
MS / Лекция_14
.pdf134
14 ПРОИЗВОДСТВО ВЫСОКОЛЕГИРОВАННОЙ СТАЛИ В КОНВЕРТЕРАХ АРГОННО-КИСЛОРОДНОГО ДУТЬЯ
Нержавеющие, жаростойкие, коррозионностойкие и ряд других марок стали содержат в своем составе 15 – 30% хрома. Выплавку такого металла це- лесообразно вести с использованием в шихте наиболее дешевого высокоугле- родистого феррохрома. Однако, углерод в этих марках стали является нежела- тельной примесью. Поэтому при производстве их с использованием высокоуг- леродистого феррохрома возникает необходимость в глубоком обезуглерожи- вании металла, которое должно сопровождаться минимальными потерями хро- ма.
При оценке условий, которые необходимы для глубокого обезуглерожи- вания металла с высоким содержанием хрома, необходимо учитывать следую- щее:
∙реакция между растворенными в металле хромом и кислородом с образо- ванием оксида Cr2O3 является сильной экзотермической реакцией, теп-
ловой эффект которой, отнесенный к одному молю кислорода, в 3 раза больше теплового эффекта реакции между растворенными в металле ки- слородом и углеродом;
∙реакция окисления хрома протекает с образованием конденсированного оксида, а реакция окисления углерода – газообразного.
Отсюда следует, что преимущественному окислению углерода способст- вуют высокая температура ванны и низкое парциальное давление СО в продук- тах реакции. Уменьшить парциальное давление СО в продуктах реакции окис- ления углерода можно при обезуглероживании металла в вакууме или путем разбавления оксида углерода инертным газом при вдувании в расплав смеси кислорода и аргона. Последний способ понижения парциального давления СО используется при обезуглероживании расплавов с высоким содержанием хрома в конвертерах аргонно-кислородного дутья (AOD конвертеры).
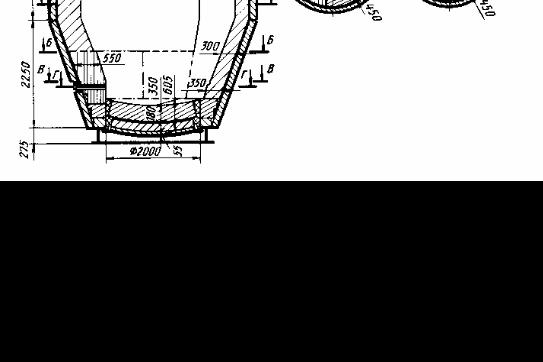
135
14.1 Конструкция AOD конвертера
Конструкция 80-т AOD конвертера с симметричной горловиной показана на рисунке 14.1.
Рисунок 14.1 – Конструкция 80-т AOD конвертера
Для подачи кислорода и аргона в металл используются фурмы, располо- женные у днища в стенке, противоположной сливному носку конвертера. Фур- мы расположены по дуге, длина которой равна 1/3 диаметра конвертера на этом уровне (разрез Г – Г). Поэтому при повалке конвертера фурмы располагаются над поверхностью металла.
В рассматриваемом конвертере фурмы состоят из центральной трубы внутренним диаметром 13 мм и наружной трубы диаметром 16 мм. По цен- тральной трубе подают смесь кислорода с аргоном, в зазор между трубами по- дают аргон для охлаждения фурмы. В данной конструкции конвертера исполь- зуется 5 фурм, оси которых смещены на угол, равный 25о. Этим достигается сравнительно равномерное распределение вдуваемого газа в ванне конвертера.
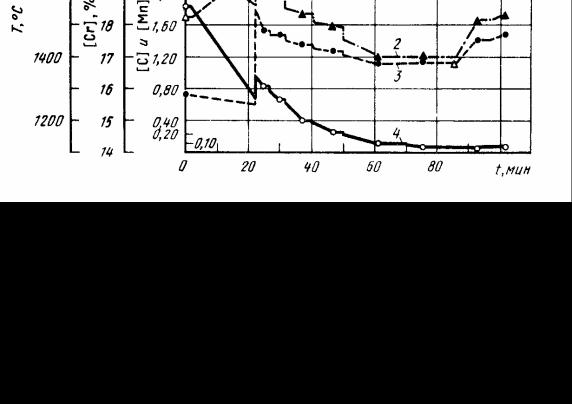
136
14.2 Технология производства легированной стали в AOD конвертерах
Сведения об изменении химического состава и температуры металла при выплавке хромоникелевой стали в 80-т AOD конвертере приведены на рисунке
14.2.
Рисунок 14.2 – Диаграмма плавки хромоникелевой стали в AOD конвертере:
I, II, III – периоды плавки; К – период кипения без продувки кислородом; В – восстановление; Д – десульфурация; 1 – температура металла; 2 – содержание хрома; 3 – содержание марганца; 4 – содержание углерода. Числа у горизон- тальных стрелок (5:1, 3:1, 2:1, 1:1, 1:2) – отношения расходов кислорода и арго- на; числа у вертикальных стрелок – масса присадок, кг
Выплавка легированного полупродукта ведется в дуговых электропечах с использованием в шихте максимального количества отходов легированной ста- ли и высокоуглеродистых ферросплавов, а также извести в количестве 30 – 40 кг/т. Металл перед выпуском содержит 1,7 – 3% С и ~ 0,2% Si. Печной шлак,

137
содержащий ~ 4% оксидов хрома, вместе с металлом сливают в ковш и залива- ют затем в конвертер. Температура металла после перелива составляет 1540оС.
