
Yang Fluidization, Solids Handling, and Processing
.pdf
Fluidized Bed Scale-up |
25 |
as a ratio of the cross sectional average, is roughly invariant over the cross section for these larger beds, the thickness of the wall layer follows from a mass balance. The upflow is proportional to the core area and the downflow to the product of perimeter and layer thickness. Thus the thickness should vary as the ratio of cross sectional area to perimeter, i.e., proportional to the hydrodynamic diameter.
Patience et al. (1992) developed a dimensionless correlation for the mean slip factor between the gas and solid by using solid suspension data from various small laboratory beds. The proposed correlation relates the slip to the Froude number based on the bed diameter. It remains to be seen if the correlation will hold at Froude numbers typical of large beds and if other dimensionless factors are important.
3.4Flow Transition
Hovmand and Davidson (1971) review Stewart’s criterion for the transition from bubbling to slug flow,
Eq. (5) |
uo -umf |
= 0.2 |
|
0.35(gD)12 |
|||
|
|||
|
|
and show it gives good agreement with most experiments. Thus, a small diameter laboratory bed may exhibit behavior which is far different than a scaled up pilot plant. There is some data which suggests the bed depth to bed diameter may also influence the bubble to slug transition.
Thiel and Potter (1977) carried out slugging flow experiments in three different diameter beds, the largest being 0.22 m in diameter. They found that the bed aspect ratio influenced the onset of slug formation. They also found that the transition to turbulent flow occurred at much lower superficial gas velocity in the 0.22 m diameter bed than in the 0.1 m bed. With the fluid cracking catalyst, the transition velocity decreased from 20 cm/s to 2.5 cm/s. Yerushalmi and Avidan (1985) assert that in large shallow beds where slugging does not occur, transition from bubbling to turbulent flow should be independent of bed size.
26Fluidization, Solids Handling, and Processing
4.0EXPERIMENTAL MEANS TO ACCOUNT FOR SCALEUP: USE OF SCALE MODELS
Since large pilot plants are costly, it may not be feasible to undertake an extensive scale-up program. Furthermore, large beds are difficult to instrument to observe detailed behavior. Thus, many test results from beds at elevated temperatures and pressure are confined to overall operating characteristics leaving the designers to speculate on the cause of shifts in performance with bed size. Full scale cold models are also expensive and require lengthy construction schedules. As we will see below, the full scale cold test may not correctly simulate the hydrodynamics of the actual process at elevated temperature and pressure. Indeed, a familiar occurrence in atmospheric bubbling fluidized bed combustors is the marked difference in flow behavior between a bed fluidized with cold air and the same bed run at normal operating conditions.
A technique which can assist in the scale-up of commercial plants designs is the use of scale models. A scale model is an experimental model which is smaller than the hot commercial bed but which has identical hydrodynamic behavior. Usually the scale model is fluidized with air at ambient conditions and requires particles of a different size and density than those used in the commercial bed. The scale model relies on the theory of similitude, sometimes through use of Buckingham’s “pi theorem,” to design a model which gives identical hydrodynamic behavior to the commercial bed. Such a method is used in the wind tunnel testing of small model aircraft or in the towing tank studies of naval vessels.
Once a technique has been established to design a model which simulates the hydrodynamics of a hot (possibly pressurized) fluidized bed, then a series of different sized models can be used to determine the influence of bed size on the performance of commercial beds, see Fig. 20. Model A´simulates the behavior of commercial bed A, model B´simulates a larger commercial bed B and so forth. Then by comparing models A´, B´ with C´ we can determine the expected changes in operating characteristics when commercial bed A is replaced by larger beds B and C.
Designing a model fluidized bed which simulates the hydrodynamics of a commercial bed requires accounting for all of the mechanical forces in the system. In some instances, convective heat transfer can also be scaled but, at present, proper scaling relationships for chemical reactions or hydromechanical effects, such as particle attrition or the rate of tube erosion, have not been established.

28 Fluidization, Solids Handling, and Processing
exact same equations and boundary conditions as the commercial bed, with the same values of the coefficients, then the model and the commercial bed should have identical behavior. The trick is to nondimensionalize all of the terms of the equations so that the model and the commercial beds have identical nondimensionalized values of the parameters. That is, if the coordinates are nondimensionalized by dividing them by the bed diameter,
Eq. (6) |
x′ = |
x |
; y′ = |
y |
|
D |
|||
|
|
D |
and the local gas velocity in the x direction is nondimensionalized by dividing it by the superficial gas velocity u′= uuo , then at the same value of x´ and y´ in a commercial bed and a properly scaled model, u´ will have the same value. Note, this nondimensionalization will extend to time as well. Generally the physical values of x, y, u, and t will be different in the model and the commercial bed, while the dimensionless values x´, y´, u´ and t´ are the same for the two beds.
