
MS / Лекция_17
.pdf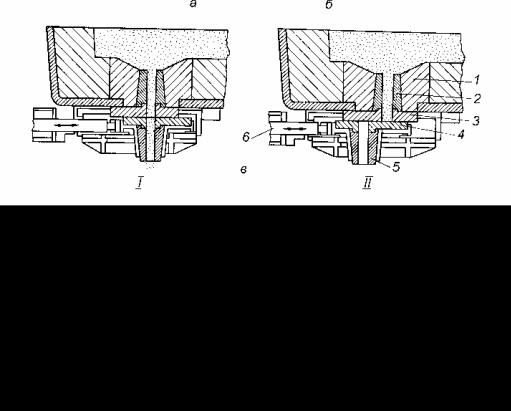
159
17 ОРГАНИЗАЦИЯ ВЫПУСКА МЕТАЛЛА ИЗ СТАЛЕПЛАВИЛЬНЫХ АГРЕГАТОВ
17.1 Конструкция сталеразливочного ковша
Сталеразливочный ковш (рисунок 17.1а) предназначен для приема метал-
ла и части шлака, выдержки металла и его разливки.
Рисунок 17.1 – Сталеразливочный ковш:
а – общий вид (1 – цапфа; 2 – носок для слива шлака; 3 – стопорный механизм; 4 – стопор; 5 – скоба для кантования ковша); б – установка стопора и стакана в ковше (1 – стакан; 2 – гнездовой кирпич; 3 – кладка ковша; 4 – стержень стопо-
ра; 5 – катушка; 6 – пробка); в – шиберный затвор в открытом (I) и закрытом
(II) положениях (1 – гнездовой кирпич; 2 – разливочный стакан; 3 – неподвиж-
ная плита; 4 – подвижная плита; 5 – стакан коллектор; 6 – шток гидроцилиндра)
Номинальная вместимость сталеразливочных ковшей составляет от 0,5 до
500 т. Основные размеры ковшей различной емкости приведены в таблице 17.1.
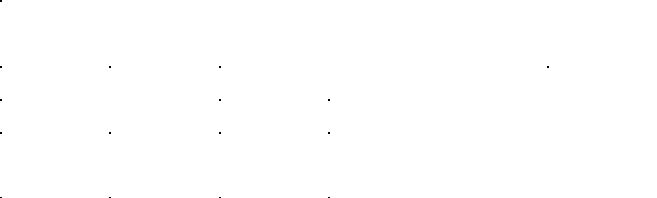
|
|
|
|
|
160 |
|
Таблица 17.1 – Основные размеры сталеразливочных ковшей |
|
|||||
|
|
|
|
|
|
|
|
Основные размеры ковша, мм |
Масса, т |
||||
Емкость |
|
|
|
|
|
|
|
диаметр |
|
груженого |
|||
ковша, т |
высота |
футеровки |
||||
|
|
|||||
|
|
вверху |
внизу |
|
ковша |
|
|
|
|
|
|
|
|
50 |
2800 |
2620 |
2340 |
9,7 |
80,0 |
|
|
|
|
|
|
|
|
100 |
3450 |
3400 |
2950 |
18,0 |
140,0 |
|
|
|
|
|
|
|
|
250 |
4350 |
4200 |
3570 |
35,8 |
320,0 |
|
|
|
|
|
|
|
|
480 |
5660 |
5340 |
4615 |
62,3 |
630,0 |
|
|
|
|
|
|
|
Ковш состоит из сварного кожуха, изготовленного из стальных листов толщиной 16 – 40 мм и имеющего форму усеченного конуса с расширением кверху. Днище ковша может быть плоским или иметь сферическую форму (в
ковшах большого объема). Оно изготавливается из более толстых листов и имеет приспособления для кантования.
Кожух ковша имеет ребра жесткости, стальной пояс, снабженный двумя цапфами, за которые ковш может быть поднят при помощи траверсы сталераз-
ливочного крана, и кронштейнами для установки на стенд. Во избежание опро-
кидывания оси цапф должны быть расположены выше центра тяжести ковша,
наполненного металлом и шлаком.
В верхней части кожуха приваривают кольцо жесткости и предусматри-
вают (если это необходимо) отверстия для шлакового носка и для крепления его на корпусе. Уровень пода носка расположен на 100 – 150 мм ниже верхнего края ковша.
