
Yang Fluidization, Solids Handling, and Processing
.pdf
Pressure and Temperature Effects 145
up along the wall. Employing the circulating fluidized model of Yang (1988), which assumes that the core region is at choking conditions, and the choking-velocity correlation of Punwani et al. (1976), the annulus thickness in a circulating fluidized bed of catalyst was calculated as a function of pressure. The results showed that the annulus thickness should decrease as system pressure was increased (Fig. 24). Karri and Knowlton (1996) measured riser density as a function of radial position at two different pressures and showed that the annulus thickness does decrease as pressure increases (Fig. 25).
System Pressure, bar (gauge)
|
0 |
1 |
2 |
|
3 |
4 |
5 |
|
|
6 |
|
0.8 |
|
|
|
|
|
|
|
|
2 |
|
|
Material: Cracking Catalyst |
|
|
|
|
|
|||
|
|
Size: 76 |
microns |
|
|
|
|
|
|
|
|
|
Density: |
107 |
3 |
|
|
3 |
|
|
|
|
|
lb/ft (1717 kg/m |
) |
|
|
|
||||
|
|
Solids Mass Flux: 30 |
lb/s-ft |
2 |
|
) |
2 |
|
||
|
0.6 |
(147 kg/s m |
|
|
||||||
|
Tube Diameter: |
12 in |
(30 cm) |
|
|
|
|
|||
|
|
|
|
|
cm |
|||||
in |
|
Gas: Air |
|
|
|
|
|
|
|
|
|
|
|
|
|
|
|
|
|
||
Annulus Thickness, |
0.4 |
|
|
|
|
|
|
|
|
1 |
|
|
|
|
|
|
|
|
|
Thickness,Annulus |
|
|
0.2 |
|
|
|
|
|
|
|
|
|
|
0 |
|
|
|
|
|
|
|
|
0 |
|
0 |
20 |
|
40 |
|
60 |
80 |
100 |
System Pressure, psig
Figure 24. Annulus thickness vs system pressure. (Calculated from model of
Yang.)
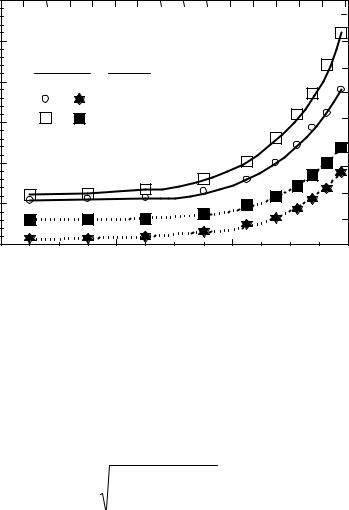
146 Fluidization, Solids Handling, and Processing
Riser Radial Location, cm
|
60 |
0 |
|
5 |
10 |
15 |
|
|
|
Elevation: 3.6 m From Solids Entry |
|
|
3 |
||
3 |
|
Ugs = 4.6 m/s |
Gas: Nitrogen |
|
|
||
50 |
|
800 |
|
||||
|
|
kg/m |
|||||
lb/ft |
Pressure |
G s |
|
||||
|
|
|
|||||
|
|
kPa |
kg/s-m 2 |
|
|
||
Density, |
|
|
|
|
Density, |
||
40 |
138 |
690 |
|
|
600 |
||
|
|
|
|||||
|
|
|
195 |
|
|||
|
|
|
|
|
|||
|
|
|
|
|
|
||
Suspension |
30 |
|
|
390 |
|
|
Suspension |
|
|
|
|
|
|||
|
|
|
|
|
400 |
||
20 |
|
|
|
|
|
||
|
|
|
|
|
|
||
Riser |
10 |
|
|
|
|
200 |
Riser |
|
|
|
|
|
|||
|
|
|
|
|
|
|
|
|
0 |
0 |
|
2 |
4 |
0 |
|
|
|
|
6 |
|
Riser Radial Location, in
Figure 25. The effect of pressure on radial density distribution in a riser.
1.11 Cyclone Efficiency
Rosin et al. (1932) derived a simple expression for cyclone efficiency for a fixed cyclone diameter based on a force balance on the particle at the cyclone inlet, i.e.,
Eq. (17) |
E |
π Ns Ui ( ρ p −ρg ) |
|
9μLw |
|||
|
|
This expression indicates that cyclone efficiency should not change with gas density because (ρp - ρg) is insensitive to changes in pressure. However, cyclone efficiency should decrease with gas viscosity because it is harder for a particle to travel to the cyclone wall in a more viscous fluid.
