
Yang Fluidization, Solids Handling, and Processing
.pdf
Heat Transfer in Fluidized Beds 155
Eq. (1) |
Re mf = [(33 .7 )2 + 0.0408 Ar ]1/2 |
− 33 .7 |
||||
where |
|
|
|
|
|
|
Remf |
= particle Reynolds number at |
|
|
|||
|
Umf = |
umf d p ρ g |
|
|
|
|
|
μ g |
|
|
|
||
|
|
|
|
|
||
Ar (Archimedes number) = |
d 3p ρ g (ρ s − ρ g )g |
|||||
μ g2 |
|
|
By definition, the terminal velocity of a particle (ut) is the superficial gas velocity which suspends an isolated particle without translational mo- tion—i.e., the terminal free fall velocity for that particle. From force balance on the particle, the terminal velocity for an approximately spherical particle can be shown to be
|
|
1 |
||
Eq. (2) |
ut |
= |
4gdp (ρs − ρg ) 2 |
|
3ρg CD |
||||
|
|
|
where CD is the drag coefficient for that particle. The magnitude of CD depends on the particle Reynolds number at the terminal velocity, as given by Fox and McDonald (1992) or other fluid dynamic texts.
2.2Heat Transfer to Submerged Surfaces
General Characteristics. Tubes carrying cooling or heating fluids are often submerged in bubbling fluidized beds to extract or add thermal energy. The effective heat transfer coefficient at the surface of such tubes are of engineering interest and has been the objective of numerous experimental studies. Figure 1 shows representative data measured by Chandran, Chen and Staub (1980) for a horizontal tube submerged in bubbling fluidized bed of spherical glass particles. The heat transfer coefficient is plotted as a function of the gas velocity in excess of the minimum fluidization velocity (ug – umf). Typical characteristics are noted as:
156Fluidization, Solids Handling, and Processing
•Heat transfer coefficient increases steeply as gas velocity exceeds minimum fluidization velocity
•A maximum value of the heat transfer coefficient is attained at some specific velocity which depends on the particle size.
•Beyond the maximum point, the heat transfer coefficient is almost constant, declining slightly as excess velocity increases.
•The absolute magnitude of the heat transfer coefficient is several folds greater than single-phase gas convection at the same superficial velocity.
•The heat transfer coefficient increases with decreasing particle size.
Similar behavior has been reported by other researchers for both vertical and horizontal tubes, though the magnitude of the heat transfer coefficients change with operating conditions, (Mickley and Trilling, 1949; Vreedenberg, 1960; Botterill and Desai, 1972; Ozkaynak and Chen, 1980).
One extra complication for horizontally submerged heat-transfer tubes is the lack of circumferential symmetry, as found in vertically placed tubes. The data in Fig. 1 represents averaged heat transfer coefficients around the entire circumference of the horizontal tube. The experiments of Chandran, Staub and Chen (1980) showed that the local heat transfer coefficients can actually vary significantly at different circumferential positions. The polar plot reproduced in Fig. 2 shows some results for a horizontal tube in a bubbling bed of glass spheres, for three different particle sizes. It is seen that there is substantial variation of the local heat transfer coefficient around the tube circumference. For small particles, the maximum heat transfer coefficient is found at the bottom and sides of the horizontal tube. The heat transfer coefficient at the top of the tube is noticeably smaller, implying the existence of a stagnant cap of solid particles which tends to insulate the heat transfer surface. An increase in particle size caused a decrease in heat transfer coefficients at the side and bottom segments while increasing the heat transfer coefficient at the top of the tube. For the largest particle size, a fairly uniform heat transfer coefficient is obtained, albeit with smaller magnitude when compared to the heat transfer coefficient for smaller particles. Similar observations have been made by Berg and Baskakov (1974), Gelperin et al., (1968, 1971) and Saxena et al. (1978). Evidently the nature of particle-surface contact and the subsequent heat transfer mechanism is different for different circumferential positions around the horizontal tube, and varies with gas flow rate.

