
Yang Fluidization, Solids Handling, and Processing
.pdfHeat Transfer in Fluidized Beds 205
Gabor, J. O., “Wall-to-Bed Heat Transfer in Fluidized and Packed beds,” AIChE Symp. Series, 66(105):76–86 (1970)
Gamson B. W., “Heat and Mass Transfer in a Fluid Solid System,” Chem. Eng. Progress, 47(1):19–28 (1951)
Geldart, D., “Types of Gas Fluidization,” Powder Technol., 7(5):285–292 (1973)
Gelperin, N. I., and Einshtein, V. G., “Heat Transfer in Fluidized Beds,”Fluidization, p. 471, London, UK (1971)
Gelperin, N. I., Einshtein, V. G., Korotjanskaja, L. A., and Perevozchikova, J. P.,
Teoreticheskie Osnovy Khimicheskoe Tech. 2:430 (1968)
Grace, J. R., Can. J. Chem. Eng. 64:353 (1986)
Grace, J., “Heat Transfer in Circulating Fluidized Beds,” Cir. Fluid. Bed Tech., 63–81 (1986)
Han, G. Y., “Experimental Study of Radiative and Particle Convective Heat Transfer in Fast Fluidized Beds,” Ph.D. Dissertation, Lehigh University (1992)
Hartige, E. U., Li, Y., and Werther, J., “Flow Structures in Fast Fluidized Beds,” Fluidization V, 345–352 (1986)
Herb, B. E., Dou, S., Tuzla, K., and Chen, J. C., “Axial Solid Concentration in CFBs: Experimental Measurements and Model Predictions,” AIChE Annual Meeting (1989)
Herb, B., Tuzla, K., and Chen, J. C., “Distribution of Solid concentrations in Circulating Fluidized Bed,” Fluidization VI, 65–72 (1989)
Herb, B. E., Dou, S., Tuzla, K., and Chen, J. C., “Solid Mass Fluxes in Circulating Fluidized Beds,” Powder Technol., 197–205 (1992)
Horio, M., Morshita, K., Tachibana, O., and Murata, M., “Solid Distribution and Movement in Circulating Fluidized Beds,” Circ. Fluid. Bed Tech. II, 147– 154 (1988)
Jacob, A., and Osberg, G. L., “Effect of Gas Thermal conductivity on Local Heat Transfer in a Fluidized Bed,” Canadian J. of Chem. Eng., 35(6):5–9 (1957)
Jestin, L., Chaberg, C., Flamant, G., and Meyer, P., “In-situ Measurement of Particle Concentration, Temperature Distribution and Heat Flux in Vicinity of A Wall in A CFB,” Circ. Fluid. Bed Tech. IV, 247–254 (1990)
Kiang, K. D., Lin, K. T., Nack, H., and Oxley, J. H., “Heat Transfer in Fast Fluidized Beds,” Fluidization Technol., 471–483 (1976)
Kobro, M., and Brereton, L., “Control and Fuel Flexibility of Circulation Fluidized Beds,” Circ. Fluid. Bed Tech., 263–272 (1986)
Kubie, J., and Broughton, J., “A Model of Heat Transfer in Gas Fluidized Beds,” Int. J. of Heat and Mass Transfer, 18:289–299 (1975)
206 Fluidization, Solids Handling, and Processing
Kunii, K., and Smith, J. M., “Heat Transfer Characteristics of Porous Rocks,” AIChE J. 6(1):71–78 (1960)
Kunii, D., and Levenspiel, O., Fluidization Eng., 2nd Ed., Butterworth-Heinemann, Boston (1991)
Leva, M., Weintrub, M., and Grummer, M., “Heat Transmission Though Fluidized Beds of Fine Particles,” Chem. Eng. Progr., 45(9):563–572 (1949)
Leva, M., and Grummer, M., “Correlation of Solids Turnovers in Fluidized Systems,” Chem. Eng. Progr., 48(6):307–313 (1952)
Levenspiel, O., and Walton, J. S., Chem. Eng. Progr. Symp. Series, 50(9):1 (1954)
Lints, M., “Particle to Wall Heat Transfer in Circulating Fluidized Beds,” Ph.D. Dissertation, MIT (1992)
Lints, M. C., and Glicksman, L. R., “Structure of Particle Clusters Near Wall of a Circulating Fluidized Bed,” AIChE Symp. Series, 89(296):35–47 (1993)
Lints, M. C., and Glicksman, L. R., “Parameters Governing Particle-to-Wall Heat Transfer in a Circulating Fluidized Bed,” Circ. Fluid. Bed Tech. IV, 297–304 (19923)