В днище ковша имеются отверстия для разливочных стаканов. На днище имеются постановочные фланцы для крепления шиберных затворов и уст-
ройств для продувки металла аргоном.
Для футеровки сталеразливочных ковшей широко используют шамотный кирпич, а также набивные или наливные кислые огнеупорные массы. При раз-
ливке стали ответственного назначения для футеровки сталеразливочных ков-
шей используют высокоглиноземистый, магнезитовый, доломитовый кирпич и
161
др. В футеровке днища ковша устанавливают гнездовой кирпич, в который вставляют разливочный стакан. Наиболее широкое распространение получили разливочные стаканы из магнезита. Диаметр канала сталеразливочного стакана изменяется от 35 до 80 мм, а для скоростной разливки – 100 – 120 мм. Вновь отфутерованный или отремонтированный ковш сушат и разогревают до 700 –
800оС.
Стойкость кислой футеровки сталеразливочных ковшей составляет 7 – 15
плавок. Промежуточные ремонты футеровки торкретированием позволяют уве-
личить ее стойкость на 30 – 50%.
Длительное время отверстия сталеразливочных стаканов перекрывали с использованием стопора – стального стержня диаметром около 50 мм, который защищали от воздействия жидкого металла шамотными катушками диаметром
185 – 220 мм и пробкой (рисунок 17.1б). Главными недостатками стопорного устройства были высокий расход огнеупоров, большой объем работ по подго-
товке стопоров и частые аварии при разливке (приваривание и отрыв пробки,
деформация и переедание стопора и др.).
В последние годы металлургические предприятия перешли к использова-
нию сталеразливочных ковшей, оборудованных шиберными затворами (рису-
нок 17.1в). Плиты шиберного затвора из корунда или периклаза позволяют раз-
ливать от одной до трех плавок.
17.2Способы отделения окислительного шлака от металла при выпуске плавки
При выпуске плавки в сталеразливочный ковш попадает окисленный шлак, который может содержать до 20 – 30% FeO. Попадание печного шлака в ковш приводит к рефосфорации металла, повышенному угару раскислителей и легирующих добавок, снижает эффективность внепечной десульфурации стали.
Методы удаления шлака с поверхности металла в ковше (рисунок 17.2)
сложны и широкого распространения не получили.
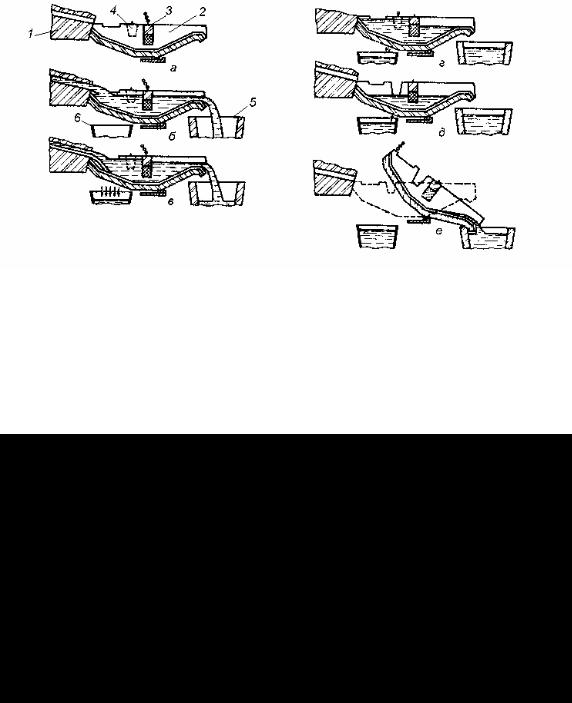
162
Рисунок 17.2 – Установка для скачивания шлака с поверхности металла в ковше
В мартеновских цехах для отделения печного шлака от металла на вы-
пуске используют желоба специальной конструкции. В качестве примера на ри-
сунке 17.3 показана схема отделения шлака от металла с помощью качающего-
ся желоба.
