
MS / Лекция_18
.pdf188
фурации стали в ковше самоплавкими шлаковыми смесями состава, % масс.: 12
– 14 алюминиевый порошок или алюминиевая стружка; 21 – 24 натриевая се- литра; 20 флюоритовый концентрат; известь – остальное. Необходимое количе- ство самоплавкой шлаковой смеси загружали в чугуновозный ковш и поджига- ли. Полученный таким способом жидкий шлак переливали из чугуновозного ковша в сталеразливочный и подавали под выпуск.
Использование самоплавких шлаковых смесей существенно упростило технологию получения синтетических шлаков. Однако, после нескольких круп- ных пожаров в отделениях подготовки смесей металлургические предприятия
СССР от их использования отказались.
В настоящее время для внепечной десульфурации стали успешно исполь- зуют твердые шлакообразующие смеси из 10 – 30% плавикового шпата и извес- ти. По ходу выпуска плавки смесь вместе с раскислителями и легирующими за- гружают в ковш, при этом плавление смеси обычно завершается в течение 1 – 2 минут.
Особенность этой технологии заключается в том, что однородный шлак получается при наполнении второй половины ковша, когда мощность переме- шивания стали и шлака падающей в ковш струей металла значительно умень- шается. В связи с этим десульфурирующая способность шлака используется не полностью. Поэтому после выпуска плавки целесообразно проводить дополни- тельное перемешивание шлака и металла продувкой в ковше аргоном.
Для повышения эффективности десульфурации стали на выпуске из ста- леплавильного агрегата применяются предварительно переплавленные легко- плавкие шлаковые смеси. Примером может служить рафинирующая смесь ИРС-2 производства ОАО «НПП «Техмет» (г. Донецк) состава, % масс.: ≤ 3 C,
53 – 60 CaOобщ, ≤ 6 MgO, ≤ 16 SiO2, 4 – 8 F, 4 – 6 (Na2O + K2O), 10 – 18 Al2O3,
≤ 0,5 S, ≤ 1,5 P2O5, ≤ 2 MnO, ≤ 3 FeO. Основность смеси, рассчитанная как от-
ношение концентраций CaO и SiO2, обычно составляет не менее 3,5. Темпера-
тура плавления смеси не превышает 1320 – 1350оС.
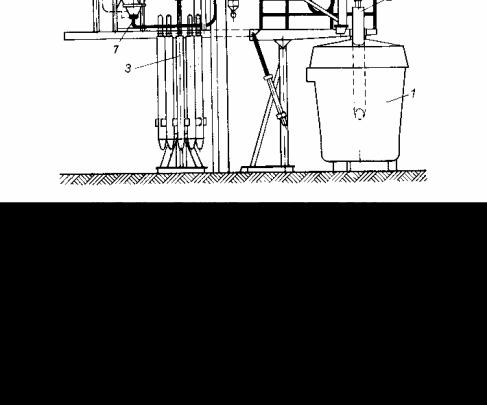
189
18.3.2 Продувка стали порошкообразными материалами
Схема установок для вдувания порошкообразных материалов в металл приведена на рисунке 18.12.
Рисунок 18.12 – Современная установка для вдувания в металл порошкообраз- ных материалов:
1 – ковш, накрытый крышкой; 2 – фурма; 3 – карусельная установка с запасны- ми фурмами; 4 – расходный бункер; 5 – накопительные бункера; 6 - пылеулав- ливающая установка; 7 трубопроводы для подачи порошков от расходного бун- кера к фурме
Для хранения и дозированной выдачи порошков служат пневмокамерный питатели, конструкция которых показана на рисунке 18.13.
Если в металл вдувают смесь порошкообразных материалов различного состава, для накопления и дозирования каждого из них предусмотрены отдель- ные бункера. Смешивание порошков осуществляется в пневмотрассе.