Для интенсификации окисления углерода по ходу продувки необходимо придерживаться оптимального соотношения между количествами вдуваемых в металл кислорода и аргона. Ниже приведены рекомендуемые соотношения рас-
ходов этих газов в различных периодах продувки: |
|
|
|
||
Период продувки |
1 |
2 |
3 |
4 |
5 |
Отношение расхода кислорода к |
|
|
|
|
|
расходу аргона |
5:1 |
3:1 |
2:1 |
1:1 |
1:2 |
Концентрация углерода в конце |
|
|
|
|
|
периода, % |
* |
0,55 |
0,35 |
0,20 |
0,08 |
*Определяется достижением температуры 1700оС
Для быстрого повышения температуры ванны первый этап продувки ве- дут без ввода в конвертер охладителей. Интенсивность продувки составляет около 1 м3/(т·мин). При температуре ~ 1700оС в конвертер вводят агломерат ок- сида никеля, ферромарганец и феррохром, в дальнейшем в качестве охладителя используют гранулированный ферроникель.
В конце окислительной продувки подачу кислорода прекращают и, про- должая продувку ванны аргоном с интенсивностью ~ 0,7 м3/(т·мин), проводят завершающий период обезуглероживания, одновременно понижая содержание растворенного в металле кислорода и оксидов железа в шлаке (период «выки- пания»). Исключением являются плавки, в которых содержание углерода в ме- талле должно составлять < 0,03%. В этом случае продувку металла смесью ки- слорода и инертного газа в соотношении 1:2 ведут до концентрации углерода ~ 0,04%, в ходе дальнейшей продувки содержание аргона в смеси непрерывно увеличивают до соотношения 1:8.
После достижения требуемой концентрации углерода для восстановления хрома из оксидов в шлаке в конвертер вводят ферросилиций, продолжая про- дувку ванны аргоном в течение 5 – 6 минут. При этом содержание оксидов хро- ма в шлаке понижается до ~ 1,7%.
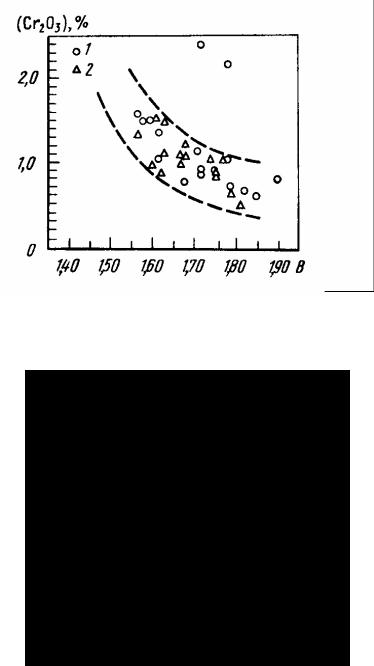
138
Установлено, что при концентрации кремния в металле более 0,2% даль- нейшее увеличение его содержания не сопровождается существенным умень- шением содержания оксидов хрома в шлаке. Зависимость содержания Cr2O3 в
шлаке в конце периода восстановления от температура ванны и основности шлака B = (CaO + MgO)/(SiO2) приведена на рисунках 14.3 и 14.4.
Рисунок 14.3 – Зависимость содержания Cr2O3 в шлаке в конце периода восстановления от температуры
Рисунок 14.4 – Зависимость содержания Cr2O3 в шлаке от его основности в конце периода восстановления:
1 – магнезитохромитовая футеровка; 2 – магнезитодоломитовая футеровка
139
По окончанию периода восстановления из конвертера сливают 2/3 шлака, вводят новую порцию флюсов и в течение 3 – 4 минут проводят десульфура- цию стали, перемешивая ванну аргоном. При необходимости в конвертер вво- дят охлаждающие добавки, чтобы понизить температуру металла в конце плав- ки до 1600оС.
При продувке металла в AOD конвертерах возможна частичная замена аргона более дешевым азотом. Установлено, что основное количество азота, поглощенного сталью в I периоде продувки (см. рисунок 14.2) при продувке смесью кислорода и азота, в последующие II и III периоды при продувке сме- сью кислорода и аргона из металла удаляется. При выплавке стали с содержа- нием хрома до 27%, никеля до 35% и минимальным содержанием углерода 0,015% расход азота может составлять 30 – 40% общего расхода инертного газа. При этом концентрация азота в стали не превышает 0,04 – 0,05%.
При выплавке 1 т стали Х18Н9 в AOD конвертерах расходуется: аргона и азота 23 м3, кремния на восстановление 11 кг, металлических охладителей 180 кг, извести в периоды окисления и восстановления 50 кг, извести для десульфу- рации 20 кг, плавикового шпата 6 кг.
В настоящее время до 80% мирового производства коррозионностойкой стали выплавляется в AOD конвертерах.
Одной из разновидностей рассмотренной выше технологии является про- цесс CLU, в котором продувку металла ведут смесью кислорода с водяным па- ром.