
SPR / Лекция_5
.pdf68
5 ВНЕПЕЧНАЯ ОБРАБОТКА СТАЛИ С ХИМИЧЕСКИМ НАГРЕВОМ В КОВШЕ
Для химического нагрева стали в ковше используется тепло экзотермиче-
ских реакций окисления растворенных в металле элементов газообразным ки-
слородом. Ниже приведены расчетные значения изменения температуры метал-
ла при окислении различных элементов в количестве 0,1%, oC:
Al |
C |
Cr |
Fe |
Mn |
Si |
+ 34 |
+ 11 |
+ 14 |
+ 5 |
+ 7 |
+ 33 |
Максимальное расчетное значение повышения температуры металла
+34оС достигается при окислении газообразным кислородом растворенного в металле алюминия. Реальное повышение температуры металла должно опреде-
ляться с учетом потерь тепла, обусловленных излучением и нагревом футеров-
ки ковша.
Аналогичное повышение температуры металла может быть достигнуто при окислении кремния. Однако, SiO2 более агрессивен по отношению к футе-
ровке ковша, чем Al2O3. Кроме того, передув при нагреве металла путем окис-
ления кремния может привести к нежелательному образованию большого ко-
личества СО, высокая температура горения которого снижает стойкость обору-
дования. При нагреве путем окисления алюминия кипение металла не наблюда-
ется. Неметаллические включения с высоким содержанием Al2O3 плохо смачи-
ваются металлом, поэтому при перемешивании скорость их удаления значи-
тельно выше, чем включений с высоким содержанием SiO2. Поэтому химиче-
ский нагрев металла предпочтительно вести с использованием алюминия.
5.1 Процесс CAS-OB
Схема разработанного фирмой «Ниппон стил Корпорэйшн» (Япония)
процесса CAS-OB (Composition Adjustment by Sealed Argon Bubbling – Oxygen
Blowing) показана на рисунке 5.1.

69
Рисунок 5.1 – Схема процесса CAS-OB
Обработка металла проводится в ковшах, оборудованных шиберными за-
творами и пористой пробкой для продувки металла аргоном.
Оборудование для реализации процесса состоит из колокола, закреплен-
ного на подвижной консоли. К верхней части колокола присоединен патрубок,
который служит для подачи внутрь колокола ферросплавов и отвода отходящих газов в систему газоочистки. Конструкция патрубка позволяет также опускать внутрь колокола манипуляторы для отбора проб, измерения температуры ме-
талла и активности растворенного в нем кислорода, кислородную фурму для химического нагрева металла, а также фурму для инжектирования в металл по-
рошкообразных десульфураторов и CaSi.
Колокол состоит из двух частей. Верхнюю его часть футеруют только из-
нутри, нижнюю – изнутри и снаружи. Футеровку колокола обычно выполняют наливной из высокоглиноземистых масс, усиленных 2% игл из нержавеющей стали. Эти же материалы применяют для футеровки кислородной фурмы и фурмы для продувки металла аргоном, которая применяется, когда не удается подать его в металл через пористую пробку.
Срок службы футеровки верхней части колокола составляет 400 – 600
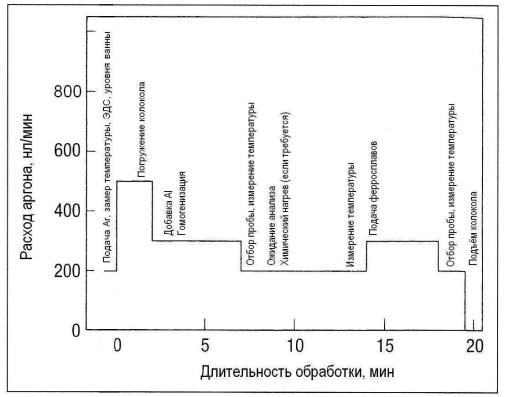
70
плавок, нижней части колокола – 50 – 150 плавок, кислородной фурмы – 100
мин., фурмы для продувки металла аргоном – 150 мин.
