
- •Процессы и инструменты механообработки
- •Введение
- •Общие положения
- •Геометрия передней поверхности сверла
- •Выводы
- •Литература
- •ДГМА, г. Краматорск, Украина
- •Введение
- •Литература
- •Введение
- •Общие положения
- •Методика исследования
- •Коэффициент технологической гибкости
- •Литература
- •Введение
- •Выводы
- •Литература
- •Введение
- •Методика исследований
- •Основная часть
- •Введение
- •Введение
- •Выводы
- •Введение
- •Экспериментальная часть исследований
- •Литература
- •Введение
- •Выводы
- •ДГМА, г.Краматорск, Украина
- •Введение
- •Выводы
- •Литература
- •ДГМА, г.Краматорск, Украина
- •Выводы
- •Вступ
- •Висновки
- •ДГМА, Краматорск, Украина
- •Введение
- •Выводы
- •Література
- •Вступ
- •Основна частина
- •Технология машиностроения
- •Вступ
- •Постановка задач дослідження
- •Результати досліджень
- •Література
- •Введение
- •Постановка проблемы, анализ публикаций
- •Выделение нерешенных ранее частей общей проблемы
- •Постановка задачи
- •Выводы
- •Литература
- •Вступ
- •Вступ
- •ПРИ МЕХАНИЧЕСКОЙ ОБРАБОТКЕ
- •Литература
- •Выводы
- •Литература
- •Поля базы данных (конечные синдромы): SMAX
- •Литература
- •Введение
- •Общие положения
- •Основная часть
- •Выводы
- •Литература
- •Введение
- •Основная часть
- •Введение
- •Выводы
- •Выводы
- •Вступ
- •Основна частина
- •Висновки
- •Фокин А.Г.
ISBN 966-7851-19-2 Надійність інструменту та оптимізація технологічних систем. №14 2003.
УДК 621.9
Клименко Г.П., Васильченко Я.В., Ткаченко Н.А.
ДГМА, г. Краматорск, Украина
ОПРЕДЕЛЕНИЕ ОГРАНИЧЕНИЙ НА РЕЖИМЫ РЕЗАНИЯ ПРИ ОПТИМИЗАЦИИ РЕГЛАМЕНТОВ ЭКСПЛУАТАЦИИ ИНСТРУМЕНТА НА ТЯЖЕЛЫХ СТАНКАХ
Restrictions of technological system on modes of cutting are investigated at processing details on heavy machine tools. The statistical data of information bank on work of tools on heavy machine tools were used. Modes of cutting are optimized.
Введение
Актуальность проблемы обусловлена тенденциями повышения производительности и конкурентоспособности машиностроения, решениями правительства Украины о создании нормативной базы. Анализ последних исследований публикаций по данной проблеме показал, что для тяжелых станков необходим дополнительный комплекс исследований, связанных с особенностями их эксплуатации.
Цель настоящей работы – повышение эффективности использования тяжелых токарных станков за счет оптимизации регламентов эксплуатации режущего инструмента.
Методика исследований
Регламенты эксплуатации режущих инструментов включают элементы режимов резания, нормы расхода и стратегии замены режущего инструмента. Оптимизация этих параметров осуществляется на основе сформированных целевых функций с учетом существующих ограничений. В качестве целевых функций традиционно применяются математические выражения себестоимости, производительности, расхода инструмента, в которых регламенты эксплуатации инструмента входят как переменные. Рациональными считают такие параметры, которые соответствуют экстремумам целевых функций с учетом действующих ограничений. Производственные испытания режущих инструментов на тяжелых станках показали, что традиционный набор ограничений, применяемых при оптимизации режимов резания на станках средних типоразмеров, нуждается в уточнении и дополнительных исследованиях.
Исследование ограничений на регламенты эксплуатации инструмента на тяжелых станках производилось на основе статистических данных информационного банка, организованного на базе ПК и включающего около 3000 случаев обработки деталей на тяжелых станках [1].
29
ISBN 966-7851-19-2 Надійність інструменту та оптимізація технологічних систем. №14 2003.
Основная часть
Определялся закон распределения величин, параметры законов, средние и максимальные значения, степень их рассеивания для станков разных типоразмеров. Характеристикой типоразмера станка принят максимальный диаметр DС заготовки, устанавливаемой над станиной токарного станка, который является косвенным показателем виброустойчивости технологической системы.
Исследование условий эксплуатации режущего инструмента на тяжелых станках [1] позволило установить, что не все традиционные ограничения при установлении рациональных режимов резания необходимо учитывать на тяжелых станках Статистические исследования показали, что при обработке на тяжелых станках ни сила резания, допускаемая механизмами станка, ни крутящий момент, не являются ограничениями на режимы резания. Мощность резания превышает эффективную мощность только для станков с Dс<1250 мм (рис.1). Существенным ограничением на режимы резания при обработке на тяжелых станках существующих конструкций является масса детали, не позволяющая в ряде случаев увеличивать частоту вращения.
Снижение средней скорости резания на тяжелых станках по сравнению со средними и мелкими станками, кроме увеличенного сечения среза, может быть объяснено тем, что указанные скорости требуют в некоторых случаях применение частоты вращения шпинделя станка, находящегося на пределе возможностей вращения тяжеловесных деталей на станках существующих конструкций, а также на пределе психофизиологических возможностей станочника.
На рис. 1 изображено распределение применяемой частоты вращения n шпинделя тяжелых токарных станков. Заштрихованная область распределения показывают ограничение станка (модели ОАО КЗТС) на частоту вращения деталей с максимальной, с точки зрения прочности конструкции станка, массой и деталей, масса которых равна 1/2 максимальной массы, допускаемой конструкцией станка.
30
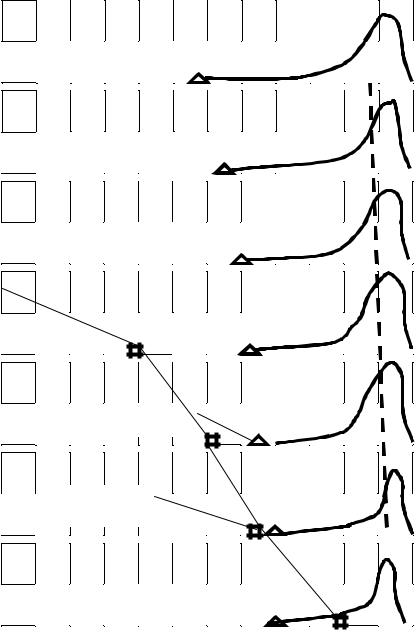
ISBN 966-7851-19-2 Надійність інструменту та оптимізація технологічних систем. №14 2003.
Dc, мм |
f(N) |
|
|
||
4000 |
1 |
|
|
0,5 |
|
|
0 |
|
3200 |
1 |
|
|
||
|
0,5 |
|
2500 |
0 |
|
|
||
|
1 |
|
|
0,5 |
|
2000 |
0 |
|
|
||
|
1 |
|
1600 |
0,5 |
|
0 |
||
|
||
|
1 |
|
1250 |
0,5 |
|
|
Nmax |
|
|
0 |
|
|
1 |
1000 |
|
Nдоп |
|
0,5 |
|
|
|
||
|
|
|
|
0
1
|
|
|
|
|
|
|
|
|
0,5 |
|
|
|
|
|
|
|
|
|
0 |
90 |
80 |
70 |
60 |
50 |
40 |
30 |
20 |
10 |
0 |
N, кВт
Рисунок 1 – Распределения мощности резания f(N) на один суппорт тяжелого токарного станка
Область ограничений перекрывает различную часть поля рассеивания частот вращения шпинделя для станков с различным значением Dс, что связанно с конструктивными особенностями станков и еще раз подтверждает необходимость учета типоразмера станка при определении рациональных регламентов эксплуатации.
31

ISBN 966-7851-19-2 Надійність інструменту та оптимізація технологічних систем. №14 2003. |
||||||||||||
|
1 |
|
|
|
|
|
|
|
|
|
|
|
4000 |
0,75 |
|
|
|
|
|
|
|
|
для деталей с Qmax |
|
|
0,5 |
|
|
|
|
|
|
|
|
|
|||
|
|
|
|
|
|
|
|
|
|
|
||
|
0,25 |
|
|
|
|
|
|
|
для деталей с Q=0.5Qmax |
|||
|
0 |
|
|
|
|
|
|
|
||||
|
|
|
|
|
|
|
|
|
|
|
|
|
|
1 |
|
|
|
|
|
|
|
|
|
|
|
3200 |
0,75 |
|
|
|
|
|
|
|
|
|
|
|
0,5 |
|
|
|
|
|
|
|
|
|
|
|
|
0,25 |
|
|
|
|
|
|
|
|
|
|
|
|
|
|
|
|
|
|
|
|
|
|
|
|
|
|
0 |
|
|
|
|
|
|
|
|
|
|
|
2500 |
1 |
|
|
|
|
|
|
|
|
|
|
|
0,75 |
|
|
|
|
|
|
|
|
|
|
|
|
|
|
|
|
|
|
|
|
|
|
|
|
|
|
0,5 |
|
|
|
|
|
|
|
|
|
|
|
|
0,25 |
|
|
|
|
|
|
|
|
|
|
|
|
0 |
|
|
|
|
|
|
|
|
|
|
|
|
1 |
|
|
|
n = 185 − 50 lg Dc |
|
|
|||||
2000 |
0,75 |
|
|
|
|
|
||||||
0,5 |
|
|
|
|
|
|
|
|
|
|
|
|
|
0,25 |
|
|
|
|
|
|
|
|
n max |
|
|
|
0 |
|
|
|
|
|
|
|
|
|
|
|
|
1 |
|
|
|
n Q max |
|
|
|
|
|
|
|
1600 |
0,75 |
|
|
|
|
|
|
|
|
|
||
|
|
|
|
|
|
|
|
|
|
|
||
0,5 |
|
|
|
|
|
|
|
|
|
|
|
|
0,25 |
|
|
|
|
|
|
|
|
|
|
|
|
|
|
|
|
|
|
|
|
|
|
|
|
|
|
0 |
|
|
|
|
|
|
|
|
|
|
|
1250 |
1 |
|
|
|
|
|
|
|
|
n 0.5Qmax |
|
|
0,75 |
|
|
|
|
|
|
|
|
|
|||
|
|
|
|
|
|
|
|
|
|
|||
|
0,5 |
|
|
|
|
|
|
|
|
|
|
|
|
0,25 |
|
|
|
|
|
|
|
|
|
|
|
|
0 |
10 |
20 |
30 |
40 |
50 |
60 |
70 |
80 |
90 |
100 |
n, |
|
0 |
|||||||||||
|
|
|
|
|
|
|
|
|
|
|
|
об/мин |
|
Рисунок 2 – Распределения частоты вращения шпинделя f(n), |
|
||||||||||
|
|
|
применяемой на тяжелых токарных станках |
|
|
Для учета данного ограничения были использованы рекомендации по определению предельной частоты вращения в зависимости от массы детали, (рис.2), разработанные в АОА «Краматорский завод тяжелого станкостроения».
При исследовании периода стойкости режущего инструмента тяжелых токарных станков был отмечен рост фактической стойкости режущего инструмента при переходе от станков с Dс≤1600 мм к более крупным
32
ISBN 966-7851-19-2 Надійність інструменту та оптимізація технологічних систем. №14 2003.
станкам. Это можно объяснить следующими причинами: а) замена инструмента производится с суппортной площадки, а не с пола (рис.7.9); б) увеличивается размер резца (Н=80 мм вместо Н=60 мм) и его масса ( 10 кг вместо 6 кг); в) растут габариты деталей и ухудшается наблюдаемость зоны резания; г) растет масса деталей, их стоимость.
Однако роль человека можно оценить так же, как элемент аппаратуры, т.е. путем использования входных и выходных параметров. Это дает возможность для описания характеристик человека и машины пользоваться общим языком и применять один и тот же математический аппарат.
С точки зрения надежности, как было показано ранее (глава 4), система "станок-инструмент-деталь-человек" при механической обработке деталей на тяжелых токарных станках является последовательной системой с восстановлением, так как отказ любого элемента этой системы приводит к прекращению ее функционирования. Главным элементом системы, обеспечивающим восстановление ее работоспособности является человек. Отказы системы, т.е. события, нарушающие ее функционирование образуют поток требований к станочнику, характеризуемый интенсивностью отказов λ. Восстановление работоспособности системы может характеризоваться интенсивностью восстановлений µ. Обе эти величины являются составляющими коэффициента готовности технологической системы.
Предположим, что наработки на отказ и восстановление технологической системы, обслуживаемой станочником, распределена согласно экспоненциальному закону. В этом случае потоки требований к станочнику являются простейшими потоками Пуассона. Интенсивность отказов суммарного потока требований λ равна сумме интенсивностей λi каждого вида
n
λ = ∑λi
отказов i=1 ,
где n - число требовании потока. Интенсивность суммарного потока восстановления µ определяется в зависимости от интенсивностей отказов λi и восстановлений µi каждого вида
|
n |
|
|
|
|
|
∑λi |
||||
µ = |
i =1 |
|
|||
|
|||||
|
n |
λ . |
|||
|
∑ |
i |
|
|
|
µi |
|||||
|
i =1 |
Для рассматриваемой системы "станок-инструмент-деталь-человек" элементами являются события, требующие вмешательства в процесс обра-
33
ISBN 966-7851-19-2 Надійність інструменту та оптимізація технологічних систем. №14 2003.
ботки детали одного или нескольких станочников: смены резца, настройки или поднастройки на размер, уборки стружки из зоны резания и т.д.
Величина коэффициента готовности системы "станок-инструмент- деталь-человек косвенно свидетельствует об уровне психофизиологическом напряженности станочника. Предположим, что условия нагружения технической части системы остаются постоянными, т.е. картина ее отказов неизменна (λ = const), а интенсивность восстановления увеличивается. Это значит, что повысилась интенсивность физической работы станочника: быстрее производится замена резца, переключение рукояток и т.п. Интенсивность суммарного потока восстановления определяемая коэффициент готовности системы в этом случае повышается. При неизменной интенсивности восстановления µi повышение интенсивности отказов элементов технической части системы λi приводит также к повышению психофизиологической нагрузки на рабочего, так как увеличивается общее число вмешательств рабочего в процесс обработки, приводящих к увеличению интенсивности суммарного потока восстановлений.
Все ручные приемы станочника по управлению станком разбиты на группы: поднастройка на размер, настройка на новый переход, смена резца, изменение режимов резания, уборка стружки, активное наблюдение - время, когда рабочий наблюдает за зоной резания визуально, в остальное время, не заполненное ручными приемами, он следит за процессом по звуку. Статистическими исследованиями подтверждено, что время наработки на различные требования к рабочему, в перечисленных выше группах, подчиняется экспоненциальному закону распределений. Интенсивность отказов суммарных потоков имеет колебание по исследованным операциям от 0,015 до 0,307. Из этого следует, что среднее время наработки на любое требование к рабочему в суммарном потоке равно от 14,3 до 3,3мин.
Установлено, что коэффициент готовности для различных обрабатываемых деталей, условий производства и операций на станках с Dс>1600 мм обладает относительным постоянством (колеблется от 0,8 до 0,86 ). в среднем равен 0,83 при обслуживании технологической системы одним станочником.
Статистические исследования показали, что фактические режимы резания на станках с Dс>1600 мм - ниже режимов минимальных приведенных затрат.
С другой стороны, необходимо учесть, что режимы резания устанавливаются станочником, сообразуясь с его психофизиологическими возможностями. Поэтому фактический коэффициент готовности системы,
34
ISBN 966-7851-19-2 Надійність інструменту та оптимізація технологічних систем. №14 2003.
равный 0,83, можно считать ограничением на режим резания (период стойкости), обусловленным психофизическими возможностями станочника. При наличии второго станочника (подручного) этот коэффициент может быть повышен до 0,94 [3].
Разработка рациональных регламентов эксплуатации для инструментов сборной конструкции производится с учетом того, что среднее время восстановления снижается. Определяем интенсивность суммарного потока требований к рабочему при условии сохранения коэффициента готовности системы равным 0,83 и τз=5 мин. В этом случае интенсивность восстановления согласно таблице 7.1 - λсб=0,1714. Условно предположив, что даже если потоки требований по настройке инструмента на размер, уборке стружки, настройки на переход, изменения режимов резания и наблюдения за зоной обработки останутся неизменными, период стойкости инструмента не должен быть ниже 60 мин.
Выводы
Разработана система математических моделей и целевых функций, которая позволяет произвести многокритериальную оптимизацию режимов резания и расхода инструмента для базовых условий качества эксплуатации и включает новые, ранее не применяемые ограничения: по надежности инструмента и технологической системы, по массе обрабатываемых деталей, по психо-физической нагрузке на станочника -, применение которых позволяет получить оптимальные элементы режимов резания в области, свободной от ограничений.
Приведенные данные показывают целесообразность более широкого внедрения станков с программным управлением и устройствами для автоматической замены инструмента.
Литература
1Клименко Г.П. Анализ условий обработки деталей на тяжелых станках на основе информационного банка данных .//Резание и инструмент в технологических системах. Межд. научн.-техн. сборник. - Харьков: ХГПУ, 1997. - Вып.51.- С.122-127.
2Клименко Г.П. Создание общемашиностроительных нормативов режимов резания с учетом требования тяжелого машиностоения// Надійність різального інструменту та оптимізація технологічних систем. збірник статей. - Краматорськ: ДДМА, 1999.- Вип. 8.- С.12-24.
3Клименко Г.П. Обеспечение оптимального уровня надежности твердосплавных резцов для тяжелых станков// Высокие технологии в машиностроении.- Харьков:
ХГПУ, 1999.- С.48-49.
35