
mehanizaciya i elektrifikaciya
.pdfПосле исходной настройки жатки включают агрегат в работу и проезжают 20...25 м, со скоростью 1,39...1,67 м/с.
Останавливают жатвенный агрегат и проверяют качество его работы: высоту среза, ширину валка, потери за жаткой, прямолинейность и равномерность укладки валка. При отклонениях от агротехнических требований агрегат регулируют повторно.
Уточняют скоростной режим движения агрегата по результатам проверки качества его работы. При хорошем качестве работы применяют повышенные скорости движения.
После изменения скорости движения вновь проверяют качество работы. Потери за жаткой не должны превышать одного - двух стеблей на 1 м2.
При объездах препятствий валок укладывают не ближе, чем 1,5 м от необработанной части поля.
5.3. Обмолот валков
Подбор и обмолот валков начинают в момент наступления полной спелости зерна через пять - семь дней после скашивания. Его проводят плавно, без разрыва и сгруживания валка. Комбайн с подборщиком должен перемещаться по полю, не повреждая соседние валки, не разваливая копны соломы, сброшенные во время предыдущего прохода комбайна.
Копны соломы выгружают на загоне рядами, параллельными короткой его стороне, число рядов которых зависит от соломистости убираемой культуры. Растягивание копен при выгрузке из копнителя комбайна не допускается.
Направление движения агрегата при подборе и обмолоте валков должно совпадать с направлением движения жатвенного агрегата. При подборе сдвоенного валка движение должно совпадать с направлением движения первого прохода жатвенного агрегата. Комбайн с платформой-подборщиком должен двигаться по полю тем же способом, что и жатвенный агрегат.
Перед работой в загоне выполняют технологическую настройку рабочих органов агрегата применительно к условиям данного поля. В дальнейшем при переездах с одного поля на другое корректируют настройку комбайна. Для этого осматривают поле и в зависимости от состояния хлебов в валках регулируют зазоры подбарабанья, устанавливают раствор жалюзийных решет и угол наклона удлинителя грохота, обороты молотильного барабана, вентилятора и корректируют их в процессе работы.
Вначале устанавливают несколько завышенные молотильные зазоры, которые в процессе обмолота постепенно уменьшают до тех пор, пока не будет достигнут хороший вымолот зерна.
После каждого изменения регулировки молотильного аппарата проверяют качество обмолота, прощупывая 50 колосков в соломе и полове, взятых в разных местах копны. Обмолот считают удовлетворительным, если в проверенных колосьях найдется не более двух - трех зёрен.
71
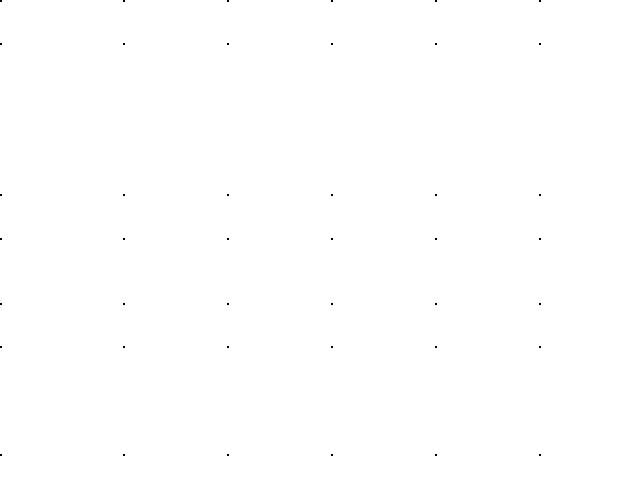
Через 50…100 м останавливают комбайн и проверяют потери за его молотилкой. При отклонениях потерь зерна от агротехнических требований уточняют скоростной режим движения комбайна.
5.4. Зерноуборочные комбайны
Зерноуборочные комбайны предназначены для уборки прямым комбайнированием, а также подбора и обмолота валков зерновых культур. Они бывают прицепные и самоходные. Наиболее распространены самоходные. По типу мо- лотильно-сепарирующих рабочих органов подразделяются на две группы: с классической молотилкой и аксиально-роторной. К первой группе относятся комбайны «Дон-1200», «Дон-1500», «Енисей-1200», СК-5М «Нива» и СК-6 «Колос», ко второй - самоходный комбайн СК-10 «Ротор».
Устройство и принцип работы перечисленных комбайнов первой группы в основном одинаковые. Различие заключается в размерах, пропускной способности молотилки и устройстве отдельных агрегатов. Техническая характеристика зерноуборочных комбайнов отечественного производства представлена в таблице 5.2.
Таблица 5.2.Техническая характеристика комбайнов
Показатель |
СК-5М |
«Енисей- |
«Дон- |
«Дон- |
СК-10 |
||||
«Нива» |
1200» |
1200» |
1500» |
«Ротор» |
|||||
|
|
|
|
||||||
Пропускная |
|
|
|
|
|
||||
способность |
|
|
|
|
|
||||
молотилки |
|
|
|
|
|
|
|||
при |
отноше- |
5…6 |
6,5…7 |
5,5…6,5 |
7…8 |
10…12 |
|||
нии |
зерна |
к |
|
|
|
|
|
||
соломе |
1:1,5 |
|
|
|
|
|
|||
кг/с |
|
|
|
|
|
|
|
|
|
Марка |
дви- |
СМД-21 |
СМД-22 |
СМД-23 |
СМД-31А |
СМД-31 |
|||
гателя |
|
|
|||||||
|
|
|
|
|
|
|
|||
Мощность |
|
|
|
|
|
|
|||
двигателя, |
|
102 |
106,7 |
118 |
178 |
184 |
|||
кВт |
|
|
|
|
|
|
|
|
|
Ширина |
|
за- |
4,1; 5 |
4,1; 5 |
5; 6 и 7 |
6; 7 и 8,6 |
6; 7 и 8,6 |
||
хвата, м |
|
|
|||||||
|
|
|
|
|
|
|
|||
Скорость |
|
|
|
|
|
|
|||
движения |
|
|
|
|
|
|
|||
(рабочая), |
|
10 |
8,8 |
10 |
10 |
10 |
|||
км/ч, |
не бо- |
|
|
|
|
|
|||
лее |
|
|
|
|
|
|
|
|
|
Масса, т |
|
|
8,06 |
9,4 |
11,5 |
13,44 |
14,8 |
Пропускная способность молотилки зерноуборочного комбайна (П) - это количество хлебной массы, обрабатываемой комбайном в единицу времени при
72

допустимом уровне потерь за молотилкой. Принятая единица измерения пропу-
скной способности молотилки - кг/с. |
|
Хлебная масса - это то, что комбайн берет с поля, т.е. |
|
Хм = З + С |
(5.1) |
где: 3 - зерновая часть урожая, выраженная в весовых частях или ц/га; С - соломистая часть урожая, выраженная в весовых частях или ц/га.
Паспортная пропускная способность молотилки измеряется при испытаниях комбайна на сухой (влажность не выше 17%) и чистой хлебной массе при отношении массы зерна к массе соломы 3:С = 1:1,5.
Паспортная пропускная способность базовой модели комбайна указана в его марке. Так, для комбайна СК-5 "Нива" паспортная пропускная способность молотилки ПП = 5,2 кг/с. В результате модернизации она, как правило, увеличивается. Для некоторых марок комбайнов паспортная пропускная способность молотилки приведена ниже.
Таблица 5.3. Паспортная пропускная способность молотилок комбайнов
Марка ком- |
СК- |
СК-6II |
СКД-6 |
Енисей- |
Дон- |
СК-10- |
байна |
5А(М) |
«Колос» |
«Сибиряк» |
1200 |
1500 |
12 «Ро- |
|
«Нива» |
|
|
|
|
тор» |
Паспортная |
5,5 |
7,9 |
6,3 |
6,3 |
8,0 |
10,0- |
пропускная |
|
|
|
|
|
12,0 |
способность, |
|
|
|
|
|
|
кг/с |
|
|
|
|
|
|
Примечание: в марках комбайнов "Енисей" и "Дон" числовое обозначение - ширина молотилки в миллиметрах
Фактическая пропускная способность молотилки комбайнов зависит от многих причин: отношения массы зерна к массе соломы, влажности, полеглости и засоренности. На уборке длинносоломистых, засоренных и влажных хлебов она существенно ниже паспортной. Так, для комбайна "Нива" в условиях Нечерноземья среднемноголетнее значение фактической пропускной способности молотилки Пф = 3,7 кг/с. В то же время при испытаниях на уборке сухих короткостебельных хлебов она достигала 13-15 кг/с.
Заметим, что фактическая пропускная способность молотилки комбайна ограничена не столько возможностями молотильного аппарата или двигателя комбайна, сколько просеивающей способностью очисток. Это очистка соломистого вороха (соломотряс) и зерновая очистка с ее решетами (рис. 5.2).
Зерновая составляющая, которая не успеет просеяться через жалюзийные поверхности клавиш соломотряса и решет, сходит в копнитель или другое устройство для сбора незерновой части урожая. А это потери зерна.
Фактическую пропускную способность молотилки комбайна ориентировочно можно определить по фактическому отношению массы зерна к массе соломы 1:Сф, составив пропорцию:
Пп соответствует 1:1,5 Пф соответствует 1 :Сф
73

Из пропорции:
П |
ф |
1,5 |
Пп |
(5.2) |
|
Сф |
|||||
|
|
|
|||
|
|
|
|
Комбайн «Дон-1500» (рис. 5.2) состоит из жатки, наклонной камеры, молотилки шириной 1500 мм, бункера, копнителя, двигателя, трансмиссии, ходовой системы, гидросистемы, кабины, органов управления, электрооборудования и электронной системы контроля технологического процесса и состояния агрегатов. В зависимости от урожайности и состояния убираемой культуры на комбайне монтируют жатки шириной захвата 6,7 или 8,6 м.
Жатка, фронтально навешенная на молотилку, может копировать рельеф поля. На ней смонтированы делители, мотовило, режущий аппарат, шнек, битер, копирующие башмаки, в наклонной камере - транспортер.
Молотилка состоит из молотильного аппарата, включающего в себя барабан и подбарабанье, отбойного битера, соломотряса, транспортной доски, очистки,
Рисунок 5.2. Комбайн «Дон-1500»:
1 - мотовило; 2 - шнек жатки; 3 - промежуточный битер; 4 - наклонная камера; 5 - транспортер; 6 - бильный барабан; 7 - решетчатая дека; 8 - отбойный битер; 9 - бункер; 10 - соломотряс; 11 - корпус молотилки; 12 - копнитель; 13 - половонабиватель; 14, 18 - скатные доски; 15, 17 - верхнее и нижнее решета; 16, 19 - колосовой и зерновой шнеки; 20 - вентилятор; 21 - грохот; 22 – домолачивающее устройство; 23 - режущий аппарат
зернового и колосового шнеков, зернового и колосового элеваторов, домолачивающего устройства. На крыше молотилки установлен бункер, снабженный загрузочным и выгрузным шнеками.
Мотовило 1 подводит стебли к режущему аппарату 22 и укладывает их после среза на платформу. Шнек 2 сужает поток стеблей (хлебную массу) и направляет их к битеру 3, а от него - к плавающему транспортеру 5. Нижняя ветвь транспортера перемещает стебли в молотильный аппарат. Вращающийся барабан 6 наносит удары по потоку хлебной массы, перемещает ее по деке 7 и обмолачивает.
74
Обмолоченная хлебная масса (грубый ворох) состоит из соломы, зерна, половы и примесей. Основная часть (70...80 %) зернового вороха в процессе обмолота проходит сквозь отверстия подбарабанья (деки) и падает на транспортную доску. Солома с остатками зернового вороха выбрасывается барабаном с большой скоростью. Отбойный битер 8 уменьшает скорость перемещения соломы и направляет ее на соломотряс 10, ступенчатые клавиши которого совершают круговые движения и интенсивно перетряхивают солому. Зерно и мелкие примеси просыпаются сквозь отверстия клавиш и сходят по их наклонному дну на транспортную доску. Гребенки клавиш продвигают солому к выходу из молотилки.
Зерновой ворох, выделенный подбарабаньем и соломотрясом, по транспортной доске ссыпается на верхнее жалюзийное решето 15 очистки. Зерно просыпается сквозь его просветы и падает на нижнее решето 17. Под решета направлена струя воздуха от вентилятора 20, которая уносит в копнитель легкие примеси (полову). Очищенное зерно, прошедшее сквозь нижнее решето, собирается в желобе зернового шнека 19 и скребковым транспортером загружается в бункер 9.
В процессе обмолота часть колосков отламывается от стеблей, и они необмолоченными поступают на очистку. Такие колоски сходят с верхнего решета на его удлинитель и сквозь просветы последнего просыпаются в желоб колосового шнека 16, который сбрасывает их на наклонный транспортер (элеватор), а последний направляет в домолачивающее устройство 22.
Вращающийся ротор устройства во взаимодействии с зубчатым подбарабаньем обмолачивает колоски и сбрасывает образовавшийся ворох на транспортную доску. В дальнейшем этот ворох поступает на верхнее решето. Из бункера зерно выгружается шнеком на ходу или при остановках машины.
Для сбора соломы и половы на комбайн навешивают гидрофицированный копнитель. В него солома подается соломонабивателем, а полова - половонабивателем. Сформированная копна выбрасывается на поле.
При необходимости на место копнителя устанавливают измельчитель соломы ПКН-1500, работающий по различным технологическим схемам (сбор измельченной соломы и половы в прицепные тележки; полова - в тележку, солома - в валок; полова - в тележку, солома разбрасывается по полю; измельченная или неизмельченная солома с половой укладывается в валок; разброс соломы с половой по полю).
При раздельном способе уборки применяют подборщики для подбора хлебной массы из валка и подачи ее на платформу жатки. Подборщик монтируют на жатке, с которой снимают мотовило. Подборщики бывают барабанные и поло- тенно-транспортерные.
Барабанный подборщик (рис. 5.3. а, в) предпочтителен при подборе валков длинностебельных хлебов (более 70...80 см) при малой засоренности полей и высоте среза 15...20 см. Он состоит из каркаса с копирующими башмаками, подбирающего грабельного механизма и привода.
Полотенно-транспортерный подборщик (рис. 5.3. г) в отличие от барабанного обеспечивает сбор урожая с меньшими потерями зерна при подборе
75
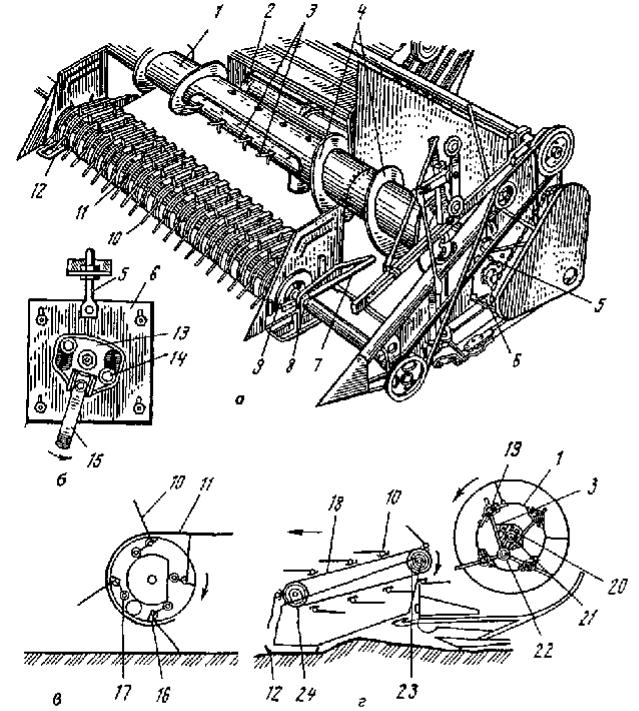
валков короткостебельных хлебов, а также легкоосыпающихся культур. Его основные части: рама, транспортер, копирующие катки и механизм привода.
Рисунок 5.3. Подборщик и шнек жатки:
а) - общий вид; б) - механизм регулирования положения пальцев шнека; в) - схема работы барабанного подборщика; г) - схема работы полотённо-транспортёрного подборщика; 1 - шнек; 2 - транспортер; 3 - пальцы шнека; 4 - витки шнека; 5 - винт подвески шнека, 6 -
плита подвески шнека; 7 - поддержка; 8 - вал подборщика, 9 - боковина, 10 - палец подборщика; 11 - кольцо-скат; 12 - башмак; 13 - щека; 14 - болт, 15 - рычаг; 16 - труба; 17 - кривошип с роликом; 18 - полотно; 19 - глазок; 20 - разъемная щека; 21 - ось; 22 - труба пальцев; 23 - ведущий вал; 24 — ведомый вал
76
ГЛАВА 6. Машины послеуборочной обработки зерна
6.1. Агротехнические требования к очистке и сортированию зерна
При уборке зерновых и других культур в бункер комбайна вместе с зерном поступают примеси — колосья, полова, кусочки соломы, семена сорняков, минеральные частицы.
Очистка необходима для того, чтобы удалить из всего зерна примеси, а также щуплые и поврежденные зерна.
Сортирование зерна предусматривает разделение его на сорта с целью выделения высококачественного посевного материала, а также продовольственного и фуражного.
Калибрование — это разделение очищенных семян на фракции по их размерам.
Очистка и сортирование сводятся к разделению (сепарации) зерновой смеси на отдельные фракции, различающиеся по каким-либо свойствам или признакам (например, размерам, свойству поверхности, плотности и др.).
Зерно, обработанное на зерноочистительных и сортировальных машинах, должно соответствовать требованиям стандартов. В процессе обработки зерна рабочие органы машин не должны повреждать его. Машины должны быть приспособлены для очистки и сортирования семян различных культур, удобны в эксплуатации и регулировках, а также безопасны в работе.
6.2. Способы очистки и сортирования
Разделение смесей в воздушном потоке основано на различии в массе и аэродинамических свойствах семян и примесей. При относительном движении тела в воздухе возникает сопротивление, которое зависит от формы, состояния поверхности, массы тела и расположения его в воздушной среде.
Совокупность свойств, определяющих способность частиц перемещаться под воздействием воздушного потока, называют аэродинамическими свойствами. Чем большее сопротивление воздуха испытывает частица, тем медленнее она движется и тем позднее упадет.
Воздушный поток в зерноочистительных машинах создается вентиляторами: нагнетательными или всасывающими.
Для разделения семян по аэродинамическим свойствам применяют горизонтальный, наклонный или вертикальный воздушный поток, создаваемый центробежным вентилятором.
В наклонном или горизонтальном воздушном потоке зерновая смесь, поступившая из питающего ковша, подвергается воздействию воздушной струи, в результате чего тяжелые зерна, имеющие малое отклонение при падении, будут попадать в первое отделение короба, а легкие примеси будут унесены дальше
— в следующее отделение короба.
77
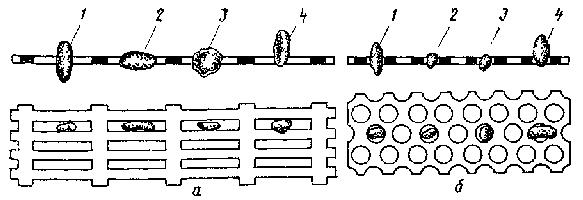
В вертикальном восходящем потоке зерно подается на сетку или непосредственно в воздушный поток. Скорость потока регулируют так, чтобы зерно оставалось на сетке, а легкие примеси поднимались и поступали в осадочную камеру.
Разделить зерновую смесь воздушным потоком можно только в том случае, если критические скорости семян и примесей различны.
Под критической скоростью, или скоростью витания данного тела, понимают скорость вертикального восходящего воздушного потока, при которой оно может находиться во взвешенном состоянии.
Скорость витания зерна пшеницы в среднем составляет 9...12 м/с, а семян сорняков — 2...7 м/с.
Разделение зерновой смеси в подвижном воздушном потоке аналогично также процессу, при котором частицы смеси с помощью механических устройств движутся в неподвижном воздухе.
Разделение по толщине и ширине зерна проводят на плоских или цилиндрических решетах.
Плоское решето представляет собой металлический лист с пробитыми в нем отверстиями одинакового размера (рис. 6.1).
Рисунок 6.1. Разделение семян на решетах с отверстиями:
а) — продолговатыми; б) - круглыми; 1, 2 и 3 — семена проходят сквозь решето; 4 — семена не проходят сквозь решето
Для разделения семян по толщине применяют решета с продолговатыми отверстиями, а для разделения по ширине — с круглыми. В первом случае рабочим размером отверстия служит его ширина, во втором — диаметр. Решета стандартизированы и значатся под номером, соответствующим размеру ширины или диаметра отверстия.
Для очистки гречихи и выделения сорных семян, имеющих трехгранную форму, применяют решета с отверстиями треугольной формы, а для очистки семян льна — с чечевицеобразными отверстиями. В этих случаях разделяют семена по форме их поперечного сечения, то есть одновременно по двум параметрам — ширине и толщине.
Вместо пробивных решет с круглыми отверстиями применяют иногда проволочные решета с квадратными отверстиями — плетеные и тканые.
78

Фракция прохода — это масса частиц, размер которых меньше рабочего размера отверстии решета, то есть проходящих сквозь него.
Фракция схода образуется более крупными частицами, не прошедшими сквозь отверстия решета и сошедшими с него в конце.
Живое сечение решета — это суммарная площадь всех его отверстий. Отношение живого сечения к общей площади решета называется относительным живым сечением. Чем выше этот показатель, тем интенсивнее и при меньшей забиваемости будет работать решето.
Разделение семян по длине происходит в триерных цилиндрах с внутренней ячеистой поверхностью (рис. 6.2). Рабочим размером, определяющим разделение, служит диаметр ячеек. При вращении цилиндра короткие зерна запа-
|
дают в ячейки глубже, чем длинные. |
|
Поэтому из ячеек сначала выпадают |
|
длинные, а затем короткие зерна. |
|
Первые, оставаясь в цилиндре, пере- |
|
мещаются к его выходу, а вторые по- |
|
падают в желоб, из которого удаляют- |
|
ся шнеком. |
|
В соответствии с ГОСТом преду- |
|
смотрено 22 размера ячеек диаметром |
|
от 1,6 до 12,5 мм, что обеспечивает |
|
очистку семян зерновых и зернобобо- |
|
вых культур, трав и льна, а также ка- |
|
либровку семян кукурузы. |
|
Наряду с цилиндрическими три- |
Рисунок 6.2. Схема работы триерно- |
ерными поверхностями применяются |
го цилиндра: 1 — шнек; 2 — желоб, 3 — |
и нецилиндрические ячеистые по- |
триерный цилиндр |
верхности. Однако принцип их рабо- |
|
ты один и тот же. |
Разделение семян по плотности применяют для получения наиболее жизнеспособных семян, а также для отделения трудноотделимых примесей (например, куриного проса от риса, дикой редьки от гречихи). Такая сепарация возможна мокрым (в воде или растворах различной концентрации) и сухим способами.
С ух о й сп о со б разделения по плотности применяется в пневматических сортировальных столах.
Мо кр ы й сп о со б ввиду сложности и громоздкости применяется в редких случаях.
Разделение по форме и состоянию поверхности применяют в тех случаях, когда по другим свойствам частицы мало отличаются одна от другой. Семена могут иметь различную поверхность (гладкую, шероховатую, пористую, бугорчатую, ямчатую, покрытую пушком) и различную форму (плоскую, продолговатую, шарообразную, трехгранную).
Совокупность формы и состояния поверхности семян определяет вид и размер коэффициента их трения по рабочей поверхности. Для сепарации зерна по
79

этому признаку используют фрикционные рабочие поверхности. В качестве устройств, имеющих наклонные фрикционные поверхности, применяются горки, винтовые сепараторы-змейки, фрикционные триеры.
Для очистки семян клевера, люцерны, льна и других культур от таких трудноотделимых семян сорных растений, как повилика, смолевка, плевел и другие, используют шероховатость поверхности последних и способность их удерживать на этой поверхности порошок тонкого помола, содержащий железо.
Разделение семян по другим признакам. Кроме перечисленных выше признаков разделения зерновых смесей, используют также различия семян по их упругости, цвету и электрическим свойствам.
Рисунок 6.3. Схемы устройств для разделения зернового материала по элек-
трическим свойствам:
а) - в статическом поле, б) - в поле коронного разряда, в) - по диэлектрической проницаемости; 1 - бункер; 2 – барабан; 3 - щетка; 4, 5 и 6 – лотки; 7 - отрицательно заряженный электрод; 8 - коронирующий электрод; 9 - перфорированный электрод, 10 - бифилярная обмотка; 11 - изолятор
По уп р уго сти семена разделяют на отражательных сортировальных сто-
лах.
По ц ве т у смеси разделяют на устройствах с фотоэлементами.
Р а зд е л ен и е с емян в э л ек тр и чес ко м п о ле основано на различии в электропроводности, диэлектрической проницаемости и других электрических свойств. При этом могут быть использованы (рис. 6.3) электрический, коронный и диэлектрический методы разделения.
Со че та н и е д в ух п р и з н ако в также иногда применяют для разделения зерновых смесей. Так, например, в центробежно-пневматическом сепараторе, имеющем в качестве основных рабочих органов решетчатый барабан и электровентилятор, частицы очищаемой смеси на поверхности барабана находятся под действием силы присасывания и центробежной силы. Результирующая сила определяет место выхода фракций, составляющих исходную смесь.
80