
MS / Лекция_1
.pdf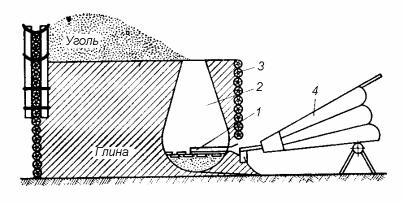
9
1 ВОЗНИКНОВЕНИЕ, РАЗВИТИЕ И ОСНОВНЫЕ ПРИНЦИПЫ ОРГАНИЗАЦИИ СТАЛЕПЛАВИЛЬНЫХ ПРОЦЕССОВ
1.1 Возникновение и развитие сталеплавильных процессов
В Европе железо впервые научились получать приблизительно за 1000
лет до нашей эры. Первым агрегатом для этого был сыродутный горн, который применялся вплоть до XV века. Затем в результате ряда усовершенствований он превратился в сыродутную печь, схема которой показана на рисунке 1.1.
Рисунок 1.1 – Вертикальный разрез сыродутной печи:
1 – сопло; 2 – рабочее пространство печи; 3 – деревянный сруб; 4
– меха
Печь представляла собой деревянный сруб, заполненный огнеупорной глиной, в которой выполнено рабочее пространство печи. Иногда внутренние части печи выкладывали огнеупорным камнем. В передней стенке сруба име-
лось отверстие, в которое вставляли сопло от мехов, подающих в печь воздух.
Через это же отверстие проводился выпуск плавки и вынимался продукт плавки
– крица.
Печь работала следующим образом. Разогретый дровами горн заполняли древесным углем, который сжигался кислородом воздуха. По мере выгорания угля в печь загружалась смесь предварительно прокаленной и просеянной руды
10
с древесным углем. Плавка продолжалась до тех пор, пока не было израсходо-
вано определенное количество руды. После этого подачу воздуха прекращали,
выпускали из нижней части горна шлак и затем выжигали остатки угля. На этом плавка заканчивалась, и из нижней части печи вынимали раскаленный ку-
сок губчатого железа (крицу). Полученную крицу проковывали под молотами для удаления из нее шлака, после чего она становилась пригодной для изготов-
ления из нее различных изделий.
Высота печи составляла от 0,5 до 2,5 м. За одну плавку продолжительно-
стью 2 – 2,5 часа в ней получали от 8 до 80 кг железа.
На протяжении многих веков этот способ получения железа был единст-
венным. Однако растущие потребности общества заставили искать пути увели-
чения производства железа, так как производительность сыродутной печи была низкой, а потери железа – большими. Это привело к увеличению размеров пе-
чи, главным образом в высоту, и количества подаваемого воздуха. Результатом этих изменений явилось снижение температуры в верхней и повышение ее в нижней части печи. Когда температура в нижней части печи оказалась доста-
точной для расплавления восстановленного железа, жидкий металл, стекая по частицам угля, интенсивно науглероживался. Это привело к коренному измене-
нию процесса – продуктом плавки было уже не мягкое, ковкое железо, а чугун,
т.е. железо с содержанием углерода около 4%.
Долгое время полученный в сыродутном процессе чугун считался бра-
ком, так как не поддавался ковке и был хрупким. Однако позже из чугуна нау-
чились делать отливки, а затем вторично переплавлять его с рудой, окислять избыточное количество углерода и получать мягкое железо. Таким образом,
вместо непосредственного получения железа из руды в сыродутной печи, т.е.
одноступенчатого процесса, появился двухступенчатый процесс – получение жидкого чугуна и последующий передел его в сталь в другом агрегате.
Несмотря на логическую нецелесообразность перехода к двухступенча-
тому способу производства стали, последний имел огромную экономическую эффективность – при восстановлении железной руды расход угля сократился в
11
два раза, выход железа увеличился в полтора раза, резко возросла производи-
тельность агрегатов. Кроме того, понизилась трудоемкость получения металла,
появилась возможность организовать производство литой стали. Поэтому все последующее развитие металлургии протекало путем совершенствования двух-
ступенчатого способа производства стали, который до настоящего времени ос-
тается наиболее экономичным и производительным.
Из сказанного выше следует, что сталеплавильные процессы возникли и развивались как процессы, основанные на окислительном рафинировании, в
которых удаление из металла большинства примесей протекает путем окисления их растворенным в железе кислородом или оксидами железа шлака и перевода нерастворимых в металле оксидов в шлак или в газовую
фазу.
Первоначально переработка чугуна в железо и сталь заключалась в рас-
плавлении чугуна в горне на древесном угле и окислении углерода, кремния,
марганца и других примесей кислородом дутья и действием шлаков богатых оксидами железа.
В 1784 г. Г. Кортом (Англия) был предложен способ получения стали пу-
тем окислительной плавки чугуна на подине отражательной печи, получившей название пудлинговой (от англ. to puddle – месить, перемешивать). Схема печи показана на рисунке 1.2.
После расплавлении чугуна в пудлинговой печи начиналось так называе-
мое вымешивание: температуру чугуна на короткий промежуток времени не-
сколько понижали и рабочие-пудлингеры перемешивали металл и шлак клюкой или ломами.