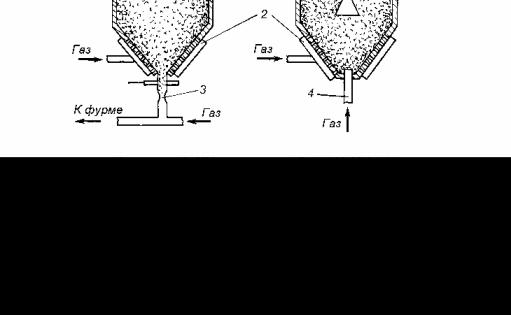
190
Рисунок 18.13 – Схемы пневмокамерных питателей для вдувания порошкооб- разных материалов:
а – питатель с нижней выдачей порошка; б – питатель с верхней выдачей по- рошка; 1 – бункер высокого давления; 2 – подвод газа для создания кипящего слоя; 3 – дозирующее отверстие; 4 – подвод газа для аэрации порошка; 5 - тру- бопровод для подачи газопорошковой смеси; 6 – люк для загрузки порошков; 7
–устройство для взвешивания
Вкачестве транспортирующего газа для вдувания порошкообразных ма- териалов в сталь обычно используют аргон.
Для десульфурации стали используют продувку порошками извести, а также смесями извести с плавиковым шпатом, алюминием, титаном и другими раскислителями. В этом случае высокая скорость десульфурации металла дос- тигается благодаря большой удельной поверхности частиц извести, а также в результате перемешивания металла с поверхностным шлаком всплывающими пузырями газа.
Впоследние годы получила широкое распространение десульфурация стали с использованием щелочноземельных металлов (ЩЗМ), а также их спла- вов и химических соединений (гранулированный магний, порошки силикокаль- ция, карбида кальция и др.).
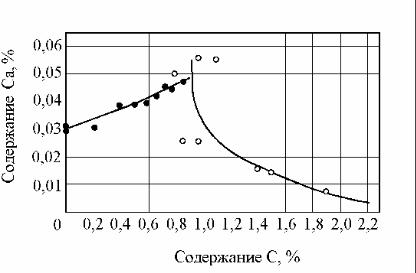
191
Характер процессов, протекающих при вводе карбида кальция в металл, поясняется рисунком 18.14.
Рисунок 18.14 – Влияние углерода на растворимость кальция в железе при
1600оС
Из приведенных данных видно, что растворимость кальция в железе уве- личивается при повышении содержания углерода примерно до 0,8 – 0,9%. Дальнейшее увеличение концентрации углерода сопровождается резким уменьшением растворимости кальция, которое объясняется началом протека- ния реакции образования карбида кальция.
Химическая устойчивость карбида кальция в высокоуглеродистых рас- плавах является причиной принципиального различия в механизме реакций, протекающих при обработке карбидом кальция низко- и среднеуглеродистой стали и чугуна. При обработке низкоуглеродистого металла карбид кальция в расплаве термодинамически не устойчив и диссоциирует по реакции
CaC2 |
= {Ca} + 2[C] . |
(18.7) |
В чугуне карбид кальция является устойчивым соединением, и реакции рафи- нирования протекают с участием твердых частиц карбида.
Рисунок 18.15 поясняет характер процессов, протекающих при вводе в
сталь силикокальция.
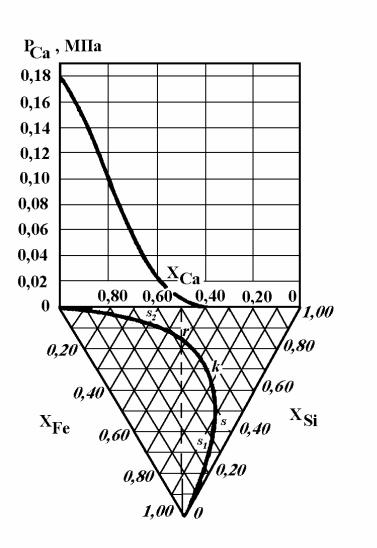
192
Рисунок 18.15 – Процессы, протекающие при растворении силикокальция в железе при 1600оС
В процессе растворения частицы силикокальция обогащаются железом. При этом их химический состав изменяется вдоль пунктирной прямой на рисунке 18.15. В точке r система расслаивается на две несмешивающиеся жидкости, одна из которых обогащена кальцием, а другая – железом. При дальнейшем растворе- нии образовавшихся жидкостей их химический состав изменяется вдоль линий r – s2 – 0 и r – s – s1 – 0 диаграммы. При этом давление насыщенного пара кальция над богатым кальцием расплавом быстро увеличивается и начинается его испаре- ние. Расчеты показывают, что при вводе силикокальция в сталь количества испа- рившегося кальция и кальция, непосредственно растворяющегося в металле, соот- носятся как 17:1.