Сообщается также об успешном использовании для футеровки нижней части колокола хромомагнезитового кирпича.
В качестве примера рассмотрим последовательность технологических операций при обработке металла в 105-т ковше (рисунок 5.2).
Рисунок 5.2 – Организация процесса CAS-OB
После доставки ковша на позицию обработки начинают продувку металла аргоном через пористую пробку в днище ковша и визуально контролируют на-
личие продувки. Одновременно измеряют высоту свободного борта ковша и рассчитывают перемещение колокола, нижний торец которого должен погру-
жаться в металл на 200 мм, измеряют температуру металла и активность рас-
творенного в нем кислорода.
Перед погружением колокола расход аргона увеличивают до 500 нл/мин.
При этом поверхность металла в зоне пятна продувки оголяется. На свободную от шлака поверхность металла опускают колокол и, после погружения его в
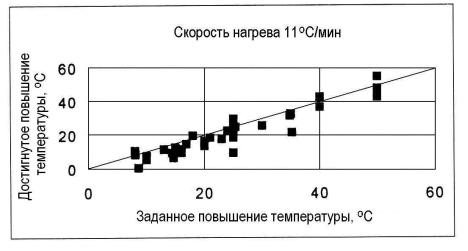
71
расплав на требуемую глубину, расход аргона уменьшают до 300 нл/мин.
На свободную от шлака поверхность металла внутри колокола подают необходимое для раскисления металла количество гранулированного алюми-
ния, после чего в течение 4 – 5 минут проводят гомогенизацию металла. После этого расход аргона уменьшают до 200 нл/мин, отбирают пробу и измеряют температуру металла.
По результатам замера температуры рассчитывают необходимое для хи-
мического нагрева металла количество алюминия и расход кислорода, удель-
ные расходы которых при расчетной скорости нагрева 11оС/мин. составляют соответственно 0,03 кг/(т·оС) и 0,025 нм3/(т·оС).
Нагрев металла обычно совмещают с ожиданием результатов химическо-
го анализа. В ходе нагрева одновременно с вдуванием кислорода внутрь коло-
кола непрерывно подают гранулированный алюминий. Фактическая скорость нагрева металла составляет 10оС/мин., что несколько ниже расчетной. Это от-
личие обусловлено потерей тепла металлом в промежутках между замерами температуры.
Сведения о точности управления температурой металла при химическом нагреве представлены на рисунке 5.3.
Рисунок 5.3 – Точность управления температурой металла в процессе CAS-OB
Сообщается, что повышение температуры металла на 90оС и более не вы-
зывает затруднений. Однако, для повышения стойкости футеровки колокола

72
нагрев металла рекомендуется вести поэтапно, увеличивая температуру в каж-
дом из периодов нагрева не более чем на 30оС. При образовании большого ко-
личества Al2O3 в ковш вводят дополнительное количество извести.
По окончанию нагрева измеряют температуру металла. После получения результатов анализа расход аргона увеличивают до 300 нл/мин и вводят на по-
верхность металла внутри колокола корректирующие присадки ферросплавов.
После подачи ферросплавов в течение 5 минут проводят гомогенизацию рас-
плава.
По окончанию гомогенизации расход аргона уменьшают до 200 нл/мин,
отбирают пробу и измеряют температуру металла. Если на основании результа-
тов замера установлено, что дополнительная корректировка температуры ме-
талла не требуется, подачу аргона прекращают и поднимают колокол.
Основные технические характеристики установок CAS-OB и УКП пред-
ставлены для сравнения в таблице 5.1.
