
SPR / Лекция_2
.pdf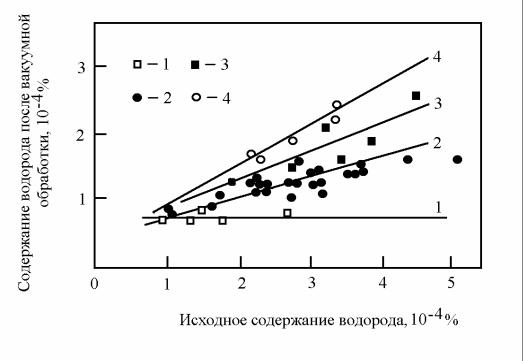
32
Рисунок 2.6 – Зависимость эффективности удаления водорода при порционном
вакуумировании от химического состава стали, %:
1 – 0,1 C, 0,2 – Si, 0,5 Mn; 2 – 0,7 C, 0,25 Si, 1,0 Mn; 3 – 0,25 C, 1,3 Si, 0,5 Mn; 4 – 0,7
C, 0,25 Si, 1,0 Mn, 0,01 – 0,02 Al
превышает 15 – 30%. При этом анализ влияния состава металла на результаты обработки дает основания предполагать, что уменьшение эффективности дега-
зации связано с наличием в расплаве ПАВ.
Подтверждением этому могут служить результаты исследования дегазации стали,
выплавленной в 220-т кислородном конвертере. В ходе исследования содержание серы в металле перед выпуском плавки составляло в среднем 0,019%. Во время вы-
пуска сталь обрабатывали в ковше кремнием, алюминием и твердой шлакообра-
зующей смесью. В результате этого содержание серы в стали понижалось до
0,013%. После выпуска ковш транспортировали к вакуумной камере, где проводили вакуумирование с одновременной продувкой расплава аргоном. Во время вакуум-
ной обработки имела место дополнительная десульфурация металла ковшевым шлаком. Результаты проведенного исследования показаны на рисунке 2.7 в виде за-
висимости между концентрациями азота и серы в стали по окончанию обработки.
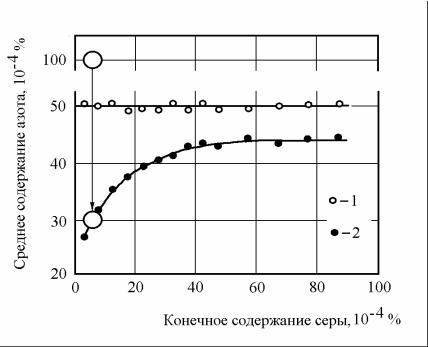
33
Рисунок 2.7 – Влияние остаточного содержания серы в стали на эффективность удаления азота при вакуумировании:
1 – до вакуумирования; 2 – после обработки
Из приведенных данных видно, что эффективность дегазации стали сущест-
венно увеличивалась, когда остаточное содержание серы в металле было получено менее 0,004%. В одном из опытов исходное содержание азота в стали было повы-
шено до 0,01% присадкой азотированных ферросплавов. Однако, в условиях глубо-
кой десульфурации металла это не вызвало увеличения концентрации азота в стали после вакуумирования.
Таким образом, если главной задачей вакуумирования является удаление из металла азота, следует стремиться к получению в расплаве минимального содержания ПАВ. С этой целью сталь перед вакуумированием должна быть глубоко раскислена. Желательно также наличие в металле минимально воз-
можного количества серы. Для обеспечения большой площади поверхности раздела взаимодействующих фаз вакуумную обработку целесообразно совме-
щать с продувкой стали инертным газом.
Процессы вакуумно-углеродного раскисления и обезуглероживания стали
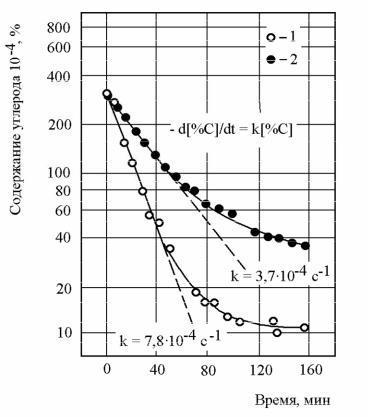
34
в вакууме с достаточной точностью описываются кинетическими уравнениями реакции первого порядка относительно концентрации удаляемой примеси, что является следствием протекания реакций в диффузионной области. В качестве примера на рисунке 2.8 приведены результаты исследования изменения кон-
центрации углерода в стали при обезуглероживании в вакууме.
Рисунок 2.8 – Изменение концентрации углерода в стали при обезуглерожива-
нии в вакууме: 1 – опыт №1; 2 – опыт №2
Из приведенных данных видно, что спустя некоторое время после начала вакуумирования скорость реакции замедляется. Это объясняется тем, что ско-
рость протекающей в диффузионной области реакции обезуглероживания стали определяется величиной площади поверхности раздела взаимодействующих фаз. В начальном периоде обработки пузыри оксида углерода зарождаются на границе металл-футеровка и, удаляясь из расплава, проходят через слой обра-
батываемого металла. Благодаря наличию в расплаве большого количества пу-
зырей и большой площади поверхности раздела взаимодействующих фаз ско-
рость реакции при этом достаточно высока. В заключительном периоде вакуу-

35
мирования условия для кипения металла на границе с футеровкой исчезают.
После этого реакция продолжается только на поверхности металла в вакуумной камере, что приводит к значительному уменьшению скорости обезуглерожива-
ния.
Чтобы увеличить скорость и глубину вакуумно-углеродного раскисления и обезуглероживания стали вакуумирование целесообразно совмещать с продувкой расплава инертным газом.
2.3.3Основные кинетические закономерности циркуляционного вакуумирования стали
Если лимитирующим звеном реакции является массоотдача примеси из объ-
ема расплава к поверхности раздела металл-газ, процесс циркуляционного вакуу-
мирования стали описывается следующим кинетическим уравнением
|
Ct |
− C |
|
p |
|
|
|
|
e− αt , |
|
||||||
1 |
|
|
|
|
= |
|
|
|
||||||||
|
C 0 |
− C |
p |
|
|
|
|
|||||||||
|
|
|
|
|
|
|
|
|
|
|
||||||
1 |
|
|
|
|
|
|
|
|
|
|
|
|
|
|||
|
|
|
|
|
|
|
|
|
|
|
|
|
|
−1 |
|
|
|
|
|
V |
|
|
V |
|
|
1 |
|
|
|||||
α = |
|
|
−1 |
1 |
+ |
|
, |
|||||||||
|
|
|
|
|
||||||||||||
|
|
V |
|
|
|
|
V |
|
|
k |
|
|||||
|
|
|
1 |
|
|
|
|
|
|
|
|
|
|
|
(2.8)
(2.9)
|
|
k = |
|
βF |
, |
(2.10) |
|
|
|
|
|||
|
|
|
|
V1 |
|
|
где C 0 |
– концентрация примеси в порции металла, поступающего в вакуумную |
|||||
1 |
|
|
|
|
|
|
камеру в момент времени |
t = 0, %; C t |
– концентрация примеси в порции ме- |
||||
|
|
1 |
|
|
|
|
талла, поступающего в вакуумную камеру в момент времени t , %; C p – равно-
весное с газовой фазой содержание примеси в металле у межфазной поверхно-
сти, %; t – продолжительность вакуумирования, с; V – объем металла в ковше,
м3; V1 – объем металла в вакуумной камере, м3; V – объем металла, протекаю-
щий через вакуумную камеру в единицу времени, м3; β – коэффициент массо-

36
отдачи примеси в металле, м/с; F – площадь поверхности раздела металл-газ внутри вакуумной камеры, м2.
Для оценки результатов вакуумирования слабо раскисленной стали в про-
мышленных условиях рекомендуется пользоваться значением k = 0,1 с–1. Ре-
зультаты вычислений по формулам (2.8) и (2.9) с использованием указанного значения коэффициента k представлены на рисунке 2.9. В ходе расчетов про-
должительность пребывания порции металла в вакуумной камере принимали равной 5, 10, 20 и 40 с, а отношение V1V равным 0,2 и 0,1.
Рисунок 2.9 – Результаты расчета кинетики дегазации металла в камере цирку-
ляционного вакуумирования. Сплошная линия – V1/V = 0,2; пунктирная – V1/V = 0,1; цифры у прямых – время пребывания металла в вакуумной камере, с
Из приведенных на рисунке данных видно, что при обработке стали на уста-
новках циркуляционного вакуумирования повышение эффективности рафинирова-
ния может быть достигнуто в результате увеличения продолжительности обработ-
ки, объема металла внутри вакуумной камеры и скорости циркуляции расплава.