Рисунок 17.3 – Схема отделения шлака от металла на выпуске из мартеновской печи при помощи качающегося желоба:
1 – желоб мартеновской печи; 2 – качающийся желоб; 3 – огнеупорная перего-
родка; 4 – огнеупорная заслонка; 5 – сталеразливочный ковш; 6 – шлаковая ча-
ша
Желоб такой конструкции успешно применялся на 180-т печах металлур-
гического завода им. А.К. Серова и 600-т печах Череповецкого металлургиче-
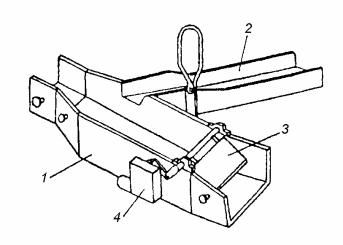
163
ского комбината. На металлургическом заводе им. А.К. Серова использование этого желоба для отделения шлака при выпуске плавки из кислой мартеновской печи в ковш с основным синтетическим шлаком позволило: уменьшить расход синтетического шлака с 56 до 39 кг/т стали; повысить степень десульфурации стали с 46 до 77%; уменьшить угар кремния с 29 до 12% и угар алюминия с 45
до 28%.
На рисунке 17.4 показана конструкция стационарного желоба для отделе-
ния шлака от металла, разработанная на Макеевском металлургическом заводе.
Рисунок 17.4 – Конструкция желоба для отделения шлака от металла на выпус-
ке из мартеновской печи:
1 – корпус желоба; 2 – шлаковый носок; 3 – поворотная заслонка; 4 – привод заслонки
В момент появления шлака заслонку поворачивают и устанавливают под оптимальным углом к потоку жидкой стали. Меняя угол установки заслонки в зависимости от расхода истекающего металла, добиваются подъема уровня шлака в приемной части желоба до уровня донной части сливного носка, по ко-
торому печной шлак отводится в шлаковую чашу.
Для отделения шлака от металла при сливе из кислородного конвертера
зарубежные фирмы используют задержку шлака в промежуточной емкости (ри-
сунок 17.5).
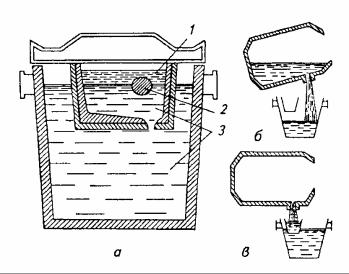
164
Рисунок 17.5 – Схема отделения шлака от металла с использованием промежу-
точной емкости:
а – разрез сталеразливочного ковша и промежуточной емкости в момент окон-
чания выпуска; б – начало выпуска; в – окончание выпуска; 1 – шлак; 2 – пла-
вающий шар – отсекатель шлака; 3 – металл
Футерованную изнутри и снаружи промежуточную емкость, имеющую отверстие в днище, устанавливают перед выпуском плавки на сталеразливоч-
ном ковше таким образом, что в начале выпуска металл из конвертера попадает непосредственно в сталеразливочный ковш (рисунок 17.5б). В заключительной части выпуска, когда вместе с металлом выходит шлак, струя падает в проме-
жуточную емкость (рисунок 17.5в). Когда из конвертера начинает вытекать один шлак, конвертер возвращают в вертикальное положение, а в промежуточ-
ную емкость забрасывают шар, плотность которого такова, что он плавает на границе раздела шлака с металлом. Промежуточную емкость поднимают кра-
ном. При этом металл стекает в сталеразливочный ковш, а плавающий шар пе-
рекрывает отверстие в днище промежуточной емкости. При этом в сталеразли-
вочный ковш шлак почти не попадает.
На отечественных заводах получили распространение способы отделения шлака от металла с помощью плавающих керамических пробок (рисунок 17.6).