193
Таким образом, характер взаимодействия кальция с расплавом при вводе в низкоуглеродистую сталь металлического кальция, силикокальция и карбида кальция существенно не различается. Опыт показывает, что в большинстве случаев результаты обработки определяются общим количеством введенного в
сталь кальция и практически не зависят от того, в каком виде он подан в ме- талл.
Низкие температуры кипения магния и кальция (магний – 1107оС, каль- ций – 1487оС) и крайне ограниченная растворимость их в расплавах железа приводят к тому, что основное количество этих реагентов удаляется из распла- ва в виде пузырей пара, у поверхности которых протекают химические реакции между парообразным десульфуратором и примесями металла. При этом высо- кая скорость десульфурации достигается благодаря большой площади поверх- ности раздела всплывающих пузырей пара ЩЗМ с расплавом.
Для эффективной десульфурации стали продувкой порошками извести и ЩЗМ необходимо соблюдение следующих требований:
∙при выпуске стали из сталеплавильного агрегата необходимо с максимально возможной полнотой отделить от металла окислительный печной шлак и на- вести в ковше новый шлак высокой основности с минимальным содержани- ем оксидов железа. Чтобы избежать оголения поверхности металла при бур- лении во время обработки количество ковшевого шлака должно быть не ме-
нее 10 – 12 кг/т;
∙перед десульфурацией сталь должна быть глубоко раскислена. Обычно с этой целью ее рекомендуют обрабатывать алюминием, остаточное со- держание которого должно быть не менее 0,02%;
∙при инжектировании порошков или гранул ЩЗМ в расплав через погру- жаемые в металл фурмы в качестве транспортирующего газа должен ис- пользоваться аргон;
∙при необходимости глубокой десульфурации стали рекомендуется также отказаться от использования сталеразливочных ковшей с шамотной фу- теровкой, заменив ее высокоглиноземистой, магнезитовой или доломито-
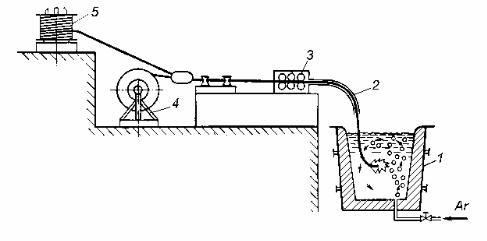
194
вой. Известно, например, что при использовании ковшей с высокоглино- земистой и магнезитовой футеровкой степень использования кальция для десульфурации стали соответственно в 1,6 и 2 раза выше, чем при обра- ботке в ковшах с шамотной футеровкой;
∙чтобы избежать повышения окислености металла и шлака при взаимо- действии с кислородом воздуха и для создания над поверхностью металла атмосферы с низким окислительным потенциалом ковш на период обра-
ботки целесообразно накрывать крышкой.
Для десульфурации и модифицирования стали ЩЗМ используют также подачу их в металл в виде порошковой проволоки (рисунок 18.16).
Рисунок 18.16 – Схема ввода порошковой проволоки в сталеразливочный ковш: 1 – ковш; 2 – направляющая труба; 3 – трайб-аппарат; 4 – разматывающее уст- ройство; 5 – бухта порошковой проволоки
Обычно с этой целью используют порошковые проволоки диаметром 10 – 16 мм. В зависимости от тоннажа ковша и температуры стали скорость ввода порошковой проволоки в металл находится в пределах 3 – 6 м/с.
18.4 Вакуумирование стали
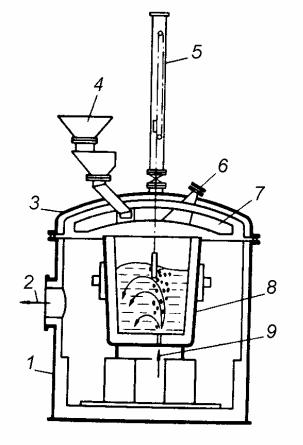
195
18.4.1 Вакуумная дегазация стали
Широко используемые промышленностью способы вакуумной дегазации стали можно разделить на три основные группы:
∙вакуумирование в ковше (в вакуумной камере, в вакуумном ковше);
∙вакуумирование порций металла (порционное и циркуляционное вакуу- мирование);
∙вакуумирование при технологических переливах (при переливе из ковша в ковш, при разливке в изложницы, на выпуске из сталеплавильного агре- гата, при переливе из сталеразливочного ковша в промежуточный ковш МНЛЗ и др.).
