
Yang Fluidization, Solids Handling, and Processing
.pdfPressure and Temperature Effects 115
Generally, correlations predict the effects of temperature and pressure on Umf well. One of the more widely-used correlations to predict Umf is the Wen and Yu Correlation (Wen and Yu, 1966). The simplified form of the Wen and Yu correlation is:
Eq. (1) |
Ar = 1650 Re |
+ 24.5 (Re )2 |
|
p,mf |
p,mf |
The first term in this equation is important if laminar, or viscous, flow predominates in a system, while the second term is important if turbulent, or inertial, flow predominates. Equation (1) can be rearranged to the form shown in Eq. (2). This form expresses Umf in terms of known system parameters.
|
|
μ |
é(33.7)2 |
+ 0.0408d |
3 |
ρ |
g |
(ρ |
p |
- ρ )g ù0.5 |
||
|
= |
ê |
|
|
p |
|
|
g |
ú |
|||
Eq. (2) |
Umf |
ρg dp |
ê |
|
μ 2 |
|
|
|
|
|
|
ú |
|
|
|
ë |
|
|
|
|
|
|
|
û |
The effect of temperature and pressure on Umf is strongly influenced by particle size. For small particles (Rep,mf < 20), the simplified Wen and Yu Equation reduces to:
|
|
d |
2 |
(ρ −ρ )g |
|
|
|
Eq. (3) |
U = |
|
p |
p g |
Re |
p,mf |
< 20 |
|
|
1650μ |
|||||
|
mf |
|
|
|
For large particles (Rep,mf > 1000), Eq. (1) becomes:
|
U mf2 |
= |
d p (ρ p −ρg |
)g |
|
|
|
Eq. (4) |
|
|
Re |
|
> 1000 |
||
24.5ρg |
|
p, mf |
|||||
|
|
|
|
|
|
||
|
|
|
|
|
|
|
Because gas viscosity does not vary significantly with pressure, the only parameter in Eq. (3) which changes with pressure is the gas density. However, because ρp for most materials is so much larger than ρg even at elevated pressures, the term (ρp - ρg) essentially does not change with pressure. Therefore, for small particles, Eq. (3) predicts that Umf will not change with pressure, and agrees with experimental findings.
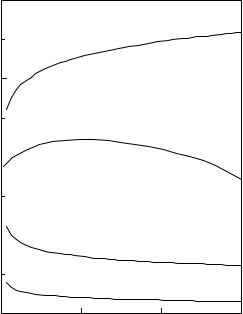
116 Fluidization, Solids Handling, and Processing
In Eq. (4), the only term which is influenced by pressure is ρg, because (ρp - ρg) does not change with pressure. For large particles, the Wen and Yu Equation predicts that Umf should vary as (1/ρg)0.5. Therefore, Umf should decrease with pressure for large particles. This is also what is observed experimentally.
The variation of Umf with temperature is also strongly affected by particle size. For large particles, Eq. (4) predicts that Umf will vary as (1/ρg)0.5. Because temperature causes ρg to decrease, Umf should increase with temperature for large particles. For small particles, Eq. (3) shows that Umf should vary as 1/μ. Therefore, Umf should decrease with temperature for small particles, where viscous effects predominate. Calculated Umf versus temperature curves obtained from the Wen and Yu Equation are shown in Fig. 2 for several different particle sizes. As indicated above, the Wen and Yu Equation predicts that Umf increases with increasing temperature for large particles (where turbulent effects dominate), and decreases with increasing temperature for small particles (when viscous effects dominate).
|
2 |
|
|
|
|
|
Material: Sand |
|
|
|
|
Pressure: 0.1 Bar Gauge |
|
|
|
|
|
|
3000 microns |
m/s |
1.5 |
|
|
|
Velocity, |
|
|
|
|
Minimum Fluidization |
1 |
|
|
|
|
|
|
2000 microns |
|
0.5 |
|
|
|
|
|
|
|
|
|
|
|
|
|
1000 microns |
|
|
|
|
500 microns |
|
0 |
|
|
|
|
0 |
400 |
800 |
1200 |
o
Temperature, C
Figure 2. The effect of temperature on minimum fluidization velocity.(Wen & Yu.)

