
SPR / Лекция_7
.pdf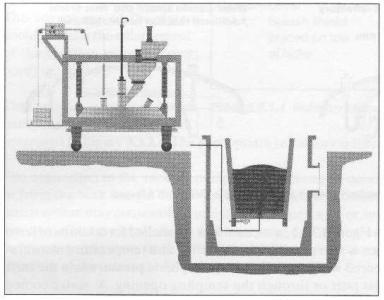
93
7 ВАКУУМИРОВАНИЕ СТАЛИ В КОВШЕ
7.1 Конструкция камерных вакууматоров
Для дегазации и обезуглероживания стали в ковше используют камерные вакууматоры (VD-процесс, VD), которые состоят из вакуумной камеры и крыш-
ки. При этом крышка или камера должны быть выполнены подвижными. Уп-
лотнение между камерой и крышкой осуществляется с помощью кольца из ре-
зины или пластмассы, причем уплотняемые поверхности, как правило, имеют водяное охлаждение.
Наибольшее распространение получили вакууматоры с подвижной крышкой (рисунок 7.1).
Рисунок 7.1 – Схема камерного вакууматора с подвижной крышкой
Цилиндрическая вакуумная камера обычно расположена в яме. Внутри камеры находится стенд для установки сталеразливочного ковша, а также ава-
рийные ямы, объем которых соответствует объему металла в ковше. Установка ковша на стенд и снятие его после дегазации осуществляется краном. В верхней части камеры расположен патрубок, соединенный с вакуумными насосами.
Удерживающие крышку металлоконструкции смонтированы на тележке,
94
которая по рельсам перемещается над вакуумной камерой. Крышка поднимает-
ся и опускается при помощи гидравлических цилиндров или системы лебедок.
На крышке монтируются бункера с вакуумными шлюзами, позволяющие вво-
дить в ковш раскислители и легирующие во время вакуумной обработки. Кроме того, на крышке имеется гляделка для визуального или с помощью телевизион-
ной камеры наблюдения за расплавом в ковше, шлюзы для отбора проб и заме-
ра температуры и др. Для интенсификации обезуглероживания и химического нагрева металла (процессы VD-OB, VOD) на крышке может также быть смон-
тирована водоохлаждаемая кислородная фурма с устройством для ее переме-
щения.
Внутренняя поверхность камеры, а также аварийные ямы футерованы шамотным кирпичом. На наружную поверхность стенда сталеразливочного ковша наносят футеровку из высокоглиноземистых масс. Для защиты от вы-
плесков и теплового излучения на внутреннюю поверхность крышки также на-
носят футеровку из высокоглиноземистых масс. Кроме того, между крышкой и верхней частью ковша могут быть дополнительно установлены защитные экра-
ны различной конструкции.
Вакуумирование металла ведут в ковшах с основной или высокоглинозе-
мистой футеровкой, оборудованных 1 – 3 пористыми пробками для перемеши-
вания расплава продувкой аргоном. Учитывая возможное вспенивание металла и шлака при вакуумировании, обычно используют ковши большей вместимо-
сти, чем та, которая соответствует массе обрабатываемого металла. Высота сво-
бодного борта ковша должна составлять 0,9 – 1,2 м.
Размеры вакуумной камеры определяются возможностью беспрепятст-
венной установки и извлечения ковша. Это требует достаточно большого сво-
бодного пространства между ковшом и внутренними стенками камеры. Разме-
ры используемых для вакуумирования металла ковшей и вакуумных камер приведены в таблице 7.1. Большие объемы вакуумных камер являются одной из главных причин, в силу которых продолжительность цикла обработки в про-
цессе VD обычно на 5 – 10 минут больше, чем процессе RH.
