
MS / Лекция_18
.pdf178
18.1.5 Модифицирование неметаллических включений в стали
Модифицирование (от английского modification – изменение) – измене- ние состава и формы неметаллических включений, целью которого является получение включений, которые оказывают минимальное негативное воздейст- вие на механические и эксплуатационные свойства металла.
Примером может служить модифицирование неметаллических включе- ний в раскисленной алюминием стали кальцием.
Обычно в раскисленной алюминием стали оксидные неметаллические включения представлены глиноземом, а сульфидные – сульфидами марганца II и III типов по классификации Симса.
Оседание включений глинозема на стенках сталеразливочных стаканов приводит к их затягиванию, что затрудняет разливку металла на МНЛЗ.
При горячей прокатке хрупкое разрушение включений глинозема и де- формация сульфидов марганца приводит к появлению дефекта, называемого анизотропией механических свойств стали.
Если после ввода алюминия сталь дополнительно обрабатывают кальци- ем, он частично заменяет алюминий в составе неметаллических включений. В результате образуются алюминаты кальция, которые имеют низкие температу- ры плавления и присутствуют в металле в виде мелких включений, форма ко- торых близка к сферической. На поверхности алюминатов кальция могут на- блюдаться сульфидные оболочки.
Включения такого состава не затягивают сталеразливочные стаканы. При горячей прокатке алюминаты кальция практически не деформируются, что спо- собствует получению изотропного металла.
18.2 Обработка стали инертным газом
Продувка инертным газом применяется для усреднения химического со- става и температуры металла, корректировки температуры стали перед разлив-
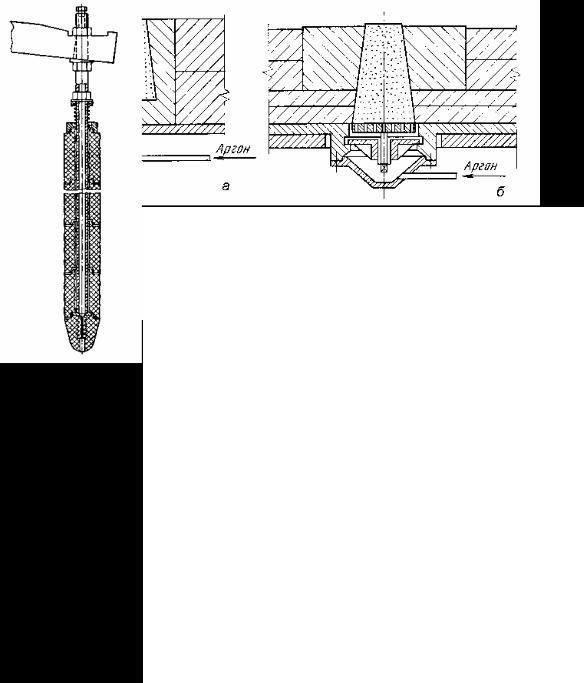
179
кой, перемешивания металла и шлака с целью повышения скорости химических реакций, дегазации расплава и удаления неметаллических включений.
Для ввода инертного газа в металл используют пористые пробки в днище сталеразливочного ковша из муллитового, корундового, магнезитового или цирконо-силикатного огнеупорного материала (рисунок 18.4) и погружаемые в расплав фурмы (рисунок 18.5). Значительно реже для продувки металла ис- пользуют фурмы, установленные в разливочном канале шиберного затвора.
Рисунок 18.4 – Схема установки пористой огнеупорной вставки в днище ковша при монтаже вставки изнутри (а) и снаружи (б)
Рисунок 18.5 – Фурма в виде ложного стопора для продув- ки металла в ковше
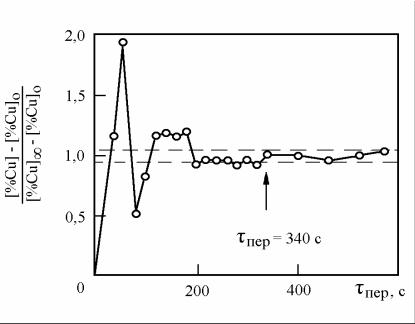
180
Для продувки металла обычно используют аргон, который является наи- более доступным из инертных газов. В некоторых случаев без ущерба для каче- ства металла его можно заменить более дешевым азотом.
18.2.1 Усреднение химического состава и температуры металла
Принцип определения времени полного перемешивания металла при продувке газом поясняется схемой на рисунке 18.6.
Рисунок 18.6 – Изменение концентрации индикатора в пробах металла во время продувки
Определение времени полного перемешивания стали при продувке обыч- но проводится согласно следующей методике. После подачи в расплав извест- ного количества индикатора в фиксированной точке внутри ковша начинают отбор проб металла для химического анализа. При этом первоначально содер- жание индикатора в отобранных пробах изменяется в широких пределах. Спус- тя некоторое время концентрация индикатора в объеме ковша выравнивается и в дальнейшем содержание его в пробах металла отличается от расчетного зна- чения не более, чем на 5%. Это время и принято считать временем полного пе- ремешивания.