Pressure and Temperature Effects 117
The predicted effects of temperature on Umf were experimentally observed by Botterill and Teoman (1980) as shown in Fig. 3. For sand particles 462 microns in diameter, they observed that Umf decreased with temperature. For larger material (2320 microns) in the “transition” region in Fig. 2 (where Umf changes from increasing with temperature to decreasing with temperature), they observed an initial increase in Umf with temperature at low temperatures, which was followed by a decrease in Umf as increasing temperature caused viscous effects to become dominant.
|
250 |
|
|
|
|
|
mm/s |
|
|
Material: Sand |
|
|
|
200 |
|
Particle Size: |
462 microns |
|
|
|
Velocity, |
|
|
|
|||
150 |
|
|
|
|
|
|
Fluidization |
|
|
|
|
|
|
100 |
|
|
|
|
|
|
|
|
|
|
|
|
|
Minimum |
50 |
|
|
|
|
|
|
|
|
|
|
|
|
|
0 |
|
|
|
|
|
|
0 |
200 |
400 |
600 |
800 |
1000 |
Bed Temperature, o C
|
1200 |
|
|
|
|
|
mm/s |
|
|
|
|
|
|
Velocity, |
1100 |
|
|
|
|
|
|
|
|
|
|
|
|
Fluidization |
1000 |
|
Material: Sand |
|
|
|
|
|
Particle Size: |
2320 microns |
|
|
|
Minimum |
|
|
|
|
||
|
|
|
|
|
|
|
|
900 |
|
|
|
|
|
|
0 |
200 |
400 |
600 |
800 |
1000 |
Bed Temperature, o C
Figure 3. The effect of temperature on the minimum fluidization velocity. (Botterill
and Teoman.)
118 Fluidization, Solids Handling, and Processing
Temperature can also affect fluidized beds if it causes the particles to sinter or become sticky. Siegell (1984) has shown that above a certain critical temperature, the fluidizing gas velocity must be increased above the minimum fluidization velocity in order to maintain fluidization in the bed. Siegell reported that the increase in velocity required to maintain fluidization was linearly proportional to the temperature increase. Increasing bed L/D, and smaller particle sizes, increased the tendency to agglomerate.
Compo (1987) also investigated the effect of temperature on the velocity required to prevent defluidization for (i) materials which agglomerated rapidly after their sintering temperature (Ts) was reached (coal, plastics, etc.), and (ii) materials which agglomerated slowly after reaching Ts (calcium chloride, etc.) For the rapidly agglomerating materials, the gas velocity had to be increased rapidly to prevent defluidization after Ts was reached. For the weakly agglomerating materials, a much smaller increase in gas velocity was required to prevent defluidization after Ts was reached.
Although the trends of varying temperature and pressure can be predicted by minimum fluidization velocity correlations, sometimes the absolute values of the predictions are significantly in error. Frequently, the primary cause of uncertainty is in determining a representative value for the average particle size to use in the Umf correlation. One technique which can be used to improve upon the accuracy of the prediction of Umf, is to first determine Umf experimentally at ambient conditions. Then, using this experimentally-obtained value for Umf, back-calculate an effective particle size from the correlation. Using this effective particle size, then calculate Umf at actual conditions. This technique can predict Umf more accurately than by using a correlation alone. It substitutes an effective value for the shape factor and the average particle size. However, it does not account for changes in voidage which might occur with changes in temperature and pressure.
