
MS / Лекция_10
.pdf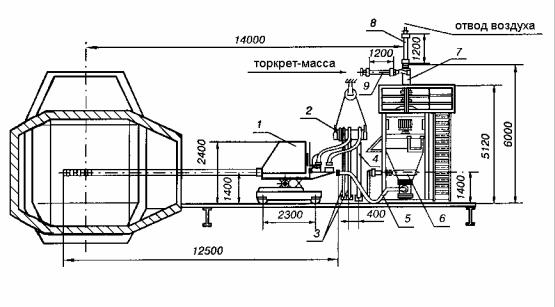
91
10 ВЫПЛАВКА СТАЛИ В КИСЛОРОДНЫХ КОНВЕРТЕРАХ ВЕРХНЕГО ДУТЬЯ
10.1 Способы восстановления футеровки кислородного конвертера
Стойкость рабочего слоя футеровки определяет продолжительность кам-
пании конвертера и существенно влияет на технико-экономические показатели его работы. Поэтому в современных сталеплавильных цехах по окончании каж-
дой или нескольких плавок персонал осматривает состояние футеровки конвер-
тера и проводит мероприятия, направленные на устранение обнаруженных де-
фектов.
Традиционным методом горячего ремонта футеровки кислородных кон-
вертеров является торкретировании. Сущность его состоит в восстановлении поврежденных участков футеровки путем нанесения на нее огнеупорной массы,
которое выполняется с помощь торкрет-машины (рисунок 10.1).
Рисунок 10.1 – Оборудование для факельного торкретирования:
1 – торкрет-машина; 2 – подвеска шлангов; 3 – гибкие рукава подачи воды; 4 –
гибкий рукав подачи кислорода; 5 – гибкий рукав подачи торкрет-массы; 6 –
камерный питатель; 7 – циклон; 8 – трубопровод сброса давления; 9 – трубо-
провод подачи торкрет-массы
92
При факельном торкретировании в полость конвертера вводится водоох-
лаждаемая фурма, через которую подается кислород и в потоке воздуха вдува-
ется торкрет-масса, состоящая из магнезитового порошка и коксовой пыли. При сгорании кокса в кислороде образуется факел, температура которого достигает
1800 – 2000оС. При этой температуре огнеупорный порошок находится в пла-
стическом состоянии и после нанесения факелом на футеровку прочно сварива-
ется с ней.
Кроме факельного торкретирования используют также полусухое, а ино-
гда и мокрое (пульповое) торкретирование. При полусухом торкретировании увлажненную огнеупорную массу наносят на футеровку конвертера струей сжатого воздуха.
Используется как торкретирование всей поверхности футеровки, так и точечное торкретирование – нанесение огнеупорной массы на отдельные наи-
более изношенные ее участки. Длительность торкретирования обычно не пре-
вышает 5 минут.
В последние годы широкое распространение получил способ повышения стойкости футеровки кислородных конвертеров путем образования на ее по-
верхности шлакового гарнисажа при раздувке окислительного высокомагнези-
ального шлака. Он предусматривает вдувание азота высокого давления через верхнюю кислородную фурму с разбрызгиванием окислительного шлака, кото-
рый полностью оставляют в конвертере после плавки. Попадая на футеровку,
шлак охлаждается, твердеет и образует слой гарнисажа, который защищает ра-
бочий слой футеровки конвертера.
Эта технология предусматривает следующие операции:
∙выпуск металла из конвертера;
∙визуальный осмотр состояния шлака с целью оценки необходимости вве-
дения добавок для его кондиционирования.
Для кондиционирования шлака в конвертер вводят известь, известняк,
уголь, доломит и другие материалы, содержащие оксид магния. Содержание
MgO в шлаке должно составлять 8 – 14%;
93
∙визуальный осмотр состояния футеровки для выявления зон, требующих особого внимания при проведении раздувания;
∙покачивание конвертера для нанесения шлака на загрузочный и выпуск-
ной участки футеровки;
∙опускание кислородной фурмы и начало продувки азотом;
∙изменение положения фурмы при помощи ЭВМ или вручную для образо-
вания шлакового гарнисажа на всей поверхности футеровки;
∙продувка необходимой продолжительности;
∙прекращение продувки и подъем фурмы;
∙слив остатков шлака в шлаковую чашу.
10.2Выплавка стали из низкофосфористого чугуна с остановкой продувки на марочном содержании углерода
При переработке низкофосфористого чугуна технология выплавки стали
вконвертере верхнего дутья включает следующие операции:
∙конвертер наклоняют на 40 – 70о, загружают в него металлический лом и заливают жидкий чугун;
∙приводят конвертер в вертикальное положение;
∙через горловину внутрь конвертера опускают кислородную фурму и на-
чинают подачу кислорода.
Обычно в начальном периоде продувки фурма располагается на значи-
тельной высоте над уровнем спокойного металла. Это связано с необходимо-
стью быстрого получения шлака с высоким содержанием FeO, кроме того, этот прием позволяет не повредить фурму при большом количестве легковесного металлического лома в завалке.
С началом продувки по расположенному над конвертером тракту сыпу-
чих материалов в него через горловину вводят 40 – 60% необходимого для плавки количества извести. Оставшееся ее количество вводят по ходу продувки

94 2 – 4 порциями. Желательно, чтобы все необходимое количество извести было подано в течение первых 50% времени продувки.
Продувка ведется до выдачи в металл расчетного количества кислорода
(45 – 60 м3/т), которое рассчитывается при помощи ЭВМ на основании сведе-
ний о массе металлической шихты, химическом составе чугуна и предполагае-
мом химическом составе металлического лома. Сведения о характере измене-
ния химического состава металла и шлака при переработке в конвертере чугуна с содержанием серы 0,030% и выше представлены на рисунке 10.2.
Рисунок 10.2 – Изменение состава металла и шлака и температуры металла при переработке низкофосфористого чугуна на низкоуглеродис-
тую сталь в 350-т конвертере
Особенности поведения серы при переработке в конвертере чугуна, пред-
варительно подвергнутого глубокой внедоменной десульфурации поясняются рисунком 10.3.

95
Рисунок 10.3 – Изменение состава и температуры металла при переработке
низкосернистого чугуна
∙после подачи в металл расчетного количества кислорода продувку пре-
кращают, извлекают из конвертера кислородную фурму, наклоняют кон-
вертер, отбирают пробы металла и шлака для химического анализа и при помощи термопары погружения измеряют температуру металла;
∙после получения результатов анализа выполняют заключительные опера-
ции, целью которых является корректировка химического состава и тем-
пературы металла в конвертере.
Наиболее часто в конце продувки наблюдаются отклонения по содержа-
нию в металле углерода и серы, а также по температуре метала. Информация о мероприятиях, которые рекомендуются для корректировки химического соста-
ва и температуры металла приведена в таблице 10.1.
Науглероживание металла можно выполнять путем присадки в ковш уг-
леродсодержащего материала, однако этим способом трудно получить металл с содержанием углерода более 0,20 – 0,30%. Возможна также завалка твердого или заливка жидкого чугуна при повалке конвертера, доливка жидкого чугуна в сталеразливочный ковш. При производстве сталей с содержанием углерода бо-
лее 0,5% хорошо зарекомендовала себя технология выпуска металла в ковш, в

96
Таблица 10.1 – Операции по корректировке результатов плавки
Характер отклонения величин |
|
||
|
|
Рекомендуемые мероприятия |
|
Содержание уг- |
Температура |
||
|
|||
лерода в металле |
металла |
|
|
Нормальное |
Высокая |
Охлаждение в конвертере или ковше |
|
Нормальное |
Низкая |
Додувка с нагревом и науглероживанием в |
|
|
|
ковше |
|
Высокое |
Нормальная |
Додувка без изменения температуры ванны |
|
Низкое |
Нормальная |
Науглероживание в ковше |
|
Высокое |
Низкая |
Додувка с нагревом |
|
Высокое |
Высокая |
Додувка с охлаждением |
|
Низкое |
Низкая |
Додувка с присадкой в конвертер чугуна или |
|
|
|
ферромарганца. Возможно и науглерожива- |
|
|
|
ние в ковше |
|
Низкое |
Высокая |
Охлаждение в конвертере или ковше, науг- |
|
|
|
лероживание в ковше |
который предварительно заливают необходимое количество жидкого чугуна,
вместе с введением небольшого количества коксика.
Охлаждение перегретого металла возможно как в конвертере, так и в ковше. Наиболее целесообразно проводить охлаждение в ковше, так как при этом можно точно регулировать температуру металла перед разливкой, что особенно важно при разливке на МНЛЗ. Кроме того, после каждой корректи-
ровки, проведенной в кислородном конвертере, необходимо снова отбирать пробы металла и замерять его температуру.
Наиболее распространенным способом охлаждения металла в ковше яв-
ляется кратковременное погружение сляба (блюма) в жидкую сталь и продувка ее аргоном. В конвертере охлаждение металла можно проводить присадкой мелкого металлического лома или твердого чугуна, а также извести, известняка,
доломита и др.
Существует также вариант этой технологии, когда для большей точности попадания в заданный состав металла продувку прекращают при содержании углерода выше марочного. После получения результатов химического анализа
97
проводят додувку, продолжительность которой определяют, исходя из избы-
точного количества углерода и известной из предыдущих плавок скорости его окисления. Причем в современных кислородно-конвертерных цехах отбор проб и замер температуры металла могут выполняться без прерывания продувки при помощи зонда, который опускают в рабочее пространство конвертера.
10.3 Выплавка стали из низкофосфористого чугуна с передувом плавки
При наличии в цехе современного оборудования для внепечной обработ-
ки стали, например, агрегата ковш-печь, для увеличения производительности конвертера обезуглероживание металла ведут до содержания углерода значи-
тельно ниже марочного (0,04 – 0,05%). При низком содержании углерода ско-
рость его окисления уменьшается и увеличивается вероятность получения за-
данного содержания углерода в металле.
Все операции по получению необходимой температуры и химического состава металла, кроме получения заданного содержания фосфора, выполняют
вковше.
10.4Материальный и тепловой балансы плавки при переработке низкофосфористого чугуна
В таблицах 10.2 и 10.3 приведены материальный и тепловой балансы плавки до раскисления при переработке жидкого чугуна состава, %: 4,20 C; 0,75
Si; 0,6 Mn; 0,15 P; 0,05 S при температуре 1340оС.
Согласно данным таблицы 10.2 и опыту отечественных и зарубежных за-
водов при переработке низкофосфористого чугуна в кислородных конвертерах верхнего дутья доля жидкого чугуна в металлической шихте составляет 75 – 80%, металлического лома 20 – 25% (при использовании твердых окислителей в количестве до 1%). При этом выход годного металла составляет 88 – 91%,
расход извести – 60 – 90 кг/т, а расход огнеупоров – 1,4 – 5,0 кг/т стали.
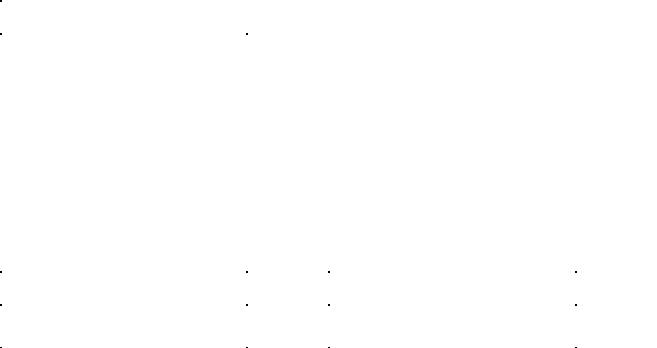
98
Таблица 10.2 – Материальный баланс плавки до раскисления на 100 кг
металлической шихты
Приходная часть баланса |
Расходная часть баланса |
|||
|
|
|
|
|
Статьи |
кг |
Статьи |
кг |
|
|
|
|
|
|
Чугун жидкий |
74,00 |
Жидкий металл |
90,34 |
|
Металлический лом |
25,10 |
Шлак |
11,44 |
|
Миксерный (доменный) |
|
Газы |
7,97 |
|
шлак и футеровка чугуно- |
|
Пыль |
1,41 |
|
возного ковша |
0,46 |
|||
|
|
|||
Загрязнения металлического |
|
Выбросы и вынос металла |
|
|
лома |
0,15 |
из конвертера |
1,0 |
|
Окалина металлолома |
0,29 |
Железо корольков в шлаке |
0,95 |
|
Плавиковый шпат |
0,15 |
|
|
|
Известь |
6,30 |
|
|
|
|
|
|||
Футеровка конвертера, пе- |
|
|
|
|
решедшая в шлак |
0,20 |
|
|
|
Кислород дутья |
6,46 |
|
|
|
|
|
|||
|
|
|
|
|
Всего |
113,11 |
Всего |
113,11 |
|
|
|
|
|
Анализ данных таблицы 10.3 показывает, что основными статьями при-
ходной части теплового баланса являются физическое тепло жидкого чугуна и тепло реакций окисления примесей металлической шихты, из которых 66% –
тепло реакций окисления углерода. Главными статьями расходной части тепло-
вого баланса являются физическое тепло жидкой стали, физическое тепло шла-
ка и тепло отходящих газов.
Расчеты показывают, что при продувке кислородом сверху обычного пе-
редельного чугуна без использования охладителей выделяется количество теп-
ла, достаточное для нагрева ванны до конца процесса до 1850 – 1900оС. Для по-
лучения в конце продувки температуры 1580 – 1650оС расход металлического лома должен составлять 24 – 28%, чугуна – 72 – 76% от массы металлической шихты в зависимости от его состава и температуры. Превышение оптимального

99
Таблица 10.3 – Тепловой баланс плавки до раскисления на 100 кг
металлической шихты в 350 – 400-тонном конвертере
Приходная часть баланса |
Расходная часть баланса |
|
|||||
|
|
|
|
|
|
|
|
Статьи |
кДж |
% |
Статьи |
|
кДж |
|
% |
|
|
|
|
|
|
|
|
Физическое тепло |
|
|
Физическое |
тепло |
|
|
|
жидкого чугуна |
92630 |
52,5 |
жидкой стали |
|
127600 |
|
72,5 |
Тепло окисления |
|
|
Физическое |
тепло |
|
|
|
примесей шихты |
60705 |
34,5 |
конечного шлака |
24955 |
|
14,2 |
|
в том числе: |
|
|
Тепло отходящих |
|
|
|
|
окисление С до |
|
|
газов |
|
13840 |
|
7,9 |
СО (90%) |
29690 |
16,9/49* |
|
|
|
|
|
окисление С до |
|
|
Тепло диссоциации |
|
|
|
|
СО2 (10%) |
10325 |
5,9/17* |
влаги шихты |
|
292 |
|
0,2 |
|
|
|
Тепло диссоциации |
|
|
|
|
окисление Si |
15950 |
9,0/26* |
CaCO3 шихты |
|
878 |
|
0,5 |
|
|
|
Тепло диссоциации |
|
|
|
|
|
|
|
оксидов железа |
|
|
|
|
окисление Mn |
2930 |
1,7/5* |
шихты |
|
1465 |
|
0,8 |
|
|
|
Тепло оксидов ды- |
|
|
|
|
окисление Р |
1810 |
1,0/3* |
ма |
|
2215 |
|
1,2 |
Тепло реакций |
|
|
|
|
|
|
|
связывания SiO2 |
|
|
|
|
|
|
|
и P2O5 в шлаке |
4990 |
2,8 |
Тепло выбросов |
920 |
|
0,5 |
|
Тепло образова- |
|
|
|
|
|
|
|
ния оксидов же- |
|
|
Тепло корольков |
|
|
|
|
леза шлака |
8150 |
4,6 |
шлака |
|
1260 |
|
0,7 |
Тепло окисления |
|
|
Потери тепла кон- |
|
|
|
|
железа дыма |
8863 |
5,1 |
вертером |
|
2695 |
|
1,5 |
Физическое тепло |
|
|
в том числе: |
|
|
|
|
миксерного (до- |
|
|
теплопроводностью |
|
|
|
|
менного) шлака |
782 |
0,5 |
через футеровку |
344 |
|
0,19 |
|
|
|
|
аккумулирование |
|
|
|
|
|
|
|
тепла футеровкой |
1915 |
|
1,07 |
|
|
|
|
с охлаждающей |
|
|
|
|
|
|
|
фурму водой |
|
436 |
|
0,24 |
Всего |
176120 |
100 |
Всего |
|
176120 |
|
100 |
расхода охладителей достигается, как правило, путем увеличения доли тепла реакций окисления железа, в результате чего снижается выход годного.
При охлаждении плавки железной рудой, окалиной, агломератом одна
массовая часть этих охладителей заменяет в среднем 3 – 4 массовых части
100
стального лома. В связи с этим при использовании твердых окислителей в ко-
личестве до 1% от массы металлической шихты расход лома составляет 20 – 25% при расходе чугуна 75 – 80%.
10.5 Выплавка стали из высокофосфористого чугуна
Переработку высокофосфористого чугуна целесообразно организовать таким образом, чтобы вместе с металлом получать фосфат-шлак, содержащий
20 – 25% P2O5 , который можно использовать в сельском хозяйстве в качестве
заменителя дорогостоящего суперфосфата.
Из рисунка 7.1 видно, что получение коэффициентов распределения фос-
фора выше 300 возможно только в узком диапазоне изменения химического со-
става шлака. Обычно значения коэффициента распределения фосфора, которые можно стабильно получать от плавки к плавке, не превышают 250 – 300.
С учетом этого переработка высокофосфористого чугуна с получением фосфат-шлака обычно проводится в два периода. В первом периоде получают фосфат-шлак и металлический полупродукт, содержание фосфора в котором соответствует его концентрации в низкофосфористом чугуне. Во втором пе-
риоде плавки после отделения от металла высокофосфористого шлака получен-
ный полупродукт перерабатывают в сталь.
Вкачестве примера ниже описана технология переработки в кислородном конвертере верхнего дутья чугуна, содержащего 0,4 – 0,5% Si, 0,4 – 0,5% Mn, 1,7 – 1,9% P.
Впервом периоде плавки для обеспечения высокой скорости дефосфора-
ции металла с момента начала продувки в конвертере частично или полностью оставляют шлак предыдущей плавки с высоким содержанием оксидов железа и кальция.
При этом в первом периоде плавки загрузку металлического лома в кон-
вертер не проводят, так как для активного шлакообразования в начальном пе-
риоде плавки необходима высокая температура ванны.