На рисунке 17.7 показана конструкция отсечного устройства, используе-
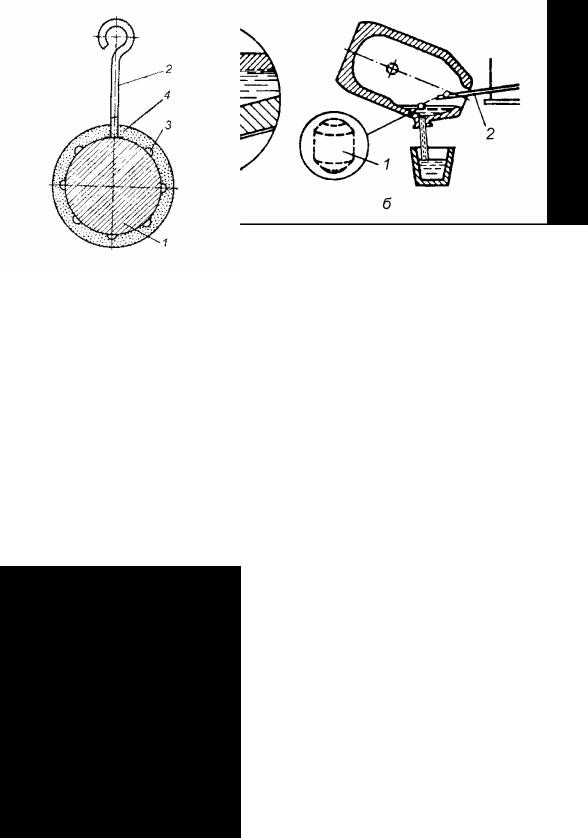
165
Рисунок 17.6 – Схема отделения шлака от металла при выпуске из конвертера:
а, б – варианты технологии; 1 – плавающая керамическая пробка; 2 – лоток для ввода пробки в конвертер; 3 – граница шлак-металл
мого Новолипецким металлургическим комбинатом. Оно представляет собой литой стальной шар диаметром 160 – 190 мм, к которому приварена стальная арматура диаметром 16 мм. Поверхность шара покрыта огнеупорной оболоч-
кой, состоящей из 60 – 65% магнезитового порошка фракции 0 – 3 мм, 25 – 30%
магнезитового порошка фракции 0 – 1 мм, 8 – 10 % шлака производства ферро-
хрома фракции 0 – 1 мм и 35 – 36% (сверх 100%) жидкого стекла.
Рисунок 17.7 – Схема отсечного устройства Новолипецкого металлургического комбината: 1 – стальное литье; 2 – хвостовик; 3 – арматура; 4 – огнеупорная оболочка
Шар-стопор вводят в полость конвертера с помощью манипуляторов,
смонтированных на тележке для ремонта сталевыпускного отверстия, за 0,5 – 1,0 минуту до окончания выпуска металла и забрасывают в район сталевыпуск-
ного отверстия. Кажущаяся плотность этого шара меньше чем у расплавленно-
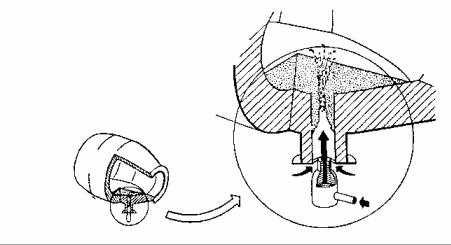
166
го металла и больше, чем у шлака. Поэтому шар плавает на границе раздела шлак-металл и после слива всего металла перекрывает отверстие.
Испытания показали, что эффективная отсечка шлака достигается на 90%
плавок. На плавках с отсечкой шлака на 0,2 кг/т стали снижается угар алюми-
ния, на 0,4 кг/т – угар марганца, восстановление фосфора составляет всего 0,001
– 0,005% (без отсечки – 0,005 – 0,015%).
В последние годы для отделения шлака от металла при сливе из конвер-
тера отечественные предприятия начинают использовать пневматические проб-
ки (рисунок 17.8), шиберные затворы и другие устройства, которые вместе с приводами устанавливают на внешней стороне корпуса конвертера.
Рисунок 17.8 – Пневматическая пробка для отсечки шлака при выпуске из конвертера
При этом момент появления шлака в потоке вытекающего из конвертера металла определяется при помощи электромагнитного индикатора. Основу это-
го устройства составляют два индуктора, которые размещают в футеровке ста-
левыпускного отверстия по обе стороны контролируемого потока. При прохо-
ждении тока заданной частоты в одном из индукторов в другом наводится ЭДС,
величина которой зависит от магнитной проницаемости среды. Поэтому появ-
ление шлака в потоке металла приводит к изменению ЭДС, что фиксируется контролирующим прибором и является сигналом к отсечке шлака.
167
При использовании таких устройств количество печного шлака в ковше по окончанию выпуска не превышает 4 кг/т стали, в то время как при обычной работе оно составляет 5 – 15 кг/т.
Следует также упомянуть следующие способы ограничения количества печного шлака в ковше, которые длительное время применяются в кислородно-
конвертерных цехах:
∙загущение шлака перед выпуском плавки;
∙неполный слив металла из конвертера, что приводит к уменьшению его производительности;
∙простым и надежным способом отделения шлака является перелив ме-
талла из ковша в ковш, главным недостатком которого являются значи-
тельные потери температуры металла. Так, например, при переливе из
100-т ковша температура металла может понижаться на 25 – 40оС в зави-
симости от нагрева футеровки приемного ковша.