There have been relatively few literature articles reporting on the observed effects of temperature and pressure on cyclone efficiency.
Pressure and Temperature Effects 147
Parker et al. (1981) conducted tests with a 5 cm diameter cyclone at temperatures up to 700°C with 20 micron fly ash. They found that cyclone efficiencies decreased with temperature as expected. Patterson and Munz (1989) investigated the effect of temperature on cyclone efficiency up to 1700°C in a 10-cm-diameter cyclone, and also found that cyclone efficiency decreased with temperature. However, this effect was only seen at very small particle sizes (below about 12 microns) where cyclones become relatively inefficient.
According to Eq. (17), pressure should have a negligible effect on cyclone efficiency. However, Parker et al. (1981) reported that gas density caused cyclone efficiency to increase over the pressure range of 2 to 13 atmospheres. Knowlton and Bachovchin (1978) varied system pressure up to 50 atmospheres and found that, at low loadings for a conventional cyclone, the efficiency increased with increasing pressure. At higher loadings, the opposite effect was noticed. As with the studies investigating the effect of temperature, the effect of pressure in both studies was only seen at particle sizes less that about 12 microns. Therefore, for particles greater than about 10 to 15 microns, cyclone efficiency seems be insensitive to gas properties.
NOTATIONS
Ar |
= Archimedes number, g dp3 ρg (ρp - ρg)/μ2 |
|||
CD |
= |
Drag Coefficient |
||
(CD)ε |
= |
Modified drag coefficient: |
||
|
|
(CD )ε = CD |
ε3 |
|
|
|
1+ (1− ε)1/3 |
|
|
D |
= |
Tube diameter |
||
do |
= |
Jet nozzle diameter |
||
dp |
= |
Average particle size |
E= Cyclone efficiency
F= Weight fraction of 0–44 micron particles in mixture
148 Fluidization, Solids Handling, and Processing
Fr |
= |
Froude number, U2/gd |
p |
|
|
|
|
Ga |
= |
Galileo number |
|
g= Gravitational constant
h= Overall bed-to-surface heat transfer coefficient
hgc |
= Gas convective heat transfer coefficient |
|
hpc |
= Particle convective heat transfer coefficient |
|
hr |
= Radiant heat transfer coefficient |
|
L |
= |
Jet penetration length |
Lw |
= Width of cyclone inlet |
|
Ns |
= Number of spirals in cyclone |
|
Mi |
= Elasticity modulus for a fluidized bed |
|
Mmb |
= Elasticity modulus at minimum bubbling |
|
n |
= |
Richardson-Zaki exponent |
Remf |
= Reynolds number at minimum fluidization, dp Umf ρg/μ |
|
Rep |
= Particle Reynolds number, dp U ρg/μ |
|
(Re)ε |
= |
Modified Reynolds number: |
|
|
(Re) |
|
é |
|
1 |
ù |
|
|
|
= Re ê |
|
|
ú |
|
|
|
ε |
e exp{5(1- e) / 3e} |
||||
|
|
|
ê |
ú |
|||
|
|
|
|
||||
|
|
|
|
ë |
|
|
û |
Ts |
= |
Sintering temperature |
|
|
|||
U |
= |
Superficial gas velocity |
|
|
|||
Ui |
= Gas inlet velocity to cyclone |
|
|||||
Uj |
= Gas velocity through jet or grid port |
|
|||||
Uc |
= Superficial gas velocity where the transition from bubbling/ |
||||||
|
|
slugging to turbulent fluidization begins |
|
||||
Uch |
= |
Chokingvelocity |
|
|
|
||
Uk |
= Superficial gas velocity where transition region from |
||||||
|
|
bubbling/slugging to turbulent fluidization ends |
|||||
Umb |
= |
Minimum bubbling velocity |
|
|
|
Pressure and Temperature Effects 149 |
Umf |
= |
Minimum fluidization velocity |
Ut |
= |
Terminal velocity |
ε= Voidage
εd |
= |
Dense-phase voidage |
εmb |
= |
Dense-phase voidage at minimum bubbling |
μ= Gas viscosity
ρg |
= |
Gas density |
ρp |
= |
Particle density |
REFERENCES