It is important to include all of the relevant physical effects in the equations to be nondimensionalized. This can be difficult because there isn’t always consensus about which effects are important. Moreover, there is controversy over how to properly represent these effects in equation form. For our purposes the question is: Have all of the important parameters been included in the nondimensional equations? Pragmatically, the success to date of the scaling experiments using the formulation as presented adds confidence to the use of these simplifications which will be employed. Also, a limited number of tests have verified the omission of parameters specifically related to several phenomena.
In some cases, if we are too precise and include effects of marginal significance, the resulting modeling rules may be overly restrictive, limiting the choice of models or requiring the models which are too big. These questions are most expeditiously settled by experiments since an exact theoretical answer is not presently available.
The equations of motion can either be formulated for individual particles and the surrounding fluid, or the fluid and the particulate phases can each be considered a continuum. Both approaches yield identical results, see Glicksman et al. (1994) for a complete derivation. For our purposes, we will base the derivation on the continuum model formulated by Jackson.
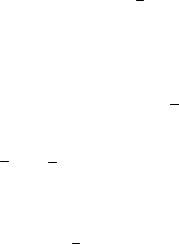
Fluidized Bed Scale-up |
29 |
4.2Governing Equations
The use of governing equations has the merit of tying specific dimensionless parameters to particular physical phenomena (Glicksman, 1984, 1988). If the proper equations can be written, even if they cannot be solved, they yield considerable insight into the process.
Early derivation of these dimensionless parameters was based on a continuum model (Scharff et al., 1978; Glicksman, 1984). Inclusion of the individual particle approach extends the results to instances where a continuum model may not be applicable.
For simplicity, the fluid will be considered incompressible although the results do not depend on this condition. The continuum equations will be developed similar to those given by Anderson and Jackson (1967). These equations are based on a continuum picture of the suspension of solids in the fluid. The solids and the fluid are considered individual phases, and variables for each phase such as velocity or voidage are average values over regions large compared to a single particle but small compared to the scale of the macroscopic bed behavior. The derivation follows that given by Jackson (1971).
For the fluid, conservation of mass is
Eq. (7) |
|
|
|
|
|
|
∂ε |
+ div(ε |
u) = 0 |
|
|
|
|
|
|
||||||||
|
|
|
|
|
|
∂t |
|
|
|
|
|
|
|||||||||||
|
|
|
|
|
|
|
|
|
|
|
|
|
|
|
|
|
|
|
|
|
|||
and for the solid phase, |
|
|
|
|
|
|
|||||||||||||||||
Eq. (8) |
|
|
|
|
|
|
∂ |
(1-ε )+ div[(1-ε ) |
υ |
]= 0 |
|
|
|
|
|||||||||
|
|
|
|
|
|
|
|
|
|
|
|
||||||||||||
|
|
|
|
|
|
|
∂t |
|
|
|
|
|
|
|
|
|
|
|
|
|
|
||
where |
u |
and |
|
υ |
|
are the vectorial form of the fluid and solid phase |
|||||||||||||||||
velocities, respectively. |
|
|
|
|
|
|
|||||||||||||||||
|
The equation of motion for the fluid can be written as, |
||||||||||||||||||||||
|
|
|
|
|
æ ¶ |
u |
|
|
|
·Ñ |
|
ö |
|
|
|
|
|
|
|
|
|||
|
|
|
|
|
|
|
|
|
|
|
|
|
|
|
|
|
|
||||||
|
|
|
|
|
|
|
|
|
|
|
|
|
|
|
|
|
|
||||||
Eq. (9) |
|
ρ |
f |
ε ç |
|
|
|
|
+ |
u |
u |
÷ + i ρ |
f |
gε - Ñ · |
E f |
+ F = 0 |
|||||||
|
|
|
|
|
|||||||||||||||||||
|
|
ç |
|
¶t |
÷ |
|
|
|
|
|
|
||||||||||||
|
|
|
|
è |
|
ø |
|
|
|
|
|
|
|
|

30 Fluidization, Solids Handling, and Processing
while for the particle phase,
Eq. (10) |
ρs |
(1 |
- ε )ÿ ¶ |
υ |
|
|
|
|
|
¶t |
|
|
|
|
|
|
+υ · Ñυ ÿ + i
ρs g(1 - ε ) - F - Ñ · Ep = 0
where i is the unit vector in the vertical direction, and the drag force between the fluid and the particle is represented by F. The terms Ef and Ep are the local average stress tensors associated with the fluid and particle phases, respectively. The proper formulation of the stress tensors is still a subject of controversy. The fluid-to-particle force term can be represented by a drag term proportional to the relative velocity between the two phases and a virtual mass term (CA is the added mass coefficient),
Eq. (11) |
|
=β ( |
|
-υ |
)+ (1-ε )C A ρf |
d |
( |
|
-υ |
) +(1-ε ) Ñ · Ef |
|
F |
|||||||||||
u |
u |
||||||||||
|
|||||||||||
|
|
|
|
|
|
dt |
Note β is, in general, not a constant, rather it must be found from a general expression for the drag force.