Yang et al. (1985) proposed another method of determining Umf at elevated temperature and pressure. As with the procedure described above, Umf is first determined experimentally at ambient conditions. This data point is then located on a curve of constant εmf on a plot of
[(Re )ε2 (C D )ε ]1mf/ 3 vs. [(Re )ε /(C D )ε ]1mf/ 3
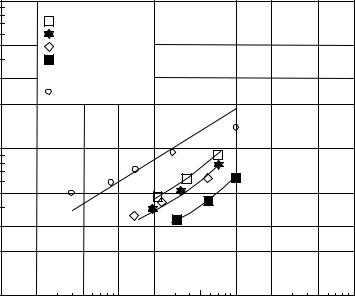
Pressure and Temperature Effects 119
where Reε and CDε are Reynolds number and drag coefficients, respectively, modified by Barnea and Mizrahi (1973) to apply to multiparticle systems. This technique produced estimates of Umf which agreed extremely well with experimental Umf data taken at pressures up to 6300 kPa. It also predicted the experimental data of Yoshida et al., (1976) and Mii et al., (1973) obtained at temperatures up to 850°C (Fig. 4). Shrivastava et al. (1986) applied this technique to the data of Saxena and Vogel (1977) also with excellent results.
|
100 |
Yoshida et al. (1976) |
|
|
|
|
|
|
|
|
|
|
|
|||
|
|
|
|
|
|
|
|
|
|
|
|
|
||||
|
|
|
Catalyst |
214 |
μ m |
|
|
|
|
|
|
|
|
|
|
|
|
|
|
Sand |
151 |
μ m |
|
|
|
|
|
|
|
|
|
|
|
|
50 |
|
Catalyst |
151 |
μ m |
|
|
|
|
|
|
|
|
|
|
|
|
|
|
Catalyst |
151 |
μ m |
|
|
|
|
|
|
|
|
|
|
|
|
30 |
|
Mii et al. (1973) |
|
|
|
|
|
|
|
|
|
|
|
|
|
|
20 |
|
Graphite 300 |
μ m |
|
|
|
|
|
|
|
|
|
|
|
|
1/3 mf |
|
|
|
|
|
|
|
|
|
|
|
emf = 0.40 |
|
|
||
|
|
|
|
|
|
|
|
|
|
|
|
|
|
|||
] |
|
|
|
|
|
|
|
|
|
|
|
|
|
|
|
|
e |
|
|
|
|
|
|
|
|
|
|
|
|
|
|
|
|
) |
|
|
|
|
|
|
|
|
|
|
|
|
|
|
|
|
D |
|
|
|
|
|
|
|
|
|
|
|
|
emf = 0.48 |
|
|
|
(C |
10 |
|
|
|
|
|
|
|
|
|
|
|
|
|
||
|
|
|
|
|
|
|
|
|
|
|
emf = 0.51 |
|
|
|||
2 e |
|
|
|
|
|
|
|
|
|
|
|
|
|
|
||
[(Re) |
|
|
|
|
|
|
|
|
|
|
|
|
|
|
||
|
|
|
|
|
|
|
|
|
|
|
|
|
emf = 0.60 |
|
|
|
5 |
|
|
|
|
|
|
|
|
|
|
|
|
|
|
|
|
|
|
|
|
|
|
|
|
|
|
|
|
|
|
|
|
|
|
3 |
|
|
|
|
|
|
|
|
|
|
|
|
|
|
|
|
2 |
|
|
|
|
|
|
|
|
|
|
|
|
|
|
|
|
1 |
|
|
|
|
|
|
|
|
|
|
|
|
|
|
|
|
0.001 |
0.002 |
0.005 |
0.01 |
0.02 |
|
0.05 |
0.1 |
0.2 |
0.5 |
1 |
|||||
|
|
|
|
|
[(Re) |
e |
/(C |
) |
e |
] |
1/3 |
|
|
|
|
|
|
|
|
|
|
|
|
|
D |
|
mf |
|
|
|
|
Figure 4. Comparison of data and Yang et al. procedure for Umf determination.
