
Методички / Курсовое проектирование деталей машин
.pdfСплавы цветных металлов выполняют на основе алюминия, меди, олова и других металлов. Сплавы на основе алюминия и магния имеют высокую удель-
ную прочность. Алюминиевые сплавы подразделяют на деформируемые (дюра-
люмины) и литейные (силумины). Применяют для корпусных деталей и в авиаци-
онной технике.
Многие цветные металлы используют как антифрикционные материалы,
применяемые в узлах трения. Латунь – сплав меди с цинком. Однофазная латунь
– деформируемая (например, патронная латунь), двухфазная – литейная, исполь-
зуемая как антифрикционный материал.
Бронза – сплав меди со всеми элементами, кроме цинка. Обладает высоки-
ми антифрикционными свойствами, сопротивлением коррозии и технологично-
стью. Наилучшие антифрикционные свойства у оловянистых бронз, например,
БрО10Ф1 ГОСТ 613-79. Безоловянистые бронзы, например, БрА10Ж4Л ГОСТ
493-79, обладают высокими механическими характеристиками, но их антифрик-
ционные свойства хуже, чем оловянистых.
Пластические массы – материалы на основе высокомолекулярных органи-
ческих соединений. По природе смол пластмассы подразделяют на термореактив-
ные и термопластичные. Термореактивные смолы в процессе изготовления под действием высокой температуры становятся неплавкими (текстолит, гетинакс,
стеклопласты и др.). Термопластичные пластмассы, размягчающиеся при высо-
кой температуре, пригодны для повторного использования (полиэтилен, фторо-
пласты, полиамиды, полиуретаны и др.).
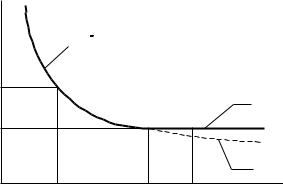
11. РАСЧЁТ ЦИЛИНДРИЧЕСКОЙ ЗУБЧАТОЙ ПЕРЕДАЧИ
Основными критериями расчета зубчатых передач являются кон-
тактная и изгибная прочность.
11.1.Коэффициент долговечности
Взубчатом зацеплении передача движения осуществляется за счет непо-
средственного контакта сопряжённых зубьев. Наиболее распространено эволь-
вентное зацепление. Теория зубчатого зацепления изложена в учебных пособиях
[4, 5]. Зубчатые передачи рассчитаны на длительную работу. При наработке меньше базовой размеры передачи могут быть уменьшены вследствие повышения предельных и допускаемых напряжений. На рис. 6 приведена кривая выносливо-
сти материала, по которой принимают предел выносливости lim0 . Он соответ-
ствует базовому числу циклов NG. При числе циклов нагружения N < NG предель-
ное напряжение будет иметь большее значение и его следует принимать по
lim
криволинейному участку, который соответствует уравнению:
|
m N 0 |
m N |
G |
const . |
(17) |
lim |
lim |
|
|
||
|
m N = const |
|
|
||
|
|
|
|||
' |
|
|
|
1 |
|
lim |
|
|
|
|
|
|
|
|
|
|
|
o |
|
|
|
|
|
lim |
|
|
|
|
|
|
|
|
|
2 |
|
N < NG |
NG |
|
N > NG |
N |
|
Рис. 6. Кривая выносливости |
|
Показатель степени т характеризует крутизну наклона кривой выносливо-
сти. Число циклов нагружения учитывают коэффициентами долговечности КНд и
КFд. При N NG КНд = КFд = 1. Эти коэффициенты также учитывают перемен-
ность нагрузки. При постоянной нагрузке класс Н 1,0. Он соответствует коэффи-

циенту эквивалентности KНE = 1. Коэффициент долговечности по контактным напряжениям определяют по формуле:
K HД K HE 3 |
N |
1 |
, |
(18) |
|
|
|||||
N HG |
|||||
|
|
|
|
где NHG — база контактных напряжений, принимать по табл. 4.
Таблица 4
База контактных напряжений
|
|
|
|
|
|
|
|
|
|
|
||
Средняя твёрдость поверхности |
НВ |
|
|
|
200 |
250 |
300 |
350 |
- |
- |
- |
|
|
|
|
|
|
|
|
|
|
|
|||
Средняя твёрдость поверхности |
|
|
|
|
- |
25 |
32 |
38 |
47 |
56 |
60 |
|
HR |
C |
|
||||||||||
|
|
|
|
|
|
|
|
|
||||
NHG, млн. циклов |
|
10 |
17 |
25 |
36 |
68 |
114 |
143 |
||||
|
|
|
|
|
|
|
|
|
|
|
|
|
Примечания. 1. Для промежуточных значений твёрдости базу контактных
напряжений определять методом линейной интерполяции.
2. В таблице приведена твёрдость поверхности в различных единицах изме-
рения (HB и HRC), что позволяет определить соответствие между ними.
Коэффициент долговечности по изгибу:
KFД KFE m |
|
N |
|
1, |
(19) |
|
|
|
|||||
NFG |
||||||
|
|
|
|
|
где NFG — база изгибных напряжений; m – показатель степени; принимать т = 6
и NFG = 10·106 при твёрдости сердцевины H 350НВ; т = 9 и NFG = 150·106 при твёрдости сердцевины H 40 HRC.
Коэффициент эквивалентности по изгибным напряжения KFE и базовый ре-
сурс t принимать по табл. 5.
|
|
|
|
|
|
|
|
|
|
Таблица 5 |
|
|
Коэффициенты эквивалентности |
|
|
||||||||
|
|
|
|
|
|
||||||
Класс |
Коэффициент |
Коэфф. эквива- |
Коэфф. эквива- |
Базовый |
|
||||||
нагрузки |
эквивалентности |
лентности KFE |
лентности KFE |
ресурс |
|
||||||
|
KНE |
при H<350 |
|
|
при H >40 |
|
|
|
|
t , час. |
|
|
НВ |
|
HR |
C |
|
||||||
Н 1,0 |
1,0 |
1,0 |
|
|
1,0 |
|
|
|
|
32000 |
|
|
|
|
|
|
|
|
|
|
|
|
|
Н 0,8 |
0,8 |
0,81 |
|
|
0,84 |
|
|
|
|
16000 |
|
|
|
|
|
|
|
|
|
|
|
|
|
Н 0,63 |
0,63 |
0,725 |
|
|
0,775 |
|
|
|
|
8000 |
|
|
|
|
|
|
|
|
|
|
|
|
|
Наработка (число циклов нагружения) при постоянной частоте вращения:
N 60cnt , (20)
где с — число потоков мощности, в планетарном редукторе оно равно числу сателлитов (с = пс); в обычных редукторах с = 1; п — частота вращения вала зуб-
чатой передачи, об/мин, t — машинное время (ресурс), ч; определяется по фор-
муле:
t L S 2008ПВ , |
(21) |
где L — срок службы, лет; S — число смен работы, рекомендуется принимать S
= 2; 2008 — число рабочих часов в году, равно 40 · 52 - 9 · 8 (40 — число рабо-
чих часов в неделю, 9 — количество праздничных дней в году, 8 — число часов работы в одну смену); ПВ — относительная продолжительность включения, при-
нимать ПВ = 0,15 при лёгком режиме, ПВ = 0,25 при среднем режиме, ПВ = 0,4
при тяжёлом режиме.
Принимать t не меньше базового ресурса (табл. 5). Коэффициент экви-
валентности по изгибу KFE принимают по классу нагрузки (табл. 4). В расчёты коэффициенты долговечности вводят лишь в том случае, когда они меньше еди-
ницы (КД 1), что приводит при расчёте зубчатых передач к уменьшению межо-
севого расстояния. Коэффициенты долговечности рассчитывают для каждого ко-
леса, принимая большее из двух значений.
11.2. Материалы зубчатых колёс и допускаемые напряжения
Зубчатые колёса в большинстве случаев изготовляют из сталей, подвергну-
тых либо нормализации или улучшению («сырые» стали), либо объёмной закалке или химико-термическому упрочнению («калёные» стали). Чугун применяют для колёс тихоходных открытых передач, шестерни в этом случае изготовляют из сталей обыкновенного качества (Ст5, Ст6).
Выбор марок сталей для шестерни и колеса зависит от желаемой стоимости зубчатой передачи и от предполагаемых габаритов редуктора. Выбор следует де-
лать из трёх групп сталей:
I группа — «сырые» стали, твёрдость обоих колёс Н 350 НВ; к ней отно-
сятся, в основном, качественные углеродистые стали, подвергнутые нормализа-
ции или улучшению. Материал шестерни необходимо принимать на 40...100 НВ
твёрже материала колеса для достижения равнопрочности колёс по изгибу: зуб шестерни в и раз чаще входит в зацепление, а форма зуба шестерни, характеризу-
емая коэффициентом формы зуба YF , хуже, чем колеса. Материалы I группы хо-
рошо прирабатываются.
II группа — «калёные» стали, твёрдость обоих колёс Н 40 HRC , она мо-
жет быть достигнута объёмной закалкой или химико-термической обработкой;
таким материалам присуща хрупкость; их стоимость наиболее высока. Материалы
IIгруппы не прирабатываются.
III группа — «высокий перепад твёрдостей», достигаемый шестерней из
«калёной» стали (Н1 40 HRC) и колесом из «сырой» стали (Н2 350 НВ); такое сочетание рекомендуется для косозубых и шевронных колёс. Приработка обес-
печивается за счёт высокой пластичности материала колеса. Наиболее распро-
странённые материалы зубчатых колёс приведены в табл. 6.
|
|
|
|
|
|
Таблица 6 |
|
Механические характеристики материалов зубчатых колёс |
|
||||
|
|
|
|
|
|
|
Марка |
Диаметр |
Термо- |
Твёрдость |
Твёрдость |
Предел |
Предел |
стали |
заготовки, |
обработка |
сердцеви- |
поверхно- |
текучести |
прочности |
|
не более |
|
ны НВ |
сти |
σт, МПа |
σв, МПа |
35 |
любой |
нормализ. |
163…192 |
163…192 |
270 |
550 |
|
|
|
|
|
|
|
45 |
любой |
нормализ. |
179…207 |
179…207 |
320 |
600 |
|
|
|
|
|
|
|
45 |
80 |
улучшен. |
269…302 |
269…302 |
650 |
890 |
|
|
|
|
|
|
|
40Х |
200 |
улучшен. |
235…262 |
235…262 |
640 |
790 |
|
|
|
|
|
|
|
40Х |
125 |
улучшен.+ |
269…302 |
45…50 |
750 |
900 |
|
|
зак. ТВЧ |
|
HRC |
|
|
35ХМ |
315 |
улучшен. |
235…262 |
235…262 |
670 |
800 |
|
|
|
|
|
|
|
35ХМ |
200 |
улучшен.+ |
269…302 |
48…53 |
790 |
920 |
|
|
зак. ТВЧ |
|
HRC |
|
|
40ХН |
315 |
улучшен. |
235…262 |
235…262 |
630 |
800 |
|
|
|
|
|
|
|
40ХН |
200 |
улучшен.+ |
269…302 |
48…53 |
750 |
920 |
|
|
зак. ТВЧ |
|
HRC |
|
|
|
|
|
|
|
|
|
18ХГТ |
200 |
улучшен.+ |
300…400 |
56…63 |
800 |
1000 |
|
|
цементац.+ |
|
HRC |
|
|
|
|
закалка |
|
|
|
|
18ХН3 |
200 |
улучшен.+ |
300…400 |
56…63 |
800 |
1000 |
А |
|
цементац.+ |
|
HRC |
|
|
|
закалка |
|
|
|
|
|
|
|
|
|
|
|
|
25ХГМ |
200 |
улучшен.+ |
300…400 |
56…63 |
800 |
1000 |
|
|
цементац.+ |
|
HRC |
|
|
|
|
закалка |
|
|
|
|
Материалы I и III групп прирабатывающиеся: колёса из материалов этих групп в начальный период работы зацепления прирабатываются друг к другу за счет местного износа, в результате снижается концентрация нагрузки на зубьях вблизи торцов. Кроме того, после начала усталостного выкрашивания края обра-
зовавшихся лунок будут обминаться и выкрашивание не будет распространяться
на большую площадь.
«Калёные» стали II группы не прирабатываются. Начавшееся усталостное выкрашивание быстро распространяется на значительную поверхность зуба вследствие хрупкого обламывания краев лунок, однако этот процесс начнется значительно позже, чем для колёс из «сырых» сталей. Для уменьшения концен-
трации нагрузки необходимо проектировать колеса небольшой ширины (с мини-
мальным коэффициентом ширины венца а).
Расчёт зубчатых передач ведут по двум критериям: контактной прочно-
сти и изгибной прочности. Расчёт по контактным напряжениям предотвращает усталостное выкрашивание в закрытых передачах и заедание в открытых переда-
чах. Расчёт на изгиб предотвращает излом зубьев.
Допускаемые напряжения определяют по общепринятому принципу — пре-
дельное напряжение делят на коэффициент запаса: |
|
lim0 / S . |
(22) |
Контактные предельные напряжения (индекс Н) и изгибные (индекс F) так
же, как и коэффициенты SН и SF , определяют по работе [11], которая является ос-
новным учебным пособием по курсовому проектированию. Изгибная прочность
зубьев шестерни и колеса различны и характеризуются рабочими изгибными напряжениями F1 и F 2 , сравниваемыми с допускаемыми изгибными напряже-
ниями и F 2 . Следует обратить внимание на то, что в табл. 4.6 [11] пределы
выносливости по изгибу зубьев приведены при работе одной стороны зуба (нере-
версивная нагрузка). При реверсивной работе обеими сторонами зубьев допуска-
емые изгибные напряжения умножают на 0,8. Расчётное допускаемое контактное напряжение определяют:
1)для прямозубых колёс — как меньшее из двух значений Н 1 и Н 2 ;
2)для прирабатывающихся косозубых колёс — как меньшее из двух значе-
ний:
|
Н |
0,45 Н 1 |
Н |
2 |
, |
(23) |
|||
|
|
1,25 |
|
|
|
|
|
|
|
|
Н |
Н |
; |
|
|
|
|
||
|
|
2 |
|
|
|
|
|
3) для конических колёс с круговыми зубьями — как меньшее из значений:
|
Н |
0,5 Н |
1 |
Н |
2 |
, |
(24) |
|
|
|
1,15 |
|
|
|
|
|
|
|
Н |
Н |
; |
|
|
|
||
|
|
2 |
|
|
|
|
4) для неприрабатывающихся колёс — по Н , общему для обоих колёс.
В тихоходных открытых передачах рекомендуют применять для шестерни
сталь обыкновенного качества (Ст5, Ст6), а для колеса больших размеров (da2 >
500 мм) — литьё стальное (40Л, 45Л и др.) или чугунное (СЧ15, ВЧ35 и др.).
Пример 3. Выбрать материалы косозубых цилиндрических колёс и рас-
считать допускаемые контактные и изгибные напряжения.
Решение.
Принимаем для косозубых колёс стали III группы – «высокий перепад твёр-
достей». Принимаем для шестерни сталь 40Х, термообработка улучшение с по-
следующей закалкой токами высокой частоты, для колеса – сталь 40Х улучшен-
ную. Механические характеристики выбранных сталей приведены в табл. 7.
|
|
|
|
|
|
|
|
|
|
|
|
Таблица 7 |
|
|
|
Механические характеристики сталей |
|
||||||||
|
Марка |
Диаметр |
Термо- |
Твёрдость |
|
Твёрдость |
Предел |
Предел |
||||
|
стали |
заготовки, |
обработка |
сердцеви- |
поверх-ности |
текучести |
прочности |
|||||
|
|
не более |
|
ны НВ |
|
|
|
|
σт, МПа |
σв, МПа |
||
|
40Х |
200 |
улучшен. |
235…262 |
|
235…262 |
640 |
790 |
||||
|
|
|
|
|
|
|
|
|||||
|
40Х |
125 |
улучшен.+ |
269…302 |
45…50HRC |
750 |
900 |
|||||
|
|
|
зак. ТВЧ |
|
|
|
|
|
|
|
|
|
|
Допускаемые контактные напряжения: |
|
|
|
|
|
||||||
|
|
|
|
|
Н |
|
0 |
/ S |
Н |
. |
|
|
|
|
|
|
|
|
Н lim |
|
|
|
|
||
|
|
|
|
|
|
|
|
|
|
|
|
|
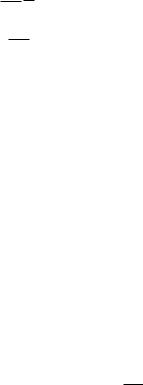
Пределы контактной выносливости [11]:
Н 0lim1 17HRC 200 17 0,5 (45 50) 200 1008 МПа;
Н 0lim 2 2HB 700 2 0,5 (235 262) 70 567 МПа.
Коэффициенты безопасности [11]: SН1 1,2; SН 2 1,1.
Допускаемые контактные напряжения [11]:
Н 1 1008 /1,2 840 МПа; Н 2 567 /1,1 515 МПа.
Расчётные допускаемые контактные напряжения – формула (20):
Н = 0,45·(840+515) = 610 МПа; Н = 1,25·515 = 644 МПа.
Принято расчётное допускаемое контактное напряжение Н = 610 МПа.
Допускаемые изгибные напряжения:
F F 0lim / SF .
Пределы изгибной выносливости [11]:
|
0 |
700 МПа; |
|
0 |
|
F lim1 |
|
|
Н lim 2 |
1,8 HB 1,8 0,5 (235 262) 447 МПа.
Коэффициенты безопасности [11]: |
SF1 1,75; SF 2 1,75. |
Допускаемые изгибные напряжения [11]: |
|
F 1 700 /1,75 400 МПа; |
F 2 447 /1,75 255 МПа. |
Пример 4. Рассчитать коэффициенты долговечности тихоходной ступени |
|
редуктора (рис. 3) по исходным данным и решению примера 1: срок службы L = 6 |
лет; частоты вращения n1 nII 815,5об / мин; n2 nIII 291,2об / мин; твёрдость поверхностей: Н1 = 45…50 HRC, H2 = 235…262 HB. Недостающими данными за-
даться.
Решение.
Принята двухсменная работа, класс нагрузки зубчатых передач Н 0,8; про-
должительность включения ПВ = 0,25. Ресурс привода – формула (211): t L S 2008ПВ = 6·2·2008·0,25 = 6024 ч.
Принят стандартный ресурс t = 16000 ч. (табл. 5). Число циклов нагруже-
ния – формула (20):
N1 60cn1t = 60·1·815,5·16000 = 782,9·106:
N2 60cn2t = 60·1·291,2·16000 = 279,6·106.
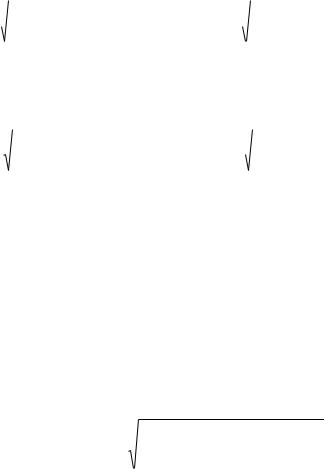
Базы контактных напряжений NHG1 = 68·106 , NHG2 = 17 ·106 (табл. 4). Коэф-
фициенты долговечности по контактным напряжениям – формула (18):
K HД1 |
0,8 6 |
|
782,9 10 |
6 |
|
1,2; |
K HД 2 0,8 6 |
|
279,6 10 |
6 |
|
1,3. |
|
|
|
|
|
|
|||||||
68 106 |
|
|
17 106 |
|
||||||||
|
|
|
|
|
|
|
|
|
|
|
На обоих валах цилиндрической передачи КД > 1. Принято K HД1 = K HД 2 =1.
Коэффициенты долговечности по изгибным напряжениям – формула (19):
K FД1 |
0,84 9 |
|
782,9 |
10 |
6 |
|
1; |
K FД 2 0,81 6 |
|
279,6 10 |
6 |
|
1,4. |
150 |
106 |
|
|
10 106 |
|
|
|||||||
|
|
|
|
|
|
|
|
|
|
|
Принято K FД1 = K FД 2 =1.
11.3. Проектные и проверочные расчёты
Расчёты на прочность цилиндрических зубчатых передач стандартизирова-
ны ГОСТ 21354. Межосевое расстояние цилиндрической передачи aw (мм) опре-
деляют из расчёта на контактную выносливость:
|
|
K |
2 |
T K |
H |
K |
H |
K |
H |
K |
HД |
|
|
a |
u 1 3 |
|
|
2 |
|
|
|
, |
(25) |
||||
|
|
|
|
|
|
|
|
|
|||||
w |
|
Н |
|
|
|
а |
|
|
|
|
|
||
|
|
u |
|
|
|
|
|
|
|
где и — передаточное число цилиндрической ступени, знак «минус» ставят для внутреннего зацепления; К —коэффициент межосевого расстояния, для прямозубых передач К = 315 МПа1/2, для косозубых и шевронных К = 270 МПа1/2, все ре-
дукторные и открытые быстроходные зубчатые передачи рекомендуется принимать косозубыми, шевронные передачи рассчитывают аналогично косозу-
бым, раздвоенная ступень аналогична шевронной; а – коэффициент ширины;
выбирают из единого ряда по ГОСТ 2185:
коробка передач |
а = 0,1; 0,125; 0,16; |
|
|
||||
раздвоенная ступень |
а = |
2(0,2; |
0,25; |
0,315); |
|
||
прямозубые колёса |
|
а = |
0,2; |
0,25; |
0,315; |
0,4; |
|
косозубые колёса |
|
а = |
0,2; |
0,25; |
0,315; |
0,4; |
0,5; |
шевронные колёса |
|
а = |
2·(0,2; |
0,25; |
0,315; |
0,4; |
0,5). |
Рекомендации к назначениюа :
1) при малых нагрузках, а также при консольном расположении одного из колёс

принимают а из начала каждого ряда;
2)для неприрабатывающихся колёс не рекомендуются большие а;
3)в многоступенчатых зубчатых передачах для последующей ступени следует назначать а выше предыдущей.
Т2 — вращающий момент на валу колеса; ставить в формулу (25) в Н мм;
коэффициенты:
КН — неравномерности распределения нагрузки между контактными ли-
ниями (принимать из табл. 8).
|
|
|
Таблица 8 |
|
Коэффициенты неравномерности |
|
|
|
|
|
|
Окружная ско- |
Степень точности |
Коэффициент КН |
Коэффициент КF |
рость v, м/с |
|
|
|
|
7 |
1,03 |
1,07 |
5 |
8 |
1,07 |
1,22 |
|
9 |
1,13 |
1,35 |
5…10 |
7 |
1,05 |
1,2 |
|
8 |
1,1 |
1,3 |
10…15 |
7 |
1,08 |
1,25 |
|
8 |
1,15 |
1,4 |
КН — концентрации нагрузки [11];
KН — динамической нагрузки [11];
КНД —долговечности (см. п. 10.1).
Коэффициенты КН и KН определяют в зависимости от окружной скорости колёс и степени точности. Ориентировочное значение окружной скорости ' в м/c
рекомендуется определять для колёс из материалов I и III групп по формуле:
|
|
n1 |
3 |
T2 |
, |
(26) |
1600 |
u 2 a |
где T2 — вращающий момент на тихоходном валу, Н·м.
Степень точности назначают по работе [11], при этом для редукторных передач степень точности рекомендуется принимать не ниже 8-й. Для прямозу-
бых передач коэффициенты КН = КF = 1. Величины KН зависят не только от окружной скорости, но и от твёрдости колёс: KН несколько меньше при более