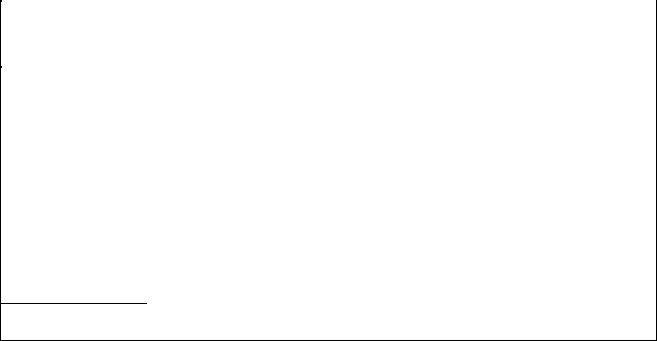
95
Таблица 7.1 – Размеры ковшей и вакуумных камер для обработки стали
Показатель |
|
Масса обрабатываемой стали, т |
|
||||
|
|
|
|
|
|
|
|
|
7 – 27 |
22 – 24 |
30 |
47 |
80 |
90 |
110 |
|
|
|
|
|
|
|
|
|
|
|
Ковши |
|
|
|
|
Емкость, т |
– |
30 |
50 |
70 |
100 |
– |
– |
Свободный |
|
|
|
|
|
|
|
борт ковша, мм |
1000 |
– |
– |
– |
– |
1070 |
1220 |
|
|
Вакуумные камеры |
|
|
|
||
Диаметр, мм |
3950 |
4300 |
– |
– |
5000 |
4877 |
6100 |
Высота, мм |
5590 |
5540 |
– |
– |
4880 |
6706 |
9140 |
Объем, м3 |
65* |
80** |
– |
– |
100* |
125** |
266** |
*Опубликованные значения **Расчетные значения
По той же причине камерные вакууматоры обычно оборудованы четырех-
или пятиступенчатыми пароэжекторными насосами с одной или двумя допол-
нительными ступенями, которые используются совместно с первой или второй основными ступенями, чтобы ускорить откачку камеры до давлений ≈ 3 кПа.
Рабочее давление четырех- и пятиступенчатых насосов не превышает 130 Па.
В некоторых установках VD вакуумная крышка устанавливается непо-
средственно на ковш, оборудованный фланцем, на который укладывается коль-
цевое уплотнение. Однако, высокая температура корпуса ковша приводит к то-
му, что уплотнение быстро теряет пластичность и деформируется.
7.2Технология обработки металла в камерных вакууматорах без использования кислорода
Обычно нераскисленный металл выпускают в хорошо прогретый ковш с основной футеровкой. Во время выпуска проводятся мероприятия, направлен-
ные на предотвращение попадания в ковш печного шлака, и присадка шлакооб-
разующих. Если вакуумная обработка выполняется с целью дегазации и кор-
96
ректировки химического состава стали, по ходу выпуска в ковш вводят раскис-
лители и легирующие. Если главной задачей вакуумирования является обезуг-
лероживание расплава, присадка ферросплавов в ковш по ходу выпуска не про-
водится.
При обработке металла на установках VD с подвижной крышкой основ-
ные технологические операции выполняются в следующей последовательности.
Ковш транспортируют к вакууматору и устанавливают на стенд внутри вакуумной камеры. Подключают систему подачи аргона. После начала продув-
ки визуально контролируют нормальную работу пористых пробок. Одновре-
менно контролируют высоту свободного борта ковша и отбирают пробу метал-
ла для химического анализа.
Устанавливают транспортирующую крышку тележку над вакуумной ка-
мерой, накрывают камеру крышкой и поочередно включают вакуумные насосы.
Во время откачки камеры металл начинает кипеть. При обработке конст-
рукционной и подшипниковой стали в нераскисленном состоянии кипение ме-
талла начинается при понижении давления до 80 – 65 кПа, при дальнейшей от-
качке интенсивность кипения постепенно увеличивается. Наиболее интенсив-
ное кипение наблюдается при давлении 4 – 1,5 кПа, после чего интенсивность кипения постепенно уменьшается. При вакуумировании частично раскисленно-
го металла (0,15% Si и 0,005% Al) заметное кипение начинается только при дос-
тижении давления 30 кПа, а при давлении 15 кПа кипение начинает затухать.