Abrahamsen, A., and Geldart, D., Powder Technol., 26:35 (1980) Barnea, E. and Mizrahi, J., Chem. Eng. J., 5:171 (1973)
Bader, R., Findlay, J. G., and Knowlton, T. M., Circulating Fluidized Bed Technol. II, (Basu, and Large, eds.), p. 123, Pergamon Press (1988)
Barreto, G. F., Yates, J. G., and Rowe, P. N., Chem. Eng. Sci., 48(12):1935 (1984)
Baskakov, A. P., Berg, B. V., Virr, O. K., Phillippovsky, N. F., Kirakosyan, V. A., Goldobin, J. M., and Suprun, V. M., Powder Technol., 8:273 (1973)
Botterill, J. S. M., Gas Fluidization Technol., (Geldart, ed.), p. 220, J. Wiley & Sons (1986)
Botterill, J. S .M., and Desai, M. Powder Technol. 6:231 (1972)
Botterill, J. S. M., and Teoman, Y. Fluidization, (Grace and Matsen, eds.), pp. 93– 100, Plenum Press, New York (1980)
Botterill, J. S. M., Teoman, Y., and Yuregir, K. R., Powder Technol., 31:101(1982)
Cai, P., Shen, S. P., Jin, Y., Yu, Z. Q., and Wang, Z. W., AIChE Symp. Series, 270(85):37–43 (1989)
Canada, G. S., and McLaughlin, M. H., AIChE Symp. Series, 176(74) (1978) Chan, I., and Knowlton, T. M., Fluidization, (Kunii and Toei, eds.) (1984)
Chan, I., and Knowlton, T. M., Presented at 76th AIChE Annual Meeting, San Francisco (1984)
Chan, I., Sishtla, C., and Knowlton, T. M., Powder Technol., 53:217 (1987) Clift, R., and Grace, J. R., Chem. Eng. Sci., 29:935 (1972)
Compo, P., Pfeffer, R., and Tardos, G., Powder Technol., 51:85–101 (1987)
150 Fluidization, Solids Handling, and Processing
Crowther, M. E., and Whitehead, J. C., Fluidization, (J. F. Davidson and D. L. Keairns, eds.), pp. 65–70, Cambridge University Press (1978)
deVries, R. J., Van Swaaij, W. P. M., Mantovani, C., and Heijkoop, A., Proc. Conf. Chem. Reaction Eng., B9–59, Amsterdam (1972)
Foscolo, P. U., and Gibilaro, L. G., Findlay, J. G., and Knowlton, T. M., Final Report for U.S. Dept. of Energy, Project, DE-AC21-83MC20314 (1985)
Geldart, D. PowderTechnol., 1:285 (1973)
Geldart, D., and Abrahamsen, A. R., Powder Technol., 19:133–136 (1978)
Geldart, D., and Abrahamsen, A. R., Chem. Eng. Prog. Symp. Ser., 77(205):160 (1981)
Geldart, D., and Kapoor, D. S., Chem. Eng. Sci., 31:842–843 (1976)
Guedes de Carvalho, J. R. F., King, D. F., and Harrison, D., Fluidization, (J. F. Davidson, and D. L. Keairns, eds.), pp. 59–64, Cambridge University Press (1978)
Hartge, E-U., Rensner, D., and Werther, J., Circulating Fluidized Bed Technol. II, (Basu, and Large, eds.), p 165, Pergamon Press (1988)
Hirsan, I., Sishtla, C., and Knowlton, T. M., Presented at 73rd AIChE Annual Meeting, Chicago (1980)
Hoffman, A. C., and Yates, J. G., Chem. Eng. Commun., 41:133–149 (1986)
Horio, M., Morishita, K., Tachibana, O., and Murata, N., Circulating Fluidized Bed Technol. II, (Basu and Large, eds.), p. 147, Pergamon Press (1988)
Institute of Gas Technol. Report No. DOE/MC/19301-10 (1985)
Jacob, K., and Weimer, A., AIChEJ ., 33:1698–1706, (1987)
Kai, T., and Furusaki, S., J. Chem. Eng. Jpn., 18(2) (1985)
Karri, S. B. R., and Knowlton, T. M., Circulating Fluidized Bed Technol. III, (Basu, Horio, and Hasatani, eds.), p. 67 (1991)
Karri, S. B. R., and Knowlton, T. M., in: Proc. of Fifth Int’l Conf. on Circulating Fluidized Beds, paper DB15, Beijing (1996)
King, D. F., and Harrison, D., Fluidization, (Grace and Matsen, eds.), p. 101, Plenum Press, New York (1980)
Kmiec, A., Chem. Eng. J., 23:133 (1982)
Knowlton, T. M., Final Report for USDOE Contract No. DE-AC21-82MC19301 (1985)
Knowlton, T. M., and Bachovchin, D. M., Fluidization Technol., (Keairns, ed.), p. 253, Hemisphere Publishing Corp. (1976)