181
Экспериментально установлено, что время полного перемешивания свя- зано с величиной скорости диссипации энергии в расплаве соотношением
τ= ( 600 ±100 )ε− 0,4 ,
где τ – время, с; ε – скорость диссипации энергии, Вт/т.
При вдувании газа в металл работа, совершаемая газом, уравнением
(18.3)
определяется
|
|
|
P |
|
|
|
P |
|
|
T |
|
|
|
T |
|
|
|
2 |
|
|
|
|
|
|
1 |
T |
+ 1 |
|
|
|
|
|
|
|
|
||||||||
ε = |
nRT |
ln |
+ η |
n |
ln |
n |
− |
|
n |
+ |
|
n |
|
|
0,5ρ |
U |
, |
(18.4) |
|||
|
|
|
|
|
|
|
|
||||||||||||||
|
|
L |
P |
|
T |
P |
|
|
T |
|
|
|
P T |
L |
|
|
n n |
|
|||
|
|
|
o |
L |
1 |
|
|
|
L |
|
|
n |
|
|
|
|
|
||||
где n – молекулярная скорость истечения газа; T |
L |
– температура металла; P – |
|||||||||||||||||||
|
|
|
|
|
|
|
|
|
|
|
|
|
|
|
|
|
|
|
|
1 |
статическое давление на уровне выходного отверстия фурмы; Po – давление над поверхностью расплава; Pn , Tn , ρn и U n – соответственно давление, темпера-
тура, плотность и скорость газа на выходе из фурмы; η – коэффициент, величи-
ной которого учитывается доля различных составляющих перемешивания, эф- фективно используемая для усреднения состава металла.
По сути первое слагаемое в правой части уравнения (18.4) представляет собой работу изотермического расширения пузырей газа при подъеме в метал- ле. Четвертое слагаемое – работа, совершаемая при передаче кинетической энергии газа жидкости. Второе и третье слагаемые – работа расширения газа, которое обусловлено изменением его температуры и давления вблизи выходно- го отверстия фурмы.
Результаты экспериментов на холодных моделях свидетельствуют о том, что численное значение коэффициента η обычно составляет 0,05 – 0,1. Поэто-
му в оценочных расчетах тремя последними слагаемыми в правой части урав- нения (18.4) с достаточной для практических целей точностью можно пренеб- речь и приравнять работу перемешивания металла газом к работе изотермиче- ского расширения всплывающих в расплаве пузырей.
В практических расчетах удобно пользоваться величинами, которые имеют следующую размерность: скорость диссипации энергии ( ε ), Вт; объем-
182
ная скорость подачи газа в металл (VG ), нм3/мин; температура стали (TL ), К;
плотность металла ( ρL ), кг/м3; ускорение силы тяжести ( g ), м/с2; глубина вво-
да газа в металл ( H o ), м; давление над поверхностью расплава ( Po ), атм. Тогда уравнение (18.4) может быть приведено к виду
|
|
|
|
|
|
|
ρ |
L |
gH |
o |
|
|
|
|
ε = |
|
|
|
|
+ |
|
|
|
|
. |
(18.5) |
|||
6,18V |
T |
L |
ln 1 |
|
|
|
|
|
|
|||||
103000P |
||||||||||||||
|
G |
|
|
|
|
|
||||||||
|
|
|
|
|
|
|
|
|
|
o |
|
|
Расчеты, проведенные согласно описанной выше методике, свидетельст- вуют о том, что в стандартных сталеразливочных ковшах с отношением высоты к диаметру равным 1,0 – 1,5 для усреднения химического состава и температу- ры стали необходим расход аргона не более 0,05 – 0,1 м3/т.
18.2.2 Корректировка температуры металла перед разливкой
Потери тепла излучением с бурлящей поверхности расплава при продув- ке металла аргоном выше, чем с поверхности спокойного расплава. Это позво- ляет использовать продувку стали в ковше аргоном как способ получения за- данной температуры металла перед разливкой.
В качестве примера на рисунке 18.7 приведены данные об изменении температуры металла перед выпуском из 200-т конвертера и перед разливкой после охлаждения до заданной температуры продувкой в ковше аргоном.
На рисунке 18.8 приведены данные о скорости понижения температуры стали при продувке аргоном в ковше. Из рисунка видно, что скорость охлажде- ния стали увеличивается при повышении расхода газа и уменьшении массы об- рабатываемого металла. Средние значения скорости охлаждения стали при про- дувке аргоном в ковше составляют 2 – 4 оС/мин.