При обезуглероживании чугуна в пудлинговой печи температура плавле-
ния металла увеличивается и наступает момент, когда она становится равной температуре в рабочем пространстве печи. Дальнейшее обезуглероживание приводит к тому, что из расплава начинают выделяться кристаллы наиболее чистого железа с высокой температурой плавления. Из этого металла «накаты-
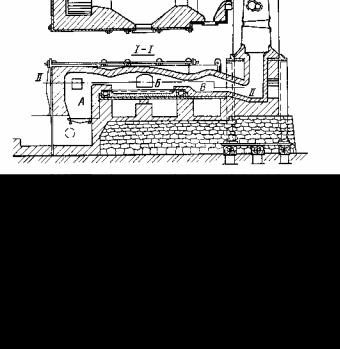
12
Рисунок 1.2 – Схема пудлинговой печи:
А – топка; Б – рабочее пространство; В – камера для предвари-
тельного подогрева чугуна отходящими газами
вают» комья по 30 – 50 кг, которые извлекают из печи и направляют для после-
дующей обработки давлением. Железо, полученное в пудлинговых печах уральских заводов, имело следующий химический состав, (% масс.): 0,1 – 0,2 C;
0,05 – 0,1 Si; ~ 0,1 Mn; ~ 0,01 P; 0,004 S.
Жидкую сталь первоначально получали путем обезуглероживания чугуна при плавке в тиглях.
В1855 г. Генри Бессемером (Англия) был предложен способ получения литой стали в больших количествах путем продувки жидкого чугуна воздухом
вконвертерах донного дутья с кислой футеровкой (бессемеровский конвертер).
В1878 – 1879 г.г. Томасом (Англия) был разработан вариант конвертер-
ного процесса, в котором использовали футеровку из основных огнеупоров
(доломита), получивший название томасовского или основного конвертерного.
В 1865 г. братья Эмиль и Пьер Мартены (Франция) успешно осуществили выплавку стали из чугуна и железного лома в регенеративных пламенных пе-
13
чах. Получение в этих печах высокой температуры, достаточной для расплав-
ления стали, стало возможным благодаря нагреву газа и воздуха перед подачей в печь. Принцип использования тепла отходящих газов для нагрева топлива и воздуха в так называемых регенераторах был предложен Сименсом (Германия).
Поэтому в ряде стран процесс называют сименс-мартеновским. В нашей стране он получил распространение под названием мартеновского.
Первые успешные работы по выплавке стали в электропечах различной конструкции были выполнены в конце XIX – начале XX столетия. В России первые промышленные электросталеплавильные печи емкостью 3 т были уста-
новлены на Обуховском заводе в 1910 г.
Первые исследования, направленные на использование кислорода для продувки металла в конвертерах донного дутья, были выполнены в 20 – 30-х
годах XX столетия. В СССР первые промышленные исследования по продувке чугуна чистым кислородом проведены М.И. Мозговым в 1933 г.
В 1948 – 1949 г.г. профессора Р. Дюрер и Г. Хольбрюге в Герлафингене
(Швейцария) провели исследования по продувке чугуна в конвертере кислоро-
дом сверху через водоохлаждаемую фурму. Ознакомившись с результатами этих исследований, Т. Суесс с сотрудниками в 1949 – 1950 г.г. провели первые успешные эксперименты в г. Линц (Австрия). Промышленные плавки стали в кислородном конвертере верхнего дутья начаты в 1952 г.
В отечественной практике продувка чугуна кислородом сверху впервые была освоена на заводе им. Г.И. Петровского (г. Днепропетровск) в 1956 г.
1.2Возможность удаления примесей металла при окислительном рафинировании
Возможность удаления различных примесей из расплавов железа при окислительном рафинировании определяется их химическим сродством к ки-
слороду. Химическое сродство элементов к кислороду можно оценить, сравнив
14
стандартные значения изменения энергии Гиббса реакций их окисления с уча-
стием 1 моля кислорода
2C + O2 |
= |
2CO , |
||
Si |
+ |
O2 |
= |
SiO2 , |
2Fe |
+ |
O2 |
= |
2FeO |
и др. При температуре 1600оС химическое сродство элементов к кислороду убывает в следующем порядке
Be, Ca, Zr, Mg, Al, Ti, C, Si, V, B, Mn, Cr, Fe, W, Mo, Co, Ni, Cu, As.
Элементы, расположенные в приведенном выше ряду левее железа, в
сравнении с ним обладают более высоким химическим сродством к кислороду.
Поэтому при окислительном рафинировании расплавов железа удаление этих примесей обычно не вызывает затруднений.
Элементы, которые располагаются в приведенном выше ряду правее же-
леза, обладают меньшим по сравнению с железом химическим сродством к ки-
слороду. Поэтому по ходу плавки железо, которое является основным компо-
нентом металлического расплава, защищает их от окисления. При окислитель-
ном рафинировании удаление этих примесей из расплавов железа сопряжено со значительными трудностями или практически не возможно.