Given the uncertainty in the form of the stress tensors, many authors have adopted a form analogous to single phase Newtonian fluid relating the stress terms to the pressure and viscosity of the fluid and particle phase, respectively.
The physical basis of the particle phase pressure and viscosity still has not been resolved in the fluidization literature. In particular, dealing with stability between minimum fluidization and minimum bubbling some investigators have considered interparticle forces as purely hydrodynamic, such as Foscolo and Gibilaro (1984) and Batchelor (1988), while others contend that the interparticle forces are due to phenomena such as electrostatic or van der Waals forces (Rietema and Piepers, 1990; Rietema et al. 1993). For very fine particles, particle to particle cohesive forces are recognized as influencing the point of bubbling for gas fluidized beds (Baeyans and Geldart, 1973).
For larger particles, the nature of interparticle forces is still unresolved. A typical operating condition for most commercial gas solid beds is well beyond the point of minimum bubbling. It might be expected that
Fluidized Bed Scale-up |
31 |
electrostatic or van der Waals forces are not as important as they are near the point of minimum fluidization. It is likely that particle-particle collisions, dependent on the coefficient of restitution and sliding friction, come into play at much higher uo /umf.
Litka and Glicksman (1985) carried out systematic experiments to determine the importance of particle mechanical properties on the behavior of bubbling beds. These tests helped to evaluate the importance of non-hydrodynamic forces on particle-particle interactions. Two beds were compared with particles having identical properties save one. In one test, particles with a different coefficient of restitution were tested, in a second test, particles with a different coefficient of sliding friction were compared. In these tests, both groups of particles had the same size, shape and density. In all tests, the two different particles exhibited the same bubble frequency and size as well as the same particle transit time both upward and downward. Chang and Louge (1992) found that in a circulating bed the vertical solids distribution could be changed if particles with artificially low surface friction were used. In the range of surface friction for usual commercial and test material there wasn’t any influence.
Given the results of Litka and Glicksman and Change and Louge, as well as the lack of consensus concerning the nature and importance of interparticle interactions, such terms will not be considered further in this development and the particle-particle forces will be considered hydrodynamic. Foscolo et al. (1990) have shown that if the interparticle forces are hydrodynamic in nature, the dimensionless parameters obtained are identical to those obtained by neglecting interparticle interaction. The success of scaling experiments for bubbling and circulating beds, which to date has omitted parameters specifically related to nonhydrodynamic interparticle interactions, suggest that in the range of parameters investigated, such an omission is valid.
The boundary conditions for the bed at the side wall with no net flow of particles across it are at
Eq. (12) |
x = 0,D |
|
υnormal = 0 |
||
|
where this is the solids velocity normal to the wall.

32 Fluidization, Solids Handling, and Processing
At the bottom
at y = 0
Eq. (13) |
υnormal |
= |
|
Gs |
|
ρs |
(1 − ε ) |
||||
|
|
|
where Gs is the average solids feed rate per unit area from outside the bed through the bottom. This form holds when the solids feed is uniformly distributed over the bottom. If solids feed takes place along the side wall, an expression similar to Eq. (13) must be used in place of Eq. (12).
For gas velocity at the walls,
Eq. (14) |
at x = 0,D |
|
|
= 0 |
||
u |
||||||
while at the distributor, |
|
|
|
|||
|
at y = 0 |
|
|
|
||
|
|
|
= i uo / |
above the distributor holes |
||
Eq. (15) |
u |
|||||
|
|
|
= 0 elsewhere |
|||
|
u |
|||||
where |
is the voidage of the distributor plate assumed in this case to be a |
perforated plate and uo is the superficial gas velocity. For bubble caps or other gas inlet devices, boundary conditions such as Eq. (15) apply over the gas inlet plane of the device. Boundary conditions, Eqs. (12) and (14), also apply to the surfaces of any internal elements in the bed, for example: heat transfer tubes.
