
ИВАНОВ А.С. гр. 0041 зу
.pdf1
Аннотация
В данном дипломном проекте разработана технологическая подготовка производства изделия «Корпус».
В проекте рассмотрен один из возможных технологических процессов обработки детали типа червяк.
При его разработке были учтены: тип производства, свойства и особенности обрабатываемого материала, точность размеров, чистота поверхности, действующие стандарты и нормативы.
Проект состоит из пояснительной записки, чертежей.
Для выполнения графической части курсового проекта использовалась система T-Flex CAD 11.
В расчетах использована прикладная программа пакета Mathcad Professional.
При оформлении пояснительной записки использовалась программа
Microsoft Word.
Графическая часть проекта содержит: чертеж детали, чертеж заготовки,
чертежи технологических эскизов с анализом точности, чертежи технологических наладок по трем операциям, чертежи трѐх приспособлений,
чертѐж механического участка, чертеж технико-экономических показателей участка.
В данной работе были развиты навыки к самостоятельному решению инженерных задач в области проектирования технологических процессов, в
выборе оборудования и режущего инструмента для получения годной детали механической обработкой.
При оформлении графической части проекта учитывались требования ЕСКД и ЕСТД.
2
1 СОДЕРЖАНИЕ
1СОДЕРЖАНИЕ……………………………………………………………….7
2ВВЕДЕНИЕ……………………………………………………………………9
3ТЕХНИКО-ЭКОНОМИЧЕСКОЕ ОБОСНОВАНИЕ ПРОЕКТА……...…..12
3.1Определение типа производства………………………………………12
3.2Служебное назначение и конструкция детали……………………….16
3.3Отработка конструкции детали на технологичность………………..18
3.4Выбор и технико-экономическое обоснование метода получения исходной заготовки…………………………………………………………….19
4ТЕХНОЛОГИЧЕСКИЙ РАЗДЕЛ……………………………………………22
4.1Разработка маршрута обработки корпуса…………………………….22
4.2Расчет припусков……………………………………………………….25
4.3Расчет режимов резания……………………………………………….34
4.4Расчет технологической нормы времени……………………………..48
5КОНСТРУКТОРСКИЙ РАЗДЕЛ……………………………………………53
5.1Конструирование станочных приспособлений…………………...…53
6РАЗРАБОТКА ПЛАНИРОВКИ УЧАСТКА………………………………..65
6.1Введение………………………………………………………….……..65
6.2Определение годовой трудоемкости обработки……………….…….66
6.3Определение количества станков………………………………..……67
6.4Определение коэффициента загрузки оборудования…………..……69
6.5Производственные рабочие………………………………………..….70
6.6Расчет производственной площади участка…………………….……73
6.7Описание и принцип работы участка…………………………………75
7БЕЗОПАСНОСТЬ ЖИЗНЕДЕЯТЕЛЬНОСТИ……………………………..77
7.1Введение…………………………………………………………….…..77
7.2Санитарно-гигиенические факторы условий труда………………….78
7.3Характеристика помещений…………………………………………...80
3
7.4 Разновидности опасных вредных факторов………………………….85
8ЭКОЛОГИЯ…………………………………………………………….……90
8.1Введение…………………………………………………………….….90
8.2Энергопотребление и материалоемкость. Способы их уменьшения91
8.3Загрязнение атмосферы……………………………………………….92
8.4Излучение, шум……………………………………………….……….95
8.5Влияние проекта на окружающую природную среду……….……..95
9ЭКОНОМИЧЕСКИЙ РАЗДЕЛ……………………………………………..96
9.1Расчет капитальных вложений……………………………………….97
9.2Расчет технологической себестоимости……………………………..98
10ЗАКЛЮЧЕНИЕ…………………………………..………………….…….105
11СПИСОК ИСПОЛЬЗОВАННОЙ ЛИТЕРАТУРЫ………………………109
Приложения……………………………………………………………...……113
4
2 ВВЕДЕНИЕ
Дипломный проект по специальности «Технология машиностроения» является заключительным этапом подготовки инженеров, это последняя ступень в профессиональной подготовке студента к самостоятельной работе в условиях современного производства.
Работа над дипломным проектом является необходимой, важной и ответственной для будущего специалиста, так как, работая над проектом,
систематизируются и закрепляются полученные в ходе обучения теоретические знания. При проектировании комплексно используются общенаучные, общеинженерные и специальные дисциплины с точки зрения их практического использования в реальных условиях производства для решения инженерных, технологических и организационных задач.
