
ИВАНОВ А.С. гр. 0041 зу
.pdf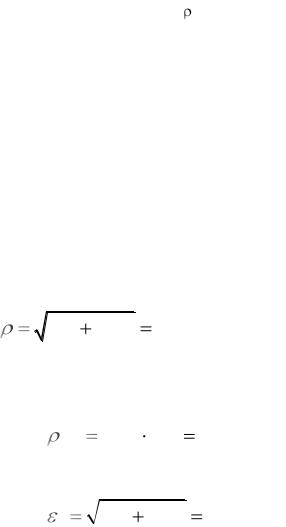
21
Таблица 2.2 Расчет припусков и предельных размеров отверстия Ø84+0,087
|
|
|
|
|
Расчетный припуск 2Zimin, мкм |
Расчетный размер dp, мм |
Допуск на изготовление Тd, мкм |
Принятые |
Получаемые |
|||
|
|
|
|
|
предельные |
|||||||
|
Элементы прикуска, |
размеры по |
||||||||||
Технолог |
припуски, |
|||||||||||
|
мкм |
|
переходам |
|||||||||
ические |
|
|
мкм |
|||||||||
|
|
|
|
(округлен- |
||||||||
переходы |
|
|
|
|
|
|
||||||
|
|
|
|
ные), мм |
|
|
||||||
обработки |
|
|
|
|
|
|
||||||
Rz |
h |
|
ε |
|
|
2Zmax |
2Zmin |
|||||
|
|
|
|
|||||||||
|
|
dmax |
dmin |
|||||||||
|
|
|
|
|||||||||
|
|
|
|
|
|
|
||||||
|
|
|
|
|
|
|
|
|
|
|||
|
|
|
|
|
|
|
|
|
|
|
|
|
Заготовка |
200 |
300 |
563 |
- |
- |
82,47 |
600 |
82,47 |
81,87 |
- |
- |
|
: литьѐ |
||||||||||||
|
|
|
|
|
|
|
|
|
|
|
||
Черновое |
|
|
|
|
|
|
|
|
|
|
|
|
растачива |
50 |
50 |
28 |
168 |
2180 |
83,65 |
400 |
83,65 |
83,25 |
2380 |
2180 |
|
ние |
|
|
|
|
|
|
|
|
|
|
|
|
Чистовое |
|
|
|
|
|
|
|
|
|
|
|
|
растачива |
25 |
25 |
- |
8 |
258 |
83,91 |
200 |
83,91 |
83,75 |
500 |
260 |
|
ние |
|
|
|
|
|
|
|
|
|
|
|
|
Тонкое |
|
|
|
|
|
|
|
|
|
|
|
|
растачива |
5 |
5 |
- |
- |
116 |
84,087 |
87 |
84,087 |
84,0 |
250 |
115 |
|
ние |
|
|
|
|
|
|
|
|
|
|
|
502 |
5602 |
563 мкм |
Остаточное пространственное отклонение после чернового растачи-
вания:
ост |
0, 05 563 28 мкм |
|
Погрешность установки:
у502 1602 168 мкм
Допуск на размер 130 для штамповки – 600 мкм. При черновом растачивании возможно получение 12-го квалитета с допуском 400 мкм. При чистовом растачивании возможно получение 10-го квалитета с допуском 160
мкм. При тонком растачивании возможно получение 9-го квалитета с допуском 87 мкм.
На основании записанных в таблице данных производим расчѐт минимальных значений межоперационных припусков, пользуясь основной формулой:
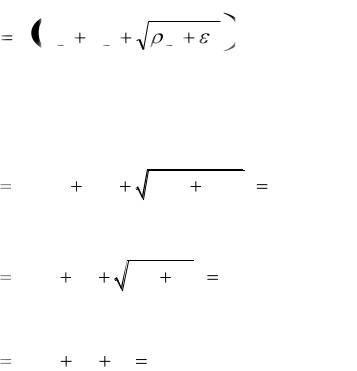
22
2Zi min 2 RZi 1 hi 1 |
2 |
2 |
(2.12) |
i 1 |
i |
Минимальный припуск под растачивание:
Черновое
2Zi min |
2 |
200 |
300 |
5632 |
1682 2180 мкм , |
чистовое |
|
|
|
|
|
|
|
|
|
|
|
2Zi min |
2 |
50 |
50 |
282 82 |
258 мкм , |
тонкое |
|
|
|
|
|
2Zi min |
2 25 |
25 8 |
116 мкм |
Определяем расчетный размер на растачивание: dр тонк. = 84 + 0,087 = 84,087 мм;
dр чист. = 84,087 – 0,116 = 83,909 мм; dр черн. = 83,909 – 0,258 = 83,651 мм. dр заг = 83,651 – 2,180 = 81,471 мм.
Определяем предельные размеры, округление производим до того знака десятичной дроби с каким дан допуск на размер каждого перехода.
Наименьшие предельные размеры вычисляем вычитанием допуска из наибольшего предельного размера .
dmin тонк. = 84,087 – 0,087 = 84 мм; dmin чист. = 83,91 – 0,16 = 83,75 мм; dmin черн. = 83,65 – 0,4 = 83,25 мм. dmin заг = 82,47 – 0,6 = 81,87 мм.
Минимальные предельные значения припусков 2Zmin равны разности наименьших предельных размеров выполняемого и предшествующего переходов, а максимальные значения 2Zmax соответственно – разности наибольших предельных размеров.
Для тонкого растачивания:
23
2Zmax тонк. = 84 – 83,75 = 250 мкм; 2Zmin тонк. = 84,087 – 83,91 = 115 мкм;
Для чистового растачивания:
2Zmax чист. = 83,75 – 83,25 = 500 мкм; 2Zmin чист. = 83,91 – 83,65 = 260 мкм;
Для чернового растачивания:
2Zmax черн. = 83,25 – 82,87 = 2380 мкм; 2Zmin черн. = 83,65 – 82,47 = 2180 мкм;
Проведем проверку выполненных расчетов:
Ттонк. – Тчист. = Zmax тонк. – Zmin тонк.
160 – 25 = 250 – 115 = 135.
Расчеты выполнены верно.
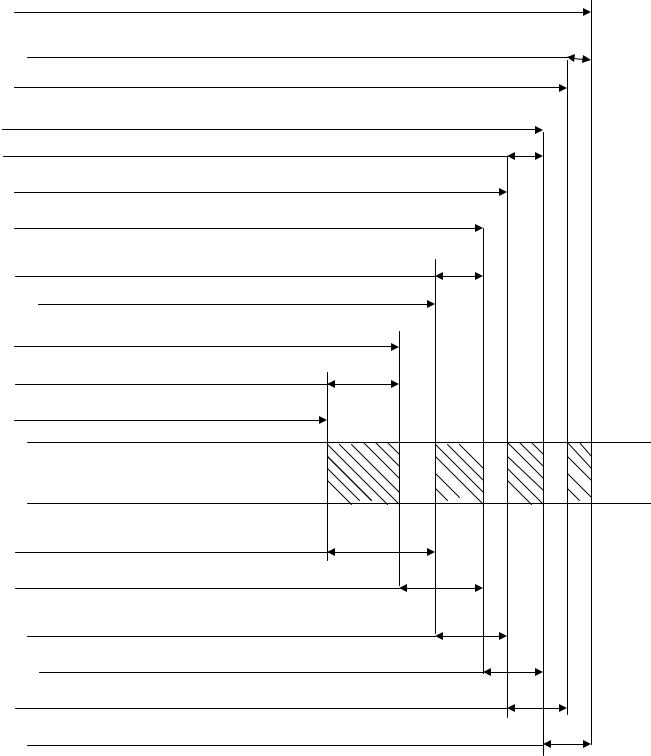
24 |
d max растачивание тонкое 84,087 мм |
δ растачивание тонкое 87 мкм |
d min растачивание тонкое 84 мм |
d max растачивание чистовое83,91 мм |
δ растачивание чистовое 160 мкм |
d min растачивание чистовое 83,75 мм |
d max растачивание черновое 83,65 мм |
δ растачивание черновое точения чист. 400 мкм |
d min растачивание черновое 83,25 мм |
d max заготовки 82,47 мм |
δ заготовки 600мкм |
d min заготовки 81,87мм |
2Z max растачивание черновое 2380 мкм |
2Z min растачивание черновое 2180 мкм |
2 Z max растачивание чистовое500 мкм |
2Z min растачивание чистовое 260 мкм |
2Z max растачивание тонкое 250 мкм |
2Z min растачивание тонкое 115 мкм |
Рис.3.1 Схема графического расположения припусков и допусков по
обработке поверхности Ø84Н9(+0,087)

25
4.2.2 Рассчитываем припуски и предельные размеры на 138-0,10 мм. Расчет припусков и предельных отклонений по технологическим переходам на обработку заносим в таблицу 3.3.
Таблица 3.3 - Расчет припусков и предельных размеров
Технолог |
|
Элементы |
Расчетный |
Расчетный |
|
Принятые |
Предельные |
|||||
|
минималь- |
Допуск |
припуски, |
|||||||||
и-ческие |
прикуска, мкм |
припуск |
размеры, мм |
|||||||||
ный раз- |
Т, мкм |
мкм |
||||||||||
переходы |
|
|
|
|
Zimin, мкм |
|
|
|||||
|
|
|
|
мер Lp, мм |
|
|
|
|
|
|||
Rz |
|
h |
|
|
Lmax |
Lmin |
Zmin |
Zmax |
||||
|
|
|
|
|
||||||||
|
|
|
|
|
|
|
|
|
|
|
|
|
Заготовка |
15 |
|
250 |
1890 |
|
139,416 |
3000 |
140,4 |
139,4 |
– |
– |
|
|
|
|
||||||||||
: поковка |
0 |
|
|
|||||||||
|
|
|
|
|
|
|
|
|
|
|||
|
|
|
|
|
|
|
|
|
|
|
|
|
Точение |
50 |
|
50 |
113 |
2580 |
138,836 |
400 |
139,3 |
138,9 |
2500 |
5100 |
|
черновое. |
|
|||||||||||
|
|
|
|
|
|
|
|
|
|
|
||
|
|
|
|
|
|
|
|
|
|
|
|
|
Точение |
30 |
|
30 |
76 |
426 |
137,90 |
100 |
138,0 |
137,90 |
1000 |
1300 |
|
чистовое |
|
|||||||||||
|
|
|
|
|
|
|
|
|
|
|
||
|
|
|
|
|
|
|
|
|
|
|
|
Суммарные отклонения расположения поверхностей определяем по формуле (3.4):
|
2 |
2 |
2 |
|
(3.4) |
|
cм |
кор |
ц |
||
|
|
||||
где см – отклонение от соосности, |
см |
1000 мкм |
|
||
|
|
|
|
|
|
кор – отклонение оси поковки от прямолинейности; |
|
||||
кор |
к L , |
|
|
(3.5) |
где к – кривизна стержня после высадки фланца, к =6 мкм/мм.
мкм на 1 мм [3, таб.19, стр187],
кор 6 85 510 мкм.
ц – погрешность оси заготовки в результате погрешности зацентровки;

|
|
|
26 |
|
|
|
|
|
|
|
|
|
|
|
|
Т |
2 |
|
|
|
ц |
|
|
0,252 , |
(3.6) |
||
2 |
|
|||||
|
|
|
|
|
|
где Т– допуск на заготовку, мкм.
|
3000 |
2 |
|
ц |
|
0,252 1520 мкм. . |
|
2 |
|||
|
|
загот
10002 5102 15202 1890 мкм.
Остаточное пространственное отклонение определяем по формуле (3.7): i = заг ki (3.7)
где ki – коэффициент учитывающий вид обработки:
для чернового точения k = 0,06;
точ.чер. = 18900,06 = 113 мкм,
для чистового точения k = 0,04;
точ.чис. = 18900,04 = 76 мкм,
Рассчитываем минимальное значение припуска при параллельной обработке поверхности по формуле (3.8):
z |
i min |
Rz h i 1 |
|
(3.8) |
|
|
i |
1 |
|
|
|
|
Точение чистовое :
zi min |
2 50 50 113 426 мкм. |
Аналогичным образом рассчитываем zi min для остальных операций.
Результаты сводим в таблицу 6.
Определяем расчетный размер на точение черновое:
Lp.min 138,41 0,426 138,836 мм.
Определяем предельные размеры. Наибольшие предельные размеры вычисляем прибавлением допуска к округленному наименьшему предельному размеру.
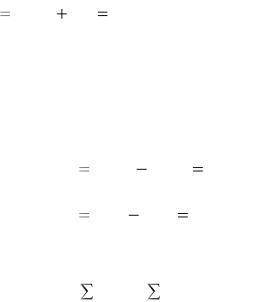
27
Для чернового точения
dмах 138,9 0, 4 139,3 мм
Предельное значение припусков zmax определяем, как разность наибольших предельных размеров, а zmin , как разность наименьших размеров предыдущего и выполняемого перехода.
zmax точ.черн. |
142,4 |
139,3 |
5,1 мм |
zmin.точ.черн. |
59,4 |
56,9 |
2,5 мм |
Производим проверку:
Tзаг. – Tдет. = zmax - zmin
2980 = 2980
Все полученные данные при вычислении предельных размеров и припусков заносим в таблицу 3.3 и строим схему расположения припусков
(рисунок 3.2).
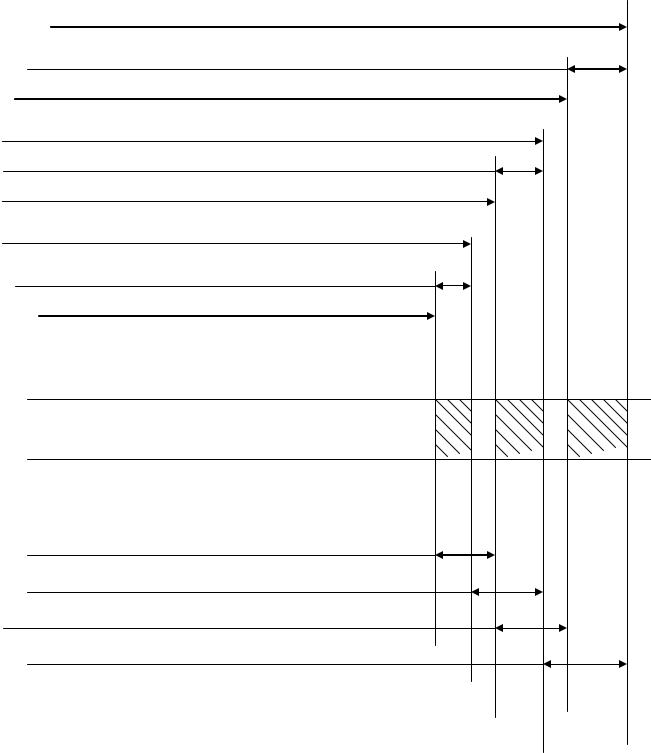
|
28 |
L max заготовка 141,4 мм |
|
δ заготовки 3000 мкм |
|
L min заготовки 139,4 мм |
|
L max точения чер. 140,3 мм |
|
δ точения чер. 400 мкм |
|
L min точения чер. 138,9 мм |
|
L max точения чист. 138,0 мм |
|
δ точения чист. 100 мкм |
|
L min точения чист. 137,9 мм |
|
Z min точения чист. |
1000 мкм |
Z max точения чист. 130 мкм |
|
Z min точения чер. |
2500 мкм |
Z max точения чер. |
5100 мкм |
Рис.3.2 Схема графического расположения припусков и допусков по
обработке поверхности 138(-0,1)

29
4.3 Расчет режимов резания
Проведѐм расчѐт режимов резания на токарную операцию 010.
Обрабатываем диаметр D=102 мм (лист 1). Инструмент – резец проходной,
режущая пластина Т15К6, главный угол в плане о = 90о; передний угол о = 10о, угол наклона главного лезвия о = 5о, вспомогательный угол в плане
о1=20о. Размер державки 25х16 мм. Обработка происходит на токарно-
винторезном станке 16А20Ф3. Мощность главного привода N=10КВт.
Материал заготовки – Сталь 40Х.
3.1.1 Глубина резания
Глубина резания t при точении и отсутствии ограничений по мощности оборудования, жѐсткости системы СПИД принимается равной припуску на обработку. В нашем случае, учитывая расчѐты, проделанные в предыдущей главе (см. таблицу 3.4.1), припуск на предварительную обработку равен 2,14
мм. Следовательно, принимаем глубину резания t равной 2,14 мм.
3.1.2 Подача
Подача s при черновом точении принимается максимально допустимой по мощности оборудования, жѐсткости системы СПИД, прочности режущей пластины и прочности державки. Выбираем подачу в соответствии с таблицей (ТМ1, стр. 267). Принимаем s = 0,31мм/об
3.1.3 Скорость резания
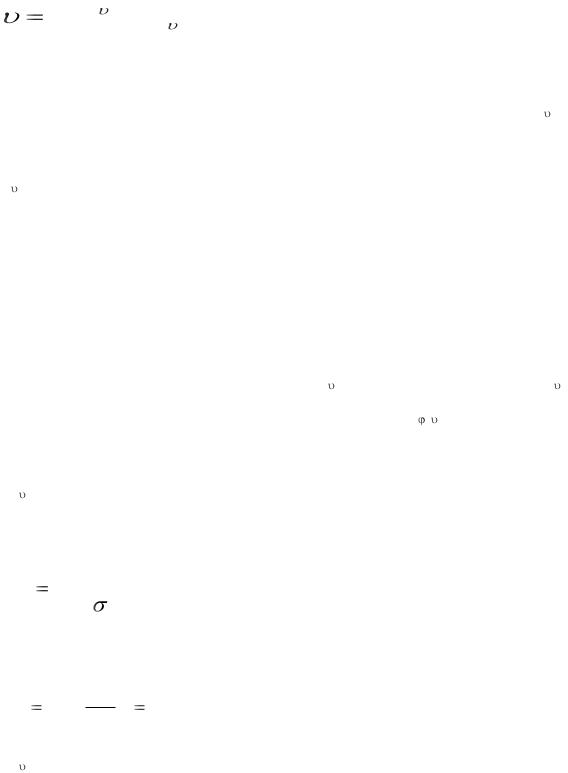
30
Скорость резания при наружном продольном и поперечном точении рассчитывают по эмпирической формуле (3.4.1).
|
С |
|
|
|
K |
|
|
|
|
|
|
(3.4.1) |
|
Т |
m |
x |
s |
y |
||
t |
|
|
|
|
Среднее значение стойкости инструмента Т при одноинструментной обработке – 30-60 мин. Принимаем Т = 45 мин. Значения коэффициента C ,
показателей степени x, y и m приведены в таблице (ТМ1, стр. 269).
C = 420
x = 0,15
y = 0,35
m = 0,20
Коэффициент Кявляется произведением коэффициентов,
учитывающих влияние материала заготовки Км , состояния поверхности Кп ,
материала инструмента Кии углов в плане резцов К
и К 1 . Выбираем вышеуказанные коэффициенты по таблицам (ТМ1, стр. 263, 265, 271).
Км определяется по формуле (3.4.2)
|
|
|
750 |
n |
|
k |
м v k |
Г ( |
|
) v |
(3.4.2) |
|
в
предел прочности ζв = 800 МПа; nv=1; kг=0,95; тогда:
kм v 0,95(800750)1 0,89
Км =0,89
Кп= 1
Ки= 1,9