
MS / Лекция_18
.pdf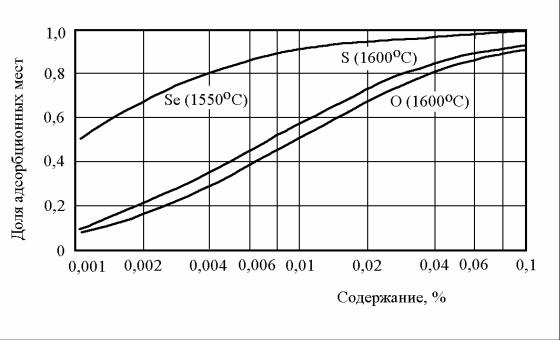
198
Рисунок 18.21 – Зависимость доли адсорбционных мест, занятых ПАВ на поверх- ности раздела фаз, от концентрации примесей в металле
вать слабо раскисленный металл. При этом в результате протекания реакции ваку- умно-углеродного раскисления в стали образуется большое количество пузырей оксида углерода и поверхность раздела фаз резко увеличивается. Примером могут служить показанные на рисунке 18.22 результаты обработки стали различной сте- пени окисленности в камере порционного вакуумирования. Из рисунка видно, что эффективность удаления водорода увеличивается, когда направляемая на вакууми- рование сталь не обрабатывается сильными раскислителями и характеризуется бо- лее высоким содержанием растворенного в металле кислорода.
В промышленных условиях при вакуумировании слабо раскисленного металла удаление водорода протекает достаточно эффективно. Степень дегаза- ции стали при этом обычно составляет 50 – 80%.
При обработке расплавов промышленной чистоты эффективность удаления азота значительно меньше, чем водорода. Степень дегазации стали обычно не превышает 15 – 30%. При этом анализ влияния состава металла на результаты об- работки дает основания предполагать, что уменьшение эффективности дегазации связано с наличием в расплаве ПАВ.
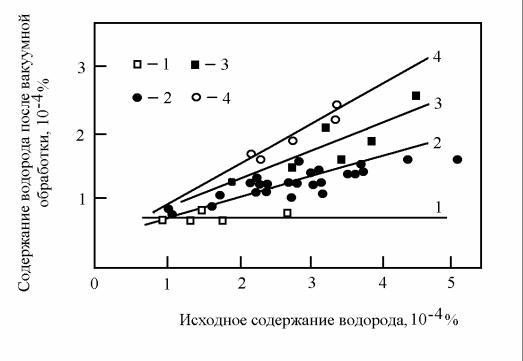
199
Рисунок 18.22 – Зависимость эффективности удаления водорода при порционном вакуумировании от химического состава стали, %:
1 – 0,1 C, 0,2 – Si, 0,5 Mn; 2 – 0,7 C, 0,25 Si, 1,0 Mn; 3 – 0,25 C, 1,3 Si, 0,5 Mn; 4 – 0,7
C, 0,25 Si, 1,0 Mn, 0,01 – 0,02 Al
Подтверждением этому могут служить результаты исследования дегазации стали, выплавленной в 220-т кислородном конвертере. В ходе исследования содер- жание серы в металле перед выпуском плавки составляло в среднем 0,019%. Во время выпуска сталь обрабатывали в ковше кремнием, алюминием и твердой шла- кообразующей смесью. В результате этого содержание серы в стали понижалось до 0,013%. После выпуска ковш транспортировали к вакуумной камере, где проводили вакуумирование с одновременной продувкой расплава аргоном. Во время вакуум- ной обработки имела место дополнительная десульфурация металла ковшевым шлаком. Результаты проведенного исследования показаны на рисунке 18.23 в виде зависимости между концентрациями азота и серы в стали по окончанию обработки.
Из приведенных данных видно, что эффективность дегазации стали сущест- венно увеличивалась, когда остаточное содержание серы в металле было получено менее 0,004%. В одном из опытов исходное содержание азота в стали было повы-
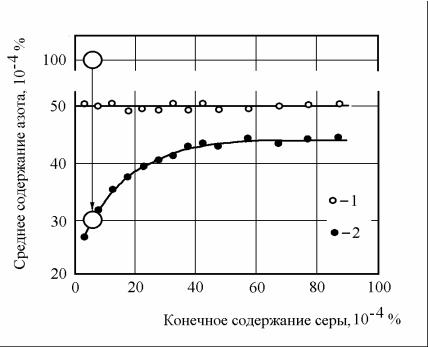
200
Рисунок 18.23 – Влияние остаточного содержания серы в стали на эффектив- ность удаления азота при вакуумировании:
1 – до вакуумирования; 2 – после обработки
шено до 0,01% присадкой азотированных ферросплавов. Однако, в условиях глубо- кой десульфурации металла это не вызвало увеличения концентрации азота в стали после вакуумирования.
