
Metodichka_k_laboratornym_po_materialovedeniyu
.pdfЗаторцовка производится на абразивных кругах или металлорежущих станках (иногда применяют опиловку напильником) без охлаждения или с ох-
лаждением водой (для закаленных сталей).
Шлифование выполняют с помощью шлифовальной бумаги, которая кладется на толстое стекло. Вначале заторцованную поверхность шлифуют в одном направлении на шлифовальной бумаге с наибольшим размером зерна до тех пор, пока не исчезнут риски, полученные после заторцовки. Затем берут шлифовальную бумагу с абразивом меньшего размера, поворачивают образец на 900 по отношению к рискам, полученных при предыдущем шлифовании, и
шлифуют до полного их удаления. Шлифование проводят на четырех или пяти номерах шлифовальной бумаги, переходя постепенно к бумаге с наименьшим размером абразивных частиц.
После шлифования необходимо произвести промывку водой микрошлифа для удаления абразивных частиц, оставшихся на образце после шлифования, а
затем сушку фильтровальной бумагой во избежание окисления шлифованной поверхности образца и отложения на ней солей.
Полирование микрошлифа выполняют на специальном полировальном станке, на котором установлен вращающийся полировальный круг, обтянутый мягким сукном или фетром. Круг должен быть смазан пастой ГОИ (иногда применяют суспензии окиси алюминия или хрома). К вращающемуся кругу прижимают образец отшлифованной поверхностью и совершают периодиче-
ские вращательные движения (прижимать образец с большой силой не реко-
мендуется во избежание вырывания его из рук). Для железоуглеродистых спла-
вов полирование необходимо проводить в течение 3…5 минут. За это время бу-
дут выведены риски, полученные при шлифовании, а при более длительном по-
лировании будет происходить выкрошивание составляющих структур.
После полирования образец необходимо промыть водой и спиртом для удаления с поверхности шлифа жирных пятен, а затем высушить с помощью фильтровальной бумагой.
60
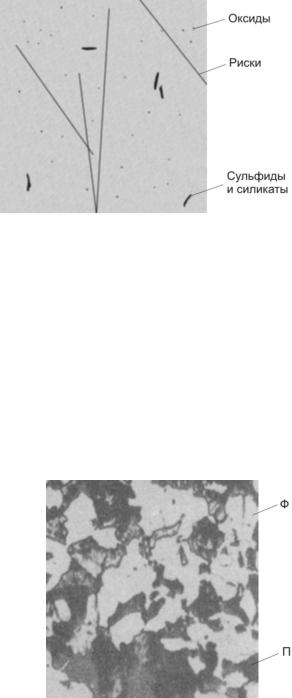
Изучение микроструктуры целесообразно начинать с рассмотрения мик-
рошлифа непосредственно после полирования, промывки и высушивания. Под микроскопом такой шлиф имеет вид светлого круга, на котором можно заме-
тить темные участки (серые или черные), иногда другого цвета, обычно не-
больших размеров. Эти участки являются следами неметаллических включе-
ний, которые в результате полирования частично выкрошиваются (рис. 3.6).
В некоторых сплавах (например, |
|
||
серые чугуны) такие участки могут |
|
||
быть структурными |
составляющими, |
|
|
характерными для данного сплава. |
|
||
Большая |
часть |
неметаллических |
|
включений является оксидами (выгля- |
|
||
дят в виде маленьких точек), сульфи- |
|
||
дами, нитридами и силикатами (вы- |
Рисунок 3.6 – Микроструктура |
||
глядят в виде полосок неправильной |
стали до травления |
||
|
формы), не отделившимися от металла при плавке, разливке и застывании. Сле-
довательно по количеству размерам и форме неметаллических включений мож-
но определить степень загрязненности ими сплава.
Травление производится методом избирательного растворения фаз. Дан-
ный метод основан на различии физико-механических свойств отдельных фаз и пограничных участков зерен. В результате различной интенсивности растворе-
ния создается микрорельеф поверхности |
|
шлифа. Если освещать протравленный шлиф |
|
падающим светом, то из-за присутствия ко- |
|
сых лучей от рассеивания света образуются |
|
теневые картины (рис. 3.7). |
|
Для травления железоуглеродистых |
|
сплавов применяют 4…5 %-ный раствор |
|
азотной кислоты в этиловом спирте. Трав- |
Рисунок 3.7 – Микроструктура |
ление осуществляется погружением полиро- |
стали после травления |
|
61
ванной поверхности в раствор или нанесением его на поверхность с помощью пипетки. Когда полированная поверхность шлифа станет слегка матовой, трав-
ление считается законченным и шлиф сразу же промывают проточной водой,
затем спиртом и высушивают фильтровальной бумагой.
8 ИНДИВИДУАЛЬНОЕ ЗАДАНИЕ Каждый студент выполняет индивидуальное задание по указанному пре-
подавателем варианту. Известно процентное содержание перлита для доэвтек-
тоидной стали и процентное содержание цементита для заэвтектоидной стали
(табл. 3.1). Рассчитать приблизительное содержание углерода в углеродистых сталях и зарисовать их микроструктуру при комнатной температуре.
Таблица 3.1 – Варианты индивидуальных заданий к лабораторной работе «Макро- и микроанализ металлов и сплавов»
Номер |
Количество |
Количество |
Номер |
Количество |
Количество |
варианта |
перлита, % |
цементита, % |
варианта |
перлита, % |
цементита, % |
1 |
20 |
2,0 |
16 |
15 |
0,5 |
2 |
35 |
3,5 |
17 |
40 |
4,0 |
3 |
60 |
6,0 |
18 |
55 |
5,5 |
4 |
75 |
7,5 |
19 |
80 |
8,0 |
5 |
10 |
10,0 |
20 |
95 |
9,5 |
6 |
25 |
4,0 |
21 |
5 |
2,0 |
7 |
65 |
7,0 |
22 |
30 |
3,5 |
8 |
90 |
8,0 |
23 |
85 |
9,0 |
9 |
40 |
4,5 |
24 |
35 |
5,0 |
10 |
15 |
10,5 |
25 |
20 |
11,0 |
11 |
85 |
9,0 |
26 |
90 |
8,5 |
12 |
70 |
6,5 |
27 |
65 |
7,0 |
13 |
45 |
5,0 |
28 |
50 |
4,5 |
14 |
30 |
2,5 |
29 |
25 |
3,0 |
15 |
5 |
1,0 |
30 |
10 |
1,5 |
Пример выполнения индивидуального задания
Вариант 0.
1 В доэвтектоидной стали согласно варианту содержится 50 % перлита,
следовательно остальные 50 % – феррит. Так как при комнатной температуре в
62
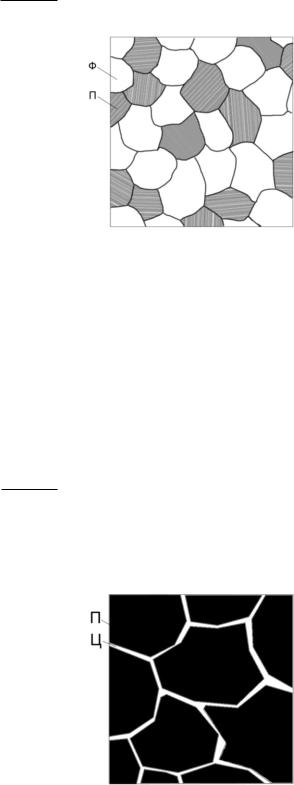
феррите содержится 0,006 % углерода, количеством углерода в феррите пре-
небрегаем. Перлит содержит 0,8 % углерода. 100 % П – 0,8 % С; 50 % П – x % С,
50 0,8
тогда x 0,4 % С – содержится в данной стали.
100
Рисунок 3.8 – Схема микроструктуры стали 40
2 В заэвтектоидной стали согласно варианту содержится 1 % цементита,
тогда остальное 99 % перлита. Цементит содержит 6,67 %, а перлит – 0,8 % уг-
лерода.
100 % П – 0,8 % С; 99 % П – x % С, тогда x |
99 0,8 |
0,792 % С. |
|
100 |
|
||
|
|
|
|
100 % Ц – 6,67 % С; 1 % Ц – y % С, |
|
|
|
1 6,67
тогда y 0,0667 % С.
100
z x y 0,792 0,0667 0,8587 0,9 % С – содержится в данной
стали.
Рисунок 3.9 – Схема микроструктуры стали У9
63
9 СОДЕРЖАНИЕ ОТЧЕТА
1 Назначение и область применения макроанализа металлов.
2 Характеристика искусственных изломов слитков и аварийных изломов деталей машин.
3 Волокнистое строение кованного коленчатого вала.
4 Метод Баумана для определения ликваций серы в сталях.
5 Назначение и область применения микроанализа металлов.
6 Устройство металлографического микроскопа.
7 Технология изготовления микрошлифов.
8 Схемы микроструктур сталей и чугунов в равновесном состоянии до и после травления.
9 Индивидуальное задание.
64
ЛАБОРАТОРНАЯ РАБОТА №4
ИССЛЕДОВАНИЕ МИКРОСТРУКТУР ЖЕЛЕЗОУГЛЕРОДИСТЫХ
СПЛАВОВ В РАВНОВЕСНОМ СОСТОЯНИИ
65
ЛАБОРАТОРНАЯ РАБОТА №5
ИССЛЕДОВАНИЕ ВЛИЯНИЯ ТЕРМИЧЕСКОЙ ОБРАБОТКИ
НА МИКРОСТРУКТУРУ И СВОЙСТВА УГЛЕРОДИСТЫХ СТАЛЕЙ
ЦЕЛЬ РАБОТЫ
1 Изучить основные виды термической обработки сталей и их назначе-
ние.
2 Научиться определять температуру нагрева, время выдержки и охлаж-
дающую среду для основных видов термообработки.
3 Получить практические навыки термообработки сталей.
1 ХАРАКТЕРИСТИКА ОСНОВНЫХ ВИДОВ ТЕРМИЧЕСКОЙ ОБРАБОТКИ СТАЛИ
Процесс термической обработки состоит в том, чтобы нагревом до оп-
ределенной температуры и последующим охлаждением вызвать желаемое из-
менение строения металла. Режим термической обработки характеризуется следующими основными параметрами: температура нагрева – максимальная температура, до которой нагревают сплав при термической обработке; время выдержки сплава при температуре нагрева; скорость охлаждения, которая мо-
жет изменяться в процессе термической обработки.
Изменяя режим (скорость) охлаждения нагретой до аустенитного состоя-
ния стали, можно в широком диапазоне изменять ее строение, следовательно получать различные комплексы механических и других свойств. На этом осно-
ваны наиболее часто применяемые виды термической обработки: отжиг, нор-
мализация и закалка. Важным видом термообработки, выполняемым после за-
калки, является отпуск.
Отжиг – термическая операция, состоящая в нагреве сплава, имеющего неустойчивое состояние в результате предшествовавшей обработки, и приво-
дящая сплав в более устойчивое состояние. Другими словами, отжиг произво-
дится с целью умягчения стали перед механической обработкой или чтобы под-
66
готовить ее структуру к окончательной термообработке, состоящей из закалки и отпуска. Отжигу подвергаются литые заготовки, имеющие неблагоприятную грубозернистую структуру, а также заготовки, прошедшие ковку, штамповку и другие виды обработки давлением. В ряде случаев, когда получающиеся после отжига свойства обеспечивают долголетнюю службу детали, он оказывается окончательным видом термической обработки.
При отжиге сталь нагревается до температуры на 30…50 0С выше линии
GSK (при полном отжиге) или выше линии PSK (при неполном отжиге), вы-
держивается при этой температуре до полного завершения структурно-фазовых превращений и охлаждается с очень малой скоростью (несколько 0С/мин) в ка-
мере печи с отключенными источниками теплоты. Заэвтектоидную сталь нельзя нагревать выше линии SE, так как образующаяся при очень медленном охлаж-
дении вокруг зерен перлита цементитная сетка затрудняет механическую обра-
ботку и охрупчивает сталь.
Нормализация. Отличается от отжига температурой нагрева (на
30…50 0С выше линии GSE) и скоростью охлаждения (несколько десят-
ков 0С/мин) на спокойном воздухе. Эти отличия обусловлены специфическими целями нормализации. Применительно к доэвтектоидным сталям данный вид термообработки за более короткое время и при большей простоте режима ох-
лаждения позволяет получить те же результаты, что и при отжиге, т.е. мелко-
зернистую структуру стали у литых и кованных заготовок, но с повышенными прочностными свойствами из-за более высокой степени переохлаждения аусте-
нита.
Иногда от материала изделия не требуется повышенных прочностных свойств и нормализация заменяет закалку. В основном это применяется для де-
талей из низкоуглеродистых сталей, для которых применение закалки исключа-
ется из-за очень высокой критической скорости закалки.
При нормализации заэвтектоидных сталей цементит вторичный доста-
точно быстро выделяется из аустенита, вследствие чего нежелательная цемен-
67
титная сетка вокруг зерен перлита не образуется. Поэтому одной из целей нор-
мализации является разрушение цементитной сетки.
Закалка – термическая операция, заключающаяся в нагреве сплава с по-
следующим достаточно быстрым охлаждением для получения структурно неус-
тойчивого состояния сплава. После закалки сталь приобретает неравновесную структуру, что прежде всего выражается в повышении твердости. Различают закалку на троостит (Трпл), бейнит (Б) и мартенсит (Мм).
Закалку на мартенсит принято считать истинной закалкой, при которой с последующим отпуском можно получить ценные комплексы свойств. В связи с этим данный вид термообработки получит более широкое применение как предварительная обработка перед отпуском. Режим закалки на мартенсит угле-
родистых сталей включает нагрев до температуры на 30…50 0С выше линии
GSK, выдержку сплава при этой температуре и охлаждение со скоростью ниже критической (несколько сотен 0С/с) в воде.
При увеличении скорости охлаждения уровень термических и фазовых напряжений возрастает и увеличивается вероятность образования трещин в де-
тали или ее коробления. В связи с этим для углеродистых сталей часто приме-
няют закалку в более мягких средах (масло, расплавы минеральных солей). За-
калку в масле (скорость охлаждения составляет несколько десятков 0С/с) назы-
вают закалкой на троостит.
Отпуск – операция нагрева закаленной стали для уменьшения остаточ-
ных напряжений и придания ей комплекса механических и других свойств, не-
обходимых для долголетней эксплуатации изделия. При отпуске закаленной на мартенсит стали происходит распад мартенсита и образование равновесного структурно-фазового состава. Интенсивность и результат этих превращений за-
висят от температуры отпуска.
Низкотемпературный (низкий) отпуск производится при 150…180 0С с низкой интенсивностью диффузионных процессов, поэтому структура закален-
ной стали практически не меняется – уменьшаются остаточные термические напряжения, следовательно снижается хрупкость изделий. Структура, получае-
68
мая в результате низкого отпуска называется мартенситом отпуска Мотп (отпу-
щенным). Данный вид отпуска производится для деталей, при работе которых требуется высокая твердость.
Среднетемпературный (средний) отпуск производится при температурах от 350 до 450 0С с полным распадом мартенсита и образованием нормальных по составу и внутреннему строению феррита и цементита. Однако в связи с недос-
таточной интенсивностью диффузионных процессов размер зерен образующих-
ся фаз оказывается очень малым – данная структура называется трооститом от-
пуска Трзерн (зернистый). Этот вид термообработки обеспечивает благоприят-
ный для пружин, рессор и им подобным изделий комплекс механических свойств.
Высокотемпературный (высокий) отпуск осуществляется при
500…650 0С с образованием более крупных зерен феррита и цементита, чем при среднем отпуске. Получающийся при этом продукт распада мартенсита, назы-
ваемый сорбитом отпуска Сзерн (зернистый), обладает максимальной для стали вязкостью с удовлетворительной прочностью. Такие свойства идеальны для де-
талей машин, подвергающихся динамическим и циклическим нагрузкам, по-
этому термообработку, заключающуюся в закалке с высоким отпуском, назы-
вают улучшением.
2 ВЫБОР ТЕМПЕРАТУР НАГРЕВА УГЛЕРОДИСТЫХ СТАЛЕЙ РАЗНОГО СОСТАВА ДЛЯ ОСНОВНЫХ ВИДОВ ТЕРМИЧЕСКОЙ ОБРАБОТКИ
Для изучения термической обработки стали основой является диаграмма железо-углерод, причем ее целесообразно рассматривать для сплавов с концен-
трацией углерода до 2,14 % и до температуры солидуса.
Критические точки обозначаются буквой А. Нижняя критическая точка соответствует превращению аустенит перлит, т.е. лежит на линии PSK и обо-
значается А1 . Верхняя критическая точка для доэвтектоидных сталей А3 лежит на линии GS и соответствует началу выпадения или концу растворения феррита
69