
SPR / Лекция_9
.pdf115
9 ПРОИЗВОДСТВО КОРРОЗИОННОСТОЙКОЙ, ЖАРОСТОЙКОЙ
ИЖАРОПРОЧНОЙ СТАЛИ
9.1Общая характеристика стали высоколегированной коррозионно- стойкой, жаростойкой и жаропрочной
Взависимости от основных свойств стали подразделяют на группы:
∙коррозионностойкие (нержавеющие) – стали, обладающие стойкостью про- тив электрохимической и химической коррозии (атмосферной, почвенной, щелочной, кислотной, солевой), межкристаллитной коррозии, коррозии под напряжением и др.;
∙жаростойкие (окалиностойкие) – стали, обладающие стойкостью против хи- мического разрушения поверхности в газовых средах при температурах вы- ше 550оС, работающие в ненагруженном или слабонагруженном состоянии;
∙жаропрочные стали, способные работать в нагруженном состоянии при вы- соких температурах в течение определенного времени и обладающие при этом достаточной жаростойкостью.
Взависимости от структуры стали и сплавы подразделяют на классы:
∙ферритные – стали, имеющие структуру феррита без α↔γ превращений;
∙мартенситные – стали с основной структурой мартенсита;
∙аустенитные – стали, имеющие структуру аустенита;
∙аустенито-ферритные – стали, имеющие структуру аустенита и феррита, со- держание феррита не более 10%.
Сведения о химической составе сталей перечисленных выше классов
приведены в таблице 9.1.
Перечисленные выше стали экономически целесообразно выплавлять с использованием наиболее дешевых марок высокоуглеродистого феррохрома. В связи с этим производство коррозиоонностойкой, жаростойкой и жаропрочной стали обычно организовано следующим образом. В электропечах с использова- нием высокоуглеродистого феррохрома, металлического лома и шихтовой заго-
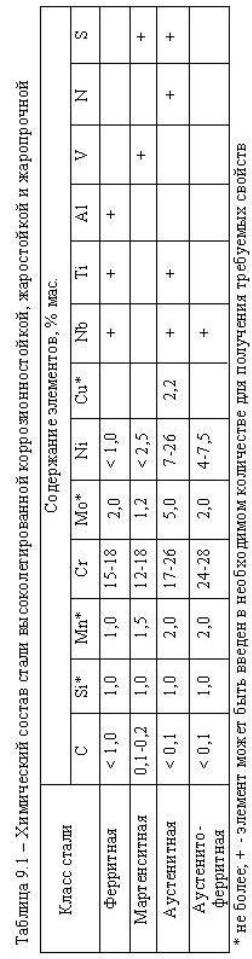
116
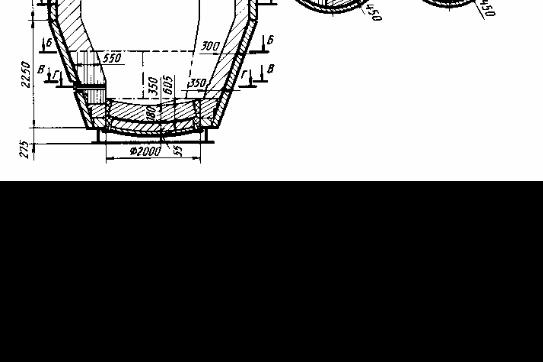
117
товки выплавляют полупродукт с высоким содержанием углерода, который за- тем подвергают обезуглероживанию в конвертерах аргонно-кислородного ду- тья (конвертеры AOD) или камерных вакууматорах с продувкой металла кисло- родом (VOD-процесс).
9.2Выплавка высоколегированной стали в конвертерах аргонно-кислородного дутья
9.2.1Конструкция конвертера аргонно-кислородного дутья
Конструкция 80-т конвертера AOD с симметричной горловиной показана на рисунке 9.1.
Рисунок 9.1 – Конструкция 80-т конвертера AOD
Для подачи кислорода и аргона в металл используются фурмы, располо- женные у днища в стенке, противоположной сливному носку конвертера. Фур- мы расположены по дуге, длина которой равна 1/3 диаметра конвертера на этом

118
уровне (разрез Г – Г). Поэтому при повалке конвертера фурмы располагаются над поверхностью металла.
В рассматриваемом конвертере фурмы состоят из центральной трубы внутренним диаметром 13 мм и наружной трубы диаметром 16 мм. По цен- тральной трубе подают смесь кислорода с аргоном, в зазор между трубами по- дают аргон для охлаждения фурмы. В данной конструкции конвертера исполь- зуется 5 фурм, оси которых смещены на угол, равный 25о. Этим достигается сравнительно равномерное распределение вдуваемого газа в ванне конвертера.
9.2.2Технология выплавки стали в конвертерах аргонно-кислородного дутья
Выплавка легированного полупродукта ведется в дуговых электропечах с использованием в шихте максимального количества отходов легированной ста- ли и высокоуглеродистых ферросплавов, а также извести в количестве 30 – 40 кг/т. Металл перед выпуском содержит 1,7 – 3% С и ~ 0,2% Si. Печной шлак, содержащий ~ 4% оксидов хрома, вместе с металлом сливают в ковш и залива- ют затем в конвертер. Температура металла после перелива составляет 1540оС.
Сведения об изменении химического состава и температуры металла при выплавке хромоникелевой стали в 80-т конвертере AOD приведены на рисунке
9.2.
Для интенсификации окисления углерода по ходу продувки необходимо придерживаться оптимального соотношения между количествами вдуваемых в металл кислорода и аргона. Ниже приведены рекомендуемые соотношения рас-
ходов этих газов в различных периодах продувки: |
|
|
|
||
Период продувки |
1 |
2 |
3 |
4 |
5 |
Отношение расхода кислорода к |
|
|
|
|
|
расходу аргона |
5:1 |
3:1 |
2:1 |
1:1 |
1:2 |
Концентрация углерода в конце |
|
|
|
|
|
периода, % |
* |
0,55 |
0,35 |
0,20 |
0,08 |
*Определяется достижением температуры 1700оС

119
Рисунок 9.2 – Диаграмма плавки хромоникелевой стали в конвертере AOD:
I, II, III – периоды плавки; К – период кипения без продувки кислородом; В – восстановление; Д – десульфурация; 1 – температура металла; 2 – содержание хрома; 3 – содержание марганца; 4 – содержание углерода. Числа у горизон- тальных стрелок (5:1, 3:1, 2:1, 1:1, 1:2) – отношения расходов кислорода и арго- на; числа у вертикальных стрелок – масса присадок, кг
Для быстрого повышения температуры ванны первый этап продувки ве- дут без ввода в конвертер охладителей. Интенсивность продувки составляет около 1 м3/(т·мин). При температуре ~ 1700оС в конвертер вводят агломерат ок- сида никеля, ферромарганец и феррохром, в дальнейшем в качестве охладителя используют гранулированный ферроникель.
В конце окислительной продувки подачу кислорода прекращают и, про- должая продувку ванны аргоном с интенсивностью ~ 0,7 м3/(т·мин), проводят завершающий период обезуглероживания, одновременно понижая содержание растворенного в металле кислорода и оксидов железа в шлаке (период «выки- пания»). Исключением являются плавки, в которых содержание углерода в ме-
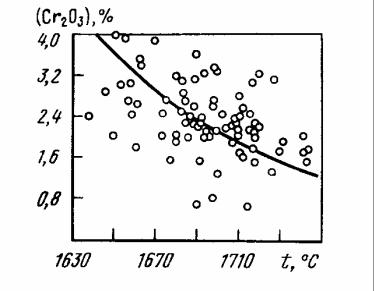
120
талле должно составлять < 0,03%. В этом случае продувку металла смесью ки- слорода и инертного газа в соотношении 1:2 ведут до концентрации углерода ~ 0,04%, в ходе дальнейшей продувки содержание аргона в смеси непрерывно увеличивают до соотношения 1:8.
После достижения требуемой концентрации углерода для восстановления хрома из оксидов в шлаке в конвертер вводят ферросилиций, продолжая про- дувку ванны аргоном в течение 5 – 6 минут. При этом содержание оксидов хро- ма в шлаке понижается до ~ 1,7%.
Установлено, что при концентрации кремния в металле более 0,2% даль- нейшее увеличение его содержания не сопровождается существенным умень- шением содержания оксидов хрома в шлаке. Зависимость содержания Cr2O3 в
шлаке в конце периода восстановления от температура ванны и основности шлака B = (CaO + MgO)/(SiO2) приведена на рисунках 9.3 и 9.4.
Рисунок 9.3 – Зависимость содержания Cr2O3 в шлаке в конце периода восста-
новления от температуры
По окончанию периода восстановления из конвертера сливают 2/3 шлака, вводят новую порцию флюсов и в течение 3 – 4 минут проводят десульфура- цию стали, перемешивая ванну аргоном. При необходимости в конвертер вво- дят охлаждающие добавки, чтобы понизить температуру металла в конце плав-
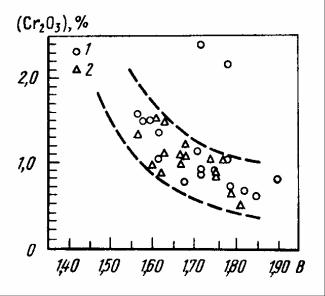
121
Рисунок 9.4 – Зависимость содержания Cr2O3 в шлаке от его основности в кон-
це периода восстановления: 1 – магнезитохромитовая футеровка; 2 – магнези- тодоломитовая футеровка
ки до 1600оС.
При продувке металла в конвертерах AOD возможна частичная замена аргона более дешевым азотом. Установлено, что основное количество азота, поглощенного сталью в I периоде продувки (см. рисунок 9.2) при продувке сме- сью кислорода и азота, в последующие II и III периоды при продувке смесью кислорода и аргона из металла удаляется. При выплавке стали с содержанием хрома до 27%, никеля до 35% и минимальным содержанием углерода 0,015% расход азота может составлять 30 – 40% общего расхода инертного газа. При этом концентрация азота в стали не превышает 0,04 – 0,05%.
При выплавке 1 т стали Х18Н9 в конвертерах AOD расходуется: аргона и азота 23 м3, кремния на восстановление 11 кг, металлических охладителей 180 кг, извести в периоды окисления и восстановления 50 кг, извести для десульфу- рации 20 кг, плавикового шпата 6 кг.

122
9.3Рафинирование высоколегированного полупродукта продувкой кислородом в камерных вакууматорах
9.3.1Оборудование для рафинирования металла продувкой кислородом в камерных вакууматорах
Продолжительность рафинирования высоколегированного полупродукта продувкой кислородом в камерных вакууматорах (процесс VOD) сравнима с длительностью выплавки его в электропечи, а в ряде случаев превышает время между выпусками металла. Поэтому, как правило, используются установки VOD с двумя вакуумными камерами, имеющими общие вакуумные насосы, систему бункеров для подачи ферросплавов и шлакообразующих и др. Схема оборудования установки VOD показана на рисунке 9.5.
Рисунок 9.5 – Схема оборудования установки VOD:
1 – вакуумная камера; 2 – крышка вакуумной камеры; 3 – водоохлаждаемый эк- ран; 4 – вакуумный шлюз; 5 – кислородная фурма; 6 – устройство для отбора проб и замера температуры; 7 – весовые воронки; 8 – бункера для ферросплавов
ишлакообразующих; 9 – пароэжекторный насос; 10 – пульт управления
Вцелом конструкция установок VOD сходна с конструкцией установок

123 VD-OB. Основные отличия заключаются в большей мощности эжекторов в об- ласти давлений 30 кПа и ниже, а также большей емкости вакуумного шлюза, который должен обеспечивать быстрый ввод большого количества шлакообра- зующих.
Для защиты вакуумной крышки от высоких тепловых нагрузок на уста- новках VOD используют брызго- и теплозащитные экраны, варианты конст- рукции которых показаны на рисунке 9.6.
Рисунок 9.6 – Устройства для защиты вакуумной крышки установок VOD:
а – футерованный брызгозащитный экран с водоохлаждаемой плитой; б - водо- охлаждаемый брызгозащитный экран
Для уплотнения зазора между брызгозащитным экраном и ковшом ис- пользуют пластиковые рукава длиной 0,5 м и диаметром 0,15 м, заполненные высокоглиноземистой массой. Стойкость футерованного брызгозащитного эк- рана обычно составляет 10 – 15 плавок, водоохлаждаемого – в 20 раз выше.
Высота свободного борта ковшей, используемых на установках VOD, должна составлять 1,2 – 1,5 м. В зоне контакта с жидким металлом рабочий слой футеровки ковша выполняют из доломитового или магнезитового кирпи- ча. Между рабочим и арматурным слоями предусмотрена набивка из доломита или магнезита толщиной около 40 мм, наличие которой сводит к минимуму
124
опасность прорыва металла через стыки кирпичей. В зоне шлакового пояса и верхней части ковша рабочий слой футеровки выполняют из периклазоуглеро- дистого кирпича, что позволяет использовать ковш и для обработки металла на УКП. Стойкость футеровки ковша обычно составляет 15 – 20 плавок.
9.3.2Технология рафинирования высоколегированного полупродукта продувкой кислородом в вакууме
Для рафинирования на установках VOD рекомендуют использовать по- лупродукт, содержащий 0,5 – 1,0% С и около 0,1% Si. Концентрация хрома должна приближаться к верхнему пределу, предусмотренному маркой выплав- ляемой стали, никеля и молибдена – к нижнему пределу. При производстве ста- ли ферритного класса полупродукт должен содержать 0,3% Mn, аустенитного – 1%. При вакуумном рафинировании потери марганца испарением составляют около 20%.
Выплавка полупродукта в электропечах сопровождается частичным окислением хрома. Поэтому перед выпуском из электропечи на шлак присажи- вают FeSi. При температуре 1660оС печной шлак вместе с металлом выпускают в ковш. Интенсивное перемешивание в ковше во время выпуска плавки способ- ствует восстановлению хрома. По окончанию выпуска шлак, содержащий, %
мас.: 45 – 50 CaO; 15 – 18 SiO2; ≈ 20 Al2O3; ≈ 5 Cr2O3; ≈ 4 MgO; ≈ 6 (FeO + MnO),
скачивают из ковша. После скачивания шлака отбирают пробу металла для хи- мического анализа, проводят замер температуры и загружают в ковш известь. Температура полупродукта, поступающего на установки VOD, должна состав- лять около 1600оС.
Последовательность технологических операций в процессе VOD рас- смотрим на примере получения аустенитной стали с содержанием углерода 0,03% из 100 т полупродукта с исходным содержанием углерода 0,5%. Уста- новка оборудована водоохлаждаемым брызгозащитным экраном, подвешенным под крышкой вакуумной камеры.