
SPR / Лекция_4
.pdf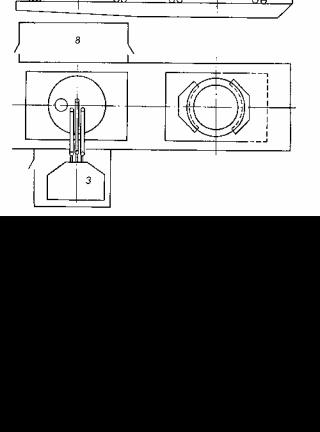
55
4 КОНСТРУКЦИЯ И ОРГАНИЗАЦИЯ РАБОТЫ АГРЕГАТА КОВШ-ПЕЧЬ
4.1 Основное технологическое оборудование установки ковш-печь
В сталеплавильных цехах отечественных и зарубежных металлургиче-
ских заводов для доводки стали по температуре и химическому составу широко используются УКП (рисунок 4.1), которые позволяют выполнять различные ви-
ды внепечной обработки одновременно с электродуговым нагревом металла в ковше.
Рисунок 4.1 – Схема установки ковш-
печь:
1 – металловозная тележка; 2 – стале-
разливочный ковш; 3 – трансформа-
тор стенда электродугового нагрева; 4 – крышка стенда электродугового нагрева; 5 – бункер для подачи фер-
росплавов и лигатур; 6 – дозирующие весы; 7 – бункера ферросплавов и ли-
гатур; 8 – пульт управления
Для обработки на УКП металл подают в ковшах, оборудованных шибер-
ными затворами и 1 – 3 пористыми пробками для продувки расплава аргоном,
которая необходима для выравнивания температуры и химического состава ме-
талла в объеме ковша. Рабочий слой футеровки ковша выполняют из основных формованных огнеупоров или тиксотропного корундошпинелидного бетона. В
зоне шлакового пояса используют периклазоуглеродистый кирпич с высоким

56
содержанием плавленого магнезита и добавлением комбинированных антиок-
сидантов и органической (полимерной) связки состава, % мас.: MgO > 97; CaO
< 2,0; SiO2 < 0,5; Fe2O3 < 0,5; Al2O3 < 0,3; остаточный углерод > 12,0 (сверх
100%). При обработке металла на УКП высота свободного борта ковша должна составлять около 0,5 м.
На металловозной тележке ковш транспортируют к стенду электродуго-
вого нагрева УКП и накрывают крышкой, которая уменьшает потери тепла при нагреве и обработке металла, создает безопасные условия работы, уменьшая разбрызгивание при подаче в ковш шлакообразующих и ферросплавов, защи-
щает металл от окисления и насыщения газами и сбора отходящих газов.
Крышку ковша современных УКП выполняют водоохлаждаемой. Она может быть выполнена в виде металлического кожуха с расположенными внутри него трубами водяного охлаждения или только из труб водяного охлаждения, вплот-
ную прилегающих друг к другу. Для уменьшения потерь тепла на внутреннюю поверхность новой крышки наносят футеровку, а в процессе эксплуатации она покрывается слоем гарнисажа.
В крышке имеются отверстия, через которые в ковш опускают графито-
вые электроды, подают ферросплавы и шлакообразующие.
Помимо оборудования, показанного на рисунке 4.1, современные УКП оборудованы манипуляторами для измерения температуры и активности кисло-
рода в металле, отбора проб металла и шлака, фурмами для продувки стали ар-
гоном и порошками, трайб-аппаратами для ввода порошковой проволоки.
Необходимую мощность трансформатора УКП можно оценить по форму-
ле
W = |
c ×v ×m × f |
, |
(4.1) |
ηтерм ×ηэл ×Cosϕ |
где W – мощность трансформатора, МВт; c – удельная энергия (для стали
0,23), кВт·ч/(т·оС); v – расчетная скорость нагрева, которая учитывает потери тепла на нагрев футеровки ковша, излучением с его поверхности и через слой шлака; m – масса металла в ковше, т; f – коэффициент перевода, равный 60
57
мин/ч; ηтерм – термический к.п.д. УКП (доля тепла электрической дуги, кото-
рая расходуется для нагрева металла); ηэл – электрический к.п.д. УКП (доля потребляемой электроэнергии, которая достигает электрической дуги).
Эффективная скорость нагрева металла зависит от потерь тепла излуче-
нием и на нагрев футеровки ковша, величина которых изменяется от 2оС/мин для ковшей малого тоннажа до 0,5оС/мин для ковшей вместимостью около 200
т.
Термический к.п.д. УКП определяется главным образом соотношением длины дуги и толщины слоя шлака. Недостаточная по отношению к длине дуги толщина слоя шлака приводит к увеличению потерь тепла излучением.
Электрический к.п.д. установки при прочих равных условиях зависит от силы тока во вторичной цепи. Работа с малыми токами (длинными дугами)
обычно связана с меньшими омическими потерями.
В оценочных расчетах рекомендуется пользоваться следующими значе-
ниями: ηтерм ≈ 0,6; ηэл ≈ 0,9; Cosϕ ≈ 0,7.
Рассчитанные по формуле (4.1) зависимости необходимой мощности трансформатора УКП от массы обрабатываемого металла для различных значе-
ний эффективной скорости его нагрева показаны на рисунке 4.2.
В таблице 4.1 приведены основные технические характеристики УКП ря-
да металлургических предприятий.
Наиболее часто встречающиеся варианты конструкции УКП представле-
ны на рисунке 4.3.
На рисунке 4.3а показана конструкция УКП со стационарной крышкой.
При использовании установок такого типа ковш располагается на металловоз-
ной тележке, которая транспортирует его на позицию обработки и далее в зону выдачи ковша.
На рисунке 4.3б показана конструкция УКП с двумя стационарными стендами. Установка ковшей на стенды и их снятие выполняется при помощи крана. Крышка и электроды (или только электроды) крепятся на вращающейся
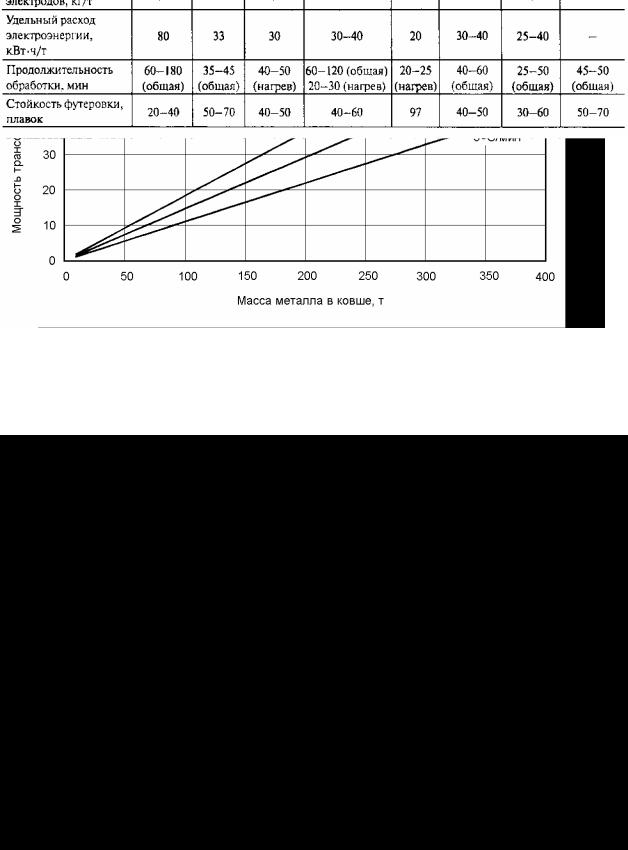
58
Рисунок 4.2 – Зависимость мощности трансформатора УКП от массы металла в
ковше и эффективной скорости нагрева
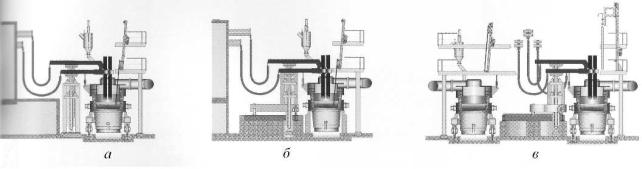
59
Рисунок 4.3 – Варианты конструкции УКП
консоли. После окончания обработки одного из ковшей консоль поворачивает-
ся на 90о и начинается обработка ковша на другом стенде.
На рисунке 4.3в показана конструкция УКП, с двумя стационарными крышками. Для транспортировки ковшей используют две металловозные те-
лежки, перемещающиеся по параллельным рельсовым путям. Электроды закре-
плены на вращающейся консоли, которая перед началом обработки следующе-
го ковша поворачивается на 180о.
