
ИВАНОВ А.С. гр. 0041 зу
.pdf91
9 ЭКОНОМИЧЕСКИЙ РАЗДЕЛ
Повышение эффективности общественного производства требует постоянного совершенствования уровня экономики и организации на каждом этапе его функционирования. Для успешного решения данной задачи большое значение имеет наличие у инженерно-технических работников необходимых знаний и опыта в области оценки экономической эффективности технологических процессов.
Большое внимание необходимо уделять усовершенствованию оборудования, средств управления всеми этапами производственного процесса. Необходима грамотная разработка технологического процесса,
включающая в себя выбор материала, выбор способа получения заготовки,
подбора оборудования, режущего инструмента и режимов резания.
В данной выпускной квалификационной работе разрабатывается технологический процесс изготовления детали «Корпус».
Технологический процесс, а с ним и проектируемый участок должны обеспечивать выпуск готовых изделий требуемого качества, в необходимом количестве. Кроме того, необходимо добиваться производства качественных деталей в единицу времени при минимальных приведенных затратах. Итак,
итогом экономического обоснования данной работы является определение затрат на изготовление Корпус.
Себестоимость изготовления складывается из инвестиционных текущих затрат. К инвестиционным затратам относятся вложения в технологическое оборудование, расходы на транспортировку и другие затраты. К текущим затратам относятся стоимость материала, требуемая электроэнергия, амортизацию оборудования ,затраты на заработную плату и др.

92 |
|
|
9.1 Расчет капитальных вложений |
|
|
Капиталовложения рассчитывается по формуле [1]: |
|
|
К = Кт.о. ∙ kзагр, |
(9.1) |
|
где Кт.о – капитальные вложения в технологическое оборудование, руб.; |
||
kзагр – средний коэффициент загрузки оборудования, %. |
|
|
Исходя из рассчитанного ранее в |
пункте 6 пояснительной |
записка |
kзагр. равен 56%. |
|
|
Капиталовложения рассчитываются по формуле [1]: |
|
|
Кт.о. = kz ∙ |
, |
(9.2) |
где kz – коэффициент, учитывающий дополнительные расходы на транспортировку оборудования, его установку и наладку, исходя из опыта
предприятий по выпуску аналогичной продукции можно принять kz =1,1[5]; m - количество единиц технологического оборудования
(количество и наименование определяются технологическим процессом пункт 2 пояснительной записки ).
Ci – оптовая цена оборудования, руб.
В таблице 9.1 указаны цены на технологическое оборудование на данный период времени. Данные цены взяты у официального дилера
продажи станков в России ООО Компания РуСтан [6].
Таблица 9.1 – Стоимость оборудования
Перечень |
Марка |
Кол- |
Стоимость |
|
Всего |
оборудования |
во |
руб. |
|
||
|
|
|
|||
|
|
|
|
|
|
Токарно-винторезный |
16К20Ф3 |
6 |
800 000 |
|
4800000 |
|
|
||||
|
|
|
|
|
|
Сверлильный |
2Р135Ф2 |
2 |
900 000 |
|
1800 000 |
|
|
||||
|
|
|
|
|
|
Горизонтально-фрезерный |
6Р82 |
2 |
570 000 |
|
1140 000 |
|
|
||||
|
|
|
|
|
|
Сверлильный |
2Н135 |
2 |
300 000 |
|
600 000 |
|
|
||||
|
|
|
|
|
|
Итого: |
|
|
|
8340000 |
|
|
|
|
|
|
|
Подставляя данные таблицы 9.1 в формулу (9. 2) можно получить:
93
Кт.о. = 1,1∙8340000=9174000 руб.
Общий объем выпуска деталей участка составляет n=20 000 шт., а
рассматриваемая партия деталей n=2000 шт.
В результате технологических расчетов получаем, что средняя годовая трудоемкость изготовления партии деталей n=1785 шт. составляет 10% от всего объема деталей, тогда
Кт.о. = 0,1 ∙ 9174000 = 917400 руб;
После расчета производственных затрат, составивших 917400 руб.,
необходимо рассчитать текущие затраты.
9.2 Расчет технологической себестоимости
9.2.1 Затраты на основные материалы Материалом, применяемым для изготовления детали «корпус»
выбрана сталь 40Х. |
|
Затраты на основные материалы определим по формуле [1]: |
|
См = Нн ∙ Цм – Но ∙ Цо , |
(9.3) |
где Нм – норма расхода на единицу продукции, исходя из расчета |
|
массы заготовки Нм = 4,4кг.; |
|
Цм – цена материала на единицу веса, исходя из [2] стоимость |
|
1тонны металла составляет 25000 руб. (25 руб./кг); |
|
Но – отходы на единицу продукции; |
|
Цо – цена отходов на единицу веса, исходя из [2] |
стоимость |
1тонны отходов металла составляет 4 000 руб. (4 руб./кг) |
|
Количество отходов на единицу продукции рассчитывается по |
|
формуле [1]: |
|
Но = Нм – Мд , |
(9.4) |
где Мд – масса готовой детали, исходя из расчета, масса готовой детали
3,8 кг.
Но = 4,4 – 3,8 = 0,6 кг;

94 |
|
|
См = 4,4∙25-0,6 ∙4 |
=107,6 руб. |
|
После расчета затрат на материалы рассчитаем затраты на |
||
технологическую энергию , необходимую для изготовления Корпуса. |
|
|
9.3.2 Затраты на технологическую энергию |
|
|
Затраты на технологическую энергию определяем по формуле [3]: |
|
|
Сэ = Нэн ∙ Цэ, |
(9.5) |
|
где Нэн – норма расхода энергии на изготовление одной детали; |
|
|
Цэ – цена 1 кВт ∙ ч в руб. Цэ = 2,89 руб./кВт ∙ ч. [4]. |
|
|
Норма расхода энергии рассчитывается по формуле [3]: |
|
|
Нэн = |
, |
(9.6) |
где Р – установленная мощность электродвигателя, кВт; К – коэффициент загрузки по мощности;
М – сменная производительность оборудования, М = 32 шт./смену, исходя из возможности оборудования и производственного технологического процесса.
Данные по затратам на энергию по всему технологическому процессу занесем в таблицу 9.2.
Коэффициенты К и Р были посчитаны ранее в пункте 5 поястнительной записки.
Таблица 9.2 – Данные по оборудованию
№ операции |
Наименование операции |
К |
Р |
Сэ |
|
|
|
|
|
015 |
Токарная |
0,7 |
10 |
1,75 |
|
|
|
|
|
020 |
Токарная |
0,7 |
10 |
1,75 |
|
|
|
|
|
025 |
Сверлильная |
0,64 |
3,7 |
0,592 |
|
|
|
|
|
030 |
Фрезерная |
0,6 |
2,2 |
0,33 |
|
|
|
|
|
040 |
Сверлильная |
0,5 |
2,2 |
0,275 |
|
|
|
|
|
045 |
Сверлильная |
0,5 |
2,2 |
0,275 |
|
|
|
|
|
050 |
Сверлильная |
0,8 |
7,5 |
1,5 |
|
|
|
|
|
Для примера рассчитаем затраты на энергию для операции 015.

95
Нэн = = 0,33 кВт ∙ ч/дет.
Сэ = 0,33 ∙ 2,89 = 0,96 руб./дет.
Для остальных операций был проведен аналогичный расчет.
Далее рассчитаем заработную плату основных рабочих.
9.3.3 Затраты на заработную плату основных производственных рабочих
Затраты на зарплату основных производственных рабочих определяем по формуле [5]:
Зш = , (9.7)
где n – количество операций технологического процесса;
Нв – норма штучного времени на операцию (определена в пункте 2
пояснительной записке);
Тст – часовая тарифная ставка с доплатами;
|
Здоп – дополнительная заработная плата (20% от Зосн – принято на |
предприятии ОАО Машиностроительный завод Контур); |
|
|
Ос – единый социальный налог, в настоящий момент принято 26,5% |
от |
, из [5]. |
Для примера рассчитаем заработную плату рабочего, выполняющего токарную операцию 015.