Liu, D., Liu, J., Li, T., and Kwauk, M., “Shallow Fluid Bed Tubular Heat Exchanger,” Fluidization, pp. 401–408, 5th Eng. Foundation Conf. on Fluidization, Engineering Foundation, NY (1986)
Louge, M., Lischer, J., and Chang, H., “Measurements of Voidage Near the wall of a Circulating Fluidized bed Riser,” Powder Tech., 62:269–276 (1990)
Mahalingan, M., and Kolar, A. K., “Heat Transfer Model for Membrane Wall of a High Temperature Circulating Fluidized Bed,” Circ. Fluid. Bed Tech. III, 239–246 (1990)
Martin, H., “Heat Transfer Between Gas Fluidized Beds of Solid Particles and the Surface of Immersed Heat Exchanger Element,” Parts I & II, Chem. Eng. Process, 18:157–169, 199–223 (1984)
Mickley, H. S., and Trilling, C. A., “Heat Transfer Characteristics of Fluidized Beds,” Ind. Eng. Chem., 41(6):1135–1147 (1949)
Mickley, H. S., and Fairbanks, D. F., “Mechanism of Heat Transfer to Fluidized Beds,” AIChE J., 1(3):374–384 (1955)
Miller, C. O., and Logwinuk, A. K., “Fluidization Studies of Solid Particles,” Ind. & Eng. Chem., 43(5):1220–1226 (1951)
Molerus, O., and Schweinzer, J., “Prediction of Gas Convective Part of the Heat Transfer to Fluidized Beds,” pp. 685–693, Fluidization IV, Eng. Foundation, New York, USA (1989)
Molerus, O., “Fluid Dynamics and Its Relevance for Basic Features of Heat Transfer in Circulating Fluidized Beds,” Circ. Fluid. Bed Tech. IV, pp. 285–290 (1993)
Heat Transfer in Fluidized Beds 207
Noë, A. R., and Knudsen, J. G., “Local and Average Heat Transfer Coefficients in a Fluidized Bed Heat Exchanger,” Chem. Eng. Prog. Symp. Series, 64(82):202–211 (1968)
Ozkaynak, T. F., and Chen, J. C., “Emulsion Phase Residence time and Its Use in Heat Transfer Models in Fluidized bed,” AIChE J., 26(4):544–550 (1980)
Ozkaynak, T., “Investigation of Packet Residence Time and Its Relation with the Heat Transfer Coefficient in Fluidized Beds,” Ph.D.. Dissertation, Lehigh University (1974)
Ozkaynak, T. F., Chen, J. C., and Frankenfield, T. R., “An Experimental Investigation of Radiant Heat Transfer in High Temperature Fluidized Bed,” Fluidization, Fourth International Conf. on Fluidization, pp. 371– 378, Engineering Foundation (1983)
Palchonok, G. I., Breitholz, C., Anderson, B. A., and Lechner, B., “Heat Transfer in the Boundary Layer of a Circulating Fluidized Bed Boiler,” Fluidization VIII, pp. 291–299 (1995)
Radauer, H. G., Glatzer, A., and Linzer, w., “A Model Combining Convective and Radiative Heat Transfer in CFB Boilers,” Circ. Fluid. Bed Tech. V, 9 (1996)
Saxena, S. C., Grewal, N. S., Gabor, J. D., Zabrodsky, S. S., and Galershtein, D. M., “Heat Transfer Between a Gas Fluidized Bed and Immersed Tubes,”
Adv. In Heat Transfer, 14:145–247 (1978)
Soong, C. H., Tuzla, K., and Chen, J. C., “Indentification of Particle Clusters in Circulating Fluidized Bed,” Circ. Fluid. Bed Tech. IV, pp. 809–814 (1993)
Soong, C. H., Tuzla, K., and Chen, J. C., “Experimental Determination of Cluster Size and Velocity in Circulating Fluidized Beds,” Fluidization VIII, Engineering Foundation, pp. 219–227 (1995)
Tamarin, A. I., Zabrodsky, S. S., and Yepanov, G., “Heat Transfer Between a Horizontal Staggered Tube Bundle and a Fluidized Bed,” Heat TransferSoviet Research, 8(5):51–55 (1976)
Vedamuthy, V. N., and Sastri, V. M. K., “An Analysis of the Conductive and Radiative Heat Transfer to Walls of Fluidized Combustors,” Intern. J. Heat Mass Transf., 17(1):1–9 (1074)
Visser, G., and Valk, M., “The Porosity in a Fluidized Bed Heat Transfer Model,”Int. J. of Heat and Mass Transfer, 36(3):627–632 (1993)