This success of this procedure implies that εmf does not change significantly with temperature and pressure. However, other researchers (see below) have reported that εmf can change substantially with temperature and pressure for Geldart Group A powders. Therefore, the authors caution that this technique may not be accurate for Geldart Group A particles.
120 Fluidization, Solids Handling, and Processing
Abrahamsen and Geldart (1980) defined Group A powders as those in which Umb /Um f > 1, and Group B powders as those where Umb /Umf = 1. They developed the following equation to predict Umb /Umf.:
|
U |
mb |
= |
2300ρg0.126 μ0.523Exp(0.716F ) |
|||
Eq. (5) |
Umf |
d |
0p.8 g |
0.934(ρ p−ρg )0.934 |
|||
|
where F is a weight fraction of 0 to 44 micron particles in the distribution Equation (5) implies that materials may shift from one Geldart Group to another as a consequence of changing system parameters. For
example, if a material is in Group B near the Group B/A boundary and either the gas density and/or the gas viscosity is increased, Umb /Umf will increase and the material can “cross” the boundary into Group A. That this can occur has been demonstrated by experiments performed by Varadi and Grace (1978). They found that Umb /Umf increased from a value of 1 to a value much greater than 1 as system pressure was increased over the range of 1 to 22 atmospheres as shown in Fig. 5. Thus, the material moved from Group B to Group A as a consequence of changing system pressure. Equation (5) predicts that Umb /Umf is more sensitive to gas viscosity than gas density. The data of de Vries et al. (1972) agree with this prediction.
1.2Bed Voidage and Bed Expansion
Voidage in a bubbling fluidized bed is also affected by temperature and pressure. Botterill et al. (1982) reported for Group B materials, that the Wen and Yu Equation generally over-predicts the reduction of Umf with temperature. They found that the overprediction was due to the increase in voidage at minimum fluidization (εmf) with increasing temperature. For Geldart Group D materials, they found that εmf was insensitive to changes in temperature.
Pressure has been found to cause the dense-phase voidage (εd) to increase for Group A materials. The effect diminishes with increasing particle size, and for large Geldart Group B and Group D materials, εd is insensitive to pressure. Weimer and Quarderer (1983) in their highpressure experiments, found that over a pressure range of 8 to 69 bar, εd for


122 Fluidization, Solids Handling, and Processing
|
0.9 |
Particle Size, microns |
|
|
|
|
|
|
|
|
|
|
|
|
|
66 |
|
|
|
|
|
0.8 |
108 |
|
|
|
|
|
|
177 |
|
|
|
|
) |
|
|
|
|
|
|
- |
|
|
|
|
|
|
( |
0.7 |
|
|
|
|
|
Voidage, |
|
|
|
|
|
|
|
|
|
Material: Activated Carbon |
|
||
0.6 |
|
|
|
|
|
|
Phase |
|
|
|
|
|
|
|
|
|
|
|
|
|
Dense |
0.5 |
|
|
|
|
|
|
|
|
|
|
|
|
|
0.4 |
|
|
|
|
|
|
0.3 |
|
|
|
|
|
|
0 |
20 |
40 |
60 |
80 |
100 |
Pressure, Bar
Figure 6. The effect of pressure on dense phase voidage. (Weimer & Quarderer.)
Subzwari et al. (1978) also reported that bed voidage and bed expansion increased with pressure for FCC catalyst (a Group A material). However, Knowlton (1977) reported little change in either bed density or bed expansion at Ucf with increasing pressure over the range of 1 to 70 atmospheres for large, -2000/+74 micron material.
The fluidized-bed voidage at minimum bubbling conditions (εmb) also has been shown to increase with increasing temperature (Fig. 7) and increasing pressure (Fig. 8).