Таблица 5.1 – Технические характеристики установок CAS-OB и УКП
Характеристики |
CAS-OB |
УКП |
|
|
|
Способ нагрева |
Продувка кислородом |
Используется тепло |
|
при атмосферном давле- |
электрической дуги |
|
нии |
|
Свободный борт ковша |
0,3 м |
0,5 м |
Футеровка |
Нет специальных требо- |
Использование MgO-C |
|
ваний |
огнеупоров в области |
|
|
шлакового пояса |
Верхняя часть ковша |
Нет специальных требо- |
Должна быть чистой |
|
ваний |
чтобы не создавать по- |
|
|
мех перемещению крыш- |
|
|
ки |
Затраты на нагрев |
0,030 кг Al/(т·оС) |
0,5 кВт·ч/(т·оС) |
|
0,025 нм3 O2/(т·оС) |
0,01 кг электродов/кВт·ч |
Скорость нагрева |
8 – 15 оС/мин |
3 – 5 оС/мин |
Масса шлака |
Увеличивается |
Не изменяется |
Десульфурация |
Продувкой порошками |
Ковшевым шлаком |
|
|
|
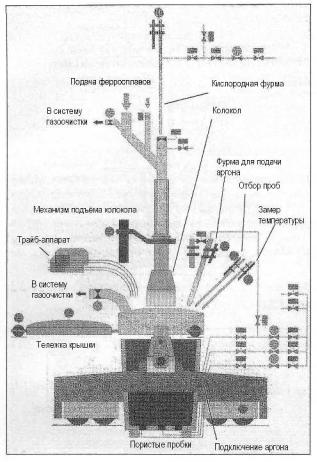
73
5.2 Процесс HALT
Схема процесса HALT (Heating Advanced Ladle Treatment) представлена на рисунке 5.4.
Рисунок 5.4 – Схема процесса HALT
Способ нагрева металла в процессе HALT сходен с тем, который исполь-
зуется в процессе CAS-OB. Однако технологические возможности установок
HALT значительно выше, предусмотрена возможность подачи в ковш шлако-
образующих и десульфурации металла ковшевым шлаком, ввода порошковой проволоки и др.
5.3 Процесс IR-UT
Процесс IR-UT (Injection Refining Up-Temperature) разработан фирмой
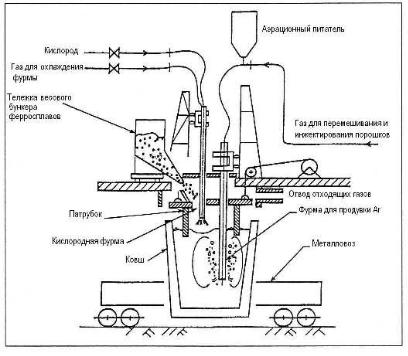
74
«Самитомо метал индастриз» (Япония). Он реализуется при помощи простого оборудования, которое можно разместить на существующих УДМ. Схема про-
цесса представлена на рисунке 5.5.
Рисунок 5.5 – Схема процесса IR-UT
Для продувки металла аргоном вместо пористой пробки используют фурму. При этом особое внимание следует уделять тому, чтобы поток всплы-
вающих пузырей аргона не выходил за пределы погружаемого в металл патруб-
ка.
Нагрев металла ведут путем продувки кислородом через опускаемую сверху внутрь патрубка кислородную фурму с одновременной подачей алюми-
ния. Сообщается, что эта технология обеспечивает несколько меньшую ско-
рость нагрева, чем процессы CAS-OB и HALT.
5.4 Процесс REHeating
Схема разработанного на «Безлехем стил» (США) процесса REHeating (Reactive Element Heating), реализация которого на существующих УДМ требу-
ет минимальных капитальных вложений, показана на рисунке 5.6.
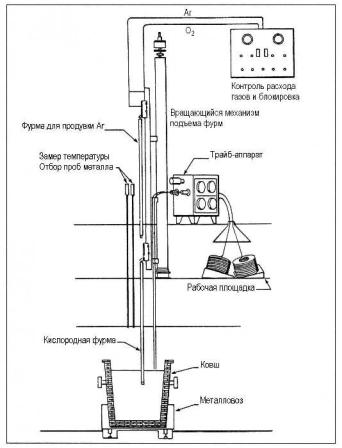
75
Рисунок 5.6 – Схема процесса REHeating
При использовании этого способа продувку металла кислородом ведут в открытом ковше с одновременным вводом алюминиевой проволоки. При этом скорость нагрева составляет 5,6оС/мин (10оF/мин).