
Yang Fluidization, Solids Handling, and Processing
.pdfFluidized Bed Scale-up |
65 |
Table 5. Scale Model of 10 Atm Commercial Hot Bed Using the Simplified Scaling Relationships
Commercial Beds |
Particle Diameter of Model with |
||
|
|
Bed Linear Scale Factor |
|
|
|
|
|
dp |
umf |
Lm/Lc = 1/4 |
Lm/Lc = 1/9 |
40 mm |
7.44 × 10-4 m/s |
31 mm |
25 mm |
|
|
|
|
60 |
1.67 × 10-3 |
46 |
38 |
|
|
|
|
100 |
4.65 × 10-3 |
78 |
63 |
|
|
|
|
200 |
1.85 × 10-2 |
155 |
126 |
|
|
|
|
400 |
7.18 × 10-2 |
310 |
250 |
|
|
|
|
1000 |
0.329 |
610 |
550 |
|
|
|
|
|
|
|
|
Commercial Bed: T = 800oC, P = 10 atm, ρs = 2500 kg/m3, gas:air Model Bed: ρs = 896 kg/m3, gas:air at STP
8.0EXPERIMENTAL VERIFICATION OF SCALING LAWS FOR BUBBLING BEDS
8.1Hydrodynamic Scaling of Bubbling Beds
Experiments using scaled models of bubbling beds have been carried out since 1980 using the scaling relationships presented in previous sections. The earliest work was concerned with experimental testing and verification of the scaling relationships. Hot bed behavior was compared to cold scaled models in several studies. In others, cold beds of different sizes were compared to each other. For bubbling beds, verification of the scaling relationships needs to include direct or indirect measurements of bubble characteristics. Since bubbles are the prime motive agents for both gas and solids displacement, a detailed verification should involve comparison of bubble properties throughout the large bed and the
66 Fluidization, Solids Handling, and Processing
scale model. This is preferable to comparison of overall performance parameters for a bed based solely on input and exhaust measurements.
For beds fluidized with air at ambient conditions, a number of direct techniques to measure or infer bubble properties exist including local capacitance probes, light reflection, light transmission, videos of bed walls and even computer tomographic techniques. These local methods are difficult, if not impossible to use in a high temperature reactor or combustor. Alternatively, many investigators have used pressure fluctuations to infer bubble characteristics. Lirag and Littman (1971) used statistical analysis of pressure fluctuations to estimate the average size of bubbles leaving a bubbling bed. Fan et al. (1981) concluded that bubble motion and coalescence are responsible for pressure fluctuations in fluidized beds. They also found that the amplitude of the pressure fluctuations is related to bubble size. Therefore, pressure fluctuation measurements, when properly made, have been shown to reflect bed hydrodynamics. For local bed behavior, the differential pressure measurements should be made over a modest bed level rather than using a single pressure tap in the bed with the other tap in the freeboard. Differential pressure measurements reflect local conditions. Roy and Davidson (1989) found that the maximum pressure difference between two closely spaced pressure taps is related to the bubble diameter at that level in the bed. Use of a single bed pressure point can be difficult to interpret since pressure fluctuations can be due to local effects, bubbles erupting at the bed surface, or even fluctuations in the supply system. Roy and Davidson found that pressure fluctuations measured using a single pressure point are primarily due to surface bubbles. They also concluded that the dominant frequency and amplitude measured at a single pressure point are independent of position in the bed. Due to the existence of pressure waves from many locations in a gas fluidized bed, Bi, Grace and Zhu (1995) concluded that absolute probes are not suitable for determining local bubble behavior. Although complete bubble characteristics cannot be determined from differential pressure fluctuations, if the time-resolved differential pressure signal from several locations in a large bed are identical to measurements at corresponding location in the scale model, it is likely that the local characteristics of bubbles are similar.
Table 6 presents the range of scaling parameters for tests undertaken by different investigators to verify the scaling relationships for a bubbling bed.

Table 6. Scaling Parameter Values for Bubbling Fluidized Bed Experimental Studies
up-Scale Bed Fluidized
67
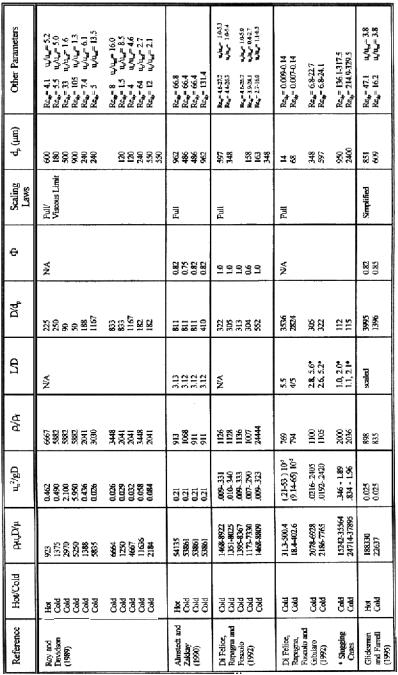
68 Fluidization, Solids Handling, and Processing
Table 6 (cont’d.)
|
N |
"' |
|
|
|
|
..,~ |
|
|
|
|
|
|
|
~~ |
|
|
|
|
|
|
|
|
|
|
|
|
|
|||
|
,., . |
|
|
|
|
~~ |
|
~~~ |
|
|
|
|
|
..;..; |
|
|
,-,C!'D |
.-:,., |
0""!"!1-- |
|
|
|
|
|
|
|
|
|
|
||
|
.'",...;-'D- |
-o~..NN |
|
|
|
|
|
|
|
|
|
|
|
|
|
I |
|
|
|
|
|
|
~~ |
|
~~~ |
|
--r-o |
|
""" |
|
~~ |
|
|
|
|
|
|
|
|
|
-N |
|
|||||
~~~~~~ |
~~~~~ |
|
|
|
|
|
|
|
..r-- |
|
|
|
|||
|
|
|
|
|
|
|
|
|
|
|
-N |
||||
~ |
-:""!,.,a~ |
""!..N |
~~~500 |
|
|
|
|
|
|
§§ |
~~ |
::;;~ |
|
||
|
|
|
~~ |
|
~~~ |
|
00 |
-0-0 |
~N |
|
!O"~ |
||||
.."".'-1-", |
~-..'D- |
|
|
|
|
|
|
||||||||
|
|
|
II II II |
II |
|
|
|
;" |
|
|
|
|
|
|
|
|
~~",{",{",{",{",{ |
",{",{",{",{",{ |
,{,{Ji |
|
|
k} |
|
}kk |
|
ii |
~~i |
ii |
|
"i~ |
|
:g |
|
|
|
|
|
|
|
|
|
|
|
|
|
|
|
-d" |
~~~~~~ |
~~~~~1~~~~1~~ |
|
|
|
~~~1~~ |
~~ |
~~1~~ |
|||||||
|
|
|
|
||||||||||||
.~~ |
II "' ] |
~ |
|
|
|
|
|
|
|
|
|
|
|
|
'B |
|
|
|
|
|
|
|
|
|
|
|
|
|
|
|
!!3 |
] |
~> |
|
|
~ |
|
|
~ |
|
|
|
~ |
|
|
|
I |
|
|
|
|
|
|
|
|
|
|
|
|
||||
e |
|
|
|
|
|
|
|
|
|
|
|
|
|
|
|
|
~ |
|
|
&!~&!&!I |
|
qqq"!q o .q |
|
~ |
|
|
|
~~ |
|||
|
|
|
00001 |
|
|
|
|
0- |
|
|
|
|
,-;,-; |
||
t |
|
|
|
~ ~~~I!:!~;;;~fi!--O N"'..'...N |
|
~~ |
~f;! |
::!=1$~ |
|||||||
|
NNa-",-- |
~~--- |
|
||||||||||||
|
000000... |
|
|
..,..,..,..,on |
|
|
|||||||||
|
~Qoo~:2 |
""":2~~ |
|
|
|
NO-Oon |
|
|
|
|
|
|
|
||
§ |
|
|
|
|
|
|
|
|
|
|
|
..*' |
. |
|
|
|
|
|
|
|
|
|
|
|
|
|
-ON |
0- |
|
|
|
|
|
|
"'NNN |
|
|
|
|
|
|
.,.;.,.; |
NN |
|
|
||
|
~ |
|
|
I |
"' |
|
|
~!$ |
~:1 |
,;!;jl |
|
i |
|||
|
|
|
"'..,..,"' |
|
|
|
|
||||||||
|
|
|
|
-:-:-:-: |
|
~ |
|
|
|
|
|
|
|
|
|
~ |
|
|
|
...~-- |
|
|
|
|
|
|
$% ~~ |
88 1 |
|
||
|
r-~~~-o |
|
~--~- |
|
I |
~~~§i |
|
|
|
~"' |
|||||
|
~~"'~~~ |
:1;~~~~ |
1.:-;;;; |
|
|
::::::-"I |
|
|
..-~ |
--~"' |
|
|
~:;1 |
||
~ |
|
|
|
|
|
|
|
|
|
|
~~ |
~~ |
~~ |
|
|
|
|
|
|
|
|
;;;g~~~ |
|
~"' |
"i"i |
.. |
|
|
|||
|
|
|
|
|
|
..,~..,~.., |
|
|
|
|
|
|
|||
..,.. |
~~§~~~ |
~~88~ |
'i 'i |
'i |
'i |
|
|
|
|
~~ |
§~ |
~~ |
|
BB |
|
|
~@§~~ |
|
|
||||||||||||
|
ooN.';oo |
00000 |
,."."."., |
|
|
|
--"~ |
|
|
|
dd |
||||
:I. |
|
|
|
...~~~~,--- |
|
|
|
|
|
|
..-0 |
1 :2 |
~~ |
|
|
~ |
|
|
|
|
I~ |
~~~;;;:5:~ |
i |
~~ |
~ |
~~ I 8!a |
|||||
|
|
|
~..,..,.., |
|
|
..,..,- |
|
||||||||
|
~§~~~~ |
~~~~~ |
|
|
|
;;:~ |
~ |
~~ |
|
~~ |
|||||
|
,...,..., |
|
|
|
|
|
|
||||||||
"0 |
|
|
|
|
|
|
|
|
|
|
|
|
|
|
|
~ |
|
|
|
|
|
|
"0"0"0"0"0 |
|
"""" |
"""" |
"""" |
I |
;1:8~"" |
||
|
|
|
~~~~ |
|
|
RRRa~ |
|
|
888888 |
|
|||||
|
|
|
|
|
|
|
|
|
|
|
|
|
|||
|
|
|
|
] |
|
|
!f ] |
|
|
~ J ]]~ |
j~ |
|
|
||
~ |
i~~ |
|
|
|
|
|
|
|
|
||||||
|
|
|
|
~ |
i |
1~o~ |
|
|
|
||||||
|
|
|
|
|
|
|
|
|
|
|
|
|
|||
~ |
2:~~, |
|
I!~ |
|
|
15 |
'"'~ |
|
|
|
|
|
Fluidized Bed Scale-up |
69 |
8.2Verification of Scaling Relationships for Bubbling and Slugging Beds
Most early experiments devoted to verifying the scaling relationships have dealt with the full set of scaling relationships. Several more recent experiments have dealt with a reduced set of dimensionless parameters. In some experiments, additional scaling parameters were unintentionally matched.
Fitzgerald and Crane (1980) were one of the first to evaluate the full set of hydrodynamic scaling parameters. They compared the hydrodynamics of two scaled beds using pressure fluctuation measurements and movies. In one bed, cork particles were fluidized with air; the other bed used sand fluidized with pressurized refrigerant 12 vapor. Movies showed qualitative agreement between bubble growth and the solids flow in the beds. The ratio of the bed minimum fluidization velocities was within 20% of the theoretical value; the difference was attributed to the angular shape of the cork particles, φS was not matched between the beds. The fast Fourier transform of the pressure fluctuations was used to determine the average frequency of the fluctuations which should be related to the bubble frequencies. The ratio of average frequencies for the two beds was in fair agreement with the theoretical velocity-time scale factor. The pressure fluctuation data were taken with a single bed pressure tap. This may be responsible for the level of agreement in the frequency ratios. Some additional qualitative slugging comparisons were made using movies of bed behavior; the slugs appeared to have the same scaled lengths and velocities.
Fitzgerald et al. (1984) measured pressure fluctuations in an atmospheric fluidized bed combustor and a quarter-scale cold model. The full set of scaling parameters was matched between the beds. The autocorrelation function of the pressure fluctuations was similar for the two beds but not within the 95% confidence levels they had anticipated. The amplitude of the autocorrelation function for the hot combustor was significantly lower than that for the cold model. Also, the experimentally determined time-scaling factor differed from the theoretical value by 24%. They suggested that the differences could be due to electrostatic effects. Particle sphericity and size distribution were not discussed; failure to match these could also have influenced the hydrodynamic similarity of the two beds. Bed pressure fluctuations were measured using a single pressure point which, as discussed previously, may not accurately represent the local hydrodynamics within the bed. Similar results were
70 Fluidization, Solids Handling, and Processing
obtained between two two-dimensional beds: a bed of reacted limestone fluidized with helium and a half-scale bed of copper fluidized with air.
Nicastro and Glicksman (1984) experimentally verified the full set of scaling laws for bubbling fluidized beds. They compared the timeresolved differential pressure measurements from a bubbling fluidized bed combustor and a scaled cold model. Good agreement was obtained between the spectral content and the probability density distribution of the differential pressure fluctuations, indicative of the bubble size distribution, between the hot combustor and the cold model. Figure 29 presents the comparisons. They concluded that hydrodynamic similarity had been achieved between the hot combustor and the cold model. The solid-to-gas density ratio, which was not matched exactly in the comparison, differed by 23%, but the Reynolds number based on particle diameter (Redp) was approximately 5, suggesting the beds were operating in the viscous limit. At low particle Reynolds numbers, viscous forces are more important than fluid inertial forces making the density ratio a less important scaling parameter. When actual hot bed material was used in the cold model, a violation of the scaling laws, the model’s behavior was very different from that of the hot bed.
Horio et al. (1986a) used three geometrically similar bubbling beds, fluidized with ambient air, to verify their proposed scaling laws. This has been shown by Glicksman (1988) to be equivalent to the viscous limit scaling laws, Eq. (66). The solid-to-gas density ratio was not varied in the experiments although it was not one of the proposed scaling parameters. By maintaining a constant density ratio, they, in essence, used the simplified set of scaling parameters, Eq. (53). Video analysis of bubble eruptions at the bed surface were used to determine the crosssectional average bubble diameter, bubble diameter distribution, and radial distribution of superficial bubble velocity. Similarity was achieved in these hydrodynamic parameters when bed Froude number, density ratio, and the ratio of superficial to minimum fluidization velocities were matched.
Horio et al. (1986b) verified the bubbling bed scaling laws of Horio et al. (1986a) for solid mixing and segregation. Sand was used as a bed material in straight and tapered bed geometries. A bed sectioning technique was used to measure the transient radial dispersion coefficient and the distribution of float tracers. They concluded that bed mixing and the behavior of floating bodies obey the scaling laws in both straight and tapered beds. The solid-to-gas density ratio was again held constant in the tests, satisfying the simplified set of scaling laws. The particle Reynolds numbers (Redp) were approximately unity or less.