158 Fluidization, Solids Handling, and Processing
Most practical cases involve multi-rows of tubes, which can affect bed side heat transfer coefficient by altering the dynamic behavior of the fluidized medium. Wood et al. (1978) showed that presence of a horizontal tube bank can suppress slugging by breaking up the bubbles. The bed becomes more uniform as compared to a similar bed without a tube bank. As a consequence, heat transfer coefficients may decrease up to 20% at gas velocities that correspond to slugging regime. At higher gas flow rates, this effect is reduced due to uniform nature of bubbling with or without tube banks. Tests made at atmospheric pressure further showed that heat transfer coefficients were independent of location (i.e., row or column number in the tube bank). Tamarin et al. (1976) also observed stabilizing effect of horizontal tube banks on bed side heat transfer coefficients. For vertically placed tube banks, however, Noë and Knudsen (1968) did not observe any change in measured heat transfer coefficients of single or multi tubes.
Parametric Effects. The heat transfer coefficient at submerged surfaces in bubbling fluidized beds is affected by a number of operating parameters. Two of these parametric effects are illustrated by the data of Jacob and Osberg (1957). As seen from Fig. 3, the maximum value of the heat transfer coefficient is significantly affected by the particle size as well as by the thermal conductivity of the fluidizing gas. With a constant gas conductivity, diminishing the particle diameter by an order of magnitude caused 150% increase in the heat transfer coefficient. For a relatively small particle (dp = 0.062 mm), increasing the gas conductivity from 0.05 to 0.2 w/m•k caused an increase of 100% in the maximum heat transfer coefficient.
Since the heat transfer coefficient is known to vary with particle size for fluidized beds of uniformly sized particles, there is a question of how mixtures of different size particles might affect the heat transfer. Biyikli and Chen (1982) measured local and circumferentially-averaged heat transfer coefficients for horizontal tubes immersed in bubbling beds with mixtures of different-sized glass beads. Figure 4a shows the particle size distribution used in their experiments; the weight-mean averaged diameter is given in the legend for each mixture. Figure 4b shows the results, indicating the circumferentially averaged heat transfer coefficient as a function of superficial gas velocity for each mixture. It is seen that the heat transfer coefficient increased continuously as the mean particle size of the mixture decreased. For all mixtures, the qualitative variation of the average
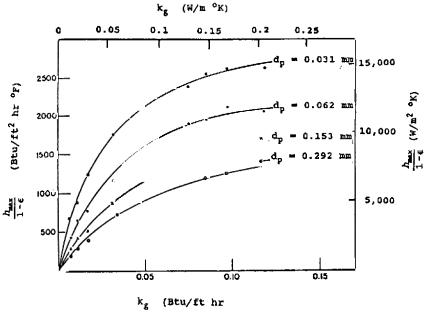

160 Fluidization, Solids Handling, and Processing
(b)
Figure 4. Effect of mixed particle sizes. (a) Particle size distribution. (b) Circumfer- ential-average heat transfer coefficients. (Data of Biyikli and Chen, 1982).
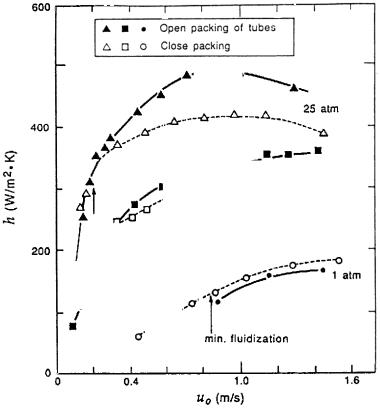
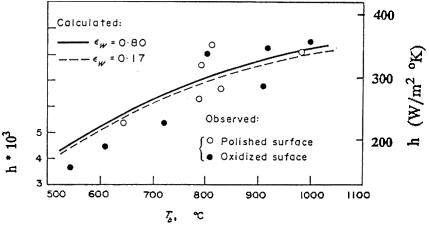
Heat Transfer in Fluidized Beds 163
For relatively shallow fluidized beds (bed depths of less than 0.1 m) it appears that the bed height itself is a parameter that affects the heat transfer coefficient at submerged surfaces. Experiments carried out by Liu et al. (1986) in shallow fluidized beds of 175 μm diameter sand particles showed that the maximum heat transfer coefficient, at optimal gas velocity and tube elevation, increased steeply with bed height, reaching a maximum at a height of approximately 30 mm before declining gradually with further increases in bed height. This parametric effect is significant only for shallow beds and would be of little consequence in most commercial applications which have bed heights greater than 0.5 m.