37
Росту эффективности рафинирования способствует также увеличение площади поверхности раздела металл-газ в вакуумной камере. Оно может дос-
тигнуто увеличением количества газа, подаваемого в подводящий патрубок ус-
тановки, а также вдуванием дополнительного количества газа в металл, нахо-
дящийся внутри вакуумной камеры.
2.3.4Основные кинетические закономерности вакуумирования стали в ковше
При отсутствии продувки аргоном эффективность вакуумирования ме-
талла в крупных ковшах обычно ниже, чем при вакуумировании стали в ковшах малого тоннажа. Это объясняется отсутствием эффективного перемешивания обрабатываемого металла в связи с тем, что кипение стали в результате проте-
кания реакции вакуумно-углеродного раскисления развивается только в верх-
них горизонтах ковша. Поэтому при вакуумировании крупных ковшей металла вакуумную обработку целесообразно совмещать с продувкой стали инертным газом.
При вакуумировании стали в ковше с одновременной продувкой аргоном через днище ковша динамика дегазации с достаточной точностью описывается кинетическим уравнением реакции первого порядка относительно концентра-
ции удаляемой примеси, решение которого имеет вид
C = C |
o |
e− kt . |
(2.11) |
|
|
|
Результаты экспериментальных исследований свидетельствуют о том, что численное значение константы скорости реакции в уравнении (2.11) определя-
ется величиной скорости диссипации энергии при перемешивании расплава.
Эту зависимость обычно приводят в виде
|
k = aεn , |
(2.12) |
где ε |
– скорость диссипации энергии при перемешивании расплава, Вт/т; a и |
|
n – |
коэффициенты. Численное значение коэффициента n |
согласно данным |
38
различных исследований составляет 0,4 – 0,6. При этом заметное увеличение константы скорости реакции наблюдается при повышении мощности переме-
шивания металла до 200 – 300 Вт/т. Дальнейшее увеличение мощности пере-
мешивания расплава не целесообразно.
2.4 Процессы при обработке стали кальцием
В настоящее время металлический кальций, а также его сплавы и химиче-
ские соединения широко используются для десульфурации и модифицирования неметаллических включений в раскисленной алюминием стали перед разлив-
кой на МНЛЗ.
2.4.1 Основные физико-химические свойства кальция
Основные требования к организации обработки стали кальцием обуслов-
лены физико-химическими свойствами этого реагента. Важнейшие физические свойства кальция и железа представлены для сравнения в таблице 2.1.
Таблица 2.1 – Физические свойства кальция и железа
Наименование свойств |
Ca |
Fe |
|
|
|
Относительная атомная масса |
40,08 |
55,84 |
Атомный радиус, нм |
0,197 |
0,126 |
Радиус иона, нм |
0,106 |
0,060 |
Плотность, кг/м3 |
1550 |
7867 |
Температура плавления, оС |
851 |
1539 |
Температура кипения, оС |
1487 |
2872 |
Теплота плавления, Дж/моль |
9336 |
13820 |
Теплота парообразования, Дж/моль |
153153 |
350016 |
|
|
|
Анализ приведенных в таблице данных показывает, что плотность каль-
39
ция значительно меньше плотности жидкого железа и шлака. Поэтому для эф-
фективной обработки стали этим реагентом требуется принудительный ввод его под уровень обрабатываемого металла.
Температуры плавления и кипения кальция намного ниже температур внепечной обработки стали. Поэтому, попадая в металл, кальций плавится и испаряется за счет тепла обрабатываемого расплава.
Зависимость давления насыщенного пара кальция от температуры описы-
вается уравнением
|
lg P |
= 9,55 − |
8026 |
, |
(2.13) |
|
T |
||||
|
Ca |
|
|
|
|
где |
P – давление насыщенного пара кальция, Па. Расчеты по уравнению |
||||
|
Ca |
|
|
|
|
(2.13) показывают, что при температурах внепечной обработки стали давление насыщенного пара кальция составляет 0,184 – 0,237 МПа. В этих условиях ис-
парение введенного в металл кальция начинается на глубине 1,17 – 1,93 м от поверхности расплава.
Известно, что высокой взаимной растворимостью обладают элементы,
имеющие сходные атомные характеристики. Если атомные радиусы элементов различаются на 30% и более, их взаимная растворимость крайне ограничена.
Ввиду значительного различия атомных радиусов кальция и железа раствори-
мость его в железе и стали очень мала.
Экспериментально установлено, что растворимость кальция в сплавах желе-
за подчиняется закону Генри
[%Ca] = kP , |
(2.14) |
Ca |
|
где P – давление пара кальция над расплавом ×10–5, Па.
Ca
В равновесии с жидким кальцием растворимость кальция в железе при
1600°С обнаружена равной 0,032%. При этой температуре давление насыщен-
ного пара кальция равно 0,182 МПа. Следовательно, при давлении пара кальция над расплавом 0,1 МПа растворимость его в железе составит 0,018%.
Растворимость кальция в сплавах железа увеличивается в присутствии
40
углерода, никеля, кремния и ряда других элементов. Для количественной оцен-
ки растворимости кальция в расплавах сложного состава рекомендуется зави-
симость
lg [%Ca] = lg 0,016 + 0,44[%Ni] + 0,34[%C] + 0,097[%Si] − 0,02[%Cr] . (2.15)
Расчеты по уравнению (2.15) показывают, что растворимость кальция в боль-
шинстве марок стали также не превышает 0,1%.
Крайне ограниченная растворимость кальция в железе и стали приводит к тому, что основное количество введенного в металл реагента удаляется из рас-
плава в виде пузырей пара, у поверхности которых протекают химические ре-
акции с примесями расплава. Поэтому для эффективной обработки кальций следует вводить в металл на максимально возможную в данных условиях глу-
бину.
2.4.2Процессы при растворении в стали сплавов и соединений кальция
В связи с высокой химической активностью металлического кальция по отношению к атмосферным газам и влаге для ввода кальция в металл часто ис-
пользуются его сплавы и химические соединения (силикокальций, карбид каль-
ция и др.). Поэтому целесообразно проанализировать процессы, протекающие при растворении в железе сплавов и соединений кальция.
Данные о влиянии углерода на величину растворимости кальция в жид-
ком железе при 1600оС представлены на рисунке 2.10. Из приведенных данных видно, что растворимость кальция в железе увеличивается при повышении со-
держания углерода примерно до 0,8 – 0,9%. Дальнейшее увеличение концен-
трации углерода сопровождается резким уменьшением растворимости кальция,
которое объясняется началом протекания реакции образования карбида каль-
ция.
Химическая устойчивость карбида кальция в высокоуглеродистых рас-
плавах является причиной принципиального различия в механизме реакций,
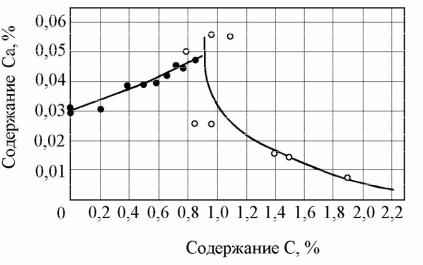
41
Рисунок 2.10 – Влияние углерода на растворимость кальция в железа при
1600оС
протекающих при обработке карбидом кальция низкоуглеродистой стали и чу-
гуна. При обработке низкоуглеродистого металла карбид кальция в расплаве термодинамически не устойчив и диссоциирует по реакции
CaC2 |
= {Ca} + 2[C] . |
(2.16) |
В чугуне карбид кальция является устойчивым соединением и реакции рафини-
рования протекают с участием твердых частиц карбида.
Характер процессов, протекающих при растворении силикокальция в желе-
зе, поясняется диаграммой на рисунке 2.11.
В процессе растворения частицы силикокальция обогащаются железом. При этом их химический состав изменяется вдоль пунктирной прямой на рисунке 2.11.
В точке r система расслаивается на две несмешивающиеся жидкости, одна из ко-
торых обогащена кальцием, а другая железом. При дальнейшем растворении об-
разовавшихся жидкостей их химический состав изменяется вдоль линий r − s2 − 0
и r − k − s − s1 − 0 диаграммы. При этом давление насыщенного пара кальция над
богатым кальцием расплавом быстро увеличивается и начинается его испарение.
Расчеты показывают, что при вводе силикокальция в сталь количества испарив-
шегося кальция и кальция, непосредственно растворяющегося в металле, соотно-