипением, для обозначения которого используют термин «искре-
ние». При нормальной окисленности стали искрение длится в течение 10 – 40 с
после наполнения изложницы.
Так как при разливке полуспокойной стали интенсивность кипения ме-
талла не достаточна для формирования плотной наружной корки слитка значи-
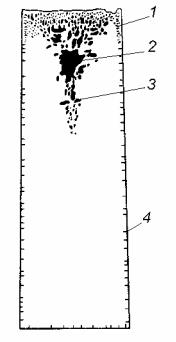
218
тельной толщины, у поверхности слитка обычно наблюдаются мелкие подкор-
ковые пузыри. Короткие сотовые или округлые пузыри могут сформироваться только в верхней его части, где условия кипения металла более благоприятны.
Слиток полуспокойной стали имеет небольшую усадочную раковину. Под уса-
дочной раковиной располагается усадочная рыхлость, глубина которой может достигать 35 – 45% высоты слитка (рисунок 19.5).
Рисунок 19.5 – Структура слитка полуспокойной стали: 1 – сотовые (округлые) пузыри; 2 – усадочная раковина; 3 – усадочная рыхлость; 4 – подкорковые пузыри
При нормальной окисленности стали над усадочной раковиной формиру-
ется «мост» пузыристого металла толщиной 200 – 250 мм, надежно изолирую-
щий ее от атмосферы.
При длительности искрения менее 10 с слитки получаются с меньшей толщиной моста и недостаточно изолированной усадочной раковиной. При продолжительности искрения свыше 40 с возможно образование сотовых пузы-
рей по всей высоте слитка.
19.4.2Основные требования к организации отливки слитков полуспокойной стали
Полуспокойную сталь обычно разливают в сквозные, расширяющиеся книзу изложницы.
219
Разливку полуспокойной стали ведут со скоростью до 5 м/мин. При вы-
сокой скорости разливки пузыри у поверхности слитка либо отсутствуют, либо наблюдаются мелкие, округлые подкорковые пузыри. Слой металла, в котором они локализованы, окисляется при нагреве слитка под прокатку.
19.5 Дефекты стальных слитков
Дефекты стальных слитков подразделяют на естественные или неизбеж-
ные, которые возникают при затвердевании и охлаждении слитка, и технологи-
ческие, которые возникают из-за несовершенства технологии выплавки и раз-
ливки металла.
К естественным дефектам относятся: усадочная раковина, осевая рых-
лость, химическая и структурная неоднородность, сотовые пузыри, эндогенные неметаллические включения.
К технологическим дефектам – трещины, плены, завороты корки, под-
корковые пузыри в слитках спокойной стали, голенища или рослость слитков кипящей стали, малая толщина плотной корки слитка и др.