1.3Основные принципы получения заданного химического состава стали
Шлаком называют неметаллический расплав, который образуется на по-
верхности металла в процессе плавки. Металлургические шлаки имеют разно-
образный химический состав. Но шлаки классических сталеплавильных про-
цессов (мартеновский, кислородно-конвертерный, выплавка стали в дуговых электросталеплавильных печах) содержат в своем составе свыше 90% оксидов.
Это позволяет охарактеризовать их как оксидные расплавы.
15
К металлургическим шлакам предъявляется большое количество разно-
образных требований, главное из которых заключается в том, что шлак не дол-
жен оказывать интенсивного разрушающего воздействия на футеровку стале-
плавильного агрегата. С этой целью плавку необходимо вести под шлаком, хи-
мический состав которого максимально близок к химическому составу футе-
ровки.
В настоящее время для футеровки сталеплавильных агрегатов применяют два типа огнеупорных материалов. Это кислые огнеупоры, главным компонен-
том которых является кислотный оксид SiO2, и основные огнеупоры на основе
CaO, MgO и др.
Если футеровка агрегата выполнена из кислых огнеупорных материалов,
плавку ведут под кислыми шлаками, главным компонентом которых также яв-
ляется SiO2. При температурах заключительного периода плавки концентрация
кремнезема в кислых сталеплавильных шлаках достигает 50 – 60%.
Если футеровка агрегата выполнена с использованием основных огне-
упоров, плавку ведут под основными шлаками, главным компонентом которых является CaO. При температурах заключительного периода плавки концентра-
ция оксида кальция в мартеновских и кислородно-конвертерных шлаках дости-
гает 45 – 50%. При выплавке стали в дуговых электросталеплавильных печах шлаки нагреты до более высокой температуры, поэтому содержание оксида кальция в них может достигать 50 – 60%.
В зависимости от химического сродства элементов к кислороду и степени возможного их окисления или восстановления в сталеплавильных ваннах в со-
стоянии термодинамического равновесия химические элементы можно разде-
лить на три группы.
К первой группе относят элементы, обладающие значительно более вы-
соким химическим сродством к кислороду, чем железо. В ходе окислительного рафинирования эти элементы окисляются практически полностью, из оксидов шлака восстанавливаются в малой степени. К концу плавки, если реакции окис-
ления элементов приближаются к состоянию термодинамического равновесия,
16
они будут сконцентрированы главным образом в шлаке в виде оксидов и в га-
зовой фазе.
К таким элементам в основном и кислом процессах относятся: кальций,
магний, алюминий, цирконий, углерод, редкоземельные металлы. В основном процессе к этой группе элементов относятся также кремний, титан и вольфрам.
Ввод этих элементов в металл целесообразно осуществлять в ковше в процессе выпуска плавки и на установках доводки металла, в промежуточном ковше МНЛЗ, в процессе наполнения кристаллизаторов и изложниц. Если по каким-либо соображениям их необходимо вводить в металл в сталеплавильном агрегате, эта операция должна выполняться в заключительном периоде плавки непосредственной перед выпуском.
Ко второй группе относят элементы, химическое сродство которых к ки-
слороду меньше, чем у железа. При окислительном рафинировании расплавов на основе железа они окисляются в незначительном количестве, а из оксидов шлака восстанавливаются практически полностью. Если реакции окисления элементов приближаются к состоянию термодинамического равновесия, они будут сконцентрированы главным образом в металлическом расплаве.
К элементам этой группы в основном и кислом процессах относятся:
медь, никель, кобальт, олово, молибден, мышьяк. В кислом процессе такое по-
ведение характерно также для фосфора и серы. Хотя следует помнить, что в
сталеплавильных процессах основное количество серы удаляется из ме-
талла в результате реакций, протекание которых не связано с окислением.
Эти элементы могут быть введены в металл в любом из периодов плавки.
Но технологически наиболее удобной является подача основного их количества
взавалку плавки с последующим вводом корректирующих добавок.
Ктретьей группе относят элементы, химическое сродство которых к ки-
слороду несколько выше, чем у железа. В ходе окислительного рафинирования расплавов железа эти примеси в значительных количествах способны окислять-
ся и восстанавливаться из оксидов. Поэтому в равновесных условиях они в зна-
чительных количествах могут присутствовать и в металле и в шлаке.
17
Только для элементов этой группы остаточные концентрации примесей в металле и шлаке могут существенно меняться в зависимости от состава шихто-
вых материалов, температурного и шлакового режимов плавки.
К этим элементам в основном и кислом процессах относятся: марганец,
хром, ванадий, ниобий. В основном процессе такое поведение характерно для фосфора и серы, в кислом процессе – для кремния, титана и вольфрама.
Чтобы избежать значительных потерь элементов этой группы в результа-
те окисления, их рекомендуется вводить в ковш по ходу выпуска плавки или на установках доводки металла. При необходимости подачи элементов в металл в сталеплавильном агрегате, эту операцию также следует выполнять в заключи-
тельном периоде плавки непосредственно перед выпуском.