Таким образом, если главной задачей вакуумирования является удаление из металла азота, следует стремиться к получению в расплаве минимального содержания ПАВ. С этой целью сталь перед вакуумированием должна быть глубоко раскислена. Желательно также наличие в металле минимально воз- можного количества серы. Для обеспечения большой площади поверхности раздела взаимодействующих фаз вакуумную обработку целесообразно совме- щать с продувкой стали инертным газом.
18.4.2 Обезуглероживание стали при вакуумировании в ковше
Для получения стали с особо низким содержанием углерода используют окислительное рафинирование с одновременным вакуумированием металла в
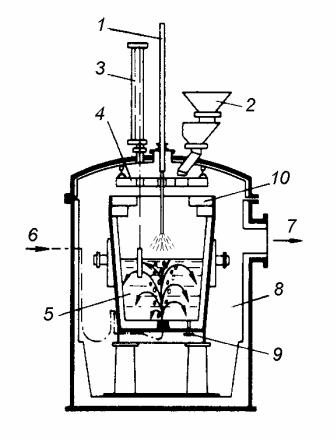
201
ковше (VOD процесс – от английского Vacuum Oxygen Decarburization), схема которого представлена на рисунке 18.24
Рисунок 18.24 – Схема установки для окислительного рафинирования при вакуумной обработке в ковше: 1 – кислородная фурма; 2 – бункер для присадок; 3 – устройство для измерения температуры и отбора проб; 4 – водоохлаждаемый экран; 5 – ковш; 6 – подвод аргона для пе- ремешивания; 7 – вакуумпровод к насосам; 8 – вакуумная камера; 9 – шиберный затвор; 10 – защитный экран
Для осуществления этого процесса в центре крышки вакуумной камеры вакуумплотно устанавливается подвижная кислородная фурма. Обязательным условием эффективного обезуглероживания является принудительное переме- шивание металла, так как при очень низких концентрациях углерода интенсив- ность образования его оксидов не достаточна для выравнивания состава и тем- пературы стали в объеме ковша. Перемешивание осуществляется продувкой металла аргоном через установленную в днище ковша пористую пробку.
В процессе VOD кислород подается в металл сверху при помощи водоох- лаждаемой фурмы. Одним из вариантов этой технологии является процесс ASV (от французского affinage sous vide), в котором для продувки металла кислоро- дом используется неохлаждаемая расходуемая фурма, подаваемая в ковш свер- ху.
Известны также способы окислительного рафинирования с одновремен- ным вакуумированием металла в ковше, в которых окисление примесей прово-
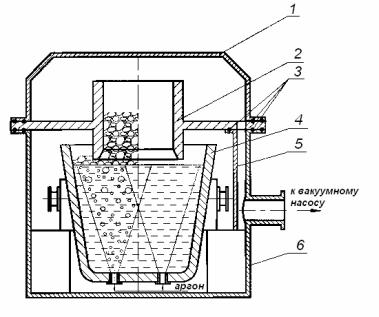
202
дят при помощи подачи в ковш твердых окислителей и последующего переме- шивания металла и шлака продувкой аргоном.
Окислительное рафинирование металла в вакууме позволяет получать сталь с содержанием углерода 0,002 – 0,005%.
Существенным недостатком рассмотренных выше технологий является необходимость в значительном недоливе сталеразливочных ковшей. Например, по данным ОАО «Северсталь» высота свободного борта ковша должна состав- лять 1200 – 1300 мм, что позволяет обрабатывать плавки значительно меньшей массы, чем вмещает стандартный сталеразливочный ковш.
Для решения проблемы высоты свободного борта ковша в ОАО «Север- сталь» разработан процесс VODF (от английского Vacuum Oxygen Decarburization Full), в котором рабочее пространство вакуумной камеры разделено на две зоны с различным разрежением (рисунок 18.25).
Рисунок 18.25 – Схема процесса VODF:
1 – теплоизоляционная крышка; 2 – надставка; 3 – уплотнения; 4 – сталеразли- вочный ковш; 5 – вставка; 6 – вакуумная камера
Для разделения рабочего пространства используется надставка с футеро- ванным патрубком, которая опирается на фланец вакуумной камеры с необхо- димыми зазорами относительно торца и борта ковша. Длина патрубка выбира-
203
ется таким образом, что при вакуумной обработке нижний его торец погружа- ется в шлакометаллическую эмульсию на определенную глубину и тем самым разделяет рабочее пространство вакуумной камеры на две зоны с различной степень разрежения. При этом разрежение в зоне над надставкой будет выше, чем под ней. При подъеме шлакометаллической эмульсии отсутствие перелива металла через борт обеспечивается за счет эффекта гидравлического затвора, при котором подъем и кипение шлакометаллической эмульсии происходит в основном внутри патрубка.