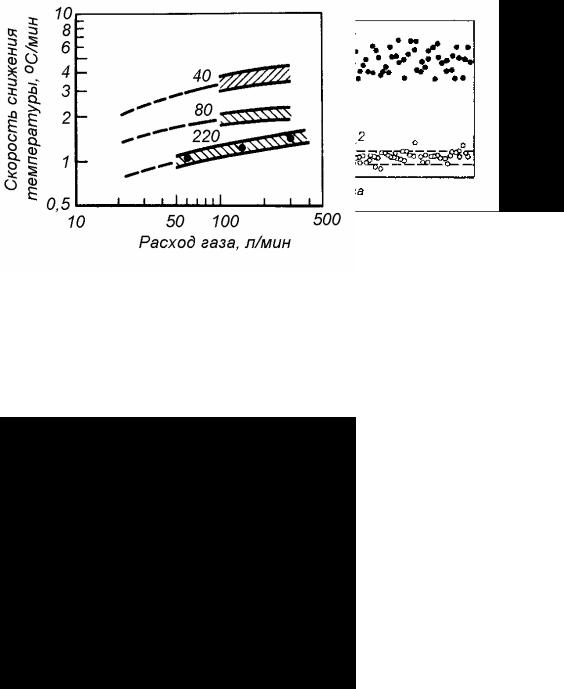
183
Рисунок 18.7 – Значения температуры металла на отдельных плавках текущего производства, следующих одна за другой:
1 – последнее измерение температуры металла в конвертере перед выпуском; 2
– последнее измерение температуры металла в ковше в конце продувки арго- ном (штриховые линии – верхняя и нижняя границы требуемой температуры)
Рисунок 18.8 – Зависимость ско- рости понижения температуры стали от расхода инертного газа (цифры у кривых – масса метал- ла в ковше, т)
18.2.3Перемешивание металла и шлака для повышения скорости химических реакций
При температурах сталеплавильных процессов большинство реакций ме- жду шлаком и металлом протекает в диффузионной области, то есть скорость реакции ограничена массоотдачей взаимодействующих веществ в объеме ме- талла или шлака. Наиболее эффективным способом повышения скорости таких реакций является увеличение площади поверхности раздела взаимодействую-
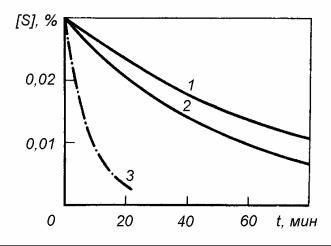
184
щих фаз.
Прохождение пузырей газа через границу раздела металл-шлак сопровож- дается выбрасыванием в шлак капель стали. Эти капли имеют малые размеры и большую удельную поверхностью, в результате чего площадь поверхности раз- дела металла и шлака существенно увеличивается.
В качестве примера на рисунке 18.9 приведены данные об изменении со- держания серы в стали при различной мощности перемешивания металла и шлака в 100-т ковше.
Рисунок 18.9 – Зависимость содер- жания серы в стали от времени при различной мощности перемешива- ния металла в 100-т ковше, Вт/м2:
1 – 500; 2 – 750; 3 – 4000
18.2.4 Дегазация стали при продувке аргоном в ковше
При продувке стали инертным газом парциальное давление азота и водо- рода в пузырьках газа в момент образования их в металле близко к нулю. Поэто- му в процессе удаления пузырей из расплава растворенные в стали газы диф- фундируют в объем пузырей и выносятся ими в атмосферу.
Для приблизительной оценки расхода нейтрального газа на дегазацию ста- ли может быть использована формула Геллера. При выводе этой зависимости сделано допущение, согласно которому за время пребывания пузырей в металле между расплавом и газовой фазой достигается состояние термодинамического равновесия. Поэтому формула позволяет оценить минимально необходимый расход нейтрального газа для дегазации стали. Если в реальных процессах за время пребывания пузырей в металле состояние равновесия не достигается, не-
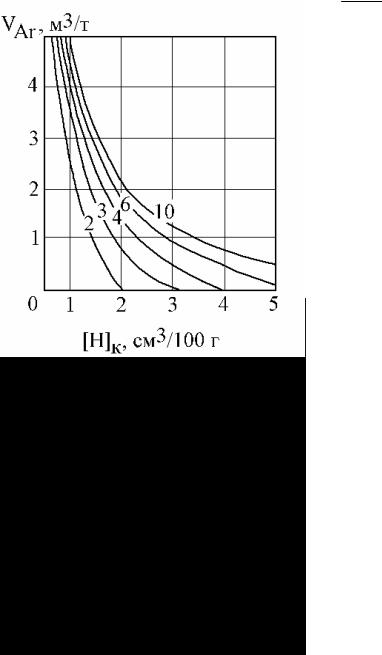
185
обходимое для дегазации стали количество нейтрального газа изменяется только в сторону увеличения.
