
SPR / Лекция_2
.pdf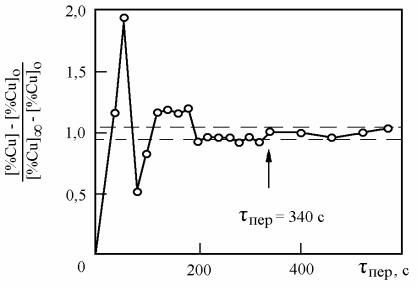
22
2 ТЕОРЕТИЧЕСКИЕ ОСНОВЫ ПРОЦЕССОВ ВНЕПЕЧНОГО РАФИНИРОВАНИЯ СТАЛИ
2.1 Процессы при продувке металла инертным газом
Продувка металла инертным газом используется для усреднения химиче-
ского состава и температуры металла в ковше, дегазации металла, перемешива-
ния металла и шлака для повышения скорости химических реакций, удаления неметаллических включений из расплава и др.
2.1.1 Усреднение состава и температуры металла в ковше
Определение времени полного перемешивания стали при продувке обыч-
но проводится согласно следующей методике. После подачи в расплав извест-
ного количества индикатора в фиксированной точке внутри ковша периодиче-
ски отбирают пробы металла для химического анализа. При этом характер из-
менения концентрации индикатора в пробах аналогичен показанному на рисун-
ке 2.1.
Рисунок 2.1 – Изменение концентрации индикатора в пробах металла во время продувки
23
Первоначально содержание индикатора в отобранных пробах изменяется в широких пределах. Спустя некоторое время концентрация индикатора в объ-
еме ковша выравнивается и в дальнейшем содержание его в пробах металла от-
личается от расчетного значения не более, чем на 5%. Это время и принято счи-
тать временем полного перемешивания.
Экспериментально установлено, что время полного перемешивания свя-
зано с величиной скорости диссипации энергии в расплаве соотношением
τ= ( 600 ±100 )ε− 0,4 ,
где ε – скорость диссипации энергии, Вт/т.
При вдувании газа в металл работа, совершаемая газом,
уравнения
(2.1)
определяется из
|
|
|
P |
|
|
|
P |
|
|
T |
|
|
|
|
T |
|
|
|
2 |
|
|
|
|
|
|
1 |
T |
+ 1 |
|
|
|
|
|
|
|
|
|
||||||||
ε = |
nRT |
ln |
+ η |
n |
ln |
n |
− |
|
n |
+ |
|
n |
|
|
0,5ρ |
U |
, |
(2.2) |
||||
P |
|
P |
T |
|
|
P T |
|
|||||||||||||||
|
|
L |
|
T |
|
|
|
|
|
|
|
L |
|
|
n n |
|
||||||
|
|
|
o |
L |
1 |
|
|
|
L |
|
|
|
n |
|
|
|
|
|
||||
где n – молекулярная скорость истечения газа; T |
L |
– температура металла; |
P – |
|||||||||||||||||||
|
|
|
|
|
|
|
|
|
|
|
|
|
|
|
|
|
|
|
|
1 |
статическое давление на уровне выходного отверстия фурмы; Po – давление над поверхностью расплава; Pn , Tn , ρn и U n – соответственно давление, темпера-
тура, плотность и скорость газа на выходе из фурмы; η – коэффициент, величи-
ной которого учитывается доля различных составляющих перемешивания, эф-
фективно используемая для усреднения состава металла.
По сути первое слагаемое в правой части уравнения (2.2) представляет собой работу изотермического расширения пузырей газа при подъеме в метал-
ле. Четвертое слагаемое – работа, совершаемая при передаче кинетической энергии газа жидкости. Второе и третье слагаемые – работа расширения газа,
которое обусловлено изменением его температуры и давления вблизи выходно-
го отверстия фурмы.
Результаты экспериментов на холодных моделях свидетельствуют о том,
что численное значение коэффициента η обычно составляет 0,05 – 0,1. Поэто-
му в оценочных расчетах тремя последними слагаемыми в правой части урав-
24
нения (2.2) с достаточной для практических целей точностью можно пренеб-
речь и приравнять работу перемешивания металла газом к работе изотермиче-
ского расширения всплывающих в расплаве пузырей.