Имеются также сообщения о том, что и при вакуумировании раскислен-
ной алюминием стали может иметь место вспенивание шлака в результате взаимодействия оксидов железа в шлаке с растворенным в металле углеродом
(подшлаковое кипение).
Поэтому во время откачки через гляделку вакуумной камеры следят за поведением металла и шлака в ковше. Скорость откачки регулируют в зависи-
мости от интенсивности кипения. В отдельных случаях, чтобы предотвратить чрезмерное вспенивание металла и перелив его через край ковша, используют напуск в вакуумную камеру аргона или азота.
97
Чтобы уменьшить вероятность вспенивания шлака во время откачки ка-
меры при обработке раскисленной алюминием стали рекомендуют следующие мероприятия: вдувание аргона расходом 0,2 – 0,5 нл/(т·мин), быстрая откачка,
добавки извести для загущения шлака.
При давлении в камере менее 300 Па расход аргона постепенно увеличи-
вают для эффективной дегазации.
Продолжительность дегазации зависит от времени, необходимого для по-
нижения содержания водорода, азота и углерода до требуемого уровня. В за-
ключительной части обработки на основании данных химического анализа ра-
нее отобранной пробы корректируют состав металла присадкой раскислителей и легирующих, после чего проводят гомогенизацию металла.
Когда обработка закончена, поочередно отключают эжекторы и заполня-
ют камеру воздухом до атмосферного давления. Затем отключают подачу арго-
на и, если требуется, через отверстие в крышке вводят в сталь кальцийсодер-
жащую порошковую проволоку. Проводят отбор пробы металла для химиче-
ского анализа и замер температуры. Поднимают крышку вакуумной камеры и перемещают тележку в нерабочее положение. Ковш извлекают из камеры и от-
правляют на разливку.
Если главной задачей обработки является удаление водорода, обработку рекомендуют вести под шлаком повышенной вязкости, который при продувке металла аргоном оттесняется к стенкам ковша. Открытая поверхность металла должна составлять около 70% площади сечения ковша. Сообщается, что при давлении в камере в момент окончания обработки 100 Па в течение 9 – 10 ми-
нут от начала откачки содержание водорода в металле может быть понижено в среднем от 6,7 ppm до 1,5 – 2,0 ppm.
При наличии в ковше высокоосновного шлака содержание серы в металле в процессе VD может быть понижено от 0,010 – 0,020 до 0,001 – 0,005%. Эф-
фективному использованию десульфурирующей способности шлака способст-
вует высокая интенсивность перемешивания его с металлом при продувке ар-
гоном в вакууме. Однако, высокая степень десульфурации металла достигается
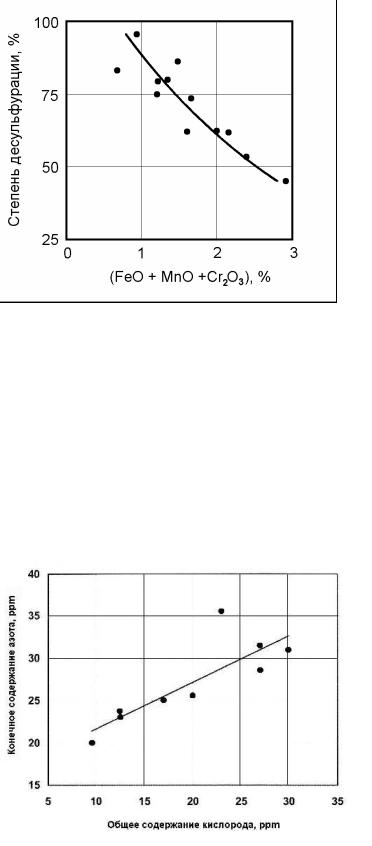
98
только при низкой окисленности шлака. В качестве примера на рисунке 7.2 по-
казана зависимость степени десульфурации раскисленной алюминием низколе-
гированной стали от суммарного содержания в шлаке FeO, MnO и Cr2O3.