Заработная плата, за изготовление 1 детали:
Зш1 = 60 ∙ 1,13= 67,8 руб./шт.
Аналогичным образом рассчитываем заработную плату на остальные операции.
Зная основную заработную плату на выполнение работы можно рассчитать полную заработную плату основных производственных рабочих.
Зш = 232,08+ 0,2∙232,08+ 0,265∙(232,08+ 46,416) =352,3 руб.\дет.
Результаты сводим в таблицу 9.3.
Разряд основных рабочих занятых по изготовлению детали Корпус 5.
Исходя из требований изготовления детали, а так же имеющегося
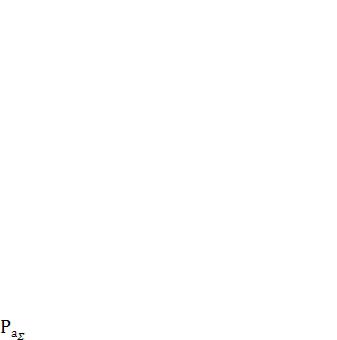
96
оборудования рабочие данной квалификации лучше других подойдут для
данного производства.
Таблица 9.3 – Расчет заработной платы
Перечень |
Часовая |
Норма |
Расход зарплаты |
|
тарифная |
||||
операций |
времени, час |
руб/шт |
||
ставка, руб. |
||||
|
|
|
||
|
|
|
|
|
Токарная |
60 |
1,13 |
67,8 |
|
|
|
|||
|
|
|
|
|
Токарная |
60 |
1,36 |
81,6 |
|
|
|
|||
|
|
|
|
|
Сверлильная |
60 |
0,35 |
21 |
|
|
|
|||
|
|
|
|
|
Фрезерная |
60 |
0,72 |
43,2 |
|
|
|
|||
|
|
|
|
|
Сверлильная |
60 |
0,106 |
6,36 |
|
|
|
|||
|
|
|
|
|
Сверлильная |
60 |
0,05 |
3 |
|
|
|
|||
|
|
|
|
|
Сверлильная |
60 |
0,152 |
9,12 |
|
|
|
|||
|
|
|
|
|
Итого: |
|
|
232,08 |
|
Далее рассчитаем амортизационные отчисления. |
|
9.2.4 |
Амортизационные отчисления |
|
Срок службы каждого из станков выбираем по паспорту и принимаем |
||
равным 10 |
годам. |
|
Годовая суммарная амортизация рассчитывается по формуле [3]: |
|
|
|
= А ∙ На, |
(9.8) |
где А – стоимость оборудования;
На – норма амортизации.
Норму амортизации находим по формуле [3]:
На = , (9.9)
где Си – срок использования станка, лет.
Произведем расчет для токарной операции 015:
На = = 0,1
Произведем все необходимые расчеты для всех станков технологического процесса. Тогда из (9.8) следует:

97
= 800 000∙0,1=80 000 руб.
С учетом, что общий объем выпуска деталей участка составляет n=20000 шт. амортизация на 1 шт. будет составлять:
=
= 4 руб.
Расчет амортизации на 1 шт. с учетом всех операций технологического процесса [3]:
|
|
Ра = , |
|
(9.10) |
||
|
|
Ра = |
= 12,85 руб. |
|
|
|
Таблица 9.4 – Годовая амортизация |
|
|
|
|||
|
|
|
|
|
|
|
|
|
|
|
|
Амортиза- |
|
Перечень |
Марка |
Кол-во, |
Стоимость, |
Срок |
ция |
|
оборудования |
шт. |
руб |
службы |
годовая, |
||
|
||||||
|
|
|
|
|
руб |
|
Токарно- |
16К20Ф3 |
6 |
800 000 |
10 |
80 000 |
|
винторезный |
|
|||||
|
|
|
|
|
||
Сверлильный |
2Р135Ф2 |
2 |
900 000 |
10 |
90 000 |
|
|
|
|
|
|
|
|
Горизонтально- |
6Р82 |
2 |
570 000 |
10 |
57 000 |
|
фрезерный |
||||||
|
|
|
|
|
||
Сверлильный |
2Н135 |
2 |
300 000 |
10 |
30 000 |
|
|
|
|
|
|
|
|
Итого |
|
|
|
|
257000 |
|
|
|
|
|
|
|
Далее произведем расчет затрат на содержание и ремонт оборудования.
9.2.4 Затраты на ремонт и содержание оборудования Затраты на ремонт и содержание оборудования составляют 15% [6] от
балансовой стоимости оборудования и находятся по формуле [4]:
Зс = С ∙ Нр, (9.11)
где Нр – годовая норма отчислений на ремонт и содержание.
Зс = 0,15∙8340000=1251000 руб.
Тогда затраты на ремонт и содержание оборудования, приходящиеся на
1 шт., для технологических процессов будут определяться по формуле [4];

|
|
98 |
|
|
|
|
ЗС.шт = |
, |
(9.12) |
|
ЗС.шт = |
= 62,55 руб.\дет. |
|
|
После расчета затрат на ремонт и содержание оборудования |
||||
рассчитаем накладные расходы. |
|
|
|
|
9.2.5 Накладные расходы |
|
|
|
|
Накладные |
расходы, |
косвенные |
затраты-расходы, |
затраты, |
сопровождающие, сопутствующие основному производству, но не связанные с ним напрямую [6]. Накладные расходы связаны с управлением,
организацией и обслуживание производства.
Накладные расходы определяем по формуле [4]: |
|
|
Цр = |
, |
(9.13) |
где Зш- заработная плата основных производственных рабочих пункт
9.3.3
160%-процентная ставка установлена на ОАО машиностроительный завод Контур.
Цр = = 563,68руб.
Все рассчитанные ранее расходы занесем в таблицу 9.5.
Таблица 9.5 – Расчет технологической себестоимости
Составляющие себестоимости |
Величина руб/дет. |
|
|
Основные материалы |
107,6 |
|
|
Технологическая энергия |
6,472 |
|
|
Зарплата раб. |
352,3 |
|
|
Амортизационные отчисления |
12,85 |
|
|
Ремонт и содержания оборудования |
62,55 |
|
|
Накладные расходы |
563,68 |
|
|
Итого |
1105,5 |
|
|
Годовые расходы |
22110000 |
|
|
99
Целью раздела было рассчитать затраты на себестоимость изготовления единицы продукции, которые составили 1105,5 руб.\дет.,
инвестиционные затраты 9174000 руб., а так же годовые затраты,
составившие 22 110 000 руб.
100
10 ЗАКЛЮЧЕНИЕ
При выполнении дипломного проекта разработаны разделы согласно заданию на проектирование.
1.Выполнена технологическая часть проекта.
Произведено определение типа производства, согласно рассчитанному коэффициенту серийности производства, производство соответствует среднесерийному. Изготовляемая деталь – корпус - предназначен для установки на трубопроводах передвижной установки в качестве запорных устройств и запорно-регулирующих с целью управления подачей рабочих сред. Корпус изготовлен из стали 40Х ГОСТ 1050-88. В условиях среднесерийного производства деталь частично технологична с точки зрения механической обработки. Конструкция детали обеспечивает свободный доступ инструмента ко всем обрабатываемым поверхностям и допускает применение высокопроизводительных методов обработки, имеет хорошие базовые поверхности последующих операций.
В результате сравнения двух методов получения исходной заготовки было определено , что метод получения исходной заготовки штамповкой технологически наиболее выгоден. Когда используем поковку в качестве исходной заготовки, мы снимаем меньшие припуски при обработке, т. е.
отходов при изготовлении корпуса из поковки будет меньше, а форма исходной заготовки наиболее близка к форме детали. Был произведен расчет стоимости исходной заготовки, в результате которого экономически выгоднее получать исходную заготовку методом штамповки.
Разработан маршрутный технологический процесс изготовления корпуса. Так как изготовление вала червячного осуществляется в условиях крупносерийного производства, то в данном технологическом процессе используются станки с ЧПУ (16А20Ф3, 2Р135Ф2), также используются