Vreedenberg H. A., “Heat Transfer Between a Fluidized Bed and a Horizontal Tube,” Chem. Eng. Sci., 9(1):52–60 (1958)
Vreedenberg H. A., “Heat Transfer Between a Fluidized Bed and a Vertical Tube,” Chem. Eng. Sci. II, 4:274–285 (1960)
Wen, C. Y., and Miller, E. N., Ind. Eng. Chem., 53:51–53 (1966)
208 Fluidization, Solids Handling, and Processing
Wen, C. Y., and Yu, Y. H., “A Generalized Method for Predicting the Minimum Fluidization Velocity, AIChE J., 12(3):610–612 (1966)
Wender, L., and Cooper, G. T., “Heat Transfer Between Fluidized-Solids Beds and Boundary Surfaces--Correlation of Data,” AIChE J., 4(1):15–23 (1958)
Werdmann, C. C., and Werther, J., “Solids Flow Pattern and Heat Transfer in an Industrial Scale Fluidized Bed Heat Exchanger,” Proc. 12th Intern. Conf. on Fluid. Bed Comb ., 2:985–990 (1993)
Werther, J., “Fluid Mechanics of Large-Scale CFB Units,” Circ. Fluid. Bed Technol. IV, pp. 1–14 (1993)
Wirth, K. E., “Zirkulierende Wirbelschichten-Stromungsmechanische Grundlagen,”
Anwendung in der Feuerungstechnik (1990)
Wirth, K. E., “Prediction of Heat Transfer in Circulating Fluidized Beds,” Circ. Fluid. Bed Tech. IV, pp. 291–296 (1993)
Wirth, K. E., “Heat Transfer in Circulating Fluidized Beds,” Chem. Eng. Sci., 50(13):2137–2151 (1995)
Wood, R. T., Staub, F. W., Canada, G. S., and McLaughlin, M. H., “Two-Phase Flow and Heat Transfer in Fluidized Beds,” Technical Report, RP 525-1, General Electric Co., Schenectady, NY (1978)
Wu, R., Grace, J., Lim, C., and Brereton, C., “Suspension to Surface Heat Transfer in a Circulating Fluidized Bed Combustor,” AIChE, J., 35:1685–1691 (1989)
Wu, R. L., “Heat Transfer in Circulating Fluidized Beds,” Ph.D.. Dissertation, Univ. of British Columbia (1989)
Xavier, A. M., and Davidson, J. F., “Heat Transfer to Surfaces Immersed in Fluidized Beds, Particularly Tube Arrays,” Fluidization, Proc. of Second Eng. Foundation Conf., pp. 333–338, Cambridge Univ. Press (1978)
Yagi, S., and Kunii, K., “Studies on Effective Thermal Conductivities in Packed Beds,” AIChE J., 3:373 (1957)
Yoshida, K., Ueno, T., and Kunii, D., “Mechanism of Bed-Wall Heat Transfer in a Fluidized Bed at High Temperature,” Chem. Eng. Sci., 29(1):77–82 (1974)
Ziegler, E. N., Koppel, L. B., and Brazelton, W. T., “Effects of Solid thermal Properties on Heat Transfer to Gas Fluidized Bed,” I&EC Fundamentals, 3(4):324–328 (1964)
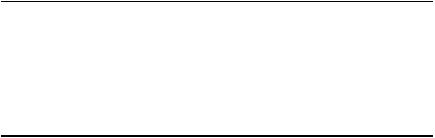
4
Gas Distributor and
Plenum Design in
Fluidized Beds
S.B. Reddy Karri and Ted M. Knowlton
1.0INTRODUCTION
The gas distributor (also called a grid) in a fluidized bed reactor is intended to induce a uniform and stable fluidization across the entire bed cross-section, operate for long periods (years) without plugging or breaking, minimize weepage of solids into the plenum beneath the grid, minimize attrition of the bed material, and support the weight of the bed material during start-up and shut-down. In practice, grids have taken a variety of forms, a few of which are discussed in subsequent pages. Whatever the physical form, all are fundamentally classifiable in terms of the direction of gas entry: either upward, laterally, or downward. The choice depends on prevailing process conditions, mechanical feasibility, and cost. In the past, grid design has been more of an art than a science. However, more recent studies now allow grid designs based on scientific principles.