Рисунок 7.2 – Зависимость степени десульфурации стали в процессе VD
от содержания оксидов в шлаке
Обязательным условием эффективного удаления азота при вакуумирова-
нии является низкое содержание в металле серы и кислорода, которые, являясь поверхностно-активными веществами, уменьшают скорость массопередачи азота через границу раздела фаз. В качестве примера, подтверждающего это положение, на рисунке 7.3 показана зависимость концентрации азота в раскис-
ленной алюминием низколегированной стали от общего содержания кислорода после вакуумирования в 100-т ковше.
Рисунок 7.3 – Влияние содер-
жания кислорода на концентра-
цию азота в стали после вакуу-
мирования
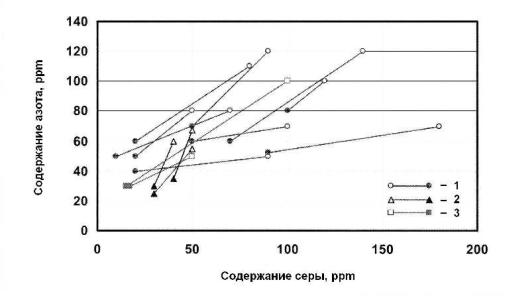
99
На рисунке 7.4 приведены сведения о влиянии содержания серы в стали на эффективность удаления азота в процессе VD в ковшах разной вместимости при различной интенсивности продувки металла аргоном.
Рисунок 7.4 – Влияние содержания серы в стали на эффективность удаления азота при вакуумировании в ковшах разной вместимости:
1 – 70-т ковш, 2 нл Ar/(т·мин); 2 – 100-т ковш, 7 нл Ar/(т·мин); 3 – 240-т ковш, 12 нл Ar/(т·мин)
Из рисунка видно, что содержание азота менее 0,004% может быть полу-
чено при концентрации серы в стали менее 0,004% и интенсивной продувке ме-
талла аргоном.
При использовании процесса VD для обезуглероживания металла в 220 – 260-т ковшах высота свободного борта ковша обычно составляет 0,7 – 1,2 м,
расход аргона – 400 – 2400 нл/мин. В этих условиях при исходной концентра-
ции углерода ≈ 300 ppm вакуумирование продолжительностью 15 – 25 мин. по-
зволяет понизить содержание его в металле до 20 – 30 ppm. Наиболее высокие скорости обезуглероживания металла наблюдаются при интенсивной продувке расплава аргоном.
100
7.3Технология обработки металла в камерных вакууматорах с продувкой кислородом
Последовательность технологических операции при обработки метала в камерных вакууматорах с продувкой кислородом (процесс VD-OB) и без про-
дувки в целом сходна. Различия заключаются в следующем.
При получении стали с ультранизким содержанием углерода концентра-
ция его в металле на выпуске из сталеплавильного агрегата может находиться в пределах 0,05 – 0,06%.
Во время откачки камеры при давлении 25 кПа начинают подачу кисло-
рода в металл для ускоренного обезуглероживания. При этом наблюдают за по-
ведением металла в ковше. При чрезмерной интенсивности кипения металла давление в камере увеличивают до тех пор, пока кипение не утихнет. После достижения давления 100 Па расход аргона увеличивают и в течение примерно
4 минут ведут интенсивную продувку для глубокого обезуглероживания.
Технология получения стали с ультранизким содержанием углерода в процессах VD и VD-OB представлена в таблице 7.2.
Процесс VD-OB также может быть эффективно использован для повыше-
ния температуры стали за счет тепла экзотермической реакции между кислоро-
дом и алюминием. Как и в процессе RH-KTB могут быть использованы два спо-
соба нагрева металла: прямой химический нагрев и нагрев с переокислением.
При прямом химическом нагреве перед продувкой кислородом в раскис-
ленную алюминием сталь вводят дополнительное количество алюминия, кото-
рое обеспечивает требуемое повышение температуры металла.
При химическом нагреве с переокислением продолжительность продувки кислородом увеличивают для переокисления нераскисленного металла, после чего измеряют активность кислорода в металле и вводят алюминий. Так как возможности переокисления металла ограничены, подъем температур при та-
ком способе обработки обычно не превышает 25оС. При необходимости более высокого нагрева выполняют несколько циклов продувки металла кислородом
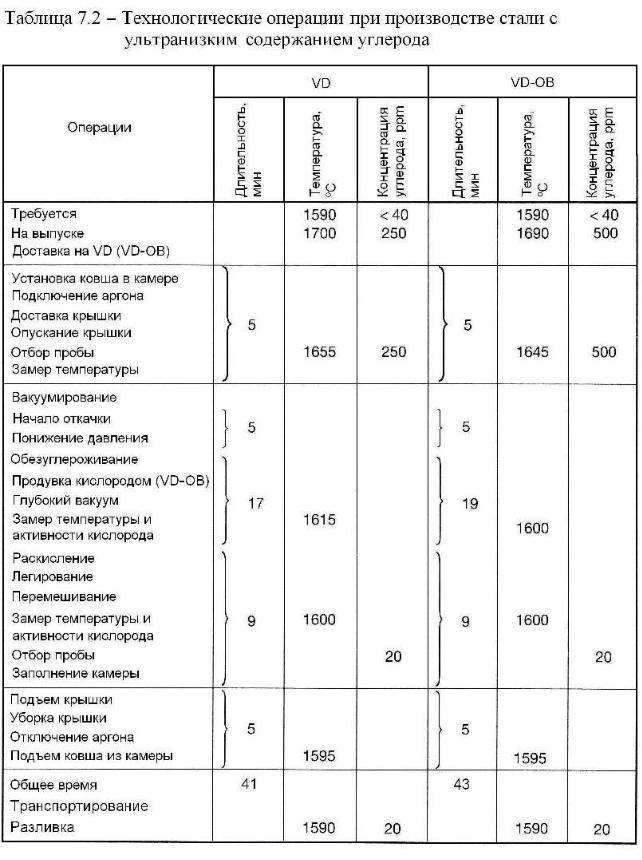
101

102
с последующим вводом алюминия.
7.4Сравнительная характеристика различных способов вакуумирования металла
Особенности процессов RH и VD представлены для сравнения в таблице
7.3.
Таблица 7.3 – Сравнительная характеристика процессов RH и VD
Наименование |
VD |
RH |
|
|
|
Высота свободно- |
Обычно ≥ 1000 мм, при про- |
Обычно ≥ 200 мм |
го борта ковша |
изводстве стали с ультра- |
|
|
низким содержанием угле- |
|
|
рода и низким содержанием |
|
|
азота ≥ 1300 мм |
|
Наличие порис- |
Необходима одна |
Не требуется |
тых пробок |
или более |
|
Отсечка печного |
Необходима |
Не требуется |
шлака |
|
|
Глубина обезуг- |
≈ 20 ppm |
≈ 15 ppm |
лероживания |
|
|
Десульфурация |
Хорошая |
Обычно не проводится |
металла |
|
|
Возможность уда- |
Несколько лучше, чем в |
Ограничена |
ления азота |
процессе RH |
|
Потери темпера- |
Выше, чем в процессе RH |
Низкие |
туры металла |
|
|
Футеровка: |
|
|
ковша |
Ускоренный износ в шлако- |
Срок службы выше, чем в |
|
вом поясе |
процессе VD |
камеры |
Ремонт футеровки вакуум- |
Дополнительные затраты, |
|
ной камеры не требуется |
связанные с ремонтом футе- |
|
|
ровки вакуумной камеры |
Капитальные |
Ниже, чем в процессе RH |
Выше, чем в процессе VD |
вложения |
|
|
Ранее отмечалось также, что производительность установок RH выше,
чем установок VD. Усвоение раскислителей и легирующих в процессе RH вы-