
Metodichka_k_laboratornym_po_materialovedeniyu
.pdf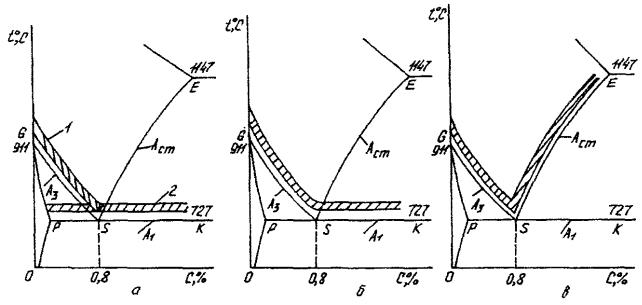
в аустените, для заэвтектоидных сталей Аm – на линии SE и соответствует на-
чалу выпадения или концу растворения цементита в аустените.
Чтобы отличить критическую точку при нагреве от критической точки при охлаждении, рядом с буквой А ставят букву с при нагреве или r при ох-
лаждении. Например, Ar1 – критическая точка превращения аустенита в перлит,
Ac1 – критическая точка превращения перлита в аустенит.
На рис. 5.1 приведены интервалы температур нагрева углеродистых ста-
лей при различных видах термической обработки.
а – отжиг полный (1) и неполный (2); б – закалка; в – нормализация Рисунок 5.1 – Температурные интервалы нагрева углеродистых сталей для различных видов термообработки
Можно записать температуры нагрева для различных видов термообра-
ботки: отжиг полный – нагрев на 30…50 0С выше Аc3 для доэвтектоидных и выше Ac1 для заэвтектоидных сталей; неполный отжиг для доэвтектоидных сталей производится при температуре нагрева на 30…50 0С выше Ac1 ; закалка – нагрев на 30…50 0С выше Аc3 для доэвтектоидных и выше Ac1 для заэвтектоид-
ных сталей; нормализация – нагрев на 30…50 0С выше Аc3 для доэвтектоидных и выше Acm для заэвтектоидных сталей. Отпуск производится с нагревом сталей ниже Ac1 .
70
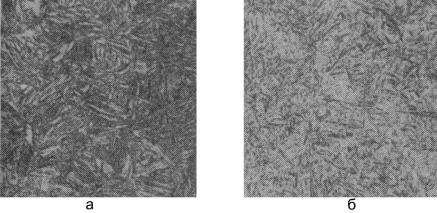
3 СТРОЕНИЕ И СВОЙСТВА МАРТЕНСИТА, ПЛАСТИНЧАТЫХ И ЗЕРНИСТЫХ СТРУКТУР ПЕРЛИТА, СОРБИТА И ТРООСТИТА
Мартенсит – пересыщенный твердый раствор внедрения углерода в Feα.
Мартенсит образуется без диффузионных процессов путем сдвига в кристалли-
ческой решетке, в результате чего углерод не успевает выделиться из Feγ и пол-
ностью остается в Feα. В зависимости от температуры начала охлаждения при закалке (размера зерен аустенита) различают крупноигольчатый (Мкр) и мелко-
игольчатый (Мм) мартенсит (рис. 5.2). Их твердость примерно одинакова, но Мкр имеет высокую хрупкость.
а – крупноигольчатый; б – мелкоигольчатый Рисунок 5.2 – Структура мартенсита
Перлит, сорбит и троостит являются продуктами распада аустенита,
протекающего с диффузионными процессами. Их различие обусловлено темпе-
ратурой, при которой аустенит распадается, т.е. степень переохлаждения аусте-
нита до начала его распада.
При малых степенях переохлаждения (распад аустенита при 700 0С) по-
лучается достаточно грубая смесь феррита и цементита, называемая перлитом
(рис. 5.3а). Перлит является самым мягким, имеет наилучшие комплекс свойств для обработки резанием и давлением.
При увеличение степени переохлаждения (распад при 650 0С) дисперс-
ность структур возрастает и твердость продуктов повышается. Такой более тонкого строения перлит получил название сорбита (рис. 5.3б). Сорбит более твердый и прочный, чем перлит, имеет достаточные механические для долго-
временной работы деталей.
71
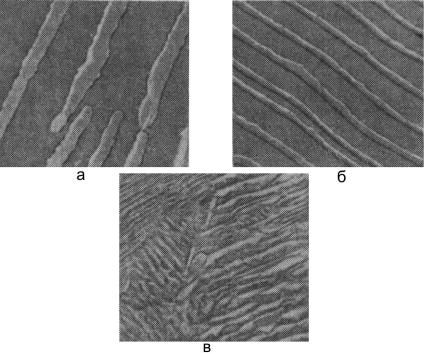
При еще большей степени переохлаждения (распад при 600 0С) дисперс-
ность продуктов еще более возрастает. Такая структура называется трооститом
(рис. 5.3в). Он является самым твердым продуктом распада аустенита.
а – перлит; б – сорбит; в – троостит Рисунок 5.3 – Структура эвтектоидной стали в зависимости
от степени переохлаждения
Перлитные структуры могут быть двух типов: зернистые (цементит в них находится в форме зернышек) или пластичные (в форме пластинок). Однород-
ный аустенит всегда превращается в пластинчатые структуры, а неоднородный дает структуры зернистые. Следует отметить, что зернистые структуры наибо-
лее прочные по сравнению с пластичнатыми.
4 СТРУКТУРНЫЕ ПРЕВРАЩЕНИЯ В СТАЛЯХ 45 И У12 ПРИ ЗАКАЛКЕ И ОТПУСКЕ
При термической обработке сталей наблюдаются четыре основные пре-
вращения: перлита в аустенит; аустенита в перлит; аустенита в мартенсит; мар-
тенсита в перлит (ферритно-цементитную смесь).
При закалке и отпуске стали 45 (учитывая, что начальное состояние стали было равновесным) соответственно будут протекать следующие структурные превращения:
72
1) Ф + П → А0,45 – при нагреве стали 45 до температуры на 30…50 0С вы-
ше Ac 3 , т.е. 800…820 0С;
2)А0,45 → Мм – при закалке на мартенсит, т.е. охлаждение в воде;
3)Мм → Мм отп – при низком отпуске, т.е. при нагреве стали до температуры 200 0С, выдержки в течение 30 минут при этой температуре и охлаждении
на спокойном воздухе;
4)Мм → Трзерн – при среднем отпуске (температура нагрева 400 0С);
5)Мм → Сзерн – при высоком отпуске (температура нагрева 600 0С).
При закалке и отпуске стали У12 будут протекать следующие структур-
ные превращения:
1) П + ЦII → А0,8 + ЦII – при нагреве стали У12 на 30…50 0С выше Ac1 , т.е. 760…780 0С;
2)А0,8 + ЦII → Мм + ЦII – при закалке в воде;
3)Мм + ЦII → Мм отп + ЦII – при низком отпуске;
4)Мм + ЦII → Трзерн + ЦII – при среднем отпуске;
5)Мм + ЦII → Сзерн + ЦII – при высоком отпуске.
5 ИНДИВИДУАЛЬНОЕ ЗАДАНИЕ Каждый студент выполняет индивидуальное задание по указанному пре-
подавателем варианту (табл. 5.1). Согласно варианту известны: наименование изделия (детали или инструмента), марка углеродистой конструкционной или инструментальной стали и ее микроструктура. Необходимо обосновать ответы на следующие вопросы задания:
1 Установить вид (виды) термической обработки, которому подвергалось изделие, с указанием возможного брака термообработки или ее незавершенно-
сти.
2 Обосновать оптимальную технологию термообработки изделия, если исходное состояние стали было нормализованным.
3 Методом условной записи показать структурные превращения в стали при оптимальной технологии термической обработки.
73

4 Установить приближенное значение твердости изделия после опти-
мальной технологии термообработки.
Таблица 5.1 – Варианты индивидуальных заданий к лабораторной работе «Исследование влияния термической обработки на микроструктуру и свойства углеродистых сталей»
Номер |
Наименование изделия |
Марка |
Микроструктура |
|
варианта |
|
материала |
|
|
1 |
Шатун двигателя |
Сталь 40 |
Мкр |
|
2 |
Плашка |
Сталь У10 |
Трпл + ЦII |
|
3 |
Коленчатый вал двигателя |
Сталь 45 |
Трзерн |
|
4 |
Метчик |
Сталь У11 |
Сзерн |
|
5 |
Пружина подвески |
Сталь 65 |
Мм + Ф |
|
6 |
Развертка |
Сталь У12 |
Трзерн + ЦII |
|
7 |
Полуось |
Сталь 35 |
Мм |
|
8 |
Рессорный лист |
Сталь 60 |
Мм + Аост |
|
9 |
Болт шатунный |
Сталь 40 |
Мм + Ф |
|
10 |
Сверло |
Сталь У9 |
Спл + ЦII |
|
11 |
Пружинная шайба |
Сталь 65Г |
Трпл + Ф |
|
12 |
Вал КПП |
Сталь 40 |
Мм отп |
|
13 |
Зубило |
Сталь У8 |
Мкр + Аост |
|
14 |
Распределительный вал |
Сталь 45 |
Трпл |
|
15 |
Кернер |
Сталь У7 |
Сзерн |
|
16 |
Ось ленивца |
Сталь 40 |
Трзерн |
|
17 |
Штамп вытяжной |
Сталь У10 |
Спл + ЦII |
|
18 |
Палец рессоры |
Сталь 45 |
Сзерн |
|
19 |
Калибр |
Сталь У11 |
Мкр + ЦII |
|
20 |
Поршневой палец |
Сталь 45 |
Мм отп |
|
21 |
Долото |
Сталь У7 |
Трпл + Ф |
|
22 |
Диск сцепления ведомый |
Сталь 50 |
Трпл |
|
23 |
Топор |
Сталь У7 |
Мм + Аост |
|
24 |
Вилка карданного вала |
Сталь 35 |
Мм + Ф |
|
25 |
Пила ручная |
Сталь У10А |
Тррл + ЦII |
|
26 |
Ступица ведомых дисков |
Сталь 45 |
Мм |
|
27 |
Молоток |
Сталь У7 |
Мкр + Аост |
|
28 |
Фланец ведущей шестерни |
Сталь 35 |
Сзерн |
|
29 |
Зенкер |
Сталь У12 |
Спл + ЦII |
|
30 |
Вилка переключения передач |
Сталь 20 |
Мкр |
|
Пример выполнения индивидуального задания
Вариант 0.
Деталь: вал.
Марка материала: сталь 40.
74
Микроструктура: Спл + Ф.
1 Судя по данной микроструктуре Спл + Ф деталь была подвергнута нор-
мализации, термообработка завершена.
2 Данная деталь при работе испытывает динамические нагрузки, следова-
тельно материал детали должен обладать повышенной прочностью с достаточ-
ной твердостью. Поэтому оптимальной термической обработкой вала является улучшение, т.е. закалка в воде + высокий отпуск.
3 |
Спл + Ф А0,4 |
Мм Сзерн. |
|
|
820...8400С |
охл. в воде |
отпуск 6000С |
4 |
Приблизительная твердость 33,0 HRC. |
|
6 СОДЕРЖАНИЕ ОТЧЕТА
1 Характеристика основных видов термической обработки стали (отжиг полный и неполный, нормализация, закалка, отпуск).
2 Выбор температур нагрева углеродистых сталей разного состава для ос-
новных видов термической обработки.
3 Строение и свойства мартенсита, пластинчатых и зернистых структур перлита, сорбита и троостита.
4 Структурные превращения в сталях 45 и У12 при закалке и отпуске.
5 Влияние разных видов термической обработки на структуру и свойства углеродистых сталей 45 и У12 (таблица экспериментальной части работы (при-
ложение 11) и анализ полученных результатов). 6 Индивидуальное задание.
75
ЛАБОРАТОРНАЯ РАБОТА №6 ЦЕМЕНТАЦИЯ СТАЛИ
ЦЕЛЬ РАБОТЫ 1 Изучить назначение и область применения цементации стали в машино-
строении.
2 Ознакомиться с технологией твердой цементации стали и термической обработкой деталей после цементации.
3 Изучить микроструктуру и свойства цементированного слоя деталей до
ипосле термической обработки.
1ОБОРУДОВАНИЕ, МАТЕРИАЛЫ, ИНСТРУМЕНТ, ИНФОРМАЦИОННЫЕ СТЕНДЫ
1.1 Лабораторная электрическая муфельная печь.
1.2 Приборы Роквелла – 2 прибора.
1.3 Цементационный тигель с крышкой – 1 комплект для одной подгруппы студентов.
1.4 Тележка с двумя закалочными ваннами: с водопроводной водой и с минеральным маслом.
1.5 Цилиндрические образцы для цементации из углеродистой стали 20
12…16 мм – 4 образца для одной подгруппы студентов.
1.6 Стандартный карбюризатор для твердой цементации.
1.7 Раствор огнеупорной глины в воде.
1.8 Образцы-свидетели цементации из стали 20 – 2 образца для одной подгруппы студентов.
1.9 Шлифовальная шкурка средней зернистости для зачистки цементованных образцов (формат листов 200100 мм) – 2 листа для одной продгруппы студентов.
1.10 Ветошь белая из хлопчатобумажной ткани для подготовки прибора Роквелла и опытных образцов к испытаниям на твердость.
76
1.11 Совок для загрузки карбюризатора в тигель.
1.12 Захват для цементационного тигля.
1.13 Поддон из листовой стали для распаковки цементационного тигля.
1.14 Клещи плоские с круглыми губками.
1.15 Слесарный молоток.
1.16 Пассатижи.
1.17 Стенд «Диаграмма железо-углерод».
1.18 Стенд с цементованными деталями автомобилей и тракторов.
1.19 Стенд «Индикатор прибора Роквелла».
1.20 Стенд «Сравнение чисел твердости по Роквеллу и Бринеллю».
2 НАЗНАЧЕНИЕ И ОБЛАСТЬ ПРИМЕНЕНИЯ ЦЕМЕНТАЦИИ СТАЛИ В МАШИНОСТРОЕНИИ
Цементацией называется один из видов химико-термической обра-
ботки стальных деталей машин и оборудования, состоящий в насыщении поверхностного слоя углеродом путем его диффузии в атомарном состоя-
нии из внешней среды при высокой температуре.
Процесс цементации известен людям с давних пор. До середины XIX века сталь умели получать только методом сквозной цементации железа.
В машиностроении применяют два основных вида цементации: твердую и газовую. Целью цементации является получение твердой и износостойкой
поверхности, что достигается обогащением поверхностного слоя детали угле-
родом и последующей закалкой с низким отпуском. Так как для цементуемых деталей применяют низкоуглеродистые конструкционные стали
(0,12…0,23 % С), то сердцевина остается мягкой и вязкой после закалки науг-
лероженного слоя. Это обеспечивает сопротивление деталей ударным нагруз-
кам. Цементация и последующая термическая обработка одновременно повы-
шают и предел выносливости.
Цементацируют многочисленные детали машин и оборудования: зубча-
тые колеса коробок переменных передач, раздаточных коробок, главных пере-
77
дач ведущих мостов автомобилей, тракторов и других транспортных и техноло-
гических машин, коробок скоростей металлорежущих, деревообрабатывающих и других станков, поршневые пальцы двигателей внутреннего сгорания, кре-
стовины карданных передач, детали рулевого управления автомобильного типа
– червяк рулевого механизма, вал-сектор рулевой сошки, шкворни поворотных цапф, детали крупных подшипников качения и др.
К цементуемым относятся многие марки углеродистых и легированных конструкционных сталей: 10, 15, 20, 25, 15Х, 20Х, 15ХР, 20ХН, 20ХГР, 20ХНР, 18ХГТ, 30ХГТ, 12ХН3А, 12Х2Н4А, 18Х2Н4ВА и др.
Для цементации детали поступают после механической обработки с при-
пуском на шлифование 0,05…0,1 мм или после окончательной обработки (на-
пример, автомобильные шестерни). Во многих случаях цементации подвергает-
ся только часть детали; тогда участки, не подлежащие упрочнению, защищают тонким слоем меди (0,02…0,05 мм), которую наносят электролитическим спо-
собом, или изолируют специальными обмазками, состоящими из смеси огне-
упорной глины, песка и асбеста, или окиси алюминия и талька, замешанных на жидком стекле.
3 МЕХАНИЗМ ОБРАЗОВАНИЯ ЦЕМЕНТОВАННОГО СЛОЯ И ЕГО СТРОЕНИЕ
Диффузия углерода в сталь возможна только в том случае, если углерод находится в атомарном состоянии, а низкоуглеродистая сталь содержит струк-
туру аустенит, способный растворять углерод в большом количестве в соответ-
ствии с линией ES диаграммы железо-углерод (см. рис. 2.2). Атомарный угле-
род образуется при диссоциации газов, содержащих углерод (CO, CH4 и др.).
Атомарный углерод адсорбируется поверхностью раскаленной стали и диф-
фундирует в глубь металла.
Цементацию проводят при температурах выше критических точек АС3
цементуемых углеродистых и легированных сталей (910…950 0С). При таких температурах сталь состоит только из аустенита, имеющего кристаллическую
78
структуру Fe . И в зависимости от температуры нагрева предел насыщения ау-
стенита углеродом (Cmax) изменяется, а также изменяется скорость диффузии углерода.
Цементованный слой имеет переменную концентрацию углерода по глу-
бине, убывающую от поверхности к сердцевине детали. После медленного ох-
лаждения в структуре цементованного слоя можно различить (от поверхности к сердцевине) три зоны: заэвтектоидную (С 0,8 %), состоящую из перлита и вторичного цементита, образующего сетку вокруг зерен перлита; эвтектоид-
ную (С 0,8 %), состоящую из зерен однородного пластинчатого перлита;
доэвтектоидную (С 0,8 %), состоящую из перлита и феррита. Количество феррита в этой зоне непрерывно возрастает по мере приближения к сердцевине.
За эффективную толщину цементованного слоя принимают сумму заэвтектоидной, эвтектоидной и половины переходной (доэвтектоидной)
зон или глубину распространения контрольной твердости свыше опреде-
ленного значения. В качестве контрольной твердости (после термической об-
работки) применяют величину твердости по Роквеллу (шкала С) – 50 единиц
(50,0 HRC), соответствующей половине доэвтектоидной зоны, где содержание углерода составляет до 0,45 %.
Эффективная толщина цементованного слоя для большинства деталей со-
ставляет от 0,5 до 1,8 мм. В отдельных случаях (детали крупных подшипников качения) необходимая толщина цементованного слоя достигает 3…4 мм.
Концентрация углерода в поверхностном слое деталей должна составлять
0,8…1,0 %. Для получения максимального сопротивления контактной устало-
сти количество углерода может быть повышено до 1,1…1,2 % (зубчатые коле-
са). Более высокое содержание углерода ведет к образованию значительного количества вторичного цементита в заэвтектоидной зоне, что вызывает повы-
шенную хрупкость цементованного слоя.
Получение высокой твердости и износостойкости поверхности детали при сохранении мягкой и вязкой сердцевины не решается одной цементацией.
Цементацией достигается лишь выгодное распределение углерода по сечению
79