
Metodichka_k_laboratornym_po_materialovedeniyu
.pdfдетали. Свойства цементованной детали окончательно формирует последующая закалка и низкий отпуск при 150…200 0С. В результате такой термической об-
работки поверхность детали должна иметь твердость 58,0…62,0 HRC, а сердце-
вина – значительно меньшую, порядка 25,0…35,0 HRC для легированных це-
ментуемых сталей и еще – для углеродистых цементуемых сталей.
4 ЦЕМЕНТАЦИЯ ТВЕРДЫМ КАРБЮРИЗАТОРОМ Этот вид цементации деталей машин широко применяется при единичном
и мелкосерийном производстве. Карбюризатором является древесный уголь
(дубовый или березовый) в зернах с поперечником от 3,5 до 10 мм или камен-
ноугольный полукокс и торфяной полукокс, к которым добавляют активизато-
ры: углекислый барий (BaCO3) и кальцинированную соду (Na2CO3) в количест-
ве от 10 до 40 % от массы угля.
На машиностроительных предприятиях широко применяют карбюриза-
тор, состоящий из древесного угля, 20…35 % BaCO3 и около 3,5 % CaCO3, ко-
торый добавляют для предотвращения спекания частиц карбюризатора. Для цементации составляют рабочую смесь из 25…35 % свежего карбюризатора и
65…75 % отработанного. Содержание BaCO3 в такой смеси 5…7 %, что обес-
печивает требуемую толщину цементованного слоя и исключает образование грубой цементитной сетки на поверхности деталей.
Для твердой цементации применяют стальные сварные или чугунные ли-
тые ящики (контейнеры) прямоугольной или цилиндрической формы. На дно ящика насыпают слой рабочей смеси карбюризатора толщиной 20…30 мм, ко-
торый следует утрамбовать, не допуская дробления зерен древесного угля. За-
тем укладывают первый ряд деталей, выдерживая расстояние между ними и до боковых стенок ящика 10…15 мм. Засыпают следующую порцию рабочей сме-
си карбюризатора и утрамбовывают ее. Карбюризатор должен отделять первый ряд деталей от второго (и т.д.) на 10…15 мм. Последний (верхний) ряд деталей засыпают слоем рабочей смеси толщиной 35…40 мм с тем, чтобы компенсиро-
вать возможную усадку карбюризатора.
80
После упаковки ящика (контейнера) его накрывают крышкой, кромки ко-
торой обмазывают огнеупорной глиной или смесью глины и речного песка,
чтобы не было доступа воздуха в ящик. Затем ящик помещают в печь и при температуре 910…930 0С проводят цементацию деталей.
Для цементации применяют печи периодического действия с горизон-
тальным неподвижным подом и с выдвижным подом, а также шахтные печи. В
одну печь может быть загружено одновременно несколько упакованных ящи-
ков.
Для контроля процесса цементации применяют контрольные образцы – свидетели цементации, которые устанавливают в один из ящиков через отвер-
стия в боковой стенке или в крышке. Рекомендуется устанавливать два-три свидетеля цементации в ящик, который является ближним к двери в подовых печах или верхним – в шахтных печах. Вокруг свидетелей отверстия следует обмазать огнеупорной глиной.
Свидетели цементации должны иметь цилиндрическую форму
8…10 мм из той же марки стали, что и цементуемые детали. При упаковке ящика, в котором будут установлены свидетели цементации, следует тщательно проконтролировать их расположение внутри карбюризатора, чтобы обеспечить их науглероживание на ту же глубину, что и детали.
По истечении расчетного времени цементации вынимают из ящика пер-
вый образец – свидетель цементации и закаливают его в воде, после чего под-
вергают поперечному излому на гидравлическом или винтовом прессе. Зака-
ленный цементованный слой свидетеля цементации имеет серебристый цвет излома, который можно измерить и сравнить с заданной глубиной цементации деталей. Если глубина цементованного слоя свидетеля соответствует заданной глубине цементации деталей, то процесс прекращают. Если требуется увели-
чить глубину слоя до заданного значения, то назначают дополнительное время цементации. Затем повторяют контроль заданной глубины цементованного слоя.
81
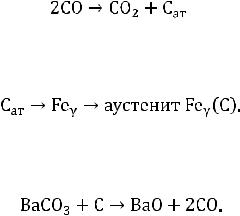
Нагрев до температуры 910…930 0С имеет продолжительность, которую можно определить из расчета 7…9 минут на 10 мм размера ящика. Продолжи-
тельность выдержки при температуре цементации составляет от 5,5 до 6,5 ч для цементованного слоя глубиной 0,6…0,9 мм(см. табл. 6.1).
Таблица 6.1 – Продолжительность процесса цементации твердым карбюризатором в зависимости от требуемой глубины цементованного слоя
Глубина слоя, мм |
Общая продолжительность процесса, ч |
0,4…0,7 |
4,5…5,5 |
0,6…0,9 |
5,5…6,5 |
0,8…1,2 |
6,2…10,0 |
1,0…1,4 |
8,0…11,5 |
1,2…1,8 |
10,0…14,0 |
1,4…1,8 |
11,5…16,0 |
После цементации ящики охлаждают на воздухе до 400…500 0С, а затем раскрывают.
Цементация стали осуществляется атомарным углеродом. При твердой цементации атомарный углерод образуется следующим образом. В цементаци-
онном ящике имеется воздух, кислород которого при высокой температуре взаимодействует с углеродом карбюризатора, образуя окись углерода. Окись углерода в присутствии раскаленной стали диссоциирует по уравнению:
.
Углерод, выделяющийся в результате этой реакции, является атомарным и диффундирует в аустенит:
Добавление углекислых солей активизирует карбюризатор, обогащая ат-
мосферу в цементационном ящике окисью углерода:
И далее процесс продолжается без дополнительного доступа в ящик воз-
духа до завершения цементации деталей на заданную глубину.
82
5 ГАЗОВАЯ ЦЕМЕНТАЦИЯ Этот вид цементации деталей машин применяется при крупносерийном и
массовом производстве (автомобильные заводы, тракторные заводы, заводы сельскохозяйственного машиностроения и др.). Процесс осуществляют нагре-
вом деталей в среде газов, содержащих углерод. Газовая цементация является прогрессивным высокопроизводительным технологическим процессом, так как сокращается трудоемкость и продолжительность цементации до получения за-
данной глубины цементованного слоя деталей, обеспечивается возможность полной механизации и автоматизации производства.
В качестве карбюризаторов используют природный газ, состоящий почти полностью из метана (CH4), а также жидкие среды (керосин, синтин, спирты и т.д.) богатые углеводородом, которые при высокой температуре разлагается с образованием цементующего газа.
Газовую цементацию проводят в безмуфельных печах непрерывного дей-
ствия. В этих установках весь цикл химико-термической обработки (цемента-
ция, закалка и низкий отпуск) полностью механизирован и автоматизирован.
Скорость газовой цементации при температуре 930…950 0С составляет
0,12…0,15 мм/ч при глубине слоя до 1,5…1,7 мм.
6 ЭКСПЕРИМЕНТАЛЬНАЯ ЧАСТЬ ЛАБОРАТОРНОЙ РАБОТЫ Данная лабораторная работа проводится в лаборатории термической об-
работки металлов в течение двух лабораторных занятий (4 академических часа).
Кроме изучения теоретических положений цементации деталей машин и обо-
рудования, лабораторная работа содержит экспериментальную часть, выполне-
ние которой требует применения действующего оборудования, материалов и инструмента.
Лабораторная работа проводится по принципу деловой игры, поэтому у ее выполнению привлекается вся подгруппа студентов. Каждый студент, участ-
вуя в выполнении экспериментальной части работы, имеет свои должностные обязанности:
83
1 Мастер участка цементации деталей твердым карбюризатором (руково-
дство бригадой при выполнении заданного объема работ, обеспечение испол-
нительской дисциплины и качества результатов цементации стали).
2 Помощник мастера участка (ответственное лицо за технику безопасно-
сти, пожарную безопасность и санитарное состояние участка).
3 Старший термист участка (исполнитель работ: по загрузке упакованно-
го тигля в лабораторную электрическую печь; по контролю за ходом процесса цементации стали; по выгрузке тигля после цементации и проведению термиче-
ской обработки контрольных образцов–свидетелей цементации и цементован-
ных образцов, загруженных в тигель).
4 Термист участка (участвует в выполнении всех работ под руководством старшего термиста).
5 Помощник термиста (открывает и закрывает дверцу печи по команде старшего термиста, подает старшему термисту необходимый инструмент, вы-
тирает губки клещей после закалки образцов в воде и масле).
6 Квалифицированный рабочий (упаковка цементационного тигля, уста-
новка образцов–свидетелей цементации для контроля глубины цементованного слоя, обмазка огнеупорной глиной кромок крышки тигля и отверстий вокруг образцов–свидетелей, поперечный излом образцов–свидетелей после их цемен-
тации и закалки).
7 Помощник квалифицированного рабочего (выполняет работы под руко-
водством квалифицированного рабочего).
8 Контролер службы технического контроля (подготовка приборов Рок-
велла к испытанию образцов после цементации и термической обработки; про-
верка качества цементации и термической обработки опытных образцов путем испытания на твердость; стандартное обозначение твердости образцов по Рок-
веллу; сравнение чисел твердости по Роквеллу и по Бринеллю; стандартное обозначение твердости образцов по Бринеллю; предоставление полученных ре-
зультатов для письменных отчетов студентов подгруппы).
84
9 Помощник контролера службы технического контроля (участвует в вы-
полнении всех работ по руководством контролера).
10 Разнорабочие участка – 3 человека (подготовка материалов, инстру-
мента, спецодежды, защитных очков; перемещение и установка тележки с зака-
лочными ваннами; установка поддона сварной конструкции из листовой стали для выгрузки цементационного тигля; зачистка опытных образцов после це-
ментации и термической обработки и представление их контролеру службы технического контроля; уборка рабочих мест в лаборатории).
Методика выполнения экспериментальной части работы:
1 На первом занятии после рассмотрения теоретических положений це-
ментации стали твердым карбюризатором преподаватель рассказывает студен-
там содержание экспериментальной части лабораторной работы, которая про-
водится с применением действующего оборудования, необходимых материалов и инструмента.
2 Учебный мастер излагает последовательность выполнения работ по упаковке двух цементационных тиглей, демонстрирует применяемое оборудо-
вание, материалы и инструмент, а также показывает безопасные приемы вы-
полнения загрузки тигля в печь для проведения цементации опытных образцов и образцов–свидетелей для контроля глубины цементованного слоя.
3 Преподаватель распределяет должностные обязанности студентов под-
группы, акцентируя внимание на вопросах техники безопасности при выполне-
нии лабораторной работы. Преподаватель ориентирует студентов на последова-
тельное самостоятельное выполнение экспериментальной части работы, опира-
ясь на необходимые консультации преподавателя и учебного мастера.
Последовательность выполнения работ:
3.1Упаковка одного цементационного тигля – 1-е занятие.
3.2Загрузка упакованного тигля в печь – 1-е занятия.
Остальные виды работ выполняются на 2-м занятии:
3.3Выгрузка из печи цементационного тигля.
3.4Закалка двух образцов–свидетелей цементации в воде.
85
3.5 Термическая обработка цементованных образцов:
– 1-й образец – закалка в воде с подстуживанием в область Ar3–Ar1 для за-
эвтектоидной зоны цементованного слоя;
–2-й образец – закалка в масле с подстуживанием в область Ar3–Ar1 для заэвтектоидной зоны цементованного слоя;
–3-й образец – нормализация.
3.6 Поперечный излом образцов–свидетелей цементации и их предъявле-
ние контролеру службы технического контроля для определения глубины це-
ментованного слоя.
3.7 Зачистка трех цементованных образцов после их термической обра-
ботки и предъявление контролеру службы технического контроля для испыта-
ния на твердость.
3.8 Испытание 4-х образцов на твердость по методу Роквелла, сравнением числе твердости по Роквеллу и Бринеллю и предоставление результатов экспе-
риментальной части для отчетов студентов подгруппы:
1-й образец – сталь 20 после цементации и закалки в воде;
2-й образец – сталь 20 после цементации и закалки в масле;
3-й образец – сталь 20 после цементации и нормализации;
4-й образец – сталь 20 (исходное состояние нормализованного проката).
7 СОДЕРЖАНИЕ ОТЧЕТА
1 Назначение и область применения цементации стали в машиностроении.
2Технология твердой цементации стали.
3Микроструктура цементованного слоя деталей до и после термической обработки (показать схемы микроструктур и дать пояснения к ним).
4Экспериментальная часть работы.
86
РЕКОМЕНДУЕМАЯ ЛИТЕРАТУРА
1 Материаловедение и технология металлов [Текс]: учеб. для студен-
тов машиностроит. спец. вузов / Г.П. Фетисов, М.Г. Карпман, В.М. Матюнин и др.; Под ред. Г.П. Фетисова. – М.: Высшая школа, 2000. – 638 с.
2 Кроха, В.А. Материаловедение [Текст]: учеб. пособие / В.А. Кроха. –
Воронеж: Воронеж. гос. лесотехн. акад., 2004. – 190 с.
3 Гуляев, А.П. Металловедение [Текст]: учеб. для вузов; 6-е изд., пере-
раб. и доп. / А.П. Гуляев. – М.: Металлургия, 1986. – 544 с.
4 Материаловедение. Методы анализа, лабораторные работы и задачи
[Текст]: учеб. пособие для вузов; 6-е изд., перераб. и доп. / Ю.А. Геллер,
А.Г. Рахштадт. – М.: Металлургия, 1989. – 456 с.
87

ПРИЛОЖЕНИЕ 1
Значения коэффициента подобия K для разных металлов
|
Металл |
|
Величина твердости |
Коэффициент |
|
|
по Бринеллю |
К |
|
|
|
|
||
Сталь, чугун, высокопрочные сплавы на |
До 140 |
10 |
||
основе Ni, Co и др. |
|
140 и более |
30 |
|
Титан и сплавы на его основе |
|
От 50 |
15 |
|
Медь и сплавы на ее основе, легкие ме- |
Менее 35 |
5 |
||
таллы и сплавы |
|
От 35 |
10 |
|
Подшипниковые сплавы |
|
От 8 до 50 |
2,5 |
|
Свинец, олово и другие мягкие металлы |
До 20 |
1 |
||
|
ПРИЛОЖЕНИЕ 2 |
|
||
Продолжительность выдержки |
индентора под действием заданного |
|||
усилия |
при измерении твердости металлов по методу Бринелля |
|||
Твердость по Бринеллю |
|
Продолжительность выдержки , с |
||
|
НВ или HBW |
|
|
|
|
До 10 |
|
180 |
|
|
Свыше 10 до 35 |
|
120 |
|
|
Свыше 35 до 100 |
|
30 |
|
|
Свыше 100 |
|
10…15 |
|
ПРИЛОЖЕНИЕ 3
Эмпирические зависимости между величинами твердости металлов по Бринеллю НВ и пределами прочности при растяжении В , кгс/мм2
Твердость по Бринеллю или состояние |
|
Зависимость между НВ и В |
||||
Сталь |
|
|
|
|
|
|
120…170 НВ |
|
В |
0,34 НВ |
|||
175…450 НВ |
|
В |
0,35 НВ |
|||
Серый чугун |
|
|
|
|
||
100…350 НВ |
|
|
|
|
НВ 40 |
|
В |
|
|||||
|
|
|
6 |
|
||
|
|
|
|
|
||
Медь, латунь, бронза |
|
|
|
|
||
Отожженная |
|
В |
0,55 НВ |
|||
Наклепанная |
|
В |
0,40 НВ |
|||
Дюралюминий |
|
|
|
|
||
Отожженный |
|
В |
0,36 НВ |
|||
После закалки и старения |
|
В |
0,35 НВ |
88

ПРИЛОЖЕНИЕ 4 Минимальная толщина испытуемого образца или изделия
при измерении твердости металлов по методу Бринелля
Диаметр |
Минимальная толщина , мм испытуемого образца или изделия |
|||||
отпечатка |
|
при диаметре шарика |
, мм |
|
||
, мм |
1,0 |
2,0 |
2,5 |
|
5,0 |
10,0 |
0,2 |
0,08 |
|
|
|
|
|
0,3 |
0,18 |
|
|
|
|
|
0,4 |
0,33 |
|
|
|
|
|
0,5 |
0,54 |
0,25 |
|
|
|
|
0,6 |
0,80 |
0,37 |
0,29 |
|
|
|
0,7 |
|
0,51 |
0,40 |
|
|
|
0,8 |
|
0,67 |
0,53 |
|
|
|
0,9 |
|
0,86 |
0,67 |
|
|
|
1,0 |
|
1,07 |
0,83 |
|
|
|
1,1 |
|
1,32 |
1,02 |
|
|
|
1,2 |
|
1,60 |
1,23 |
|
0,58 |
|
1,3 |
|
|
1,46 |
|
0,69 |
|
1,4 |
|
|
1,72 |
|
0,80 |
|
1,5 |
|
|
2,00 |
|
0,92 |
|
1,6 |
|
|
|
|
1,05 |
|
1,7 |
|
|
|
|
1,19 |
|
1,8 |
|
|
|
|
1,34 |
|
1,9 |
|
|
|
|
1,50 |
|
2,0 |
|
|
|
|
1,67 |
|
2,2 |
|
|
|
|
2,04 |
|
2,4 |
|
|
|
|
2,46 |
1,17 |
2,6 |
|
|
|
|
2,92 |
1,38 |
2,8 |
|
|
|
|
3,43 |
1,60 |
3,0 |
|
|
|
|
4,00 |
1,84 |
3,2 |
|
|
|
|
|
2,10 |
3,4 |
|
|
|
|
|
2,38 |
3,6 |
|
|
|
|
|
2,68 |
3,8 |
|
|
|
|
|
3,00 |
4,0 |
|
|
|
|
|
3,34 |
4,2 |
|
|
|
|
|
3,70 |
4,4 |
|
|
|
|
|
4,08 |
4,6 |
|
|
|
|
|
4,48 |
4,8 |
|
|
|
|
|
4,91 |
5,0 |
|
|
|
|
|
5,36 |
5,2 |
|
|
|
|
|
5,83 |
5,4 |
|
|
|
|
|
6,33 |
5,6 |
|
|
|
|
|
6,86 |
5,8 |
|
|
|
|
|
7,42 |
6,0 |
|
|
|
|
|
8,00 |
89