Models and Correlations. For bubbling dense beds, it is recognized that mechanisms contributing to heat transfer at submerged surfaces include gaseous convection during times of bubble contact, particle conduction/convection during times of solid contact, and radiation in the case of high temperature operation. The effective heat transfer coefficient is often represented as the sum of the coefficients for various contributing mechanisms,
Eq. (3) |
h = fl hl + (1 − fl)hd + hr |
where h = total effective heat transfer coefficient
hl = heat transfer coefficient for “lean” gas phase contact
hd = heat transfer coefficient for “dense” (particle) phase contact
hr = heat transfer coefficient for radiation fl = time fraction of contact by lean phase
This additive representation is itself an assumption—that the various mechanisms can be superimposed, weighted by the time fraction of lean gas contact or dense particle contact at the heat transfer surface. Most researchers concur that for bubbling fluidized beds, the lean/gas convection is relatively unimportant and can often be ignored (Kunii and Levenspiel, 1991; Ozkaynak and Chen, 1980). Most modeling efforts have been focused on the dense/particle phase contribution, (1 - fl ) hd ,or on the total convective contribution [fl hl + (1 - fl ) hd ] = hc . Examination of the literature reveals that the modeling approaches fall into four groups, each
164 Fluidization, Solids Handling, and Processing
emphasizing a particular mechanism for heat transport: (i) transient conduction during short contacts by particle packets, (ii) particle disruption of convective boundary layer, (iii) gaseous convection through interstitial spaces between particles packed at the heat transfer surface, and (iv) energy transport due to random motion of the particles. Each of these approaches are briefly reviewed below.
The first type of model considers the heat transfer surface to be contacted alternately by gas bubbles and packets of closely packed particles. This leads to a surface renewal process whereby heat transfer occurs primarily by transient conduction between the heat transfer surface and the particle packets during their time of residence at the surface. Mickley and Fairbanks (1955) provided the first analysis of this renewal mechanism. Treating the particle packet as a pseudo-homogeneous medium with solid volume fraction, ε s,pa , and thermal conductivity (kpa ), they solved the transient conduction equation to obtain the following expression for the average heat transfer coefficient due to particle packets,
Eq. (4) |
h pa= 2 |
é k pa ρs C ps ε |
s, pa |
ù 1/2 |
||
ê |
|
|
|
ú |
||
π τ pa |
|
|
||||
|
|
ë |
|
|
û |
where τpa is the root-square average residence time for packets on the heat transfer surface, summed over all packets,
Eq. (5) |
é |
Sτ |
ù 2 |
|
τ pa= ê |
ú |
|||
1/2 |
||||
|
ë |
S(τ ) |
û |
Assuming that this packet renewal mechanism accounts for all the heat transfer associated with the particle phase, hpa can be equated to hd in Eq. (3).
This packet renewal model has been widely accepted and in the years since 1955 many researchers have proposed various modifications in attempts to improve the Mickley-Fairbanks representation. Several of these modifications dealt with the details of the thermal transport process between the heat transfer surface and the particle packet. The original Mickley-Fairbanks model treated the packet as a pseudo-homogeneous medium with a constant “effective thermal conductivity,” suggesting that