В практических расчетах удобно пользоваться величинами, которые имеют следующую размерность: скорость диссипации энергии ( ε ), Вт; объем-
ная скорость подачи газа в металл (VG ), нм3/мин; температура стали (TL ), К;
плотность металла ( ρL ), кг/м3; ускорение силы тяжести ( g ), м/с2; глубина вво-
да газа в металл ( H o ), м; давление над поверхностью расплава ( Po ), атм. Тогда
уравнение (2.2) может быть преобразовано к виду
|
|
|
|
|
|
|
ρ |
L |
gH |
o |
|
|
|
|
ε = |
|
|
|
|
+ |
|
|
|
|
. |
(2.3) |
|||
6,18V |
T |
L |
ln 1 |
|
|
|
|
|
|
|||||
103000P |
||||||||||||||
|
G |
|
|
|
|
|
||||||||
|
|
|
|
|
|
|
|
|
|
o |
|
|
Расчеты, проведенные согласно описанной выше методике, свидетельст-
вуют о том, что в стандартных сталеразливочных ковшах с отношением высоты к диаметру равным 1,0 – 1,5 для усреднения химического состава и температу-
ры стали необходим расход аргона не более 0,05 – 0,1 м3/т.
Из уравнений (2.1) и (2.3) следует, что при одинаковой интенсивности про-
дувки время полного перемешивания металла уменьшается при увеличении глу-
бины подачи газа в расплав. Поэтому более эффективной является продувка стали в ковшах с большим отношением высоты к диаметру. Скорость диссипации энер-
гии увеличивается при понижении давления над поверхностью металла. Поэтому при равных расходах газа время, необходимое для усреднения химического соста-
ва и температуры металла, существенно уменьшается при продувке в вакууме.
2.1.2 Дегазация стали при продувке инертным газом
При продувке стали инертным газом парциальное давление азота и водо-
рода в пузырьках газа в момент образования их в металле близко к нулю. Поэто-
му в процессе удаления пузырей из расплава растворенные в стали газы диф-
фундируют в объем пузырей и выносятся ими в атмосферу.
25
Для приблизительной оценки расхода нейтрального газа на дегазацию ста-
ли может быть использована формула Геллера. При выводе этой зависимости сделано допущение, согласно которому за время пребывания пузырей в металле между расплавом и газовой фазой достигается состояние термодинамического равновесия. Поэтому формула Геллера позволяет теоретически оценить мини-
мально необходимый расход нейтрального газа для дегазации стали. Если в ре-
альных процессах за время пребывания пузырей в металле состояние равновесия не достигается, необходимое для дегазации стали количество нейтрального газа изменяется только в сторону увеличения.
Ниже приведена формула Геллера для случая, когда продувка ведется с целью удаления из металла водорода
|
|
|
224 |
|
2 |
1 |
|
1 |
|
|
|
|
|
|
|
|
||
V |
|
= |
PK |
− |
|
+ [H] − [H] |
|
|
, |
(2.4) |
||||||||
Ar |
M |
|
|
[H] |
[H] |
|
|
|||||||||||
|
|
H |
|
|
H |
|
|
|
|
|
o |
|
|
|||||
|
|
|
|
2 |
|
|
|
|
|
o |
|
|
|
|
|
|
||
|
|
|
|
|
|
|
|
|
|
|
|
|
|
|
|
|
|
|
где V Ar – объем продуваемого через металл аргона, м3/т; |
M H |
2 |
– относитель- |
|||||||||||||||
|
|
|
|
|
|
|
|
|
|
|
|
|
|
|
|
|
|
|
ная молекулярная масса удаляемого газа; |
P – давление над поверхностью ме- |
талла × 10–5, Па; K H – константа равновесия реакции растворения газа в ме-
талле; [H]o и [H] – исходная и конечная концентрации водорода в стали, %.
Результаты проведенного согласно уравнению (2.4) расчета необходимого для дегазации металла расхода аргона показаны на рисунке 2.2. Анализ приве-
денных на рисунке данных показывает, что для получения в стали остаточного содержания водорода менее 2 см3/100 г необходим расход аргона 1,5 – 2 м3/т.
На практике при продувке стали инертным газом с целью усреднения химиче-
ского состава и температуры, а также интенсификации перемешивания металла с ковшевым шлаком удельный расход аргона составляет 0,05 – 0,2 м3/т. Поэто-
му продувка стали аргоном в открытых ковшах обычно не сопровождается су-
щественной дегазацией металла.
Анализ уравнения (2.4) свидетельствует также, что необходимый для де-
газации стали расход аргона быстро уменьшается при понижении давления над
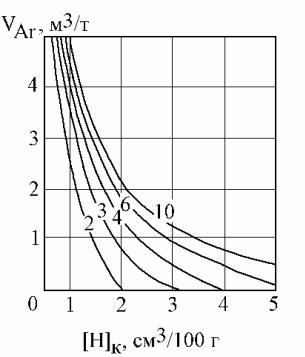
26
Рисунок 2.2 – Зависимость расхода аргона от начального и конечного содержа-
ния водорода в стали. Цифры у кривых – исходное содержание водорода,
см3/100 г металла
поверхностью расплава. В связи с этим продувка стали инертным газом в ва-
кууме может быть весьма эффективным способом ее дегазации.
2.2 Десульфурация металла ковшевым шлаком
Эффективность десульфурации металла шлаком принято характеризовать величинами равновесного и фактического коэффициента распределения серы между шлаком и металлом ( Ls = (S)[S] ).
Константа равновесия реакции
[S] + Fe + (CaO) = (CaS) + (FeO) . |
(2.5) |
определяется из выражения
K = |
a(CaS) ×a(FeO) |
. |
(2.6) |
|
|||
|
a[S] ×a(CaO) |
|
С учетом соотношения
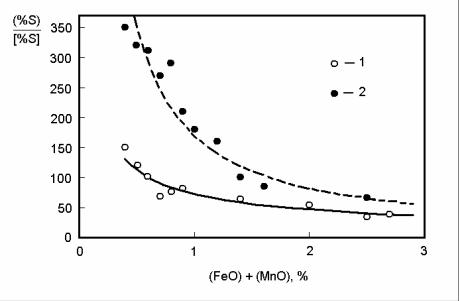
|
|
|
|
|
|
|
|
|
|
|
|
|
|
|
27 |
a |
|
= |
|
MCaS |
× |
f |
|
|
×(S) |
(2.7) |
|||||
|
|
|
|
|
|
|
|||||||||
|
(CaS) |
|
|
|
M S |
|
(CaS) |
|
|
|
|||||
|
|
|
|
|
|
|
|
|
|
|
|
|
|||
из уравнения (2.6) получим |
|
|
|
|
|
|
|
|
|
|
|
|
|
|
|
|
(S) |
= |
|
M S |
K |
|
|
f S |
× |
a(CaO) |
. |
(2.8) |
|||
|
[S] |
|
|
f |
|
|
|||||||||
|
|
|
M |
CaS |
CaS |
|
a |
|
|||||||
|
|
|
|
|
|
|
|
(FeO) |
|
Из уравнения (2.8) следует, что высокие значения коэффициента распределения серы между шлаком и металлом могут быть получены при высокой основности шлака и низком содержании оксида железа, а также обладающего сходными химическими свойствами оксида марганца.
На рисунке 2.3 приведены данные о влиянии расхода аргона, а также со-
держания оксидов железа и марганца в шлаке на величину коэффициента рас-
пределения серы при обработке стали на УКП в 50-т ковше.
Рисунок 2.3 – Зависимость коэффициента распределения серы между шлаком и металлом от окисленности шлака и интенсивности продувки: 1 – расход аргона
0,5 нм3/мин; 2 – 1,8 нм3/мин
Из рисунка видно, что при наличии в шлаке FeO и MnO величина коэф-
фициента распределения серы между шлаком и металлом быстро уменьшается.
Поэтому для внепечной десульфурации металла рекомендуют использовать
28
шлаки, в которых содержание CaO приближается к растворимости его в шлаке при температуре обработки, а суммарное содержание FeO и MnO не превышает
1,0 – 1,5%.
Зависимость фактических значений коэффициента распределения серы от интенсивности продувки свидетельствует о том, что реакция десульфурации не достигает термодинамического равновесия и результаты обработки определя-
ются кинетическими факторами.
При десульфурации металла шлаком реакция протекает в диффузионной области. При этом ход процесса описывается кинетическим уравнением реак-
ции первого порядка относительно концентрации серы в металле
[S] = [S] e−kt |
, |
(2.5) |
o |
|
|
где [S]o и [S] – исходное и конечное содержание серы в стали, %; k |
– кон- |
|
станта скорости реакции, мин–1; t – время, мин. |
|
|
Экспериментально установлено, что при продувке стали в ковше аргоном
зависимость константы скорости реакции в уравнении (2.5) от мощности пере-
мешивания описывается уравнением
k = k |
o |
ε( 0,6 − 0,8 ) . |
(2.6) |
|
|
|
При высокой интенсивности продувки дальнейшее увеличение расхода газа не сопровождается соответствующим ростом константы скорости реакции. Име-
ются данные о том, что при десульфурации металла шлаком константа скоро-
сти реакции быстро увеличивается при повышении скорости диссипации энер-
гии до 200 – 300 Вт/т. Дальнейшее увеличение интенсивности продувки не це-
лесообразно.
2.3 Процессы при вакуумной обработке стали
2.3.1 Термодинамическая оценка глубины дегазации металла
Растворимость кислорода, азота и водорода в металле подчиняется закону
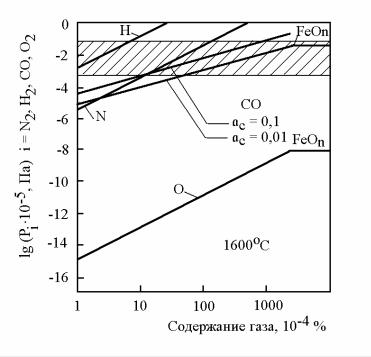
29
Сивертса. Отсюда следует, что содержание газов в стали можно уменьшить пу-
тем понижения их парциального давления в контактирующей с металлом газо-
вой фазе при обработке стали в вакууме.