Knowlton, T. M, and Bachovchin, D., Coal Processing Technol., 4:122–127 (1978)
Knowlton, T. M., AIChE Symp. Series, 161(73):22–28 (1977)
Pressure and Temperature Effects 151
Kono, H., AIChE Symp. Series, 205 (77):96 (1981)
Marzocchella, A., and Salatino, P., AIChE Symp. Series, (D. King, ed.), 92:25–30 (1996)
May, W. G., and Russell, F. R., Paper presented at New Jersey Section of A.C.S. Meeting-in-Miniature (1953)
Mii, T., Yoshida, K., and Kunii, D., J. Chem. Eng., 6:100–102, Japan.(1973)
Otake, T., Tone, S., Kawashima, M., and Shibata, T., J. Chem. Eng. Jpn., 8(5) (1975)
Parker, R., Jain, R., Calvert, S., Drehmel, D., and Abbott, J., Environmental Sci. Technol., 15(4):451 (1981)
Patterson, P., and Munz, R., Can. J. Chem. Eng., 67:321 (1989)
Punwani, D., Modi, M., and Tarman, P., Proc. Int’l. Powder and Bulk Solids Handling and Processing Conf. (1976)
Rhodes, M., Laussmann, P., Villain, F., and Geldart, D., Circulating Fluidized Bed Technol. II, (Basu and Large, eds.), p. 155, Pergamon Press (1988)
Richardson, S. F., Fluidization, (Davidson and Harrison, eds.), Academic Press, London (1971)
Rietema, K., Cottar, E. J. E., and Piepers, H. W.,Chem. Eng. Sci., 48:1687–1697 (1993)
Rosin, P., Rammler, E., and Intelmann, W., Zeitschrift Verein Deutscher Engenieure, 76:433 (1932)
Rowe, P. N., Chem. Eng. Sci., 39(1):173 (1984)
Rowe, P. N., Foscolo, P. U., Hoffman, A. C., and Yates, J. G., Fluidization, (Kunii and Toei, eds.), p. 53 (1984)
Saxena, S., and Vogel, G., Trans. Inst. Chem. Engrs., 55:184 (1977)
Sakuraya, K., Morinaka, I., Kamiya, K., and Tanaka, M., Tetsu-to -Hagame, 65:176 (1976)
Shrivastava, S., Mathur, S., and Saxena, S., AIChE J., 32(7):1227 (1986) Siegell, J. H., Powder Technol., 38:13 (1984)
Sishtla, C., Personal Communication
Sishtla, C., Chan, I., Findlay, J., and Knowlton, T. M., AIChE Symp. Series 270, 85:83 (1989)
Sishtla, C., Chan, I., and Knowlton, T. M., Fluidization V, (Ostergaard, and Sorenson, eds.), p. 127, Engineering Foundation (1986)
Sittiphong, N., George, A. H., and Bushnell, D., Chem. Eng. Sci., 36:1260–1263 (1981)
Sobreiro, L. E. L., and Monteiro, J. L. F, Powder Technol., 33:95 (1982)
Subzwari, M. P., Clift, R., and Pyle, D. L., Fluidization, (Davidson and Keairns, eds.), Cambridge, England (1978)
152 Fluidization, Solids Handling, and Processing
Takeuchi, H., Hirama, T., Chiba, T., Biswas, J., and Leung, L. S., Powder Tech., 47(2):195–199 (1986)
Varadi, T., and Grace, J. R., Fluidization, (Davidson and Keairns, eds.), Cambridge University Press (1978)
Weimer, A. W., and Quarderer, G. J., Paper 11e, presented at the 1983 Annual AIChE Meeting, Washington, D.C. (1983)
Weinstein, H., Shao, M., and Schnitzlein, M., Circulating Fluidized Bed Technol., (Basu, ed.), p. 201, Pergamon Press (1986)
Wen, C. Y., and Yu, Y. H., AIChE. J., 12:610 (1966)
Wittman, K., Helmrich, H., and Schugerl, K.,Chem. Eng. Sci., 36(10):1673 (1981)
Wu, S. Y., and Baeyens, J., Powder Technol., 67:217–220 (1991)
Xavier, A. M., King, D. F., Davidson, J. F., and Harrison D., Fluidization, (Grace and Matsen, eds.), p. 201, Plenum Press (1980)
Yang, W.-C., I & E C Fundamentals, 20:297 (1981)
Yang, W.-C., AIChE J., 31(7):1086 (1985)
Yang, W.-C., Circulating Fluidized Bed Technol. II, (Basu and Large, eds.), p. 181, Pergamon Press (1988)
Yang, W. C., and Chitester, D. C., AIChE Symp. Series, 262(84):10–21 (1988)
Yates, J. G., Bejcek, V., and Cheesman, D. J., Fluidization V, (Ostergaard, and Sorenson, eds.), Engineering Foundation, New York (1986)
Yates, J. G., and Cheesman, Chem. Eng. Sci. (1995)