Опробование этой технологии в конвертерном цехе Череповецкого ме- таллургического комбината ОАО «Северсталь» показало, что она позволяет об- рабатывать плавки массой до 375 т вместо обычных 320 – 330 т.
18.5 Корректировка химического состава стали в ковше
При раскислении и легировании стали основное количество ферроспла- вов обычно вводят под струю металла в сталеразливочном ковше по ходу вы- пуска плавки.
После наполнения ковша, отбора пробы и получения результатов анализа проводят корректировку химического состава стали на установках доводки ме- талла (УДМ), в камерах порционного и циркуляционного вакуумирования и др.
Вкачестве примера на рисунке 18.26 показана схема УДМ в 350-т ковшах кислородно-конвертерного цеха ОАО «Металлургический комбинат «Азов- сталь».
Ниже приведены результаты исследования усвоения корректирующих и микролегирующих присадок при выплавке углеродистых и низколегированных марок стали с доводкой металла в 350-т ковшах с кислой, основной и высоко- глиноземистой футеровкой.
Входе исследования силикокальций и углеродсодержащие материалы вдували в металл в порошкообразном состоянии через погружаемую в расплав фурму в потоке аргона. Алюминий в виде стандартный чушек вводили вручную
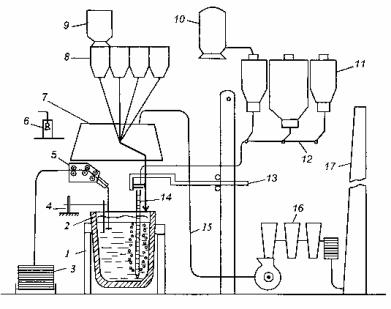
204
Рисунок 18.26 – Схема УДМ в 350-т ковшах комбината «Азовсталь»:
1 – стенд; 2 – ковш; 3 – бухта алюминиевой катанки или порошковой проволо- ки; 4 – манипулятор для отбора проб металла; 5 – трайб-аппарат; 6 - пневмо- почта; 7 – вытяжной зонт; 8 – система бункеров-дозаторов; 9 – бадья для куско- вых материалов; 10 – контейнер для порошков; 11 – пневматический питатель; 12 – трубопровод с переключателями потоков; 13 – подъемник фурмы; 14 – фурма; 15 – отвод отходящих газов; 16 – газоочистка; 17 – дымовая труба
на шлак, а в виде катанки – под уровень металла с помощью трайб-аппарата. Остальные ферросплавы и лигатуры вводили в ковш в кусковом виде через шлак самотеком из бункеров-дозаторов. В процессе ввода, плавления и раство- рения присадок металл продували аргоном с расходом 60 – 70 нм3/ч.
Обобщенные данные о средних значениях степени усвоения элементов при доводке по химическому составу и микролегировании спокойной стали в ковше представлены в таблице 18.1.
Из таблица 18.1 видно, что степень усвоения элементов при внепечной обработке стали в наполненном ковше на 5 – 40 % (абс.) выше, чем в процессе выпуска металла из агрегата. При этом существенного изменения усвоения корректирующих и микролегирующих добавок в зависимости от их массы не выявлено.
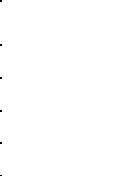
205
Таблица 18.1 – Данные об усвоении элементов из корректирующих и микроле- гирующих добавок при доводке спокойной стали в ковше
Элемент |
Материал и вид добавки |
Усвоение, |
|
% |
|||
|
|
||
Марганец |
Ферромарганец, металлический марганец, |
96 |
|
|
силикомарганец |
|
|
Алюминий |
Вторичный алюминий (чушки) |
45 |
|
Первичный алюминий (катанка) |
70 |
||
|
|||
|
|
|
|
Кремний |
Ферросилиций (45 – 65% Si), силикомарганец |
90 |
|
|
|
|
|
Титан |
Ферротитан (30 – 42% Ti) |
80 |
|
|
|
|
|
Ванадий |
Феррованадий (35 – 50% V) |
90 |
|
|
|
|
|
Ниобий |
Феррониобий (55 – 65% Nb) |
97 |
|
|
|
|
|
Бор |
Ферробор (7 – 10% B) |
55 |
|
|
|
|
|
Кальций |
Силикокальций (25 – 32% Ca) |
15 |
|
|
|
|
|
РЗМ |
Лигатура РЗМ (20 – 25% РЗМ) |
10 |
|
|
|
|
|
Углерод |
Коксик, графит |
95 |
|
|
|
|
Усвоение марганца, алюминия, ванадия, ниобия, титана, бора и углерода из твердых добавок при аргонной продувке мало зависит от вида футеровки сталеразливочных ковшей и состава ковшевого шлака. Незначительное (на 2 – 5 % абс.) повышение усвоения алюминий наблюдается при использовании ков- шей с основной футеровкой. Усвоение кальция и РЗМ в значительной мере оп- ределяется окисленностью стали, видом футеровки ковша и окисленностью шлака. Максимальная степень усвоения кальция наблюдалась при вдувании по- рошкообразного силикокальция в струе аргона в ковш с основной футеровкой под синтетическим шлаком при содержании алюминия в металле не менее
0,03%.
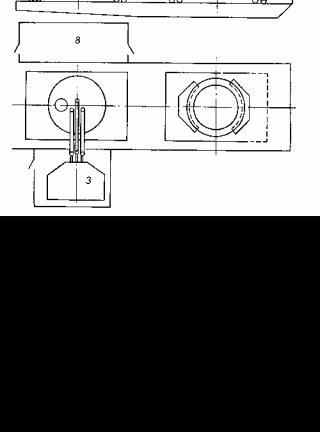
206
18.6 Внепечная обработка стали с нагревом в ковше
В последние годы в сталеплавильных цехах отечественных металлурги- ческих заводов получила широкое распространение технология обработки ста- ли на установках ковш-печь (рисунок 18.27), которые позволяют выполнять различные виды внепечного рафинирования стали одновременно с электроду- говым нагревом металла в ковше.
Рисунок 18.27 – Схема установки ковш-печь:
1 – металловозная тележка; 2 – стале- разливочный ковш; 3 – трансформа- тор стенда электродугового нагрева; 4 – крышка стенда электродугового нагрева; 5 – бункер для подачи фер- росплавов и лигатур; 6 – дозирующие весы; 7 – бункера ферросплавов и ли- гатур; 8 – пульт управления
Для обработки на установке ковш-печь металл подают в ковшах, обору- дованных шиберными затворами и пористыми пробками для продувки расплава аргоном, которая необходима для выравнивания температуры и химического состава металла в объеме ковша. На металловозной тележке ковш транспорти- руют к стенду электродугового нагрева, где накрывают крышкой. Крышку ковша современных установок ковш-печь обычно выполняют водоохлаждае- мой. В крышке имеются отверстия, через которые в ковш опускают графитовые электроды. В зависимости от мощности трансформатора скорость нагрева ме- талла при обработке на установке ковш-печь изменяется в пределах 2 – 5
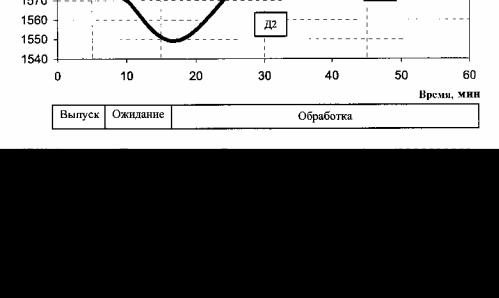
207
оС/мин. Помимо оборудования, показанного на рисунке 18.27, современные ус- тановки ковш-печь имеют также манипуляторы для измерения температуры металла, отбора проб металла и шлака, а также оборудование для обработки стали порошками путем вдувания через погружаемые в металл фурмы или вво- да порошковой проволоки.
В качестве примера рассмотрим технологию получения с использованием установки ковш-печь 155 т стали 20Г состава, % мас.: 0,20 C, 0,25 Si, 1,4 Mn, 0,005 S, 0,015 P, 0,040 Al. Сведения об изменении температуры металла во вре- мя выпуска и внепечной обработки показаны на рисунке 18.28.
Рисунок 18.28 – Изменение температуры стали при выпуске и обработке на установке ковш-печь
На выпуске из сталеплавильного агрегата при температуре 1630оС хими- ческий состав металла был следующим, % мас.: 0,04 C, 0,02 Si, 0,15 Mn, 0,015 S, 0,015 P, 0,00 Al (проба П0 на рисунке 18.28).
По ходу выпуска в ковш присаживали 368 кг ферросилиция, 561 кг фер- ромарганца, 124 кг алюминия, 148 кг углеродсодержащих материалов и 1000 кг смеси извести с флюоритовым концентратом (добавка Д1 на рисунке 18.28). К моменту окончания выпуска температура металла понизилась до 1575оС. За время транспортирования ковша к установке ковш-печь температура металла