209
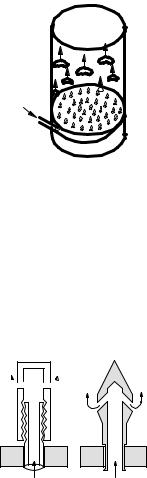
210 Fluidization, Solids Handling, and Processing
2.0TYPES OF GRIDS
2.1Perforated Plates (Upwardly-Directed Flow)
Main Advantages: Simple fabrication; most common; inexpensive; easy to modify hole size; easy to scale up or down; easy to clean; can be flat, concave, convex, or double dished; ports are easily shrouded.
Possible Disadvantages: Bed weepage to plenum; high pressure drop; can be subject to buckling or thermal distortion; requires peripheral seal to vessel shell; requires support over long spans.
2.2Bubble Cap (Laterally-Directed Flow)
(A)
(B)
Main Advantages: Minimizes weeping; good turndown ratio; lower pressure drop; can incorporate caps as stiffening members; can support internals.
Possible Disadvantages: Expensive; difficult to avoid stagnant regions; more subject to immediate bubble merger; difficult to clean; difficult to modify; not advisable for sticky solids; requires peripheral seal; ports not easily shrouded.
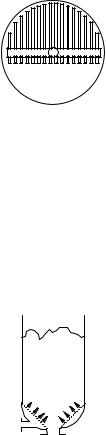
Gas Distributor and Plenum Design 211
2.3Sparger (Laterally or Downwardly-Directed Flow)
Main Advantages: Can minimize weeping; good turndown ratio; low pressure drop; can support internals; can undergo thermal expansion without damage; ports are easily shrouded; well suited to multilevel fluid injection; solids can flow from above the grid to below.
Possible Disadvantages: Defluidizedsolids beneath the grid; can be a less-for- giving mechanical design.
2.4Conical Grids (Laterally-Directed Flow)
Main Advantages: Promotes solidmixing; prevents stagnant solids buildup, minimizes solids segregation.
Possible Disadvantages: Difficult to construct, requires careful design to ensure good gas distribution, requires high pressure drop for good gas distribution.
Among the foregoing advantages and limitations, the designer must select those most pertinent or critical to his process application. There are, for example, instances in which solids below the grid level are tolerable, where grid thermal expansion is significant, where bed solids are very friable, where pressure drop and, therefore, the cost of compressive
212 Fluidization, Solids Handling, and Processing
horsepower is critical, where solids are “sticky” and must be kept in motion throughout, where internal impellers or stirrers must be provided, or where grids are expected to have a short life due to corrosion.
These and many other specifics have dictated a host of design variations. It should be emphasized that each application requires thoughtful engineering consideration before final design selection.
3.0GRID DESIGN CRITERIA
3.1Jet Penetration
Gas flowing from the grid holes can either take the form of a series of bubbles or a permanent jet, depending on system parameters and operating conditions. However, a permanent jet prevails for most industrial conditions. Jet penetration is one of the most important design parameters since it helps in:
(a)Determining how far to keep the bed internals, such as feed nozzles, heat exchanger tubes, etc., away from the grid to minimize erosion of internals.
(b)Deciding on grid design parameters such as hole size and the gas jet velocity required to achieve a certain jetting region.
(c)Minimizing or maximizing particle attrition at grids.