Ниже приведена формула Геллера для случая, когда продувка проводится с целью удаления из металла водорода
V Ar |
= |
224 |
||
|
|
|||
M H |
2 |
|||
|
|
|||
|
|
|
|
2 |
|
1 |
|
PK |
||||
|
[H] |
|||
|
H |
|||
|
|
|
|
− 1
[H]o
|
+ [H] − [H] |
|
|
|
, |
(18.6) |
|
|
|
o |
|
|
|
||
|
|
|
где V Ar – объем продуваемого через металл аргона, м3/т; M H 2 – относитель-
ная молекулярная масса удаляемого газа; P – давление над поверхностью ме-
талла × 10–5, Па; K H – константа равновесия реакции растворения газа в ме-
талле; [H]o и [H] – исходная и конечная концентрации водорода в стали, %.
Результаты проведенного согласно уравнению (18.6) расчета необходимо- го для дегазации металла расхода аргона показаны на рисунке 18.10.
Рисунок 18.10 – Зависимость расхода аргона от начального и конечного со- держания водорода в стали. Цифры у кривых – исходное содержание водо- рода, см3/100 г металла
Анализ приведенных на рисунке данных показывает, что для получения в стали остаточного содержания водорода менее 2 см3/100 г необходим расход аргона 1,5 – 2 м3/т. На практике при продувке стали инертным газом с целью усреднения химического состава и температуры, а также интенсификации пе-

186
ремешивания металла с ковшевым шлаком удельный расход аргона обычно со- ставляет 0,05 – 0,2 м3/т. В связи с этим продувка стали аргоном в открытых ковшах обычно не сопровождается существенной дегазацией металла.
Анализ уравнения (18.6) свидетельствует также о том, что необходимый для дегазации стали расход аргона быстро уменьшается при понижении давле- ния над поверхностью расплава. В связи с этим сочетание продувки стали инертным газом и вакуумной обработки может быть весьма эффективным спо- собом ее дегазации.
18.2.5 Удаление неметаллических включений
Перемешивание металла при продувке аргоном в ковше способствует по- вышению скорости удаления из расплава неметаллических включений, для ко- торых характерны высокие значения межфазного натяжения на границе металл- включение, например, глинозема. В качестве примера на рисунке 18.11 приве- дены экспериментально установленные зависимости скорости удаления вклю- чений от концентрации глинозема в стали без продувки аргоном и при ее ис- пользовании.
Рисунок 18.11 – Зависимость скорости изменения концентрации глинозема в стали от начального его содержания:
1 – плавки без продувки металла ар- гоном; 2 – плавки с продувкой
187
18.3 Внепечная десульфурация стали
18.3.1Обработка стали синтетическими шлаками, самоплавкими и твердыми шлакообразующими смесями
Синтетическим (от английского synthetic – искусственный) называют предназначенный для обработки стали в ковше шлак, который получают вне сталеплавильного агрегата.
Синтетические шлаки выплавляют в электропечах, циклонных плавиль- ных установках и других агрегатах. Жидкий шлак в необходимом количестве сливают в сталеразливочный ковш, который подают под выпуск. В процессе выпуска струя падающего в ковш металла эмульгирует шлак и металл с после- дующим разделением фаз . В результате эмульгирования резко увеличивается площадь поверхности раздела шлак-металл и скорость протекающих реакций. Результаты обработки определяются высотой падения струи металла, массой металла и шлака, физическими характеристиками и составом шлака и др. Обычно при расходах синтетического шлака 30 – 50 кг/т такая обработка по- зволяет в ходе выпуска плавки получать степень десульфурации стали равную 30 – 70%. Наиболее эффективная десульфурация металла наблюдается при вы- пуске плавки из крупнотоннажных агрегатов.
Первоначально для внепечной десульфурации стали были разработаны известково-глиноземистые шлаки состава, % масс.: 50 – 55 CaO, 37 – 43 Al2O3, ≤ 7 SiO2, ≤ 7 MgO, ≤ 0,5 FeO. Для выплавки синтетических шлаков такого со-
става требовались дефицитные материалы с низким содержанием кремнезема. Впоследствии была показана возможность эффективной десульфурации
стали известково-шамотными шлаками состава, % масс.: 48 – 56 CaO, 6 – 10
MgO, 18 – 22 SiO2, 12 – 16 Al2O3, 0,5 CaF2, ≤ 0,5 FeO.
Широкое использование синтетических шлаков сдерживалось отсутстви- ем возможности размещения в существующих сталеплавильных цехах обору- дования для их выплавки. В связи с этим была разработана технология десуль-