Схема процесса вакуумной обработки стали в ковше представлена на ри-
сунке 18.17
Рисунок 18.17 – Схема процесса ваку- умной обработки стали в ковше:
1 – вакуумная камера; 2 – вакуумпровод к вакуумным насосам; 3 – крышка ваку- умной камеры; 4 – бункер для ввода раскислителей и легирующих; 5 – уст- ройство для отбора проб металла и за- мера температуры; 6 – гляделка; 7 – за- щитный экран; 8 – сталеразливочный ковш; 9 – подача аргона
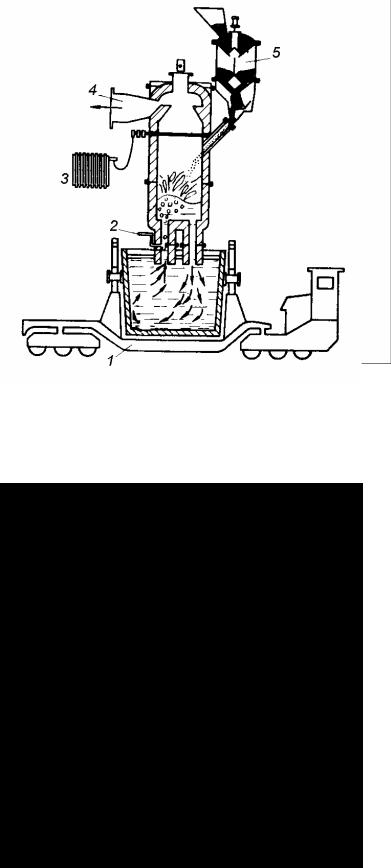
196
На рисунке 18.18 приведена схема процесса порционного вакуумирова- ния стали (DH процесс – от названия фирмы «Dortmund-Hörder Hüttennunion», ФРГ).
Рисунок 18.18 – Схема про- цесса порционного вакууми- рования стали:
а – камера в нижнем положе- нии; б – камера в верхнем положении; 1 – ковш; 2 – ва- куумная камера; 3 – бункер для ввода раскислителей и легирующих; 4 – графитовый электрод для нагрева футе- ровки камеры
Схема процесса циркуляционного вакуумирования стали (RH процесс – от названий фирм «Ruhrstahl AG» и «Heraeus», ФРГ) показана на рисунке
18.19.
Рисунок 18.19 – Схема процесса циркуляционного вакуумирова- ния стали:
1 – тележка; 2 – подача транс- портирующего газа; 3 – транс- форматор; 4 – вакуумпровод к вакуумным насосам; 5 – бункер для раскислителей и легирую- щих
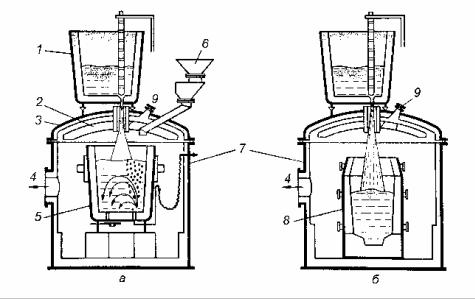
197
Схема процесса вакуумной обработки стали при технологических пере- ливах приведена на рисунке 18.20.
Рисунок 18.20 – Схема процесса вакуумирования стали при переливе:
а – из ковша в ковш; б – при отливке слитков; 1 – первый сталеразливочный ковш; 2 – защитный экран; 3 – крышка вакуумной камеры; 4 – вакуумпровод к вакуумным насосам; 5 – второй сталеразливочный ковш; 6 – бункер для рас- кислителей и легирующих; 7 – вакуумная камера; 8 – изложница; 9 - гляделка
Технология вакуумной дегазации стали должна учитывать возможное влияние на результаты обработки поверхностно-активных примесей металла (ПАВ). Высокой поверхностной активностью в расплавах железа обладают ки- слород, сера и ряд других примесей. В качестве примера на рисунке 18.21 пока- заны результаты оценки доли адсорбционных мест, которые занимают на меж- фазной поверхности атомы серы, кислорода и селена при различной концен- трации их в расплаве.
Установлено, что присутствие в расплаве ПАВ не оказывает сильного влия- ния на скорость удаления из металла водорода. В этих условиях повышение скоро- сти дегазации может быть достигнуто, в первую очередь, путем увеличения площа- ди поверхности границы раздела металл-газ. По этой причине, когда главной зада- чей обработки является удаление из металла водорода, целесообразно вакуумиро-