4.2 Технология обработки металла на установке ковш-печь
В качестве примера рассмотрим технологию доводки на УКП низкоугле-
родистой стали состава, % мас.: 0,05 C; 0,25 Mn; 0,05 Si; 0,010 P; 0,007 S; 0,020
Alобщ. Температура металла после обработки на УКП должна составлять 1605оС.
Сведения о технологических операциях, выполняемых при доводке металла представлены в таблице 4.2, сведения об изменении электрической мощности и расхода аргона приведены на рисунке 4.4.
Нераскисленный металл, содержащий 0,04% C, 0,08 ÷ 0,10% Mn и 0,012%
S, выпускают в ковш при температуре 1690оС. По ходу выпуска в ковш приса-
живают ферромарганец, алюминий и шлакообразующую смесь. По окончанию выпуска ковш при помощи крана транспортируют к УКП.
После доставки на УКП ковш устанавливают на металловозную тележку.

60
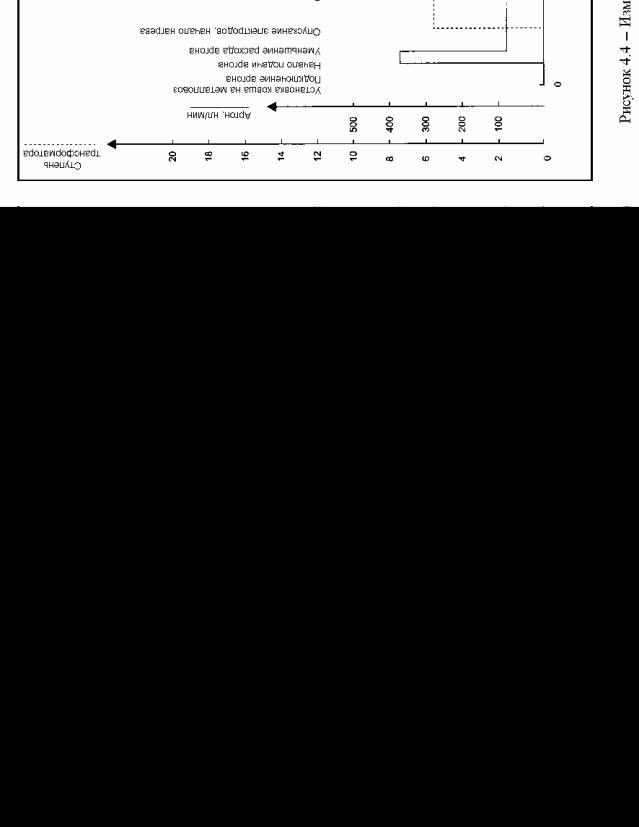
61
62
При установке ковша автоматически выполняется подключение продувочных пробок к трубопроводу подачи аргона. При расходе аргона 400 нл/мин по нали-
чию продувочного пятна на поверхности шлака визуально контролируют нача-
ло продувки, после чего расход аргона уменьшают до 100 нл/мин и транспор-
тируют ковш на позицию обработки. Суммарная продолжительность этих опе-
раций составляет 4 минуты.
После доставки на позицию обработки ковш накрывают крышкой, при этом автоматически включается система отвода отходящих газов. Одновремен-
но с опусканием крышки электроды раздельно опускают к поверхности распла-
ва и начинают нагрев. Продолжительность этих операций составляет 1 минуту.
Нагрев металла на УКП обычно начинается на малой мощности. Это обеспечивает стабильное горение коротких дуг и быстрое расплавление ковше-
вого шлака. Старт на высокой мощности может привести к нестабильному го-
рению дуг и сильной осцилляции (качанию) электродов. Причина возникнове-
ния осцилляции заключается в том, что к этому времени формирование жидко-
го ковшевого шлака еще не завершилось. Твердые куски флюсов движутся по поверхности расплава и попадают в зону горения дуги.
В первом периоде нагрева обычно решаются задачи усреднения химиче-
ского состава и температуры металла в ковше, а также формирования жидкого ковшевого шлака высокой основности с минимальным содержанием оксидов железа и марганца. Для этого используют присадки флюсов и обработку шлака раскислителями (алюминием, карбидом кальция, углеродсодержащими мате-
риалами и др.). В первом периоде нагрева возможна также подача в ковш фер-
росплавов.
В рассматриваемом случае через 3 минуты после начала нагрева питание отключили, провели замер температуры и отбор 1-й пробы металла для хими-
ческого анализа, после чего продолжили нагрев. В этот момент при температу-
ре 1600оС металл содержал, % мас.: 0,04 C; 0,19 Mn; 0,02 Si; 0,009 P; 0,011 S;
0,015 Al.