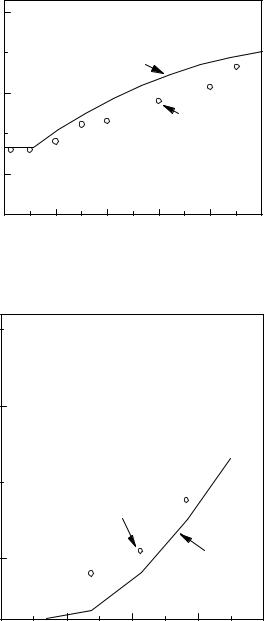
Pressure and Temperature Effects 123
|
0.6 |
Gas: Air |
|
|
|
|
|
|
Material: 103-micron FCC Catalyst |
|
|
||
|
|
|
Foscolo and Gibilaro Model |
|
|
|
mb |
0.5 |
|
|
|
|
|
e |
|
|
|
|
|
|
|
|
|
|
Data |
|
|
|
0.4 |
|
|
|
|
|
|
0 |
200 |
400 |
600 |
800 |
1000 |
|
|
|
|
o |
|
|
|
|
|
Temperature, C |
|
|
Figure 7. The effect of temperature on εmb . (Rapagna et al., 1994; Yates, 1995.)
|
Gas: CF 4 |
|
|
|
|
Material: Synclyst |
|
|
|
0.8 |
|
|
|
|
mb |
|
|
|
|
e |
|
|
|
|
|
|
Data |
|
|
0.7 |
|
|
Foscolo and |
|
|
|
|
Gibilaro Model |
|
0 |
20 |
40 |
60 |
80 |
|
|
Pressure, bar |
|
|
Figure 8. The effect of pressure on εmb . (Crowther & Whitehead, Fluidization,
Davidson and Keairns, eds., 65–70, 1978.)
124 Fluidization, Solids Handling, and Processing
1.3Bubbles in Fluidized Beds
Hydrodynamically, fluidized beds are considered to be stable when they are not bubbling and unstable when they are bubbling. Several researchers (Knowlton, 1977; Hoffman and Yates, 1986; Guedes de Carvalho et al., 1978) have reported that fluidized beds become “smoother” at elevated pressures (i.e., have smaller bubbles) and, therefore, are more stable at high pressures. There are generally two approaches as to what causes instability in fluidized beds. Rietema and co-workers (Rietema et al. 1993) forwarded the theory that the stability of the bed depends on the level of interparticle forces in the bed. However, Foscolo and Gibilaro (1984) have proposed that hydrodynamics determines whether a fluidized bed is stable.
With the Interparticle Force Theory, interparticle forces (van der Waals, etc.) are what cause the bed to be “elastic.” Bed elasticity is characterized by an Elasticity Modulus, Mi. The criterion which determines when the fluidized bed starts to bubble is determined by the relative magnitudes of the two sides of Eq. (7).
|
|
ρp3 dp4 g 2 |
é |
150(1 - ε |
mb |
) ù2 |
|
Eq. (7) |
|
|
= ê |
|
|
ú |
|
2 |
2 |
|
|
||||
|
|
μ Mmb |
ê |
|
|
ú |
|
|
|
ëεmb (2 - 2εmb )û |
|||||
|
If the LHS of Eq. (7) is < the RHS: The bed is STABLE |
||||||
|
If the LHS of Eq. (7) is > the RHS: |
The bed will BUBBLE |
In this theory, increasing pressure causes gas to be absorbed onto the surface of the particles. This results in an increase in Mi, and, by Eq. (7), an increase in the stability of the fluidized bed.
The Hydrodynamic Theory of fluidized bed stability was proposed by Foscolo and Gibilaro who adapted the stability principle of Wallis. They postulated that a fluidized bed is composed of two interpenetrating fluids. One fluid is the gas phase, and the solids phase is also considered as a continuous fluid phase. In this theory, voidage disturbances in the bed propagate as dynamic and kinetic waves. The stability of the fluidized bed depends upon the relative velocities of these two waves. The velocities of the kinetic wave (uε ) and the dynamic wave (ue) are: