
Yang Fluidization, Solids Handling, and Processing
.pdf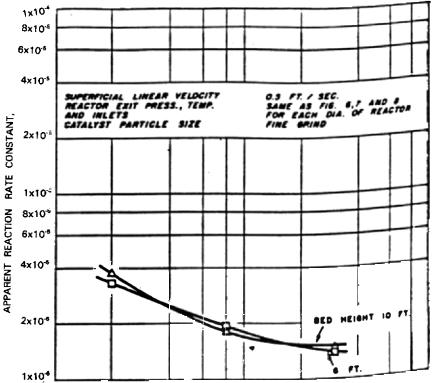
6 Fluidization, Solids Handling, and Processing
May (1959) reports results of tests done in cold models used to simulate the flow through large reactors whose performance had been found to be inferior to that of smaller pilot units. The importance of this problem can be appreciated from the scale of the equipment used. Figure 2 shows the 5 foot diameter unit used for the scale-up tests. This unit was fluidized with compressed air at 27 to 38°C (80 to 100°F) and pressures up to 689 KPa (100 psi). Gas residence time in the bed was determined by the use of tracer gas. Radioactive solid tracers were introduced into the bed to determine solid mixing. The data obtained in the larger units are much more erratic with evidence of large scale mixing patterns. Figure 3 shows the axial mixing coefficients obtained in experiments with different size beds. Mixing in the larger diameter bed is an order of magnitude larger than that in a small laboratory unit. The measured hydrodynamic behavior of the gas and solid was combined with a reaction model to predict the reactor behavior. Here again, there should be concern about the accuracy with the air experiments done at ambient temperature. Use of identical bed geometry and bed solid material does not guarantee identical hydrodynamics. The shift in gas properties from the cold model to the hot reactor may cause a marked difference in behavior. Additional scaling parameters must be maintained constant between the reactor and the cold model to insure identical hydrodynamics, and in some cases just to guarantee identical flow regimes!
Volk et al. (1962) show the effect of bed diameter on the conversion of CO in the “Hydrocol” reaction in which hydrogen and carbon dioxide are converted over an iron catalyst to hydrocarbons and oxygenated hydrocarbons in a bubbling or possibly slugging bed. Figure 4 shows the CO conversion. It is seen that the conversion rate is reduced as the reactor diameter increases. Volk used vertical tubes within the reactor to reduce the equivalent diameter of the system, equal to the hydraulic diameter, four times the free cross sectional area divided by the wetted perimeters of all surfaces in the cross section. The performance was found to be correlated by the equivalent diameter. It was also found that bed expansion was correlated with bed diameter. In their process, larger beds were built with internals which kept the equivalent diameter the same as that of smaller units. The large units with internals appeared to give comparable gas-to-solid contacting. The use of vertical internals may not be feasible for a number of reasons, such as tube erosion. The use of the equivalent diameter approach may not be universally valid.



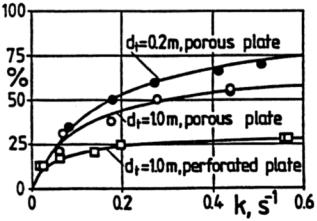
10 Fluidization, Solids Handling, and Processing
Bauer et al. (1981) measured the influence of bed diameter on the catalytic decomposition of ozone. Figure 6 shows the decrease of the conversion with bed diameter for Bauer’s data. This figure also shows the influence of distributor design on conversion. In many small scale experiments, a porous plate is used which will give better performance than the distributors used in large shallow bed commercial designs.
Avidan and Edwards (1986) successfully scaled up from bench scale to demonstration plant from 0.04 m to 0.6 m diameter while maintaining nearly 100% conversion for a fluid bed methanol to gasoline process. In this case, they ran at a superficial gas velocity which was high enough to be in the turbulent flow regime suppressing bubbles. By this technique they eliminated the losses associated with gas bypassing in bubbles.
Figure 6. Conversion catalytic decomposition of ozone for different bed diameters and distributors. (From Werther, 1992.)
3.0INFLUENCE OF BED DIAMETER ON HYDRODYNAMICS
3.1Bubbling Beds
In the studies mentioned above, the major objective was the experimental determination of conversion as a function of overall design