В данной работе представлена технология изготовления Корпуса.
Производство корпусов актуально в настоящее время, так как корпус является деталью, необходимой для слива и налива различных жидкостей,
максимально применяемых в цистернах железнодорожных составов для нефтяной и химической промышленности.
Эффективность производства корпусов, технологический процесс изготовления, качество выпускаемых изделий во многом зависят от опережающего развития производства, станков, оборудования, оснастки, от внедрения новых более эффективных прогрессивных технологий, методов обработки и методов технико-экономического анализа. Важной целью является изучение структуры производства, повышение качественных характеристик машин и оборудования. В связи с этим необходимым условием является длительный непрерывный режим работ при достаточно высоких режимах резания с учетом возможности автоматической замены инструмента.
5
Главной задачей при технологической подготовке производства изготовления корпусов является выпуск изделий заданного качества в
необходимом количестве с минимальной себестоимостью и в заданные сроки. От принятой технологии производства во многом зависит долговечность и надежность работы корпусов. Довольно актуальна проблема повышения технологичности, обеспечения точности, оценки возможных и выбор оптимальных технологических процессов. Вместе с тем развитие новых прогрессивных технологий способствует конструированию более современных машин. При этом весьма важно следить, чтобы воздействие на окружающую среду и человека было минимальным.
Производство изделия, его сущность и методы оказывают
наиболее весомое влияние на технологические, эксплуатационные,
эргономические, эстетические и, конечно, функциональные характеристики
этой продукции, а , следовательно, на еѐ себестоимость, от которой в прямой зависимости находятся цена изделия, спрос на него со стороны
пользователей, объемы продаж, прибыль от реализации, то есть, на все
экономические показатели, которые и определяют финансовую
устойчивость предприятия, его рентабельность и долю на рынке. Таким образом, то, как изготовляется продукция, оказывает влияние на весь жизненный цикл товара.
Также при проектировании необходимо учитывать то обстоятельство,
что производство корпусов может иметь большое количество конкурентов.
Поэтому особо важно оценить все аспекты производства, распространения
и потребления изделия еще на стадии его разработки, чтобы избежать неэффективного использования ресурсов предприятия. Но уделяя большое внимание организации производства, нельзя не упомянуть среди прочего и тот факт, что производство должно быть безопасным для жизни и здоровья человека. Необходимо создание безопасных условий труда производственных рабочих, наладчиков, обслуживающего персонала на
6
данном участке. Опасности и вредности производственной средыто, что окружает человека на рабочем месте. Задача проектированияпринять все меры, которые сведут к минимуму неблагоприятное воздействие этой среды.
А также надо не забывать об окружающей среде. Поэтому при проектировании необходимо оценить степень воздействия проекта на окружающую среду, а также сформулировать мероприятия по защите окружающей среды, а при реализации проекта запустить в работу.
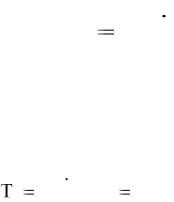
7
3 ТЕХНИКО-ЭКОНОМИЧЕСКОЕ ОБОСНОВАНИЕ ПРОЕКТА
3.1 Определение типа производства
Тип производства определяется через программу выпуска и трудоемкость изготовления детали.
У нас:
-задана программа выпуска в 20000шт/год;
-режим работы- 2 смены;
-действительный годовой фонд времени работы оборудования Fд=4029 ч
[3, с. 22 ].
Известно, что годовая программа выпуска определяет такт выпуска -
промежуток времени между выпуском двух, следующих одна за другой,
деталей.
Определяем такт выпуска по формуле
Т в |
60 FД |
|
|
N |
, где |
(3.1) |
|
|
|
|
Fд - действительный годовой фонд времени работы оборудования;
N- годовая программа выпуска;
Fд=4029 ч. [3 ]
|
60 |
4029 |
12,087 |
мин. |
|
в |
|
|
|||
20000 |
|||||
|
|
|
Трудоемкость определяется штучным средним временем действующего или аналогичного технологического процесса:
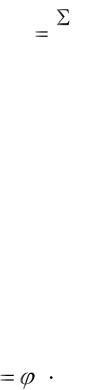
|
|
|
|
|
|
|
|
|
8 |
|
|
|
|
|
|
Т |
i |
|
|
|
|||
|
|
Тш т.ср. |
ш т |
|
|
|
|
||||
|
|
|
n |
[3 ], |
|
(3.2) |
|||||
|
|
|
|
|
|
|
|
||||
|
|
где Т |
i |
|
|
|
|
|
|
|
|
|
|
ш т -штучное время i-ой операции; |
|
||||||||
|
|
n- количество операций (число методов обработки). |
|
||||||||
|
|
Для определения Тшт.ср. воспользуемся приближенными формулами |
|||||||||
для определения норм времени по обрабатываемой поверхности, |
|||||||||||
|
|
содержащимся в источнике [ 3, с.146]. |
|
|
|||||||
|
|
Штучное время i-ой операции рассчитывается по следующей |
|||||||||
формуле: |
|
|
|
|
|
|
|
|
|
||
|
|
Тшт |
к То |
[3 ] , |
|
|
(3.3) |
||||
где То – основное технологическое время. |
|
|
|||||||||
Таблица 3.1. Определение норм времени |
|
|
|||||||||
|
|
|
|
|
|
|
|
|
|||
|
Наименование |
|
|
|
|
Размер обработки, |
Формулы для |
ТО |
|||
|
операций и |
|
|
|
|
выдержать |
определения ТО |
|
|||
|
переходов |
|
|
|
|
|
|
размеры |
|
|
|
|
|
|
|
|
|
|
|
|
мм |
|
мин |
|
1 Точить поверхность |
|
|
|
|
D=150 d=84 |
0,000052(D²d²) |
0,8 |
|||
|
|
|
|
|
|
|
|
|
|||
|
2 Точить поверхность |
|
|
|
|
D=84 L=71,5 |
0,00018*D*L |
1,08 |
|||
|
|
|
|
|
|
|
|
|
|||
|
3 Точить поверхность |
|
|
|
|
D=84 d=65 |
0,000052(D²d²) |
0,147 |
|||
|
4 Точить поверхность |
|
|
|
|
D=65 L=9,5 |
0,00018*D*L |
0,1 |
|||
|
5 Точить поверхность |
|
|
|
|
D=65 d=53 |
0,000052(D²d²) |
0,08 |
|||
|
|
|
|
|
|
|
|
|
|||
|
6 Точить поверхность |
|
|
|
|
D=53 L=9,5 |
0,00018*D*L |
0,09 |
|||
|
7 Точить поверхность |
|
|
|
|
D=50 L=60 |
0,00018*D*L |
0,54 |
|||
|
8 Точить поверхность |
|
|
|
|
D=80 d=50 |
0,000052(D²d²) |
0,2 |
|||
|
9 Точить поверхность |
|
|
|
|
D=80 L=36 |
0.00018*D*L |
0,52 |
|||
|
10 |
Точить поверхность |
|
|
|
D=100 d=69 |
0,000052(D²d²) |
0,09 |
|||
|
11 |
Точить поверхность |
|
|
|
D=100 L=102 |
0.00018*D*L |
1,84 |
|||
|
12 |
Точить поверхность |
|
|
|
D=150 L=100 |
0,000052(D²d²) |
0,65 |
|||
|
|
|
|
|
|
|
|
|
|||
|
13 |
Точить поверхность |
|
|
|
D=150 L=12 |
0.00018*D*L |
0,33 |
|||
|
14 |
Нарезать резьбу |
|
|
|
|
d=80 l=36 |
0,019*d*l |
5,4 |
||
|
|
|
|
|
|
|
|
|
|
||
|
15 |
Сверлить |
|
|
|
|
D=13 L=12 |
0.00052*D*L |
0,35 |
||
|
|
|
|
|
|
|
|
|
|
||
|
16 |
Фрезеровать |
|
|
|
|
L=112 |
0.007*L |
0,79 |
||
|
17 |
Сверлить |
|
|
|
|
D=15 L=13 |
0.00052*D*L |
0,1 |
||
|
|
|
|
|
|
|
|
|
|
||
|
18 |
Сверлить |
|
|
|
|
D=1,5 L=10 |
0,000052*D*L |
0,006 |
||
|
|
|
|
|
|
|
|
|
|
||
|
19 |
Сверлить |
|
|
|
|
D=5 L=10 |
0.000052*D*L |
0,024 |
||
|
|
|
|
|
|
|
|
|
|
|
|
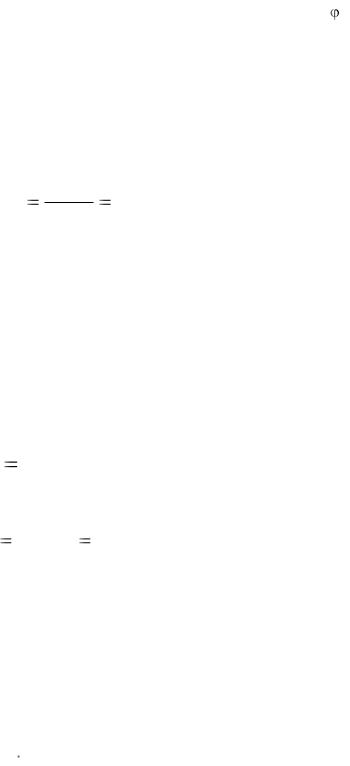
9
|
20 Сверлить |
|
D=6 L=10 |
|
0,000052*D*L |
0,026 |
|
||
|
|
|
|
|
|
|
|
|
|
|
21 Сверлить |
|
D=26 L=10 |
|
0.00052*D*L |
0,14 |
|
||
|
|
|
|
|
|
|
|
|
|
|
22 Сверлить |
|
D=32 L=1 |
|
0.00052*D*L |
0,01664 |
|
||
|
|
|
|
|
|
|
|
|
|
|
Итого: |
|
|
|
|
|
|
13,3 |
|
Таблица 3.2 Расчѐт штучного времени |
|
|
|
|
|
||||
|
|
|
|
|
|
|
|
||
|
Наименование |
Значение ТО, |
|
Значение к |
|
Тшт, |
|
||
|
Операции |
|
мин |
|
[3, с.147 ] |
|
мин |
|
|
|
Точение |
11,87 |
|
2,14 |
|
25,43 |
|
||
|
Сверление |
0,656 |
|
1,72 |
|
1,15 |
|
||
|
Фрезерование |
0,79 |
|
1,84 |
|
1,5 |
|
||
|
|
|
|
|
|
Итого: |
|
28,08 |
|
28,08
Тшт.ср. 8 3,5мин.
Приняты следующие значения коэффициента серийности:
-для массового производства kс = 1
-для крупносерийного kс = 2 – 10
-для среднесерийного kс = 10 – 20
-для мелкосерийного kс > 20
Коэффициент серийности определяется по формуле:
Кс |
|
|
Тв |
|
|
|
|
Тшт.ср. |
(3.4) |
||
|
|
|
|
||
Кс |
12,087 |
|
12 |
||
|
|
|
|
||
3,5 |
|
||||
|
|
|
По ГОСТ 14.004 – 74 Кс =12 соответствует среднесерийному производству.
На нашем участке запуск изделий производится партиями с периодичностью запуска 24 дня.
Расчѐтное количество деталей в партии [3]:
n= |
N a |
(3.5) |
|
F |
|||
|
|
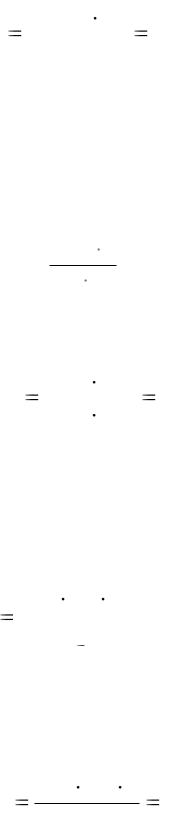
10
где N = 20000 шт. – годовая программа изделия;
а = 24 дня – периодичность запуска – выпуска изделий;
F = 254 дня – число рабочих дней в году.
n |
20000 |
24 |
188шт. |
|
|
||
254 |
|
||
|
|
|
Нам необходимо скорректировать размер партий с учетом удобства планирования и организации производства. Корректировка у нас будет состоять в определении расчетного числа смен на обработку всей партии деталей на основных рабочих местах.
Расчѐтное число смен на обработку партии детали на участке
c= Tшк.ср. n , [3, с.23]
476 0.8
где Tшк.ср. = 7,02 мин – среднее штучно - калькуляционное время по основным
операциям
с |
7,02 |
188 |
3,47. |
|
|
|
|||
476 |
0,8 |
|||
|
|
Принятое число смен спр=4(то есть - это то количество смен, за которые обработается 1 партия деталей).
Затем определим число деталей в партии, необходимых для загрузки оборудования на основных операциях в течение целого числа смен:
nпр. |
476 0,8 cпр |
|
|
[3, с. 23], |
|
|
Тшт к.ср. |
где 476действительный фонд времени работы оборудования в смену, мин;
0,8- нормативный коэффициент загрузки станков в серийном производстве.
476 0,8 4
nпр. 7,02 217шт