Определение возможной глубины дегазации металла при вакуумировании проводят, сравнивая расчетные значения равновесного парциального давления газа над расплавом с величиной остаточного давления в вакуумной камере. В
случаях, когда расчетная величина равновесного парциального давления газа над металлом превышает давление в вакуумной камере, дегазация металла счи-
тается возможной.
Результаты расчета равновесных парциальных давлений кислорода, азота и водорода в газовой фазе при различном содержании газов в железе показаны на рисунке 2.4. Штриховкой на рисунке отмечена область остаточных давле-
ний, которые могут быть получены в промышленных вакуумных камерах.
Рисунок 2.4 – Результаты термодинамической оценки остаточного содержания газов в железе при вакуумировании
Из рисунка видно, что при вакуумировании расплавов железа в промыш-
ленных условиях возможно глубокое рафинирование металла от водорода, ос-
таточное содержание которого может быть получено равным 0,0001% и менее.
30
Условия удаления азота менее благоприятны и не позволяют понизить концентрацию его в металле менее 0,001%.
Удаление кислорода из расплава в газовую фазу в молекулярной форме не возможно, так как при любой его концентрации равновесное парциальное давление газа над расплавом на несколько порядков меньше остаточного дав-
ления в вакуумных камерах.
При вакуумной обработке стали равновесие реакции
[C] + [O] = {CO} |
(2.7) |
смещается в направлении образования дополнительного количества оксида уг-
лерода. Если реакция (2.7) протекает без поступления в металл дополнительно-
го количества кислорода, содержание растворенного в металле кислорода уменьшается в результате вакуумно-углеродного раскисления. Если одновре-
менно с протеканием реакции (2.7) в металл поступает дополнительное количе-
ство кислорода, возникают условия для глубокого обезуглероживания металла.
2.3.2Особенности кинетики реакций дегазации и обезуглероживания стали
Технология вакуумной дегазации стали должна учитывать возможное влияние на результаты обработки поверхностно-активных примесей металла
(ПАВ). Высокой поверхностной активностью в расплавах железа обладают ки-
слород, сера и ряд других примесей. В качестве примера на рисунке 2.5 показа-
ны результаты оценки доли адсорбционных мест, которую занимают на меж-
фазной поверхности атомы серы, кислорода и селена при различной концен-
трации их в расплаве.
Установлено, что присутствие в расплаве ПАВ не оказывает сильного влия-
ния на скорость удаления из металла водорода. В этих условиях повышение скоро-
сти дегазации может быть достигнуто, в первую очередь, путем увеличения площа-
ди поверхности раздела металл-газ. По этой причине, когда главной задачей обра-
ботки является удаление из металла водорода, целесообразно вакуумировать слабо
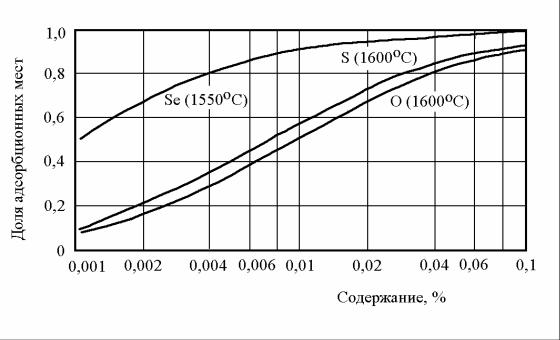
31
Рисунок 2.5 – Зависимость доли адсорбционных мест, занятых ПАВ на поверхно-
сти раздела фаз, от концентрации примесей в металле
раскисленный металл. При этом в результате протекания реакции вакуумно-
углеродного раскисления в стали образуется большое количество пузырей оксида углерода и площадь поверхности раздела фаз резко увеличивается. Примером мо-
гут служить показанные на рисунке 2.6 результаты обработки стали различной сте-
пени окисленности в камере порционного вакуумирования. Из рисунка видно, что эффективность удаления водорода увеличивается, когда направляемая на вакууми-
рование сталь не обрабатывается сильными раскислителями и характеризуется бо-
лее высоким содержанием растворенного в металле кислорода.
В промышленных условиях при вакуумировании слабо раскисленного металла удаление водорода протекает достаточно эффективно. Степень дегаза-
ции стали при этом обычно составляет 50 – 80%. Если по каким-либо причинам металл перед вакуумированием должен подвергаться глубокому раскислению,
большую площадь поверхности раздела фаз можно получить путем продувки металла аргоном.
При обработке расплавов промышленной чистоты эффективность удаления азота значительно меньше, чем водорода. Степень дегазации стали обычно не