Knowlton and Hirsan (1980) reported that the jet penetration for upwardly-directed jets fluctuated greatly. Karri (1990) noted that jet penetration can vary as much as 30% for upwardly-directed jets. However, the jet emanating from a downwardly-directed grid hole is stable and its penetration length doesn’t significantly fluctuate with time. Figure 1 indicates jet penetration configurations for jets oriented upwardly, horizontally, and downwardly. According to Karri, the jet penetrations for various orientations can be approximately related by:
Eq. (1) Lup ≈ 2Lhor ≈ 3Ldown
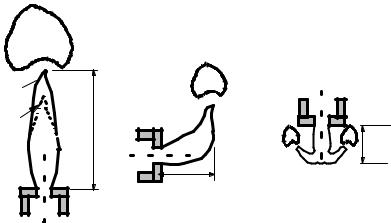
Gas Distributor and Plenum Design 213
maximum
minimum
Lup |
Ldown |
Lhor
Upwardly |
Horizontally |
Downwardly |
Directed Jet |
Directed Jet |
Directed Jet |
Figure 1. Jet penetrations at grid holes for different orientations.
There are numerous jet penetration correlations (Zenz, 1969; Shakhova, 1968; Merry, 1971; Yang and Keairns, 1979; Knowlton and Hirsan, 1980; Yates et al., 1986; Blake et al., 1990; Roach, 1993) in the literature. Massimilla (1985) and Karri (1990) have shown that the jet penetrations predicted by these correlations can vary by a factor of 100 or more. Among them, Merry’s correlation for horizontal jets was shown (Karri; Chen and Weinstein, 1993; Roach) to give reliable predictions. Merry’s correlation to calculate the penetration of horizontal jets is:
|
Lhor |
|
æ |
ρ U 2 |
ö0.4 |
æ |
ρ |
ö0.2 |
æ d |
ö0.2 |
|||
Eq. (2) |
= 5.25 |
ç |
g,h h |
÷ |
ç |
|
g,b ÷ |
ç |
|
p ÷ |
|||
dh |
ç |
|
÷ |
ç |
|
|
÷ |
ç |
|
|
÷ |
||
|
|
è |
ρ p (1-ε mf ) gd p ø |
è |
ρ p ø |
è dh ø |
The jet penetration lengths for upwardly and downwardly directed jets can be calculated from Eq. (1). These equations take into account the effects of pressure and temperature on jet penetration. Knowlton and Hirsan (1980) and Yates et al. found that the jet penetration increases significantly with system pressure. In addition, Sishtla et al. (1989) found that the jet penetration decreases with increasing system temperature. Bed
214 Fluidization, Solids Handling, and Processing
internals should not be placed in the jetting zone near the grid, otherwise the internals could be severely eroded.
3.2Grid Pressure-Drop Criteria
For a grid, achieving equal distribution of gas flow through many parallel paths requires equal resistances and sufficient resistance to equal or exceed the maximum value of any unsteady-state pressure fluctuation. It has been determined experimentally that the “head” of solids in some fluidized beds above an upwardly-directed grid port can vary momentarily by as much as 30%. This is due to large fluctuations in the jet penetration for an upwardly-directed jet as discussed in the previous section. The equivalent variation downstream of a downwardly-directed port is less than 10%. Thus, as a rule of thumb, the criteria for good gas distribution based on the direction of gas entry are:
(a) For upwardly and laterally-directed flow:
Eq. (3) |
Pgrid ³ 0.3 Pbed |
(b) For downwardly-directed flow:
Eq. (4) |
Pgrid ³ 0.1 Pbed |
(c)Under no circumstances should the pressure drop across a large-scale commercial grid be less than 25 cm of water, i.e.,
Eq. (5) |
Pgrid ³ 25 cm H2O |
Several investigators (Hiby, 1964; Zuiderweg, 1967; Whitehead, 1971; Siegel, 1976; and Mori and Moriyama, 1978) have found the ratio of pressure drops to be in the range of 0.015 to 0.4.
If turndown is desired, the grid pressure-drop criteria (Eqs. 3 and 4) must apply at the minimum gas flow rate. Also, if the grid is curved, i.e., concave, convex, or conical, the criterion must apply with respect to the