
MS / Лекция_13
.pdf122
13 СПОСОБЫ УВЕЛИЧЕНИЯ ДОЛИ МЕТАЛЛИЧЕСКОГО ЛОМА В ШИХТЕ КИСЛОРОДНЫХ КОНВЕРТЕРОВ
В настоящее время наиболее широко используются следующие способы увеличения доли лома в металлической шихте кислородных конвертеров верх-
него дутья:
∙повышение температуры заливаемого в конвертер чугуна;
∙дожигание СО отходящих газов до СО2 в рабочем пространстве конвер-
тера;
∙использование химических теплоносителей, включая ввод твердого топ-
лива;
∙предварительный нагрев металлического лома в рабочем пространстве конвертера с использованием жидкого и газообразного топлива;
∙предварительный нагрев металлического лома с использованием тепла отходящих газов;
∙выплавка стали под минимальным количеством шлака.
13.1 Повышение температуры заливаемого в конвертер чугуна
Температура передельного чугуна на выпуске из доменных печей обычно составляет 1500 – 1550оС.
Традиционная технология доставки чугуна к сталеплавильным агрегатам предусматривает выпуск его в 100-т или 140-т чугуновозные ковши и доставку в миксерное отделение сталеплавильного цеха. В миксерных отделениях из чу-
гуновозных ковшей скачивают ковшевой шлак и сливают металл в миксер, где происходит накопление чугуна и усреднение химического состава металла, по-
ступающего из разных доменных печей. Из миксера необходимое для плавки количество чугуна переливают в заливочный ковш, в котором металл транспор-
тируют к сталеплавильному агрегату, и заливают в конвертер. При таком спо-

123
собе доставки температура заливаемого в конвертер чугуна обычно не превы-
шает 1300 – 1350оС.
В современных сталеплавильных цехах для доставки чугуна из доменно-
го цеха используются 480 – 600-т ковши миксерного типа (рисунок 13.1).
Рисунок 13.1 – Чугуновозный ковш миксерного типа
В сталеплавильном цехе из ковшей миксерного типа металл переливают в заливочный ковш и после скачивания шлака заливают в сталеплавильный агре-
гат. Такая технология доставки чугуна позволяет уменьшить потери температу-
ры металла на 50 – 70оС.
Для увеличения доли лома в металлической шихте зарубежными фирма-
ми опробована работа кислородных конвертеров с предварительным нагревом чугуна. В качестве примера на рисунке 13.2 приведена схема установки для на-
грева чугуна фирмы «Ajax Magnethermix». Она представляет собой сходный с обычным миксером цилиндрический сосуд, футерованный огнеупорным кир-
пичом и вращающийся вокруг своей оси для выпуска чугуна через летку. Длина этой установки 15 м, диаметр 5,7 м, вместимость 1500 т.
Нагрев чугуна ведется с помощью шести высокопроизводительных ин-
дукционных нагревателей канального типа, расположенных на нижней стороне цилиндра. Под действием электромагнитных сил металл циркулирует по кана-
лам индукционных нагревателей, в которых происходит его нагрев, и возвраща-
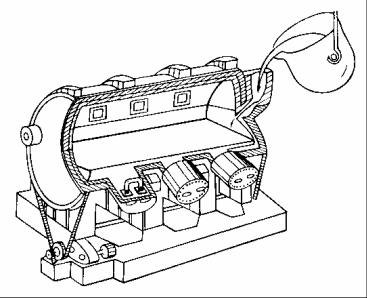
124
Рисунок 13.2 – Схема устройст-
ва для нагрева чугуна с шестью индукционными нагревателями канального типа
ется в ванну. Источником тепла является электрический ток промышленной частоты. Мощность каждого из индукторов может быть доведена до 2,5 МВт.
Расход электроэнергии на нагрев 1 т чугуна на 100оС с учетом электриче-
ских и тепловых потерь в нагревателе составляет 28 кВт·ч. Отсюда следует, что установка с шестью индукторами суммарной мощностью 15 МВт будет иметь производительность 536 т/ч при нагреве металла на 100оС или 179 т/ч при на-
греве на 300оС. Коэффициент полезного действия нагревателей равен 84%.
Так как в рассматриваемом устройстве нагрев металла выполняется при наличии на его поверхности минимального количества шлака, износ футеровки незначителен. Имеются сведения о том, что ее меняют раз в 2 года после пере-
работки 3 млн. т чугуна.
Согласно данным фирмы «Energy Materials Conservation Corporation» (США) производительность кислородно-конвертерного цеха при использова-
нии оборудования для предварительного нагрева чугуна может увеличиться на
13 – 15% без роста его потребления. При этом расход электроэнергии на 1 т до-
полнительно выплавленной стали составляет 450 кВт·ч, что на 25% ниже, чем в дуговых электросталеплавильных печах.
Вместе с тем не следует забывать, что на тепловых электростанциях ко-
эффициент полезного использования энергии топлива составляет менее 40%, а
также о потерях в электрических сетях. В результате суммарный коэффициент
125
использования энергии топлива при применении установок такого типа для на-
грева чугуна составляет ~ 30%. Он выше чем при переработке металлического лома в электропечах (20 – 24%), но существенно ниже чем при непосредствен-
ном сжигании топлива в рабочем пространстве конвертера и частичном исполь-
зовании тепла отходящих газов в котлах-утилизаторах. Поэтому экономическая целесообразность повышения температуры чугуна с использованием индукци-
онного нагрева окончательно не ясна и требует дополнительной проработки для условий каждого завода.
13.2Дожигание оксида углерода отходящих газов в рабочем пространстве конвертера
Отходящие из кислородного конвертера газы содержат 80 – 90% СО, до-
жигание которого до СО2 сопровождается выделением большого количества тепла ( ΔH 298o = – 565,64 кДж/моль О2).
Однако, работа конвертера с дожиганием СО отходящих газов в рабочем пространстве имеет также ряд существенных недостатков:
∙температура горения нагретого СО в кислороде достигает 3000оС, в ре-
зультате чего резко снижается стойкость футеровки верхней части кон-
вертера;
∙при дожигании СО в рабочем пространстве конвертера увеличивается окисленность шлака и потери металла с ним;
∙шлаки с повышенным содержанием FeO склонны к вспениванию, что за-
трудняет использование полученного от дожигания СО тепла для нагрева металла.
Для дожигания оксида углерода в конвертерах верхнего дутья кислород
подается с помощью двухъярусных фурм. В качестве примера рисунке 13.3 по-
казана конструкция двухъярусной фурмы, которая использовалась при выплав-
ке стали в 130-т конвертерах комбината «Криворожсталь». Головкой ее служи-
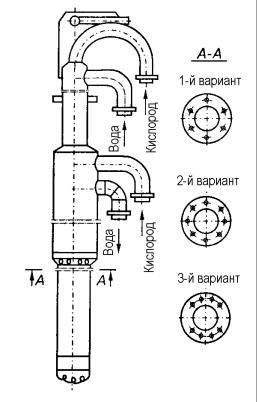
126
Рисунок 13.3 – Двухъярусная кислородная фурма для дожигания СО отходящих газов в рабочем пространстве конвертера
ла обычная пятисопловая кислородная фурма с углом наклона оси сопел к вер-
тикали 20о, рассчитанная на расход кислорода 6,7 – 8,3 м3/с. При продувке го-
ловка фурмы располагалась на 1000 мм выше уровня спокойной ванны. Фурмы второго яруса имели диаметр 15 и 18 мм, угол наклона оси фурмы к вертикали
30 и 45о и располагались на удалении 1650 мм от нижнего торца головки. Рас-
ход кислорода через верхние сопла составлял 30 – 35% расхода кислорода через сопла головки фурмы.
Было установлено, что в 130-т конвертерах дожигание СО позволяет по-
высить содержание СО2 в отходящих газах на уровне горловине конвертера до
25 – 30%. За счет тепла, полученного при дожигании оксида углерода, долю металлического лома в шихте можно увеличить на 3 – 10% (рисунок 13.4). Од-
новременно при том же газоотводящем тракте можно увеличить интенсивность продувки, повысив производительность конвертера на 10 – 27%.
Коэффициент использования тепла от дожигания СО, рассчитанный как отношение приращения теплоемкости жидкого металла к общему количеству тепла, выделившегося при протекании реакции, авторами различных исследо-
ваний оценивается в 50 – 65%.
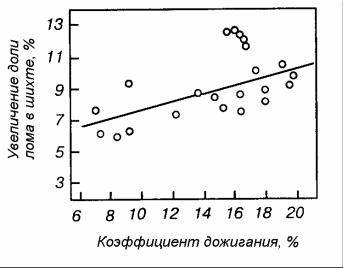
127
Рисунок 13.4 – Зависимость увели-
чения доли лома в металлической шихте от коэффициента дожигания оксида углерода
Донниичерметом разработана технология конвертерной плавки с цикли-
ческим перемещением фурмы обычной конструкции по ходу продувки. После опускания в рабочее положение и 3 – 5 минут продувки фурма начинает совер-
шать возвратно-поступательное движение в вертикальной плоскости с заранее заданной амплитудой. Длительность одного цикла перемещения фурмы состав-
ляет не более 30 секунд. Перемещение фурмы прекращают за 1 – 2 минуты до окончания продувки. В каждом из циклов при движении фурмы вверх происхо-
дит дожигание СО и осаждение вспененного шлака, а при движении вниз - пе-
редача тепла жидкому металлу. Такой режим продувки позволяет увеличить расход металлического лома на 20 – 30 кг/т с соответствующим уменьшением расхода чугуна.
13.3 Использование химических теплоносителей и твердого топлива
С целью увеличения доли металлического лома в шихте кислородных конвертеров зарубежные предприятия широко используют растворение в чугу-
не алюминиевого лома, присадку в конвертер SiC, CaC2 и др.
Присадка CaC2 предпочтительна, так как при этом не увеличивается мас-
са шлака и для получения необходимой его основности требуется меньший расход извести. Сообщается, что использование CaC2 в количестве 50 кг/т вы-
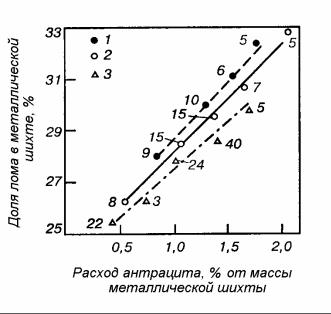
128
плавляемой стали расход металлического лома увеличивается до 50% от массы металлической шихты.
На металлургических предприятиях Украины наиболее целесообразным способом увеличения доли лома в металлической шихте за счет использования твердого топлива считается загрузка в конвертер кокса или антрацита вместе со скрапом и сжигание его в потоке кислорода, подаваемого через верхнюю фур-
му.
В конвертеры верхнего дутья топливо загружают в виде скрап-угольных брикетов или в чистом виде перед завалкой металлического лома. Опробована также подача топлива на поверхность жидкого чугуна в конвертере одновре-
менно с началом продувки. При этом химическое тепло топлива используется на ~ 25%.
Зависимость доли лома в металлической шихте от расхода антрацита, по-
лученная по результатам исследований в 130-т конвертерах комбината «Криво-
рожсталь», показана на рисунке 13.5.
Рисунок 13.5 – Зависимость доли лома в металлической шихте от расхода антрацита:
1 – при использовании скрап-угольных брикетов; 2 – при за-
грузке твердого топлива до завалки лома; 3 – присадка антраци-
та на поверхность жидкого чугуна
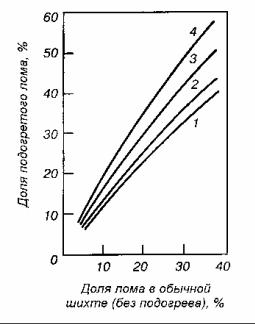
129
13.4 Использованием жидкого и газообразного топлива
На рисунке 13.6 представлена расчетная зависимость доли лома в метал-
лической шихте кислородного конвертера от температуры его нагрева. Из ри-
сунка видно, что значительное увеличение доли металлического лома в шихте возможно только при нагреве его до температур не менее 700 – 800оС.
Рисунок 13.6 – Зависимость доли лома в ме-
таллической шихте от температуры его на-
грева, оС:
1 – 260; 2 – 538; 3 – 815; 4 – 1093
Нагрев лома с использованием кислородно-топливных горелок возможен как в специальных устройствах (печах, ковшах, совках) перед загрузкой в кон-
вертер, так и непосредственно в рабочем пространстве конвертера.
Предварительный нагрев лома в простых устройствах типа совков или ковшей не обеспечивает существенного увеличения доли его в шихте. Это свя-
зано с тем, что средняя температура нагрева лома в этом случае не превышает
500 – 600оС. Превышение этих пределов приводит к оплавлению его поверхно-
сти и образованию конгломератов больших размеров, что делает невозможной загрузку лома в конвертер.
На рисунке 13.7 показана зависимость средней температуры металличе-
ского лома от продолжительности его нагрева мазутными и газовыми горелка-
ми тепловой мощностью 35 МВт, полученная по результатам исследования в
130-т конвертерах комбината «Криворожсталь».

130
Рисунок 13.7 – Зависимость средней температуры металлического лома от продолжительности его нагрева в
130-т конвертерах горелками с теп-
ловой мощностью 35 МВт
Из рисунка видно, что для повышения средней температуры металличе-
ского лома до 700 – 800оС необходимо время, сопоставимое с продолжительно-
стью продувки. Поэтому при работе конвертеров с нагревом лома в рабочем пространстве их производительность значительно понижается.
13.5 Использование физического тепла отходящих газов
Примером агрегата, в котором для нагрева металлического лома успешно используется тепло отходящих газов, является конвертер (печь) EOF (от анг-
лийского Energy Optimizing Furnace). Внешний вид агрегата показан на рисун-
ке 13.8, принцип его работы поясняется схемой на рисунке 13.9.
Конвертер EOF имеет круглое рабочее пространство, футерованное из-
нутри огнеупорной кладкой, с водоохлаждаемыми стенками и сводом.
В подине конвертера установлены фурмы типа «труба в трубе», которые позволяют вдувать в жидкую ванну, где протекают реакции рафинирования,
кислород в защитной оболочке из азота или СО2 и угольную пыль.
В корпусе печи смонтированы инжекторы кислорода. С их помощью ки-
слород подается в газошлакометаллическую смесь над расплавом, в которой происходит дожигание выделяющегося из металла СО до СО2 с частичной пе-
редачей тепла жидкой ванне. Имеются также кислородные горелки, которые ис-

131
Рисунок 13.8 – Внешний вид конвертера
EOF
Рисунок 13.9 – Схема конвертера EOF: 1 – жидкая ванна; 2 – газошлакометал-
лическая смесь над расплавом; 3 – зона
газовой фазы; 4 – нагреватель металли-
ческого лома; 5 – нагреватель воздуха