|
At all xs , ys (internal surfaces) |
||
Eq. (16) |
|
|
= 0, υ N = 0 |
u |
|||
Also at the distributor |
|||
Eq. (17) |
at y = 0, P=Po |

Fluidized Bed Scale-up |
33 |
Nondimensionalizing the variables as,
|
υ |
|
|
|
υ |
, |
|
¢ = |
|
|
|
|||
|
¢ = |
u |
||||||||||||
|
u |
|||||||||||||
|
|
|
|
|
|
|
|
|||||||
|
|
|
|
|
|
uo |
uo |
|||||||
|
Ñ' = LÑ, |
|
|
|
||||||||||
|
t¢ = |
uo |
t |
|
|
|
||||||||
|
|
|
|
|
|
|
|
|||||||
|
|
|
|
|
L |
|
|
|
||||||
Eq. (18) |
|
x¢ = |
x |
|
|
|
|
|
|
|||||
|
|
L |
|
|
|
|||||||||
|
|
|
|
|
|
|
|
|||||||
|
|
y¢ = |
y |
|
|
|
|
|||||||
|
|
L |
|
|
|
|||||||||
|
|
|
|
|
|
|
|
where L is a typical bed dimension, e.g., the bed height or diameter. Note that u´, υ´ as well as ε are dependent variables of x ′, y ′, and t ′ which are determined by the boundary conditions and the independent dimensionless parameters of the governing equations.
Applying these definitions to the governing equations and rearranging them so the parameters form nondimensional groups, the continuity equations become
Eq. (19) |
¶ε |
+ div(ε |
|
¢) |
|
|
u |
||||||
|
¶t¢ |
|
|
|
|
|
and |
|
|
|
|
|
|
Eq. (20) |
¶ |
(1 - ε ¢)+ div[(1 - ε ¢)υ |
¢] = 0 |
|||
¶t¢ |
||||||
|
|
|
|
|
The fluid-particle interaction force, omitting the virtual mass term and combining the pressure terms in the equation of motion becomes
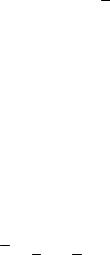
34 Fluidization, Solids Handling, and Processing
|
|
|
|
|
|
|
|
|
|
β L |
( |
|
¢ -υ |
¢) |
|
|
|
|
||||||
Eq. (21) |
|
|
|
|
LF |
= |
|
|
|
|
||||||||||||||
|
|
|
|
u |
|
|
|
|
||||||||||||||||
|
|
|
|
ρf uo2 |
|
|
|
|
|
|
||||||||||||||
|
|
|
|
|
|
ρf |
uo |
|
|
|
|
|
|
|||||||||||
The equations of motion in dimensionless form are, |
||||||||||||||||||||||||
|
ε |
¶ |
|
¢ |
+ |
|
¢ · Ñ¢u¢ |
|
|
|
gL |
ε - Ñ¢ · |
p |
+ |
Lβ |
= 0 |
||||||||
|
u |
|||||||||||||||||||||||
Eq. (22) |
u |
+ i |
||||||||||||||||||||||
|
|
|
|
|
|
|
2 |
|
||||||||||||||||
ÿ |
¶t¢ |
|
|
|
|
|
ÿ |
2 |
|
|
|
ρf uo |
||||||||||||
|
|
|
|
|
|
|
|
|
|
|
|
uo |
|
|
ρf uo |
|
and for the particle phase, without the particle stress tensor,
Eq. (23)
(1 - ε )ÿ ¶υ ¢
¶t¢
+υ ¢ · Ñ¢υ ¢ÿ +
|
|
|
ρf |
|
|
Lβ |
|
||
i gL |
|||||||||
ÿ |
ÿ |
||||||||
2 |
(1 - ε )-ÿ |
|
ÿÿ |
ρf uo |
ÿ |
||||
|
uo |
ρs |
|
|
|||||
|
|
|
|
|
|
|
|
|
The dimensionless boundary conditions become,
at x' = 0, D/L
Eq. (24) |
υnormal |
= 0 |
|
|
|
||||
|
|
|
|
||||||
|
at y = 0 |
|
|
|
|
||||
Eq. (25) |
υnormal |
= |
|
Gs |
|
1 |
|||
|
ρsuo |
1 − ε |
|||||||
|
|
|
|
|
|
||||
|
at x = 0, |
D |
|
|
|
||||
Eq. (26) |
|
|
|
||||||
|
|
¢ = 0 |
|
|
L |
|
|
||
|
|
|
|
|
|
|
|
|
|
|
u |
|
|
|
|
|
|