После 8 минут нагрева питание отключили и в течение 1 минуты провели
63
гомогенизацию металла, увеличив расход аргона до 250 нл/мин. Затем повтор-
но провели замер температуры, отобрали 2-ю пробу металла для химического анализа и возобновили нагрев. К концу первого периода нагрева при темпера-
туре 1600оС химический состав металла был следующим, % мас.: 0,04 C; 0,20
Mn; 0,03 Si; 0,009 P; 0,008 S; 0,011 Al.
В начале второго периода нагрева в течение 1 минуты в металл были по-
даны корректирующие добавки ферросплавов, после чего нагрев продолжался в течение 7 минут.
После отключения питания расход аргона увеличили до 400 нл/мин и в течение 3 минут проводили десульфурацию, перемешивая металл с ковшевым шлаком. Затем в течение 2 минут проводили гомогенизацию металла при рас-
ходе аргона 100 нл/мин.
После этого провели замер температуры и отобрали 3-ю пробу металла.
На основании результатов анализа 3-й пробы металл содержал, % мас.: 0,05 C; 0,26 Mn; 0,04 Si; 0,009 P; 0,006 S; 0,025 Al. Температура металла была равной 1615оС.
После отбора 3-й пробы в течение 5 минут проводилась «мягкая» продув-
ка металла аргоном с расходом 75 нл/мин, в ходе которой решалась задача ра-
финирования металла от неметаллических включений. Затем подачу аргона прекратили и в течение 2 минут металл обрабатывали кальцийсодержащей по-
рошковой проволокой.
Через 2 минуты после ввода порошковой проволоки ковш был отправлен на разливку. При этом температура металла была равной 1605оС, а состав ме-
талла следующим, % мас.: 0,05 C; 0,26 Mn; 0,04 Si; 0,009 P; 0,005 S; 0,025 Al.
Взаключение следует отметить, что усвоение ферросплавов при вводе их
враскисленный металл на УКП значительно выше, чем при подаче в ковш во время выпуска плавки. Однако, при этом увеличивается продолжительность обработки металла на УКП и удельный расход электроэнергии. Поэтому вопрос о количестве ферросплавов, которое целесообразно вводить в металл в ходе об-
работки на УКП, в каждом конкретном случае требует дополнительного анали-
64
за.
4.3 Шлаковый режим установок ковш-печь
Доводку металла на УКП обычно ведут под высокоосновными шлаками с минимальным содержанием оксидов железа и марганца, которые обеспечивают эффективную десульфурацию металла. Кроме того, для повышения стойкости футеровки ковша в области шлакового пояса желательно наличие в шлаке 5 – 10% оксида магния.
Обработку раскисленной алюминием стали рекомендуют вести под шла-
ком состава, % мас.:
|
CaO |
SiO2 |
MgO |
Al2O3 |
FeO |
MnO |
|
|
58 – 62 |
8 – 10 |
6 – 8 |
20 – 25 < 0,5 |
0,13 – 0,15 |
|
|
Для обработки стали, раскисленной только кремнием, рекомендуют шла- |
|||||||
ки состава, % мас.: |
|
|
|
|
|
|
|
CaO |
SiO2 |
MgO |
|
Al2O3 |
FeO |
MnO |
CaF2 |
58 – 62 |
8 – 10 |
6 – 8 |
|
5 – 8 |
< 0,5 0,13 – 0,15 |
5 – 10 |
Обычно рекомендуется и на многих металлургических предприятиях ис-
пользуется визуальная оценка качества ковшевого шлака. С этой целью тонкий слой шлака намораживается на кислородную трубку или пруток и после осты-
вания осматривается. Шлак может быть черного, коричневого, серого, зеленого,
желтого или белого цвета с промежуточными оттенками. Цвет шлака характе-
ризует следующее:
∙черный – суммарное содержание FeO и MnO в шлаке более 2%;
∙от серого до коричневого – суммарное содержание FeO и MnO 1,0 – 2,0%;
∙зеленый – повышенное содержание Cr2O3;
∙от белого до серого – суммарное содержание FeO и MnO менее 1,0%;
∙светло-синий с белизной – высокое содержание Al2O3.
Хорошо раскисленный высокоосновной шлак должен иметь светло-
серый, желтый или, желательно, белый цвет, иметь матовую шероховатую по-