Yoshida, K. Ueno, T., and Kunii, D., Chem. Eng. Sci. 29:77–82 (1974)
Yoshida, K., Fujii, S., and Kunii, D., Fluidization Technol., (Keairns, ed.), 43–48 (1976)

3
Heat Transfer in
Fluidized Beds
John C. Chen
1.0INTRODUCTION
Fluidized beds are widely used to achieve either chemical reactions or physical processing that require interfacial contact between gas and particles. Heat transfer is important in many of these applications, either to obtain energy transfer between the solid and gas phases or to obtain energy transfer between the two-phase mixture and a heating/cooling medium. The latter case is particularly important for fluidized bed reactors which require heat addition or extraction in order to achieve thermal control with heats of reaction.
Heat transfer between gas and particle phases tend to be efficient due to the large volumetric concentration of interface surface. Hence this topic is rarely of significant concern and will not be dealt with in this chapter. Most of the chapter concerns heat transfer between the twophase medium and submerged surfaces. This is the most pertinent engineering problem since heat addition or extraction from the fluidized or conveyed mixture is commonly achieved by use of heat exchangers integral to the vessel wall or submerged in the particle/gas medium.
153
154 Fluidization, Solids Handling, and Processing
As discussed in other chapters of this book, two-phase flows of gas and particles occur with different flow regimes. The mechanisms for heat transfer and the resulting heat transfer coefficients are strongly affected by the different flow characteristics, resulting in different design correlations and predictive models for each flow regime. This chapter will deal with the two most often encountered flow regimes:
•Bubbling dense fluidization
•Circulating fast fluidization
2.0BUBBLING DENSE FLUIDIZATION
2.1Hydrodynamic Characteristic
The key characteristic of fluidized beds is the levitation of solid
particles against gravity by shear-drag of the flowing gas. The resulting two-phase mixture of gas and particles behaves as a “fluid” in its response to pressure gradients. Upward flow of gas past solid particles can be classified into several fluidization regimes. At low flow rates, the gas percolates through the void spaces between stationary particles; this is termed flow through packed beds. With increasing gas velocity, a point is reached when the drag force between particles and fluid counterbalances the gravitational force on the particles resulting in suspension of particles by the upward flowing gas. This is the point of minimum fluidization, marking the transition from packed to fluidized beds. Particles of Geldart (1973) classification A or B (diameters in range of 50 to 500 μm and densities in range of 0.3 to 3 gm/cm3) can be smoothly fluidized. For such particles, gas velocities above the minimum fluidization value result in bubbling fluidization wherein some fraction of the gas flows as discrete bubbles through the mobile mixture of suspended particles. The upper limit of gas velocity for bubbling dense fluidization occurs when interfacial drag becomes sufficient to entrain the particles and transport them upward through the vessel. Thus bubbling fluidization is bounded between gas velocities for minimum fluidization and terminal transport.
Using the Ergun (1952) equation for the interfacial friction factor, Wen and Yu (1966) derived the following general equation to estimate the minimum fluidization superficial velocity Umf for spherical particles: